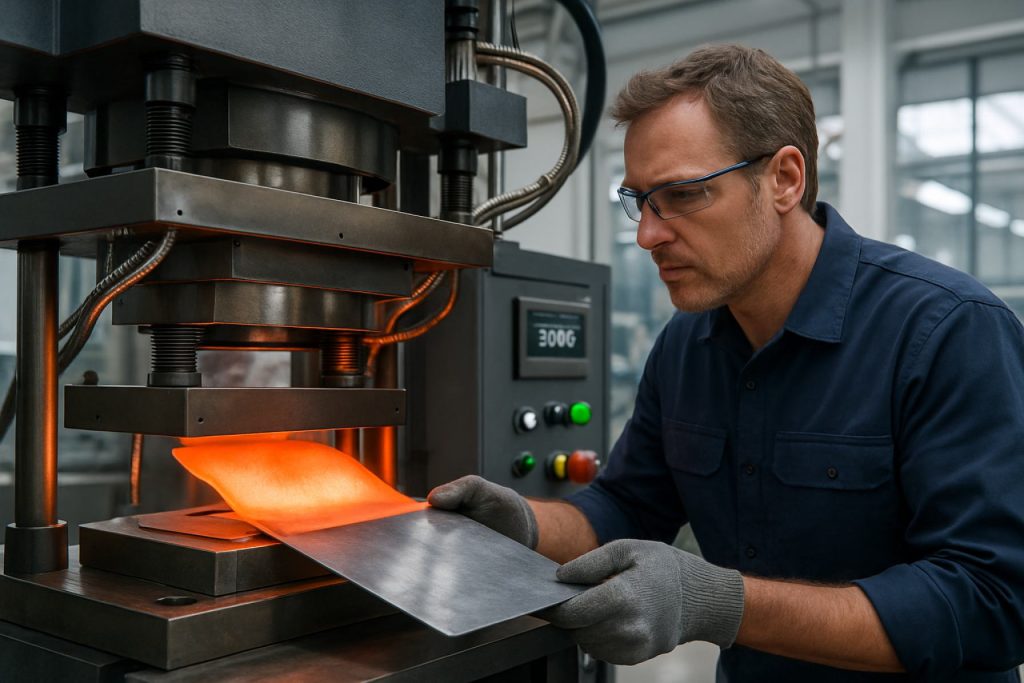
Unlocking the Power of Warm-Forming: How Magnesium Alloys Are Transforming Lightweight Engineering. Discover the Science, Technology, and Future Impact of This Game-Changing Process. (2025)
- Introduction to Warm-Forming and Magnesium Alloys
- Material Properties: Why Magnesium Alloys?
- Warm-Forming Process Fundamentals
- Key Equipment and Technological Innovations
- Comparative Analysis: Warm-Forming vs. Cold and Hot Forming
- Industrial Applications: Automotive, Aerospace, and Beyond
- Challenges and Solutions in Warm-Forming Magnesium Alloys
- Sustainability and Environmental Impact
- Market Trends and Growth Forecasts (2024–2030)
- Future Outlook: Research Directions and Emerging Opportunities
- Sources & References
Introduction to Warm-Forming and Magnesium Alloys
Warm-forming of magnesium alloys is an advanced metalworking process that has gained significant attention in recent years, particularly as industries seek lightweight, high-strength materials for automotive, aerospace, and electronics applications. Magnesium, being the lightest structural metal, offers a unique combination of low density and high specific strength, making it an attractive alternative to aluminum and steel. However, its hexagonal close-packed (HCP) crystal structure limits ductility at room temperature, posing challenges for conventional cold-forming techniques. Warm-forming, typically conducted at temperatures between 200°C and 400°C, addresses these limitations by enhancing the ductility and formability of magnesium alloys, enabling the production of complex shapes with reduced risk of cracking.
As of 2025, the global push for vehicle lightweighting and improved fuel efficiency continues to drive research and industrial adoption of warm-forming processes for magnesium alloys. The automotive sector, in particular, is leveraging these advancements to reduce vehicle mass and meet stringent emissions regulations. Leading automakers and suppliers are collaborating with research institutions to optimize warm-forming parameters and alloy compositions, aiming to balance manufacturability, mechanical performance, and cost-effectiveness. For example, the International Magnesium Association (IMA), a key industry body, actively promotes the development and application of magnesium technologies worldwide, supporting initiatives that advance warm-forming techniques.
