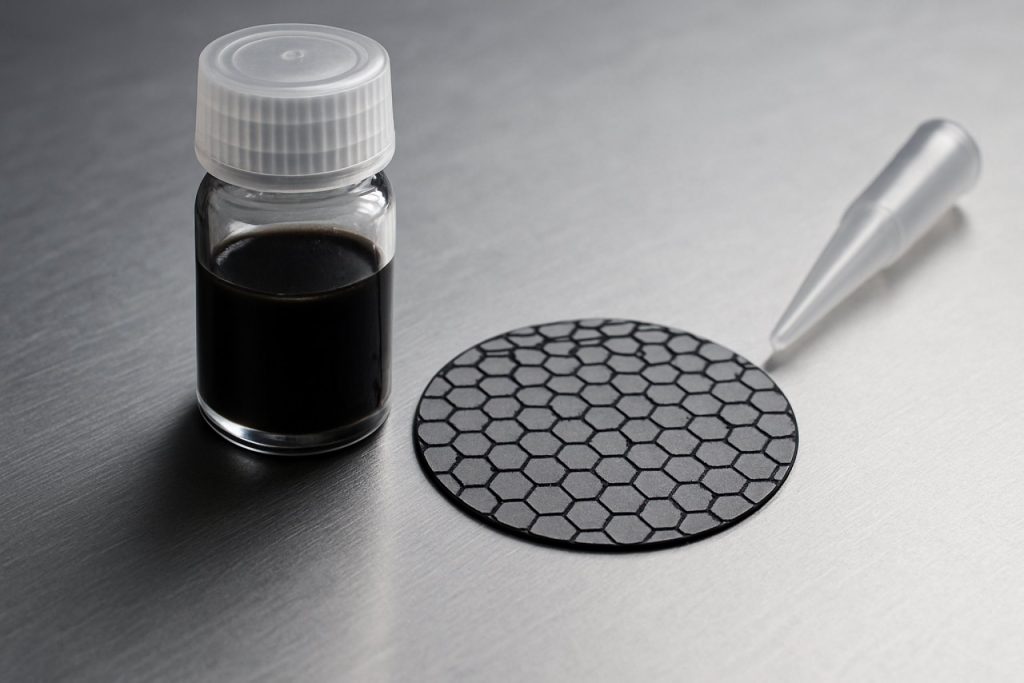
2025 Marks a Turning Point for Rheological Graphene Nanocomposites: How Advanced Engineering Is Reshaping Materials Science and Industry for the Next 5 Years
- Executive Summary: Key Trends in 2025 and Beyond
- Market Size & Forecast: Growth Projections to 2030
- Breakthroughs in Rheological Engineering of Graphene Nanocomposites
- Key Applications Across Industries: Aerospace, Automotive, and Electronics
- Competitive Landscape: Leading Companies and Innovator Profiles
- Regulatory and Quality Standards: 2025 Compliance Requirements
- Supply Chain & Raw Material Dynamics: Graphene Sourcing and Processing
- Challenges and Barriers: Scalability, Cost, and Technical Hurdles
- Emerging Technologies: AI, Automation, and Sustainable Manufacturing
- Future Outlook: Investment Hotspots and Strategic Roadmaps
- Sources & References
Executive Summary: Key Trends in 2025 and Beyond
Rheological graphene nanocomposite engineering is poised for significant transformation in 2025 and beyond, as the sector matures from laboratory-scale innovation to broad industrial adoption. The integration of graphene—a two-dimensional carbon nanomaterial—into polymer, elastomer, and thermoset matrices is driving a wave of new high-performance materials, particularly in automotive, aerospace, energy storage, and advanced manufacturing sectors. In 2025, several key trends are defining the market landscape and technical direction of rheological graphene nanocomposites.
