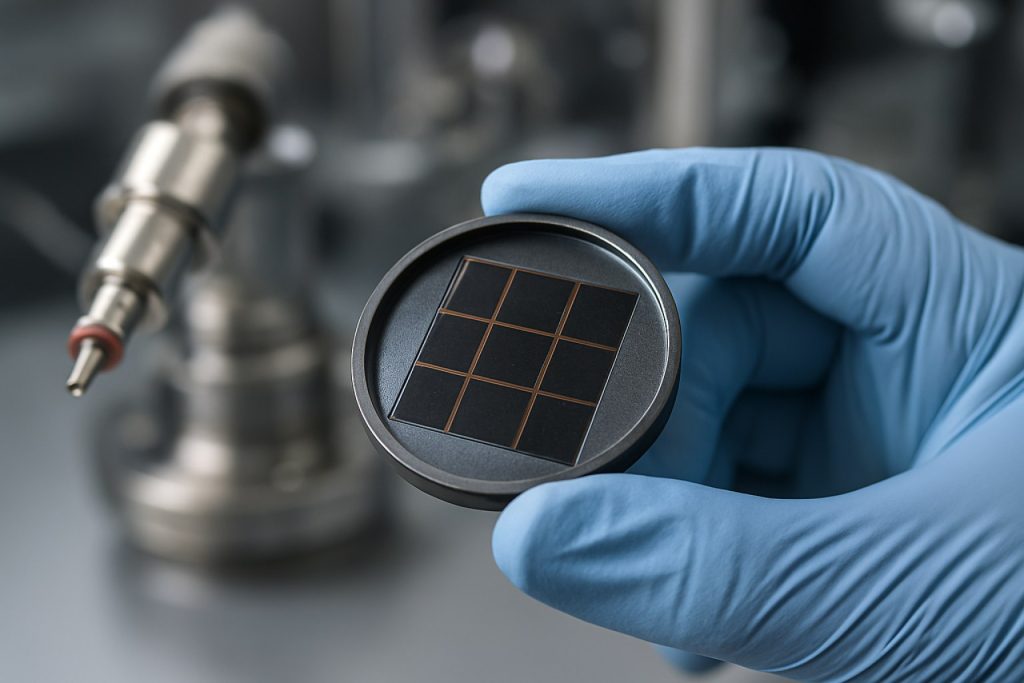
Revolutionizing Electrochemistry: The 2025 Outlook for Conductive Diamond Electrodes Manufacturing. Explore Market Growth, Breakthrough Technologies, and Strategic Opportunities Shaping the Next Five Years.
- Executive Summary: Key Trends and 2025 Market Snapshot
- Global Market Size, Growth Rate, and 2025–2030 Forecasts
- Technological Innovations in Conductive Diamond Electrode Manufacturing
- Major Players and Competitive Landscape (e.g., element6.com, neocoat.ch, sp3inc.com)
- Raw Materials, Supply Chain, and Sustainability Initiatives
- Emerging Applications: Water Treatment, Sensors, and Energy Storage
- Regulatory Environment and Industry Standards (e.g., ieee.org, iec.ch)
- Regional Analysis: North America, Europe, Asia-Pacific, and Rest of World
- Investment, M&A Activity, and Strategic Partnerships
- Future Outlook: Disruptive Trends and Market Opportunities Through 2030
- Sources & References
Executive Summary: Key Trends and 2025 Market Snapshot
The manufacturing of conductive diamond electrodes is entering a pivotal phase in 2025, marked by rapid technological advancements, increased industrial adoption, and strategic investments from leading players. These electrodes, primarily based on boron-doped diamond (BDD) films, are gaining traction due to their exceptional chemical stability, wide electrochemical window, and resistance to fouling, making them highly desirable for applications in water treatment, electroanalysis, and advanced oxidation processes.
Key trends shaping the sector include the scaling up of chemical vapor deposition (CVD) techniques, which enable the production of high-quality, large-area diamond films at lower costs. Companies such as Element Six—a subsidiary of the De Beers Group and a global leader in synthetic diamond materials—are at the forefront, leveraging proprietary CVD processes to supply BDD electrodes for both research and industrial markets. Element Six continues to expand its manufacturing capabilities, with a focus on improving electrode uniformity and scalability.
