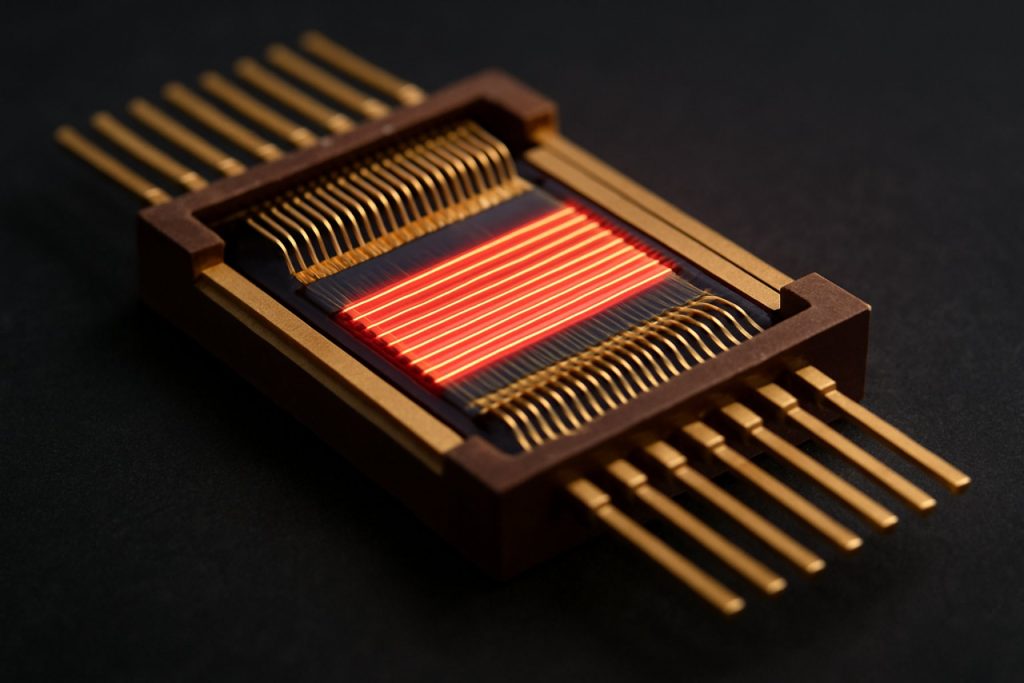
Gallium Arsenide Laser Array Manufacturing in 2025: Pioneering Photonics, Accelerating Market Growth, and Shaping the Future of High-Performance Optoelectronics. Discover the Key Drivers, Innovations, and Strategic Opportunities in This Rapidly Evolving Sector.
- Executive Summary: 2025 Market Landscape and Key Takeaways
- Gallium Arsenide Laser Array Technology: Fundamentals and Recent Breakthroughs
- Global Market Size, Segmentation, and 2025–2030 Growth Forecasts
- Key Application Sectors: Telecom, Data Centers, Sensing, and Beyond
- Competitive Landscape: Leading Manufacturers and Strategic Alliances
- Manufacturing Innovations: Yield, Scalability, and Cost Reduction
- Supply Chain Dynamics: Raw Materials, Wafer Sourcing, and Logistics
- Regulatory Environment and Industry Standards (e.g., IEEE, OSA)
- Emerging Trends: Integration with Silicon Photonics and Quantum Technologies
- Future Outlook: Investment Hotspots, R&D Priorities, and Market Opportunities
- Sources & References
Executive Summary: 2025 Market Landscape and Key Takeaways
The global landscape for Gallium Arsenide (GaAs) laser array manufacturing in 2025 is characterized by robust demand, technological innovation, and strategic investments from leading semiconductor and photonics companies. GaAs laser arrays, prized for their high efficiency, fast modulation speeds, and superior performance in optical communications, sensing, and industrial applications, are increasingly central to next-generation data centers, automotive LiDAR, and advanced medical devices.
