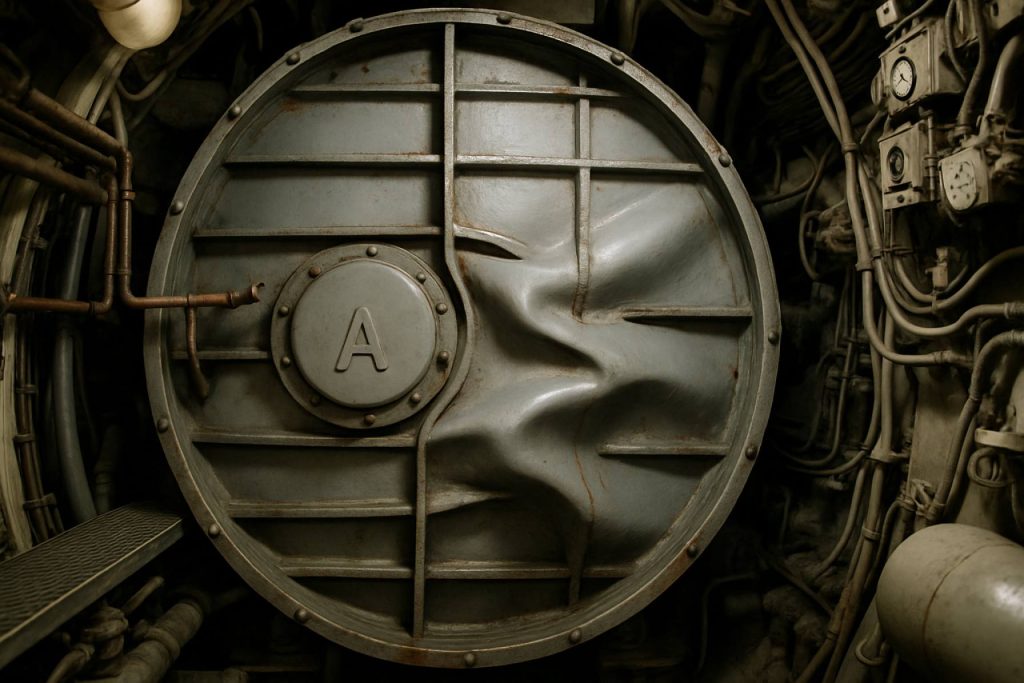
Table of Contents
- Executive Summary and 2025 Outlook
- Market Size and Growth Forecasts Through 2029
- Key Drivers and Challenges in Bulkhead Buckling Analysis
- Latest Advances in Submarine Hull Materials and Engineering
- Emerging Simulation and Modeling Technologies
- Regulatory Standards and Industry Guidelines (e.g., asme.org, ieee.org)
- Major Players and Recent Innovations (e.g., navsea.navy.mil, baeSystems.com)
- Case Studies: Next-Gen Submarines and Real-World Buckling Performance
- Investment Trends and R&D Pipelines for Structural Integrity
- Future Prospects: Predictions for Bulkhead Buckling Analysis and Submarine Safety
- Sources & References
Executive Summary and 2025 Outlook
The structural integrity of submarine bulkheads is a critical aspect of underwater vessel safety and operational readiness, with buckling analysis forming a cornerstone of contemporary naval engineering. As of 2025, advances in computational modeling, materials science, and regulatory standards are shaping the industry’s approach to mitigating the risk of buckling in submarine hull bulkheads. This executive summary provides an overview of key developments and the near-term outlook for bulkhead structural buckling analysis in submarine applications.
In recent years, the adoption of high-fidelity finite element analysis (FEA) tools has enabled more accurate simulation of complex loading conditions, including hydrostatic pressure, dynamic shock, and accidental scenarios. Leading defense contractors and naval engineering firms, such as Naval Group and BAE Systems, have integrated these digital tools into their design cycles, allowing for earlier detection of potential buckling zones and the optimization of reinforcement strategies. The use of advanced steels and composite materials has also gained momentum, providing improved strength-to-weight ratios and enhanced resistance to local and global instabilities.
