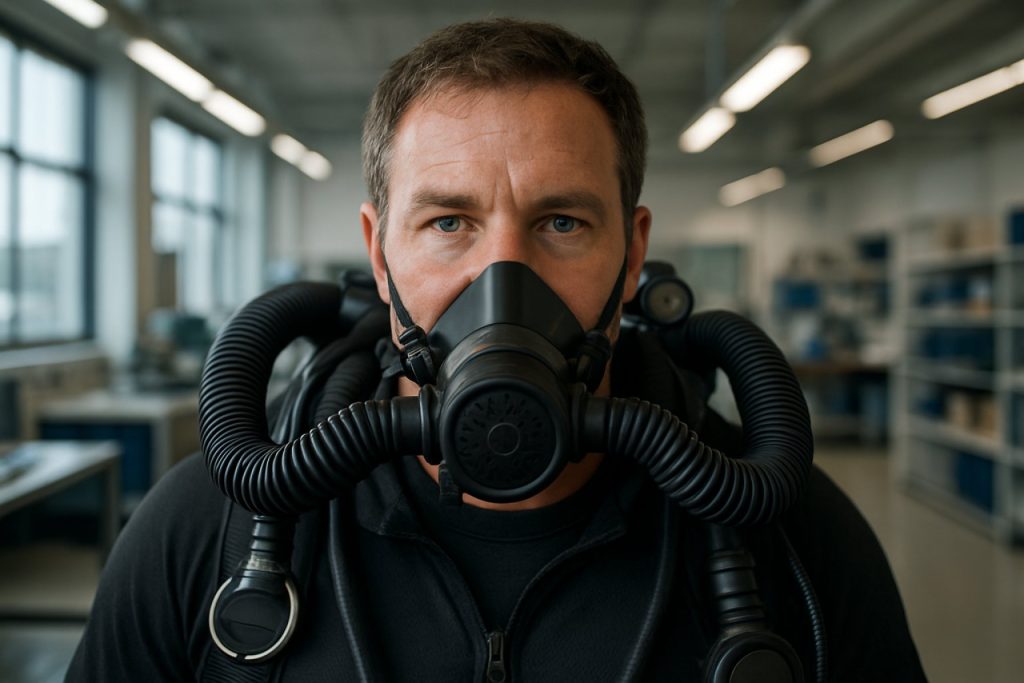
Sumário
- Resumo Executivo: Trajetória de Mercado 2025–2030
- Tecnologias Emergentes de Microfabricação em Componentes de Rebreathers
- Principais Atores & Parcerias Estratégicas (por exemplo, hollis.com, apeksdiving.com)
- Aplicações Atuai: Mergulho, Defesa e Além
- Inovações em Materiais: Nano-Revestimentos, MEMS e Fabricação Aditiva
- Paisagem Regulatória e Normas da Indústria (por exemplo, ssi.com, padi.com)
- Fatores que Influenciam o Mercado: Sustentabilidade, Miniaturização e Demandas de Segurança
- Análise Competitiva & Paisagem de Patentes
- Previsões de Mercado 2025–2030: Receita, Volume e Tendências Regionais
- Perspectivas Futuras: Tecnologia Disruptiva & Oportunidades de Investimento
- Fontes & Referências
Resumo Executivo: Trajetória de Mercado 2025–2030
O período de 2025 a 2030 deve testemunhar avanços significativos na microfabricação de componentes de rebreathers, impulsionados pela inovação contínua em ciência dos materiais, engenharia de precisão e automação. À medida que os rebreathers se tornam cada vez mais vitais para aplicações militares e civis — que vão desde a exploração em alto-mar até operações em ambientes perigosos — a demanda por componentes compactos, confiáveis e altamente eficientes está crescendo. As tecnologias de microfabricação estão no cerne dessa tendência, permitindo a produção de sensores, válvulas e módulos de gerenciamento de gás miniaturizados que são leves e robustos.
Fabricantes líderes, como a JFD e a Teledyne Marine, estão investindo em processos de microfabricação de ponta, incluindo fabricação aditiva avançada e usinagem a laser de precisão. Esses métodos facilitam a integração de novos materiais, como cerâmicas de alta resistência e polímeros especializados, otimizando tanto a durabilidade quanto a densidade funcional de componentes críticos de rebreathers. Por exemplo, sensores de oxigênio e transdutores de pressão baseados em sistemas microeletromecânicos (MEMS) estão agora entrando em fases de produção piloto, oferecendo confiabilidade e formatos melhores em relação aos designs legados.
