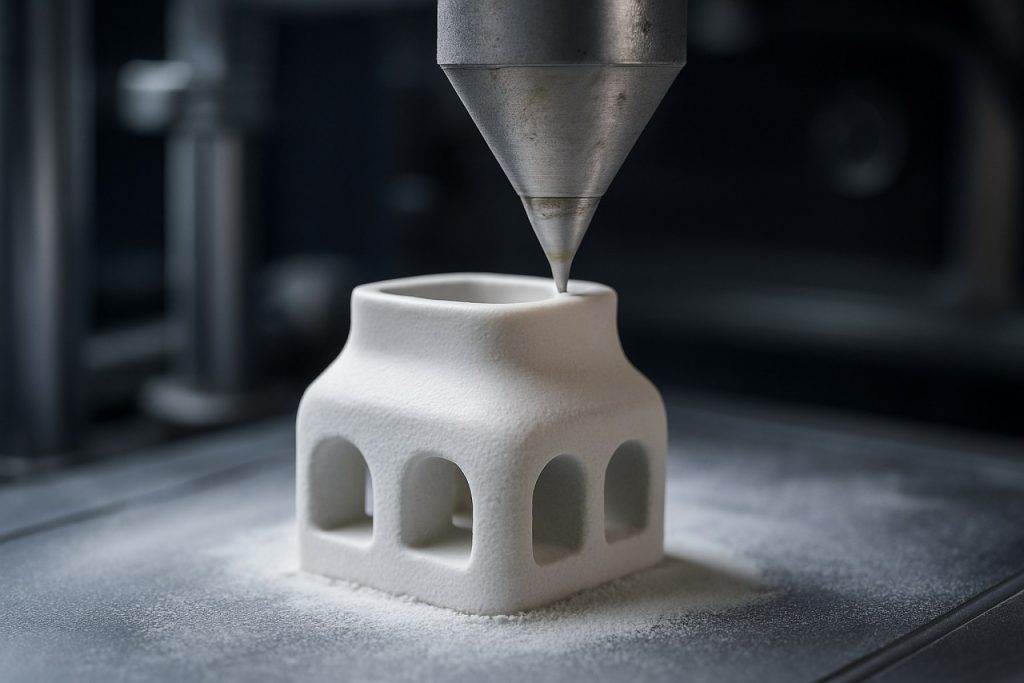
Zirkonia-Keramische Additive Fertigung im Jahr 2025: Transformation der fortschrittlichen Fertigung mit zweistelligem Wachstum. Entdecken Sie, wie Durchbrüche in Materialien und 3D-Druck die Zukunft von Hochleistungs-Keramiken gestalten.
- Executive Summary: Wichtige Trends und Marktreiber im Jahr 2025
- Marktgröße, Wachstumsrate und Prognose (2025–2030)
- Technologische Innovationen in der Zirkonia-Keramischen 3D-Druck
- Wichtige Akteure und strategische Partnerschaften
- Emerging Applications: Medizin, Luft- und Raumfahrt sowie Elektronik
- Lieferkette und Rohstoffüberlegungen
- Regulatorische Landschaft und Branchenstandards
- Wettbewerbsanalyse: Stärken, Schwächen und Differenzierungsmerkmale
- Nachhaltigkeit und Umweltimpact
- Zukünftige Perspektiven: Chancen, Herausforderungen und strategische Empfehlungen
- Quellen & Referenzen
Executive Summary: Wichtige Trends und Marktreiber im Jahr 2025
Die additive Fertigung (AM) mit Zirkonia-Keramik steht im Jahr 2025 vor einem signifikanten Wachstum, angetrieben durch Fortschritte in der Materialwissenschaft, Prozessoptimierung und wachsende industrielle Akzeptanz. Zirkonia, bekannt für ihre außergewöhnliche mechanische Festigkeit, Bruchzähigkeit und Biokompatibilität, wird in Sektoren wie Zahnmedizin, Medizin, Luft- und Raumfahrt sowie Elektronik zunehmend nachgefragt. Das Zusammenkommen dieser Eigenschaften mit der Gestaltungsfreiheit der AM ermöglicht die Produktion komplexer, hochleistungsfähiger Komponenten, die zuvor durch traditionelle Fertigungsmethoden unerreichbar waren.
Zu den wichtigen Trends im Jahr 2025 gehört die Reifung von pulverbasierten AM-Techniken – wie selektivem Lasersintern (SLS), Stereolithographie (SLA) und digitaler Lichtverarbeitung (DLP) – die speziell für Zirkonia-Keramiken entwickelt wurden. Führende Gerätehersteller wie 3D Systems und Stratasys erweitern ihre Portfolios um keramikkompatible Plattformen, während spezialisierte Firmen wie Lithoz GmbH und XJet die Grenzen mit proprietären Technologien für hochdichte, hochpräzise Zirkonia-Teile verschieben. Zum Beispiel hat Lithoz GmbH erhebliche Steigerungen in Durchsatz und Teilequalität mit ihren LCM (Lithographie-basierte Keramikfertigung) Systemen berichtet, die nun von zahmedizinischen Laboren und Herstellern von Medizinprodukten weltweit übernommen werden.