Regulatory organizations, including Bureau Veritas and Lloyd’s Register, have updated their submarine design and classification rules to reflect current knowledge on buckling phenomena, taking into account both material advances and evolving operational profiles. These standards now demand rigorous verification of bulkhead performance under both design and accidental loads, prompting designers to leverage probabilistic assessment methods and full-scale validation testing.
Looking to 2025 and beyond, the outlook is shaped by increasing demand for multi-mission submarines and the growing complexity of underwater environments. The integration of digital twin technologies—virtual models continuously updated with real-world data—by companies like Saab is expected to enhance predictive maintenance and adaptive structural assessments throughout the vessel’s lifecycle. Furthermore, collaborative research initiatives between shipbuilders and research institutes are poised to drive innovation in buckling mitigation, including smart materials and real-time hull monitoring systems.
In summary, bulkhead structural buckling analysis for submarine hulls is rapidly evolving, driven by technological innovation, stricter regulatory oversight, and the imperative for operational safety. The next few years will likely see greater reliance on simulation, advanced materials, and data-driven approaches to ensure the robustness and survivability of future submarine fleets.
Market Size and Growth Forecasts Through 2029
The market for bulkhead structural buckling analysis in submarine hulls is poised for measured but steady growth through 2029, driven by the modernization of naval fleets, increasing submarine procurement, and the evolution of advanced simulation technologies. As of 2025, leading naval construction nations—including the United States, United Kingdom, France, China, and India—continue to invest significantly in both new submarine platforms and mid-life upgrades, all of which require rigorous structural buckling analyses of pressure bulkheads to ensure safety and survivability under deep-sea pressures.
The demand for specialized structural analysis, including finite element modeling and non-linear buckling simulations, is expected to grow at a compound annual growth rate (CAGR) of approximately 5-7% through 2029. This trend is underpinned by ongoing programs such as the U.S. Navy’s Columbia-class and Virginia-class submarines, both of which rely on advanced digital engineering and computer-aided verification processes for bulkhead integrity assessments (General Dynamics Electric Boat). Similarly, the United Kingdom’s Dreadnought-class and France’s Barracuda-class programs have incorporated increasingly sophisticated buckling analysis methods to optimize hull design and minimize weight without compromising structural resilience (BAE Systems; Naval Group).
On the technology provider side, firms specializing in naval structural engineering and simulation software—such as ANSYS and Siemens—are reporting increased adoption of advanced analysis tools by submarine designers and defense shipyards. These tools facilitate more accurate prediction of critical buckling loads and failure modes, directly supporting the market’s expansion. Additionally, material innovations, such as high-strength steel and composite laminates, are prompting further demand for tailored buckling analyses to validate new hull and bulkhead configurations (Huntington Ingalls Industries).
Looking ahead, growth prospects are reinforced by the rising number of submarine acquisition programs in Asia-Pacific and increased requirements for life extension of existing fleets in Europe and North America. Furthermore, strict classification society standards—such as those set by Lloyd's Register—mandate comprehensive buckling analysis for certification, ensuring sustained market activity through at least 2029.
In summary, the bulkhead structural buckling analysis market segment for submarine hulls will likely maintain a robust growth trajectory, propelled by defense spending, technological innovation, and regulatory demands across major naval shipbuilding nations.
Key Drivers and Challenges in Bulkhead Buckling Analysis
The analysis of bulkhead structural buckling in submarine hulls is increasingly influenced by evolving operational demands, regulatory requirements, and technological advancements. As navies worldwide push for deeper-diving, stealthier, and longer-endurance submarines, the need for precise and reliable buckling analysis of hull bulkheads has become critical. In 2025 and the near future, several key drivers and challenges are shaping this field.
- Stricter Classification Standards: Regulatory bodies such as Lloyd's Register and DNV are continuously updating rules to address new materials, high operational pressures, and safety margins for submarine hulls. Modern standards require rigorous computational and experimental validation of buckling behavior, increasing the complexity of compliance.