Key industry players such as ams OSRAM, Lumentum Holdings, and Coherent Corp. (formerly II-VI Incorporated) are expanding their GaAs laser array production capacities to meet surging global demand. ams OSRAM continues to leverage its vertically integrated manufacturing and R&D capabilities, focusing on high-power laser arrays for automotive and industrial markets. Lumentum Holdings is investing in advanced wafer processing and packaging technologies to enhance the performance and reliability of its GaAs-based photonic products, particularly for telecom and 3D sensing applications. Coherent Corp. is scaling up its wafer fabrication and epitaxial growth facilities, targeting both telecom and emerging quantum technology sectors.
In 2025, the market is witnessing a shift toward larger wafer sizes (6-inch and above) and the adoption of automated, high-throughput manufacturing lines. This transition is driven by the need to reduce unit costs and improve yield, as well as to support the growing complexity of multi-emitter laser arrays. Industry data indicates that the integration of advanced process control and in-line metrology is becoming standard practice, enabling tighter quality control and higher device reliability.
Geographically, Asia-Pacific remains the dominant manufacturing hub, with significant investments from companies such as TrueLight Corporation and Panasonic Semiconductor Solutions. These firms are capitalizing on regional supply chain strengths and proximity to major electronics and automotive OEMs. Meanwhile, North American and European manufacturers are focusing on high-value, specialized applications and securing supply chain resilience through strategic partnerships and onshoring initiatives.
Looking ahead, the GaAs laser array manufacturing sector is poised for continued growth, propelled by the proliferation of AI-driven data centers, expansion of 5G/6G networks, and the electrification of vehicles. Key takeaways for 2025 include intensified competition, accelerated process innovation, and a growing emphasis on sustainability and supply chain security. Companies that invest in advanced manufacturing technologies and strategic collaborations are expected to maintain a competitive edge in this dynamic market.
Gallium Arsenide Laser Array Technology: Fundamentals and Recent Breakthroughs
Gallium arsenide (GaAs) laser arrays are at the forefront of optoelectronic device manufacturing, driven by their superior electron mobility, direct bandgap, and high quantum efficiency. In 2025, the manufacturing landscape for GaAs laser arrays is characterized by rapid advancements in epitaxial growth, wafer processing, and device integration, with a strong focus on scaling production for applications in data communications, sensing, and emerging quantum technologies.
The core of GaAs laser array manufacturing remains molecular beam epitaxy (MBE) and metal-organic chemical vapor deposition (MOCVD), which enable precise control over layer thickness and composition. Leading manufacturers such as Coherent Corp. (formerly II-VI Incorporated) and Lumentum Holdings have invested heavily in advanced MOCVD reactors and in-situ monitoring systems to improve yield and uniformity across 4-inch and 6-inch GaAs wafers. These improvements are critical for fabricating high-density laser arrays with consistent performance, especially as demand grows for 3D sensing and LiDAR in automotive and consumer electronics.
Recent breakthroughs include the integration of distributed feedback (DFB) and distributed Bragg reflector (DBR) structures within GaAs laser arrays, enabling narrower linewidths and higher spectral purity. Companies like TRIUMPH TECHNOLOGY and ams OSRAM have demonstrated scalable processes for monolithic integration of multiple emitters, which is essential for high-power and wavelength-stabilized arrays used in industrial and medical applications. Additionally, hybrid integration techniques—combining GaAs laser arrays with silicon photonics—are being actively developed by Intel Corporation and ams OSRAM, aiming to bridge the gap between III-V optoelectronics and mainstream CMOS platforms.
Yield optimization and defect reduction remain key challenges, particularly as array sizes increase and device architectures become more complex. Automated wafer inspection and advanced metrology tools are being deployed by manufacturers such as Veeco Instruments to monitor defect densities and ensure process repeatability. Furthermore, the adoption of digital twin and AI-driven process control is expected to accelerate in the next few years, enabling predictive maintenance and real-time optimization of manufacturing lines.
