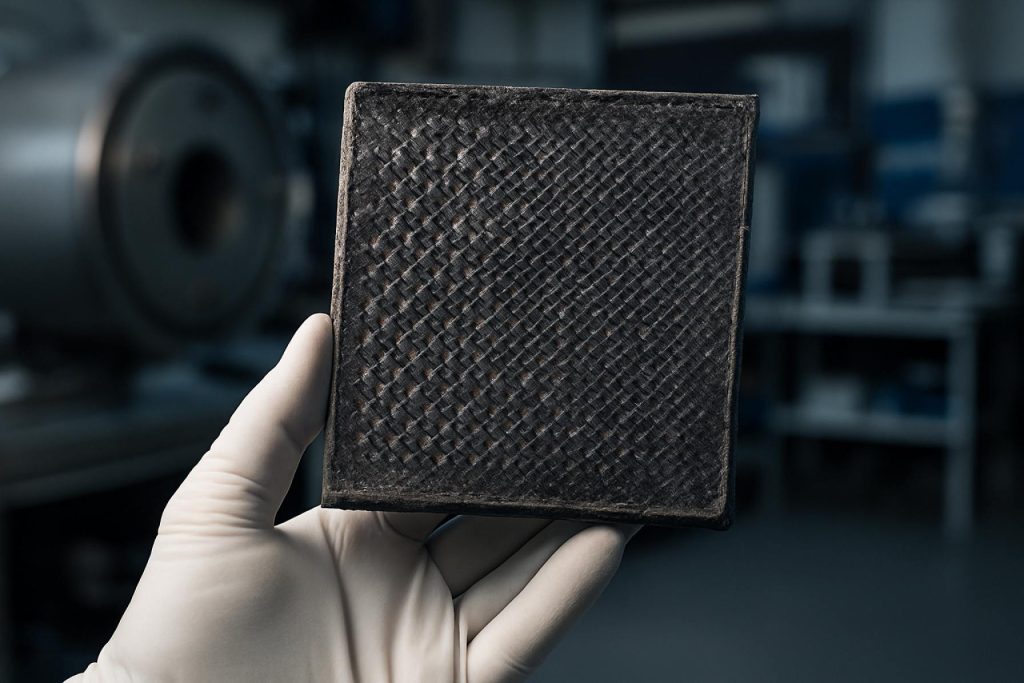
Contenido
- Resumen Ejecutivo: CMCs Listos para un Crecimiento Explosivo
- Visión General del Mercado 2025: Jugadores Clave y Líderes Emergentes
- Últimos Avances en Tecnologías de Procesamiento de CMC
- Sectores Principales de Usos Finales: Aeroespacial, Energía, Automotriz y Más
- Innovaciones en la Cadena de Suministro y Estrategias de Sourcing de Materias Primas
- Puntos Calientes Regionales: Norteamérica, Europa y Tendencias en Asia-Pacífico
- Inversión, M&A y Asociaciones Estratégicas en la Fabricación de CMC
- Sostenibilidad e Impacto Ambiental de la Producción de CMC
- Pronóstico del Mercado 2025–2030: Ingresos, Volumen y Perspectivas de Precios
- Perspectiva Futura: Aplicaciones de Nueva Generación y Hoja de Ruta Tecnológica
- Fuentes & Referencias
Resumen Ejecutivo: CMCs Listos para un Crecimiento Explosivo
La fabricación de Compuestos de Matriz Cerámica (CMC) está preparada para una expansión significativa en 2025 y en los años inmediatos, impulsada por la creciente demanda en los sectores aeroespacial, de defensa, energía y automotriz. Los CMCs—fabricados con fibras cerámicas incrustadas en una matriz cerámica—ofrecen una excepcional estabilidad térmica, baja densidad y resistencia a la corrosión, convirtiéndolos en un material crítico para aplicaciones de alta performance de próxima generación.
Las recientes actividades en la industria subrayan este impulso. Los principales OEMs aeroespaciales han aumentado drásticamente su inversión en capacidades de CMC. Por ejemplo, GE Aerospace ha expandido su huella de fabricación de CMC en los Estados Unidos, incluyendo su instalación en Carolina del Norte, para satisfacer los pedidos crecientes de componentes de motores a reacción ligeros y eficientes en combustible. Al mismo tiempo, Safran continúa escalando la integración de CMC, particularmente para programas de motores de aeronaves de próxima generación, aprovechando la fabricación interna así como empresas conjuntas.