Materiallieferanten spielen ebenfalls eine entscheidende Rolle. Unternehmen wie Tosoh Corporation und 3DCeram investieren in die Entwicklung fortschrittlicher Zirkonia-Pulver und druckbare Pasten, die für AM-Prozesse optimiert sind. Diese Materialien bieten verbesserte Sinterbarkeit, reduzierte Porosität und verbesserte mechanische Eigenschaften und beseitigen frühere Einschränkungen in der Keramik-AM. Die Verfügbarkeit von medizinischen und hochreinen Zirkonia-Rohstoffen beschleunigt regulatorische Genehmigungen und die Akzeptanz in kritischen Anwendungen, insbesondere in der Zahnersatztechnik und orthopädischen Implantaten.
Die Markttreiber im Jahr 2025 umfassen die wachsende Nachfrage nach patientenspezifischen Medizinprodukten, leichten und verschleißfesten Komponenten in der Luft- und Raumfahrt sowie miniaturisierten Elektronikkomponenten. Die Fähigkeit, schnell Prototypen herzustellen und maßgeschneiderte Geometrien mit minimalem Materialabfall zu produzieren, zieht Hersteller an, die ihre Lieferketten optimieren und die Vorlaufzeiten reduzieren möchten. Darüber hinaus führen Nachhaltigkeitsüberlegungen zu einer Verschiebung hin zu additiven Prozessen, da diese im Vergleich zu subtraktiven Methoden einen geringeren Energieverbrauch und weniger Abfall bieten.
Mit Blick auf die Zukunft ist die Perspektive für Zirkonia-Keramik AM robust. Branchensynergien, laufende F&E und das Eintreten neuer Akteure werden voraussichtlich die Kosten weiter senken und die Palette druckbarer Zirkonia-Formulierungen erweitern. Mit der Verbesserung der Prozesszuverlässigkeit und der Teilezertifizierung wird Zirkonia-AM eine gängige Lösung für hochwertige, mission-kritische Anwendungen in mehreren Branchen werden.
Marktgröße, Wachstumsrate und Prognose (2025–2030)
Der globale Markt für zirkonia-keramische additive Fertigung (AM) wird von 2025 bis 2030 ein robustes Wachstum verzeichnen, angetrieben durch die zunehmende Akzeptanz in hochwertigen Sektoren wie Zahnmedizin, Medizin, Elektronik und fortgeschrittener Technik. Zirkonia, bekannt für ihre außergewöhnliche mechanische Festigkeit, Biokompatibilität und Widerstandsfähigkeit gegen Verschleiß und Korrosion, wird zunehmend zum bevorzugten Material für Anwendungen, in denen traditionelle Keramiken oder Metalle versagen. Der Markt wird derzeit von einer Kombination aus etablierten Akteuren und innovativen Startups geprägt, die jeweils zur schnellen Entwicklung von Materialien und AM-Hardware beitragen.
Im Jahr 2025 wird der Markt für zirkonia-keramische AM auf mehrere Hundert Millionen USD geschätzt, mit einer voraussichtlichen jährlichen Wachstumsrate (CAGR), die im zweistelligen Bereich liegt bis 2030. Dieses Wachstum wird durch die zunehmende Verfügbarkeit von industriellen Zirkonia-Pulvern und -Schlämmen, die für additive Prozesse wie Stereolithographie (SLA), digitale Lichtverarbeitung (DLP) und Bindemittel-Jetting optimiert sind, unterstützt. Unternehmen wie 3D Systems und Stratasys entwickeln und vermarkten aktiv keramische AM-Lösungen, während spezialisierte Firmen wie Lithoz GmbH und CeramTec sich auf hochleistungsfähige keramische Materialien und spezielle AM-Plattformen konzentrieren.
Der Zahnarztsektor bleibt der größte Endverbraucher von Zirkonia-AM, wobei dentalen Kronen, Brücken und Implantate, die über additive Fertigung hergestellt werden, eine überlegene Passform und verkürzte Vorlaufzeiten im Vergleich zu herkömmlichen Methoden bieten. Lithoz GmbH hat einen signifikanten Anstieg der Nachfrage nach seiner LCM (Lithographie-basierten Keramikfertigung) Technologie gemeldet, die die Produktion dichter, hochpräziser Zirkonia-Teile ermöglicht, die für medizinische und zahnmedizinische Anwendungen geeignet sind. Inzwischen erweitert CeramTec sein Portfolio an fortschrittlichen keramischen Komponenten sowohl für medizinische als auch für industrielle Anwendungen und nutzt additive Fertigung zur Bewältigung komplexer Geometrien und Anpassungen.
