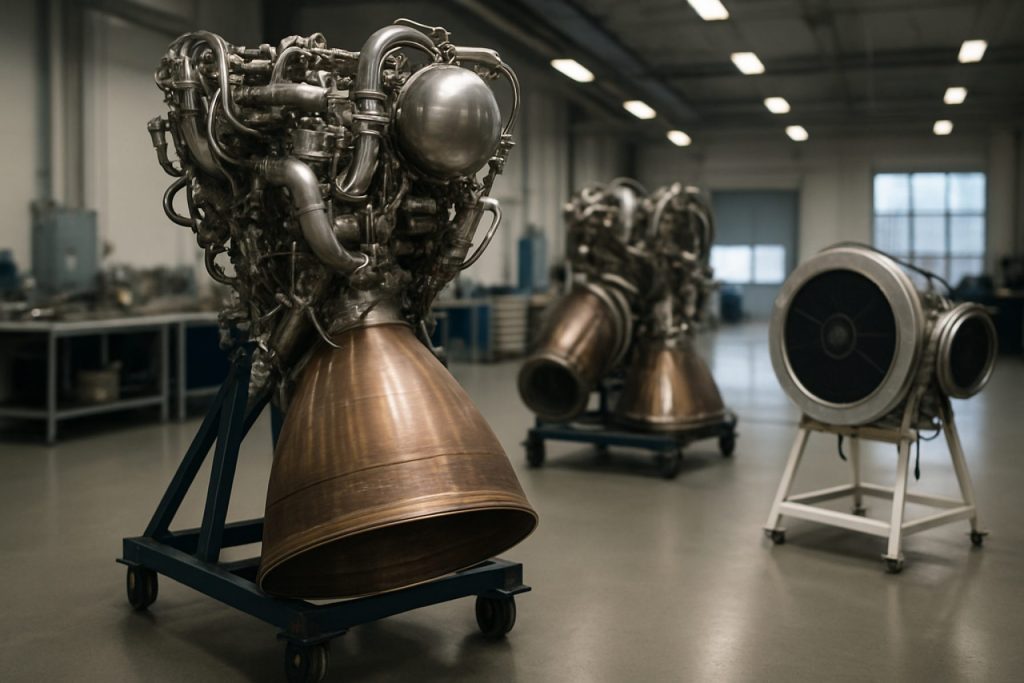
Spacecraft Propulsion Components Engineering in 2025: Unveiling the Technologies and Market Forces Shaping the Future of Space Exploration. Discover How Advanced Engineering is Accelerating the Next Era of Propulsion Innovation.
- Executive Summary: Key Trends and Market Drivers in 2025
- Global Market Forecast: Growth Projections Through 2030
- Propulsion Component Technologies: State of the Art and Emerging Innovations
- Major Players and Strategic Partnerships (e.g., aerojetrocketdyne.com, spacex.com, nasa.gov)
- Materials Science and Manufacturing Advances in Propulsion Components
- Regulatory Landscape and Industry Standards (e.g., nasa.gov, esa.int, ieee.org)
- Supply Chain Dynamics and Critical Component Sourcing
- Applications: Commercial, Government, and Defense Spacecraft
- Challenges and Opportunities: Sustainability, Cost, and Performance
- Future Outlook: Disruptive Technologies and Long-Term Market Evolution
- Sources & References
Executive Summary: Key Trends and Market Drivers in 2025
The field of spacecraft propulsion components engineering is undergoing rapid transformation in 2025, driven by the convergence of commercial space expansion, government investments, and technological breakthroughs. The demand for advanced propulsion systems is intensifying as satellite constellations, lunar missions, and deep space exploration projects proliferate. Key trends shaping the sector include the miniaturization of propulsion components, the adoption of electric and green propulsion technologies, and the emergence of new manufacturing techniques such as additive manufacturing.
A significant driver is the surge in small satellite launches, with companies like Aerojet Rocketdyne and Northrop Grumman supplying propulsion modules tailored for CubeSats and microsatellites. These systems demand compact, efficient thrusters and valves, spurring innovation in micro-propulsion and integrated component design. Meanwhile, the push for sustainable space operations is accelerating the shift toward non-toxic propellants and electric propulsion. ArianeGroup and OHB SE are advancing green propulsion solutions, while European Space Agency programs are supporting the qualification of new thruster technologies for both commercial and scientific missions.