- Advanced Materials and Manufacturing: The adoption of high-strength steels and advanced composite materials, as supplied by organizations like thyssenkrupp Steel, demands updated analysis techniques. The anisotropic properties of these materials and the potential for novel failure modes require the use of sophisticated finite element analysis (FEA) tools and real-world testing to ensure structural integrity.
- Digital Design and Simulation: Companies such as BAE Systems and Naval Systems Inc. are investing in high-fidelity digital twins and advanced simulation environments. These enable detailed analysis of local and global buckling phenomena under complex loading scenarios, reducing the risk of unforeseen failures and optimizing bulkhead design for weight and strength.
- Operational Envelope Expansion: The push for deeper operating depths—such as those targeted in the next-generation submarines by Naviris—exposes bulkheads to higher hydrostatic pressures and dynamic loads, increasing the risk of buckling. This necessitates more conservative design factors and real-time structural health monitoring solutions.
- Cost and Time Pressures: The need for faster submarine development cycles and lifecycle cost reduction is driving adoption of rapid prototyping and virtual testing. However, this must be balanced against the risk of underestimating complex buckling phenomena, which remain a leading cause of catastrophic hull failure.
Looking ahead, the convergence of regulatory rigor, advanced materials, and digital engineering will continue to drive innovation in bulkhead buckling analysis. However, the primary challenge remains the accurate prediction of structural behavior under extreme conditions, with ongoing research and industry collaboration essential to meet the demands of next-generation submarine platforms.
Latest Advances in Submarine Hull Materials and Engineering
Recent years have witnessed significant developments in the structural buckling analysis of submarine hull bulkheads, driven by the increasing demand for deeper operational depths, enhanced survivability, and stringent safety standards. The focus has shifted towards optimizing bulkhead geometries and material compositions to prevent catastrophic buckling failures under extreme hydrostatic pressures encountered at depth.
In 2025, leading naval engineering firms and defense agencies are leveraging advanced finite element analysis (FEA) and high-fidelity modeling to predict and mitigate buckling phenomena more accurately than ever before. For instance, General Dynamics Electric Boat and BAE Systems have been incorporating nonlinear buckling simulations into their submarine design processes, enabling them to tailor bulkhead thickness, stiffener spacing, and support configurations to specific mission profiles and depth requirements.
Material innovation is another key driver of progress. The adoption of high-strength, low-alloy steels and advanced composite laminates, as reported by Huntington Ingalls Industries, allows for lighter and more resilient structures without compromising on safety margins. New welding and joining techniques, validated by Naval Sea Systems Command (NAVSEA), are further enhancing the integrity of bulkheads, especially at weld seams which are typical initiation points for buckling under compressive loads.
The application of sensor arrays and real-time structural health monitoring systems is also becoming mainstream. thyssenkrupp Marine Systems has begun outfitting new builds with distributed fiber-optic sensors embedded in bulkheads, providing continuous data on strain and deformation. This enables predictive maintenance and rapid response to critical load events, reducing the likelihood of undetected buckling damage during extended deployments.
Looking ahead, the industry is expected to further integrate digital twin technologies, as being piloted by Rolls-Royce in their naval product lines, for holistic lifecycle management and failure prediction of submarine hull structures. Regulatory bodies such as Lloyd's Register are anticipated to update their classification rules to reflect these technological advancements, setting new benchmarks for buckling resistance and structural reliability in submarine hulls through 2025 and beyond.
Emerging Simulation and Modeling Technologies
The ongoing evolution of simulation and modeling technologies is fundamentally transforming the approach to bulkhead structural buckling analysis in submarine hulls. As of 2025, the integration of high-fidelity computational tools and digital twin frameworks is enabling naval architects and engineers to predict failure modes with greater accuracy and efficiency. Advanced finite element analysis (FEA) platforms, such as those offered by ANSYS and Siemens, are now routinely used to simulate complex loading scenarios, including non-linear buckling phenomena influenced by material anisotropy, weld imperfections, and real-world operational conditions.