Another significant player, Advent Diamond, is advancing the integration of diamond electrodes into microelectronic and sensor platforms, targeting high-value applications in harsh environments. Their efforts are complemented by Neocoat, a Swiss company specializing in custom BDD electrode fabrication, which is expanding its product portfolio to address growing demand in environmental monitoring and industrial electrochemistry.
In 2025, the market is witnessing increased collaboration between manufacturers and end-users, particularly in the water treatment sector, where BDD electrodes are being deployed for the electrochemical destruction of persistent organic pollutants and disinfection. Partnerships with water technology firms and utilities are accelerating pilot projects and commercial rollouts, especially in regions with stringent environmental regulations.
Looking ahead, the outlook for conductive diamond electrode manufacturing is robust. Industry forecasts anticipate double-digit annual growth rates over the next few years, driven by the convergence of regulatory pressures, sustainability goals, and the need for advanced materials in energy and environmental technologies. Manufacturers are investing in automation, quality control, and process optimization to meet rising demand and ensure consistent electrode performance.
In summary, 2025 marks a year of significant momentum for conductive diamond electrode manufacturing, with established leaders like Element Six, innovators such as Advent Diamond, and specialized suppliers like Neocoat driving the sector forward through technological innovation, capacity expansion, and strategic partnerships.
Global Market Size, Growth Rate, and 2025–2030 Forecasts
The global market for conductive diamond electrodes, particularly those based on boron-doped diamond (BDD) technology, is poised for significant growth between 2025 and 2030. This expansion is driven by increasing demand in water treatment, electrochemical sensing, and advanced oxidation processes, where the unique properties of diamond electrodes—such as chemical inertness, wide potential window, and high durability—offer clear advantages over traditional materials.
As of 2025, the market is characterized by a relatively concentrated landscape, with a handful of specialized manufacturers leading innovation and production. Key players include Element Six (a De Beers Group company), which is widely recognized for its industrial synthetic diamond expertise and supplies BDD electrodes for both research and industrial applications. Advent Diamond is another notable manufacturer, focusing on high-performance diamond materials for electronics and electrochemistry. NeoCoat, based in Switzerland, specializes in the chemical vapor deposition (CVD) process for producing high-quality BDD electrodes, serving both laboratory and industrial markets.
Recent years have seen increased investment in scaling up manufacturing capacity and improving deposition techniques, such as microwave plasma-assisted CVD, to meet growing demand. For example, Element Six has expanded its production capabilities to supply larger-area electrodes and custom geometries, addressing the needs of water treatment plants and electrochemical reactors. Similarly, NeoCoat has reported advances in electrode uniformity and doping control, which are critical for consistent performance in industrial-scale applications.
Market growth rates for conductive diamond electrodes are projected to exceed 8% annually through 2030, with the Asia-Pacific region expected to be a major driver due to rapid industrialization and stringent environmental regulations. The adoption of BDD electrodes in municipal and industrial wastewater treatment is particularly notable, as these systems require robust, long-lasting materials capable of withstanding harsh chemical environments.
Looking ahead, the sector is likely to benefit from ongoing R&D into lower-cost manufacturing methods and the integration of diamond electrodes into next-generation electrochemical devices. Companies such as Advent Diamond are exploring new applications in energy storage and biomedical sensing, which could further expand the addressable market. As manufacturing processes mature and economies of scale are realized, the cost per unit is expected to decrease, making conductive diamond electrodes more accessible for a wider range of industries.
Technological Innovations in Conductive Diamond Electrode Manufacturing
The manufacturing of conductive diamond electrodes is experiencing significant technological advancements as the industry moves into 2025. These electrodes, primarily based on boron-doped diamond (BDD), are valued for their exceptional chemical stability, wide potential window, and low background current, making them highly desirable for applications in electrochemical sensing, water treatment, and advanced oxidation processes.
A key innovation in recent years has been the refinement of chemical vapor deposition (CVD) techniques, particularly microwave plasma-assisted CVD (MPCVD), which enables the controlled growth of high-purity, uniform diamond films on various substrates. Companies such as Element Six, a subsidiary of De Beers Group, have been at the forefront of scaling up CVD processes to produce both polycrystalline and single-crystal BDD electrodes with tailored properties for industrial and research applications. Their ongoing investments in reactor design and process automation are expected to further improve throughput and consistency in 2025.
Another notable trend is the development of large-area and three-dimensional (3D) electrode architectures. Manufacturers like Advent Diamond are leveraging advanced lithography and etching techniques to fabricate micro- and nano-structured diamond surfaces, which significantly increase the effective surface area and enhance electrochemical performance. These innovations are particularly relevant for high-demand applications such as wastewater treatment and energy storage, where electrode efficiency and durability are critical.
