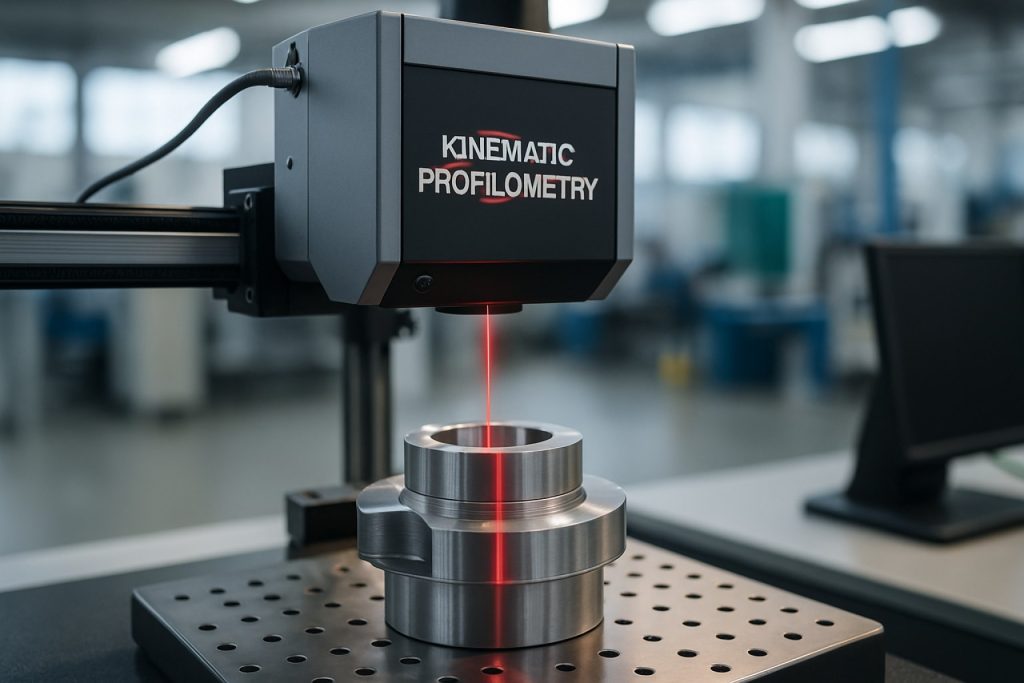
Table of Contents
- Executive Summary: Market Outlook to 2030
- Core Principles of Workpiece Kinematic Profilometry
- Key Industry Players and Technology Innovators
- 2025 Market Size, Segmentation, and Forecasts
- Emerging Applications Across Manufacturing Sectors
- Technological Breakthroughs and Hardware Advancements
- Integration with Automation, AI, and Smart Factories
- Competitive Landscape and Strategic Partnerships
- Challenges, Barriers, and Regulatory Considerations
- Future Trends: What’s Next for Kinematic Profilometry?
- Sources & References
Executive Summary: Market Outlook to 2030
Workpiece kinematic profilometry, a technology enabling high-precision surface and dimensional analysis during or after machining processes, is poised for significant evolution and adoption through 2030. As global manufacturing sectors—including automotive, aerospace, precision engineering, and electronics—continue their push towards smarter and more automated factories, demand for real-time, non-contact metrology solutions is accelerating.
In 2025, the market is witnessing notable advances in inline profilometry systems that integrate directly with production lines. Companies such as Carl Zeiss AG and Keyence Corporation have launched new generations of non-contact sensors and automated inspection systems capable of nanometer-scale accuracy, supporting both static and dynamic measurement of complex workpiece geometries. These solutions leverage sophisticated kinematic tracking and real-time data analytics, enabling rapid defect detection and adaptive process control.
A key trend is the adoption of machine vision and artificial intelligence (AI) in profilometry platforms. Industrial leaders like Renishaw plc have introduced AI-enabled measurement heads that self-calibrate and optimize inspection routines for varying workpiece movement profiles, reducing cycle times and manual intervention. Furthermore, open interface standards promoted by organizations such as VDMA (Verband Deutscher Maschinen- und Anlagenbau) are facilitating interoperability between profilometry devices and broader factory automation ecosystems.