A notable trend in 2025 is the increased adoption of multi-physics simulations that couple structural, hydrodynamic, and thermal effects. Recent collaborations between submarine manufacturers and software providers have resulted in the implementation of these integrated approaches for critical components such as bulkheads, which are subjected to highly variable pressure differentials and dynamic impacts. For example, Naval Sea Systems Command (NAVSEA) has reported the use of digital engineering and simulation-driven design to support the rapid prototyping and qualification of new hull structures, emphasizing the early identification of buckling risks and design optimization under life-cycle loading profiles.
Additionally, machine learning algorithms are being introduced to enhance predictive accuracy by analyzing large datasets generated from both simulated and experimental buckling tests. This data-driven methodology, supported by partnerships with leaders in materials science and submarine construction such as BAE Systems and HII Newport News Shipbuilding, enables the real-time refinement of simulation models and the identification of previously unrecognized failure precursors. As a result, the industry anticipates both improved safety margins and reduced development cycles.
Looking forward, the next few years are expected to see further integration of cloud-based simulation platforms, facilitating collaborative design and remote verification of buckling resistance for submarine bulkheads. Initiatives such as the Naval Group digital transformation program are likely to accelerate the deployment of these technologies, making advanced buckling analysis more accessible across international submarine programs. This progress is set to deliver not only more robust hull designs but also significant cost and time savings throughout the submarine construction lifecycle.
Regulatory Standards and Industry Guidelines (e.g., asme.org, ieee.org)
The regulatory landscape governing bulkhead structural buckling analysis for submarine hulls is evolving in response to advances in materials science, computational modeling, and the push for deeper-diving, higher-performance underwater vessels. As of 2025, the dominant standards for submarine hull and bulkhead design are primarily set by organizations such as the American Society of Mechanical Engineers (ASME) and the American Bureau of Shipping (ABS), with additional guidelines from international bodies like the Det Norske Veritas (DNV).
ASME’s Boiler and Pressure Vessel Code (BPVC) Section VIII, while originally designed for surface pressure vessels, continues to influence submarine hull and bulkhead criteria through its provisions on buckling under external pressure and material performance at depth. The 2025 edition is expected to integrate feedback from recent subsea projects and research, with an emphasis on finite element analysis (FEA) validation for non-standard hull geometries and advanced alloys. Additionally, ASME’s ongoing collaboration with the U.S. Navy is likely to produce updates addressing modern high-yield steels and composite structures used in military and research submersibles.
The ABS Rules for Building and Classing Underwater Vehicles, Systems and Hyperbaric Facilities, revised in 2024, now explicitly require advanced buckling analysis for all major bulkheads. This includes mandatory non-linear FEA and probabilistic approaches to account for variability in material properties and manufacturing tolerances, reflecting lessons learned from recent deep-diving vehicle incidents and prototype testing (ABS Group). Meanwhile, DNV’s “Rules for Classification of Naval Submarines” (2025 edition) emphasizes lifecycle integrity management, mandating periodic reassessment of buckling margins as part of in-service inspection protocols (DNV).
On the international front, the International Maritime Organization (IMO) continues its work on harmonizing safety codes for underwater craft, with technical subcommittees in 2025 focusing specifically on hull buckling safety factors and the adoption of digital twin technologies for real-time structural health monitoring.
Looking ahead, industry guidelines are expected to increasingly require validation of design models with full-scale or sub-scale physical testing, and to incorporate AI-enhanced simulations for uncertainty quantification in buckling assessments. These developments underscore a shift toward risk-informed, performance-based standards, ensuring that submarine bulkheads not only meet minimum safety requirements but are also resilient to unforeseen operational scenarios.
Major Players and Recent Innovations (e.g., navsea.navy.mil, baeSystems.com)
In 2025, the analysis of bulkhead structural buckling in submarine hulls continues to be a focal point for leading naval defense contractors and research organizations. Recent years have seen significant investments in computational modeling, advanced materials, and testing protocols to ensure the integrity of submarine structures under extreme pressure conditions.