Recent data from industry and academic sources indicate a steady increase in the adoption of warm-forming for magnesium alloys, with pilot production lines and demonstration projects underway in Asia, Europe, and North America. Notably, organizations such as the The Minerals, Metals & Materials Society (TMS) and the National Institute of Standards and Technology (NIST) are facilitating knowledge exchange and standardization efforts, which are critical for broader commercialization. These bodies provide technical resources, host conferences, and support collaborative research to address challenges such as die wear, process control, and alloy development.
Looking ahead to the next few years, the outlook for warm-forming of magnesium alloys remains positive. Ongoing advancements in process simulation, tool design, and alloy engineering are expected to further improve formability and reduce production costs. As sustainability and energy efficiency become even more central to manufacturing strategies, the role of magnesium alloys—enabled by warm-forming—will likely expand across multiple sectors. Continued support from industry organizations and government agencies will be essential in overcoming technical barriers and accelerating the integration of these lightweight materials into mainstream production.
Material Properties: Why Magnesium Alloys?
Magnesium alloys have garnered significant attention in recent years, particularly for their application in warm-forming processes. The primary driver behind this interest is magnesium’s status as the lightest structural metal, with a density approximately two-thirds that of aluminum and one-quarter that of steel. This low density, combined with a high specific strength, makes magnesium alloys highly attractive for industries such as automotive and aerospace, where weight reduction is directly linked to improved fuel efficiency and reduced emissions.
Despite these advantages, the widespread adoption of magnesium alloys has historically been limited by their poor formability at room temperature. This limitation arises from their hexagonal close-packed (HCP) crystal structure, which restricts the number of available slip systems for plastic deformation. As a result, magnesium alloys tend to exhibit brittle behavior and limited ductility under cold-forming conditions.
Warm-forming, typically conducted in the temperature range of 200–350°C, has emerged as a solution to these challenges. At elevated temperatures, additional slip systems become active in the HCP structure, significantly enhancing ductility and reducing the risk of cracking. Recent studies and industrial trials have demonstrated that warm-forming can increase the elongation to failure of common magnesium alloys such as AZ31 and ZK60 by several times compared to room temperature forming. For example, elongation values can rise from less than 10% at room temperature to over 30% at optimal warm-forming temperatures.
The automotive sector, in particular, is accelerating the adoption of warm-formed magnesium components. Major automakers and suppliers are collaborating with research institutions to optimize alloy compositions and forming parameters. Organizations such as International Magnesium Association (IMA) and The Minerals, Metals & Materials Society (TMS) are actively supporting research, standardization, and dissemination of best practices in this field. These efforts are expected to yield new magnesium alloy grades with improved formability and corrosion resistance, tailored for warm-forming applications.
Looking ahead to 2025 and beyond, the outlook for warm-forming of magnesium alloys is promising. Ongoing research is focused on further improving the mechanical properties of magnesium alloys through alloying and thermomechanical processing. Additionally, advances in simulation and process control are enabling more precise prediction and optimization of warm-forming operations. As sustainability and lightweighting remain top priorities for manufacturers, magnesium alloys—enabled by warm-forming—are poised to play an increasingly important role in next-generation transportation and consumer products.
Warm-Forming Process Fundamentals
Warm-forming of magnesium alloys is a critical manufacturing process that addresses the inherent limitations of magnesium’s low ductility at room temperature. Magnesium alloys, prized for their low density and high specific strength, are increasingly sought after in automotive, aerospace, and electronics industries for lightweighting applications. However, their hexagonal close-packed (HCP) crystal structure restricts slip systems at ambient conditions, resulting in poor formability. Warm-forming—typically conducted in the temperature range of 200°C to 350°C—enables activation of additional slip systems, significantly improving ductility and reducing the risk of cracking during deformation.
In 2025, research and industrial adoption of warm-forming processes for magnesium alloys are accelerating, driven by the need for sustainable mobility and energy efficiency. The process fundamentals involve precise control of temperature, strain rate, and forming speed to optimize microstructural evolution and mechanical properties. Recent studies, including those supported by the National Institute for Materials Science (NIMS) in Japan and the The Minerals, Metals & Materials Society (TMS), have demonstrated that warm-forming at 250°C–300°C can increase elongation to failure by up to 300% compared to room temperature forming, while also reducing required forming forces by 30–50%.
