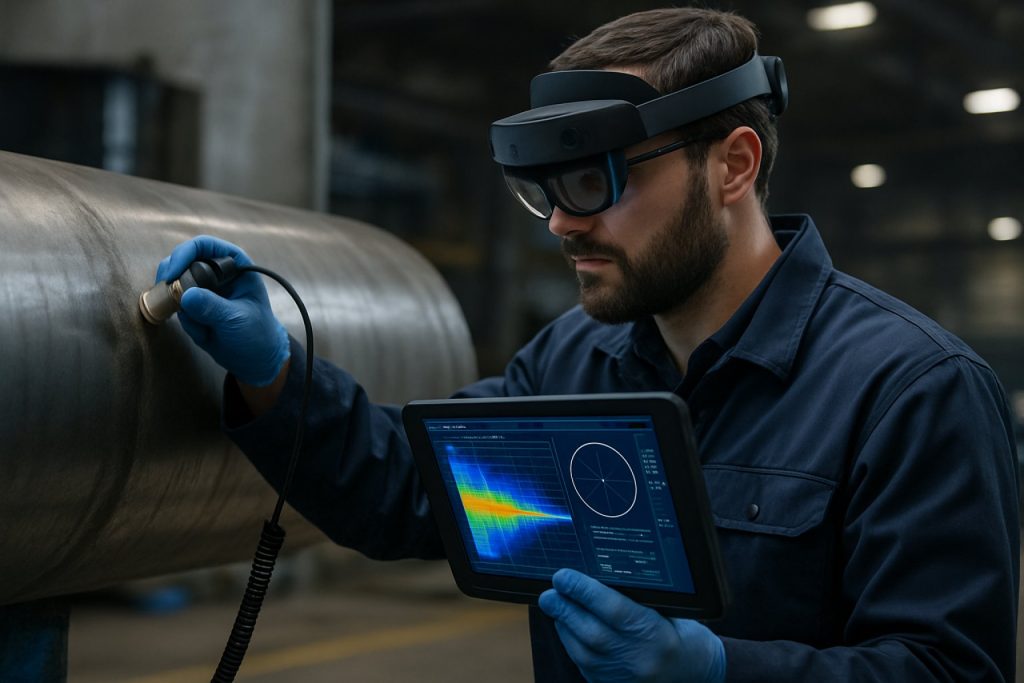
Cómo la Realidad Extendida (XR) Está Transformando la Inspección No Destructiva: Desbloqueando una Precisión, Eficiencia y Capacitación Sin Precedentes para la Próxima Generación de Inspectores (2025)
- Introducción: La Convergencia de XR y la Inspección No Destructiva
- Tecnologías Clave: AR, VR y MR en Aplicaciones NDT
- Casos de Uso Clave en la Industria: Aeroespacial, Energía e Infraestructura
- Capacitación y Certificación Mejoradas por XR para Profesionales NDT
- Visualización de Datos en Tiempo Real y Colaboración Remota
- Beneficios: Mayor Precisión, Seguridad y Eficiencia de Costos
- Desafíos y Barreras para la Adopción de XR en NDT
- Crecimiento del Mercado e Interés Público: Pronósticos 2024–2030
- Innovadores Líderes y Normas Oficiales (e.g., asnt.org, asme.org)
- Perspectivas Futuras: La Próxima Década de XR en la Inspección No Destructiva
- Fuentes y Referencias
Introducción: La Convergencia de XR y la Inspección No Destructiva
La integración de la Realidad Extendida (XR)—un término general que abarca la Realidad Virtual (VR), la Realidad Aumentada (AR) y la Realidad Mixta (MR)—con la Inspección No Destructiva (NDT) está transformando rápidamente las prácticas de inspección y mantenimiento industrial a partir de 2025. La NDT, una disciplina crítica para garantizar la integridad y seguridad de infraestructuras y componentes sin causar daño, ha dependido tradicionalmente de técnicas manuales y equipos especializados. Sin embargo, la convergencia con las tecnologías XR está dando lugar a una nueva era de digitalización, colaboración remota y visualización de datos mejorada.
