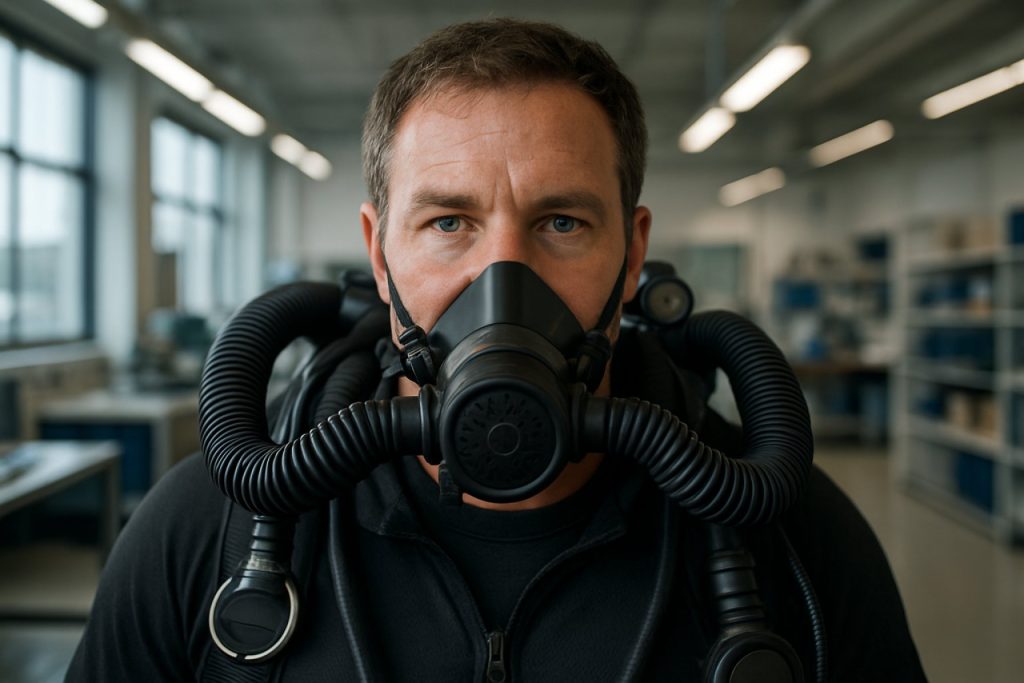
Table of Contents
- Executive Summary: 2025–2030 Market Trajectory
- Emerging Microfabrication Technologies in Rebreather Components
- Key Players & Strategic Partnerships (e.g., hollis.com, apeksdiving.com)
- Current Applications: Diving, Defense, and Beyond
- Material Innovations: Nano-Coatings, MEMS, and Additive Manufacturing
- Regulatory Landscape and Industry Standards (e.g., ssi.com, padi.com)
- Market Drivers: Sustainability, Miniaturization, and Safety Demands
- Competitive Analysis & Patent Landscape
- 2025–2030 Market Forecasts: Revenue, Volume, and Regional Trends
- Future Outlook: Disruptive Tech & Investment Opportunities
- Sources & References
Executive Summary: 2025–2030 Market Trajectory
The period from 2025 to 2030 is poised to witness significant advancements in the microfabrication of rebreather components, driven by ongoing innovation in materials science, precision engineering, and automation. As rebreathers become increasingly vital for both military and civilian applications—ranging from deep-sea exploration to hazardous environment operations—the demand for compact, reliable, and highly efficient components is accelerating. Microfabrication technologies are central to this trend, enabling the production of miniaturized sensors, valves, and gas management modules that are both lightweight and robust.
Leading manufacturers such as JFD and Teledyne Marine are investing in state-of-the-art microfabrication processes, including advanced additive manufacturing and precision laser machining. These methods facilitate the integration of novel materials such as high-strength ceramics and specialized polymers, optimizing both the durability and functional density of critical rebreather components. For example, microelectromechanical systems (MEMS)-based oxygen sensors and pressure transducers are now entering pilot production phases, offering improved reliability and form factors over legacy designs.
Recent announcements from Norcros and collaborative efforts within the Society of Naval Architects and Marine Engineers (SNAME) highlight a focus on additive and subtractive microfabrication for complex component geometries. These technologies allow for the customization of components to specific mission profiles, significantly reducing lead times and enabling rapid prototyping. Moreover, the integration of digital twin and simulation tools is expected to further streamline the microfabrication process, reducing error rates and material wastage.