Mit Blick in die Zukunft wird die Marktentwicklung durch fortlaufende F&E-Investitionen und den Eintritt neuer Akteure, insbesondere in Asien und Nordamerika, gestützt. In den nächsten Jahren werden weitere Verbesserungen bei der Prozesszuverlässigkeit, der Skalierbarkeit der Teilegrößen und der Automatisierung der Nachbearbeitung erwartet, die dazu beitragen werden, Kosten zu senken und die Akzeptanz zu verbreitern. Darüber hinaus wird erwartet, dass Kooperationen zwischen Herstellern von AM-Hardware und Lieferanten keramischer Materialien die Entwicklung von schlüsselfertigen Lösungen für Zirkonia beschleunigen werden. Da sich die regulatorischen Wege für medizinische und zahnmedizinische Geräte klären und industrielle Anwender nach leichten, hochleistungsfähigen Alternativen zu Metallen suchen, wird die additive Fertigung von Zirkonia-Keramik bis 2030 zu einer gängigen Produktionstechnologie werden.
Technologische Innovationen in der Zirkonia-Keramischen 3D-Druck
Die additive Fertigung (AM) mit Zirkonia-Keramik erlebt rapide technologische Fortschritte, während der Sektor ins Jahr 2025 übergeht, angetrieben durch die Nachfrage nach hochleistungsfähigen Keramiken in medizinischen, zahnmedizinischen und industriellen Anwendungen. Die außergewöhnliche mechanische Festigkeit, Bruchzähigkeit und Biokompatibilität von Zirkonia machen sie zu einem bevorzugten Material für den 3D-Druck komplexer, hochqualitativer Komponenten.
Eine der bedeutendsten Innovationen ist die Verfeinerung der Verfahren zur Behälter-Photopolymerisation und zum Bindemittel-Jetting, die speziell für Zirkonia entwickelt wurden. Unternehmen wie Lithoz GmbH haben die LCM (Lithographie-basierte Keramikfertigung) herausgebracht, die die Herstellung dichter, hochpräziser Zirkonia-Teile mit komplexen Geometrien ermöglicht. Ihre Systeme werden in der Zahn- und medizinischen Geräteherstellung weitgehend übernommen, wo Genauigkeit und Materialeigenschaften kritisch sind. Ähnlich hat 3DCeram die Stereolithographie (SLA) für technische Keramiken weiterentwickelt und bietet schlüsselfertige Lösungen für die industrielle Produktion von Zirkonia-Teilen an.
Die Materialentwicklung ist ein weiterer Schwerpunktbereich. Die Einführung von vorkeramischen Harzen und optimierten Zirkonia-Schlämmen hat die Druckfähigkeit und die Ergebnisse der Nachbearbeitung verbessert. CeramTec, ein global führendes Unternehmen im Bereich fortschrittlicher Keramiken, entwickelt aktiv neue Zirkonia-Formulierungen für die additive Fertigung, die eine verbesserte Dichte und mechanische Leistung nach dem Sintern anvisieren. Diese Innovationen sollen die Kluft zwischen konventionell gefertigten und additiv gefertigten Zirkonia-Komponenten verringern.
Hybride Fertigungsansätze sind ebenfalls im Kommen, wobei additive und subtraktive Techniken kombiniert werden, um überlegene Oberflächenqualitäten und dimensionale Toleranzen zu erreichen. XJet hat seine NanoParticle Jetting™-Technologie commercialisiert, die die Produktion hochdetaillierter Zirkonia-Teile mit minimaler Nachbearbeitung ermöglicht. Diese Technologie gewinnt an Bedeutung im Zahnarztsektor, wo patientenspezifische Implantate und Restaurationen sowohl Präzision als auch Biokompatibilität erfordern.
Mit einem Blick in die Zukunft ist die Perspektive für Zirkonia-Keramik AM robust. Die laufende Miniaturisierung von medizinischen Geräten, der Anstieg der personalisierten Gesundheitsversorgung und der Bedarf an leichten, langlebigen industriellen Komponenten werden voraussichtlich die Akzeptanz weiter vorantreiben. Branchenführer investieren in Automatisierung, Inline-Qualitätskontrolle und skalierbare Produktionssysteme, um die steigende Nachfrage zu decken. Da immer mehr Unternehmen, wie 3DCeram und Lithoz GmbH, ihre globale Reichweite und Anwendungsportfolios erweitern, steht die Zirkonia-Keramische 3D-Drucktechnologie bereit, in den kommenden Jahren zu einer gängigen Fertigungstechnologie zu werden.
Wichtige Akteure und strategische Partnerschaften
Der Sektor der Zirkonia-Keramischen Additiven Fertigung (AM) im Jahr 2025 ist geprägt von einem dynamischen Zusammenspiel etablierter Keramikkhersteller, innovativer AM-Technologieanbieter und strategischer Kooperationen, die darauf abzielen, die Produktion zu skalieren und die Anwendungsgebiete zu erweitern. Mehrere wichtige Akteure gestalten die Wettbewerbslandschaft, indem sie proprietäre Technologien nutzen und Partnerschaften schmieden, um die Akzeptanz von zirkonium-basiertem 3D-Druck zu beschleunigen.
Unter den bedeutendsten Unternehmen sticht 3D Systems mit seinen Investitionen in keramische AM, einschließlich Zirkonia, über seine Figure 4-Plattform und kontinuierliche Materialentwicklung hervor. Das Unternehmen arbeitet mit Industriepartnern zusammen, um Arbeitsabläufe für zahnmedizinische, medizinische und industrielle Anwendungen zu optimieren, was einen breiteren Trend widerspiegelt, sich auf hochwertige, präzisionsfordernde Sektoren zu konzentrieren.