La aplicación de XR en NDT se impulsa por la necesidad de mayor precisión, eficiencia y seguridad en sectores como el aeroespacial, la energía, la fabricación y la infraestructura civil. Al superponer información digital en entornos del mundo real (AR), sumergir a los inspectores en escenarios simulados (VR) o mezclar ambos (MR), XR permite a los técnicos visualizar defectos subsuperficiales, acceder a datos de sensores en tiempo real y seguir procedimientos de inspección guiados sin usar las manos. Esta convergencia es particularmente significativa a medida que las industrias enfrentan una creciente complejidad en los activos y una escasez de inspectores experimentados.
En los últimos años, importantes organizaciones e instituciones de investigación han estado pilotando y desplegando soluciones de NDT basadas en XR. Por ejemplo, NASA ha explorado AR para la guía remota en el mantenimiento e inspección de naves espaciales, mientras que Siemens ha integrado AR en sus ofertas de servicio industrial para apoyar a los técnicos de campo con superposiciones de datos en tiempo real y asistencia de expertos remotos. La Sociedad Americana de Inspección No Destructiva (ASNT), un organismo profesional líder, ha destacado a XR como una tendencia clave en sus conferencias y publicaciones recientes, enfatizando su potencial para abordar los desafíos de capacitación y transferencia de conocimiento de la fuerza laboral.
La convergencia de XR y NDT también es respaldada por avances en hardware—como cascos AR livianos y cámaras de alta resolución—y plataformas de software que permiten una integración fluida con instrumentos NDT y gemelos digitales. A partir de 2025, varios dispositivos industriales XR están certificados para su uso en entornos peligrosos, lo que amplía aún más su aplicabilidad en los sectores de petróleo y gas, generación de energía y procesamiento químico.
De cara al futuro, se espera que la adopción de XR en NDT se acelere en los próximos años, impulsada por las iniciativas de transformación digital en curso, la maduración de la conectividad 5G y la creciente disponibilidad de soluciones XR estandarizadas. Los interesados en la industria anticipan que XR no solo mejorará la calidad y seguridad de las inspecciones, sino que también permitirá nuevos modelos de servicio, como auditorías remotas y mantenimiento predictivo, transformando fundamentalmente el futuro de la inspección no destructiva.
Tecnologías Clave: AR, VR y MR en Aplicaciones NDT
La Realidad Extendida (XR)—que abarca la Realidad Aumentada (AR), la Realidad Virtual (VR) y la Realidad Mixta (MR)—está transformando rápidamente las prácticas de inspección no destructiva (NDT) en industrias como la aeroespacial, la energía y la fabricación. A partir de 2025, la integración de las tecnologías XR en los flujos de trabajo de NDT está acelerándose, impulsada por la necesidad de una mejor visualización, capacitación mejorada y mayor eficiencia operativa.
AR superpone información digital sobre el mundo físico, lo que permite a los inspectores visualizar defectos subsuperficiales, datos de medidas o pasos de procedimiento directamente sobre los componentes que se están examinado. Por ejemplo, se están utilizando cascos AR en inspecciones de campo para proporcionar orientación en tiempo real y visualización de datos, reduciendo errores humanos y el tiempo de inspección. Empresas como Microsoft (con HoloLens) y Lenovo están desarrollando activamente plataformas de hardware y software AR que apoyan aplicaciones industriales NDT, incluyendo asistencia remota de expertos e integración de flujos de trabajo digitales.
VR, por otro lado, se utiliza principalmente para capacitación inmersiva y simulación. Los técnicos de NDT pueden practicar procedimientos de inspección complejos en un entorno virtual libre de riesgos, mejorando la adquisición de habilidades y la seguridad. Organizaciones como la Sociedad Americana de Inspección No Destructiva (ASNT) están promoviendo módulos de capacitación basados en VR para abordar la escasez global de personal calificado en NDT y estandarizar la competencia en distintas regiones. VR también permite la simulación de escenarios raros o peligrosos, que de otro modo son difíciles de replicar en la vida real.
MR combina elementos de AR y VR, permitiendo a los usuarios interactuar tanto con objetos reales como virtuales. En NDT, se está explorando MR para inspecciones colaborativas, donde expertos remotos pueden anotar vistas 3D en vivo de equipos, guiando a los técnicos in situ a través de evaluaciones complejas. Esto es particularmente valioso en sectores como la energía nuclear y la aeroespacial, donde la disponibilidad de expertos es limitada y el equipo es altamente especializado.