A primary trend is the increased sophistication of graphene dispersion and functionalization techniques, which are crucial for tailoring composite rheological behavior and ensuring uniform property enhancement. Companies such as Directa Plus and Versarien plc are advancing scalable production of high-purity graphene nanoplatelets and inks, enabling more predictable and tunable viscoelastic properties in polymer matrices. These advancements directly impact end-use performance, such as improved processability, enhanced mechanical strength, and superior barrier properties.
Another key trend is the strategic collaboration between nanomaterial producers and major polymer manufacturers. For example, Cabot Corporation has expanded partnerships to supply graphene-enhanced masterbatches and compounds, targeting automotive and consumer electronics applications where flow characteristics and mechanical reinforcement are mission-critical. This reflects a broader industry shift toward vertically integrated supply chains and co-development models to accelerate product qualification and regulatory compliance.
Data from 2025 indicate a marked increase in adoption of graphene-reinforced composites in additive manufacturing (AM) and 3D printing, where rheological control is essential for layer resolution and mechanical fidelity. Companies such as XG Sciences are supplying tailored graphene nanoplatelets for extrusion-based AM processes, supporting the push for lightweight, high-strength components in aerospace and medical sectors. This dovetails with growing demand for sustainable, lower-emission manufacturing enabled by graphene’s ability to reduce material usage while enhancing performance.
Looking ahead, the outlook for rheological graphene nanocomposite engineering remains robust. The next few years will likely see accelerated commercialization as cost structures improve and safety/standardization frameworks mature—an area being addressed by industry groups such as the Graphene Council. Continued R&D investment, alongside regulatory alignment and supply chain integration, will underpin the transition from niche applications to mainstream adoption across multiple industries.
Market Size & Forecast: Growth Projections to 2030
The market for rheological graphene nanocomposite engineering is poised for significant expansion through 2030, driven by escalating demand from sectors such as automotive, aerospace, energy storage, and advanced manufacturing. As of 2025, the global graphene-based nanocomposites market is witnessing increased adoption due to their exceptional mechanical strength, electrical conductivity, and tunable rheological properties, which are critical for next-generation materials and components.
Several leading producers and material innovators are actively scaling up manufacturing capacities and forming strategic partnerships. For instance, Versarien plc—a UK-based advanced materials engineering group—has invested heavily in graphene-enhanced composite materials for automotive and aerospace applications. Similarly, Directa Plus, headquartered in Italy, is expanding its production of graphene nanoplatelets and masterbatches tailored for polymers and elastomers, enabling enhanced rheological performance in end-use products.
Demand is further bolstered by the increasing use of graphene nanocomposites in energy storage and electronics. Companies such as First Graphene Limited in Australia are commercializing high-purity graphene materials designed to improve the processability and performance of thermoplastic and thermoset composites, including those requiring precise rheological control. These advancements are crucial for applications like battery electrodes, lightweight automotive parts, and conductive adhesives.
In Asia, China continues to be a major growth engine, with key players like The Sixth Element (Changzhou) Materials Technology ramping up large-scale production of graphene oxide and functionalized graphene for polymer nanocomposites. This regional momentum is supported by government initiatives promoting advanced materials manufacturing to meet both domestic and export demand.
By 2030, industry forecasts anticipate a compound annual growth rate (CAGR) well above the general composites market, as the unique rheological properties imparted by graphene additives enable the development of lighter, stronger, and more functional end-products. Regulatory agencies and industry groups are also working toward standardization, which will further accelerate market penetration and adoption in critical sectors.
Overall, the outlook for rheological graphene nanocomposite engineering is robust, with innovation cycles shortening and commercialization pathways strengthening. As production costs decrease and supply chains mature, adoption is expected to broaden beyond early adopters to mainstream markets, especially in automotive lightweighting, flexible electronics, and energy systems, consolidating the market’s growth trajectory through the latter half of the decade.