A principal driver of innovation is the Naval Sea Systems Command (NAVSEA), which maintains rigorous standards for submarine hull integrity and oversees the implementation of state-of-the-art buckling analysis methodologies. NAVSEA’s ongoing initiatives include the refinement of finite element analysis (FEA) models to simulate both global and local buckling phenomena in bulkheads, with validation from full-scale pressure hull trials. In 2024 and 2025, NAVSEA has prioritized digital twin technologies, integrating real-time sensor data from in-service submarines to calibrate and improve predictive buckling models.
Among defense contractors, BAE Systems has made notable advancements in the use of high-strength, low-alloy steels and composite reinforcements for submarine bulkheads. Their recent work, as part of the UK’s Dreadnought-class program, has included the deployment of laser ultrasonic testing and acoustic emission monitoring during pressure testing, offering unprecedented insight into precursors to buckling events. These techniques are expected to be fully integrated into operational procedures by mid-2025.
Another major player, HII (Huntington Ingalls Industries), responsible for the construction of the Virginia-class and Columbia-class submarines, continues to refine their buckling analysis workflow. HII employs advanced multi-physics simulation platforms, enabling engineers to assess the interaction between mechanical loads, temperature effects, and material aging on bulkhead stability. In 2024, HII reported successful application of these tools in reducing the weight of internal bulkheads without compromising safety margins, directly contributing to improved payload capacity and fuel efficiency.
Looking ahead, collaborations between industry and academia—often facilitated by organizations such as American Society of Naval Engineers (ASNE)—are expected to accelerate the adoption of machine learning for anomaly detection and enhanced predictive analytics in structural health monitoring. With the growing complexity of submarine missions and the push for extended service lives, the outlook for bulkhead buckling analysis is one of continual evolution, increasingly reliant on digital tools, new materials, and real-world data feedback to ensure the highest standards of underwater vessel safety and performance.
Case Studies: Next-Gen Submarines and Real-World Buckling Performance
In the rapidly evolving field of submarine design, the structural buckling performance of bulkheads remains a critical determinant of overall hull integrity and survivability under deep-sea pressures. Recent years have seen a surge in case studies focusing on next-generation submarines that employ advanced analysis methods and innovative materials to address buckling challenges. As new classes of military and scientific submarines are introduced, real-world data from sea trials and full-scale testing are informing best practices and setting new benchmarks for bulkhead performance.
A prominent example can be observed in the development of the U.S. Navy’s Columbia-class ballistic missile submarines, where extensive finite element modeling and physical testing have been conducted to ensure resistance against local and global buckling modes. The General Dynamics Electric Boat shipyard has implemented nonlinear buckling analyses on critical bulkheads, incorporating lessons learned from previous Ohio-class vessels. These analyses are validated with strain gauge data collected during pressure hull trials, which have consistently confirmed the conservative safety margins predicted by simulation.
Similarly, the United Kingdom’s Dreadnought-class program leverages digital twin technology to monitor the structural health of bulkheads in real time. By integrating data from distributed sensor networks, BAE Systems engineers can detect the onset of buckling far earlier than with traditional inspection regimes. This proactive approach allows for rapid intervention and provides valuable real-world feedback to refine predictive models for future designs.
On the commercial front, research institutions and builders such as Thyssenkrupp Marine Systems are collaborating with classification societies to certify new hull forms that utilize high-strength, low-alloy steels and composite reinforcements. Recent trials with the Type 212CD submarine have included deliberately overstressing test sections to capture buckling signatures—data that is then used to update design codes and enhance simulation accuracy.
Looking forward, the next few years will see the integration of machine learning algorithms with traditional buckling analyses, enabling predictive maintenance and adaptive design optimization. International partnerships, such as the trilateral AUKUS agreement, are expected to accelerate knowledge transfer and standardization of best practices across allied submarine fleets. As digital tools mature and more operational data becomes available, the industry is poised for significant advances in both the prevention and detection of bulkhead buckling, ensuring the safety and mission readiness of submarines operating in the world’s deepest waters.
