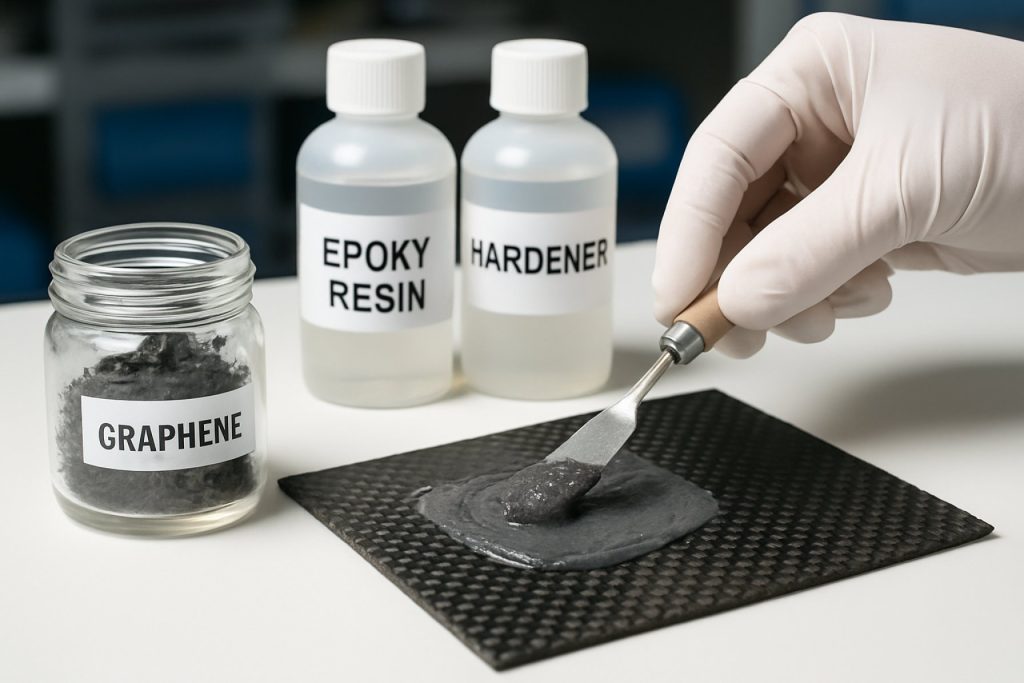
Graphene-Based Epoxy Nanocomposite Manufacturing in 2025: Unleashing Next-Gen Performance and Market Expansion. Explore How Advanced Materials Are Reshaping Industrial Applications and Driving 30%+ CAGR Through 2030.
- Executive Summary: 2025 Market Snapshot & Key Drivers
- Technology Overview: Graphene-Epoxy Nanocomposite Fundamentals
- Manufacturing Innovations: Process Advances and Scale-Up Challenges
- Key Players & Industry Ecosystem (e.g., grapheneplatform.com, haydale.com, graphene-info.com)
- Market Size, Segmentation & 2025–2030 Growth Forecasts
- Application Landscape: Aerospace, Automotive, Electronics, and Beyond
- Competitive Analysis: Differentiators and Strategic Positioning
- Regulatory Environment & Industry Standards (e.g., graphene-flagship.eu, ieee.org)
- Investment Trends, Partnerships, and M&A Activity
- Future Outlook: Disruptive Opportunities and Long-Term Impact
- Sources & References
Executive Summary: 2025 Market Snapshot & Key Drivers
The global market for graphene-based epoxy nanocomposite manufacturing is poised for significant growth in 2025, driven by escalating demand for advanced materials in sectors such as aerospace, automotive, electronics, and renewable energy. Graphene’s exceptional mechanical, thermal, and electrical properties, when integrated into epoxy matrices, are enabling the development of composites with superior strength-to-weight ratios, enhanced conductivity, and improved durability compared to conventional materials.
Key industry players are scaling up production capacities and refining dispersion techniques to address challenges related to uniform graphene distribution and cost-effective mass manufacturing. Companies such as Directa Plus, a leading European graphene producer, and First Graphene in Australia, are actively supplying graphene nanoplatelets and powders tailored for epoxy composite applications. These firms are collaborating with epoxy resin manufacturers and end-users to optimize formulations for specific industrial requirements.
In 2025, the automotive sector remains a primary adopter, leveraging graphene-epoxy nanocomposites for lightweight structural components, improved corrosion resistance, and enhanced electrical properties for battery enclosures and electronic modules. The aerospace industry is also advancing the integration of these materials to achieve weight reduction and increased fuel efficiency, with companies like Haydale Graphene Industries providing functionalized graphene additives for high-performance epoxy systems.