Material integration is also advancing, with companies such as sp3 Diamond Technologies focusing on the deposition of BDD films onto non-traditional substrates, including metals and ceramics. This expands the range of possible device configurations and enables the production of electrodes with improved mechanical robustness and application-specific geometries.
Automation and quality control are becoming increasingly important as the market for conductive diamond electrodes grows. Industry leaders are implementing in-line monitoring systems and adopting machine learning algorithms to optimize deposition parameters and ensure reproducibility. These digitalization efforts are expected to reduce manufacturing costs and accelerate the commercialization of next-generation diamond electrodes.
Looking ahead, the outlook for conductive diamond electrode manufacturing is robust. With continued investment in process innovation and material science, the sector is poised to meet rising demand from environmental, biomedical, and energy industries. The next few years will likely see further breakthroughs in scalable production, cost reduction, and the development of application-specific electrode designs, solidifying the role of conductive diamond technology in advanced electrochemical systems.
Major Players and Competitive Landscape (e.g., element6.com, neocoat.ch, sp3inc.com)
The global landscape for conductive diamond electrode manufacturing in 2025 is characterized by a small but highly specialized group of companies, each leveraging proprietary chemical vapor deposition (CVD) technologies and focusing on high-value industrial, environmental, and electrochemical applications. The sector is marked by a combination of established multinational corporations and innovative niche players, with competition centering on electrode quality, scalability, and application-specific customization.
A leading force in the market is Element Six, a member of the De Beers Group, which has decades of experience in synthetic diamond production. Element Six’s conductive diamond electrodes are widely used in water treatment, electrochemical synthesis, and advanced oxidation processes. The company’s global manufacturing footprint and robust R&D capabilities allow it to serve both large-scale industrial clients and research institutions, maintaining a strong competitive edge through continuous innovation in boron-doped diamond (BDD) technology.
Another prominent player is Neocoat, based in Switzerland, which specializes exclusively in the development and production of BDD electrodes. Neocoat is recognized for its ability to deliver highly customized electrode solutions, including both planar and three-dimensional geometries, tailored for specific applications such as ozone generation, organic pollutant degradation, and electrochemical sensors. The company’s close collaborations with academic and industrial partners have enabled it to rapidly prototype and commercialize new electrode designs, positioning it as a key innovator in the European market.
In the United States, sp3 Diamond Technologies is a significant manufacturer, offering a range of BDD-coated products for electrochemical and semiconductor industries. sp3’s expertise lies in scalable CVD processes and the integration of diamond coatings onto complex substrates, which is critical for expanding the use of conductive diamond electrodes in emerging fields such as energy storage and advanced electronics. The company’s focus on quality control and process repeatability has made it a preferred supplier for high-specification industrial applications.
Other notable contributors include Advent Diamond, which is developing next-generation diamond materials for both quantum and electrochemical applications, and Condias in Germany, which manufactures BDD electrodes for water treatment and disinfection systems. These companies are expected to play increasingly important roles as demand for advanced water purification and green chemistry solutions grows.
Looking ahead, the competitive landscape is likely to see incremental expansion as new entrants emerge from regions investing in clean technologies and as established players scale up production to meet rising demand. Strategic partnerships, intellectual property development, and advances in CVD reactor design will be key differentiators in the race to deliver cost-effective, high-performance conductive diamond electrodes over the next several years.
Raw Materials, Supply Chain, and Sustainability Initiatives
The manufacturing of conductive diamond electrodes in 2025 is shaped by evolving raw material sourcing strategies, supply chain dynamics, and a growing emphasis on sustainability. The core material for these electrodes is synthetic diamond, typically produced via chemical vapor deposition (CVD) processes. The quality and availability of high-purity carbon sources, such as methane and hydrogen, are critical, as are the metallic dopants—most commonly boron—used to impart electrical conductivity.
Key suppliers of CVD diamond materials, such as Element Six (a De Beers Group company), continue to expand their production capabilities to meet rising demand from electrochemical and environmental technology sectors. Element Six is recognized for its vertically integrated supply chain, controlling the process from raw carbon feedstock to finished diamond products, which helps mitigate risks associated with material shortages and price volatility.