Investment Trends and R&D Pipelines for Structural Integrity
In 2025, investment and research and development (R&D) pipelines for bulkhead structural buckling analysis in submarine hulls are experiencing notable expansion, driven by both defense modernization initiatives and the rise of advanced materials and simulation capabilities. Naval shipbuilders and defense agencies are increasingly prioritizing the structural integrity of submarine hulls, with a specific focus on the buckling resistance of bulkheads, which are critical for maintaining compartmentalization and survivability under high hydrostatic pressures.
Significant investments are being channeled into computational modeling and experimental validation techniques. For instance, BAE Systems and Naval Sea Systems Command are actively collaborating on projects aimed at refining finite element analysis (FEA) models that predict local and global buckling phenomena in complex bulkhead geometries. These collaborations are leveraging high-performance computing to simulate extreme pressure scenarios and validate results through scaled physical testing, narrowing the gap between theoretical predictions and real-world performance.
Material advancements are another focus area; the adoption of high-strength duplex steels and composite reinforcements is being explored to enhance buckling resistance without incurring significant weight penalties. thyssenkrupp Marine Systems continues to invest in R&D for weldable, high-strength steels with improved ductility, specifically tailored for submarine applications where bulkhead stability is paramount.
Government funding and public-private partnerships are also fueling innovation. The Office of Naval Research has announced multi-year grant programs targeting the development of predictive buckling models and the integration of real-time structural health monitoring (SHM) systems into new submarine designs. These SHM systems, utilizing fiber-optic sensors and acoustic emission monitoring, are in pilot deployment phases, enabling early detection of stress concentrations and potential buckling events on operational vessels.
Looking ahead, the outlook for 2025 and the subsequent years suggests a continued increase in both capital and intellectual investment in this sector. With next-generation submarines—such as the UK’s Dreadnought class and the US Columbia class—relying on enhanced bulkhead designs, stakeholders are expected to maintain high R&D spend on both simulation technologies and advanced materials. These investments are anticipated to result in safer, more resilient submarine hulls capable of withstanding deeper dives and prolonged missions, reinforcing the strategic value of cutting-edge buckling analysis in naval architecture.
Future Prospects: Predictions for Bulkhead Buckling Analysis and Submarine Safety
As the strategic and operational demands on submarines continue to intensify through 2025 and beyond, the future of bulkhead structural buckling analysis is set to experience significant advancements. Bulkheads, which play a critical role in maintaining watertight integrity and resisting collapse under extreme pressure, are the focus of both defense and commercial naval architects seeking enhanced safety and efficiency.
In the near term, the integration of digital twin technology and advanced finite element modeling is expected to become standard practice. Leading submarine manufacturers such as Naval Group and BAE Systems are investing in computational tools that can simulate real-time stress distribution and predict buckling phenomena under various operational scenarios. These tools leverage high-performance computing, enabling rapid design iterations and validation against both simulated and real-world data.
Materials science is another domain poised for transformation. The adoption of new high-strength, corrosion-resistant alloys and composite structures is anticipated to improve bulkhead performance, particularly under cyclic loading and extreme depths. Companies like HII (Huntington Ingalls Industries) are exploring novel fabrication methods, including additive manufacturing, to optimize the geometry and structural resilience of submarine bulkheads while reducing weight and material waste.
Standardization bodies and naval authorities, such as United States Navy and DNV, are expected to update guidelines and certification procedures in light of these technological advancements. The incorporation of probabilistic buckling analysis methods into design codes is anticipated, enabling more accurate risk assessment and lifecycle management for next-generation submarine fleets.
Looking ahead, the coupling of artificial intelligence (AI) with sensor data from in-service submarines will further enhance bulkhead safety. Real-time monitoring of stress, strain, and micro-cracking will allow for predictive maintenance, mitigating the risk of catastrophic failure due to buckling. The push toward autonomous or remotely operated underwater vehicles (ROVs) will also drive innovation in compact and robust bulkhead architectures, with manufacturers like Saab actively developing such systems.
Overall, the next few years are set to witness a convergence of simulation, advanced materials, and digital monitoring, resulting in safer, more efficient, and longer-lasting submarine hull bulkheads. These trends will not only bolster naval capabilities but also set new benchmarks for underwater vehicle safety worldwide.