Key process variants include warm deep drawing, warm rolling, and warm hydroforming. These methods are being refined to produce complex automotive components such as door panels, seat frames, and instrument housings. For instance, the International Magnesium Association reports that several leading automakers are piloting warm-formed magnesium parts in next-generation electric vehicles, aiming to reduce vehicle weight by 10–20% without compromising safety or performance.
Process modeling and simulation are also advancing, with organizations like the National Institute of Standards and Technology (NIST) developing digital twins and predictive models to optimize warm-forming parameters and minimize defects. These efforts are supported by the growing availability of high-purity magnesium alloys and improved die materials that withstand elevated temperatures and cyclic loading.
Looking ahead to the next few years, the outlook for warm-forming of magnesium alloys is robust. Ongoing collaborations between research institutes, industry consortia, and standards bodies are expected to yield new alloy compositions and process innovations. The focus will remain on enhancing formability, reducing energy consumption, and scaling up production for mass-market applications, particularly in transportation and consumer electronics. As regulatory pressures for lightweight, low-emission products intensify, warm-forming is poised to become a mainstream manufacturing solution for magnesium alloys.
Key Equipment and Technological Innovations
The warm-forming of magnesium alloys is a rapidly advancing field, driven by the need for lightweight, high-strength components in automotive, aerospace, and electronics industries. As of 2025, several key equipment developments and technological innovations are shaping the landscape of magnesium alloy processing.
Warm-forming processes typically operate in the temperature range of 200–350°C, where magnesium alloys exhibit improved ductility and reduced forming forces compared to room temperature. This has led to the adaptation and refinement of conventional forming equipment, such as hydraulic and servo-mechanical presses, to accommodate precise temperature control and rapid heating/cooling cycles. Leading equipment manufacturers are integrating advanced thermal management systems, including induction and resistance heating, to ensure uniform temperature distribution across dies and workpieces. These systems are critical for minimizing defects such as cracking and for achieving consistent mechanical properties in formed parts.
A significant innovation in 2025 is the deployment of closed-loop process control systems, which utilize real-time feedback from embedded sensors to monitor temperature, strain, and force during forming. This data-driven approach enables adaptive control of process parameters, resulting in higher part quality and reduced scrap rates. Additionally, the integration of digital twins—virtual replicas of the forming process—allows for predictive maintenance and process optimization, further enhancing equipment reliability and productivity.
Research institutions and industry consortia, such as the The Minerals, Metals & Materials Society (TMS) and the National Institute for Materials Science (NIMS) in Japan, are actively collaborating with equipment manufacturers to develop next-generation warm-forming technologies. These include hybrid forming methods that combine warm-forming with superplastic forming or incremental sheet forming, expanding the range of achievable geometries and reducing tooling costs. Notably, automotive OEMs and tier-one suppliers are investing in pilot lines equipped with these advanced systems to accelerate the adoption of magnesium components in vehicle structures.
Looking ahead, the outlook for warm-forming equipment is characterized by increasing automation, greater use of artificial intelligence for process optimization, and the development of modular forming cells that can be rapidly reconfigured for different alloy grades and part geometries. The continued collaboration between research organizations, equipment suppliers, and end-users is expected to drive further breakthroughs, making magnesium alloy warm-forming more cost-effective and scalable for mass production applications in the coming years.
Comparative Analysis: Warm-Forming vs. Cold and Hot Forming
The comparative analysis of warm-forming versus cold and hot forming of magnesium alloys is a focal point in current materials engineering, especially as the automotive and aerospace sectors intensify their search for lightweight, high-performance components. Warm-forming, typically conducted in the temperature range of 200–350°C, is increasingly recognized for its ability to balance the limitations of cold and hot forming processes, particularly for magnesium alloys, which are known for their poor room-temperature ductility and high reactivity at elevated temperatures.