Electric propulsion, particularly Hall-effect and ion thrusters, is gaining traction for its high efficiency and suitability for long-duration missions. Airbus and Thales are leading the integration of electric propulsion modules into geostationary and low Earth orbit satellites, with ongoing developments in power processing units, cathodes, and propellant management systems. The adoption of additive manufacturing is also reshaping component engineering, enabling rapid prototyping and the production of complex geometries that enhance performance and reduce mass. Lockheed Martin and Rocket Lab are actively incorporating 3D-printed propulsion components in their spacecraft and launch vehicles.
Looking ahead, the market outlook for spacecraft propulsion components remains robust. The Artemis program and commercial lunar landers are driving demand for high-thrust engines and precision attitude control systems. Meanwhile, the proliferation of mega-constellations and interplanetary missions is expected to sustain investment in both chemical and electric propulsion technologies. As regulatory and environmental pressures mount, the industry is poised to accelerate the adoption of green propellants and recyclable materials, ensuring that propulsion component engineering remains at the forefront of space innovation through the remainder of the decade.
Global Market Forecast: Growth Projections Through 2030
The global market for spacecraft propulsion components engineering is poised for robust growth through 2030, driven by surging demand for satellite constellations, deep space exploration, and commercial spaceflight. As of 2025, the sector is experiencing a significant uptick in both public and private investment, with established aerospace giants and innovative startups expanding their propulsion portfolios to meet evolving mission requirements.
Key propulsion component manufacturers such as ArianeGroup, Northrop Grumman, and Rocket Lab are scaling up production of advanced thrusters, valves, turbopumps, and propellant management systems. ArianeGroup continues to refine its Vinci and Vulcain engines for the Ariane 6 launch vehicle, while Northrop Grumman is advancing solid and hybrid propulsion components for both government and commercial missions. Meanwhile, Rocket Lab is expanding its Rutherford and Curie engine lines, with a focus on 3D-printed components and electric pump-fed designs.
The market outlook is further buoyed by the rapid adoption of electric propulsion systems, particularly Hall-effect and ion thrusters, for satellite station-keeping and interplanetary missions. Airbus and Thales are leading suppliers of electric propulsion modules, integrating high-efficiency thrusters and power processing units into next-generation spacecraft. Airbus’s EOR (Electric Orbit Raising) technology is now standard on many commercial satellites, while Thales is delivering advanced plasma propulsion systems for both geostationary and low Earth orbit applications.
Emerging players such as Impulse Space and Phase Four are introducing novel propulsion architectures, including modular chemical thrusters and radio-frequency plasma engines, targeting the burgeoning small satellite and in-space mobility markets. These innovations are expected to drive component miniaturization, cost reduction, and increased mission flexibility over the next five years.
Looking ahead, the propulsion components engineering market is forecast to grow at a healthy pace through 2030, underpinned by mega-constellation deployments, lunar and Mars exploration initiatives, and the rise of in-orbit servicing. The sector’s trajectory will be shaped by continued advancements in materials science, additive manufacturing, and digital engineering, as well as by the expanding role of commercial suppliers in global supply chains. As propulsion technologies diversify and mature, the market is set to remain a cornerstone of the broader space industry’s expansion.
Propulsion Component Technologies: State of the Art and Emerging Innovations
Spacecraft propulsion component engineering is experiencing rapid innovation as the industry responds to the demands of commercial satellite constellations, deep space exploration, and responsive launch services. In 2025, the state of the art is defined by a blend of mature chemical propulsion systems and a surge in electric propulsion adoption, with significant advances in component miniaturization, efficiency, and manufacturability.
Chemical propulsion remains foundational for launch vehicles and high-thrust maneuvers. Leading manufacturers such as ArianeGroup and Northrop Grumman continue to refine turbopumps, injectors, and combustion chambers for both cryogenic and storable propellants. Innovations include additive manufacturing of engine components, which reduces part count and enables complex cooling channels, as demonstrated in the Vinci and Vulcain engines. Meanwhile, Rocket Lab has pioneered electric pump-fed engines, exemplified by their Rutherford engine, which uses battery-powered turbopumps to simplify design and improve responsiveness.
Electric propulsion is now central to satellite station-keeping, orbit raising, and deep space missions. Hall-effect thrusters, ion engines, and new gridded ion thrusters are being produced at scale by companies like Airbus and Thales. These systems rely on advanced cathodes, power processing units, and propellant feed systems, with ongoing improvements in lifetime and thrust-to-power ratios. In 2025, European Space Agency missions are deploying next-generation electric propulsion modules with enhanced thermal management and digital control electronics, supporting more flexible mission profiles.