En años recientes, ha habido proyectos piloto y despliegues iniciales de XR en NDT por importantes actores industriales. Por ejemplo, Siemens y GE están invirtiendo en soluciones de inspección habilitadas por XR para agilizar los procesos de mantenimiento y aseguramiento de calidad. Estas iniciativas están respaldadas por avances en hardware (cascos más livianos y robustos), software (reconocimiento de defectos impulsado por IA) y conectividad (5G, computación en la nube).
De cara al futuro, las perspectivas para XR en NDT son prometedoras. A medida que los costos de los dispositivos disminuyan y la interconectividad mejore, se espera una adopción más amplia, especialmente en entornos remotos y peligrosos. Se prevé que los esfuerzos de estandarización de organismos como ISO y ASME aceleren aún más la integración, garantizando la seguridad y fiabilidad. Para 2027, se proyecta que XR se convertirá en un componente central de las estrategias digitales de NDT, transformando fundamentalmente los paradigmas de inspección, capacitación y mantenimiento.
Casos de Uso Clave en la Industria: Aeroespacial, Energía e Infraestructura
La Realidad Extendida (XR)—que abarca la Realidad Aumentada (AR), la Realidad Virtual (VR) y la Realidad Mixta (MR)—está transformando rápidamente la inspección no destructiva (NDT) en industrias críticas como la aeroespacial, la energía y la infraestructura. A partir de 2025, la integración de las tecnologías XR está pasando de proyectos piloto a despliegues operativos, impulsada por la necesidad de mayor seguridad, eficiencia y capacitación de la fuerza laboral.
En el sector aeroespacial, XR se está utilizando para mejorar la precisión y velocidad de las inspecciones NDT en componentes complejos como las palas de turbinas, estructuras de fuselaje y materiales compuestos. Los principales fabricantes de aeronaves y organizaciones de mantenimiento están utilizando cascos de AR para superponer esquemas digitales y datos de sensores en tiempo real sobre activos físicos, lo que permite a los técnicos identificar defectos y seguir protocolos de inspección estandarizados con un error mínimo. Por ejemplo, el uso de flujos de trabajo guiados por AR ha demostrado reducir los tiempos de inspección y mejorar la precisión de la documentación, apoyando el cumplimiento de estándares regulatorios estrictos. Organizaciones como NASA han explorado XR para colaboración remota y capacitación en procedimientos de NDT, particularmente para hardware destinado al espacio donde la precisión es primordial.
En la industria energética, particularmente en el petróleo y gas y la energía nuclear, XR está abordando los desafíos de inspeccionar entornos peligrosos o de difícil acceso. Los técnicos equipados con dispositivos AR pueden acceder a datos en vivo de equipos de prueba ultrasónica, radiográfica o de corrientes de Eddy mientras mantienen la conciencia situacional. Este acceso sin manos a información digital aumenta la seguridad y reduce la probabilidad de errores humanos. Empresas como Shell han pilotado soluciones de NDT basadas en AR para inspecciones de tuberías y refinaciones, permitiendo que expertos remotos guíen al personal in situ en tiempo real. La capacidad de grabar y reproducir sesiones de inspección XR también apoya el cumplimiento regulatorio y la transferencia de conocimiento a medida que los inspectores experimentados se retiran.
Para la infraestructura, incluyendo puentes, túneles y redes de transporte, XR está facilitando la gestión de activos a gran escala y el mantenimiento predictivo. Los municipios y empresas de ingeniería están adoptando AR y MR para visualizar defectos subsuperficiales, corrosión o fatiga estructural detectada por métodos NDT. Esta capacidad de visualización ayuda a priorizar reparaciones y comunicar hallazgos a las partes interesadas. La Sociedad Americana de Inspección No Destructiva, un organismo profesional líder, ha destacado el creciente papel de XR en la capacitación de la próxima generación de profesionales NDT, ofreciendo simulaciones inmersivas que replican escenarios de inspección del mundo real.
De cara al futuro, se espera que la convergencia de XR con la inteligencia artificial y dispositivos NDT habilitados por IoT simplifique aún más los flujos de trabajo de inspección, reduzca costos y aborde la escasez de mano de obra calificada. A medida que los organismos de normalización y los líderes de la industria continúan validando las aplicaciones de XR, se prevé que la adopción se acelere en los sectores aeroespacial, energético e infraestructura hasta finales de la década de 2020.