Anúncios recentes da Norcros e esforços colaborativos dentro da Society of Naval Architects and Marine Engineers (SNAME) destacam um foco em microfabricação aditiva e subtrativa para geometrias de componentes complexas. Essas tecnologias permitem a personalização de componentes para perfis de missão específicos, reduzindo significativamente os tempos de entrega e possibilitando prototipagem rápida. Além disso, a integração de ferramentas de gêmeos digitais e simulação deve ainda acelerar o processo de microfabricação, reduzindo taxas de erro e desperdício de material.
- Eventos: 2025 é marcada pela iniciação de consórcios conjuntos entre a indústria e a academia, com o intuito de padronizar protocolos de microfabricação e acelerar a transferência de tecnologia. Pilotos industriais estão se expandindo em centros de fabricação chave na Europa e na América do Norte.
- Dados: Ensaios de campo iniciais da JFD e da Teledyne Marine sugerem uma redução de 20–30% no peso dos componentes e uma diminuição de até 40% no tempo de montagem para módulos de rebreather de próxima geração.
- Perspectivas: Entre 2025 e 2030, a rápida maturação da microfabricação deve permitir mais miniaturização, melhor interoperabilidade dos componentes e uso ampliado de sistemas de monitoramento inteligentes dentro de rebreathers. A adoção de práticas da Indústria 4.0 e robótica nas linhas de fabricação provavelmente tornará a componente de rebreathers mais avançados mais acessíveis e econômicos, apoiando uma implantação mais ampla em setores de defesa, mergulho comercial e pesquisa científica.
No geral, a trajetória da microfabricação de componentes de rebreather nos próximos cinco anos é definida por uma inovação acelerada, colaboração entre setores e um movimento acentuado em direção a ambientes de produção digitalizados e de alta precisão.
Tecnologias Emergentes de Microfabricação em Componentes de Rebreathers
As tecnologias de microfabricação estão fazendo avanços substanciais no design e fabricação de componentes avançados para rebreathers, com 2025 marcando um período de rápida transição da pesquisa de laboratório para prototipagem comercial e adoção inicial. Tradicionalmente, os sistemas de rebreather dependiam de métodos convencionais de usinagem e montagem para peças chave, como sensores de gás, válvulas e cartuchos de purificação. No entanto, a demanda por sistemas menores, mais leves e mais robustos — impulsionada tanto pelo mercado militar quanto pelo de mergulho recreativo — está acelerando a integração de sistemas microeletromecânicos (MEMS), fabricação aditiva e microfabricação avançada de polímeros.
Sensores de oxigênio e dióxido de carbono baseados em MEMS estão agora sendo desenvolvidos e testados para rebreathers de circuito fechado de próxima geração. Esses sensores, fabricados utilizando micro-usinagem em silício e deposição de filmes finos, prometem melhor tempo de resposta, miniaturização e confiabilidade aprimorada em comparação com as células eletroquímicas tradicionais. Vários fabricantes, incluindo Teledyne Technologies e AMETEK, estão refinando ativamente plataformas de sensores de gás MEMS proprietárias para integração em sistemas de suporte à vida portáteis. Protótipos de início de 2025 demonstraram operação estável em ambientes de alta pressão e alta umidade, e ensaios de campo estão previstos para o final de 2025.
A fabricação aditiva, especialmente a sinterização seletiva a laser em microescala (SLS) e a estereolitografia (SLA), está sendo utilizada para a prototipagem rápida de canais de fluxo complexos, micro-válvulas e casas de purificadores miniaturizadas. Líderes da indústria, como Stratasys e 3D Systems, expandiram seus portfólios para incluir capacidades de microfabricação de polímeros e metais de alta precisão, que agora estão sendo aproveitadas por fabricantes de equipamento original (OEMs) para produzir peças de rebreather personalizadas e com gradientes funcionais. A capacidade de iterar designs rapidamente e fabricar geometrias intrincadas com recursos de sensoriamento embutidos deverá reduzir ciclos de desenvolvimento e permitir montagens de rebreather mais ergonômicas e eficientes até 2026 e além.