Breakthroughs in Rheological Engineering of Graphene Nanocomposites
The landscape of rheological engineering in graphene nanocomposites is undergoing rapid transformation as the sector enters 2025. Recent breakthroughs stem from both academic and industrial research, focusing on optimizing the dispersion and integration of graphene within various polymer matrices to unlock superior mechanical, thermal, and electrical properties. At the heart of these innovations lies the control of rheological (flow and deformation) behavior to ensure scalability and performance consistency in commercial applications.
A pivotal development has been the tailored surface modification of graphene nanoplatelets, which significantly improves their compatibility with thermoplastic and thermoset resins. This engineering controls the nanofiller distribution, which is critical for achieving desirable viscosity and shear-thinning properties during processing. Companies with deep graphene portfolios—such as Directa Plus and Versarien—are pushing the boundaries in scalable production and customization of graphene nanoplatelets and inks. Their efforts are supported by advanced compounding technologies, enabling precise rheological tuning for automotive, aerospace, and electronics sectors.
- Directa Plus has developed proprietary plasma-based production for high-purity graphene, which is being integrated into elastomers and thermoplastics, yielding composites with improved flow and formability while retaining electrical conductivity.
- Versarien has commercialized graphene-enhanced polymers with controlled viscosity profiles for use in additive manufacturing and coatings, demonstrating repeatable shear responses crucial for 3D printing.
In parallel, the introduction of continuous mixing and in-situ polymerization processes by leading chemical manufacturers—including BASF—has enabled more homogeneous dispersion of graphene at industrial scales. These process advances directly address long-standing challenges of agglomeration and poor interfacial bonding, which historically undermined the mechanical and electrical benefits of graphene nanocomposites.
Recent collaborative projects between manufacturers and end-users are also notable. For instance, SABIC has partnered with automotive OEMs to co-develop graphene-infused thermoplastic grades with optimized rheological properties for lightweight structural components, targeting both improved processability and end-use performance.
Looking ahead, the outlook for 2025 and beyond suggests that rheological engineering will become increasingly data-driven. The adoption of AI-powered modeling and real-time rheometry by companies like Arkema is expected to accelerate the tailoring of nanocomposite formulations for specific manufacturing techniques. With the ongoing expansion of production capacity and cross-sector partnerships, graphene nanocomposites are poised to gain a firmer foothold in high-volume commercial applications, leveraging rheological breakthroughs to meet industry demands for performance, sustainability, and cost-effectiveness.
Key Applications Across Industries: Aerospace, Automotive, and Electronics
Rheological graphene nanocomposite engineering has rapidly transitioned from research laboratories to real-world applications, especially in sectors where advanced material performance is critical. As of 2025 and looking into the next several years, aerospace, automotive, and electronics industries are at the forefront of integrating graphene-enhanced polymer nanocomposites, driven by both performance demands and sustainability goals.
In aerospace, the push for lighter, stronger, and more durable components has intensified interest in graphene nanocomposites. The unique rheological behavior of graphene-infused resins—enabling lower viscosity during processing and enhanced mechanical properties in the cured state—facilitates advanced manufacturing techniques such as resin transfer molding (RTM) and additive manufacturing. Major aerospace suppliers and OEMs have announced collaborative research and pilot projects to exploit these properties for lightweight panels, structural adhesives, and EMI shielding. For example, Airbus continues to explore graphene-based nanocomposites for secondary structural components, seeking both weight reduction and improved electrical conductivity for next-generation aircraft systems.
Within the automotive sector, companies are leveraging rheologically engineered graphene nanocomposites to replace traditional materials in body panels, interiors, and under-hood components. This approach not only reduces vehicle weight—directly impacting fuel efficiency and electric vehicle (EV) range—but also enhances impact resistance and thermal management. Toray Industries, a global leader in advanced composites, has recently expanded production capacity for graphene-enhanced thermoplastics specifically targeting automotive OEMs and Tier 1 suppliers. Additionally, LG Chem has disclosed ongoing development of graphene-polymer blends for high-performance battery casings and thermal interface materials, responding to the demand for safer and more efficient EV batteries.