Looking ahead, the outlook for GaAs laser array manufacturing is robust. The sector is poised for further growth as 800G and 1.6T optical transceivers, solid-state LiDAR, and quantum photonic circuits move toward commercialization. Strategic investments in wafer-scale integration, packaging automation, and heterogeneous integration are anticipated to define the competitive landscape through 2025 and beyond, with established players and new entrants alike racing to meet the surging global demand for high-performance photonic devices.
Global Market Size, Segmentation, and 2025–2030 Growth Forecasts
The global market for gallium arsenide (GaAs) laser array manufacturing is poised for robust growth from 2025 through 2030, driven by expanding applications in telecommunications, data centers, automotive LiDAR, medical devices, and consumer electronics. GaAs laser arrays are increasingly favored for their high efficiency, superior wavelength stability, and ability to operate at higher frequencies compared to silicon-based alternatives. This technological edge is fueling demand across both established and emerging sectors.
In 2025, the GaAs laser array manufacturing market is estimated to be valued in the low single-digit billions (USD), with Asia-Pacific—particularly China, Japan, and South Korea—accounting for the largest share of production and consumption. This regional dominance is underpinned by the presence of major optoelectronic component manufacturers and robust investments in 5G infrastructure and advanced driver-assistance systems (ADAS). Key industry players such as Coherent Corp. (formerly II-VI Incorporated), OSRAM, and Lumentum Holdings are actively expanding their GaAs laser array production capacities to meet surging demand for high-speed optical transceivers and automotive sensing modules.
Market segmentation is typically delineated by application (telecommunications, automotive, medical, industrial, and consumer electronics), wavelength (near-infrared, visible, and others), and array configuration (edge-emitting, vertical-cavity surface-emitting lasers [VCSELs], and custom arrays). The VCSEL segment, in particular, is expected to witness the fastest growth, propelled by its adoption in 3D sensing for smartphones, facial recognition, and in-cabin automotive monitoring systems. Companies like ams OSRAM and TRIOPTICS are at the forefront of VCSEL innovation and manufacturing scale-up.
Looking ahead to 2030, the GaAs laser array manufacturing market is forecast to achieve a compound annual growth rate (CAGR) in the high single digits, with total market value potentially doubling from 2025 levels. This outlook is supported by ongoing advancements in wafer-scale manufacturing, improvements in device reliability, and the proliferation of high-bandwidth optical networks. Strategic investments by leading manufacturers, such as Broadcom Inc. and Hamamatsu Photonics, are expected to further accelerate innovation and capacity expansion.
- Asia-Pacific will remain the largest and fastest-growing regional market, with North America and Europe also seeing significant investments in next-generation photonics manufacturing.
- Telecommunications and automotive applications will continue to drive the majority of demand, but medical and consumer electronics segments are projected to grow at above-average rates.
- Ongoing R&D in high-power and high-density GaAs laser arrays will open new opportunities in industrial and defense sectors.
In summary, the period from 2025 to 2030 will be marked by strong market expansion, technological innovation, and increased global competition in GaAs laser array manufacturing, with established players and new entrants alike vying for leadership in this critical photonics domain.
Key Application Sectors: Telecom, Data Centers, Sensing, and Beyond
Gallium arsenide (GaAs) laser arrays are at the forefront of photonics innovation, with their manufacturing processes underpinning critical advances across telecom, data centers, sensing, and emerging sectors. In 2025, the demand for high-speed, energy-efficient optical components is accelerating, driven by the exponential growth in data traffic, the rollout of 5G/6G networks, and the proliferation of AI-powered cloud services. GaAs laser arrays, known for their superior electron mobility and direct bandgap, are increasingly favored for their ability to deliver high output power, narrow linewidths, and excellent temperature stability.