Recent data from industry sources indicate that the adoption of graphene-based epoxy nanocomposites is accelerating, with pilot-scale and commercial-scale projects underway across Europe, Asia, and North America. For example, Graphenea and Versarien are expanding their graphene material portfolios and establishing partnerships with composite manufacturers to facilitate broader market penetration.
Key drivers for market expansion in 2025 include ongoing improvements in graphene production scalability, cost reduction strategies, and the development of standardized quality metrics for nanomaterial-enhanced epoxies. Regulatory support for lightweight, energy-efficient materials in transportation and infrastructure is further catalyzing demand. Looking ahead, the next few years are expected to witness increased commercialization, with a focus on sustainable manufacturing practices and the integration of graphene-epoxy nanocomposites into emerging applications such as wind turbine blades, smart coatings, and advanced electronics.
Overall, the 2025 market snapshot reveals a dynamic landscape characterized by technological innovation, strategic collaborations, and a clear trajectory toward mainstream adoption of graphene-based epoxy nanocomposites across multiple high-value industries.
Technology Overview: Graphene-Epoxy Nanocomposite Fundamentals
Graphene-based epoxy nanocomposites represent a rapidly advancing segment within advanced materials manufacturing, driven by the exceptional mechanical, thermal, and electrical properties imparted by graphene to traditional epoxy matrices. As of 2025, the manufacturing landscape is characterized by both incremental process improvements and the scaling up of production capabilities, with a focus on achieving uniform graphene dispersion, cost-effective processing, and reliable property enhancement.
The fundamental challenge in manufacturing these nanocomposites lies in the homogeneous integration of graphene—whether as pristine graphene, graphene oxide (GO), or reduced graphene oxide (rGO)—into the epoxy resin. Techniques such as solution mixing, in-situ polymerization, and high-shear mixing are widely adopted, with ongoing optimization to prevent agglomeration and maximize interfacial bonding. Recent years have seen the increased use of functionalized graphene derivatives, which improve compatibility with epoxy matrices and facilitate scalable processing.
Key industry players are actively commercializing graphene-epoxy systems. Directa Plus, a leading European graphene producer, supplies graphene nanoplatelets and masterbatches tailored for epoxy resin enhancement, targeting applications in coatings, composites, and electronics. Versarien has developed proprietary processes for incorporating graphene into thermoset resins, with a focus on automotive and aerospace sectors. In North America, XG Sciences offers graphene nanoplatelets and dispersions specifically engineered for epoxy nanocomposite manufacturing, supporting both pilot and commercial-scale production.
Manufacturing advances in 2025 are increasingly focused on process automation and quality control. Inline monitoring technologies, such as rheological sensors and spectroscopic analysis, are being integrated to ensure consistent graphene dispersion and batch-to-batch reproducibility. Additionally, companies are investing in upscaling production lines to meet growing demand from sectors such as wind energy, automotive lightweighting, and high-performance electronics.
Sustainability and regulatory compliance are also shaping manufacturing strategies. Producers are exploring greener synthesis routes for graphene, including electrochemical exfoliation and biomass-derived precursors, to reduce environmental impact. Furthermore, the use of water-based dispersions and solvent-free processing is gaining traction, aligning with evolving industry standards and customer requirements.
Looking ahead, the next few years are expected to bring further integration of graphene-epoxy nanocomposites into mainstream manufacturing, supported by ongoing collaboration between material suppliers, end-users, and industry consortia. As production costs decrease and process reliability improves, adoption is projected to accelerate, particularly in applications demanding superior strength-to-weight ratios, thermal management, and electrical conductivity.
Manufacturing Innovations: Process Advances and Scale-Up Challenges
The manufacturing of graphene-based epoxy nanocomposites is undergoing significant transformation in 2025, driven by both process innovations and the persistent challenge of scaling up production. The integration of graphene into epoxy matrices promises substantial improvements in mechanical, thermal, and electrical properties, but realizing these benefits at industrial scale remains complex.
A primary focus in recent years has been the development of more efficient dispersion techniques. Uniform dispersion of graphene within the epoxy matrix is critical for achieving the desired enhancements. Companies such as Directa Plus and Versarien have reported advances in proprietary mixing and exfoliation processes, enabling better control over graphene particle size and distribution. These methods include high-shear mixing, ultrasonication, and in situ polymerization, which are being optimized for both batch and continuous production lines.
