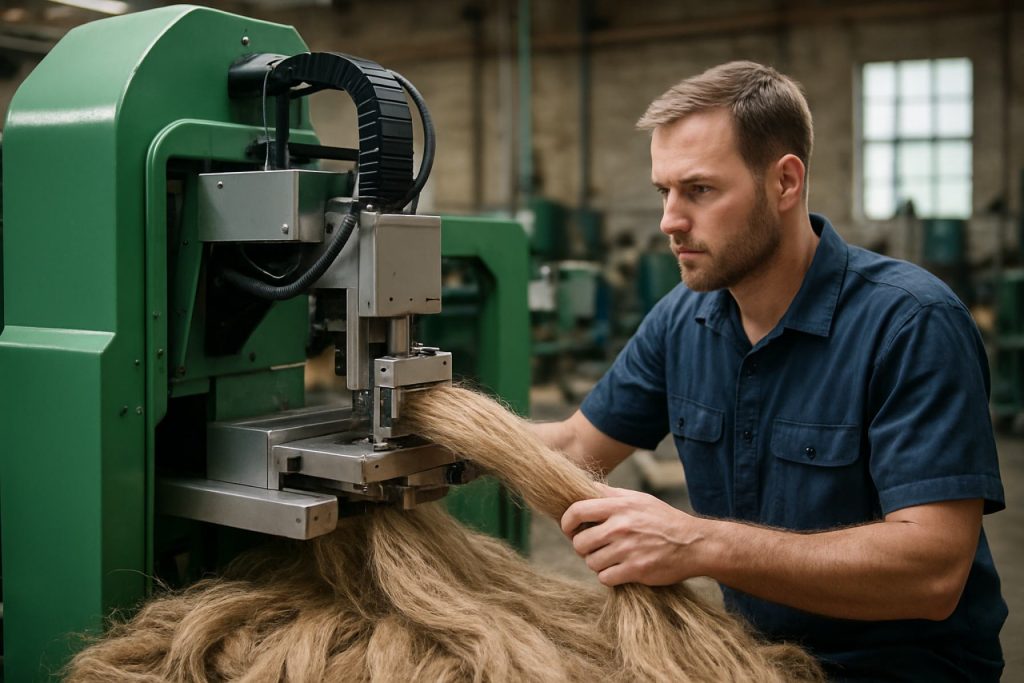
Table of Contents
- Executive Summary: The 2025 Jute Equipment Market in Focus
- Global Demand Drivers and Emerging Markets
- Key Players and Strategic Alliances (Based on Official Manufacturer Data)
- Technological Breakthroughs in Jute Processing Machinery
- Sustainability and Eco-Efficiency Trends
- Regulatory Landscape and Industry Standards (Referencing IJMA and National Bodies)
- Market Forecasts: 2025-2030 Growth Projections
- Supply Chain Dynamics and Sourcing Innovations
- Barriers, Opportunities, and Risk Factors
- Future Outlook: Next-Gen Equipment and Industry 4.0 Integration
- Sources & References
Executive Summary: The 2025 Jute Equipment Market in Focus
The global market for high-quality jute processing equipment is positioned for significant transformation in 2025, influenced by technological innovation, sustainability imperatives, and strategic capacity expansion in major jute-producing regions. Jute, often referred to as the “golden fiber,” underpins a sector vital to the economies of Bangladesh, India, and other South and Southeast Asian countries. As demand for eco-friendly natural fibers rises, so does the requirement for advanced machinery that ensures efficiency, precision, and minimal environmental impact.
Key manufacturers are intensifying their investments in automation and digitalization, integrating features such as programmable logic controllers, IoT-enabled monitoring, and energy-efficient drives. Companies like Lathagri Group and Bhowmik Industries, both headquartered in India, are at the forefront, producing a wide range of high-speed carding, spinning, and weaving machines tailored for both traditional and technical jute applications. These firms are also focusing on the modularity and retrofitting of legacy equipment, allowing mills to upgrade existing infrastructure without full-scale replacement.
- In Bangladesh, government-backed modernization programs are accelerating the adoption of advanced jute machinery. Partnerships with machinery suppliers, including Bangladesh Jute Mills Corporation, are enabling local mills to implement high-efficiency processing lines, with an emphasis on product quality and export competitiveness.