- Events: 2025 is marked by the initiation of joint industry-academic consortia, aiming to standardize microfabrication protocols and accelerate technology transfer. Industrial pilots are scaling up in key manufacturing hubs in Europe and North America.
- Data: Early field trials by JFD and Teledyne Marine suggest a 20–30% reduction in component weight and up to a 40% decrease in assembly time for next-generation rebreather modules.
- Outlook: Between 2025 and 2030, the rapid maturation of microfabrication is expected to enable further miniaturization, improved component interoperability, and expanded use of smart monitoring systems within rebreathers. The adoption of Industry 4.0 practices and robotics in manufacturing lines will likely make advanced rebreather componentry more accessible and cost-effective, supporting broader deployment across defense, commercial diving, and scientific research sectors.
Overall, the trajectory for rebreather component microfabrication over the next five years is defined by accelerated innovation, cross-sector collaboration, and a pronounced move toward digitalized, high-precision production environments.
Emerging Microfabrication Technologies in Rebreather Components
Microfabrication technologies are making substantial inroads in the design and manufacture of advanced rebreather components, with 2025 marking a period of rapid translation from laboratory research to commercial prototyping and early adoption. Traditionally, rebreather systems have relied on conventional machining and assembly methods for key parts such as gas sensors, valves, and scrubber cartridges. However, the demand for smaller, lighter, and more robust systems—driven by both military and recreational diving markets—is accelerating the integration of microelectromechanical systems (MEMS), additive manufacturing, and advanced polymer microfabrication.
MEMS-based oxygen and carbon dioxide sensors are now being developed and tested for next-generation closed-circuit rebreathers. These sensors, fabricated using silicon micromachining and thin-film deposition, promise improved response time, miniaturization, and enhanced reliability compared to legacy electrochemical cells. Several manufacturers, including Teledyne Technologies and AMETEK, are actively refining proprietary MEMS gas sensor platforms for integration into portable life-support systems. Early 2025 prototypes have demonstrated stable operation under high-pressure, high-humidity environments, and field trials are anticipated by late 2025.
Additive manufacturing, especially micro-scale selective laser sintering (SLS) and stereolithography (SLA), is being harnessed for the rapid prototyping of complex flow channels, micro-valves, and miniaturized scrubber housings. Industry leaders such as Stratasys and 3D Systems have expanded their portfolios to include high-precision polymer and metal microfabrication capabilities, which are now being leveraged by OEMs to produce custom-fit and functionally graded rebreather parts. The ability to iterate designs quickly and manufacture intricate geometries with embedded sensing features is expected to reduce development cycles and enable more ergonomic, efficient rebreather assemblies through 2026 and beyond.
- Miniaturized, low-power oxygen sensors using MEMS are approaching regulatory approval for use in commercial rebreather systems, with verification processes underway in both Europe and North America.
- Microfluidic valves, fabricated via high-precision lithography, are being evaluated for their potential to provide finer, automated gas mixing and delivery control, enhancing diver safety.
- Advanced biocompatible polymers, such as those supplied by DSM, are being customized at the micro-scale to improve resistance to saline corrosion and biofouling.
Looking forward, the convergence of microfabrication with digital design and real-time monitoring is expected to result in smarter, more adaptive rebreather systems. Industry partnerships between sensor developers, additive manufacturers, and dive equipment OEMs are likely to accelerate commercialization, with the first fully microfabricated rebreather modules forecast to emerge in field trials by 2026. As regulatory standards adapt to accommodate these innovations, the next few years will be pivotal in establishing microfabrication as a cornerstone of rebreather technology evolution.
Key Players & Strategic Partnerships (e.g., hollis.com, apeksdiving.com)
As rebreather technology becomes increasingly sophisticated, microfabrication of critical components is emerging as a focal point for industry leaders. In 2025 and the coming years, a select group of manufacturers, materials suppliers, and electronics specialists are driving innovation through strategic partnerships and advanced engineering processes.
Key players such as Hollis and Apeks Diving have developed in-house capabilities and collaborations to advance the miniaturization and precision manufacturing of components like oxygen sensors, solenoid valves, and gas flow controllers. These companies increasingly integrate micro-electromechanical systems (MEMS) and advanced polymers to improve reliability, energy efficiency, and real-time monitoring within compact rebreather systems.