Data from major machine tool and measurement system manufacturers indicate robust growth in demand for inline, kinematic surface metrology across Asia-Pacific and North America. Investments in e-mobility (notably electric vehicle component manufacturing), semiconductors, and high-precision medical devices are fueling orders for advanced profilometry systems. For instance, Hommel-Etamic (a division of Jenoptik) and Marposs S.p.A. have both reported double-digit annual increases in sales of integrated surface measurement solutions since 2023.
Looking ahead to 2030, the workpiece kinematic profilometry market is expected to benefit from ongoing advances in sensor miniaturization, cloud-based data integration, and the proliferation of digital twins. Manufacturers are increasingly prioritizing closed-loop quality control and predictive maintenance, both of which rely on the high-resolution, real-time measurement data that kinematic profilometry delivers. As industrial standards mature and costs decline, adoption is projected to extend beyond large enterprises to small and medium-sized manufacturers, driving a broad-based expansion of the market.
Core Principles of Workpiece Kinematic Profilometry
Workpiece Kinematic Profilometry (WKP) refers to the precise measurement and analysis of the motion and surface profile of a workpiece during or after manufacturing processes. The core principles of WKP in 2025 center on high-resolution, non-contact metrology, real-time data acquisition, and advanced kinematic modeling to ensure product quality and process optimization.
At the heart of WKP is the integration of advanced sensor technologies—such as laser triangulation, white light interferometry, and chromatic confocal sensors—capable of capturing surface topography and motion with sub-micron accuracy. These sensors are frequently mounted on coordinate measuring machines (CMMs), robotic arms, or directly within machining centers to enable in-process or post-process inspection. Leading metrology companies like Carl Zeiss AG and KEYENCE CORPORATION have developed profilometers that combine surface profiling with positional tracking, allowing for kinematic analysis of workpieces in dynamic environments.
A core WKP principle is the use of mathematical algorithms to reconstruct the kinematic path of a workpiece based on time-stamped position data. This involves synchronizing motion capture with surface measurement to analyze how the workpiece moves and deforms under operational loads. Recent advances leverage high-speed data acquisition systems and edge computing to process this information in real time. For instance, Renishaw plc offers solutions that combine laser interferometry with motion tracking, enabling detailed analysis of workpiece kinematics in precision machining environments.
Digital twin technology is increasingly incorporated, whereby a virtual representation of the workpiece, updated in real time, mirrors the actual kinematic and surface profile data. This principle allows for predictive analysis and adaptive process control, reducing rework and improving yield. Companies such as Hexagon AB are actively integrating digital twins with their metrology platforms, enabling seamless feedback between measurement and manufacturing systems.
The outlook for 2025 and the coming years points towards tighter integration of WKP within Industry 4.0 ecosystems. The core principles will expand to include AI-driven defect detection, machine learning-based kinematic modeling, and cloud-based analytics, further enhancing the speed and accuracy of workpiece inspection. As metrology hardware and software continue to evolve, WKP will remain central to advanced manufacturing, especially in aerospace, automotive, and precision engineering sectors.
Key Industry Players and Technology Innovators
The global landscape of workpiece kinematic profilometry in 2025 is shaped by a dynamic mix of established metrology leaders, agile innovators, and specialist equipment manufacturers. These industry players are pushing the boundaries in non-contact surface measurement, precision motion tracking, and real-time kinematic (RTK) analysis for both research and industrial manufacturing applications.
Among the leading entities, Carl Zeiss AG continues to set benchmarks with its coordinate measuring machines (CMMs) and advanced optical profilometry solutions, integrating multi-sensor platforms and kinematic compensation algorithms to achieve sub-micron precision. Zeiss’s recent expansion in automated, in-line metrology underscores the growing demand for high-throughput, real-time profilometry directly on the production floor.
