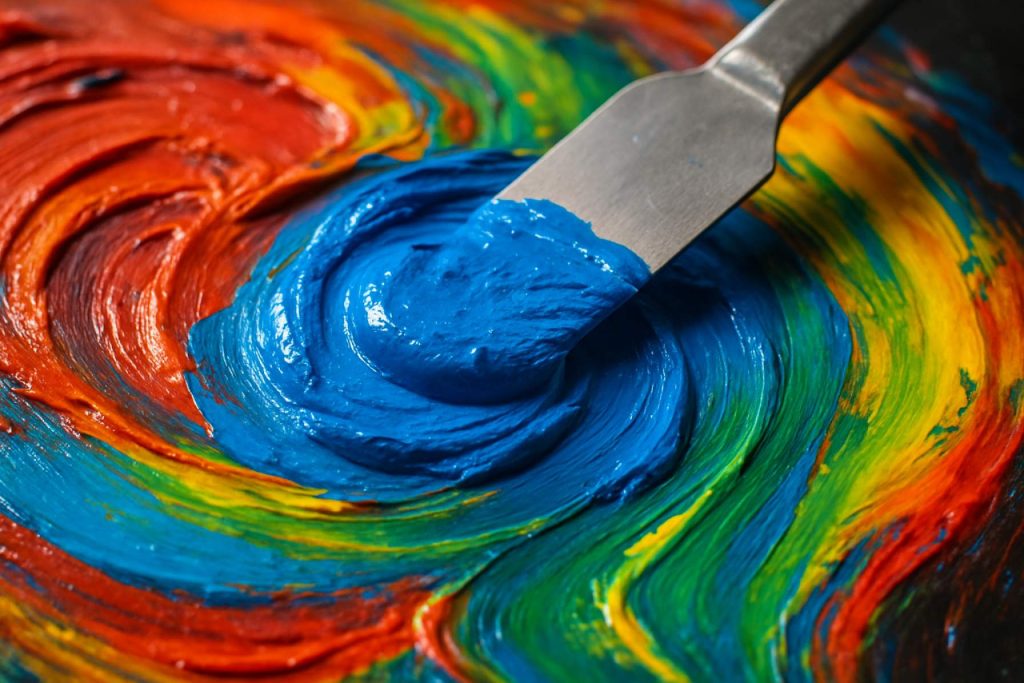
Mastering Pigment Dispersion: The Science, Technology, and Future of Color in Modern Materials. Discover How Innovations Are Transforming Industries from Paints to Plastics. (2025)
- Introduction: The Critical Role of Pigment Dispersion
- Fundamentals of Pigment Dispersion Science
- Key Technologies and Equipment in Pigment Dispersion
- Raw Materials: Types of Pigments and Dispersing Agents
- Industrial Applications: Paints, Coatings, Plastics, and Inks
- Quality Control and Measurement Techniques
- Environmental and Regulatory Considerations
- Recent Innovations and Patented Methods
- Market Trends and Growth Forecasts (2024–2030)
- Future Outlook: Sustainability, Digitalization, and Emerging Demands
- Sources & References
Introduction: The Critical Role of Pigment Dispersion
Pigment dispersion is a foundational process in the formulation of a wide array of products, including paints, coatings, inks, plastics, cosmetics, and pharmaceuticals. At its core, pigment dispersion involves the uniform distribution of pigment particles within a liquid or solid medium, ensuring that the colorant is evenly spread and stabilized throughout the final product. This process is critical because the quality of dispersion directly influences the color strength, gloss, opacity, stability, and overall performance of the end material.
The importance of effective pigment dispersion extends across multiple industries. In the coatings and paints sector, for example, well-dispersed pigments are essential for achieving consistent color, optimal hiding power, and resistance to fading or degradation over time. In the plastics industry, uniform pigment dispersion ensures that molded or extruded products exhibit consistent coloration and mechanical properties. Similarly, in the cosmetics field, the safety, appearance, and sensory attributes of products such as lipsticks and foundations depend on the fine and stable dispersion of pigments.