Another innovation is the functionalization of graphene to improve compatibility with epoxy resins. Surface modification techniques, such as the introduction of oxygen-containing groups or silane coupling agents, are being adopted to enhance interfacial bonding. Avana Nano and First Graphene are among the companies commercializing functionalized graphene products specifically tailored for epoxy systems, reporting improved processability and end-use performance.
Scale-up remains a central challenge. While laboratory-scale production has demonstrated promising results, translating these processes to industrial volumes introduces issues such as agglomeration, viscosity management, and quality consistency. Graphenea and Oxford Advanced Surfaces are investing in pilot-scale facilities and automated quality control systems to address these hurdles. The focus is on developing robust supply chains for both graphene and epoxy precursors, as well as on-line monitoring technologies to ensure batch-to-batch uniformity.
Environmental and regulatory considerations are also shaping manufacturing strategies. Companies are increasingly adopting solvent-free or low-VOC (volatile organic compound) processes, and exploring bio-based epoxy resins to align with sustainability goals. Industry bodies such as the Graphene Flagship are supporting collaborative projects to standardize testing protocols and accelerate the adoption of safe, scalable manufacturing practices.
Looking ahead, the outlook for graphene-based epoxy nanocomposite manufacturing is cautiously optimistic. With ongoing investments in process automation, material functionalization, and quality assurance, the sector is poised for broader commercialization in automotive, aerospace, and electronics applications over the next few years. However, the pace of adoption will depend on continued progress in overcoming scale-up and cost barriers, as well as on the establishment of industry-wide standards for material performance and safety.
Key Players & Industry Ecosystem (e.g., grapheneplatform.com, haydale.com, graphene-info.com)
The graphene-based epoxy nanocomposite manufacturing sector in 2025 is characterized by a dynamic ecosystem of material producers, technology integrators, and end-use manufacturers. The industry is driven by the need for advanced materials with superior mechanical, thermal, and electrical properties, targeting applications in aerospace, automotive, electronics, and energy storage.
Key players in this space include vertically integrated graphene producers, specialized nanomaterial suppliers, and composite manufacturers. Graphene Platform Corporation is a prominent Japanese company offering a range of graphene materials, including graphene oxide and reduced graphene oxide, which are widely used as additives in epoxy matrices. Their focus on scalable production and quality control has enabled partnerships with composite manufacturers seeking to enhance epoxy performance.
In the UK, Haydale Graphene Industries stands out for its patented plasma functionalization technology, which improves the dispersion and compatibility of graphene within epoxy resins. Haydale collaborates with industrial partners to develop customized nanocomposite solutions, with recent announcements highlighting supply agreements for graphene-enhanced prepregs and coatings.
Another significant contributor is Directa Plus, an Italian company specializing in the production of pristine graphene nanoplatelets. Their G+® graphene products are incorporated into epoxy systems for applications ranging from sports equipment to automotive components, with a focus on sustainability and regulatory compliance.
The industry ecosystem is further supported by information and networking platforms such as Graphene-Info, which aggregates updates on commercial developments, product launches, and regulatory trends. These platforms facilitate knowledge exchange between material suppliers, research institutions, and end-users, accelerating the adoption of graphene-based epoxy nanocomposites.
In 2025, the sector is witnessing increased investment in pilot-scale and commercial-scale production facilities, with companies like First Graphene (Australia) and Versarien (UK) expanding their manufacturing capacities. These firms emphasize quality assurance, supply chain traceability, and compliance with international standards, which are critical for market acceptance in regulated industries.
Looking ahead, the industry is expected to see further consolidation as larger chemical and materials companies enter the market, either through partnerships or acquisitions. The focus will remain on improving graphene dispersion techniques, cost reduction, and the development of application-specific epoxy nanocomposite formulations. The collaborative ecosystem—spanning raw material suppliers, technology developers, and end-users—will be pivotal in driving commercial adoption and scaling up production over the next few years.
Market Size, Segmentation & 2025–2030 Growth Forecasts
The market for graphene-based epoxy nanocomposite manufacturing is poised for significant expansion between 2025 and 2030, driven by the unique mechanical, thermal, and electrical properties that graphene imparts to epoxy matrices. As of 2025, the sector is characterized by increasing adoption in industries such as aerospace, automotive, electronics, and energy, where enhanced material performance is critical.