Another significant player, Adamas Nanotechnologies, focuses on nanodiamond and diamond-based materials, supplying both research and industrial markets. Their efforts to secure reliable sources of precursor gases and dopants are crucial, especially as geopolitical factors and energy market fluctuations impact global chemical supply chains.
Sustainability initiatives are increasingly central to the sector. Manufacturers are investing in energy-efficient CVD reactors and exploring renewable energy integration to reduce the carbon footprint of diamond synthesis. Element Six has publicly committed to reducing greenhouse gas emissions across its operations, aligning with broader sustainability goals set by its parent company, De Beers Group. Additionally, companies are investigating the use of recycled carbon sources and closed-loop water systems to minimize environmental impact.
Supply chain transparency is also gaining traction, with manufacturers seeking to certify the ethical sourcing of all input materials. This is partly driven by customer demand in high-value applications such as water treatment and medical devices, where traceability and compliance with international standards are paramount.
Looking ahead, the sector is expected to see further consolidation among suppliers of high-purity gases and dopants, as well as increased collaboration between diamond manufacturers and end-users to develop application-specific electrode materials. The ongoing push for greener manufacturing and robust supply chains is likely to accelerate innovation in both process technology and raw material sourcing, positioning conductive diamond electrodes as a sustainable solution for advanced electrochemical applications in the coming years.
Emerging Applications: Water Treatment, Sensors, and Energy Storage
The manufacturing of conductive diamond electrodes is experiencing significant advancements in 2025, driven by their expanding role in emerging applications such as water treatment, sensors, and energy storage. These electrodes, typically fabricated by chemical vapor deposition (CVD) of boron-doped diamond (BDD) films onto substrates like silicon or niobium, offer exceptional chemical stability, wide potential windows, and low background currents. Such properties are increasingly sought after in industries aiming for robust, long-lasting, and high-performance electrochemical devices.
In water treatment, conductive diamond electrodes are at the forefront of advanced oxidation processes (AOPs) for the degradation of persistent organic pollutants and disinfection. Companies such as Degrenne Technologies and Advent Diamond are actively scaling up the production of BDD electrodes, focusing on modular reactor designs and cost-effective manufacturing. Degrenne Technologies has reported the deployment of large-area BDD electrodes in municipal and industrial wastewater treatment plants, with ongoing projects in Europe and Asia aiming to demonstrate both environmental and economic benefits. The company’s proprietary CVD processes are being optimized for higher throughput and lower energy consumption, addressing one of the main barriers to widespread adoption.
In the sensor market, the unique electrochemical properties of BDD electrodes are enabling the development of highly sensitive and selective sensors for biomedical, environmental, and industrial monitoring. Advent Diamond is leveraging its expertise in diamond growth and microfabrication to produce miniaturized BDD-based sensor platforms. These sensors are being integrated into point-of-care diagnostic devices and real-time water quality monitoring systems, with pilot deployments expected to expand in 2025 and beyond. The company’s focus on wafer-scale manufacturing is anticipated to reduce costs and facilitate integration with existing semiconductor technologies.
Energy storage is another promising area, with BDD electrodes being explored for use in supercapacitors and advanced batteries. Their high overpotential for oxygen and hydrogen evolution reactions makes them attractive for stable, high-voltage applications. Element Six, a member of the De Beers Group, is a leading supplier of synthetic diamond materials and is investing in R&D to tailor BDD electrode properties for energy storage devices. The company’s collaborations with academic and industrial partners are expected to yield new electrode architectures and scalable manufacturing techniques over the next few years.
Looking ahead, the outlook for conductive diamond electrode manufacturing is positive, with ongoing investments in process optimization, scale-up, and application-driven innovation. As regulatory pressures and market demand for sustainable technologies intensify, the sector is poised for accelerated growth, particularly in water treatment and sensor applications. The next few years will likely see further reductions in production costs, broader commercial deployments, and the emergence of new application domains.
Regulatory Environment and Industry Standards (e.g., ieee.org, iec.ch)
The regulatory environment and industry standards for conductive diamond electrodes manufacturing are evolving rapidly as the technology matures and finds broader applications in water treatment, electrochemical sensing, and advanced energy systems. In 2025, the sector is increasingly shaped by international standards organizations and technical committees, which are working to harmonize safety, performance, and environmental criteria for both manufacturers and end-users.