Capacitación y Certificación Mejoradas por XR para Profesionales NDT
La Realidad Extendida (XR)—que abarca la Realidad Virtual (VR), la Realidad Aumentada (AR) y la Realidad Mixta (MR)—está transformando rápidamente los procesos de capacitación y certificación para los profesionales de la Inspección No Destructiva (NDT). A partir de 2025, la integración de tecnologías XR en la educación NDT se está acelerando, impulsada por la necesidad de soluciones de capacitación más seguras, efectivas y escalables en industrias como la aeroespacial, la energía y la fabricación.
Las organizaciones líderes, incluyendo la Sociedad Americana de Inspección No Destructiva (ASNT), han reconocido el potencial de XR para abordar desafíos críticos en la capacitación NDT. La capacitación tradicional práctica a menudo requiere acceso a equipos costosos, entornos peligrosos y supervisión experta. Las plataformas XR, en contraste, permiten a los estudiantes sumergirse en simulaciones realistas de escenarios de inspección, practicar procedimientos complejos y recibir retroalimentación instantánea, todo sin los riesgos o limitaciones logísticas de las configuraciones físicas.
En los últimos años, se han desplegado simuladores basados en VR para pruebas ultrasónicas, radiográficas y de corrientes de Eddy, lo que permite a los usuarios interactuar con instrumentos virtuales y modelos de defectos. Por ejemplo, la Agencia Internacional de Energía Atómica (IAEA) ha pilotado módulos de VR para capacitación NDT en seguridad nuclear, reportando una mejora en la retención del conocimiento y adquisición de habilidades entre los participantes. De manera similar, los principales fabricantes aeroespaciales están colaborando con proveedores de tecnología XR para crear flujos de trabajo de inspección guiados por AR, donde las superposiciones digitales ayudan a los estudiantes a identificar defectos y seguir procedimientos estandarizados.
Los organismos de certificación están comenzando a adaptar sus marcos de evaluación para acomodar exámenes prácticos basados en XR. La ASNT ha iniciado investigaciones sobre la validez y confianza de la certificación asistida por XR, con resultados iniciales que indican que las evaluaciones virtuales pueden igualar o superar los métodos tradicionales en la evaluación de la competencia de los candidatos. Se espera que este cambio se expanda en los próximos años, a medida que las plataformas XR se vuelvan más asequibles y accesibles.
De cara al futuro, las perspectivas para la capacitación NDT mejorada por XR son muy positivas. Los avances en retroalimentación háptica, generación de escenarios impulsados por IA y colaboración en la nube están listos para mejorar aún más el realismo y la escalabilidad. Para 2027, se anticipa que una proporción significativa de profesionales NDT pasará al menos parte de su capacitación o certificación a través de entornos XR, apoyados por estándares y mejores prácticas desarrollados por organizaciones como ASNT y la Organización Internacional de Normalización (ISO). Esta evolución promete no solo mejorar la preparación de la fuerza laboral, sino también abordar la escasez global de personal NDT calificado.
Visualización de Datos en Tiempo Real y Colaboración Remota
La Realidad Extendida (XR)—que abarca la Realidad Aumentada (AR), la Realidad Virtual (VR) y la Realidad Mixta (MR)—está transformando rápidamente la visualización de datos en tiempo real y la colaboración remota en la Inspección No Destructiva (NDT) a partir de 2025. La integración de tecnologías XR está permitiendo a inspectores, ingenieros y tomadores de decisiones interactuar con conjuntos de datos complejos y colaborar a distancia con una eficiencia y precisión sin precedentes.
Un impulsor clave de la adopción de XR en NDT es la necesidad de visualización en tiempo real de datos de inspección. Los cascos XR y las gafas inteligentes ahora permiten a los técnicos superponer datos de sensores en vivo, como resultados ultrasónicos o radiográficos, directamente sobre el activo físico que se está inspeccionando. Este contexto espacial reduce los errores de interpretación y acelera la identificación de defectos. Por ejemplo, el HoloLens 2 de Microsoft se está desplegando en entornos industriales para proyectar modelos 3D y flujos de datos en vivo en equipos, lo que permite el acceso sin manos a información crítica durante las inspecciones.
La colaboración remota es otra área donde XR está logrando avances significativos. Con la infraestructura global envejeciendo y la escasez de profesionales NDT calificados, las organizaciones están aprovechando plataformas XR para conectar a inspectores de campo con expertos remotos en tiempo real. A través de entornos XR compartidos, los expertos remotos pueden ver exactamente lo que el técnico en el sitio ve, anotar transmisiones de video en vivo y guiar los procedimientos como si estuvieran presentes en la ubicación. Siemens y GE han pilotado sistemas de soporte remoto basados en XR para NDT, reportando reducciones en costos de viaje y resolución más rápida de desafíos de inspección complejos.