In telecommunications, GaAs-based vertical-cavity surface-emitting lasers (VCSELs) and edge-emitting laser arrays are integral to high-speed optical transceivers used in fiber-optic networks. Major manufacturers such as Coherent Corp. (formerly II-VI Incorporated) and Lumentum Holdings are scaling up production of GaAs laser arrays to meet the needs of next-generation coherent and direct-detect optical modules. These arrays enable data rates exceeding 400 Gbps per channel, supporting the backbone of hyperscale data centers and metro networks.
Data centers, in particular, are a key growth sector. The shift toward co-packaged optics and the adoption of parallel optical interconnects are driving demand for multi-channel GaAs laser arrays. Companies like Broadcom Inc. and Advanced Micro Devices, Inc. (AMD) (following its acquisition of Xilinx) are integrating GaAs-based photonic solutions into their high-performance computing and networking platforms. The focus is on reducing power consumption and latency while increasing bandwidth density, with GaAs laser arrays playing a pivotal role in enabling these advances.
Sensing applications are also expanding rapidly. GaAs laser arrays are central to 3D sensing, LiDAR, and industrial metrology, where their fast modulation speeds and high reliability are essential. Triad Semiconductor and ams OSRAM are notable for their investments in GaAs VCSEL array manufacturing for automotive and consumer electronics markets. These arrays are being deployed in advanced driver-assistance systems (ADAS), facial recognition, and gesture control, with production volumes expected to rise through 2025 and beyond.
Looking ahead, the outlook for GaAs laser array manufacturing is robust. The sector is witnessing increased investment in wafer-scale manufacturing, advanced epitaxial growth techniques, and automated testing to improve yield and reduce costs. As quantum communications, medical diagnostics, and AR/VR applications mature, GaAs laser arrays are poised to capture new markets, reinforcing their strategic importance across the photonics landscape.
Competitive Landscape: Leading Manufacturers and Strategic Alliances
The competitive landscape for gallium arsenide (GaAs) laser array manufacturing in 2025 is characterized by a concentrated group of established global players, emerging innovators, and a growing trend toward strategic alliances. The sector is driven by demand from telecommunications, data centers, automotive LiDAR, and advanced sensing applications, with manufacturers racing to scale production and improve device performance.
Among the leading manufacturers, Lumentum Holdings Inc. stands out as a dominant force, leveraging its vertically integrated supply chain and advanced wafer fabrication capabilities. Lumentum’s GaAs-based laser arrays are widely used in 3D sensing and optical networking, and the company continues to invest in expanding its manufacturing footprint to meet rising demand. Another major player, Coherent Corp. (formerly II-VI Incorporated), has consolidated its position through acquisitions and now offers a broad portfolio of GaAs laser arrays for industrial, medical, and consumer electronics markets.
In Asia, Hamamatsu Photonics K.K. is a key manufacturer, known for its high-reliability GaAs laser arrays used in scientific instrumentation and automotive applications. The company’s focus on R&D and proprietary epitaxial growth technologies has enabled it to maintain a competitive edge. Meanwhile, TrueLight Corporation in Taiwan is expanding its GaAs laser array production, targeting optical communication and sensing markets with cost-effective solutions.
Strategic alliances and joint ventures are increasingly shaping the industry. For example, Lumentum and Advanced Micro Devices, Inc. (AMD) have announced collaborations to integrate GaAs laser arrays into next-generation data center architectures, aiming to boost optical interconnect speeds and energy efficiency. Similarly, ams OSRAM is partnering with automotive OEMs to co-develop GaAs-based LiDAR modules for autonomous vehicles, leveraging its expertise in optoelectronic integration.
Looking ahead, the competitive landscape is expected to intensify as new entrants from China and South Korea ramp up GaAs laser array production, supported by government initiatives and investments in compound semiconductor manufacturing. Established players are responding by deepening partnerships, investing in automation, and pursuing M&A to secure supply chains and intellectual property. The next few years will likely see further consolidation, with leading manufacturers focusing on scaling up, reducing costs, and accelerating innovation to capture emerging opportunities in AI, automotive, and quantum technologies.