KEYENCE CORPORATION further strengthens its position with the launch of new laser profilometers capable of 3D kinematic surface mapping at production speeds. Their focus on user-friendly, high-speed inline measurement systems responds to automotive, electronics, and medical device manufacturers’ needs for rapid feedback and adaptive process control.
In the domain of high-precision motion tracking, Renishaw plc has advanced its 5-axis CMM and machine tool probing systems, employing complex kinematic models to profile and compensate for dynamic errors during high-speed machining. Their calibration and compensation technologies are increasingly adopted in aerospace, where part tolerances are exceptionally tight.
Specialist innovators such as Bruker Corporation are pioneering non-contact white light interferometry and atomic force microscopy, extending kinematic profilometry to the nanoscale. Bruker’s instruments are pivotal in research labs and semiconductor fabs where critical dimension measurements must account for complex motion-induced artifacts.
Collaborative industry-academic projects, notably those coordinated by organizations like VDMA (German Engineering Federation), are accelerating the development of open, modular platforms for kinematic profilometry that enable easier integration into diverse manufacturing environments.
Looking ahead, the outlook for workpiece kinematic profilometry is defined by further convergence of sensor fusion, AI-driven data analysis, and cloud-based process monitoring. The next few years will likely see increased adoption of smart profilometry systems capable of self-calibration and predictive maintenance, as well as more widespread deployment in additive manufacturing and micromachining sectors.
2025 Market Size, Segmentation, and Forecasts
The global market for workpiece kinematic profilometry is poised for notable growth in 2025, driven by the expanding adoption of advanced metrology solutions across precision manufacturing, automotive, aerospace, and electronics sectors. This technique—enabling high-resolution, real-time surface measurement and motion tracking—has become integral for ensuring product quality and process optimization in high-value industries.
Based on recent updates from industry leaders, the segmentation of the market is primarily delineated by end-use industry, measurement technology (such as laser-based, interferometric, and optical profilometry), and regional uptake. Key manufacturers such as Carl Zeiss AG and Keyence Corporation report increasing demand for integrated profilometry systems capable of both static and dynamic surface analysis. This is particularly relevant in automotive and semiconductor manufacturing, where the need for sub-micron accuracy in kinematic profiling is accelerating investments in next-generation measurement platforms.
- Automotive & Aerospace: In 2025, these sectors are projected to contribute over 35% of total market revenue, as per data from Hexagon AB, due to the proliferation of complex component geometries and lightweight materials requiring precise surface characterization.
- Electronics & Semiconductor: Increased adoption of profilometers by companies like Bruker Corporation is anticipated, with the sector expected to see double-digit growth rates, fueled by miniaturization and higher quality standards for microelectronic devices.
- Regional Trends: Asia-Pacific remains the fastest-growing geography, as noted by Keyence Corporation, reflecting substantial investments in electronics manufacturing and automotive production hubs in China, South Korea, and Japan.
Looking ahead, market forecasts through 2027 suggest a compound annual growth rate (CAGR) between 7-10%, propelled by developments such as AI-assisted profilometry, enhanced automation capabilities, and the integration of profilometers into Industry 4.0 environments. Major suppliers continue to invest in R&D for faster, more user-friendly systems that can deliver actionable data in real time, a trend visible in recent product launches from Carl Zeiss AG and Bruker Corporation.
In summary, the 2025 outlook for workpiece kinematic profilometry is robust, with market expansion underpinned by ongoing technological innovation and the critical role profilometry plays in modern precision manufacturing.
Emerging Applications Across Manufacturing Sectors
Workpiece kinematic profilometry—a non-contact, high-precision method to measure the movement and surface profile of parts during manufacturing—has rapidly advanced in its adoption and scope across diverse industrial sectors. In 2025, this technology is increasingly pivotal for ensuring component quality, optimizing production processes, and enabling real-time digital feedback in smart manufacturing environments.
The automotive industry remains at the forefront, leveraging kinematic profilometry to monitor surface finish and dimensional integrity of critical components such as gears, shafts, and engine parts. For example, Carl Zeiss AG has developed inline profilometry systems integrated with robotic handling, allowing for 100% inspection directly on the production line. This approach reduces scrap, supports traceability, and meets the stringent tolerances required for electrified drivetrains and autonomous vehicle components.