La convergencia de XR con el Internet Industrial de las Cosas (IIoT) está mejorando aún más la visualización de datos en tiempo real. Los sensores embebidos en los activos transmiten datos a plataformas en la nube, que luego se visualizan a través de dispositivos XR. Esta integración permite el mantenimiento predictivo y la respuesta inmediata a anomalías detectadas durante NDT. Organizaciones como La Sociedad Americana de Inspección No Destructiva (ASNT) están promoviendo activamente la investigación y estandarización en flujos de trabajo de NDT habilitados por XR, reconociendo el potencial de la tecnología para mejorar la seguridad y fiabilidad.
De cara a los próximos años, las perspectivas para XR en NDT son robustas. Se esperan avances en conectividad inalámbrica (5G/6G), hardware XR más liviano y ergonómico, y analítica de datos impulsada por IA que continuarán agilizando la colaboración y visualización en tiempo real. A medida que los organismos reguladores y los grupos de la industria desarrollen pautas para el uso de XR en inspecciones críticas para la seguridad, es probable que la adopción se acelere, convirtiendo a XR en una parte integral del kit de herramientas de NDT a finales de la década de 2020.
Beneficios: Mayor Precisión, Seguridad y Eficiencia de Costos
La Realidad Extendida (XR)—que abarca la Realidad Aumentada (AR), la Realidad Virtual (VR) y la Realidad Mixta (MR)—está transformando rápidamente la inspección no destructiva (NDT) al mejorar la precisión, la seguridad y la eficiencia de costos. A partir de 2025, los sectores industriales líderes como el aeroespacial, la energía y la fabricación están integrando cada vez más XR en sus flujos de trabajo de NDT, impulsados por la necesidad de inspecciones más confiables y eficiencia operativa.
Uno de los principales beneficios de XR en NDT es la mejora de la precisión. XR superpone datos en tiempo real, modelos 3D y salidas de sensores directamente sobre los activos físicos, lo que permite a los inspectores visualizar defectos subsuperficiales y geometrías complejas con una claridad sin precedentes. Por ejemplo, los cascos AR pueden proyectar resultados de escaneo ultrasónico sobre un componente, permitiendo a los técnicos localizar fallas con precisión milimétrica. Esta capacidad reduce el error humano y apoya una toma de decisiones más consistente, como se demuestra en proyectos piloto de importantes fabricantes aeroespaciales y empresas energéticas. Organizaciones como NASA han explorado XR para la inspección y mantenimiento remotos, reportando tasas de detección mejoradas y reducción de rehacer en sistemas críticos.
La seguridad es otra ventaja significativa. XR permite la colaboración remota, permitiendo a los expertos guiar al personal in situ a través de inspecciones complejas sin estar físicamente presentes en entornos peligrosos. Esto reduce la exposición a condiciones peligrosas, como alta radiación o espacios confinados, y apoya el cumplimiento de regulaciones de seguridad estrictas. En el sector nuclear, por ejemplo, los operadores han utilizado XR para simular procedimientos de inspección y capacitar al personal, lo que ha resultado en menos incidentes en el sitio y una mejor preparación ante emergencias. La Agencia Internacional de Energía Atómica (IAEA) ha destacado el papel de XR en la mejora de los protocolos de seguridad para inspecciones en instalaciones nucleares.
La eficiencia de costos se materializa a través de la reducción del tiempo de inactividad, la optimización de la asignación de recursos y la minimización de gastos de viaje. Los módulos de capacitación basados en XR permiten a los técnicos practicar técnicas NDT en entornos virtuales inmersivos, acelerando la adquisición de habilidades y reduciendo la necesidad de costosos simulacros físicos. Además, el soporte remoto a través de XR puede disminuir la frecuencia y duración de las visitas al sitio por parte de expertos externos, lo que conduce a ahorros de costos sustanciales. Líderes industriales como Siemens han reportado reducciones medibles en los tiempos de inspección y costos de mantenimiento después de implementar soluciones XR en sus operaciones de NDT.