Ein weiterer wichtiger Akteur ist Lithoz GmbH, ein österreichischer Spezialist für keramisches 3D-Drucken. Die LCM-Technologie (Lithographie-basierte Keramikfertigung) von Lithoz ist weithin anerkannt für ihre Fähigkeit, dichte, hochfeste Zirkonia-Teile zu produzieren. Das Unternehmen hat Partnerschaften mit führenden Keramikkherstellern und Forschungseinrichtungen etabliert, um die Nutzung von Zirkonia in zahnmedizinischen, biomedizinischen und ingenieurtechnischen Anwendungen auszubauen. Das globale Netzwerk von Kunden und Partnern von Lithoz positioniert es als zentralen Knotenpunkt im Zirkonia-AM-Ökosystem.
In Asien ist die Tosoh Corporation ein bedeutender Anbieter von Zirkonia-Pulvern und hat aktiv die Entwicklung druckbarer Zirkonia-Materialien für AM-Prozesse unterstützt. Die Kooperationen von Tosoh mit Druckerherstellern und Endbenutzern zielen darauf ab, die Materialkonsistenz und -leistung sicherzustellen, die für den Ausbau der Produktion in regulierten Branchen wie dem Gesundheitswesen entscheidend sind.
Strategische Partnerschaften werden zunehmend häufiger, da Unternehmen bestreben, Fachwissen in Materialwissenschaft, Druckhardware und Anwendungsengineering zu kombinieren. CeramTec, ein globaler Marktführer im Bereich fortschrittlicher Keramiken, hat an gemeinsamen Entwicklungsprojekten mit AM-Technologieanbietern gearbeitet, um die Qualifikation von Zirkonia-Komponenten für medizinische und industrielle Anwendungen zu beschleunigen. Ähnlich avanciert XJet mit seiner NanoParticle Jetting-Technologie für Keramiken, einschließlich Zirkonia, und hat Kooperationen mit zahnmedizinischen und industriellen Partnern angekündigt, um neue Anwendungen zu validieren.
Blickt man in die Zukunft, wird in den nächsten Jahren mit weiteren Konsolidierungen und bereichsübergreifenden Allianzen gerechnet, da Unternehmen darauf abzielen, Herausforderungen in Bezug auf Skalierung, Kosten und regulatorische Konformität anzugehen. Die Konvergenz von Materiallieferanten, Innovatoren der AM-Hardware und Endnutzerindustrien wird voraussichtlich die Reifung der zirkonia-keramischen additiven Herstellung vorantreiben, wobei wichtige Akteure weiterhin in F&E und strategische Partnerschaften investieren, um ihre Wettbewerbsfähigkeit zu sichern.
Emerging Applications: Medizin, Luft- und Raumfahrt sowie Elektronik
Die additive Fertigung (AM) mit Zirkonia-Keramik schreitet schnell voran, und 2025 wird voraussichtlich ein entscheidendes Jahr für ihre Akzeptanz in hochwertigen Sektoren wie Medizin, Luft- und Raumfahrt sowie Elektronik sein. Die einzigartigen Eigenschaften von Zirkonia – außergewöhnliche Festigkeit, Bruchzähigkeit und Biokompatibilität – treiben ihre Integration in Anwendungen voran, in denen traditionelle Fertigungsmethoden an Grenzen stoßen.
Im medizinischen Bereich revolutioniert Zirkonia AM die Produktion von Zahnimplantaten, Prothesen und chirurgischen Instrumenten. Die Fähigkeit, patientenspezifische Geometrien mit hoher Präzision zu fabrizieren, ist besonders wertvoll. Unternehmen wie 3D Systems und CeramTec entwickeln und liefern aktiv zirkonia-basiertes AM-Lösungen für zahnmedizinische und orthopädische Anwendungen. Diese Lösungen ermöglichen die Schaffung komplexer, maßgeschneiderter Implantate, die im Vergleich zu Metallalternativen eine verbesserte Osseointegration und Langlebigkeit bieten. Es wird erwartet, dass dieser Trend sich beschleunigt, während sich die regulatorischen Wege für 3D-gedruckte medizinische Keramiken in den nächsten Jahren stärker etablieren.
Die Luft- und Raumfahrt ist ein weiterer Sektor, der zunehmend Zirkonia AM annimmt. Die hohe Temperaturstabilität und der Widerstand gegen thermischen Schock machen das Material ideal für Komponenten wie Turbinenschaufeln, thermische Barrierebeschichtungen und Sensor-Gehäuse. Oxford Instruments und XJet sind unter den Technologieanbietern, die es Luft- und Raumfahrt-Herstellern ermöglichen, komplexe Zirkonia-Teile zu prototypisieren und zu produzieren, die zuvor nicht machbar waren. In den nächsten Jahren ist mit einer weiteren Integration von Zirkonia AM in Antriebssystemen und hyperschallfähigen Fahrzeugkomponenten zu rechnen, da die Branche nach leichteren, langlebigeren Materialien sucht, um die Kraftstoffeffizienz und Leistung zu verbessern.