- Environmental regulations coming into force in 2025—especially in Europe and North America—are boosting international demand for jute-based products, further spurring investment in top-tier processing equipment. Manufacturers are responding with machinery designed to minimize fiber wastage and energy consumption while maximizing output consistency.
- The global supply chain for jute machinery remains concentrated in South Asia, but European and Chinese equipment makers are increasing their presence, introducing hybrid technologies and collaborative manufacturing models.
Looking ahead, the outlook for high-quality jute processing equipment manufacturing remains robust. Industry stakeholders expect sustained growth through 2025 and beyond, driven by rising jute consumption across packaging, textiles, and composites sectors. Technological collaborations and government incentives are likely to further accelerate the pace of innovation, with the sector moving towards greater automation and digital integration. As market dynamics evolve, companies that prioritize advanced production technologies and sustainability will be best positioned to capture emerging opportunities in the global jute economy.
Global Demand Drivers and Emerging Markets
The global demand for high-quality jute processing equipment is on an upward trajectory in 2025, spurred by a combination of environmental regulations, sustainable packaging initiatives, and expanding applications of jute products. Major jute-producing countries such as India and Bangladesh have intensified their focus on modernizing processing infrastructure to meet export standards and diversify product lines. This modernization has directly fueled the need for advanced machinery capable of increasing yield, reducing manual labor, and improving fiber quality.
Several key factors are shaping the demand landscape. First, governments and industry bodies are implementing policies to reduce reliance on synthetic fibers. For example, India’s mandatory packaging norms and the ongoing “Plastic Waste Management” push are driving the replacement of plastics with jute-based alternatives, thus necessitating efficient processing equipment (National Jute Board). The Bangladesh government has also launched initiatives to revive the jute sector, including incentives for upgrading mills and adopting new technologies (Bangladesh Jute Mills Corporation).
Emerging markets in Southeast Asia and Africa are increasingly being recognized as growth engines for the industry. Countries like Myanmar, Pakistan, and Ethiopia are investing in jute cultivation and processing to tap into global eco-friendly packaging trends. These markets often require robust, cost-effective equipment tailored to local conditions, presenting opportunities for manufacturers to introduce modular and automated solutions.
In addition to traditional applications such as sacks and textiles, there is a noticeable shift toward value-added jute products—composites, geotextiles, and home furnishings—especially in Europe and North America. This diversification demands flexible, high-precision processing machinery that can handle varying grades and blends of jute fiber (Lakshmi Machine Works). Established manufacturers are responding with innovations in carding, spinning, and weaving technologies, while also focusing on energy efficiency and digital integration.
Looking ahead to the next few years, the outlook for high-quality jute processing equipment manufacturing is robust. Rising awareness of the environmental benefits of jute, ongoing government support, and the unlocking of new applications are set to drive sustained investment. Companies with the capability to localize equipment design and provide after-sales support in emerging markets are poised to capture significant market share as global supply chains increasingly prioritize sustainability and traceability.
Key Players and Strategic Alliances (Based on Official Manufacturer Data)
The high-quality jute processing equipment manufacturing sector in 2025 is characterized by a robust network of established manufacturers and emerging technology specialists, primarily concentrated in South Asia but with a growing international footprint. Notable key players include Lagan Engineering Company Ltd., Bajaj Steel Industries Ltd., and Jutex Industries Private Limited, whose machinery is widely adopted across major jute-producing regions. These companies have consistently invested in research and development to enhance automation, productivity, and energy efficiency in jute processing lines.
Strategic alliances have become increasingly prominent as manufacturers respond to rising global demand for sustainable fibers and stricter quality standards. For instance, Lagan Engineering Company Ltd. has entered technical collaborations with international component suppliers to integrate advanced control systems and IoT-enabled monitoring into their carding and spinning equipment. Such partnerships are designed to minimize downtime and enable predictive maintenance, a vital requirement for large-scale jute mills targeting export markets.
Meanwhile, Bajaj Steel Industries Ltd. has focused on forming distribution and service alliances with regional partners in Bangladesh, Vietnam, and Africa, strengthening after-sales support and local customization of equipment. By 2025, these strategic efforts are expected to help expand the company’s market share beyond India’s domestic sector, tapping into the growing trend of jute-based packaging alternatives driven by environmental regulations.