In aerospace, where material integrity and precision are paramount, companies like KEYENCE Corporation and Renishaw plc have pushed the envelope with high-speed profilometers that can capture topography and detect minute defects on turbine blades and fuselage panels during both additive and subtractive manufacturing. These systems support predictive maintenance and certification processes, as demanded by evolving regulatory standards.
Medical device manufacturing is another sector seeing significant gains from kinematic profilometry. The miniaturization trend in implants and surgical tools necessitates non-destructive, ultra-fine measurement capabilities. Bruker Corporation has introduced solutions capable of mapping complex geometries in orthopedic and dental components, enhancing both reliability and patient safety.
Electronics and semiconductor fabrication also present fertile ground. Profilometry systems from KLA Corporation are being adopted to manage layer thickness and surface uniformity in wafer processing, supporting the production of advanced microchips where sub-micron precision is crucial.
Looking ahead, the next few years will likely see further convergence of kinematic profilometry with machine learning, big data analytics, and digital twin architectures. Real-time feedback loops between profilometers and manufacturing execution systems are expected to drive autonomous process control—minimizing downtime and maximizing throughput. Industry bodies such as VDMA are promoting interoperability standards to facilitate integration across multi-vendor environments, ensuring that profilometry data can be leveraged enterprise-wide for both quality assurance and process optimization.
Technological Breakthroughs and Hardware Advancements
Workpiece kinematic profilometry, which involves the precise measurement of surface profiles during dynamic machining and manufacturing operations, is undergoing significant technological advancements as of 2025. These breakthroughs are driven by increasingly stringent quality requirements in sectors such as aerospace, automotive, and precision engineering, where real-time surface assessment is crucial for process optimization and component validation.
A major leap forward has been the integration of high-speed, non-contact optical sensors, combining laser triangulation and confocal chromatic techniques. Recent systems, such as those developed by KEYENCE CORPORATION and Carl Zeiss AG, offer micron-level resolution even on moving workpieces, enabling true in-process profilometry. These advances are complemented by multi-axis synchronization hardware, allowing for the capture of complex geometries as parts are rotated or translated during machining.
Another notable development is the adoption of advanced data acquisition and processing platforms. Companies like Renishaw plc have introduced ultra-fast data streaming protocols and FPGA-based controllers that can process vast volumes of surface data in real time. This capability is crucial for high-throughput environments, where feedback from kinematic profilometry can be used to trigger adaptive machining corrections on the fly.
The integration of Artificial Intelligence (AI) and machine learning algorithms is also becoming standard in leading-edge profilometry systems. Hexagon AB has embedded AI-driven surface defect recognition and trend analysis into their metrology platforms, enabling predictive maintenance and faster root-cause analysis. These features are particularly valuable as manufacturers face increasing pressure to minimize downtime and scrap rates.
Looking ahead to the next few years, further miniaturization of sensors and the proliferation of edge-computing hardware are expected. Companies such as SICK AG are actively developing compact, ruggedized profilometers that can be integrated directly onto machine tools, even in harsh shop-floor environments. This trend is anticipated to expand the applicability of kinematic profilometry beyond traditional high-value manufacturing, making it accessible to a broader range of industries.
In summary, the ongoing hardware and technological breakthroughs in workpiece kinematic profilometry are positioning it as a cornerstone of the smart manufacturing revolution, with real-time, in-process measurement capabilities set to become ubiquitous across production sectors in the near future.
Integration with Automation, AI, and Smart Factories
Workpiece kinematic profilometry (WKP) is increasingly being integrated into automated manufacturing environments, leveraging advancements in automation, artificial intelligence (AI), and smart factory architectures. As of 2025, industry leaders in metrology and automation are deploying WKP systems that operate seamlessly within digital production lines, aiming to enhance real-time quality control, traceability, and process optimization.