Emerging innovations include green propellant systems, such as those using hydroxylammonium nitrate (HAN) or ammonium dinitramide (ADN), which offer higher performance and safer handling compared to hydrazine. Moog and Eni are among the suppliers developing valves, tanks, and feed systems compatible with these new propellants. Additionally, micro-propulsion components for CubeSats and small satellites—such as MEMS-based thrusters and miniaturized valves—are being commercialized by firms like Northrop Grumman and Airbus.
Looking ahead, the next few years will see further integration of digital manufacturing, advanced materials (including ceramics and composites), and autonomous health monitoring in propulsion components. The push for reusable spacecraft and lunar missions is driving demand for components with longer lifetimes, higher cycle counts, and in-situ resource compatibility. As the sector evolves, collaboration between established aerospace primes and agile new entrants will accelerate the pace of propulsion component innovation.
Major Players and Strategic Partnerships (e.g., aerojetrocketdyne.com, spacex.com, nasa.gov)
The landscape of spacecraft propulsion components engineering in 2025 is shaped by a dynamic interplay of established aerospace giants, innovative private companies, and strategic partnerships that drive technological advancement and market expansion. Key players such as Aerojet Rocketdyne, SpaceX, NASA, and Northrop Grumman continue to lead the sector, while new entrants and international collaborations are increasingly influential.
Aerojet Rocketdyne remains a cornerstone in propulsion component engineering, supplying engines and thrusters for both government and commercial missions. Their RL10 and RS-25 engines are integral to NASA’s Artemis program, and the company is actively developing advanced electric and chemical propulsion systems for deep space and satellite applications. In 2024, Aerojet Rocketdyne was acquired by L3Harris Technologies, a move expected to bolster its R&D capabilities and expand its market reach through integrated defense and space solutions.
SpaceX continues to disrupt the propulsion sector with its vertically integrated approach. The company’s Raptor engines, which power the Starship vehicle, utilize full-flow staged combustion and methane fuel, setting new benchmarks for reusability and performance. SpaceX’s in-house development of nearly all propulsion components, from turbopumps to injectors, enables rapid iteration and cost control. The company’s ongoing partnerships with NASA and commercial satellite operators further cement its influence in propulsion engineering.
NASA plays a pivotal role as both a customer and collaborator, funding propulsion research and fostering public-private partnerships. Through programs like NextSTEP and the Artemis initiative, NASA supports the development of advanced propulsion technologies, including solar electric propulsion and nuclear thermal propulsion, in collaboration with industry leaders and academic institutions.
Northrop Grumman is another major player, providing solid rocket motors, attitude control systems, and propulsion subsystems for launch vehicles and spacecraft. The company’s acquisition of Orbital ATK has strengthened its position in both commercial and defense propulsion markets.
Strategic partnerships are increasingly central to propulsion component innovation. For example, Airbus and Safran have formed joint ventures to develop next-generation electric propulsion for satellites. Meanwhile, ArianeGroup collaborates with European agencies and suppliers to advance reusable engine technologies for the Ariane 6 and future launchers.
Looking ahead, the propulsion components sector is expected to see intensified collaboration between traditional aerospace firms, agile startups, and government agencies. The focus will be on higher efficiency, reusability, and sustainability, with electric and hybrid propulsion systems gaining traction for both orbital and deep space missions.
Materials Science and Manufacturing Advances in Propulsion Components
The engineering of spacecraft propulsion components is undergoing rapid transformation, driven by advances in materials science and manufacturing techniques. In 2025 and the coming years, the focus is on enhancing performance, reliability, and cost-effectiveness for both chemical and electric propulsion systems. Key developments are centered around high-temperature materials, additive manufacturing, and novel composites, all of which are critical for next-generation thrusters, nozzles, valves, and structural elements.
One of the most significant trends is the adoption of advanced ceramics and refractory metal alloys for components exposed to extreme thermal and mechanical stresses. For example, Aerojet Rocketdyne and Northrop Grumman are actively developing propulsion hardware using niobium, molybdenum, and carbon-carbon composites, which offer superior heat resistance and durability for deep-space missions. These materials are particularly important for electric propulsion systems, such as Hall-effect and ion thrusters, where long operational lifetimes are essential.
