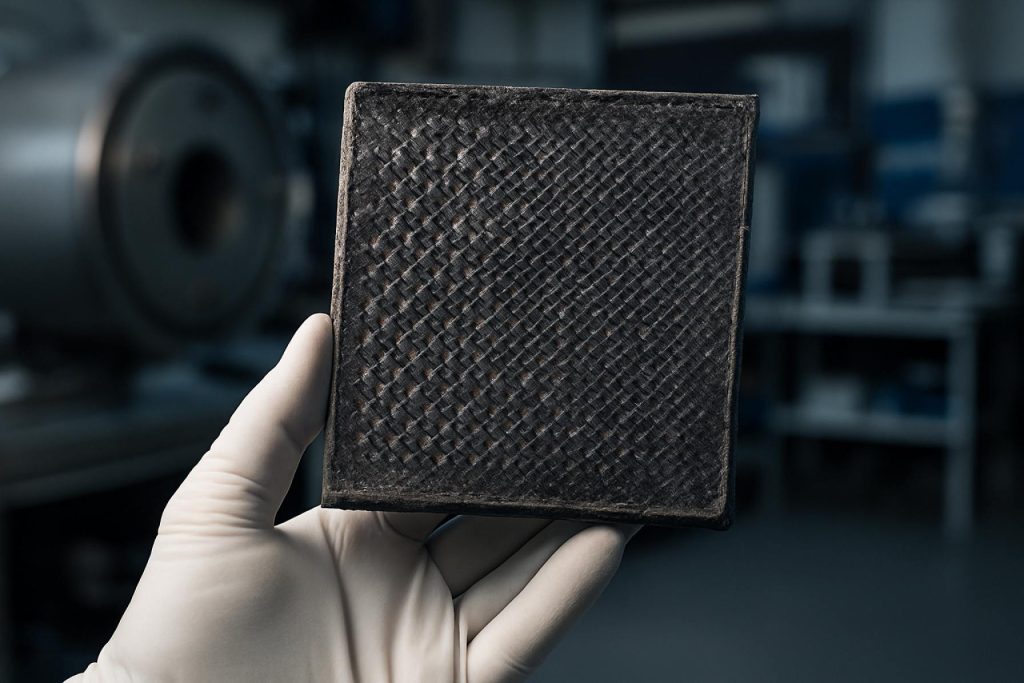
Inhaltsverzeichnis
- Zusammenfassung: CMCs stehen vor explosivem Wachstum
- Marktübersicht 2025: Schlüsselakteure und aufstrebende Führungskräfte
- Neueste Durchbrüche in der CMC-Verarbeitungstechnologie
- Wichtige Endverbrauchersektoren: Luft- und Raumfahrt, Energie, Automobil und mehr
- Innovationen in der Lieferkette und Strategien zur Rohstoffbeschaffung
- Regionale Hotspots: Nordamerika, Europa und asiatisch-pazifische Trends
- Investitionen, M&A und strategische Partnerschaften in der CMC-Produktion
- Nachhaltigkeit und Umweltauswirkungen der CMC-Produktion
- Marktprognose 2025–2030: Umsatz-, Volumen- und Preisanalysen
- Zukünftige Ausblicke: Anwendungen der nächsten Generation und Technologie-Roadmap
- Quellen & Referenzen
Zusammenfassung: CMCs stehen vor explosivem Wachstum
Die Herstellung von keramischen Matrixverbunden (CMC) steht 2025 und in den kommenden Jahren vor einer signifikanten Expansion, die durch die steigende Nachfrage in den Bereichen Luft- und Raumfahrt, Verteidigung, Energie und Automobilwesen vorangetrieben wird. CMCs – aus Keramikfasern, die in einer keramischen Matrix eingebettet sind – bieten eine außergewöhnliche thermische Stabilität, eine geringe Dichte und eine Korrosionsbeständigkeit, was sie zu einem entscheidenden Material für Anwendungen der nächsten Generation mit hoher Leistung macht.
Jüngste Aktivitäten in der Branche untermauern diesen Schwung. Große Luft- und Raumfahrt-OEMs haben ihre Investitionen in CMC-Fähigkeiten drastisch erhöht. Beispielsweise hat GE Aerospace seine CMC-Produktion in den USA, einschließlich seiner Einrichtung in North Carolina, ausgebaut, um der steigenden Nachfrage nach leichten, kraftstoffeffizienten Triebwerkskomponenten gerecht zu werden. Gleichzeitig steigert Safran weiterhin die Integration von CMCs, insbesondere für Triebwerksprogramme der nächsten Generation, indem es sowohl eigene Fertigung als auch Joint Ventures nutzt.
Im Energiesektor treibt Siemens Energy die Adaption von CMCs in industriellen Gasturbinen voran, um Effizienz und Lebensdauer zu verbessern und damit auf den globalen Druck zur Dekarbonisierung und zur Senkung der Energiekosten zu reagieren. Auch die Automobilindustrie beginnt, CMCs für Hochleistungsbremsbeläge und andere thermisch kritische Komponenten zu erkunden, wobei Lieferanten wie Brembo neue Pilotlinien einführen, um der frühen Nachfrage gerecht zu werden.