Achieving optimal pigment dispersion is technically challenging due to the natural tendency of pigment particles to agglomerate or form clusters. These agglomerates can lead to defects such as color streaking, poor coverage, and reduced durability. The process typically involves mechanical energy—using equipment like high-speed mixers, bead mills, or ultrasonic devices—to break down these clusters and distribute the particles evenly. Additionally, the use of dispersing agents or surfactants is common to stabilize the particles and prevent re-agglomeration, thereby enhancing the longevity and quality of the product.
The science of pigment dispersion is governed by principles of colloid chemistry and surface science. Factors such as particle size, surface area, and the chemical compatibility between pigment and medium play pivotal roles in determining the ease and effectiveness of dispersion. Leading organizations such as the International Organization for Standardization (ISO) and the ASTM International have established standardized test methods and guidelines to assess pigment dispersion quality, reflecting its critical importance in industrial applications.
As industries continue to demand higher performance and sustainability from their products, the role of advanced pigment dispersion technologies is becoming even more significant. Innovations in dispersing equipment, surface modification of pigments, and eco-friendly dispersants are shaping the future of this essential process, ensuring that pigment dispersion remains at the heart of material science and product development in 2025 and beyond.
Fundamentals of Pigment Dispersion Science
Pigment dispersion is a fundamental process in the formulation of paints, inks, plastics, cosmetics, and other materials where color uniformity and stability are critical. At its core, pigment dispersion involves the even distribution of solid pigment particles within a liquid or solid medium, ensuring that the colorant is homogeneously integrated and remains stable over time. The science of pigment dispersion encompasses several interrelated physical and chemical phenomena, including wetting, deagglomeration, and stabilization.
The process begins with wetting, where the surface of pigment particles is coated by the surrounding medium, typically a resin, solvent, or binder. Effective wetting reduces the interfacial tension between the pigment and the medium, allowing the liquid to penetrate and displace air or moisture on the pigment surface. This is often facilitated by surfactants or dispersing agents, which are specifically designed to enhance compatibility between the pigment and the vehicle.
Following wetting, deagglomeration is necessary to break down pigment aggregates into primary particles or smaller clusters. Pigments, due to their high surface energy, tend to form agglomerates during storage and handling. Mechanical energy, applied through milling or high-shear mixing, is used to separate these clusters. The efficiency of deagglomeration directly impacts the final color strength, gloss, and opacity of the product.
Once the pigment particles are adequately dispersed, stabilization mechanisms prevent re-agglomeration. Stabilization can be achieved through electrostatic repulsion, steric hindrance, or a combination of both, depending on the nature of the dispersing agents and the medium. Proper stabilization ensures that pigment particles remain evenly distributed, preventing settling, flocculation, or color shifts during storage and application.
The quality of pigment dispersion is typically evaluated by parameters such as particle size distribution, viscosity, and optical properties. Advanced analytical techniques, including laser diffraction and electron microscopy, are employed to assess dispersion quality and optimize processing conditions. The International Organization for Standardization (ISO) provides standardized test methods for evaluating pigment dispersion in various applications, ensuring consistency and reproducibility across industries.
Understanding the fundamentals of pigment dispersion is essential for developing high-performance materials with desired color properties, durability, and processability. Ongoing research by organizations such as the Royal Society of Chemistry continues to advance the science of dispersion, exploring new materials, additives, and processing technologies to meet evolving industry demands.
Key Technologies and Equipment in Pigment Dispersion
Pigment dispersion is a critical process in industries such as coatings, inks, plastics, and cosmetics, where the uniform distribution of pigment particles within a medium determines the final product’s color strength, stability, and performance. Achieving optimal dispersion requires a combination of advanced technologies and specialized equipment designed to break down pigment agglomerates and ensure consistent particle size distribution.
One of the foundational technologies in pigment dispersion is high-shear mixing. High-shear mixers utilize rapidly rotating blades or rotors to generate intense mechanical forces, effectively deagglomerating pigment clusters and distributing them evenly throughout the liquid medium. This technology is widely adopted in the paint and coatings industry due to its efficiency and scalability. Another essential technology is bead milling, which employs grinding media (such as glass, ceramic, or steel beads) within a closed chamber. As the chamber agitates, the beads collide with pigment particles, reducing their size and enhancing dispersion quality. Bead mills are particularly valued for their ability to achieve sub-micron particle sizes, which is crucial for high-performance applications.