- Sensores de oxigênio miniaturizados e de baixo consumo usando MEMS estão se aproximando da aprovação regulatória para uso em sistemas comerciais de rebreathers, com processos de verificação em andamento tanto na Europa quanto na América do Norte.
- Válvulas microfluídicas, fabricadas através de litografia de alta precisão, estão sendo avaliadas por seu potencial de fornecer controle de mistura e entrega de gás mais fino e automatizado, melhorando a segurança do mergulhador.
- Polímeros biocompatíveis avançados, como os fornecidos pela DSM, estão sendo personalizados em microescala para melhorar a resistência à corrosão salina e ao biofouling.
Olhando para o futuro, a convergência da microfabricação com design digital e monitoramento em tempo real deve resultar em sistemas de rebreather mais inteligentes e adaptáveis. Parcerias da indústria entre desenvolvedores de sensores, fabricantes aditivos e OEMs de equipamentos de mergulho devem acelerar a comercialização, com os primeiros módulos de rebreather totalmente microfabricados previstos para emergir em ensaios de campo até 2026. À medida que os padrões regulatórios se adaptarem para acomodar essas inovações, os próximos anos serão fundamentais para estabelecer a microfabricação como uma pedra angular da evolução da tecnologia de rebreathers.
Principais Atores & Parcerias Estratégicas (por exemplo, hollis.com, apeksdiving.com)
À medida que a tecnologia de rebreather se torna cada vez mais sofisticada, a microfabricação de componentes críticos está se tornando um ponto focal para os líderes da indústria. Em 2025 e nos anos seguintes, um seleto grupo de fabricantes, fornecedores de materiais e especialistas em eletrônica está impulsionando a inovação por meio de parcerias estratégicas e processos de engenharia avançados.
Atores-chave, como Hollis e Apeks Diving, desenvolveram capacidades internas e colaborações para avançar a miniaturização e a fabricação de precisão de componentes como sensores de oxigênio, válvulas solenóides e controladores de fluxo de gás. Estas empresas estão cada vez mais integrando sistemas microeletromecânicos (MEMS) e polímeros avançados para melhorar a confiabilidade, eficiência energética e monitoramento em tempo real dentro de sistemas compactos de rebreather.
Parcerias estratégicas entre marcas de mergulho estabelecidas e empresas especializadas em eletrônica ou materiais estão moldando o cenário competitivo. A Hollis, por exemplo, se envolveu com fornecedores de tecnologia de sensores e controle para co-desenvolver sensores de oxigênio miniaturizados e transdutores de pressão proprietários que suportam o exigente ambiente subaquático. Enquanto isso, a Apeks Diving colabora com fornecedores de elastômeros de alta performance e montagens de micro-válvulas, ressaltando a importância de alianças entre setores para avançar na segurança e eficiência dos rebreathers.
Além dos fabricantes de equipamentos de mergulho tradicionais, fornecedores de componentes, como a TE Connectivity, estão ativamente envolvidos na microfabricação de sensores de pressão e gás adaptados para montagens de rebreather. Esses sensores, frequentemente construídos usando tecnologia MEMS, oferecem maior precisão e tamanho reduzido, permitindo ainda mais miniaturização da eletrônica do ciclo respiratório. Além disso, a Parker Hannifin continua a fornecer válvulas solenóides micro avançadas e soluções de vedação adequadas para os rigorosos requisitos dos rebreathers de circuito fechado.
Olhando para frente, a indústria antecipa uma integração crescente da fabricação aditiva e micromachining de precisão na produção de componentes de rebreather. À medida que a demanda por sistemas compactos, leves e duráveis cresce — especialmente para mergulho militar, científico e técnico — as colaborações entre fabricantes de equipamentos originais (OEMs) e especialistas em microfabricação estabelecidos devem se intensificar. Essas parcerias visam empurrar os limites da ciência dos materiais e da fabricação digital, impulsionando a evolução dos rebreathers de alto desempenho até 2025 e além.
Aplicações Atuai: Mergulho, Defesa e Além
As tecnologias de microfabricação tornaram-se centrais na evolução dos componentes de rebreather, impulsionando avanços no mergulho, defesa e setores adjacentes ao longo de 2025. À medida que missões subaquáticas exigem durações mais longas, maior confiabilidade e sistemas de suporte à vida mais compactos, a integração de elementos microfabricados — como sensores de gás, válvulas e purificadores — ganhou importância crítica. Esses componentes miniaturizados oferecem eficiência e segurança aprimoradas ao reduzir o tamanho do dispositivo, otimizar o fluxo de gás e melhorar as capacidades de monitoramento em tempo real.