Segmentation within the market is primarily based on end-use industries, graphene type (e.g., graphene oxide, reduced graphene oxide, pristine graphene), and the form of epoxy (liquid, solid, or powder). The aerospace and automotive sectors are expected to remain the largest consumers, leveraging graphene-epoxy nanocomposites for lightweighting, improved durability, and superior thermal management. The electronics industry is also emerging as a key segment, utilizing these materials for advanced printed circuit boards and EMI shielding applications.
Several leading companies are actively scaling up production and application development. Directa Plus, a prominent European graphene producer, has expanded its portfolio to include graphene-enhanced epoxy resins targeting automotive and industrial coatings. Versarien is collaborating with manufacturers to integrate graphene nanomaterials into composite matrices for high-performance applications. In North America, XG Sciences supplies graphene nanoplatelets specifically engineered for epoxy systems, supporting both bulk and specialty composite manufacturers. Meanwhile, First Graphene in Australia is commercializing high-purity graphene additives for epoxy formulations, focusing on scalability and consistent quality.
From a regional perspective, Asia-Pacific is anticipated to witness the fastest growth, propelled by robust manufacturing bases in China, Japan, and South Korea, and strong government support for advanced materials. Europe and North America are also expected to see steady growth, underpinned by innovation-driven demand and the presence of established composite manufacturers.
Looking ahead to 2030, the market outlook is optimistic. Ongoing investments in production capacity, process optimization, and application development are expected to lower costs and broaden adoption. The increasing availability of standardized graphene materials and improved dispersion techniques will further enhance the performance and reliability of epoxy nanocomposites. As regulatory frameworks evolve and sustainability becomes a greater focus, graphene-based epoxy systems are likely to gain traction in sectors seeking both performance and environmental benefits.
Overall, the period from 2025 to 2030 is set to be transformative for graphene-based epoxy nanocomposite manufacturing, with market growth underpinned by technological advancements, expanding end-use applications, and the strategic initiatives of leading industry players.
Application Landscape: Aerospace, Automotive, Electronics, and Beyond
The application landscape for graphene-based epoxy nanocomposites is rapidly expanding across high-performance sectors such as aerospace, automotive, and electronics, with 2025 marking a pivotal year for commercial adoption and scale-up. These nanocomposites, which integrate graphene’s exceptional mechanical, thermal, and electrical properties into traditional epoxy matrices, are increasingly being targeted for advanced structural and functional components.
In the aerospace sector, the drive for lighter, stronger, and more durable materials is accelerating the integration of graphene-enhanced epoxies. Companies like Airbus and Boeing have publicly acknowledged ongoing research and pilot projects involving graphene nanocomposites for applications such as lightweight panels, radomes, and anti-static coatings. The focus is on leveraging graphene’s high strength-to-weight ratio and electrical conductivity to improve fuel efficiency and safety, while also enhancing resistance to lightning strikes and environmental degradation.
In the automotive industry, manufacturers are exploring graphene-based epoxy nanocomposites for both structural and functional parts. Ford Motor Company has reported the use of graphene in foam and composite components to achieve weight reduction and improved noise, vibration, and harshness (NVH) performance. The trend is expected to intensify through 2025, with more OEMs and tier-one suppliers piloting graphene-epoxy blends for under-the-hood parts, body panels, and battery enclosures, aiming for enhanced mechanical strength, thermal management, and EMI shielding.
The electronics sector is witnessing significant momentum, as graphene-based epoxy nanocomposites offer superior thermal conductivity and electrical properties. Companies such as Samsung Electronics and Sony Group Corporation are actively investigating these materials for use in printed circuit boards, thermal interface materials, and encapsulants. The goal is to address the growing demand for miniaturization and heat dissipation in next-generation consumer electronics and high-power devices.
Beyond these core sectors, graphene-epoxy nanocomposites are being trialed in energy storage, marine, and construction applications. For example, Vestas Wind Systems is exploring graphene-enhanced composites for wind turbine blades, targeting improved fatigue resistance and longer service life. In the construction industry, companies like Sika AG are developing graphene-epoxy coatings for enhanced durability and corrosion protection.
Looking ahead, the outlook for 2025 and beyond is characterized by increased collaboration between material suppliers, such as Directa Plus and Versarien plc, and end-users to optimize formulations and scale up production. As manufacturing processes mature and regulatory standards evolve, graphene-based epoxy nanocomposites are poised to become integral to the next generation of high-performance, multifunctional materials across diverse industries.