In cold forming, magnesium alloys exhibit limited formability due to their hexagonal close-packed (HCP) crystal structure, which restricts slip systems at room temperature. This often results in cracking and low elongation, making cold forming suitable only for simple shapes or requiring extensive post-processing. In contrast, hot forming (above 350°C) enhances ductility but introduces challenges such as oxidation, grain growth, and increased energy consumption, which can compromise surface quality and dimensional accuracy.
Warm-forming emerges as a compromise, offering improved ductility and formability without the severe oxidation and grain coarsening seen in hot forming. Recent studies and industrial trials in 2024–2025 have demonstrated that warm-forming can achieve elongations of 20–30% in common magnesium alloys such as AZ31 and ZK60, compared to less than 10% at room temperature. This improvement is attributed to the activation of additional slip systems and dynamic recrystallization at intermediate temperatures, which facilitate more uniform deformation and reduce the risk of cracking.
Automotive manufacturers, including those affiliated with the Toyota Motor Corporation and BMW Group, have reported ongoing research and pilot production lines utilizing warm-forming for structural and interior components. These efforts are supported by collaborative projects with research institutions such as the National Institute for Materials Science (NIMS) in Japan and the Fraunhofer Society in Germany, both of which are recognized for their advanced materials research and process optimization.
Looking ahead to 2025 and beyond, the outlook for warm-forming of magnesium alloys is promising. The process is expected to gain further traction as industries seek to reduce vehicle weight and improve fuel efficiency without sacrificing mechanical performance. Ongoing advancements in die design, temperature control, and alloy development are anticipated to expand the range of applications and further close the gap between laboratory-scale results and mass production. As regulatory pressures for lightweighting and sustainability intensify, warm-forming is poised to become a mainstream manufacturing route for magnesium alloy components, offering a compelling balance of formability, cost, and performance.
Industrial Applications: Automotive, Aerospace, and Beyond
The industrial application of warm-forming magnesium alloys is poised for significant growth in 2025 and the coming years, driven by the increasing demand for lightweight, high-strength components in sectors such as automotive, aerospace, and consumer electronics. Warm-forming, typically conducted at temperatures between 200°C and 400°C, addresses the limited ductility and formability of magnesium alloys at room temperature, enabling the production of complex shapes with improved mechanical properties.
In the automotive industry, the push for fuel efficiency and reduced emissions is accelerating the adoption of magnesium alloys for structural and non-structural components. Major automakers and suppliers are actively developing warm-forming processes to manufacture parts such as instrument panels, seat frames, and transmission housings. For example, Toyota Motor Corporation and BMW Group have both explored magnesium alloy applications in their vehicle platforms, leveraging the material’s low density to achieve significant weight savings. The trend is expected to intensify as regulatory pressures on emissions tighten globally, and as electric vehicles (EVs) require further mass reduction to extend driving range.
In aerospace, the need for lightweight materials is even more pronounced. Organizations such as Airbus and Boeing are investigating the use of warm-formed magnesium alloys for interior components, seat structures, and even certain airframe elements. The ability to form intricate geometries at moderate temperatures without compromising strength or corrosion resistance is particularly attractive for next-generation aircraft designs. The aerospace sector’s stringent safety and performance standards are driving ongoing research into alloy development and process optimization, with collaborative efforts involving research institutes and industry consortia.
Beyond automotive and aerospace, warm-forming of magnesium alloys is finding applications in consumer electronics, where the demand for thin, lightweight casings for laptops, tablets, and smartphones continues to grow. Companies such as Lenovo and Samsung Electronics have incorporated magnesium alloy components in their product lines, benefiting from the material’s favorable strength-to-weight ratio and electromagnetic shielding properties.
Looking ahead, the outlook for warm-forming of magnesium alloys is promising. Advances in alloy design, process simulation, and forming equipment are expected to further expand the range of feasible applications. Industry partnerships and government-supported initiatives, particularly in Asia, Europe, and North America, are likely to accelerate technology transfer from research to mass production. As sustainability and energy efficiency remain top priorities, the industrial adoption of warm-formed magnesium alloys is set to play a pivotal role in shaping the next generation of lightweight engineering solutions.