Technologische Fortschritte in der CMC-Herstellung beschleunigen das sektorale Wachstum weiter. Innovationen in der chemischen Dampfabscheidung, der Polymerinfiltration und Pyrolyse sowie in schlickerbasierten Verfahren reduzieren die Zykluszeiten und ermöglichen komplexere Geometrien, während digitale Prozessüberwachung und Automatisierung die Qualität und Skalierbarkeit verbessern. Hersteller arbeiten zunehmend mit Forschungskonsortien und Regierungsbehörden zusammen, um Kostentrukturen zu verfeinern und neue CMC-Qualitäten zu entwickeln, die auf extreme Umgebungen zugeschnitten sind.
Prognosen für 2025 und die nahe Zukunft zeigen robuste zweistellige Wachstumsraten für den globalen CMC-Markt, mit Expansionen der Lieferkette in Nordamerika, Europa und Asien. Führende Hersteller wie Morgan Advanced Materials und CoorsTek investieren in zusätzliche Produktionskapazitäten und die Entwicklung neuer Produkte, um sich emerging Chancen zu sichern.
Insgesamt betritt die CMC-Produktion einen Wendepunkt mit stark steigender sektorübergreifender Akzeptanz, signifikanten Investitionen und laufenden Durchbrüchen in der Materialwissenschaft, was das Fundament für explosives Wachstum bis zum Ende des Jahrzehnts legt.
Marktübersicht 2025: Schlüsselakteure und aufstrebende Führungskräfte
Im Jahr 2025 wird der Sektor der keramischen Matrixverbunde (CMC) durch eine Kombination etablierter globaler Akteure und einer wachsenden Gruppe aufstrebender Innovatoren geprägt, die durch die steigende Nachfrage aus Luft- und Raumfahrt, Energie und Automobilindustrie angetrieben wird. Der Markt wird durch Materialfortschritte, erweiterte Produktionskapazitäten und strategische Investitionen geprägt, die darauf abzielen, die Skalierbarkeit und Zuverlässigkeit von CMCs für Hochtemperatur- und Leichtbauanwendungen zu erhöhen.
An der Spitze des Marktes stehen langjährige Hersteller wie General Electric, Safran und COI Ceramics, die alle erheblich in CMC-Forschung, Pilotproduktionslinien und komerziellen Herstellungsanlagen investiert haben. General Electric baut seine CMC-Produktionskapazität in den USA weiter aus, um kritische Triebwerkskomponenten für kommerzielle und militärische Jet-Triebwerke bereit zu stellen. Ebenso hat Safran CMCs in sein LEAP-Triebwerksprogramm integriert und arbeitet aktiv an Triebwerksystemen der nächsten Generation mit weiteren CMC-Inhalten, um Gewicht zu reduzieren und die thermische Effizienz zu verbessern.
Auf der Zuliefererseite sind 3M und Morgan Advanced Materials wichtige Anbieter von CMC-Rohstoffen und Halbfabrikaten, die das Wachstum der nachgeordneten Fertigung unterstützen. Morgan Advanced Materials hat insbesondere sein Portfolio an Metalloxid- und Nichtmetalloxid-CMCs für Industrie- und Verteidigungsanwendungen erweitert, während 3M Innovationen im Bereich hochtemperaturbeständiger Faserverstärkungen fortsetzt.
Aufstrebende Führungskräfte gewinnen ebenfalls an Bedeutung, insbesondere CeramTec und SGL Carbon, die beide erhebliche Fortschritte in der Prozessautomatisierung und der Anpassung von CMC-Komponenten erzielt haben. CeramTec investiert in skalierbare Fertigung für elektrische Mobilität und Energieanwendungen, während SGL Carbon die Produktion von kohlenstofffaserverstärkten Keramiken für Luft- und Raumfahrt und Halbleiteranlagen erhöht hat.
Die Zusammenarbeit zwischen Herstellern und Endbenutzern intensiviert sich, wobei Joint Ventures und langfristige Lieferverträge häufiger werden. Dies ist in den Partnerschaften zwischen Triebwerks-OEMs und CMC-Spezialisten deutlich, die die Akzeptanz von CMCs in der Serienproduktion fördern. Gleichzeitig bemühen sich asiatische Akteure wie Toshiba und Nippon Carbon um strategische Schritte zur Erweiterung ihrer globalen Präsenz mit einem Fokus sowohl auf Luftfahrt als auch auf industrielle Wärmeverwaltung.
Die Aussichten für die nächsten Jahre weisen auf weitere Kapazitätserweiterungen hin, mit signifikanten Investitionen in Automatisierung und digitale Prozesskontrolle, die voraussichtlich die Qualitätskonsistenz und Kosteneffizienz verbessern werden. Da CMCs für Hochleistungssektoren unverzichtbar werden, wird sich die Wettbewerbslandschaft wahrscheinlich weiter diversifizieren, mit neuen Allianzen und einem nachhaltigen Fokus auf Skalierung, um den zunehmend strengen Anforderungen an Leistung und Nachhaltigkeit gerecht zu werden.