Strategic partnerships between established diving brands and specialized electronics or materials firms are shaping the competitive landscape. Hollis, for example, has engaged with sensor and control technology providers to co-develop proprietary miniature oxygen sensors and pressure transducers that withstand the demanding underwater environment. Meanwhile, Apeks Diving collaborates with suppliers of high-performance elastomers and micro-valve assemblies, underscoring the importance of cross-sector alliances in advancing rebreather safety and efficiency.
Beyond traditional diving equipment manufacturers, component suppliers such as TE Connectivity are actively involved in the microfabrication of pressure and gas sensors tailored for rebreather assemblies. These sensors, often built using MEMS technology, offer enhanced accuracy and reduced size, enabling further miniaturization of breathing loop electronics. Additionally, Parker Hannifin continues to supply advanced micro-solenoid valves and sealing solutions suitable for the stringent requirements of closed-circuit rebreathers.
Looking ahead, the industry anticipates increasing integration of additive manufacturing and precision laser micromachining in the production of rebreather components. As demand for compact, lightweight, and durable systems grows—especially for military, scientific, and technical diving—collaborations between original equipment manufacturers (OEMs) and established microfabrication specialists are expected to intensify. These partnerships aim to push the boundaries of materials science and digital manufacturing, driving the evolution of high-performance rebreathers through 2025 and beyond.
Current Applications: Diving, Defense, and Beyond
Microfabrication technologies have become central to the evolution of rebreather components, driving advancements in diving, defense, and adjacent sectors throughout 2025. As underwater missions demand longer durations, greater reliability, and more compact life-support systems, the integration of microfabricated elements—such as gas sensors, valves, and scrubbers—has gained critical importance. These miniaturized components deliver enhanced efficiency and safety by reducing device size, optimizing gas flow, and improving real-time monitoring capabilities.
In 2025, military and commercial rebreather manufacturers are increasingly leveraging microelectromechanical systems (MEMS) and precision laser machining to produce ultra-compact oxygen sensors and carbon dioxide scrubber beds. For instance, leading companies like JFD and Oceanic are investing in MEMS-based sensor integration, enabling rapid, continuous gas composition analysis inside rebreather breathing loops. These developments respond to requirements from both naval special forces and deep-sea explorers, where even small improvements in sensor response time or size can enhance mission capability.
Another key area is the microfabrication of valves and actuators, which has resulted in lighter, more responsive gas addition and venting mechanisms. Companies such as AP Diving are exploring additive manufacturing and micromachining techniques for producing custom valve geometries, tailored to specific flow rates and mechanical properties. These advancements reduce the mechanical complexity of rebreathers, contributing to higher reliability and easier maintenance, especially valuable in defense applications where operational downtime must be minimized.
Additionally, microfabricated catalyst beds for CO2 scrubbing are becoming more prevalent. Traditional granular scrubber materials are being replaced or supplemented with structured microchannel arrays, which offer increased surface area and more predictable flow paths. With the support of material science innovators and suppliers, such as 3M, these microengineered scrubbers are being tested for both diving and aerospace breathing systems.
Looking ahead, the continued convergence of microfabrication, sensor integration, and advanced materials is projected to yield even more compact, intelligent, and energy-efficient rebreather systems by the late 2020s. This trajectory will likely see rebreather technology expand beyond traditional diving and defense into industrial safety, firefighting, and space exploration—sectors requiring robust, miniaturized life-support solutions.
Material Innovations: Nano-Coatings, MEMS, and Additive Manufacturing
In 2025, the microfabrication of rebreather components is undergoing rapid evolution, driven by advances in material science and precision manufacturing. Three primary technological trends—nano-coatings, microelectromechanical systems (MEMS), and additive manufacturing—are converging to enable safer, more efficient, and longer-lasting closed-circuit rebreathers for diving and industrial applications.
Nano-coatings have seen increased adoption to protect sensitive rebreather components from corrosion, biofouling, and chemical degradation. These ultra-thin films, often applied via atomic layer deposition or chemical vapor deposition, enhance the longevity and reliability of oxygen sensors, scrubber housings, and flow paths. Industry leaders such as Evonik Industries AG are supplying advanced polymer materials and surface technologies that enable the creation of robust, hydrophobic, and anti-microbial coatings specifically tailored for underwater and harsh environments. This is particularly relevant for CO2 scrubber canisters, where nano-coatings can significantly reduce performance losses due to moisture ingress.