Manufacturing Innovations: Yield, Scalability, and Cost Reduction
The manufacturing of gallium arsenide (GaAs) laser arrays is undergoing significant innovation in 2025, driven by the need for higher yields, improved scalability, and cost reduction. GaAs laser arrays are critical components in optical communications, sensing, and advanced display technologies, and their production is being shaped by both technological advances and market pressures.
One of the most notable trends is the adoption of advanced epitaxial growth techniques, such as metal-organic chemical vapor deposition (MOCVD) and molecular beam epitaxy (MBE), which enable precise control over layer thickness and composition. Leading manufacturers like ams OSRAM and Lumentum Holdings are investing in these methods to improve uniformity across large wafers, directly impacting device yield and performance consistency. The shift to larger wafer diameters—moving from 2-inch to 4-inch and even 6-inch GaAs substrates—has also been observed, allowing for more devices per wafer and thus reducing per-unit costs.
Yield improvement remains a central focus, as even minor defects can render entire arrays unusable. Companies are deploying in-line metrology and advanced inspection systems to detect and mitigate defects early in the process. Coherent Corp. (formerly II-VI Incorporated) has reported the integration of AI-driven process control to optimize growth and etching steps, resulting in measurable yield gains. Additionally, the use of patterned substrates and selective area growth is being explored to further enhance device uniformity and reduce dislocation densities.
Scalability is being addressed through automation and modular production lines. TRIOPTICS, a supplier of optical manufacturing equipment, is collaborating with laser array producers to implement automated alignment and testing systems, which are crucial for high-throughput manufacturing. These systems not only increase throughput but also reduce labor costs and variability, supporting the industry’s move toward mass production for applications such as automotive LiDAR and high-speed data links.
Cost reduction strategies are multifaceted. In addition to economies of scale from larger wafers and automation, manufacturers are optimizing material utilization and recycling processes for expensive GaAs substrates. Some, like Vixar (a subsidiary of ams OSRAM), are developing hybrid integration techniques that combine GaAs laser arrays with silicon photonics, leveraging the cost advantages of silicon processing while maintaining the performance benefits of GaAs.
Looking ahead, the outlook for GaAs laser array manufacturing is positive, with continued investment in process innovation and supply chain optimization expected to further drive down costs and enable broader adoption across emerging markets. As demand for high-performance photonic devices grows, the sector is poised for robust expansion through 2025 and beyond.
Supply Chain Dynamics: Raw Materials, Wafer Sourcing, and Logistics
The supply chain for gallium arsenide (GaAs) laser array manufacturing in 2025 is characterized by a complex interplay of raw material sourcing, wafer production, and global logistics. The foundation of this supply chain is the procurement of high-purity gallium and arsenic, both of which are critical for producing GaAs substrates. Gallium is primarily obtained as a byproduct of aluminum and zinc production, with major suppliers located in China, Germany, and Japan. Arsenic, while more widely available, requires stringent handling and purification due to its toxicity and volatility.
Wafer production is dominated by a handful of specialized manufacturers with vertically integrated operations. Companies such as Sumitomo Chemical and Wafer Technology Ltd. are recognized for their expertise in producing high-quality GaAs wafers, which serve as the substrate for epitaxial growth of laser structures. These wafers must meet exacting standards for purity, crystallographic orientation, and defect density, as even minor imperfections can significantly impact laser performance and yield.
Epitaxial wafer suppliers, including IQE plc, play a pivotal role by providing custom-engineered GaAs epitaxial structures tailored for laser array applications. IQE, for example, operates multiple facilities in the UK, US, and Asia, ensuring a geographically diversified supply chain that can mitigate regional disruptions. The company’s focus on molecular beam epitaxy (MBE) and metal-organic chemical vapor deposition (MOCVD) processes enables the production of wafers with precise layer thickness and doping profiles, essential for high-performance laser arrays.