Electronics manufacturers are increasingly adopting graphene nanocomposites for applications requiring precise rheological control, such as in conductive adhesives, flexible displays, and advanced encapsulants. The ability to finely tune viscosity and flow properties during screen printing or inkjet deposition is crucial for scalable electronics manufacturing. Samsung Electronics has filed multiple patents and announced R&D initiatives around graphene-based inks and pastes for high-frequency, low-resistance interconnects in next-generation devices. Industrial chemical suppliers like BASF are also scaling up production of graphene dispersions tailored for electronic component manufacturing, supporting global supply chains.
Looking forward, the convergence of rheological engineering with scalable graphene production methods is expected to accelerate adoption across these industries. With ongoing investment from both material suppliers and end users, the next few years will likely see commercialization of graphene nanocomposite components in high-volume aerospace, automotive, and electronics applications, as companies increasingly target the dual imperatives of performance enhancement and environmental sustainability.
Competitive Landscape: Leading Companies and Innovator Profiles
The competitive landscape of rheological graphene nanocomposite engineering in 2025 is characterized by a dynamic interplay between established advanced materials companies, specialized nanomaterials manufacturers, and ambitious startups. The sector is witnessing rapid innovation, as stakeholders seek to commercialize graphene-enhanced composites for demanding applications in automotive, aerospace, electronics, and energy storage.
Among the industry leaders, Directa Plus stands out for its scalable production of pristine graphene nanoplatelets and tailor-made graphene-based additives. The company’s G+ technology platform has enabled partnerships with composite manufacturers to optimize the rheological behavior of thermoset and thermoplastic matrices, resulting in improved processability and performance. In 2024 and into 2025, Directa Plus has expanded its collaborations, particularly in the automotive and elastomer sectors, targeting lightweighting and durability enhancements.
Similarly, First Graphene Limited, headquartered in Australia, is leveraging its proprietary electrochemical exfoliation process to deliver high-purity graphene additives. Their PureGRAPH® range is designed for consistent rheological modification in polymer systems, facilitating better dispersion and viscosity control. First Graphene is actively working with polymer compounders and chemical manufacturers to scale up applications in coatings, adhesives, and construction composites.
A notable European innovator, Versarien plc, is deploying its Nanene and graphene-enhanced masterbatches to address the persistent challenge of uniform graphene dispersion in polymer matrices. Versarien’s research collaborations have led to demonstrable improvements in shear-thinning behavior and mechanical reinforcement in both thermoplastics and rubbers, with ongoing pilot projects in the packaging and industrial sectors through 2025.
In North America, XG Sciences continues to be a significant developer of graphene nanoplatelets and customized nanocomposite solutions. Their expertise in rheological engineering supports the manufacture of high-performance thermoset resins, enabling enhanced flow properties and end-use reliability for electronics and energy storage devices.
Emerging players such as Graphenea (Spain) and Avanano (USA) are rapidly advancing dispersion technologies and surface-functionalized graphene products. These companies are focusing on scalable, industrially viable routes for integrating graphene into complex composite formulations, including 3D printing filaments and specialty elastomers.
Looking ahead, the competitive landscape is expected to intensify as companies invest in automated dispersion systems, digital twin modeling for rheology, and circular economy initiatives. Strategic alliances with polymer producers and end-user OEMs will be crucial in moving beyond pilot scale and achieving regulatory acceptance, especially in transportation and infrastructure. The next few years will likely see the emergence of ecosystem partnerships and vertically integrated supply chains as graphene nanocomposites transition from niche to mainstream manufacturing.
Regulatory and Quality Standards: 2025 Compliance Requirements
The rapid evolution of rheological graphene nanocomposite engineering is increasingly intersecting with stringent regulatory and quality standards as global markets mature in 2025. Regulatory bodies and standards organizations are intensifying their frameworks to ensure the safe, reproducible, and high-performance integration of graphene-based nanocomposites, particularly as these materials advance from laboratory to industrial-scale applications.