Neueste Durchbrüche in der CMC-Verarbeitungstechnologie
Keramische Matrixverbunde (CMCs) haben im Jahr 2025 bedeutende technologische Fortschritte in den Herstellungsverfahren erzielt, die durch die steigende Nachfrage in den Bereichen Luft- und Raumfahrt, Energie und Industrie angetrieben werden. Jüngste Durchbrüche konzentrieren sich auf die Verbesserung der Skalierbarkeit, Kosteneffizienz und Komponentenleistung, insbesondere in Hochtemperatur- und Hochbelastungsanwendungen.
Eine bemerkenswerte Entwicklung ist der Fortschritt in der chemischen Dampfabscheidung (CVI) und in Schlamm-Infiltrationstechniken. Diese Methoden profitieren jetzt von erhöhtem Automatisierungsgrad und Echtzeit-Prozesskontrolle, was engere Qualitätsstandards und kürzere Produktionszyklen ermöglicht. Große Akteure der Branche wie GE Aerospace haben automatisierte CVI zur Produktion von Triebwerksteilen der nächsten Generation implementiert und berichten von verkürzten Zyklen und verbesserter Wiederholbarkeit für komplexe Geometrien. Dies ist entscheidend, um der wachsenden Nachfrage nach kraftstoffeffizienten Triebwerken gerecht zu werden, bei denen CMCs konventionelle Superlegierungen in heißen Bereichen von Turbinen ersetzen.
Gleichzeitig hat sich die Polymerinfiltration und Pyrolyse (PIP) weiterentwickelt, wobei Unternehmen wie Safran den Prozess für die großflächige Herstellung von CMC-Teilen optimieren. Zu den Innovationen gehören modifizierte präkeramische Polymere und fortschrittliche Faserarchitekturen, die zu einer verbesserten Matrixdichtheit und Schadensresistenz führen. Die neuesten PIP-Fortschritte haben die Produktion von größeren, komplizierteren Komponenten ermöglicht, ohne die mechanischen Eigenschaften zu beeinträchtigen, was besonders für die Märkte der Luft- und Raumfahrt und von Energie-Gasturbinen relevant ist.
Ein weiterer entscheidender Durchbruch ist die Einführung von additiver Fertigung (AM) für CMCs. Pioniere wie Siemens nutzen 3D-Druck zur Herstellung komplexer SiC/SiC- und Oxid/Oxid-CMC-Komponenten, wodurch Materialabfälle und Durchlaufzeiten reduziert werden. AM ermöglicht neue Designmöglichkeiten, darunter integrierte Kühllösungen und leichte Gitterstrukturen, die mit traditionellen Fertigungsmethoden zuvor nicht erreichbar waren.
Darüber hinaus wurden verbesserte Faserschutzschichten und hybride Verstärkungsstrategien eingeführt, um die interfacialen Eigenschaften und die Rissresistenz zu steigern. Kooperationen zwischen Industrie und Materiallieferanten haben zu robusten Faser-Matrix-Bindungen und oxidationsbeständigen Beschichtungen geführt, die die Lebensdauer von CMCs in extremen Umgebungen weiter verlängern.
Blickt man in die Zukunft, erwartet die Industrie eine kontinuierliche Integration von digitalen Fertigungstools, wie z.B. prozessoptimierenden Machine-Learning-Methoden und In-situ-Qualitätsüberwachung. Diese Fortschritte sollen die Kosten weiter senken und die Einführung von CMCs in neuen Anwendungen, einschließlich fortschrittlicher Mobilität und Wasserstoffenergiesystemen, beschleunigen. Da führende Hersteller weiterhin in Innovation investieren, stehen die CMC-Verarbeitungstechnologien vor einer breiteren Industrialisierung und einer stärkeren Marktdurchdringung bis 2025 und darüber hinaus.
Wichtige Endverbrauchersektoren: Luft- und Raumfahrt, Energie, Automobil und mehr
Keramische Matrixverbunde (CMCs) verzeichnen ein bemerkenswertes Wachstum in der Fertigung über wichtige Endverbrauchersektoren hinweg, angetrieben durch ihre überlegene thermische Stabilität, geringe Dichte und hohe mechanische Festigkeit. Ab 2025 und in den darauf folgenden Jahren stehen die Luft- und Raumfahrt, Energie und Automobilindustrie an der Spitze bei der Einführung von CMCs, mit laufenden Fortschritten in der Fertigungstechnik und einer soliden Pipeline von Kommerzialisierungsbemühungen.