Em 2025, os fabricantes de rebreathers militares e comerciais estão cada vez mais aproveitando sistemas microeletromecânicos (MEMS) e usinagem a laser de precisão para produzir sensores de oxigênio ultra compactos e leitos de purificação de dióxido de carbono. Por exemplo, empresas líderes como JFD e Oceanic estão investindo na integração de sensores baseados em MEMS, permitindo análise contínua e rápida da composição gasosa dentro dos ciclos respiratórios dos rebreathers. Esses desenvolvimentos respondem a exigências de forças especiais navais e exploradores em alto-mar, onde até pequenas melhorias no tempo de resposta dos sensores ou no tamanho podem aumentar a capacidade de missão.
Outra área chave é a microfabricação de válvulas e atuadores, que resultou em mecanismos de adição e ventilação de gás mais leves e responsivos. Empresas como AP Diving estão explorando técnicas de fabricação aditiva e micromachining para produzir geometrias customizadas de válvulas, ajustadas para taxas de fluxo específicas e propriedades mecânicas. Esses avanços reduzem a complexidade mecânica dos rebreathers, contribuindo para maior confiabilidade e manutenção mais fácil, especialmente valiosas em aplicações de defesa onde o tempo de inatividade operacional deve ser minimizado.
Além disso, leitos de catalisadores microfabricados para purificação de CO2 estão se tornando mais prevalentes. Materiais de purificação granulares tradicionais estão sendo substituídos ou complementados por matrizes de microcanais estruturados, que oferecem maior área de superfície e caminhos de fluxo mais previsíveis. Com o suporte de inovadores e fornecedores em ciência dos materiais, como a 3M, esses purificadores microengenheirados estão sendo testados tanto para sistemas de respiração submarina quanto aeroespaciais.
Olhando para o futuro, a continuidade da convergência entre microfabricação, integração de sensores e materiais avançados deve resultar em sistemas de rebreather ainda mais compactos, inteligentes e energeticamente eficientes até o final da década de 2020. Essa trajetória provavelmente verá a tecnologia de rebreathers se expandir além do mergulho tradicional e da defesa para segurança industrial, combate a incêndios e exploração espacial — setores que exigem soluções de suporte à vida robustas e miniaturizadas.
Inovações em Materiais: Nano-Revestimentos, MEMS e Fabricação Aditiva
Em 2025, a microfabricação de componentes de rebreather está passando por rápida evolução, impulsionada por avanços em ciência dos materiais e fabricação de precisão. Três tendências tecnológicas principais — nano-revestimentos, sistemas microeletromecânicos (MEMS) e fabricação aditiva — estão convergindo para possibilitar rebreathers de circuito fechado mais seguros, eficientes e duráveis para aplicações em mergulho e industrial.
Nano-revestimentos estão sendo cada vez mais adotados para proteger componentes sensíveis de rebreathers contra corrosão, biofouling e degradação química. Esses filmes ultrafinos, frequentemente aplicados por meio de deposição de camada atômica ou deposição de vapor químico, aumentam a longevidade e a confiabilidade de sensores de oxigênio, casas de purificadores e caminhos de fluxo. Líderes da indústria, como a Evonik Industries AG, estão fornecendo materiais poliméricos avançados e tecnologias de superfície que permitem a criação de revestimentos robustos, hidrofóbicos e antimicrobianos, especificamente adaptados para ambientes subaquáticos e severos. Isso é particularmente relevante para cartuchos de purificação de CO2, onde nano-revestimentos podem reduzir significativamente perdas de desempenho devido à entrada de umidade.
Simultaneamente, a integração de MEMS está revolucionando a miniaturização e o desempenho dos sensores. Sensores de oxigênio e dióxido de carbono baseados em MEMS, incorporando eletrodos e canais em microescala, oferecem tempos de resposta mais rápidos, menor consumo de energia e maior durabilidade em comparação com seus equivalentes em macroescala. Empresas como a ams OSRAM e a Sensirion AG estão desenvolvendo sensores de gás MEMS compactos com encapsulamento robusto e capacidades de autocorreção. A implantação desses sensores dentro de rebreathers deve aprimorar o monitoramento em tempo real dos gases e o diagnóstico do sistema, contribuindo para a segurança geral do mergulhador.