De cara al futuro, se espera que la adopción de XR en NDT se acelere, impulsada por avances en hardware portátil, integración de datos en tiempo real y reconocimiento de defectos impulsado por IA. A medida que los organismos de regulación y los consorcios de la industria continúen validando los métodos NDT habilitados por XR, la tecnología está lista para convertirse en una herramienta estándar para garantizar la integridad y seguridad de la infraestructura crítica en todo el mundo.
Desafíos y Barreras para la Adopción de XR en NDT
La adopción de tecnologías de Realidad Extendida (XR)—incluyendo Realidad Aumentada (AR), Realidad Virtual (VR) y Realidad Mixta (MR)—en la Inspección No Destructiva (NDT) está acelerándose, pero persisten varios desafíos y barreras significativas a partir de 2025. Estos obstáculos abarcan dominios técnicos, organizacionales y regulatorios, influyendo en el ritmo y la escala de la integración de XR en industrias críticas como la aeroespacial, la energía y la manufactura.
Un desafío técnico primario es la integración de los sistemas XR con los equipos y flujos de trabajo NDT existentes. Muchos procesos NDT dependen de hardware antiguo y software propietario, lo que dificulta el intercambio de datos sin problemas y la visualización en tiempo real. Por ejemplo, aunque organizaciones como la Sociedad Americana de Inspección No Destructiva (ASNT) están promoviendo activamente la transformación digital, la falta de formatos de datos estandarizados y interfaces complica el despliegue de soluciones XR en diversos entornos de inspección.
Otra barrera es la precisión y fiabilidad de las inspecciones asistidas por XR. Las superposiciones de XR deben alinearse con precisión con los componentes del mundo real para evitar la mala interpretación de defectos o errores de medición. Lograr este nivel de precisión espacial requiere un seguimiento avanzado, calibración y fusión de sensores, que aún están en evolución. Además, factores ambientales como la iluminación, la interferencia electromagnética y los espacios confinados pueden degradar el rendimiento de los dispositivos XR, como se ha señalado en discusiones técnicas por líderes de la industria como GE y Siemens, ambos están desarrollando activamente soluciones NDT digitales y habilitadas por XR.
La preparación de la fuerza laboral es otra preocupación significativa. Los profesionales de NDT requieren capacitación especializada para utilizar efectivamente las herramientas XR, que difieren sustancialmente de los métodos de inspección tradicionales. La transición no solo demanda mejora técnica, sino también un cambio cultural dentro de las organizaciones acostumbradas a prácticas establecidas. Iniciativas de organismos como ASME (Sociedad Americana de Ingenieros Mecánicos) están comenzando a abordar estas brechas a través de programas de capacitación actualizados y rutas de certificación, pero la adopción generalizada tomará tiempo.
La seguridad de los datos y la privacidad también presentan desafíos, especialmente en sectores que manejan infraestructura sensible o diseños propietarios. Los sistemas XR a menudo dependen de la conectividad en la nube y el intercambio de datos en tiempo real, lo que plantea preocupaciones sobre el acceso no autorizado o violaciones de datos. Los marcos regulatorios para la NDT digital, incluidos aquellos de la Organización Internacional de Normalización (ISO), están evolucionando, pero las pautas claras para los riesgos específicos de XR aún están emergiendo.
De cara al futuro, superar estas barreras requerirá esfuerzos coordinados entre proveedores de tecnología, organizaciones de estándares y usuarios finales. Se espera que los avances en interoperabilidad, robustez del dispositivo y desarrollo de la fuerza laboral reduzcan gradualmente los obstáculos a la adopción, pero es probable que el progreso significativo se produzca en los próximos años a medida que la industria madure.
Crecimiento del Mercado e Interés Público: Pronósticos 2024–2030
La integración de la Realidad Extendida (XR)—que abarca la Realidad Aumentada (AR), la Realidad Virtual (VR) y la Realidad Mixta (MR)—en la Inspección No Destructiva (NDT) está ganando rápidamente impulso a medida que las industrias buscan mejorar la precisión de las inspecciones, la seguridad y la capacitación de la fuerza laboral. A partir de 2025, el mercado de XR en NDT está experimentando un sólido crecimiento, impulsado por la creciente complejidad de los activos industriales, la necesidad de colaboración remota y la continua transformación digital en sectores como el aeroespacial, la energía y la fabricación.