In der Luft- und Raumfahrt werden CMCs schnell sowohl in zivilen als auch in verteidigungstechnischen Anwendungen integriert, insbesondere für Komponenten im heißen Triebwerksbereich. Führende Triebwerkshersteller wie GE Aerospace und Safran haben die Produktion von CMC-Turbinenverkleidungen, Brennkammerverkleidungen und Düsen für Triebwerke der nächsten Generation erhöht. Diese Komponenten ermöglichen höhere Betriebstemperaturen und verbessern die Kraftstoffeffizienz, was direkt zur Erreichung von Nachhaltigkeitszielen beiträgt. Bis 2025 plant GE Aerospace, die CMC-Produktion in ihren spezialisierten Einrichtungen in den USA zu skalieren, während Safran weiterhin an gemeinsamen Anstrengungen in Europa arbeitet, um die Integration von CMCs in kommerzielle und militärische Plattformen zu erweitern.
Der Energiesektor, insbesondere Gasturbinen zur Stromerzeugung, entwickelt sich ebenfalls zu einem bedeutenden Anwender. Unternehmen wie Siemens Energy investieren in CMC-Technologie, um die Lebensdauer und Effizienz von Komponenten in Hochtemperatur-Gasturbinenumgebungen zu verbessern. Dieser Trend wird voraussichtlich an Fahrt gewinnen, da Unternehmen nach Wegen suchen, um Emissionen und Wartungskosten zu senken, indem sie die Widerstandsfähigkeit von CMCs gegenüber Oxidation und thermischer Ermüdung nutzen.
In der Automobilindustrie wächst die Akzeptanz von CMCs, insbesondere in Hochleistungs- und Elektrofahrzeugen, wo Gewichtseinsparung und Wärmemanagement entscheidend sind. Pioniere wie Brembo setzen CMCs in fortschrittlichen Bremssystemen ein, die eine verbesserte Wärmeableitung und Haltbarkeit für Sport- und Luxusfahrzeuge bieten. Mit steigenden regulatorischen Anforderungen an Emissionen und Elektrifizierung wird erwartet, dass Automobilhersteller CMCs auch für Strukturkomponenten und Wärmeschutzsysteme bis 2025 und darüber hinaus weiter evaluieren.
Auch andere Sektoren wie die industrielle Verarbeitung, Verteidigung und Raumfahrt erkunden CMCs für Anwendungen, die von Schutzpanzern bis zu Hitzeschildern reichen. Wichtige Hersteller wie CoorsTek und 3M erweitern ihre Produktportfolios und Fertigungskapazitäten, um dieser wachsenden Nachfrage gerecht zu werden.
In der Zukunft bleibt die Perspektive für die CMC-Produktion in diesen Sektoren stark, mit laufenden Investitionen in automatisierte Produktionsmethoden, dem Ausbau der Faserproduktion und strategischen Partnerschaften zwischen OEMs und Materialanbietern. Diese Entwicklungen werden wahrscheinlich die weitere Integration von CMCs in mission-kritische Komponenten vorantreiben und ihre Position als transformative Materialklasse im Verlauf des Jahrzehnts festigen.
Innovationen in der Lieferkette und Strategien zur Rohstoffbeschaffung
Die Herstellung von keramischen Matrixverbunden (CMC) erlebt im Jahr 2025 transformative Innovationen in der Lieferkette und Strategien zur Rohstoffbeschaffung, die durch die erhöhte Nachfrage aus den Sektoren Luft- und Raumfahrt, Verteidigung und Energie angetrieben werden. Da OEMs und Tier-1-Zulieferer ihren Fokus auf leichte, temperaturbeständige Materialien verstärken, reagiert der CMC-Sektor mit sowohl upstream- als auch downstream-Änderungen, um die Versorgungssicherheit und Kosteneffizienz sicherzustellen.
Ein wichtiger Trend im Jahr 2025 ist die vertikale Integration der Rohstoffbeschaffung. Führende CMC-Hersteller wie GE und Safran haben langfristige Lieferverträge für kritische Eingänge wie hochreine Siliziumkarbid (SiC)-Fasern und Aluminiummatrizen gesichert. Diese Strategien sollen gegen Rohstoffengpässe und geopolitische Risiken absichern, insbesondere für SiC-Fasern, die aufgrund der begrenzten weltweiten Produktionskapazität einen Flaschenhals darstellen. Unternehmen wie Mitsubishi Chemical haben ihre SiC-Faser-Produktion erweitert, um den sprunghaften Anforderungen an die Produktion von CMC-Komponenten in großen Mengen gerecht zu werden.
Um Herausforderungen in Bezug auf Nachhaltigkeit und Kosten zu begegnen, übernehmen CMC-Produzenten zunehmend geschlossene Recyclingverfahren und alternative Vorläuferbeschaffungen. So hat Rolls-Royce Programme zur Wiederverwertung von nicht konformen CMC-Reststoffen pilotiert und recycelte Fasern in neue Produktionschargen eingeführt, was die Abhängigkeit von Primärmaterialien verringert und die Gesamtkosten senkt. Gleichzeitig erkundet die Branche die Verwendung von biobasierten und recycelten Vorläufern zur Matrizbildung, obwohl diese 2025 noch im Demonstrationsstadium sind.