A fabricação aditiva (AM), particularmente a sinterização seletiva a laser (SLS) e impressão 3D de múltiplos materiais, está ganhando espaço para prototipagem rápida e produção de geometrias complexas de rebreathers que, de outra forma, seriam difíceis de fabricar. Isso permite que os fabricantes otimizem os caminhos de fluxo, integrem defletores e reduzam a contagem de componentes, tudo isso enquanto utilizam polímeros de alto desempenho e ligas metálicas. Por exemplo, a Stratasys Ltd. e a 3D Systems Corporation estão colaborando com fabricantes de defesa e equipamentos de mergulho para produzir casas e bocais de rebreathers personalizados e leves, aproveitando a liberdade de design e o potencial iterativo da AM.
Olhando para o futuro, os próximos anos devem ver uma maior convergência dessas tecnologias, possibilitando a integração de superfícies nanoengenheiradas, sensores MEMS embutidos e arquiteturas fabricadas aditivamente em uma nova geração de rebreathers inteligentes e autônomos. A contínua miniaturização e os ganhos de desempenho devem melhorar a resistência das missões e a segurança operacional, expandindo o uso de rebreathers em setores profissionais e recreativos.
Paisagem Regulatória e Normas da Indústria (por exemplo, ssi.com, padi.com)
A paisagem regulatória para a microfabricação de componentes de rebreather está em rápida evolução, refletindo a mudança da indústria em direção a técnicas avançadas de fabricação e a importância crítica da segurança em sistemas de suporte à vida. Desde 2025, a integração de componentes microfabricados — como sensores de oxigênio de precisão, cartuchos de purificação miniaturizados e microválvulas personalizadas — levou tanto a indústria quanto os órgãos reguladores a reavaliar os padrões e procedimentos de supervisão existentes.
Agências de certificação de mergulho de destaque, como a Scuba Schools International (SSI) e a Professional Association of Diving Instructors (PADI), têm fornecido diretrizes para uso de rebreathers, com foco principalmente na segurança operacional, treinamento de mergulhadores e manutenção de equipamentos. No entanto, a emergência da microfabricação na fabricação de componentes de rebreathers agora está compelindo essas organizações a consultar fabricantes e órgãos de normas para abordar novos riscos e variáveis de desempenho associadas a peças miniaturizadas.
Fabricantes que adotam processos de microfabricação para elementos críticos de rebreather estão cada vez mais referenciando normas internacionais tanto para segurança do produto quanto para validação do processo. A série ISO 24801 e ISO 10218, que dizem respeito ao treinamento de mergulhadores e à segurança de máquinas, são frequentemente citadas, mas agora estão sendo suplementadas por orientações específicas para sistemas microeletromecânicos (MEMS) e fabricação de dispositivos médicos de precisão. Essa mudança é evidente nas práticas de empresas como a Ambient Pressure Diving e a PADI TecRec, que estão engajadas em esforços colaborativos para garantir que as peças microfabricadas atendam aos critérios emergentes de durabilidade, precisão e compatibilidade com montagens tradicionais de rebreathers.
Em 2025, o escrutínio regulatório é mais pronunciado na certificação e testes de micro-sensores e elementos de purificação, onde a falha do componente poderia comprometer diretamente a segurança do mergulhador. Há uma tendência crescente para testes e certificação de terceiros, com agências exigindo que os fabricantes forneçam documentação sobre condições de fabricação em sala limpa, rastreabilidade de matérias-primas e testes rigorosos em lotes para peças microfabricadas. Isso é apoiado por parcerias técnicas entre fabricantes e organizações como a Divex, que estão trabalhando para alinhar a garantia de qualidade interna com padrões internacionais em evolução.
Olhando para o futuro, os próximos anos devem trazer uma harmonização mais rigorosa entre padrões de microfabricação industrial e regulamentações de equipamentos de mergulho. Grupos da indústria antecipam novas especificações técnicas ISO adaptadas para componentes de suporte à vida microfabricados. Organizações de treinamento, como a SSI e a PADI, estão se preparando para atualizar seus padrões e materiais de treinamento para refletir os desafios únicos de manutenção e inspeção impostos pelos componentes de rebreather miniaturizados, garantindo que a segurança do mergulhador permaneça primordial à medida que a tecnologia avança.