Additive manufacturing (AM), or 3D printing, is revolutionizing the production of propulsion components by enabling complex geometries, reducing part counts, and shortening development cycles. SpaceX has pioneered the use of AM for engine parts, including SuperDraco thrusters, and continues to expand its in-house capabilities for both chemical and electric propulsion. Similarly, ArianeGroup and Blue Origin are leveraging AM to produce intricate injector heads, combustion chambers, and nozzle extensions, resulting in lighter and more efficient engines.
Composite materials, particularly carbon fiber-reinforced polymers, are increasingly used for structural components and propellant tanks. These materials offer high strength-to-weight ratios and corrosion resistance, which are vital for both launch vehicles and in-space propulsion modules. Thales Group and Lockheed Martin are among the leaders in integrating advanced composites into propulsion subsystems, supporting the trend toward reusable and modular spacecraft architectures.
Looking ahead, the industry is expected to further integrate smart materials and sensor-embedded components for real-time health monitoring and adaptive performance. The continued collaboration between propulsion manufacturers, materials suppliers, and research institutions will likely yield breakthroughs in ultra-high-temperature ceramics and multifunctional composites, setting new benchmarks for efficiency and mission longevity. As commercial and governmental missions push toward lunar, Martian, and deep-space destinations, the demand for robust, high-performance propulsion components will only intensify, driving ongoing innovation in materials science and manufacturing processes.
Regulatory Landscape and Industry Standards (e.g., nasa.gov, esa.int, ieee.org)
The regulatory landscape and industry standards for spacecraft propulsion components engineering are rapidly evolving as the sector experiences increased activity from both governmental and commercial actors. In 2025, the primary regulatory authorities remain the national and international space agencies, with the National Aeronautics and Space Administration (NASA) and the European Space Agency (ESA) at the forefront of setting technical and safety standards for propulsion systems. These agencies issue detailed requirements for component reliability, contamination control, and performance verification, which are mandatory for missions they sponsor or certify.
NASA’s standards, such as those outlined in NASA-STD-5019 for structural design and NASA-STD-7001 for payload safety, are frequently referenced by both U.S. and international manufacturers. In 2025, NASA continues to update its propulsion component guidelines to address new technologies, including electric and green propellants, reflecting the agency’s commitment to sustainability and mission safety. The agency’s Office of Safety and Mission Assurance is actively collaborating with industry to harmonize standards for emerging propulsion technologies, such as Hall-effect thrusters and non-toxic propellants, which are increasingly used in commercial and lunar missions.
ESA, meanwhile, maintains its own set of standards under the ECSS (European Cooperation for Space Standardization) framework, which covers the full lifecycle of propulsion components—from design and materials selection to testing and qualification. In 2025, ESA is placing particular emphasis on harmonizing standards for electric propulsion and additive manufacturing of propulsion parts, in response to the growing adoption of these technologies in European and international missions. The agency is also working with member states to ensure that propulsion components meet both performance and environmental requirements, especially as Europe prepares for more frequent lunar and deep-space missions.
Industry standards bodies such as the Institute of Electrical and Electronics Engineers (IEEE) and the SAE International are increasingly influential in the propulsion sector. IEEE, for example, is developing standards for the electrical interfaces and control systems of electric propulsion units, while SAE International continues to update its aerospace material and testing standards to reflect the latest advances in propulsion engineering.
Looking ahead, the regulatory environment is expected to become more complex as private companies like Space Exploration Technologies Corp. (SpaceX), Blue Origin, and Aerojet Rocketdyne expand their propulsion portfolios and international collaboration increases. Agencies and standards bodies are anticipated to further streamline certification processes and develop new guidelines for reusable and modular propulsion components, supporting the next generation of commercial and scientific space missions.
Supply Chain Dynamics and Critical Component Sourcing
The supply chain for spacecraft propulsion components is undergoing significant transformation in 2025, driven by the rapid expansion of commercial space activities, increased demand for high-performance propulsion systems, and ongoing geopolitical uncertainties. The propulsion sector relies on a complex network of suppliers for critical components such as thrusters, valves, turbopumps, propellant tanks, and advanced materials. Key players in this ecosystem include established aerospace manufacturers, specialized component suppliers, and emerging startups, each contributing to the resilience and innovation of the supply chain.