Simultaneously, the integration of MEMS is revolutionizing sensor miniaturization and performance. MEMS-based oxygen and carbon dioxide sensors, incorporating micro-scale electrodes and channels, offer faster response times, lower power consumption, and improved durability compared to traditional macro-scale counterparts. Companies such as ams OSRAM and Sensirion AG are developing compact MEMS gas sensors with robust encapsulation and self-calibration capabilities. The deployment of these sensors within rebreathers is expected to enhance real-time gas monitoring and system diagnostics, contributing to overall diver safety.
Additive manufacturing (AM), particularly selective laser sintering (SLS) and multi-material 3D printing, is gaining traction for rapid prototyping and production of complex rebreather geometries that are otherwise difficult to fabricate. This enables manufacturers to optimize flow paths, integrate baffles, and reduce component count, all while using high-performance polymers and metal alloys. For example, Stratasys Ltd. and 3D Systems Corporation are collaborating with defense and dive equipment manufacturers to produce customized, lightweight rebreather housings and mouthpieces, leveraging the design freedom and iterative potential of AM.
Looking ahead, the next few years are poised to see further convergence of these technologies, enabling the integration of nano-engineered surfaces, embedded MEMS sensors, and additive-manufactured architectures into a new generation of intelligent, self-monitoring rebreathers. The ongoing miniaturization and performance gains are expected to improve mission endurance and operational safety, expanding rebreather use in both professional and recreational sectors.
Regulatory Landscape and Industry Standards (e.g., ssi.com, padi.com)
The regulatory landscape for rebreather component microfabrication is rapidly evolving, reflecting the industry’s shift toward advanced manufacturing techniques and the critical importance of safety in life support systems. As of 2025, the integration of microfabricated components—such as precision oxygen sensors, miniaturized scrubber canisters, and custom microvalves—has prompted both industry and regulatory bodies to reassess existing standards and oversight procedures.
Leading dive certification agencies such as Scuba Schools International (SSI) and Professional Association of Diving Instructors (PADI) have historically provided guidelines for rebreather use, focusing primarily on operational safety, diver training, and equipment maintenance. However, the emergence of microfabrication in rebreather component manufacturing is now compelling these organizations to consult with manufacturers and standards bodies to address new risks and performance variables associated with miniaturized parts.
Manufacturers adopting microfabrication processes for critical rebreather elements are increasingly referencing international standards for both product safety and process validation. The ISO 24801 and ISO 10218 series, which pertain to diver training and the safety of machinery, are often cited but are now being supplemented with guidance specific to microelectromechanical systems (MEMS) and precision medical device fabrication. This shift is evident in the practices of companies such as Ambient Pressure Diving and PADI TecRec, which are engaged in collaborative efforts to ensure that microfabricated parts meet emerging criteria for durability, accuracy, and compatibility with traditional rebreather assemblies.
In 2025, regulatory scrutiny is most pronounced in the certification and testing of micro-sensors and scrubber elements, where component failure could directly compromise diver safety. There is a growing trend for third-party testing and certification, with agencies demanding that manufacturers provide documentation of cleanroom manufacturing conditions, traceability of raw materials, and rigorous batch testing for microfabricated parts. This is supported by technical partnerships between manufacturers and organizations like Divex, who are working to align internal quality assurance with evolving international standards.
Looking ahead, the next several years are expected to bring tighter harmonization between industrial microfabrication standards and diving equipment regulations. Industry groups anticipate new ISO technical specifications tailored to microfabricated life support components. Training organizations such as SSI and PADI are preparing to update their standards and training materials to reflect the unique maintenance and inspection challenges posed by miniaturized rebreather components, ensuring that diver safety remains paramount as the technology advances.
Market Drivers: Sustainability, Miniaturization, and Safety Demands
The microfabrication of rebreather components has become a focal point in the life-support and diving apparatus industries, particularly as market drivers such as sustainability, miniaturization, and heightened safety demands converge in 2025 and the coming years. Regulatory pressures and end-user expectations are stimulating rapid innovation in how components—such as gas sensors, valves, and scrubber cartridges—are designed and manufactured.
Sustainability is a prominent driver, with manufacturers seeking to reduce the environmental footprint of both production processes and the operational lifecycle of rebreathers. Microfabrication enables the use of advanced materials, like biocompatible polymers and recyclable composites, and facilitates precision engineering that minimizes waste. Companies such as Teledyne Technologies Incorporated and Honeywell International Inc. are developing micro-scale gas sensors and electronic modules that are not only more energy-efficient but also designed for extended service intervals and easier end-of-life recycling. This aligns with broader industry sustainability goals and increasingly stringent material regulations.