Logistics for GaAs laser array manufacturing are increasingly globalized, with raw materials and wafers often crossing multiple borders before reaching device fabrication plants. The industry has responded to recent geopolitical and pandemic-related disruptions by diversifying suppliers and increasing inventory buffers. Leading device manufacturers such as Lumentum Holdings and Coherent Corp. (formerly II-VI Incorporated) have established multi-sourcing strategies and closer collaborations with upstream suppliers to ensure continuity and quality.
Looking ahead, the outlook for the GaAs laser array supply chain in the next few years is shaped by ongoing investments in capacity expansion and process automation. Companies are also exploring recycling and recovery of gallium from production scrap to reduce dependence on primary sources. As demand for high-speed optical communications, 3D sensing, and automotive LiDAR continues to grow, the resilience and flexibility of the GaAs supply chain will remain a strategic priority for manufacturers and their partners.
Regulatory Environment and Industry Standards (e.g., IEEE, OSA)
The regulatory environment and industry standards for gallium arsenide (GaAs) laser array manufacturing in 2025 are shaped by a combination of international safety protocols, material handling regulations, and performance benchmarks established by leading industry bodies. As GaAs laser arrays become increasingly integral to applications in telecommunications, data centers, medical devices, and advanced sensing, compliance with these standards is critical for manufacturers seeking global market access and customer trust.
Key industry standards are set by organizations such as the Institute of Electrical and Electronics Engineers (IEEE) and the Optica (formerly Optical Society of America, OSA). The IEEE provides a framework for the performance, reliability, and testing of semiconductor lasers, including GaAs-based devices, through standards such as IEEE 802.3 for optical transceivers and related protocols. Optica, meanwhile, plays a central role in defining optical measurement techniques, safety guidelines, and best practices for laser array characterization and integration.
In 2025, regulatory oversight also extends to environmental and worker safety, particularly due to the toxic nature of arsenic compounds used in GaAs wafer fabrication. Manufacturers must adhere to strict handling, waste disposal, and emissions standards, often guided by national agencies such as the U.S. Occupational Safety and Health Administration (OSHA) and the European Chemicals Agency (ECHA). These regulations mandate the use of advanced filtration, containment, and monitoring systems in production facilities to minimize occupational exposure and environmental impact.
On the product side, international laser safety standards such as IEC 60825, maintained by the International Electrotechnical Commission (IEC), are widely adopted. These standards classify laser products by hazard level and specify labeling, interlock, and user protection requirements. Compliance is essential for market entry, especially in sectors like healthcare and consumer electronics.
Major GaAs laser array manufacturers, including Coherent Corp. (formerly II-VI Incorporated), Lumentum Holdings, and TRUMPF, actively participate in standards development and often lead industry consortia to harmonize requirements across regions. Their engagement ensures that evolving standards reflect both technological advances and practical manufacturing considerations.
Looking ahead, the regulatory landscape is expected to evolve in response to emerging applications such as automotive LiDAR and quantum communications, which demand even tighter control over device reliability and safety. Industry bodies are anticipated to update standards to address new integration challenges, while regulatory agencies may introduce stricter environmental controls as sustainability becomes a higher priority in semiconductor manufacturing.
Emerging Trends: Integration with Silicon Photonics and Quantum Technologies
The integration of gallium arsenide (GaAs) laser arrays with silicon photonics and quantum technologies is rapidly advancing, driven by the demand for high-speed data transmission, compact photonic circuits, and scalable quantum systems. In 2025, several key trends are shaping the manufacturing landscape for GaAs laser arrays, particularly as they intersect with these emerging fields.
A primary trend is the hybrid integration of GaAs-based laser arrays onto silicon photonic platforms. This approach leverages the superior light-emitting properties of GaAs with the mature, scalable fabrication processes of silicon. Companies such as ams OSRAM and Lumentum Holdings are actively developing wafer bonding and flip-chip assembly techniques to enable high-yield, high-density integration of GaAs lasers with silicon waveguides. These methods are crucial for next-generation optical transceivers and on-chip optical interconnects, where minimizing footprint and maximizing bandwidth are essential.