In 2025, the European Union’s regulatory landscape demands that all graphene nanocomposite materials comply with the Registration, Evaluation, Authorisation and Restriction of Chemicals (REACH) framework. For rheological modifiers and nanofillers, manufacturers must provide detailed risk assessments and demonstrate compliance with chemical safety protocols, including exhaustive toxicological profiling and environmental impact data. The European Chemicals Agency (ECHA) oversees this process, and enforcement actions for non-compliance have increased as graphene adoption accelerates in advanced composites. The EU’s approach is influencing global harmonization efforts, with similar requirements being adopted in other jurisdictions.
In the United States, the Environmental Protection Agency (EPA) regulates graphene and its composites under the Toxic Substances Control Act (TSCA). Companies must submit premanufacture notices (PMNs) for new graphene-based substances and provide comprehensive data on material characteristics, intended uses, and exposure scenarios. Rheological graphene nanocomposites targeting automotive, aerospace, and packaging sectors face additional scrutiny under the Occupational Safety and Health Administration (OSHA) and the Food and Drug Administration (FDA) for workplace and consumer safety.
On the quality standards front, the International Organization for Standardization (ISO) and ASTM International (ASTM International) are publishing new and updated guidelines relevant to graphene nanocomposite specifications, rheological measurement protocols, and quality assurance methods. ISO/TS 21356-1:2021, for instance, outlines characterization protocols for graphene materials, which are now being extended to cover nanocomposite formulations with a focus on dispersion quality and batch-to-batch consistency. Industry leaders such as Graphenea and First Graphene are publicly emphasizing their compliance to these standards, investing in certified production lines and third-party audits to guarantee traceability and reproducibility.
Looking ahead, 2025 and beyond will see a growing convergence of regulatory and quality frameworks. The trend is toward end-to-end supply chain transparency, digital compliance documentation, and real-time quality monitoring, propelled by both customer demands and regulatory mandates. Stakeholders in rheological graphene nanocomposite engineering are expected to invest heavily in compliance infrastructure and to participate in international standardization initiatives to maintain market access and competitive advantage.
Supply Chain & Raw Material Dynamics: Graphene Sourcing and Processing
The supply chain and raw material dynamics for graphene nanocomposite engineering in 2025 are increasingly defined by the interplay between advanced sourcing, scalable processing, and end-use application requirements. Sourcing high-quality graphene—ranging from monolayer to few-layer forms and various oxide derivatives—remains a pivotal challenge but is steadily improving as global suppliers scale up production and refine quality control. Major industry players such as GrapheneCA and First Graphene Limited have reported notable progress in expanding their synthetic and mined graphene output, while emphasizing the importance of consistent dispersion and purity required for rheologically-engineered nanocomposites.
Rheological performance in nanocomposites depends heavily on graphene’s aspect ratio, surface chemistry, and defect density, driving demand for precise structural control during processing. In 2025, commercial suppliers have responded with tailored grades: for example, Directa Plus, headquartered in Italy, offers graphene nanoplatelets with customized surface functionalities for polymer and elastomer matrices, explicitly targeting end-uses in automotive and consumer goods. Their production leverages a patented chemical-free process, minimizing contaminants that can compromise rheological properties.
Geographical diversification of supply chains is also underway, with companies in North America, Europe, and Asia scaling up to meet regional demand surges. Versarien plc (UK) has invested in vertically integrated graphene production, ensuring control from raw graphite sourcing to final dispersion, while Haydale Graphene Industries (UK) focuses on plasma functionalization to enhance compatibility with various nanocomposite matrices. Meanwhile, Asian suppliers such as The Graphene Council report rapid growth in Chinese and South Korean production, supporting a robust electronics and coatings sector.