Competitive Analysis: Differentiators and Strategic Positioning
The competitive landscape of graphene-based epoxy nanocomposite manufacturing in 2025 is shaped by a combination of technological innovation, supply chain integration, and strategic partnerships. Key differentiators among leading players include the quality and consistency of graphene materials, scalability of production processes, and the ability to tailor nanocomposite formulations for specific end-use applications such as aerospace, automotive, electronics, and energy storage.
A major competitive advantage is the vertical integration of graphene production with epoxy compounding. Companies like Directa Plus and First Graphene have invested in proprietary graphene manufacturing technologies, enabling them to control the purity, morphology, and functionalization of graphene nanoplatelets and powders. This control is critical for ensuring uniform dispersion within epoxy matrices, which directly impacts mechanical, thermal, and electrical performance of the final nanocomposite.
Another differentiator is the development of scalable, environmentally friendly production methods. Versarien and Graphenea have focused on water-based exfoliation and green chemistry approaches, reducing the environmental footprint and aligning with increasingly stringent regulatory requirements in Europe and North America. These companies are also leveraging their R&D capabilities to offer customized graphene-epoxy masterbatches, which simplify downstream processing for manufacturers in diverse sectors.
Strategic positioning is further enhanced by partnerships with major epoxy resin producers and end-users. For example, Huntsman Corporation and Hexion Inc. have both announced collaborations with graphene suppliers to co-develop advanced epoxy systems for high-performance composites. Such alliances accelerate the commercialization of graphene-enhanced products and provide access to established distribution networks.
In terms of market outlook, the next few years are expected to see increased adoption of graphene-based epoxy nanocomposites in sectors demanding lightweighting, improved durability, and multifunctionality. The ability to demonstrate consistent, repeatable enhancements in properties—such as a 30–50% increase in tensile strength or significant improvements in thermal conductivity—remains a key selling point. Companies that can provide robust technical support, application-specific data, and regulatory compliance documentation are likely to gain a competitive edge.
Overall, the sector is moving toward greater standardization, with industry bodies such as the Graphene Flagship playing a role in establishing best practices and facilitating pre-competitive collaboration. As production costs continue to decline and supply chains mature, the competitive focus will increasingly shift from raw material supply to value-added formulation and application engineering.
Regulatory Environment & Industry Standards (e.g., graphene-flagship.eu, ieee.org)
The regulatory environment and industry standards for graphene-based epoxy nanocomposite manufacturing are rapidly evolving as the sector matures and commercial applications expand. In 2025, the focus is on harmonizing safety, quality, and performance benchmarks to facilitate broader adoption across industries such as aerospace, automotive, and electronics.
A key driver in this landscape is the European Union’s Graphene Flagship, one of the world’s largest research initiatives dedicated to bringing graphene innovations from the laboratory to the market. The Flagship has been instrumental in developing guidelines for the safe handling, processing, and integration of graphene and its derivatives into epoxy matrices. Their collaborative efforts with industry partners and regulatory bodies have resulted in preliminary best practices for material characterization, dispersion quality, and environmental health and safety (EHS) protocols, which are increasingly referenced by manufacturers and end-users.
On the international stage, organizations such as the IEEE are actively working on standardization frameworks for nanomaterials, including graphene-based composites. The IEEE’s standards committees are developing protocols for electrical, mechanical, and thermal property testing, which are critical for certifying the performance of graphene-epoxy systems in high-reliability applications. These standards are expected to be referenced in procurement and qualification processes by major OEMs in the coming years.
In the United States, the American National Standards Institute (ANSI) and the ASTM International are collaborating with industry stakeholders to establish consensus-based standards for graphene material quality, purity, and functionalization. ASTM has already published several standards related to nanomaterial characterization, and ongoing work aims to address the unique challenges of dispersing graphene in epoxy resins, such as agglomeration and interfacial compatibility.
Manufacturers like Directa Plus and Haydale Technologies are actively participating in these standardization efforts, contributing data from their proprietary production processes and advocating for clear labeling and traceability requirements. These companies are also aligning their quality management systems with ISO standards, anticipating future regulatory requirements for nanocomposite materials.
Looking ahead, the regulatory environment is expected to become more stringent, with increased emphasis on lifecycle assessment, recyclability, and end-of-life management of graphene-epoxy composites. Industry consortia and regulatory agencies are likely to introduce new certification schemes and eco-labels to support sustainable manufacturing practices. As the market grows, compliance with evolving standards will be a prerequisite for market access, especially in regulated sectors such as transportation and consumer electronics.