Das digitale Lieferkettenmanagement ist ein weiteres schnell fortschreitendes Gebiet. Hersteller nutzen digitale Zwillinge, Blockchain-Rückverfolgbarkeit und fortgeschrittene Analytik, um Lagerbestände zu optimieren, die Qualität der Zulieferer zu überwachen und die Transparenz zu erhöhen. Safran hat beispielsweise eine Echtzeitverfolgung kritischer Rohmateriallieferungen implementiert, um agil auf Störungen reagieren und die Zusammenarbeit mit upstream-Partnern verbessern zu können.
Für die Zukunft bleibt die Perspektive für Innovationen in der CMC-Lieferkette robust. Während globale Luft- und Raumfahrtprogramme, insbesondere die von GE und Rolls-Royce, die Produktion von Triebwerken der nächsten Generation steigern, wird die Nachfrage nach qualitativ hochwertigen, zuverlässigen CMC-Inputstoffen weitere Kapazitätserweiterungen und neue Akteure in der Faserproduktion anziehen. Die Branchenakteure erwarten, dass die Partnerschaften zwischen CMC-Produzenten und Materiallieferanten fortgesetzt werden, um die Sicherheit der Versorgung zu gewährleisten und die Einführung fortschrittlicher Beschaffungsstrategien bis mindestens zum Ende des Jahrzehnts zu beschleunigen.
Regionale Hotspots: Nordamerika, Europa und asiatisch-pazifische Trends
Die Herstellung von keramischen Matrixverbunden (CMC) erlebt dynamisches regionales Wachstum, das durch die steigende Nachfrage in den Bereichen Luft- und Raumfahrt, Verteidigung, Energie und Automobilindustrie angetrieben wird. Im Jahr 2025 stechen Nordamerika, Europa und der asiatisch-pazifische Raum als Haupt-Hotspots hervor, die jeweils mit unterschiedlichen Strategien und Investitionen voranschreiten.
Nordamerika – angeführt von den USA – dominiert weiterhin die CMC-Innovation und -Produktion, insbesondere für Luft- und Raumfahrt- und Verteidigungsanwendungen. Große Hersteller wie GE Aerospace und Northrop Grumman erweitern den Einsatz von CMC-Komponenten in Flugzeugtriebwerken und hypersonischen Plattformen. Besonders hervorzuheben ist GE’s CMC-Werk in Huntsville, Alabama, das die Produktion für Triebwerke der nächsten Generation erhöht und dabei die proprietäre Siliziumkarbidmatrix-Technologie des Unternehmens nutzt. Auch das US-Energieministerium hat kollaborative Maßnahmen zur Beschleunigung der heimischen Widerstandsfähigkeit der Lieferkette für fortschrittliche Keramiken angekündigt, was auf anhaltende staatliche Unterstützung bis 2025 und darüber hinaus hinweist.
Europa festigt seine Position durch strategische Partnerschaften und Investitionen, die auf saubere Mobilität und Energieeffizienz fokussiert sind. Unternehmen wie Safran und Rolls-Royce integrieren CMCs in neue Aero-Triebwerksdesigns, um Gewicht zu reduzieren und die thermische Leistung zu verbessern. Die Horizont-Programme der Europäischen Union fördern grenzüberschreitende Forschung zu Verbundstoffen der nächsten Generation, während Deutschland und Frankreich führend in der Produktion bleiben. Darüber hinaus erkundet der Automobilsektor in Europa CMCs für Hochleistungs-Bremssysteme und andere Komponenten, wobei Zulieferer wie Brembo in diesem Bereich innovativ sind.
Asiatisch-Pazifischer Raum, angeführt von China und Japan, beschleunigt die CMC-Kapazität sowohl für den Inlandsbedarf als auch für die globale Versorgung. Chinesische Hersteller einschließlich Aviation Industry Corporation of China (AVIC) skalieren ihre Einrichtungen, um den Anforderungen der schnell wachsenden Luft- und Raumfahrt- und Energiemärkte gerecht zu werden. Japans Mitsubishi Heavy Industries und Toray Industries sind Pioniere in Technologien zur Verbesserung der Materialeigenschaften und der Fertigungseffizienz von CMCs. Die Region erlebt auch eine zunehmende Investition durch Regierungen, die die Lokalisierung fortschrittlicher Materialien unterstützen, mit einem Fokus auf den Übergang zur Energieerzeugung und den Hochgeschwindigkeitsverkehr.
Für die Zukunft sind diese regionalen Hotspots gut positioniert, um das globale Wachstum der CMC-Produktion voranzutreiben, angetrieben von einer Nachfrage aus mehreren Sektoren und fortlaufenden technologischen Fortschritten. Strategische Partnerschaften, staatliche Unterstützung und ein Fokus auf Nachhaltigkeit werden die Wettbewerbslandschaft bis Ende der 2020er Jahre prägen.