Ultrasonic dispersion is another advanced method, utilizing high-frequency sound waves to create cavitation bubbles in the dispersion medium. The collapse of these bubbles generates localized high-energy zones, breaking apart pigment agglomerates and promoting uniform distribution. This technique is especially useful for dispersing nanoparticles and sensitive pigments that may be damaged by mechanical shear.
Key equipment in pigment dispersion includes high-speed dispersers, bead mills, three-roll mills, and ultrasonic homogenizers. High-speed dispersers are commonly used for pre-mixing and initial wetting of pigments, while bead mills and three-roll mills are employed for fine grinding and achieving the desired particle size. Ultrasonic homogenizers, on the other hand, are increasingly used in research and specialty applications where precise control over particle size and distribution is required.
The selection of dispersion technology and equipment depends on several factors, including pigment type, desired particle size, formulation viscosity, and end-use application. Leading organizations such as the American Coatings Association and the Society of Cosmetic Chemists provide technical resources and guidelines to support best practices in pigment dispersion. Equipment manufacturers continually innovate to improve energy efficiency, process control, and scalability, ensuring that pigment dispersion technologies meet the evolving demands of modern industries.
Raw Materials: Types of Pigments and Dispersing Agents
Pigment dispersion is a critical process in the formulation of paints, coatings, inks, plastics, and other materials where color uniformity and stability are essential. The effectiveness of pigment dispersion depends largely on the selection and compatibility of raw materials, particularly the types of pigments and dispersing agents used. Understanding the properties and interactions of these components is fundamental to achieving optimal color strength, gloss, and durability in the final product.
Pigments are finely divided solid particles that impart color and opacity to a medium. They are generally classified into two main categories: organic and inorganic pigments. Inorganic pigments—such as titanium dioxide, iron oxides, and chromium oxides—are valued for their opacity, lightfastness, and chemical stability. Organic pigments, including phthalocyanines, azo compounds, and quinacridones, offer a broader color range and higher tinting strength but may be less stable under certain conditions. The choice between organic and inorganic pigments depends on the application’s requirements for color, durability, and environmental resistance.
The dispersion of pigments involves breaking down agglomerates and distributing the pigment particles uniformly throughout the medium. This process is facilitated by dispersing agents, also known as surfactants or wetting agents. Dispersing agents are typically amphiphilic molecules that adsorb onto the pigment surface, reducing interparticle attraction and preventing re-agglomeration. Common classes of dispersing agents include polyacrylates, polyurethanes, and nonionic surfactants. The selection of a suitable dispersing agent is influenced by the pigment’s surface chemistry, the medium’s polarity, and the desired end-use properties.
The quality of pigment dispersion directly affects the optical and mechanical properties of the final product. Poor dispersion can lead to issues such as color inconsistency, reduced gloss, sedimentation, and compromised durability. To address these challenges, manufacturers often employ high-shear mixing, milling, or ultrasonic techniques in combination with optimized dispersing agents. The Dow and BASF are among the leading chemical companies that develop and supply advanced dispersing agents and pigment technologies for various industries.
In summary, the careful selection and combination of pigment types and dispersing agents are foundational to successful pigment dispersion. Advances in raw material chemistry and processing technologies continue to enhance the performance and sustainability of colored materials across multiple sectors.
Industrial Applications: Paints, Coatings, Plastics, and Inks
Pigment dispersion is a critical process in the industrial production of paints, coatings, plastics, and inks, directly influencing the performance, appearance, and durability of the final products. The process involves the uniform distribution of pigment particles within a liquid or solid medium, ensuring optimal color strength, stability, and application properties. Achieving effective pigment dispersion is essential to prevent issues such as flocculation, sedimentation, and poor color development, which can compromise product quality.
In the paints and coatings industry, pigment dispersion determines the opacity, gloss, and weather resistance of the finished surface. Manufacturers employ high-shear mixers, bead mills, and other mechanical methods to break down pigment agglomerates and achieve fine, stable dispersions. The choice of dispersing agents—specialized surfactants or polymers—plays a pivotal role in stabilizing pigment particles and preventing re-agglomeration. Organizations such as the American Coatings Association provide resources and standards to guide best practices in pigment dispersion for coatings applications.