Processing advancements are increasingly collaborative, involving both material suppliers and downstream manufacturers. For instance, First Graphene Limited has partnered with polymer compounders to optimize mixing and shear protocols, ensuring stable graphene dispersion and predictable viscosity profiles in final composites. These partnerships are vital for the consistent scale-up of rheologically engineered products.
Looking forward, the next few years are expected to see further integration of supply chains, with blockchain-enabled traceability and AI-driven quality control emerging as differentiators. As sustainability pressures mount, companies are investing in greener extraction and processing techniques, aiming to reduce the environmental footprint of graphene nanomaterial production. Overall, the evolving landscape in 2025 and beyond points toward greater supply chain resilience and material specificity, directly supporting the sophisticated demands of rheological graphene nanocomposite engineering.
Challenges and Barriers: Scalability, Cost, and Technical Hurdles
Rheological graphene nanocomposite engineering has garnered significant attention due to its promise in creating advanced materials with superior mechanical, electrical, and thermal properties. However, as the field approaches 2025, several substantial challenges and barriers continue to impact the industrial scalability and commercial viability of these advanced composites.
A primary obstacle remains the scalable and cost-effective production of high-quality graphene. While companies such as Directa Plus, First Graphene, and Versarien have advanced methods for producing graphene materials, consistent quality at the nanoscale and at ton-scale volumes is not yet universally reliable. Variability in flake size, number of layers, and purity can strongly influence the rheological behavior and, subsequently, the performance of nanocomposites. The lack of industry-wide standardization in graphene material characteristics also complicates downstream processing and reproducibility.
Another technical barrier is the efficient dispersion of graphene within polymer or resin matrices. Aggregation of graphene sheets during mixing leads to uneven distribution, resulting in suboptimal rheological and final composite properties. Methods such as solution blending, melt mixing, and in-situ polymerization are continually refined, but industrial-scale consistency remains elusive. Companies like Haydale Graphene Industries and Advanced Graphene Products are developing functionalization techniques to enhance graphene’s compatibility and dispersibility, yet these often introduce additional costs and process complexity.
Cost remains a decisive barrier for broad adoption. While the price per kilogram of graphene has decreased markedly in the past five years, it is still considerably higher than conventional fillers such as carbon black or silica. The economic argument for replacing established materials hinges on demonstrable and significant performance improvements in end-use products. This cost-performance balance is not always favorable in commodity applications, relegating graphene nanocomposites primarily to high-value sectors like aerospace, automotive, and energy storage for the immediate future.
The outlook to 2025 and beyond is for incremental, rather than revolutionary, progress. Expansion of production capacity by key manufacturers, improved standardization efforts (such as those spearheaded by industry bodies like Graphene Flagship), and the development of application-specific, tailored graphene composites will be central to overcoming current barriers. However, until scalable manufacturing and reliable integration techniques are established, the full commercial potential of rheological graphene nanocomposite engineering will remain partially constrained.
Emerging Technologies: AI, Automation, and Sustainable Manufacturing
Rheological graphene nanocomposite engineering is undergoing rapid evolution as advanced technologies like artificial intelligence (AI), automation, and sustainable manufacturing practices reshape the field in 2025 and beyond. The integration of AI-driven modeling and real-time analytics is enabling unprecedented control over the complex rheological behaviors of graphene-based polymer nanocomposites. This is particularly vital for industries seeking to tailor mechanical, electrical, and thermal properties at scale, while minimizing waste and energy consumption.
One notable trend is the deployment of AI algorithms for predictive rheology, where machine learning models analyze vast datasets from extrusion, injection molding, and 3D printing processes to optimize nanoparticle dispersion and polymer-filler interactions. Companies such as BASF and SABIC are actively investing in digital platforms that use AI to accelerate the discovery of new nanocomposite formulations and process parameters, aiming for both performance and sustainability. These systems enhance process consistency and product quality by adapting in real-time to variations in raw materials or environmental conditions.