Investitionen, M&A und strategische Partnerschaften in der CMC-Produktion
Die Landschaft von Investitionen, Fusionen und Übernahmen (M&A) und strategischen Partnerschaften in der Herstellung von keramischen Matrixverbunden (CMC) unterliegt bis 2025 bemerkenswerten Veränderungen, die durch die steigende Nachfrage in den Sektoren Luft- und Raumfahrt, Energie und Automobilindustrie angetrieben werden. Die Hochleistungsmerkmale von CMCs – wie ihre thermische Stabilität, Haltbarkeit und ihr geringes Gewicht – ziehen weiterhin erhebliche Kapitalzuflüsse und gemeinsame Initiativen sowohl etablierter Akteure als auch neuer Mitbewerber an.
Im vergangenen Jahr haben mehrere große CMC-Hersteller neue Investitionsrunden und Produktionskapazitätserweiterungen angekündigt. Beispielsweise hat GE Aerospace weiter in seine CMC-Herstellungseinrichtungen in den USA investiert, um sowohl die Anwendungen in der Luftfahrt als auch in der Energiebranche anzusprechen. Die Anlage in Auburn, Alabama, bleibt ein Eckpfeiler seiner Strategie, mit laufenden Upgrades, die darauf abzielen, die Produktionskapazität und die Automatisierung der Prozesse zu erhöhen.
In Europa haben Safran und Airbus ihre langjährige Partnerschaft verstärkt, die sich auf die Industrialisierung von CMCs mit Oxid-Oxid- und SiC/SiC-Qualitäten für Turbinen- und Strukturkomponenten konzentriert. Die Partnerschaft zwischen Safran und MTU Aero Engines hat ebenfalls zugenommen, unter anderem durch gemeinsame Entwicklungsprojekte und gemeinsame Investitionen in F&E, um die technologische Bereitschaft für die kommerzielle Luftfahrt zu beschleunigen.
Strategische Allianzen nehmen weiter zu, insbesondere zwischen CMC-Herstellern und Zulieferern von fortschrittlichen Fasern und Vorläufern. CeramTec hat ihre Zusammenarbeit mit Faseranbietern vertieft, um die upstream-Wertschöpfungskette abzusichern und sowohl Qualität als auch Skalierbarkeit zu gewährleisten. In der Zwischenzeit hat COI, ein japanischer CMC-Hersteller, seine Partnerschaften mit Automobil-OEMs ausgeweitet, um gemeinsam CMC-Bremskomponenten zu entwickeln und die wachsende Nachfrage nach hochleistungsfähigen, leichten Autoteilen zu erfassen.
Die M&A-Aktivitäten werden voraussichtlich bis 2025 und darüber hinaus robust bleiben, da größere Akteure Nischentechnologieanbieter erwerben und sich Wettbewerbsvorteile in Prozess-technologien oder geistigem Eigentum sichern möchten. Dieser Trend ist durch das anhaltende Interesse von Konglomeraten wie 3M veranschaulicht, das historisch sein Portfolio an fortschrittlichen Materialien durch gezielte Akquisitionen erweitert hat. Zudem signalisiert die zunehmende Präsenz von Private-Equity- und Staatsfonds, insbesondere in Nordamerika und Asien, wachsende Zuversicht in die langfristigen Perspektiven des Sektors.
In Zukunft wird der CMC-Herstellungssektor voraussichtlich intensivere grenzüberschreitende Investitionen, weiterhin vertikale Integration und einen Anstieg in gemeinschaftlichen F&E-Vorhaben erleben – Faktoren, die für die Skalierung der Produktion und die Erfüllung der strengen Anforderungen an zukünftige Luftfahrt- und Energiesysteme entscheidend sind.
Nachhaltigkeit und Umweltauswirkungen der CMC-Produktion
Die Nachhaltigkeit und die Umweltauswirkungen der Herstellung keramischer Matrixverbunde (CMC) werden 2025 und darüber hinaus zu zentralen Anliegen der Branche. Da die Nachfrage nach CMCs in den Anwendungen Luft- und Raumfahrt, Energie und Automobil steigt, stehen die Hersteller unter zunehmendem Druck, den ökologischen Fußabdruck ihrer Prozesse zu minimieren. CMCs, insbesondere Siliziumkarbid- und oxidbasierte Verbunde, bieten gegenüber herkömmlichen Legierungen erhebliche ökologische Vorteile im Lebenszyklus – primär durch Gewichtsreduzierung, verbesserte Kraftstoffeffizienz und erhöhte Haltbarkeit im Betrieb. Allerdings erhalten die Umweltauswirkungen ihrer Produktionsprozesse, einschließlich Energieverbrauch, Rohstoffbeschaffung und Abfallproduktion, verstärkte Aufmerksamkeit.