Fatores que Influenciam o Mercado: Sustentabilidade, Miniaturização e Demandas de Segurança
A microfabricação de componentes de rebreather tornou-se um ponto focal nas indústrias de equipamentos de suporte à vida e mergulho, especialmente à medida que fatores de mercado como sustentabilidade, miniaturização e demandas de segurança crescentes convergem em 2025 e nos anos seguintes. Pressões regulatórias e expectativas dos usuários finais estão estimulando inovação rápida em como componentes — como sensores de gás, válvulas e cartuchos de purificação — são projetados e fabricados.
A sustentabilidade é um motor proeminente, com os fabricantes buscando reduzir a pegada ambiental tanto dos processos de produção quanto do ciclo operacional dos rebreathers. A microfabricação possibilita o uso de materiais avançados, como polímeros biocompatíveis e compósitos recicláveis, e facilita a engenharia de precisão que minimiza desperdícios. Empresas como a Teledyne Technologies Incorporated e a Honeywell International Inc. estão desenvolvendo sensores de gás em microescala e módulos eletrônicos que são não apenas mais eficientes em termos energéticos, mas também projetados para intervalos de serviço prolongados e reciclagem facilitada ao final de sua vida útil. Isso está alinhado com metas mais amplas de sustentabilidade da indústria e regulamentações de materiais cada vez mais rigorosas.
A miniaturização continua a ser uma tendência crítica, impulsionada por aplicações profissionais e recreativas, onde sistemas vestíveis e compactos são desejados. As técnicas de microfabricação, como MEMS (Sistemas Microeletromecânicos) e fabricação aditiva avançada, permitem a integração de funcionalidades complexas em espaços menores. A Smiths Group plc reportou investimentos contínuos em válvulas de controle microfluídicas e matrizes de sensores compactas adaptadas para montagens de rebreather, visando melhorar tanto a portabilidade quanto a confiabilidade. Esses avanços permitem que os fabricantes ofereçam unidades de rebreather mais leves e menos intrusivas que não comprometem o desempenho, um diferenciador-chave em mercados competitivos.
Considerações de segurança também estão acelerando a adoção de componentes microfabricados. O monitoramento em tempo real aprimorado da composição gasosa e diagnósticos do sistema — possíveis através de sensores sensíveis em microescala — melhora tanto a confiança do usuário quanto a conformidade com os padrões de segurança em evolução. Empresas como a Drägerwerk AG & Co. KGaA estão na vanguarda, integrando sensores de gás microfabricados e sistemas de controle à prova de falhas em seus últimos modelos de rebreathers para atender tanto requisitos do setor civil quanto de defesa.
Olhando para o futuro, os próximos anos devem ver uma adoção mais ampla de processos de microfabricação automatizados e de alto rendimento, reduzindo custos unitários e melhorando ainda mais as métricas de sustentabilidade. A contínua convergência entre sustentabilidade, miniaturização e demandas de segurança provavelmente impulsionará esforços colaborativos entre fabricantes estabelecidos e empresas especializadas em microfabricação, criando novos padrões para a qualidade e desempenho dos componentes de rebreather.
Análise Competitiva & Paisagem de Patentes
O cenário para microfabricação de componentes de rebreather está evoluindo rapidamente à medida que fabricantes e fornecedores de tecnologia respondem à crescente demanda por aparelhos de respiração compactos, eficientes e confiáveis para aplicações profissionais e recreativas. A partir de 2025, o ambiente competitivo é definido por um punhado de jogadores estabelecidos, startups emergentes e uma atividade substancial de propriedade intelectual (PI), particularmente na miniaturização de sensores, válvulas e sistemas de gerenciamento de gás.
Principais líderes da indústria, como a JFD Global e a Ambient Pressure Diving, estão investindo ativamente em técnicas de microfabricação para melhorar as características de desempenho e segurança de suas linhas de produtos de rebreathers. Essas empresas estão aproveitando os avanços em sistemas microeletromecânicos (MEMS) para reduzir as dimensões dos componentes, melhorando a durabilidade e a integração com sistemas de monitoramento digital. Por exemplo, sensores de oxigênio baseados em MEMS e válvulas solenóides compactas estão se tornando cada vez mais prevalentes, impulsionados pela necessidade de maior confiabilidade e menor consumo de energia.