In der Elektronik fördern der Miniaturisierungstrend und die Nachfrage nach leistungsstarken Substraten das Interesse an Zirkonia AM. Die elektrische Isolierung, thermische Leitfähigkeit und chemische Inertheit von Zirkonia machen es geeignet für Substrate, Isolatoren und Sensorbauteile. Die Tosoh Corporation, ein wichtiger Anbieter von Zirkonia-Pulvern, arbeitet mit Herstellern von AM-Systemen zusammen, um die Rohstoffe für elektronische Anwendungen zu optimieren. In den kommenden Jahren werden Fortschritte im Mehrmaterialdruck und der Integration von Zirkonia mit leitfähigen Tinten erwartet, was die Herstellung komplexer, multifunktionaler elektronischer Geräte ermöglicht.
Mit einem Blick in die Zukunft ist die Perspektive für die additive Fertigung von Zirkonia-Keramik robust. Während sich Materialformulierungen, Drucktechnologien und Nachbearbeitungsmethoden weiterentwickeln, wird sich das Anwendungsspektrum in den Bereichen Medizin, Luft- und Raumfahrt sowie Elektronik erweitern. Branchenführer investieren in die Skalierung der Produktion und die Qualifikation von AM-Zirkonia-Teilen für kritische Endanwendungen, was einen Wandel von der Prototypenfertigung hin zur Massenproduktion bis Ende der 2020er Jahre signalisiert.
Lieferkette und Rohstoffüberlegungen
Die Lieferkette für die additive Fertigung (AM) mit Zirkonia-Keramik entwickelt sich rapide, da die Nachfrage nach fortschrittlichen Keramiken in leistungsstarken Anwendungen wächst. Im Jahr 2025 ist der Sektor durch ein reifendes Ecosystem von Pulverliferanten, Geräteherstellern und Endverbrauchern geprägt, mit einem Fokus auf die Sicherstellung der Materialqualität, -konsistenz und -skalierbarkeit.
Zirkonia (Zirkoniumdioxid, ZrO₂) wird für ihre außergewöhnliche mechanische Festigkeit, Bruchzähigkeit und chemische Stabilität geschätzt, was sie zu einem bevorzugten Material für zahnmedizinische, medizinische und industrielle Bauteile macht. Die Lieferkette beginnt mit dem Abbau und der Raffinierung von Zirkonmineralien, die hauptsächlich aus Australien, Südafrika und China stammen. Diese Rohstoffe werden zu hochreinen Zirkonia-Pulvern verarbeitet, die dann für additive Fertigungsprozesse wie Stereolithographie (SLA), digitale Lichtverarbeitung (DLP) und Bindemittel-Jetting angepasst werden.
Zu den Hauptlieferanten von Zirkonia-Pulvern für AM gehören die Tosoh Corporation, ein globaler Marktführer im Bereich fortschrittlicher Keramiken, und 3DCeram, das sich auf druckbereite Keramikschlämme spezialisiert hat. Die Tosoh Corporation ist bemerkenswert für ihre yttria-stabilisierten Zirkonia-Pulver (YSZ), die aufgrund ihrer überlegenen Eigenschaften und ihrer Konsistenz von Charge zu Charge sowohl in der traditionellen als auch in der additiven Fertigung weit verbreitet sind. 3DCeram liefert nicht nur Materialien, sondern entwickelt auch AM-Systeme und Lösungen zur Nachbearbeitung, was eine vertikal integrierte Lieferkette unterstützt.
Auf der Geräte-Seite verbessern Unternehmen wie Lithoz GmbH und CeramTec die Fähigkeiten des keramischen 3D-Drucks. Lithoz GmbH bietet LCM (Lithographie-basierte Keramikfertigung) Systeme an, die für Zirkonia optimiert sind, während CeramTec sein AM-Portfolio erweitert, um den industriellen Produktionsanforderungen gerecht zu werden. Diese Hersteller arbeiten zunehmend mit Pulverliferanten zusammen, um Prozesskompatibilität und Reproduzierbarkeit zu gewährleisten.
Die Resilienz der Lieferkette ist ein wachsendes Anliegen, insbesondere im Hinblick auf geopolitische Spannungen und die Konzentration der Zirkoniummineralressourcen. Unternehmen investieren in alternative Beschaffungsstrategien und Recyclinginitiativen, um Risiken zu mindern. Beispielsweise untersucht die Tosoh Corporation das geschlossene Recycling von Zirkonia-Abfällen aus AM-Prozessen, um die Abhängigkeit von neuem Rohmaterial zu verringern.
Mit Blick in die Zukunft sind die Aussichten für die Lieferketten der Zirkonia-Keramik-AM in den kommenden Jahren positiv, mit einem voraussichtlichen Wachstum sowohl bei der Verfügbarkeit von Materialien als auch bei der Prozessautomatisierung. Branchenbeteiligte werden voraussichtlich digitale Rückverfolgbarkeit, Qualitätssicherung und nachhaltige Beschaffungspraktiken priorisieren müssen, um den strengen Anforderungen der Gesundheits- und Luft- und Raumfahrtindustrie gerecht zu werden. Wenn die additive Fertigung von Zirkonia-Komponenten zunimmt, werden Partnerschaften zwischen Pulverproduzenten, Druckerherstellern und Endbenutzern entscheidend sein, um eine robuste und reaktionsfähige Lieferkette zu gewährleisten.