Emerging entrants like Jutex Industries Private Limited are leveraging joint ventures with textile machinery innovators to accelerate the adoption of modular and energy-efficient processing units. These alliances are particularly crucial as sustainability certifications become prerequisites for international buyers, necessitating traceability and standardized output quality.
Industry bodies, including the Indian Jute Mills Association, play a pivotal role in facilitating collaboration between equipment manufacturers and jute mills, promoting the standardization of machinery and the dissemination of best practices. The association’s capacity-building initiatives and technical workshops are instrumental in driving adoption of advanced machinery and fostering technology transfer between established players and new entrants.
Looking ahead to the next few years, the sector is set to witness intensified collaboration, with strategic alliances not only advancing technical capabilities but also supporting compliance with evolving global sustainability benchmarks. As automation and digitalization become central to jute processing, the role of key players—and their ability to forge effective partnerships—will remain critical in shaping the industry’s competitive landscape.
Technological Breakthroughs in Jute Processing Machinery
The jute processing equipment manufacturing sector is undergoing significant technological transformation in 2025, driven by the rising global demand for sustainable natural fibers and increasing pressure to improve both productivity and quality. High-quality jute processing machinery is at the core of this evolution, with manufacturers introducing innovations aimed at reducing labor intensity, minimizing fiber loss, and enhancing finished product consistency.
A central trend in 2025 is the integration of automation and digital monitoring systems into traditional jute machinery. Leading manufacturers are equipping their carding, drawing, and spinning machines with programmable logic controllers (PLCs) and sensor-based feedback loops. Such advancements enable precise control of critical parameters like tension, speed, and temperature, which is instrumental in minimizing defects and improving yield. Companies like Laxmi Enterprises and Bhowmick Jute Machinery have showcased semi-automatic jute spinning and carding units with digital interfaces, allowing operators to monitor operational health and intervene proactively when anomalies are detected.
Another breakthrough area is energy efficiency and environmental compliance. Modern jute processing equipment now incorporates variable frequency drives (VFDs), energy-optimized motors, and improved dust extraction systems. These features not only reduce operational costs but also align with tightening regulatory standards on emissions and workplace safety in major jute-producing regions. Companies such as Bhowmick Jute Machinery are deploying advanced dust control systems and eco-friendly processing modules, which help mills meet both local and international environmental requirements.
Precision engineering in key machinery components—such as high-tolerance rollers, hardened combs, and anti-corrosive finishes—is further elevating reliability and longevity. This is particularly evident in the latest batch of looms and spinning frames, which are being designed for reduced maintenance and consistent output quality even under demanding operating conditions. Indian and Bangladeshi manufacturers continue to dominate the sector, but machinery exports are rising as mills in Africa and Southeast Asia seek to modernize their operations.
Looking ahead, the outlook for high-quality jute processing equipment manufacturing is robust. The sector is anticipated to see continued investment in automation, Internet of Things (IoT) integration, and sustainability-focused design improvements over the next few years. As consumer and regulatory emphasis on eco-friendly materials intensifies, manufacturers able to offer technologically advanced, reliable, and energy-efficient jute machinery are poised for strong growth and expanded international reach.
Sustainability and Eco-Efficiency Trends
The drive for sustainability and eco-efficiency is reshaping the global landscape of high-quality jute processing equipment manufacturing in 2025. As consumer and regulatory demands for environmentally responsible production intensify, equipment manufacturers are prioritizing the development of machinery that minimizes resource consumption, energy use, and waste across the jute value chain.
Key players in the sector are investing in advanced technologies such as automated retting systems, closed-loop water recycling, and energy-efficient fiber extraction mechanisms. For example, manufacturers like Lagan Engineering Company Ltd.—a prominent supplier with a substantial footprint in India and Bangladesh—have incorporated variable frequency drives and smart control systems into their latest jute carding and spinning machines, which reduce electricity consumption by up to 20%. Such initiatives not only cut operational costs for mill owners but also significantly lower the carbon footprint of jute processing.