Startups e fornecedores especializados, como a Norcotek, estão fazendo progressos desenvolvendo sensores microfabricados proprietários e controladores de fluxo adaptados para os ambientes exigentes dos rebreathers subaquáticos. Essas inovações não estão apenas sendo incorporadas em novos designs de produtos, mas também estão sendo licenciadas para OEMs estabelecidos, intensificando ainda mais a competição e fomentando um cenário dinâmico de PI.
Os pedidos de patentes nos últimos dois anos refletem essas tendências, com um aumento notável em aplicações relacionadas a sensores de gás miniaturizados, montagens de micro-válvulas e tecnologias de vedação avançadas. Bancos de dados de patentes mostram um número crescente de pedidos tanto de fabricantes incumbentes quanto de novos entrantes, indicando uma corrida para garantir tecnologias fundamentais. Por exemplo, a Teledyne Technologies e a Honeywell expandiram seus portfolios de patentes nas áreas de detecção de gás baseada em MEMS e controle microfluídico relevantes para montagens de rebreather, sugerindo um potencial para transferência de tecnologia entre indústrias.
Olhando para frente, o setor está preparado para uma maior consolidação à medida que entidades maiores buscam adquirir startups promissoras para garantir acesso a processos de microfabricação inovadores e PI única. Ao mesmo tempo, colaborações entre fabricantes de componentes e integradores de sistemas devem acelerar a tradução de inovações em escala de laboratório em produtos comerciais. Normas regulatórias e especificações militares também estão influenciando as prioridades de design, exigindo maior robustez e rastreamento do ciclo de vida em nível de componente.
No geral, o cenário competitivo e de patentes para a microfabricação de componentes de rebreather em 2025 é caracterizado por estratégias agressivas de PI, parcerias entre setores e um forte foco na miniaturização, sinalizando um período de inovação sustentada e diferenciação de mercado por meio de tecnologia proprietária.
Previsões de Mercado 2025–2030: Receita, Volume e Tendências Regionais
O período de 2025 a 2030 deve testemunhar avanços significativos e expansão de mercado na microfabricação de componentes de rebreather. A microfabricação, que possibilita a produção de componentes altamente miniaturizados e precisos, é cada vez mais crítica para melhorar o desempenho, a segurança e a facilidade de uso dos sistemas de rebreather em aplicações militares e comerciais de mergulho.
Líderes do setor estão investindo pesadamente em sistemas microeletromecânicos (MEMS) e processos avançados de fabricação aditiva para produzir sensores, válvulas e módulos eletrônicos integrados em microescala. Empresas como Parker Hannifin e Honeywell estão expandindo suas capacidades de microfabricação, fornecendo componentes críticos de sensores e controle que sustentam a segurança e eficiência dos rebreathers de circuito fechado.
As previsões de receita para o setor de microfabricação de componentes de rebreather são otimistas, impulsionadas pela crescente adoção de rebreathers de circuito fechado (CCRs) em mercados militares, profissionais e recreativos. Até 2030, as receitas globais anuais para componentes de rebreather microfabricados devem ultrapassar $300 milhões, marcando uma taxa de crescimento anual composta (CAGR) de 8–10% em relação aos níveis de 2025. A produção em volume deve aumentar correspondentemente, com a produção de sensores e microválvulas baseados em MEMS aumentando mais de 30% para atender à demanda crescente, particularmente de programas de aquisição de defesa e operadores de mergulho comercial.
Regionalmente, espera-se que a América do Norte e a Europa mantenham a liderança de mercado, apoiadas por OEMs estabelecidos, infraestrutura robusta de P&D e gastos significativos em defesa. Os Estados Unidos, em particular, provavelmente verão investimento sustentado tanto do Departamento de Defesa quanto de contratantes principais como a Lockheed Martin e a Northrop Grumman, que estão integrando sensores e elementos de controle microfabricados avançados em rebreathers para mergulhadores de combate de próxima geração. Na Europa, empresas como a Divex (parte da JFD Global) também estão acelerando a adoção de eletrônicos microfabricados e módulos de controle de gás.