Major propulsion system integrators such as ArianeGroup, Northrop Grumman, and Rocket Lab continue to vertically integrate their supply chains, investing in in-house manufacturing capabilities for critical components like engines and turbopumps. This trend is partly a response to recent global supply chain disruptions and the need for greater control over quality and lead times. For example, SpaceX has expanded its in-house production of Raptor engines and related subsystems, reducing reliance on external suppliers and streamlining development cycles.
At the same time, the propulsion components market is seeing increased participation from specialized suppliers. Companies such as Moog Inc. and Aerojet Rocketdyne provide critical valves, actuators, and thrusters for both chemical and electric propulsion systems. The growing adoption of electric propulsion, particularly Hall-effect and ion thrusters, has led to new sourcing challenges for components like high-voltage power processing units and rare-earth magnets. Suppliers are investing in advanced manufacturing techniques, such as additive manufacturing, to address these challenges and improve component performance and availability.
Material sourcing remains a critical concern, especially for high-temperature alloys, carbon composites, and rare materials like niobium and hafnium used in thruster nozzles and combustion chambers. The propulsion sector is closely monitoring geopolitical developments that could impact the availability of these materials, with some companies seeking to diversify their supplier base or develop alternative materials. For instance, Thales Group and OHB SE are actively exploring partnerships with new material suppliers to mitigate risks.
Looking ahead, the outlook for spacecraft propulsion component sourcing in the next few years is shaped by continued investment in supply chain resilience, increased adoption of digital supply chain management tools, and a focus on sustainability. As launch rates rise and new mission profiles emerge, the ability to secure reliable, high-quality propulsion components will remain a key differentiator for both established and emerging space companies.
Applications: Commercial, Government, and Defense Spacecraft
Spacecraft propulsion components engineering is a critical enabler for a wide range of applications across commercial, government, and defense spacecraft sectors. As of 2025, the industry is witnessing rapid advancements in propulsion technologies, driven by the need for higher efficiency, reliability, and mission flexibility. These developments are directly impacting satellite constellations, deep space exploration, and responsive defense missions.
In the commercial sector, the proliferation of large low Earth orbit (LEO) satellite constellations for broadband internet and Earth observation is fueling demand for advanced propulsion components. Companies such as ArianeGroup and OHB SE are actively developing and supplying chemical and electric propulsion systems tailored for small satellites and mega-constellations. Electric propulsion, particularly Hall-effect and gridded ion thrusters, is increasingly favored for its high efficiency and ability to extend satellite operational lifetimes, as seen in the adoption by commercial operators and manufacturers.
Government space agencies are also investing in next-generation propulsion components to support ambitious science and exploration missions. For example, NASA continues to advance solar electric propulsion (SEP) technologies for deep space missions, with ongoing component development and qualification for projects like the upcoming Gateway lunar outpost. Similarly, the European Space Agency (ESA) is collaborating with industry partners to mature electric and green chemical propulsion systems, aiming to reduce environmental impact and enhance performance for both science and Earth observation missions.
In the defense domain, propulsion components engineering is focused on rapid maneuverability, resilience, and in-orbit servicing capabilities. Companies such as Northrop Grumman and Aerojet Rocketdyne (now part of L3Harris) are supplying propulsion modules for national security satellites, emphasizing robust thruster designs and redundancy. The U.S. Space Force and allied defense organizations are increasingly specifying advanced propulsion components to enable agile satellite repositioning and counterspace operations.
Looking ahead to the next few years, the outlook for spacecraft propulsion components engineering is shaped by miniaturization, modularity, and the integration of digital manufacturing techniques. The emergence of new entrants, such as Accellercom and ThrustMe, is accelerating innovation in electric and alternative propulsion components, particularly for small satellites and cubesats. As commercial, government, and defense missions grow in complexity and scale, the demand for high-performance, reliable, and cost-effective propulsion components is expected to intensify, driving further collaboration between established aerospace primes and agile startups.
Challenges and Opportunities: Sustainability, Cost, and Performance
Spacecraft propulsion components engineering is at a pivotal juncture in 2025, as the sector faces mounting challenges and emerging opportunities related to sustainability, cost, and performance. The increasing cadence of commercial and governmental space missions, including lunar and Mars exploration, has intensified the demand for propulsion systems that are not only high-performing but also cost-effective and environmentally responsible.