For plastics, pigment dispersion is integrated into compounding processes, where pigments are blended with polymer resins to produce masterbatches or pre-colored materials. Uniform dispersion is vital to ensure consistent color and mechanical properties throughout molded or extruded plastic products. The Plastics Industry Association represents companies involved in these processes and supports research into advanced dispersion technologies, including twin-screw extrusion and ultrasonic mixing.
In the ink industry, pigment dispersion affects print quality, color vibrancy, and ink stability. Fine dispersions are necessary to prevent clogging in printing equipment and to achieve sharp, uniform prints. The National Association of Printing Ink Manufacturers (NAPIM) is a key authority, offering technical guidance and standards for ink formulation and pigment dispersion.
Across all these sectors, advances in pigment chemistry and dispersion technology are enabling the use of novel pigments, including nanoparticles and organic pigments, which offer enhanced color properties and environmental benefits. Industry standards and testing protocols, often developed by organizations such as ASTM International, ensure that pigment dispersions meet rigorous performance and safety criteria. As sustainability becomes increasingly important, manufacturers are also exploring waterborne and low-VOC dispersion systems to reduce environmental impact while maintaining high product quality.
Quality Control and Measurement Techniques
Quality control and measurement techniques are critical in ensuring the consistency, stability, and performance of pigment dispersions across industries such as coatings, inks, plastics, and cosmetics. The primary goal is to achieve uniform distribution of pigment particles within a medium, preventing agglomeration and ensuring optimal color strength, gloss, and durability.
A fundamental aspect of quality control in pigment dispersion is particle size analysis. The particle size and its distribution directly influence the optical properties, stability, and application performance of the final product. Techniques such as laser diffraction, dynamic light scattering, and sedimentation analysis are widely used to measure particle size distribution. These methods provide rapid, reproducible results and are suitable for both laboratory and production environments. For example, International Organization for Standardization (ISO) standards, such as ISO 13320, outline procedures for laser diffraction particle size analysis, ensuring consistency and comparability across laboratories.
Another key measurement is the assessment of dispersion stability. Stability tests often involve accelerated aging protocols, such as centrifugation or thermal cycling, to predict long-term behavior. Visual inspection, combined with instrumental techniques like turbidimetry or zeta potential measurement, helps determine the tendency of pigments to settle or flocculate over time. Zeta potential, in particular, is a critical parameter indicating the electrostatic repulsion between particles; higher absolute values generally correlate with better dispersion stability.
Colorimetric analysis is also central to quality control. Spectrophotometers are used to measure color strength, hue, and tinting strength, ensuring that pigment dispersions meet precise color specifications. The International Commission on Illumination (CIE) provides standardized color measurement systems, such as the CIE Lab* color space, which are widely adopted for objective color evaluation.
Rheological measurements, including viscosity and flow behavior, are essential for predicting the processability and application performance of pigment dispersions. Instruments such as rotational viscometers and rheometers are employed to characterize the flow properties under different shear conditions, which is particularly important for applications like printing inks and paints.
To ensure comprehensive quality control, manufacturers often implement statistical process control (SPC) and adhere to Good Manufacturing Practices (GMP), as recommended by organizations like the ASTM International. These practices help maintain batch-to-batch consistency and compliance with regulatory standards.
In summary, robust quality control and advanced measurement techniques are indispensable for producing high-performance pigment dispersions. By leveraging standardized methods and instrumentation, manufacturers can ensure product reliability, regulatory compliance, and customer satisfaction.
Environmental and Regulatory Considerations
Pigment dispersion, a critical process in industries such as paints, coatings, plastics, inks, and cosmetics, is subject to increasing environmental and regulatory scrutiny in 2025. The environmental impact of pigment dispersion arises from the use of organic solvents, surfactants, and certain pigment chemistries, some of which may be hazardous to human health and ecosystems. Regulatory frameworks are evolving to address these concerns, with a focus on reducing volatile organic compound (VOC) emissions, restricting hazardous substances, and promoting sustainable manufacturing practices.