Another significant development is the push toward monolithic integration, where GaAs laser arrays and silicon photonic components are fabricated on a single substrate. While technical challenges remain—such as lattice mismatch and thermal expansion differences—research and pilot production lines are making progress. imec, a leading research institute, is collaborating with industry partners to refine epitaxial growth and direct wafer bonding processes, aiming for commercial viability within the next few years.
In the quantum technology sector, GaAs laser arrays are gaining attention for their role in quantum dot single-photon sources and entangled photon pair generation. These applications require precise control over emission properties and integration with photonic circuits. Companies like QD Laser are advancing the fabrication of highly uniform GaAs quantum dot laser arrays, targeting quantum communication and computing markets. The ability to mass-produce such arrays with consistent performance is expected to be a differentiator as quantum photonic systems move toward commercialization.
Looking ahead, the outlook for GaAs laser array manufacturing is robust. The convergence of silicon photonics and quantum technologies is expected to drive further investment in advanced packaging, heterogeneous integration, and automated testing. Industry roadmaps suggest that by 2027, hybrid and monolithic GaAs-silicon laser arrays will be standard in high-performance data centers and emerging quantum networks, supported by ongoing innovation from both established manufacturers and research consortia.
Future Outlook: Investment Hotspots, R&D Priorities, and Market Opportunities
The future of gallium arsenide (GaAs) laser array manufacturing is poised for significant growth and innovation through 2025 and beyond, driven by surging demand in data communications, sensing, and advanced manufacturing. As the global appetite for high-speed optical interconnects and precision sensing expands, GaAs laser arrays are increasingly favored for their superior efficiency, high modulation speeds, and reliability compared to silicon-based alternatives.
Investment hotspots are emerging in regions with established compound semiconductor ecosystems, notably the United States, Europe, and East Asia. In the U.S., Coherent Corp. (formerly II-VI Incorporated) and Lumentum Holdings Inc. are scaling up GaAs laser array production, targeting datacenter interconnects and 3D sensing for consumer electronics. In Europe, TRUMPF is investing in GaAs-based high-power laser arrays for industrial and medical applications, leveraging its expertise in photonics and precision manufacturing. Meanwhile, in Asia, Hamamatsu Photonics and Sharp Corporation are expanding R&D and manufacturing capacity to serve automotive LiDAR and optical communication markets.
R&D priorities for 2025 focus on improving array uniformity, yield, and integration with silicon photonics. Companies are investing in advanced epitaxial growth techniques, such as metal-organic chemical vapor deposition (MOCVD), to enhance wafer-scale uniformity and reduce defect densities. There is also a strong push toward heterogeneous integration—bonding GaAs laser arrays directly onto silicon substrates—to enable compact, energy-efficient photonic integrated circuits. ams OSRAM is at the forefront of this trend, developing miniaturized GaAs laser arrays for automotive and consumer applications.
Market opportunities are expanding rapidly in several sectors. The proliferation of AI and cloud computing is driving demand for high-speed optical transceivers, where GaAs laser arrays offer the bandwidth and reliability required for next-generation datacenters. Automotive LiDAR, a critical technology for advanced driver-assistance systems (ADAS), is another high-growth area, with GaAs arrays enabling higher resolution and longer-range sensing. Additionally, the medical device sector is adopting GaAs laser arrays for precise surgical tools and diagnostic equipment.
Looking ahead, the convergence of public and private investment, ongoing R&D in materials and integration, and the diversification of end-use applications position GaAs laser array manufacturing as a dynamic and strategically important field through 2025 and the following years. Companies with robust vertical integration and strong intellectual property portfolios are expected to capture the largest share of emerging opportunities.