Another notable trend is the adoption of modular equipment designs that allow for easier upgrades, repair, and recycling of machine components, extending the lifecycle of capital assets and reducing e-waste. Companies like Bhowmick Jute Machinery are marketing modular systems that operators can adapt to different jute varieties and processing requirements, further minimizing excess resource use and material wastage.
Water management is a critical aspect of sustainability in jute processing. Modern machinery increasingly features integrated water-saving technologies. For instance, manufacturers have developed specialized washers and softening machines that recycle and filter water in closed systems, dramatically reducing freshwater intake and effluent discharge. This is particularly important in regions where water scarcity is a growing concern and environmental regulations are tightening.
In 2025 and the coming years, the outlook for sustainable jute processing equipment manufacturing remains robust. Policy frameworks in major producing countries—such as India and Bangladesh—are expected to further incentivize the adoption of eco-efficient machinery through subsidies, tax breaks, and green certification schemes. Equipment manufacturers are also aligning with international sustainability standards and collaborating with organizations like the Indian Jute Mills Association to promote best practices in environmental management.
As the global demand for biodegradable fibers and eco-friendly products continues to rise, high-quality jute processing equipment manufacturers will remain at the forefront of innovation, leveraging sustainability as both a market differentiator and a driver for long-term growth.
Regulatory Landscape and Industry Standards (Referencing IJMA and National Bodies)
The regulatory landscape governing high-quality jute processing equipment manufacturing in 2025 is shaped by both national and international bodies focused on promoting sustainable practices, technology standards, and operational safety. The Indian Jute Mills Association (IJMA) remains a central authority, working closely with manufacturers to ensure compliance with evolving technical and environmental standards. IJMA facilitates collaboration between equipment producers, jute mills, and policymakers, helping to translate regulatory changes into practical enhancements in machinery design and performance.
Key industry standards focus on energy efficiency, machinery safety, and compatibility with eco-friendly jute processing techniques. The Bureau of Indian Standards (BIS) regularly updates its codes for textile machinery, including those specific to jute, to reflect technological advances and sustainability goals. In 2025, BIS is expected to reinforce standards for emissions control, machine durability, and operator safety, in alignment with both national targets and international commitments to greener textiles manufacturing. Jute equipment manufacturers must adhere to these standards to access government procurement and export markets.
At the national level, the Ministry of Textiles plays a pivotal regulatory role, mandating certification schemes and encouraging industry-wide adoption of best practices. Incentive programs under schemes like the National Jute Policy are tied to compliance with quality and safety benchmarks set by recognized bodies. The Ministry has also intensified monitoring in 2025 to ensure that new equipment installations in jute mills meet prescribed efficiency and environmental criteria.
The regulatory framework is further influenced by export requirements, as major importing countries enforce their own product safety and sustainability standards. Jute processing equipment destined for international markets often undergoes additional certification, such as CE marking for the European Union, which is overseen by both national and international conformity assessment bodies. This trend is pushing Indian and Bangladeshi manufacturers to continuously upgrade their quality management systems.
Looking ahead, the regulatory outlook for the next few years suggests a tightening of standards, particularly regarding automation, digital monitoring, and emissions mitigation. The Indian Jute Mills Association and BIS are expected to roll out new guidelines to facilitate the integration of Industry 4.0 solutions into jute machinery, aiming to boost global competitiveness and sustainability of the sector. Manufacturers investing in compliance and certification are likely to benefit from expanded market access and enhanced operational efficiencies.
Market Forecasts: 2025-2030 Growth Projections
The market for high-quality jute processing equipment is projected to experience moderate yet sustained growth between 2025 and 2030, driven by increasing demand for eco-friendly textiles, modernization initiatives in traditional jute-producing regions, and evolving global sustainability standards. As major economies continue to emphasize circular and green manufacturing, jute—being a biodegradable and renewable fiber—has gained renewed attention, leading to more investments in efficient jute processing technologies.
According to recent industry discussions and strategic announcements from leading manufacturers, the modernization of jute mills and the integration of automated and energy-efficient machinery are expected to be key growth drivers over this period. Companies such as Lakshmi Machine Works, a recognized textile machinery manufacturer with a diverse portfolio, and Rieter, which has a global presence in spinning systems, are reportedly exploring expansions and technology upgrades that can be adapted for jute spinning and processing. These efforts align with government-backed initiatives—particularly in South Asian countries like India and Bangladesh, long-standing leaders in jute production—to incentivize the adoption of modern jute processing equipment through subsidies and technical support. The Government of India, for instance, continues to implement technology upgrade funds and modernization schemes targeting jute mills, aiming to increase both the quality and yield of processed jute fiber.