One of the primary environmental concerns is the emission of VOCs during the dispersion process, particularly in solvent-based systems. VOCs contribute to air pollution and the formation of ground-level ozone, which is regulated under the United States Environmental Protection Agency (EPA) Clean Air Act. The EPA sets limits on VOC content in paints, coatings, and related products, driving manufacturers to adopt water-based or high-solids formulations that minimize VOC emissions. Similarly, the European Chemicals Agency (ECHA) enforces the Registration, Evaluation, Authorisation and Restriction of Chemicals (REACH) regulation, which restricts the use of certain hazardous substances in pigment formulations and dispersants.
Heavy metal-based pigments, such as those containing lead, cadmium, or chromium, are subject to stringent restrictions due to their toxicity and persistence in the environment. Both the EPA and ECHA have established limits or outright bans on these substances in consumer products. The Occupational Safety and Health Administration (OSHA) in the United States also sets workplace exposure limits for hazardous dusts and fumes generated during pigment dispersion, ensuring worker safety.
In response to these regulatory pressures, the pigment dispersion industry is increasingly adopting greener alternatives. This includes the use of bio-based or biodegradable dispersants, the development of non-toxic inorganic and organic pigments, and the implementation of closed-loop manufacturing systems to minimize waste and emissions. Industry organizations such as the International Organization for Standardization (ISO) provide guidelines for environmental management systems (e.g., ISO 14001), which many pigment manufacturers follow to demonstrate compliance and commitment to sustainability.
Looking ahead to 2025, regulatory agencies are expected to further tighten controls on hazardous substances and emissions associated with pigment dispersion. Companies operating in this sector must remain vigilant, continuously monitoring regulatory updates and investing in research and development to ensure compliance and minimize environmental impact.
Recent Innovations and Patented Methods
Recent years have witnessed significant advancements in pigment dispersion technologies, driven by the demand for higher performance, sustainability, and compatibility with emerging application fields such as digital printing, advanced coatings, and functional materials. Innovations in 2025 focus on improving pigment stability, reducing energy consumption during dispersion, and enhancing the environmental profile of both pigments and dispersing agents.
One notable trend is the development of engineered dispersants tailored for specific pigment chemistries and end-use requirements. For example, polymeric dispersants with controlled molecular architectures are being designed to optimize pigment wetting, prevent agglomeration, and maintain long-term stability in both aqueous and non-aqueous systems. These dispersants often incorporate functional groups that interact selectively with pigment surfaces, resulting in improved color strength and reduced viscosity. Such approaches are particularly relevant for high-performance coatings and inks, where pigment loading and stability are critical.
Another area of innovation involves the use of advanced milling and mixing technologies. High-energy bead mills and ultrasonic dispersion methods are being refined to achieve finer particle sizes and more uniform distributions, which are essential for applications requiring transparency or high gloss. Some patented methods now integrate real-time monitoring of particle size and dispersion quality, enabling process optimization and consistent product quality. These process improvements also contribute to lower energy consumption and reduced waste generation.
Sustainability is a key driver in recent patent activity. Companies are introducing bio-based and biodegradable dispersants, as well as waterborne pigment concentrates that minimize the use of volatile organic compounds (VOCs). For instance, several major pigment manufacturers have announced new product lines that comply with increasingly stringent environmental regulations, particularly in the European Union and North America. These innovations align with the broader industry shift toward greener chemistries and circular economy principles.
Intellectual property filings in 2025 reflect these trends, with patents granted for novel dispersant chemistries, hybrid organic-inorganic pigment systems, and process intensification techniques. Organizations such as the European Patent Office and the United States Patent and Trademark Office have reported a steady increase in pigment dispersion-related patents, underscoring the sector’s dynamic innovation landscape.
Industry leaders, including members of the European Color Manufacturers Association and the International Color Consortium, are actively collaborating on standardization and best practices for pigment dispersion, further accelerating the adoption of new technologies and methods across global markets.
Market Trends and Growth Forecasts (2024–2030)
The pigment dispersion market is poised for significant growth between 2024 and 2030, driven by expanding applications across industries such as paints and coatings, plastics, inks, and textiles. Pigment dispersions—finely distributed pigment particles stabilized in a liquid medium—are essential for imparting color, opacity, and durability to a wide range of products. The increasing demand for high-performance and sustainable color solutions is shaping the market’s trajectory, with manufacturers focusing on innovations that enhance dispersion stability, color strength, and environmental compatibility.