A major trend is the embedding of non-contact profilometry sensors—such as laser triangulation and white-light interferometry—directly onto robotic arms and CNC machines. For example, Carl Zeiss Industrielle Messtechnik and Keyence Corporation have expanded their profilometry solutions to support high-speed, in-line measurements compatible with Industry 4.0 frameworks. These systems collect surface geometry data during or immediately after machining, minimizing downtime and reducing the need for manual inspection.
Integration with AI-driven analytics is another key development. Companies like Renishaw plc are utilizing machine learning algorithms to interpret vast profilometric datasets, enabling automatic detection of surface deviations and predictive maintenance. These AI-enhanced systems can identify wear or tooling issues before they escalate, feeding actionable insights back into the manufacturing execution system (MES) for closed-loop process control.
In the context of smart factories, WKP is being incorporated into digital twins and networked environments. Hexagon AB has recently showcased solutions that link profilometry equipment with factory-wide data platforms, supporting centralized monitoring and adaptive manufacturing strategies. Data interoperability is facilitated through standards such as OPC UA and MTConnect, which enable seamless communication between profilometers, robots, and enterprise systems.
Looking forward, the next few years are expected to see further advances in WKP automation, including greater sensor miniaturization and increased use of collaborative robots (cobots) for flexible inspection tasks. There is also ongoing development in edge computing, allowing profilometry devices to preprocess and analyze data locally for faster decision-making. As smart factories evolve, WKP’s integration with cloud-based analytics, digital twins, and adaptive feedback loops is set to further enhance manufacturing agility and product quality.
Competitive Landscape and Strategic Partnerships
The competitive landscape for workpiece kinematic profilometry is rapidly evolving as manufacturers and technology firms intensify efforts to deliver greater precision, speed, and automation in surface measurement. In 2025, the sector is shaped by the integration of advanced sensor technologies, AI-driven data analytics, and Industry 4.0 connectivity. Major players, including Carl Zeiss AG, KEYENCE CORPORATION, and Hexagon AB, continue to expand their profilometry portfolios, seeking differentiation through innovations in non-contact measurement, real-time data capture, and user-friendly interfaces.
Recent events highlight a trend towards strategic collaborations between metrology specialists and automation providers. In early 2025, Carl Zeiss AG announced a partnership with multiple robotics integrators to streamline in-line profilometric inspections for automotive and aerospace manufacturing, reducing cycle times and improving defect detection rates. Similarly, KEYENCE CORPORATION entered into a joint initiative with industrial AI developers to embed machine learning algorithms directly into profilometry systems, enabling predictive maintenance and process optimization.
On the mergers and acquisitions front, 2024 and 2025 have seen continued consolidation. Hexagon AB acquired a boutique profilometry software developer, aiming to bolster its cloud-based metrology solutions. This move reflects a broader industry shift towards offering comprehensive, interoperable platforms that address both hardware and analytical needs.
Collaborative ecosystems are becoming more common, with companies like Renishaw plc participating in cross-industry consortia to establish common data standards and interoperability frameworks, facilitating seamless integration of kinematic profilometry tools into smart factory environments. Such efforts are supported by industry bodies like VDMA, which is driving standardization initiatives across the European manufacturing sector.
Looking ahead, the next few years are expected to bring further convergence of profilometry with robotics, cloud computing, and machine vision. Key players are likely to deepen partnerships with automation firms, software developers, and OEMs, accelerating the deployment of intelligent, networked profilometry solutions. These collaborations will be essential for meeting the rising demand for high-throughput, high-accuracy inspection in sectors such as automotive, aerospace, medical device manufacturing, and precision engineering.
Challenges, Barriers, and Regulatory Considerations
Workpiece kinematic profilometry—an advanced metrological technique for capturing surface topographies and motion profiles during manufacturing—faces several significant challenges and regulatory considerations as the technology matures through 2025 and into the near future.