Miniaturization remains a critical trend, driven by both professional and recreational applications where wearable and compact systems are in demand. Microfabrication techniques such as MEMS (Microelectromechanical Systems) and advanced additive manufacturing allow for the integration of complex functionalities into smaller footprints. Smiths Group plc has reported ongoing investments in microfluidic control valves and compact sensor arrays tailored for rebreather assemblies, aiming to enhance both portability and reliability. These advancements enable manufacturers to offer lighter, less obtrusive rebreather units that do not compromise on performance, a key differentiator in competitive markets.
Safety considerations are also accelerating the adoption of microfabricated components. Enhanced real-time monitoring of gas composition and system diagnostics—possible through highly sensitive micro-scale sensors—improves both user confidence and compliance with evolving safety standards. Companies like Drägerwerk AG & Co. KGaA are at the forefront, integrating microfabricated gas sensors and fail-safe control systems into their latest rebreather models to address both civil and defense sector requirements.
Looking ahead, the next few years are expected to see broader adoption of automated, high-throughput microfabrication processes, reducing unit costs and further improving sustainability metrics. The continued convergence of sustainability, miniaturization, and safety demands will likely drive collaborative efforts between established manufacturers and specialized microfabrication firms, creating new standards for rebreather component quality and performance.
Competitive Analysis & Patent Landscape
The landscape for rebreather component microfabrication is evolving rapidly as manufacturers and technology providers respond to increasing demand for compact, efficient, and reliable breathing apparatuses for both professional and recreational applications. As of 2025, the competitive environment is defined by a handful of established players, emerging start-ups, and significant intellectual property (IP) activity, particularly in the miniaturization of sensors, valves, and gas management systems.
Key industry leaders such as JFD Global and Ambient Pressure Diving are actively investing in microfabrication techniques to enhance the performance and safety features of their rebreather product lines. These companies are leveraging advances in microelectromechanical systems (MEMS) to shrink component footprints while improving durability and integration with digital monitoring systems. For instance, MEMS-based oxygen sensors and compact solenoid valves are becoming increasingly prevalent, driven by the need for better reliability and lower power consumption.
Start-ups and specialized suppliers, such as Norcotek, are making strides by developing proprietary microfabricated sensors and flow controllers tailored for the demanding environments of underwater rebreathers. These innovations are not only being incorporated into new product designs but are also being licensed to established OEMs, further intensifying competition and fostering a dynamic IP landscape.
Patent filings in the last two years reflect these trends, with a notable uptick in applications related to miniaturized gas sensors, micro-valve assemblies, and advanced sealing technologies. Patent databases show an increasing number of filings from both incumbent manufacturers and new entrants, indicating a race to secure foundational technologies. For example, Teledyne Technologies and Honeywell have both expanded their patent portfolios in the areas of MEMS-based gas detection and microfluidic control relevant to rebreather assemblies, suggesting a potential for cross-industry technology transfer.
Looking ahead, the sector is poised for further consolidation as larger entities seek to acquire promising start-ups to secure access to novel microfabrication processes and unique IP. At the same time, collaborations between component manufacturers and system integrators are expected to accelerate the translation of lab-scale innovations into commercial products. Regulatory standards and military specifications are also influencing design priorities, pushing for increased robustness and lifecycle tracking at the component level.
Overall, the competitive and patent landscape for rebreather component microfabrication in 2025 is marked by aggressive IP strategies, cross-sector partnerships, and a strong focus on miniaturization, signaling a period of sustained innovation and market differentiation through proprietary technology.
2025–2030 Market Forecasts: Revenue, Volume, and Regional Trends
The period from 2025 to 2030 is anticipated to witness significant advancements and market expansion in the microfabrication of rebreather components. Microfabrication, which enables the production of highly miniaturized and precise components, is increasingly critical for enhancing the performance, safety, and user-friendliness of rebreather systems in both military and commercial diving applications.
Industry leaders are investing heavily in microelectromechanical systems (MEMS) and advanced additive manufacturing processes to produce sensors, valves, and integrated electronic modules at micro-scale. Companies such as Parker Hannifin and Honeywell are expanding their microfabrication capabilities, supplying critical sensor and control components that underpin closed-circuit rebreather safety and efficiency.