A key trend influencing the pigment dispersion market is the shift toward water-based and low-VOC (volatile organic compound) formulations, particularly in the paints and coatings sector. Regulatory bodies such as the United States Environmental Protection Agency and the European Chemicals Agency are enforcing stricter environmental standards, prompting manufacturers to develop eco-friendly dispersions that minimize hazardous emissions. This regulatory push is expected to accelerate the adoption of waterborne pigment dispersions, especially in regions with robust environmental policies.
Technological advancements are also shaping market dynamics. Companies are investing in novel dispersion techniques and surface modification technologies to improve pigment compatibility with various substrates and enhance end-use performance. For example, the use of advanced surfactants and dispersing agents enables the production of dispersions with superior stability and color uniformity, meeting the stringent requirements of industries such as automotive coatings and digital printing.
Geographically, the Asia-Pacific region is anticipated to lead market growth, fueled by rapid industrialization, urbanization, and rising consumer demand for colored products. Major economies such as China and India are witnessing increased investments in construction, automotive, and packaging sectors, all of which are significant consumers of pigment dispersions. Meanwhile, North America and Europe are expected to maintain steady growth, supported by ongoing innovation and a strong focus on sustainability.
Looking ahead to 2030, the pigment dispersion market is expected to benefit from the proliferation of smart and functional coatings, as well as the growing popularity of digital printing technologies. Industry leaders, including members of the European Coatings Association and global pigment manufacturers, are likely to continue prioritizing research and development to address evolving customer needs and regulatory requirements. Overall, the market outlook remains robust, with sustainability, performance, and technological innovation serving as the primary growth drivers.
Future Outlook: Sustainability, Digitalization, and Emerging Demands
The future outlook for pigment dispersion is shaped by three converging forces: sustainability, digitalization, and evolving market demands. As industries ranging from coatings and plastics to inks and cosmetics seek to reduce their environmental footprint, the pigment dispersion sector is under increasing pressure to innovate with eco-friendly solutions. Regulatory bodies such as the United States Environmental Protection Agency and the European Chemicals Agency are tightening restrictions on hazardous substances, driving manufacturers to develop water-based, solvent-free, and bio-based dispersions. These sustainable alternatives aim to minimize volatile organic compound (VOC) emissions and reduce the reliance on petrochemical-derived raw materials, aligning with global climate and health objectives.
Digitalization is another transformative trend, particularly as the pigment dispersion industry integrates advanced manufacturing technologies and data-driven quality control. The adoption of digital color matching, real-time process monitoring, and automated dispersion systems is enhancing consistency, reducing waste, and accelerating product development cycles. Organizations such as the International Organization for Standardization (ISO) are instrumental in setting global standards for pigment quality, dispersion stability, and testing methodologies, supporting the digital transformation of production and quality assurance processes.
Emerging demands are also reshaping the pigment dispersion landscape. The rapid growth of digital printing, for example, requires dispersions with ultra-fine particle sizes and high color strength to meet the performance needs of inkjet and 3D printing technologies. In the automotive and construction sectors, there is a rising demand for dispersions that offer enhanced durability, weather resistance, and functional properties such as heat reflection or antimicrobial activity. The cosmetics and personal care industries are increasingly seeking dispersions that are not only vibrant and stable but also compliant with stringent safety and sustainability standards, as outlined by authorities like the U.S. Food and Drug Administration.
Looking ahead to 2025 and beyond, the pigment dispersion industry is expected to accelerate its shift toward circular economy principles, with greater emphasis on recyclability, renewable feedstocks, and closed-loop manufacturing. Collaboration between manufacturers, regulatory agencies, and end-users will be crucial in driving innovation and ensuring that pigment dispersions meet the evolving technical, environmental, and regulatory requirements of a rapidly changing global market.
Sources & References
- International Organization for Standardization
- ASTM International
- Royal Society of Chemistry
- American Coatings Association
- BASF
- Plastics Industry Association
- International Commission on Illumination (CIE)
- European Chemicals Agency
- European Patent Office
- European Color Manufacturers Association
- European Coatings Association