The Institute of Electrical and Electronics Engineers (IEEE) plays a significant role in setting standards for electrochemical devices, including those utilizing conductive diamond electrodes. IEEE standards address aspects such as electrical safety, device interoperability, and testing protocols, which are critical for ensuring the reliability and scalability of diamond-based technologies. While there is not yet a diamond electrode-specific IEEE standard, ongoing discussions within relevant working groups are expected to yield new guidelines tailored to the unique properties of boron-doped diamond (BDD) electrodes in the coming years.
Similarly, the International Electrotechnical Commission (IEC) is actively involved in developing standards for electrochemical equipment and materials. The IEC’s Technical Committee 113, which focuses on nanotechnology for electrotechnical products and systems, is particularly relevant as conductive diamond electrodes often involve nanostructured surfaces and coatings. The IEC’s framework covers material characterization, environmental impact, and lifecycle assessment, all of which are increasingly important as manufacturers scale up production and seek international market access.
On the manufacturing side, companies such as Element Six—a global leader in synthetic diamond materials—are closely monitoring and contributing to the development of these standards. Element Six, part of the De Beers Group, supplies conductive diamond materials for industrial and research applications, and its involvement in standardization efforts helps ensure that new regulations are both practical and reflective of current manufacturing capabilities. Other key players, including Advent Diamond and Neocoat, are also engaged in industry consortia and technical committees to shape the regulatory landscape.
Looking ahead, the next few years are expected to bring greater regulatory clarity, with new or revised standards addressing the unique challenges of conductive diamond electrode manufacturing—such as purity requirements, doping uniformity, and environmental safety. As adoption grows in sensitive sectors like water purification and medical diagnostics, compliance with international standards will become a prerequisite for market entry, driving further collaboration between manufacturers and standards bodies.
Regional Analysis: North America, Europe, Asia-Pacific, and Rest of World
The global landscape for conductive diamond electrodes manufacturing in 2025 is characterized by distinct regional strengths, ongoing investments, and emerging players. North America, Europe, and Asia-Pacific remain the primary hubs, while the Rest of World is gradually increasing its presence through niche applications and technology transfer.
North America continues to be a leader in both research and commercial production of conductive diamond electrodes. The United States, in particular, benefits from a robust ecosystem of advanced materials companies and academic-industry collaborations. Firms such as Advent Diamond are at the forefront, leveraging proprietary chemical vapor deposition (CVD) techniques to produce high-purity boron-doped diamond (BDD) electrodes for electrochemical and sensor applications. The region’s focus on water treatment, energy storage, and biomedical devices is driving demand for scalable, high-performance diamond electrodes. Additionally, partnerships with national laboratories and universities are accelerating the translation of laboratory-scale processes to industrial manufacturing.
Europe is distinguished by its emphasis on sustainable manufacturing and regulatory compliance. Countries like Germany, Switzerland, and the United Kingdom host several key players, including Element Six, a subsidiary of De Beers Group, which operates one of the world’s largest synthetic diamond production facilities. European manufacturers are investing in automation and process optimization to reduce costs and environmental impact, aligning with the European Union’s Green Deal objectives. The region is also witnessing increased funding for pilot projects in advanced water purification and electrochemical synthesis, further stimulating the adoption of conductive diamond electrodes.
Asia-Pacific is rapidly expanding its manufacturing capacity, driven by strong demand from electronics, environmental, and industrial sectors. Japan and China are particularly active, with companies such as NeoCoat (with operations in both Europe and Asia) and several domestic Chinese manufacturers scaling up production lines for BDD electrodes. The region benefits from lower production costs, government incentives, and a growing base of skilled engineers. Strategic collaborations between local universities and industry are fostering innovation in electrode design and application-specific customization.
Rest of World regions, including Latin America and the Middle East, are at an earlier stage of market development. However, technology transfer initiatives and joint ventures with established manufacturers are enabling gradual entry into specialized markets, such as mining wastewater treatment and niche electrochemical processes. As global demand for advanced water treatment and green energy solutions grows, these regions are expected to play a more significant role in the supply chain over the next few years.
Looking ahead, the competitive landscape is likely to intensify as new entrants emerge and established players invest in capacity expansion, automation, and application-driven R&D. Regional specialization, supply chain resilience, and regulatory alignment will be key factors shaping the future of conductive diamond electrode manufacturing worldwide.
Investment, M&A Activity, and Strategic Partnerships
The conductive diamond electrode manufacturing sector is experiencing a notable uptick in investment, mergers and acquisitions (M&A), and strategic partnerships as the technology matures and finds broader industrial applications. In 2025, this momentum is driven by the growing demand for advanced electrochemical solutions in water treatment, energy storage, and electronics manufacturing.