Regulatorische Landschaft und Branchenstandards
Die regulatorische Landschaft und die Branchenstandards für die additive Fertigung (AM) von Zirkonia-Keramik entwickeln sich schnell weiter, während die Technologie reift und die Akzeptanz in Sektoren wie Zahnmedizin, Medizin und industriellen Anwendungen zunimmt. Im Jahr 2025 intensivieren die Regulierungsbehörden und Branchenorganisationen die Bemühungen, klare Rahmenbedingungen zu schaffen, die die Sicherheit, Zuverlässigkeit und Qualität von Zirkonia-AM-Teilen insbesondere für kritische Anwendungen gewährleisten.
Im medizinischen und zahnmedizinischen Sektor werden Zirkonia-Keramiken aufgrund ihrer Biokompatibilität und mechanischen Festigkeit weitgehend für Implantate, Kronen und Prothesen eingesetzt. Die regulatorische Aufsicht wird überwiegend von Behörden wie der U.S. Food and Drug Administration (FDA) und der European Medicines Agency (EMA) geregelt, die strenge Validierungen sowohl der Materialien als auch der Fertigungsprozesse erfordern. Die additive Fertigung bringt neue Variablen mit sich – wie die schichtweise Fabrikation und Nachbearbeitung – die aktualisierte Richtlinien erforderlich machen. Im Jahr 2024 und 2025 hat die FDA weiterhin ihren Ansatz zur AM verfeinert, wobei der Fokus auf Prozessvalidierung, Rückverfolgbarkeit und Materialcharakterisierung für keramische Geräte liegt. Die Internationale Organisation für Normung (ISO) hat auch Standards wie ISO 13356 (für yttria-stabilisierte Zirkonia) aktualisiert und arbeitet an spezifischen AM-Standards unter der ISO/ASTM 52900-Serie, die Terminologie, Tests und Qualifizierung für AM-Teile betreffen.
Branchengrößen nehmen aktiv an der Entwicklung und Einhaltung von Standards teil. 3D Systems, ein wichtiger Akteur im Bereich keramische AM, arbeitet mit Regulierungsbehörden und Normungsorganisationen zusammen, um sicherzustellen, dass seine zahnmedizinischen und medizinischen Zirkonia-Lösungen den sich entwickelnden Anforderungen entsprechen. XJet, bekannt für seine NanoParticle Jetting-Technologie, ist ebenfalls an Qualifikationsprozessen für seine Zirkonia-AM-Teile beteiligt, insbesondere für zahnmedizinische und industrielle Kunden. Lithoz, ein Spezialist für keramischen 3D-Druck, hat zu den Entwicklungen von Prozessvalidierungsprotokollen beigetragen und arbeitet mit Partnern zusammen, um die Einhaltung sowohl der ISO- als auch der FDA-Richtlinien zu gewährleisten.
Mit Blick in die Zukunft wird in den nächsten Jahren mit einer weiteren Harmonisierung der Standards gerechnet, wobei der Fokus auf der Überwachung im Prozess, digitalen Rückverfolgbarkeit und dem Lebenszyklusmanagement von Zirkonia-AM-Komponenten liegt. Branchenkonsortien und Arbeitsgruppen, wie die von ASTM International koordinierte, beschleunigen die Erstellung von Best Practices und Qualifizierungswegen. Mit der Verbesserung der regulatorischen Klarheit wird die Akzeptanz der Zirkonia-keramischen AM voraussichtlich beschleunigt, insbesondere in regulierten Branchen, in denen die Zertifizierung eine Voraussetzung für den Marktzugang ist.
Wettbewerbsanalyse: Stärken, Schwächen und Differenzierungsmerkmale
Die Wettbewerbslandschaft der zirkonia-keramischen additiven Fertigung (AM) im Jahr 2025 wird von einer ausgewählten Gruppe von Technologieführern, etablierten Keramikproduzenten und innovativen Startups geprägt. Der Sektor ist durch rasante Fortschritte in der Materialwissenschaft, Prozessoptimierung und anwendungsspezifischen Lösungen gekennzeichnet, mit einem Fokus auf zahnmedizinischen, medizinischen und industriellen Komponenten.
Stärken im Zirkonia-AM-Sektor ergeben sich aus den außergewöhnlichen mechanischen Eigenschaften des Materials – hohe Bruchzähigkeit, Verschleißfestigkeit und Biokompatibilität – die es ideal für anspruchsvolle Anwendungen machen. Unternehmen wie 3D Systems und XJet haben proprietäre Technologien für hochdichte, hochpräzise Zirkonia-Teile entwickelt. 3D Systems nutzt seine Figure 4-Plattform für zahnmedizinische Zirkonia, während XJet’s NanoParticle Jetting komplexe Geometrien und feine Details ermöglicht. Lithoz, ein österreichischer Pionier, ist anerkannt für seinen LCM (Lithographie-basierte Keramikfertigung)-Prozess, der dichte, hochfeste Zirkonia-Komponenten für medizinische und industrielle Anwendungen liefert. Diese Unternehmen profitieren von robusten F&E, etablierten Kundenbasen und validierten Produktionsabläufen.