Investment Trends, Partnerships, and M&A Activity
The landscape of investment, partnerships, and mergers & acquisitions (M&A) in graphene-based epoxy nanocomposite manufacturing is evolving rapidly as the sector matures and commercial applications expand. In 2025, the industry is witnessing a marked increase in strategic investments and collaborations, driven by the demand for advanced materials in automotive, aerospace, electronics, and energy storage sectors.
Key players such as Directa Plus, a leading producer of graphene-based products, and Versarien, known for its graphene-enhanced composites, have continued to attract investment and form partnerships with end-users and manufacturers. Directa Plus has expanded its collaborations with industrial partners to integrate graphene nanoplatelets into epoxy matrices, targeting improved mechanical and thermal properties for composites. Similarly, Versarien has entered into joint development agreements with global manufacturers to accelerate the adoption of graphene-enhanced epoxy systems in high-performance applications.
In 2025, the sector is also seeing increased activity from established chemical and materials companies. Huntsman Corporation, a major supplier of epoxy resins, has announced initiatives to incorporate graphene additives into its product lines, often through partnerships with graphene producers. Arkema, another global specialty chemicals company, is investing in R&D and pilot-scale production of graphene-epoxy nanocomposites, aiming to serve the growing demand in transportation and electronics.
M&A activity is intensifying as larger players seek to secure access to proprietary graphene technologies and manufacturing capabilities. In recent years, several acquisitions have been reported, with companies aiming to vertically integrate graphene production and composite manufacturing. For example, First Graphene has pursued strategic investments and acquisitions to expand its supply chain and application development capabilities, particularly in the Asia-Pacific region.
Looking ahead, the outlook for 2025 and beyond suggests continued consolidation and partnership formation. The drive for scalable, cost-effective production of graphene-based epoxy nanocomposites is expected to attract further investment from both established industry leaders and emerging technology firms. As regulatory standards and end-user requirements evolve, collaborations between graphene producers, resin manufacturers, and OEMs will likely intensify, shaping the competitive landscape and accelerating commercialization.
Future Outlook: Disruptive Opportunities and Long-Term Impact
The future outlook for graphene-based epoxy nanocomposite manufacturing in 2025 and the coming years is marked by significant disruptive opportunities and the potential for long-term impact across multiple industries. As the demand for advanced materials with superior mechanical, thermal, and electrical properties intensifies, graphene-enhanced epoxy systems are positioned to play a transformative role in sectors such as aerospace, automotive, electronics, and renewable energy.
Key manufacturers and suppliers are scaling up production capacities and refining dispersion techniques to address longstanding challenges in uniform graphene integration and cost-effective mass production. Companies like Directa Plus and Versarien are actively expanding their graphene material portfolios, focusing on high-purity graphene nanoplatelets and tailored formulations for epoxy matrices. These efforts are expected to accelerate the adoption of graphene-based nanocomposites in structural components, coatings, and adhesives, where enhanced strength-to-weight ratios and improved durability are critical.
In 2025, the industry is witnessing a shift from laboratory-scale demonstrations to commercial-scale applications. Haydale Graphene Industries has reported progress in developing functionalized graphene additives that improve the dispersion and interfacial bonding within epoxy resins, leading to measurable gains in mechanical performance and electrical conductivity. Such advancements are crucial for enabling next-generation lightweight composites in electric vehicles and aircraft, where reducing weight directly translates to energy savings and lower emissions.
The construction and infrastructure sectors are also exploring graphene-epoxy nanocomposites for corrosion-resistant coatings and high-performance adhesives. Graphenea and First Graphene are collaborating with industrial partners to validate the long-term reliability and environmental benefits of these materials in harsh operating conditions. Early field trials suggest that graphene-enhanced epoxies can extend maintenance intervals and reduce lifecycle costs for bridges, pipelines, and offshore platforms.
Looking ahead, the convergence of digital manufacturing, advanced characterization, and scalable graphene production is expected to unlock new application domains. The integration of graphene-based nanocomposites with additive manufacturing and smart sensor technologies could enable multifunctional components with real-time monitoring capabilities. Industry bodies such as the Graphene Flagship are fostering cross-sector collaboration to standardize material specifications and accelerate regulatory acceptance, paving the way for broader commercialization.
Overall, the next few years are likely to see graphene-based epoxy nanocomposites transition from niche innovations to mainstream solutions, driving sustainability, performance, and competitiveness across global value chains.