Wichtige CMC-Produzenten wie GE Aerospace, Safran und COI Ceramics haben Maßnahmen ergriffen, um diese Herausforderungen zu adressieren. Aktuelle Bemühungen konzentrieren sich auf die Optimierung des Energieverbrauchs in energieintensiven Verarbeitungsschritten wie chemischer Dampfabscheidung und Sintern. So hat GE Aerospace öffentlich über seine Fortschritte bei der Reduzierung des CO2-Fußabdrucks seiner CMC-Produktion berichtet und setzt dabei auf erneuerbare Energiequellen sowie verbesserte Prozesskontrollen, um die Emissionen pro produzierter Einheit zu senken.
Abfallmanagement und Recycling sind ebenfalls zu wichtigen Prioritäten geworden. Die von Natur aus inerten und stabilen keramischen Matrizen erschweren das Recycling, aber Branchenführer pilotieren geschlossene Systeme, um Abfälle und fehlerhafte Teile zurückzugewinnen. Safran hat Entwicklungsprogramme angekündigt, die darauf abzielen, Produktionsabfälle in neue Komponenten zu reintegrieren, um Abfall auf Deponien und die Nachfrage nach Primärrohstoffen zu reduzieren. Einige Hersteller erkunden auch bioabgeleitete Vorläufer und Bindemittel, um die Abhängigkeit von fossilen Chemikalien zu verringern.
Der Wasserverbrauch und gefährliche Nebenprodukte werden besonders in Verfahren, die Schlammen oder chemische Behandlungen umfassen, untersucht. Führende Firmen investieren in fortschrittliche Filtersysteme und Lösungsmittelrückgewinnung, um Umweltentlastungen zu reduzieren.
In den nächsten Jahren wird die Branche voraussichtlich eine größere Zusammenarbeit im Bereich von Nachhaltigkeitsstandards und Lebenszyklusbewertungsmethoden (LCA) für CMCs erleben. Organisationen wie die EUROPEAN CONFERENCE FOR AERONAUTICS AND SPACE SCIENCES (EUCASS) fördern den Dialog über harmonisierte Kriterien und bewährte Verfahren. Da der Druck durch regulatorische Anforderungen zunimmt und Kunden zunehmend grüne Herstellungszertifikate verlangen, werden CMC-Produzenten wahrscheinlich ihre Einführung sauberer Technologien und Kreislaufwirtschaftsprinzipien beschleunigen. Dieser Wandel wird voraussichtlich das Nachhaltigkeitsprofil von CMCs verbessern und ihre Rolle bei der Ermöglichung von kohlenstoffärmeren, leistungsstarken Ingenieurlösungen weiter stärken.
Marktprognose 2025–2030: Umsatz-, Volumen- und Preisanalysen
Der Sektor der keramischen Matrixverbunde (CMC) steht von 2025 bis 2030 vor robustem Wachstum, untermauert durch die steigende Nachfrage in den Bereichen Luft- und Raumfahrt, Verteidigung, Energie und Automobilindustrie. Ab 2025 erwarten die Akteure der Branche einen fortdauernden Anstieg sowohl des Umsatzes als auch der Produktionsvolumina, was einen strategischen Wandel hin zu hochleistungsfähigen, leichten Materialien widerspiegelt, die extremen Bedingungen standhalten können.
Anwendungen in der Luft- und Raumfahrt bleiben der Haupttreiber für die Einführung von CMCs, da Unternehmen wie General Electric die Integration von CMCs in die Triebwerke der nächsten Generation beschleunigen. Die Triebwerke LEAP und GE9X von GE verfügen beispielsweise über CMC-Turbinenkomponenten, die zu einer verbesserten Kraftstoffeffizienz und reduzierten Emissionen beitragen. Safran und Rolls-Royce verfolgen ebenfalls ähnliche Initiativen und investieren in CMC-Produktionskapazität und Forschung für Triebwerksysteme. Es wird erwartet, dass diese Projekte die Produktionsmengen zwischen 2025 und 2030 erheblich steigern, da die Programme für kommerzielle und militärische Flugzeuge ansteigen.
Im Energiesektor nutzt Siemens CMCs zur Verbesserung der Leistung von industriellen Gasturbinen, mit dem Ziel, die thermische Widerstandsfähigkeit und die Betriebslebensdauer zu erhöhen. Automobilhersteller erkunden ebenfalls CMCs für Hochtemperaturanwendungen wie Bremssysteme, wobei Brembo die Entwicklung von CMC-Bremsbelägen für Premium- und Elektrofahrzeuge leitet – ein Trend, der voraussichtlich während dieses Zeitraums an kommerzieller Dynamik gewinnt.
Die Branchenexperten prognostizieren, dass die globalen Einnahmen aus der CMC-Herstellung eine jährliche Wachstumsrate (CAGR) im hohen einstelligen Bereich erfahren werden und die gesamte Marktwert möglicherweise mehrere Milliarden USD bis 2030 überschreiten könnte. Das Volumenwachstum wird durch Investitionen in fortgeschrittene Fertigungstechniken, einschließlich automatisierter Faserplatzierung und chemischer Dampfabscheidung, unterstützt, wie sie von Herstellern wie COI Ceramics und Snecma (ein Unternehmen von Safran) genutzt werden. Es wird erwartet, dass diese Fortschritte helfen werden, die Produktionskosten zu senken und die Skalierbarkeit zu verbessern.