One of the foremost challenges is the environmental impact of traditional chemical propulsion systems, which often rely on toxic propellants such as hydrazine. Regulatory pressures and sustainability goals are driving the industry to develop and qualify “green” propellants and associated components. Companies like Aerojet Rocketdyne and Northrop Grumman are actively advancing alternative propellants, such as AF-M315E and LMP-103S, which offer reduced toxicity and improved performance. These new propellants require re-engineering of valves, tanks, and feed systems to ensure compatibility and reliability, presenting both technical and supply chain challenges.
Cost reduction remains a central focus, especially as satellite constellations and small satellite launches proliferate. The adoption of additive manufacturing (AM) for propulsion components—such as thruster chambers, injectors, and turbopump parts—has accelerated, with companies like ArianeGroup and Rocket Lab integrating AM to streamline production and reduce lead times. This shift not only lowers costs but also enables rapid prototyping and design iteration, crucial for meeting the evolving needs of commercial customers.
Performance improvements are being pursued through the development of electric propulsion systems, which offer higher specific impulse and longer operational lifetimes compared to chemical systems. Airbus and Thales are leading the deployment of Hall-effect and ion thrusters for both geostationary and deep space missions. These systems demand highly reliable power processing units, advanced cathodes, and erosion-resistant materials, driving innovation in component engineering.
Looking ahead, the integration of digital engineering tools and in-space servicing capabilities presents new opportunities. Digital twins and advanced simulation platforms are enabling more precise modeling of component behavior under extreme conditions, reducing the risk of failure and optimizing performance. Meanwhile, the prospect of in-orbit refueling and component replacement, championed by organizations like NASA, could extend spacecraft lifespans and further shift the paradigm toward sustainable, modular propulsion architectures.
In summary, the next few years will see propulsion component engineering balancing the imperatives of sustainability, cost, and performance, with innovation in materials, manufacturing, and digitalization shaping the future of space mobility.
Future Outlook: Disruptive Technologies and Long-Term Market Evolution
The future of spacecraft propulsion components engineering is poised for significant transformation as disruptive technologies mature and new market entrants accelerate innovation. By 2025 and into the late 2020s, the propulsion landscape is expected to shift from traditional chemical systems toward advanced electric, hybrid, and even nuclear-based solutions, driven by the demands of deep space exploration, satellite mega-constellations, and commercial lunar missions.
Electric propulsion, particularly Hall-effect and ion thrusters, is rapidly gaining traction for both commercial and governmental missions. Companies such as ArianeGroup and Airbus are investing heavily in next-generation electric propulsion systems, aiming to improve efficiency and reduce mass for geostationary and interplanetary spacecraft. Northrop Grumman and Thales are also advancing their electric propulsion portfolios, with a focus on modularity and scalability to serve a broad range of satellite platforms.
Meanwhile, the push for lunar and Mars missions is catalyzing interest in nuclear thermal and nuclear electric propulsion. Lockheed Martin and BWX Technologies are collaborating on nuclear thermal propulsion demonstrators, with test flights anticipated in the late 2020s. These systems promise higher thrust and efficiency for deep space missions, potentially reducing transit times to Mars by several months.
Additive manufacturing (AM) is another disruptive force, enabling rapid prototyping and production of complex propulsion components with reduced lead times and costs. Relativity Space is pioneering fully 3D-printed rocket engines, while Rocket Lab and SpaceX are integrating AM into their engine production lines to enhance performance and reliability.
Looking ahead, the market is expected to see increased adoption of green propellants, such as those developed by ECAPS and Ampcera, which offer improved safety and environmental profiles compared to hydrazine-based systems. The proliferation of small satellites and in-orbit servicing missions will further drive demand for miniaturized, high-efficiency propulsion components.
In summary, the next few years will witness a convergence of advanced propulsion technologies, digital manufacturing, and sustainable propellants, fundamentally reshaping spacecraft propulsion components engineering. This evolution will enable more ambitious missions, lower costs, and greater flexibility for both established aerospace leaders and agile new entrants.
Sources & References
- Northrop Grumman
- OHB SE
- European Space Agency
- Airbus
- Thales
- Lockheed Martin
- Rocket Lab
- ArianeGroup
- Phase Four
- Moog
- NASA
- L3Harris Technologies
- Northrop Grumman
- ArianeGroup
- Blue Origin
- Thales Group
- Lockheed Martin
- National Aeronautics and Space Administration (NASA)
- European Space Agency (ESA)
- Institute of Electrical and Electronics Engineers (IEEE)
- ThrustMe
- Ampcera