Schwächen bestehen insbesondere hinsichtlich Durchsatz, Skalierbarkeit und Kosten. Zirkonia-AM-Prozesse erfordern häufig Nachbearbeitungsmaßnahmen wie Entbinder und Sintern, die die Vorlaufzeiten verlängern und Variabilität einführen können. Die Materialkosten bleiben im Vergleich zur traditionellen Fertigung hoch, und der Bedarf an spezialisierten Geräten schränkt die Zugänglichkeit für kleinere Unternehmen ein. Darüber hinaus ist die Qualifizierung und Zertifizierung von AM-Zirkonia-Teilen für regulierte Industrien (z. B. medizinische Implantate) ein langwieriger und ressourcenintensiver Prozess, der eine Barriere für die schnelle Akzeptanz darstellt.
Differenzierungsmerkmale zwischen Wettbewerbern sind zunehmend durch Prozessinnovation, Anwendungsfokus und Ökosystemintegration definiert. XJet hebt sich durch seinen supportfreien Druck und die Fähigkeit hervor, komplexe interne Kanäle zu produzieren, was neue Designmöglichkeiten eröffnet. Lithoz’s LCM-Technologie ist bemerkenswert für ihre hohe Auflösung und Eignung sowohl für Prototypen als auch für die Serienproduktion. 3D Systems nutzt seine globale Reichweite und Partnerschaften mit zahnmedizinischen Labors, um die Akzeptanz in der digitalen Zahnmedizin zu beschleunigen. In der Zwischenzeit kooperieren Unternehmen wie CeramTec und Tosoh – bedeutende Anbieter von Zirkonia-Pulvern – zunehmend mit AM-Hardwareanbietern, um die Materialformulierungen für additive Prozesse zu optimieren.
Mit Blick in die Zukunft wird der Wettbewerbsvorteil voraussichtlich davon abhängen, inwieweit validierte, Endanwendungszirkonia-Teile in großem Maßstab mit optimierten Arbeitsabläufen und kosteneffektiven Lösungen geliefert werden können. Strategische Partnerschaften zwischen Materiallieferanten, Druckerherstellern und Endbenutzern werden voraussichtlich zunehmen und im kommenden Jahr weitere Innovationen und Marktdurchdringung vorantreiben.
Nachhaltigkeit und Umweltimpact
Die Zirkonia-keramische additive Fertigung (AM) gewinnt im Jahr 2025 als nachhaltige Alternative zur traditionellen Keramikverarbeitung an Bedeutung, angetrieben sowohl durch Umweltvorschriften als auch durch die Nachfrage der Industrie nach umweltfreundlicheren Produktionsmethoden. Das Nachhaltigkeitsprofil von Zirkonia AM wird durch mehrere Faktoren geprägt, darunter Materialeffizienz, Energieverbrauch, Abfallreduktion und Recyclierbarkeit.
Ein wesentlicher Umweltvorteil von Zirkonia AM ist die Fähigkeit, Materialabfälle zu minimieren. Im Gegensatz zur subtraktiven Fertigung, die häufig erhebliche Abfälle produziert, verwenden AM-Verfahren wie Stereolithographie (SLA), digitale Lichtverarbeitung (DLP) und Bindemittel-Jetting nur das Material, das erforderlich ist, um das Teil zu erstellen. Führende Hersteller wie 3DCeram und Lithoz haben proprietäre Verfahren entwickelt, die die Verwendung von Pulvern optimieren und das Recycling von ungenutztem Zirkonia-Pulver ermöglichen, wodurch die Abfallströme weiter reduziert werden.
Der Energieverbrauch ist ein weiterer kritischer Aspekt. Während das Sintern energieintensiv bleibt, helfen Fortschritte in der AM-Prozesskontrolle und die Verwendung effizienterer Öfen, den gesamten Energiefußabdruck zu senken. Unternehmen wie CeramTec und XJet investieren in Forschung, um die Effizienz des Sinterns zu verbessern und die Zykluszeiten zu reduzieren, was voraussichtlich in den nächsten Jahren zu schrittweisen Nachhaltigkeitsgewinnen führen wird.
Der Wasserverbrauch und die Emissionen sind ebenfalls geringer im AM im Vergleich zur herkömmlichen keramischen Fertigung, die häufig mit Nassmahlung und umfangreicher Nachbearbeitung verbunden ist. Der schichtweise Ansatz des AM reduziert den Bedarf an wasserbasierten Prozessen und minimiert die Freisetzung von Partikeln und flüchtigen organischen Verbindungen (VOCs). Dies steht im Einklang mit den Umweltzielen großer Keramikhersteller wie Tosoh, die hochreine Zirkonia-Pulver liefern und aktiv nachhaltige Praktiken in ihrer Lieferkette fördern.