Trotz der zu erwartenden Volumenzunahmen werden die CMC-Preise aufgrund der komplexen Verarbeitungsanforderungen und hohen Rohstoffkosten – insbesondere für Siliziumkarbidfasern und -matrizen – wahrscheinlich hoch bleiben im Vergleich zu herkömmlichen Keramiken oder Metalllegierungen. Allerdings könnten mit der Reifung der Herstellungsprozesse und der Realisierung von Kostensenkungs-Beschleunigungen allmähliche Preissenkungen beobachtet werden, was die Zugänglichkeit für breitere industrielle Anwendungen verbessert.
Insgesamt wird die Perspektive für die CMC-Herstellung von 2025 bis 2030 durch erweiterte Kapazitäten, technologische Reifung und einen stetigen Zustrom einer Endmarktnachfrage geprägt sein, was auf eine Phase dynamischen Wachstums und Wandels für den Sektor hinweist.
Zukünftige Ausblicke: Anwendungen der nächsten Generation und Technologie-Roadmap
Im Blick auf 2025 und die darauffolgenden Jahre steht der Sektor der keramischen Matrixverbunde (CMC) vor bedeutenden Fortschritten, die durch die Reifung von Technologien, Investitionen in die Lieferkette und die wachsende Annahme in Endanwendungen vorangetrieben werden. CMCs, geschätzt für ihr außergewöhnliches Verhältnis von Festigkeit zu Gewicht und Temperaturbeständigkeit, sind zunehmend entscheidend in den Anwendungen Luft- und Raumfahrt, Energie, Verteidigung und Automobil.
Die Luft- und Raumfahrt bleibt der führende Treiber für die nächste Generation der CMC-Produktion. Große Triebwerkshersteller steigern die Integration von CMCs sowohl in kommerzielle als auch militärische Jet-Triebwerke. So hat GE Aerospace weiterhin in die CMC-Produktionskapazität investiert, um eine erhöhte Verwendung in Komponenten für heiße Bereiche zu ermöglichen, die höhere Betriebstemperaturen und verbesserte Kraftstoffeffizienz ermöglichen. Ebenso beschleunigt Safran die Einführung von CMCs in seinen LEAP-Triebwerken und arbeitet eng mit Zulieferern zusammen, um die Skalierbarkeit zu verbessern und die Zykluszeiten zu reduzieren.
Im technologische Bereich tauchen mehrere Prozessinnovationen auf. Fortschrittliche automatisierte Faserplatzierung, schnelle chemische Dampfabscheidung (CVI) und Schlamm-Infiltrationstechniken werden verfeinert, um die Produktion zu optimieren und die Kosten zu senken. SGL Carbon fördert die Verwendung hybrider Fertigungsansätze, die additive Fertigung mit traditioneller CVI kombinieren, um komplexere Geometrien zu schaffen und Abfälle zu minimieren. Der Fokus verschiebt sich außerdem hin zur Digitalisierung – der Integration von Echtzeit-Prozessüberwachung und prädiktiver Analytik, um Qualität und Wiederholbarkeit zu verbessern.
Über die Luft- und Raumfahrt hinaus gewinnen Energieanwendungen an Dynamik. Siemens Energy untersucht CMCs für hocheffiziente Gasturbinen, wo deren thermische Stabilität einen Betrieb bei höheren Temperaturen und Drücken ermöglicht. Auch die Automobilindustrie zeigt ein erneutes Interesse, wobei Brembo und andere Bremshersteller CMC-basierte Bremsscheiben für Leistungs- und Elektrofahrzeuge entwickeln, mit einem Fokus auf Langlebigkeit, Gewichtsreduzierung und hohe Wärmeleitfähigkeit.
Entwicklungen in der Lieferkette sind ebenfalls zentral für die CMC-Roadmap. Schlüsselmateriel-Lieferanten, einschließlich Hexcel und Toray Industries, erweitern ihre Möglichkeiten zur Produktion von Fasern und Vorformen, um die prognostizierte Nachfrage zu decken. Übergreifende Branchenkooperationen werden voraussichtlich die Qualifikationszyklen und die Standardisierung der Fertigungsprozesse beschleunigen, sodass neue Anwendungsbereiche weiter erschlossen werden können.
Bis Ende der 2020er Jahre, mit fortgesetzten Investitionen in Automatisierung, digitale Prozesskontrolle und Materialforschung und -entwicklung, wird erwartet, dass die CMC-Herstellung eine breitere Skalierung und Kostenwettbewerbsfähigkeit erreicht. Dies wird nicht nur die weitere Einführung in traditionellen Märkten anstoßen, sondern auch neue Anwendungen in Bereichen wie hypersonischen Fahrzeugen, industrieller Verarbeitung und Wasserstoffenergiesystemen eröffnen.