Key industry players such as Element Six (a De Beers Group company) and Advent Diamond are at the forefront of this activity. Element Six continues to invest in expanding its synthetic diamond production capabilities, with a focus on chemical vapor deposition (CVD) processes that enable the fabrication of high-quality, boron-doped diamond (BDD) electrodes. The company’s ongoing capital investments are aimed at scaling up production to meet the increasing demand from water treatment and advanced manufacturing sectors.
Meanwhile, Advent Diamond is leveraging its expertise in diamond-based electronics and sensors to form strategic partnerships with both established industrial firms and research institutions. In 2025, the company has announced collaborations targeting the integration of conductive diamond electrodes into next-generation semiconductor devices and high-performance sensors, reflecting a trend toward cross-sector innovation.
On the M&A front, the sector is witnessing consolidation as larger materials and technology companies seek to acquire specialized diamond electrode manufacturers to enhance their product portfolios. For example, sp3 Diamond Technologies, a recognized supplier of diamond coatings and electrodes, has attracted interest from multinational corporations aiming to secure proprietary manufacturing know-how and intellectual property. Such acquisitions are expected to accelerate technology transfer and commercialization, particularly in the Asia-Pacific and North American markets.
Strategic partnerships are also being forged between electrode manufacturers and end-users in the water treatment and energy storage industries. These collaborations often focus on co-developing application-specific electrode solutions, optimizing performance, and reducing costs. For instance, Neocoat, a Swiss company specializing in diamond electrode technology, has entered into agreements with water treatment equipment manufacturers to jointly develop advanced electrochemical oxidation systems.
Looking ahead, the outlook for investment and partnership activity in conductive diamond electrode manufacturing remains robust. The sector is expected to benefit from increased public and private funding, as well as from the growing recognition of diamond electrodes’ unique properties—such as chemical inertness and high conductivity—in enabling sustainable industrial processes. As the market expands, further M&A and strategic alliances are anticipated, particularly as new entrants and established players vie for technological leadership and market share.
Future Outlook: Disruptive Trends and Market Opportunities Through 2030
The manufacturing landscape for conductive diamond electrodes is poised for significant transformation through 2030, driven by advances in materials science, process scalability, and expanding end-use applications. As of 2025, the sector is characterized by a shift from laboratory-scale production to industrial-scale manufacturing, with several key players investing in automation, quality control, and cost reduction strategies.
One of the most disruptive trends is the adoption of chemical vapor deposition (CVD) techniques for producing boron-doped diamond (BDD) electrodes. CVD enables precise control over doping levels and film thickness, resulting in electrodes with superior conductivity and chemical stability. Companies such as Element Six, a subsidiary of De Beers Group, are at the forefront of scaling up CVD diamond manufacturing, supplying both bulk and thin-film diamond materials for electrochemical applications. Their ongoing investments in R&D and production capacity are expected to lower costs and improve electrode performance, making BDD electrodes more accessible for water treatment, electroanalysis, and energy storage markets.
Another notable development is the integration of advanced automation and in-line quality monitoring in electrode fabrication. Advent Diamond and sp3 Diamond Technologies are leveraging proprietary reactor designs and process analytics to ensure consistent product quality at scale. These innovations are critical for meeting the stringent requirements of medical, semiconductor, and environmental sectors, where electrode reliability and reproducibility are paramount.
The market outlook is further buoyed by the growing demand for sustainable and robust electrode materials in water purification and industrial wastewater treatment. BDD electrodes are increasingly recognized for their ability to degrade persistent organic pollutants and resist fouling, positioning them as a preferred choice for next-generation electrochemical oxidation systems. Industry leaders such as Neocoat and Condias are expanding their product portfolios to address these emerging opportunities, with a focus on modular electrode systems and custom solutions for municipal and industrial clients.
Looking ahead, the sector is expected to benefit from cross-industry collaborations, particularly in the integration of diamond electrodes with digital monitoring and smart control systems. This convergence is anticipated to unlock new market opportunities in decentralized water treatment, on-site chemical synthesis, and advanced sensing. As manufacturing costs continue to decline and performance metrics improve, conductive diamond electrodes are set to play a pivotal role in enabling cleaner, more efficient, and resilient electrochemical technologies through 2030.