One of the primary technical barriers is the integration of profilometry systems with high-speed, automated production lines. Many manufacturers demand real-time, in-line inspection capabilities; however, achieving accurate measurements at production speeds without sacrificing precision remains a challenge. Sensor latency, data processing bottlenecks, and vibration sensitivity can introduce errors or require expensive vibration isolation solutions. Major equipment suppliers such as Carl Zeiss AG and KEYENCE CORPORATION are actively developing faster, more robust profilometers and signal processing algorithms to address these issues, but full compatibility with all manufacturing environments is still a work in progress.
Data management and security also pose challenges. Kinematic profilometry generates large volumes of high-resolution, time-stamped surface data that must be stored, processed, and transmitted securely, particularly when integrated with cloud-based manufacturing execution systems (MES). Ensuring interoperability between devices from different manufacturers and maintaining data integrity across the digital thread are ongoing concerns. Organizations such as Hexagon AB are investing in standardized data protocols and encryption practices to facilitate smoother, safer data exchange within smart factories.
Calibration and traceability represent another technical and regulatory hurdle. High-precision profilometry systems must be regularly calibrated to national and international standards to ensure measurement reliability. Regulatory bodies and standards organizations—including the National Institute of Standards and Technology (NIST)—are collaborating with industry stakeholders to update calibration methodologies and certification procedures as new kinematic profilometry modalities emerge.
From a regulatory perspective, there is increasing attention on how profilometric data is used for quality assurance and compliance documentation, especially in tightly regulated sectors such as aerospace and medical devices. Manufacturers must ensure measurement processes conform to relevant standards (e.g., ISO 25178 for surface texture) and provide auditable records for end-to-end traceability. Regulatory scrutiny is expected to intensify as digital manufacturing and automated inspection become more prevalent, requiring companies to maintain sophisticated documentation and risk management practices.
Looking ahead, continued collaboration between equipment manufacturers, standards bodies, and end-users will be critical to overcoming integration, data, and regulatory barriers. The evolution of open standards, secure data architectures, and modular integration frameworks will likely shape the future landscape of workpiece kinematic profilometry.
Future Trends: What’s Next for Kinematic Profilometry?
Workpiece kinematic profilometry is poised for significant transformation in the near future, driven by advancements in sensor technologies, data analytics, and automation. As of 2025, several manufacturers and industry bodies have signaled a shift toward higher-precision, real-time surface characterization, with integration into broader smart manufacturing ecosystems.
A notable trend is the miniaturization and increased robustness of non-contact profilometry sensors, enabling in-line monitoring even in harsh manufacturing environments. Companies like KEYENCE CORPORATION and Carl Zeiss AG continue to release optical profilometers with enhanced speed and resolution, supporting high-throughput industrial applications. These systems leverage confocal, interferometric, and focus variation techniques to deliver real-time, nanometer-scale surface topography data, which is critical for sectors such as automotive, aerospace, and semiconductor manufacturing.
Integration with Industry 4.0 frameworks is accelerating. Profilometry systems are increasingly designed for plug-and-play connectivity with factory automation and quality control networks. For example, Bruker Corporation has developed profilometry solutions that enable direct data transfer to manufacturing execution systems (MES), facilitating adaptive process control and predictive maintenance. This capability is expected to become an industry standard, as manufacturers seek to reduce downtime and improve yield through closed-loop feedback.
Artificial intelligence and machine learning are also shaping the future of kinematic profilometry. Companies such as Zygo Corporation are developing software platforms that automatically classify surface defects, correlate kinematic data with process variables, and identify trends that would be difficult or impossible to discern manually. This trend is expected to intensify over the next few years, with AI-driven analytics offering actionable insights for process optimization and quality assurance.
- Expect increased deployment of multisensor systems that combine profilometry with other modalities (e.g., spectroscopy, 3D scanning) for comprehensive workpiece analysis.
- There is growing industry collaboration on metrology standards and data interoperability, as spearheaded by organizations such as VDMA (German Mechanical Engineering Industry Association) and ISO.
- Portable and handheld profilometry devices are in development for field-based inspections—potentially expanding applications beyond the factory floor.
Looking ahead, workpiece kinematic profilometry is set to become more autonomous, connected, and intelligent, cementing its role as a foundational technology in digital manufacturing and quality assurance over the next several years.