On the supply side, equipment manufacturers are prioritizing the development of machinery that reduces fiber wastage, improves consistency, and minimizes energy and water consumption. Firms like Ludlow Jute & Specialities Limited, which has expanded into manufacturing and upgrading jute processing machinery, are investing in R&D to meet the anticipated surge in demand for high-precision equipment. The increasing adoption of digital controls and automation in new installations is expected to further enhance efficiency and throughput while meeting the growing expectations for product traceability and compliance with international quality standards.
Market estimates for 2025-2030 anticipate a compound annual growth rate (CAGR) in the mid-single digits for the jute processing equipment sector, with the largest gains projected in Asia-Pacific, followed by emerging opportunities in Africa and Latin America as these regions seek to diversify their agricultural exports. The sector’s outlook remains positive, underpinned by robust policy support, rising consumer preference for natural fibers, and ongoing innovation among established and emerging manufacturers. Strategic collaborations between mill owners, technology providers, and government agencies are likely to define the next phase of industry growth, positioning high-quality jute processing equipment as a cornerstone of sustainable textile manufacturing for the coming years.
Supply Chain Dynamics and Sourcing Innovations
The supply chain dynamics in high-quality jute processing equipment manufacturing are undergoing significant evolution as the industry adapts to rising global demand for sustainable materials and improved machinery performance. In 2025, manufacturers are focusing on integrating advanced sourcing strategies and digital innovations to boost both the resilience and efficiency of their supply chains.
A key trend is the increased localization and diversification of critical component sourcing. Major equipment producers such as Lakshmi Machine Works and Bajaj Steel Industries are collaborating more closely with domestic part suppliers to reduce dependency on volatile international logistics and tariffs. This shift is further supported by investments in quality certification and supplier development programs, ensuring that locally sourced components match international standards required for precision jute processing machinery.
In parallel, digitalization is playing a central role in supply chain management. Real-time inventory tracking, predictive analytics, and integrated procurement platforms are being adopted to enhance transparency and responsiveness. Companies like Bajaj Steel Industries are deploying digital supply chain tools to monitor the flow of raw materials and finished components, minimizing lead times and improving production planning accuracy. Such technologies are critical in responding swiftly to fluctuations in both demand and input availability—a challenge highlighted in recent years by pandemic-related disruptions.
Sourcing innovations also extend to strategic partnerships with technology providers and research institutions. Equipment manufacturers are working closely with R&D centers to source cutting-edge automation modules, sensors, and energy-efficient drive systems. For instance, partnerships between machinery makers and universities in India and Bangladesh are yielding custom solutions tailored to the specific processing needs of regional jute varieties, further enhancing supply chain flexibility.
Sustainability considerations are increasingly influencing sourcing decisions as well. There is a growing emphasis on traceability of materials and compliance with environmental standards. Leading manufacturers, including Lakshmi Machine Works, are integrating eco-friendly materials and processes into their equipment production lines, not only to meet regulatory requirements but also to align with the sustainability goals of downstream textile producers.
Looking ahead, the supply chain for high-quality jute processing equipment is expected to become more integrated and digitally enabled, featuring robust collaborations across the value chain. As manufacturers continue to invest in technology and local supplier ecosystems, the sector is poised for greater agility and innovation, positioning it to meet the evolving needs of the global jute industry through 2025 and beyond.
Barriers, Opportunities, and Risk Factors
The landscape of high-quality jute processing equipment manufacturing in 2025 presents a dynamic interplay of barriers, opportunities, and risk factors as the sector adapts to evolving global requirements and technological advancements.