A região da Ásia-Pacífico deve registrar o crescimento mais rápido, impulsionada pela crescente atividade marítima e programas de modernização naval em países como China, Coreia do Sul e Austrália. Fabricantes regionais estão começando a investir em capacidades de microfabricação doméstica, com o objetivo de reduzir a dependência de importações e desenvolver tecnologias de rebreather indígenas.
Olhando para o futuro, a contínua miniaturização e integração funcional de componentes de rebreather através da microfabricação permanecerão centrais para a inovação de produtos. A integração de sensoriamento de gás em tempo real, telemetria sem fio e controle de fluxo automatizado em microescala é esperada para estabelecer novos padrões de desempenho e segurança, reforçando a trajetória ascendente deste segmento de mercado até 2030.
Perspectivas Futuras: Tecnologia Disruptiva & Oportunidades de Investimento
O cenário da microfabricação de componentes de rebreather está prestes a passar por uma transformação significativa até 2025 e nos anos seguintes, impulsionada por avanços em ciência dos materiais, fabricação aditiva e técnicas de miniaturização. À medida que a exploração subaquática, defesa e operações de resgate exigem sistemas de suporte à vida cada vez mais confiáveis e compactos, a integração estratégica de tecnologias de microfabricação disruptivas oferece tanto melhorias de desempenho quanto novas avenidas de investimento.
Os principais players do mercado de rebreathers, como James Fisher and Sons plc (através de sua subsidiária Divex) e a Teledyne Marine, estão cada vez mais aproveitando a fabricação em microescala para desenvolver purificadores de CO2 mais leves e eficientes, sensores de oxigênio avançados e reguladores de fluxo de alta precisão. Esses componentes se beneficiam dos processos de sistemas microeletromecânicos (MEMS), permitindo a integração de sensores e microválvulas diretamente em plataformas em escala de chip, reduzindo a complexidade de montagem e pontos de falha.
A partir de 2025, a adoção da indústria de microreatores cerâmicos e materiais micro-porosos está acelerando, inspirada por desenvolvimentos nos setores mais amplos de medicina e aeroespacial. Empresas como a Oxis Energy (notada por sua experiência em tecnologia de bateria de lítio-enxofre e materiais avançados) estão explorando sinergias em microfabricação tanto para armazenamento de energia quanto para gerenciamento de gás dentro de aparelhos de respiração de circuito fechado. A convergência da impressão 3D com microfluídica está permitindo a prototipagem rápida de componentes de rebreather projetados sob medida, adaptados a perfis de missão específicos ou dados fisiológicos do usuário.
No front de investimentos, parcerias estratégicas entre contratantes de defesa, fabricantes de rebreathers estabelecidos e empresas de engenharia de precisão devem se intensificar. O foco está na ampliação da produção de sensores de oxigênio baseados em MEMS e na integração de diagnósticos inteligentes em módulos de controle compactos. A Honeywell International Inc. continua a investir na miniaturização de sensores e tecnologias de monitoramento ambiental robustas, com aplicações potenciais para sistemas de rebreather de próxima geração.
Olhando para frente, a maturação da embalagem em nível de wafer, revestimentos biocompatíveis e catalisadores nanoestruturados está prestes a interromper ainda mais abordagens tradicionais para o design de componentes de rebreather. Analistas da indústria antecipam que, até o final da década de 2020, peças microfabricadas se tornarão padrão em equipamentos de mergulho profissional e recreativo, proporcionando maior segurança, maior resistência nas missões e capacidades de manutenção preditiva. Essa evolução abre novas oportunidades de investimento para stakeholders em materiais, automação de fabricação e ecossistemas de suporte à vida habilitados para IoT, cimentando a microfabricação como uma pedra angular da inovação futura em rebreathers.
Fontes & Referências
- Teledyne Marine
- Norcros
- Society of Naval Architects and Marine Engineers
- Teledyne Technologies
- AMETEK
- Stratasys
- 3D Systems
- DSM
- AP Diving
- Evonik Industries AG
- ams OSRAM
- Sensirion AG
- Professional Association of Diving Instructors (PADI)
- Ambient Pressure Diving
- Honeywell International Inc.
- Smiths Group plc
- Norcotek
- Lockheed Martin
- Northrop Grumman
- JFD Global