Challenges and Solutions in Warm-Forming Magnesium Alloys
The warm-forming of magnesium alloys, a process typically conducted at temperatures between 200°C and 400°C, continues to face several technical and industrial challenges as of 2025. Magnesium’s hexagonal close-packed (HCP) crystal structure limits its ductility at room temperature, necessitating elevated temperatures to enable sufficient plastic deformation for forming complex shapes. However, even at these temperatures, issues such as limited formability, rapid oxidation, and tool wear persist, impacting the widespread adoption of magnesium alloys in automotive, aerospace, and electronics sectors.
One of the primary challenges is the narrow processing window. Magnesium alloys exhibit improved ductility only within a specific temperature range; outside this window, the risk of cracking or insufficient formability increases. Recent research, including collaborative projects led by organizations such as the National Institute for Materials Science (NIMS) in Japan and the Fraunhofer Society in Germany, has focused on alloy design and process optimization to widen this window. For example, the addition of rare earth elements and zinc has shown promise in enhancing formability and reducing anisotropy, but cost and supply chain considerations remain.
Oxidation at elevated temperatures is another significant concern. Magnesium is highly reactive, and surface oxidation can lead to defects and compromised mechanical properties. To address this, research groups and industrial consortia, including those coordinated by the International Magnesium Association, are developing advanced protective atmospheres and coatings for dies and workpieces. These solutions aim to minimize oxidation without introducing excessive complexity or cost to the forming process.
Tool wear and die life are also critical issues, as magnesium’s abrasiveness at warm-forming temperatures can lead to frequent maintenance and downtime. The The Minerals, Metals & Materials Society (TMS) has highlighted ongoing efforts to develop new die materials and surface treatments that can withstand the harsh conditions of warm-forming, thereby improving process economics and reliability.
Looking ahead, the outlook for warm-forming magnesium alloys is cautiously optimistic. Advances in simulation and process control, supported by digital manufacturing initiatives from organizations like the National Institute of Standards and Technology (NIST), are expected to further refine forming parameters and reduce trial-and-error in industrial settings. As sustainability and lightweighting remain priorities, especially in transportation, overcoming these challenges will be crucial for broader adoption of magnesium alloys in the next few years.
Sustainability and Environmental Impact
The sustainability and environmental impact of warm-forming magnesium alloys are increasingly significant as industries seek to reduce their carbon footprint and improve resource efficiency. Magnesium alloys, being among the lightest structural metals, offer substantial weight reduction potential for automotive, aerospace, and electronics sectors, directly contributing to lower fuel consumption and emissions during the use phase of products. Warm-forming, typically conducted at temperatures between 200°C and 400°C, enables the processing of magnesium alloys with improved ductility and formability compared to cold-forming, while consuming less energy than traditional hot-forming methods.
In 2025, the environmental benefits of warm-forming magnesium alloys are being recognized in several ongoing industrial and research initiatives. For example, the International Magnesium Association (IMA), a leading global body promoting magnesium use, highlights that the adoption of warm-forming processes can reduce overall energy consumption in manufacturing by up to 30% compared to conventional hot-forming. This reduction is attributed to lower processing temperatures and shorter cycle times, which also decrease greenhouse gas emissions associated with production.
Furthermore, magnesium is highly recyclable, and the warm-forming process is compatible with recycled feedstock, supporting circular economy principles. The European Aluminium Association, which also covers light metals including magnesium, reports that recycling magnesium requires only about 5% of the energy needed for primary production, amplifying the sustainability benefits when combined with efficient forming technologies.
Life cycle assessments (LCAs) conducted by research consortia and industry partners in 2024 and 2025 indicate that magnesium components produced via warm-forming can achieve up to 20% lower cradle-to-gate CO2 emissions compared to those formed by traditional methods. These findings are driving increased interest from automotive OEMs, particularly in Europe and Asia, where regulatory pressures on vehicle emissions are intensifying.
Looking ahead, the outlook for warm-forming of magnesium alloys is positive, with ongoing research focused on further reducing energy consumption, improving alloy recyclability, and minimizing process waste. Organizations such as the National Institute of Standards and Technology (NIST) in the United States are supporting projects aimed at optimizing process parameters and developing new alloy compositions tailored for sustainable manufacturing. As these efforts mature, the environmental advantages of warm-forming magnesium alloys are expected to become even more pronounced, reinforcing their role in the transition to greener manufacturing practices.