Actores clave de la industria, incluyendo Siemens, GE, y Shell, han comenzado a pilotar y desplegar soluciones de NDT basadas en XR. Estos sistemas permiten a los inspectores superponer información digital sobre el equipo del mundo real, realizar recorridos virtuales por los sitios de inspección y simular escenarios de detección de defectos. Por ejemplo, Siemens ha demostrado el uso de cascos AR para guía en tiempo real durante inspecciones ultrasónicas y radiográficas, reduciendo el error humano y mejorando la documentación. De manera similar, GE ha integrado módulos de VR en sus programas de capacitación NDT, permitiendo a los técnicos practicar procedimientos complejos en entornos inmersivos.
Las organizaciones de investigación públicas y privadas también están contribuyendo al campo. La Sociedad Americana de Inspección No Destructiva (ASNT) ha destacado a XR como una tecnología transformadora en sus conferencias y publicaciones técnicas recientes, enfatizando su potencial para abordar la escasez de profesionales NDT calificados y estandarizar la calidad de la inspección. Mientras tanto, la Administración Nacional de Aeronáutica y del Espacio (NASA) ha explorado XR para NDT remoto de componentes espaciales, subrayando la relevancia de la tecnología en entornos de alto riesgo.
De cara a 2030, las perspectivas para XR en NDT son altamente optimistas. Las proyecciones de la industria anticipan una tasa de crecimiento anual compuesta (CAGR) de dos dígitos para soluciones NDT habilitadas por XR, a medida que más empresas inviertan en infraestructura digital y el hardware XR se vuelva más asequible y ergonómico. Se espera que la adopción se acelere en regiones con bases industriales sólidas, como América del Norte, Europa y Asia Oriental. Además, los organismos reguladores están comenzando a reconocer las inspecciones asistidas por XR como métodos válidos, allanando el camino para una aceptación y estandarización más amplias.
En resumen, se espera que el período de 2024 a 2030 experimente una expansión significativa en el uso de XR para NDT, impulsada por avances tecnológicos, necesidades de la fuerza laboral y un creciente interés público y de la industria en prácticas de inspección más seguras y eficientes.
Innovadores Líderes y Normas Oficiales (e.g., asnt.org, asme.org)
La Realidad Extendida (XR)—que abarca la Realidad Aumentada (AR), la Realidad Virtual (VR) y la Realidad Mixta (MR)—está transformando rápidamente el panorama de la Inspección No Destructiva (NDT) al mejorar la visualización, capacitación y colaboración remota. A partir de 2025, varias organizaciones líderes y organismos de normas están moldeando activamente la integración de tecnologías XR en las prácticas NDT, con un enfoque en la seguridad, fiabilidad y desarrollo de la fuerza laboral.
La Sociedad Americana de Inspección No Destructiva (ASNT) es el principal organismo profesional en los Estados Unidos dedicado a promover la NDT. La ASNT ha reconocido el potencial de XR para mejorar la capacitación y evaluación de competencias de los inspectores. En los últimos años, la ASNT ha organizado sesiones técnicas y talleres sobre aplicaciones de XR en sus conferencias anuales, destacando estudios de caso donde se utilizan cascos AR y simuladores VR para capacitación práctica y ensayo de procedimientos. Se espera que estas iniciativas se expandan, con comités de la ASNT explorando el desarrollo de prácticas recomendadas y pautas para la capacitación y certificación NDT basadas en XR.
La Sociedad Americana de Ingenieros Mecánicos (ASME), un líder mundial en normas de ingeniería, también ha comenzado a abordar el papel de XR en NDT. Los comités de desarrollo de normas de ASME están monitoreando la integración de herramientas XR para la inspección y el mantenimiento en sectores como recipientes a presión, tuberías y generación de energía. En 2024 y 2025, ASME ha organizado seminarios web y paneles técnicos que discuten la validación y estandarización de flujos de trabajo de inspección asistidos por XR, con la expectativa de formalizar mejores prácticas en próximas revisiones de códigos.
En el frente de la innovación, grandes empresas de tecnología industrial están colaborando con fabricantes de equipos NDT para desplegar soluciones XR. Por ejemplo, Siemens y GE han pilotado sistemas de inspección guiados por AR que superponen instrucciones digitales y datos de sensores en tiempo real sobre activos físicos, permitiendo que técnicos menos experimentados realicen inspecciones complejas con supervisión experta. Estos sistemas están siendo evaluados para cumplir con estándares industriales y se espera su adopción más amplia a medida que maduren los marcos regulatorios.