Automation is also streamlining the scale-up and manufacturing of graphene nanocomposites. Robotic handling and in-line rheometers now allow continuous monitoring and precise control over viscosity, shear thinning, and other critical flow properties during production. Arkema is a pioneer in integrating automated compounding lines for advanced composites, ensuring uniform graphene distribution and reducing batch-to-batch variability. Meanwhile, manufacturers like Directa Plus specialize in automated production of pristine graphene nanoplatelets, feeding the growing demand from automotive, aerospace, and energy storage sectors.
Sustainable manufacturing is increasingly at the forefront, with a focus on reducing the environmental impact of nanocomposite production. Industry leaders are incorporating bio-based or recycled polymers as matrices and employing closed-loop water and solvent systems to minimize waste. Novamont is developing bio-based nanocomposites with improved rheological performance, targeting biodegradable packaging and eco-friendly engineering plastics. Life cycle assessments and green chemistry approaches are becoming standard practice, as regulatory and market pressures intensify.
Looking ahead, the convergence of AI, automation, and sustainability is set to accelerate the commercialization of rheologically engineered graphene nanocomposites. The coming years will likely see broader adoption of digital twins and autonomous process control, further reducing development time and environmental footprint. As standards evolve and more scalable, cost-effective technologies emerge, graphene nanocomposites will play a pivotal role in next-generation manufacturing solutions across multiple high-tech sectors.
Future Outlook: Investment Hotspots and Strategic Roadmaps
The future landscape of rheological graphene nanocomposite engineering is characterized by accelerating industrial investment, heightened cross-sector collaboration, and the emergence of dedicated manufacturing hubs. As the global appetite for advanced composite materials intensifies, several regions and companies are positioning themselves at the forefront, focusing on scalable production, process innovation, and commercialization strategies for graphene-enhanced rheological systems.
A notable hotspot is the European Union, where coordinated initiatives like the Graphene Flagship are channeling substantial resources into developing graphene supply chains and application-specific nanocomposites. These efforts are fostering partnerships between research institutions and industrial stakeholders to optimize rheological properties for automotive, aerospace, and energy storage sectors. Additionally, the EU’s emphasis on sustainability and circularity is prompting companies to explore bio-based polymer matrices and recyclable graphene composites, a trend expected to gain momentum through 2025 and beyond.
In North America, leading graphene manufacturers such as Versarien and First Graphene are scaling up production of graphene nanoplatelets and dispersions tailored for rheological modification in polymer and rubber compounds. These firms are investing in process control technologies to ensure reproducibility and performance consistency, thereby addressing a critical barrier to widespread adoption. Simultaneously, partnerships with automotive manufacturers and chemical companies are accelerating the integration of rheological graphene nanocomposites into real-world products, particularly in lightweighting and heat management applications.
Asia-Pacific is emerging as both a manufacturing and consumption powerhouse. Companies like Directa Plus (with significant operations in Europe and Asia) and Haydale Graphene Industries are actively expanding their presence, targeting markets in China, South Korea, and Japan. These regions benefit from robust electronics, coatings, and battery industries, which are increasingly demanding rheologically optimized nanocomposites for better performance and manufacturability.
Looking ahead to 2025 and the subsequent years, strategic roadmaps will likely focus on further reducing the cost of graphene nanomaterials, developing universal dispersion technologies, and creating open innovation platforms to accelerate testing and certification. Regulatory clarity and standards development, spearheaded by organizations such as the Graphene Flagship and national materials institutes, will play a decisive role in unlocking new investment and commercial pathways.
In summary, rheological graphene nanocomposite engineering is poised for significant expansion, with investment hotspots in Europe, North America, and Asia-Pacific. The sector’s strategic trajectory points toward scalable, cost-effective production, cross-industry alliances, and a strong focus on application-driven development—setting the stage for widespread market penetration in the near future.