Market Trends and Growth Forecasts (2024–2030)
The market for warm-forming of magnesium alloys is poised for significant growth between 2024 and 2030, driven by the increasing demand for lightweight materials in automotive, aerospace, and electronics industries. Magnesium alloys, known for their low density and high specific strength, are particularly attractive for applications where weight reduction is critical. Warm-forming processes, typically conducted at temperatures between 200°C and 400°C, enable improved ductility and formability of magnesium alloys compared to cold-forming, addressing one of the key challenges in their broader adoption.
In 2025, the automotive sector remains the largest consumer of warm-formed magnesium components, as manufacturers intensify efforts to meet stringent emissions and fuel efficiency standards. Major automakers and suppliers are investing in advanced forming technologies to integrate more magnesium parts into vehicle structures, such as instrument panels, seat frames, and transmission cases. The European Aluminium Association and the European Automobile Manufacturers’ Association have both highlighted the role of lightweight metals, including magnesium, in achieving the European Union’s Green Deal targets for decarbonization and vehicle efficiency.
Aerospace applications are also expanding, with organizations like NASA and the European Space Agency exploring magnesium alloys for structural and interior components to reduce launch weights and improve payload capacities. The electronics industry, particularly in Asia, is adopting warm-formed magnesium alloys for casings and frames in smartphones, laptops, and other portable devices, capitalizing on the material’s electromagnetic shielding properties and lightness.
Recent data from the WorldAutoSteel consortium and the International Atomic Energy Agency (which tracks materials innovation for energy applications) indicate a compound annual growth rate (CAGR) for magnesium alloy demand in the range of 7–10% through 2030, with warm-forming processes accounting for a growing share of this expansion. This growth is supported by ongoing R&D investments from leading producers and research institutions, such as International Magnesium Association, which coordinates global efforts to improve alloy compositions and forming techniques.
Looking ahead, the market outlook for warm-forming of magnesium alloys is robust, with anticipated breakthroughs in alloy design and forming equipment expected to further reduce costs and expand application areas. Regulatory support for lightweighting, combined with advances in process automation and quality control, will likely accelerate adoption across multiple sectors by 2030.
Future Outlook: Research Directions and Emerging Opportunities
The future of warm-forming magnesium alloys is poised for significant advancements as research and industrial interest intensifies in 2025 and the coming years. Magnesium alloys, prized for their low density and high specific strength, are increasingly targeted for lightweighting applications in automotive, aerospace, and electronics sectors. However, their limited formability at room temperature has historically constrained widespread adoption. Warm-forming—processing at intermediate temperatures (typically 200–400°C)—offers a promising pathway to overcome these challenges by enhancing ductility and reducing forming forces.
Current research is focused on optimizing process parameters, alloy compositions, and tool designs to further improve the formability and mechanical properties of magnesium components. Notably, several leading research institutions and industry consortia are collaborating to develop new magnesium alloy grades specifically tailored for warm-forming. For example, the The Minerals, Metals & Materials Society (TMS) continues to coordinate international symposia and working groups dedicated to magnesium processing innovations, fostering knowledge exchange and standardization efforts.
Emerging opportunities are also being driven by the automotive industry’s push to meet stricter emissions and fuel efficiency standards. Major automakers and suppliers are investing in pilot lines and demonstration projects to validate warm-forming processes for structural and closure parts. The Magna International, a global automotive supplier, has publicly committed to expanding its lightweight materials portfolio, including magnesium, to support next-generation vehicle architectures. Similarly, the European Aluminium Association and its partners are supporting research into multi-material joining and hybrid structures, where warm-formed magnesium could play a critical role.
On the scientific front, advanced characterization techniques—such as in-situ electron microscopy and synchrotron X-ray diffraction—are being leveraged to unravel the microstructural evolution of magnesium alloys during warm-forming. This knowledge is expected to inform the design of new alloys with improved texture control and reduced anisotropy, addressing key barriers to industrial adoption. Furthermore, digital manufacturing and simulation tools are being integrated into process development, enabling rapid prototyping and optimization of forming operations.
Looking ahead, the next few years are likely to see increased commercialization of warm-formed magnesium components, particularly in electric vehicles and lightweight consumer electronics. Continued collaboration between academia, industry, and standards organizations will be essential to address remaining technical challenges and to ensure the reliability and cost-effectiveness of these advanced manufacturing processes.