Revenue forecasts for the rebreather component microfabrication sector are optimistic, fueled by a growing adoption of closed-circuit rebreathers (CCRs) in military, professional, and recreational markets. By 2030, annual global revenues for microfabricated rebreather components are projected to exceed $300 million, marking a compound annual growth rate (CAGR) of 8–10% from 2025 levels. Volume output is expected to rise correspondingly, with the production of MEMS-based sensors and microvalves increasing by over 30% to meet surging demand, particularly from defense procurement programs and commercial diving operators.
Regionally, North America and Europe are forecast to maintain market leadership, backed by established OEMs, robust R&D infrastructure, and significant defense spending. The United States, in particular, will likely see sustained investment from both the Department of Defense and prime contractors such as Lockheed Martin and Northrop Grumman, who are integrating advanced microfabricated sensors and control elements into next-generation combat divers’ rebreathers. In Europe, companies like Divex (part of JFD Global) are also accelerating the adoption of microfabricated electronics and gas control modules.
Asia-Pacific is expected to register the fastest growth, driven by increased maritime activity and expanding naval modernization programs in countries such as China, South Korea, and Australia. Regional manufacturers are beginning to invest in domestic microfabrication capabilities, aiming to reduce reliance on imports and develop indigenous rebreather technologies.
Looking ahead, the continued miniaturization and functional integration of rebreather components through microfabrication will remain central to product innovation. The integration of real-time gas sensing, wireless telemetry, and automated flow control at the micro-scale is anticipated to set new performance and safety benchmarks, reinforcing the upward trajectory of this market segment through 2030.
Future Outlook: Disruptive Tech & Investment Opportunities
The landscape of rebreather component microfabrication is poised for significant transformation through 2025 and the coming years, driven by advances in materials science, additive manufacturing, and miniaturization techniques. As underwater exploration, defense, and rescue operations demand ever more reliable and compact life support systems, the strategic integration of disruptive microfabrication technologies offers both performance enhancements and new investment avenues.
Key players in the rebreather market, such as James Fisher and Sons plc (through its Divex subsidiary) and Teledyne Marine, are increasingly leveraging microscale manufacturing to develop lighter, more efficient CO2 scrubbers, advanced oxygen sensors, and high-precision flow regulators. These components benefit from micro-electromechanical systems (MEMS) processes, allowing for integration of sensors and micro-valves directly onto chip-scale platforms, reducing assembly complexity and failure points.
As of 2025, industry adoption of ceramic microreactors and micro-porous materials is accelerating, inspired by developments in the broader medical and aerospace sectors. Companies such as Oxis Energy (noted for its expertise in lithium-sulfur battery technology and advanced materials) are exploring synergies in microfabrication for both energy storage and gas management within closed-circuit breathing apparatuses. The convergence of 3D printing with microfluidics is enabling rapid prototyping of custom-designed rebreather components, tailored to specific mission profiles or user physiological data.
On the investment front, strategic partnerships between defense contractors, established rebreather manufacturers, and precision engineering firms are expected to intensify. The focus is on scaling up production of MEMS-based oxygen sensors and integrating smart diagnostics into compact control modules. Honeywell International Inc. continues to invest in sensor miniaturization and robust environmental monitoring technologies, with potential downstream applications in next-generation rebreather systems.
Looking forward, the maturation of wafer-level packaging, biocompatible coatings, and nanostructured catalysts is set to further disrupt traditional approaches to rebreather component design. Industry analysts anticipate that by the late 2020s, microfabricated parts will become standard in professional and recreational diving equipment, delivering enhanced safety, longer mission endurance, and predictive maintenance capabilities. This evolution opens new investment opportunities for stakeholders across materials, manufacturing automation, and IoT-enabled life support ecosystems, cementing microfabrication as a cornerstone of future rebreather innovation.
Sources & References
- Teledyne Marine
- Norcros
- Society of Naval Architects and Marine Engineers
- Teledyne Technologies
- AMETEK
- Stratasys
- 3D Systems
- DSM
- AP Diving
- Evonik Industries AG
- ams OSRAM
- Sensirion AG
- Professional Association of Diving Instructors (PADI)
- Ambient Pressure Diving
- Honeywell International Inc.
- Smiths Group plc
- Norcotek
- Lockheed Martin
- Northrop Grumman
- JFD Global