Barriers in this sector are primarily rooted in the need for significant capital investment and specialized technological expertise. The high cost of precision engineering, automation integration, and adherence to international safety and environmental standards poses a challenge for both established and emerging manufacturers. Additionally, many traditional jute-producing regions face infrastructure deficits that can hamper the installation and maintenance of sophisticated processing machinery. The availability of skilled labor, particularly for advanced automation and electronic control systems, remains limited in some key markets, further constraining growth. Moreover, fluctuations in raw jute supply due to climate variability and agricultural practices can impact the equipment market, as consistent demand from jute mills is necessary to justify large-scale machinery upgrades.
At the same time, notable opportunities are arising from increasing global demand for sustainable and biodegradable textiles. Governments and major textile buyers are emphasizing eco-friendly supply chains, leading to renewed investment in modernizing jute processing. Manufacturers that focus on energy-efficient, low-emission machinery and digital process optimization are positioned to benefit as mills seek to reduce operational costs and meet regulatory requirements. Collaborative initiatives between equipment makers and research institutes are fostering innovation in automation, fiber quality enhancement, and waste reduction. For instance, companies like Lakshmi Machine Works and Rieter—while more prominent in cotton machinery—have demonstrated adaptability in textile machinery and could extend expertise into jute processing as market opportunities expand. Additionally, growing export prospects to Africa, Southeast Asia, and Latin America, where modernization of jute industries is underway, offer new revenue streams for established manufacturers.
However, several risk factors must be considered. The sector is exposed to uncertainties in global trade policies, especially those affecting the movement of machinery and parts. Currency volatility and unpredictable costs for steel and electronic components can impact profitability. Intellectual property concerns, particularly in regions with lax enforcement, pose risks for manufacturers investing heavily in R&D. Furthermore, as digitalization and automation become more prevalent, cybersecurity emerges as a new vulnerability, potentially threatening operational continuity and proprietary data. Environmental regulations, while driving demand for cleaner equipment, also necessitate ongoing investment to ensure compliance—posing a continuous cost pressure.
In summary, the 2025 outlook for high-quality jute processing equipment manufacturing is shaped by the tension between substantial entry barriers and compelling opportunities driven by sustainability trends, with risk factors largely tied to market volatility, regulatory shifts, and technological adoption.
Future Outlook: Next-Gen Equipment and Industry 4.0 Integration
The integration of next-generation technologies and Industry 4.0 principles is rapidly transforming the landscape of high-quality jute processing equipment manufacturing as of 2025. Industry leaders are increasingly investing in automation, data-driven solutions, and smart machinery to enhance productivity, product quality, and sustainability throughout the jute supply chain.
A key trend is the adoption of advanced automation and robotics for processes such as carding, spinning, and weaving. Automated systems are designed to deliver consistent output while reducing manual intervention, leading to higher efficiency and minimized defects. Companies such as Lakshmi Machine Works and Rieter—both recognized for their textile machinery portfolios—are actively deploying intelligent automation modules tailored for natural fiber processing, including jute. These advancements help address persistent industry challenges such as labor shortages and the need for precision in yarn quality.
Digitalization is another cornerstone of the sector’s evolution. Smart sensors and IoT-enabled equipment are now being integrated into jute mills, providing real-time monitoring of parameters like moisture, fiber length, and machine health. Such data-driven approaches allow for predictive maintenance, reducing downtime and extending equipment lifespan. Notably, Lakshmi Machine Works has initiated the development of interconnected machinery platforms that enable centralized control and analytics, supporting optimization across entire production lines.
Sustainability considerations are also shaping equipment design. Energy-efficient drives, reduced water usage, and waste minimization features are becoming standard in new machinery models. Leading manufacturers, including Rieter, are integrating eco-friendly components and offering retrofitting solutions to upgrade legacy equipment, aligning with global environmental mandates and customer expectations.
Looking ahead to the next few years, the jute processing equipment sector is expected to deepen its embrace of Industry 4.0. Collaborative robots (cobots), machine learning algorithms for defect detection, and cloud-based production management systems are on the horizon. The continued cross-pollination of expertise between traditional machinery manufacturers and technology solution providers will likely result in highly modular and adaptable equipment, further boosting the competitiveness of jute as a sustainable fiber.
In summary, the future of high-quality jute processing equipment manufacturing is marked by smart automation, digital connectivity, and sustainability. Manufacturers that invest in these next-generation solutions are poised to lead the industry, supporting both operational excellence and the broader global shift toward eco-friendly materials.