A nivel internacional, la Organización Internacional de Normalización (ISO) está rastreando la evolución de XR en aplicaciones industriales, incluyendo NDT. Los comités técnicos de ISO están considerando las implicaciones de XR para la integridad de datos, calificación de operadores y seguridad, con la posibilidad de nuevos estándares o enmiendas en los próximos años.
De cara al futuro, se prevé que la convergencia de XR y NDT se acelere, impulsada por la colaboración continua entre los organismos de estándares, los líderes de la industria y los desarrolladores de tecnología. Es probable que los próximos años vean la publicación de pautas formales y el establecimiento de rutas de certificación para NDT habilitado por XR, asegurando que estas herramientas avanzadas se desplieguen de manera segura y efectiva en los sectores de infraestructura crítica.
Perspectivas Futuras: La Próxima Década de XR en la Inspección No Destructiva
La integración de la Realidad Extendida (XR)—que abarca la Realidad Aumentada (AR), la Realidad Virtual (VR) y la Realidad Mixta (MR)—en la Inspección No Destructiva (NDT) está lista para acelerar significativamente hasta 2025 y durante la próxima década. A medida que industrias como la aeroespacial, la energía y la fabricación buscan mejorar la seguridad, la eficiencia y la toma de decisiones basada en datos, XR está surgiendo como una herramienta transformadora tanto para las aplicaciones NDT de campo como de laboratorio.
En 2025, varios importantes actores industriales y organizaciones de investigación están pilotando y desplegando soluciones XR para NDT. Por ejemplo, Siemens ha demostrado el uso de cascos AR para superponer datos de inspección en tiempo real sobre activos físicos, permitiendo a los técnicos visualizar defectos subsuperficiales y acceder a gemelos digitales durante pruebas ultrasónicas y radiográficas. De manera similar, Shell ha reportado el uso de módulos de capacitación basados en VR para inspectores de tuberías, reduciendo el tiempo de capacitación y mejorando la precisión de los procedimientos en entornos peligrosos.
La adopción de XR en NDT está impulsada por varias tendencias convergentes:
- Colaboración Remota: Las plataformas XR están permitiendo que expertos remotos guíen a los inspectores en el sitio en tiempo real, reduciendo los costos de viaje y acelerando inspecciones complejas. Organizaciones como La Sociedad Americana de Inspección No Destructiva (ASNT) están explorando activamente estándares y mejores prácticas para las inspecciones asistidas por XR de forma remota.
- Integración de Datos: Los dispositivos XR son cada vez más capaces de integrarse con instrumentos NDT, permitiendo a los inspectores visualizar datos de sensores, modelos 3D y registros históricos en contexto. Esto se espera que mejore las tasas de detección de defectos y reduzca el error humano.
- Desarrollo de la Fuerza Laboral: A medida que los profesionales experimentados NDT se jubilan, la capacitación y simulación basadas en XR se están convirtiendo en esenciales para capacitar a nuevos técnicos. Organizaciones como NASA han pilotado entornos VR para simular escenarios de inspección complejos, mejorando tanto la seguridad como la competencia.
De cara al futuro, se espera que en la próxima década XR se convierta en un componente estándar de los flujos de trabajo NDT. Se prevé que los avances en hardware portátil, conectividad 5G y analítica impulsada por IA mejoren aún más las capacidades de los sistemas XR. Se anticipa que los organismos reguladores y grupos industriales, incluida la Organización Internacional de Normalización (ISO), desarrollen nuevas pautas para garantizar la fiabilidad y seguridad de las inspecciones asistidas por XR.
Para 2030, se proyecta que XR permitirá crear entornos de inspección completamente inmersivos y ricos en datos, apoyando el mantenimiento predictivo y la toma de decisiones en tiempo real en sectores de infraestructura crítica. La colaboración continua entre proveedores de tecnología, líderes de la industria y organizaciones de estándares será crucial para realizar todo el potencial de XR en la inspección no destructiva.
Fuentes y Referencias
- NASA
- Siemens
- Sociedad Americana de Inspección No Destructiva (ASNT)
- Microsoft
- Lenovo
- GE
- ISO
- ASME
- Shell
- Sociedad Americana de Inspección No Destructiva (ASNT)
- Agencia Internacional de Energía Atómica (IAEA)
- Sociedad Americana de Ingenieros Mecánicos (ASME)
- Siemens
- Organización Internacional de Normalización (ISO)