Mit Blick in die Zukunft sind die Perspektiven für Nachhaltigkeit in der Zirkonia-keramischen AM positiv. Branchenkooperationen und Standardisierungsanstrengungen, wie sie von The American Ceramic Society geleitet werden, werden voraussichtlich die Einführung von Best Practices und Lebenszyklusbewertungsmethodologien beschleunigen. Wenn die regulatorischen Anforderungen zunehmen und die Endbenutzer umweltfreundlichere Lösungen fordern, werden die Hersteller voraussichtlich in geschlossene Recyclingverfahren, die Integration erneuerbarer Energiequellen und umweltfreundliche Bindemittelsysteme investieren. Bis 2027 wird erwartet, dass Zirkonia AM neue Maßstäbe für nachhaltige fortschrittliche Keramikfertigung setzen wird und sowohl der Umweltschutz als auch die wirtschaftliche Wettbewerbsfähigkeit unterstützt.
Zukünftige Perspektiven: Chancen, Herausforderungen und strategische Empfehlungen
Die zukünftige Perspektive für die Zirkonia-keramische additive Fertigung (AM) im Jahr 2025 und in den kommenden Jahren wird von einem dynamischen Zusammenspiel technologischer Fortschritte, Marktchancen und anhaltender Herausforderungen geprägt. Mit der wachsenden Nachfrage nach hochleistungsfähigen Keramiken über Sektoren hinweg, wie Zahnmedizin, Medizin, Luft- und Raumfahrt und Elektronik, positionieren sich die einzigartigen Eigenschaften von Zirkonia – außergewöhnliche Festigkeit, Bruchzähigkeit und Biokompatibilität – als Material der Wahl für zukünftige AM-Anwendungen.
Wichtige Branchenakteure intensivieren ihren Fokus auf die Skalierung der Produktion und die Verbesserung der Prozesszuverlässigkeit. 3D Systems und XJet sind hervorzuheben für ihre laufenden Investitionen in Bindemittel-Jetting- und Nanopartikel-Jetting-Technologien, die es ermöglichen, dichte, komplexe Zirkonia-Teile mit feiner Detailauflösung herzustellen. Lithoz, ein Pionier in der keramischen Stereolithographie, erweitert weiterhin sein Portfolio und zielt sowohl auf industrielle als auch auf medizinische Märkte mit neuen Druckermodellen und Materialformulierungen ab. Von diesen Unternehmen wird erwartet, dass sie die Akzeptanz weiter vorantreiben, indem sie Durchsatz- und Kostenbarrieren angehen.
Es gibt zahlreiche Chancen im zahnmedizinischen Sektor, wo Zirkonia AM bereits die traditionelle subtraktive Fertigung disruptiert. Die Fähigkeit, patientenspezifische Kronen, Brücken und Implantate mit weniger Materialabfall und schnellerer Bearbeitung herzustellen, beschleunigt die Akzeptanz. CeramTec und Ivoclar nutzen AM, um maßgeschneiderte Zahnmedizinlösungen anzubieten, und fortlaufende Kooperationen mit zahnmedizinischen Laboren werden voraussichtlich 2025 zunehmen. Im Bereich Luft- und Raumfahrt und Elektronik wird der Antrieb nach leichten, thermisch stabilen und elektrisch isolierenden Komponenten voraussichtlich neue Märkte für Zirkonia AM eröffnen, insbesondere da die Qualifizierungsstandards reifen.
Es bleiben jedoch Herausforderungen. Das Erreichen konsistenter Dichte, Minimierung von Defekten und Gewährleistung reproduzierbarer mechanischer Eigenschaften sind laufende technische Hürden. Die Nachbearbeitung, einschließlich Entbinder und Sintern, erhöht die Komplexität und die Kosten, insbesondere bei größeren oder komplexen Teilen. Die Materialkosten für hochreine Zirkonia-Pulver bleiben ebenfalls eine Einschränkung, obwohl eine zunehmende Konkurrenz unter Lieferanten wie Tosoh und Kyocera im Laufe der Zeit dazu beitragen könnte, die Preise zu moderieren.
Strategische Empfehlungen für Interessengruppen umfassen Investitionen in Prozessautomatisierung, Inline-Qualitätsüberwachung und digitale Workflow-Integration, um die Skalierbarkeit und Rückverfolgbarkeit zu verbessern. Partnerschaften zwischen Herstellern von AM-Technologien, Materiallieferanten und Endnutzern werden entscheidend sein, um die Qualifikations- und Standardisierungsanstrengungen zu beschleunigen. Während sich die regulatorischen Rahmenbedingungen für medizinische und Luft- und Raumfahrtanwendungen weiterentwickeln, wird proaktive Zusammenarbeit mit Branchenverbänden und Zertifizierungsstellen entscheidend für den Marktzugang sein.
Zusammenfassend lässt sich sagen, dass die zirkonia-keramische additive Fertigung im Jahr 2025 und darüber hinaus vor einem signifikanten Wachstum steht, angetrieben durch Innovationen, sich erweiternde Anwendungsbereiche und ein reifendes Ökosystem. Unternehmen, die Prozessoptimierung, Zusammenarbeit und regulatorische Bereitschaft priorisieren, werden am besten positioniert sein, um von den sich ergebenden Chancen zu profitieren.