En el sector energético, Siemens Energy está promoviendo la adopción de CMC en turbinas de gas industriales para mejorar la eficiencia y la vida útil operativa, respondiendo al impulso global hacia la descarbonización y la reducción de costos de energía. La industria automotriz también está comenzando a explorar los CMCs para discos de freno de alta performance y otros componentes térmicamente críticos, con proveedores como Brembo iniciando nuevas líneas piloto para abordar la demanda temprana.
Los avances tecnológicos en la fabricación de CMC están acelerando aún más el crecimiento del sector. Las innovaciones en infiltración de vapor químico, infiltración y pirólisis de polímeros, y métodos basados en lodos están reduciendo los tiempos de ciclo y permitiendo geometrías más complejas, mientras que el monitoreo digital de procesos y la automatización están mejorando la calidad y escalabilidad. Los fabricantes están colaborando cada vez más con consorcios de investigación y agencias gubernamentales para refinar estructuras de costos y desarrollar nuevas calidades de CMC adaptadas a entornos extremos.
Las previsiones para 2025 y el corto plazo indican tasas de crecimiento de dos dígitos robustas para el mercado global de CMC, con expansiones en la cadena de suministro en América del Norte, Europa y Asia. Productores líderes como Morgan Advanced Materials y CoorsTek están invirtiendo en capacidad de producción adicional y desarrollo de nuevos productos para capturar oportunidades emergentes.
En general, la fabricación de CMC está entrando en un punto de inflexión, con una adopción creciente entre sectores, una inversión de capital significativa y avances constantes en ciencia de materiales que establecen el escenario para un crecimiento explosivo durante el resto de la década.
Visión General del Mercado 2025: Jugadores Clave y Líderes Emergentes
En 2025, el sector de fabricación de compuestos de matriz cerámica (CMC) se define por una combinación de jugadores globales establecidos y un creciente grupo de innovadores emergentes, impulsados por la creciente demanda de las industrias aeroespacial, energética y automotriz. El mercado está moldeado por avances en materiales, capacidad de producción ampliada e inversiones estratégicas centradas en aumentar la escalabilidad y confiabilidad de los CMCs para aplicaciones de alta temperatura y bajo peso.
Liderando el mercado están fabricantes de larga data como General Electric, Safran y COI Ceramics, todos los cuales han invertido significativamente en investigación de CMC, líneas de producción piloto y fabricación a escala comercial. General Electric continúa expandiendo su capacidad de producción de CMC en los Estados Unidos, suministrando componentes críticos de motores para motores a reacción comerciales y militares. De manera similar, Safran ha integrado los CMCs en su programa de motores LEAP y está trabajando activamente en sistemas de propulsión de próxima generación con mayor contenido de CMC para reducir el peso y mejorar la eficiencia térmica.
En el lado de los proveedores, 3M y Morgan Advanced Materials son proveedores clave de materias primas de CMC y productos semiacabados, apoyando el crecimiento de la fabricación en downstream. Morgan Advanced Materials en particular ha ampliado su cartera de CMCs de óxido y no óxido para aplicaciones industriales y de defensa, mientras que 3M continúa innovando en el área de refuerzos de fibra de alta temperatura.
Los líderes emergentes también están ganando prominencia, notablemente CeramTec y SGL Carbon, ambas han realizado avances sustanciales en la automatización de procesos y la personalización de componentes de CMC. CeramTec está invirtiendo en la fabricación escalable para movilidad eléctrica y aplicaciones energéticas, mientras que SGL Carbon ha aumentado la producción de cerámicas reforzadas con fibra de carbono para equipos aeroespaciales y semiconductores.
La colaboración entre fabricantes y usuarios finales se está intensificando, con empresas conjuntas y acuerdos de suministro a largo plazo volviéndose más comunes. Esto es evidente en las asociaciones entre OEMs de motores y especialistas en CMC, fomentando la aceleración de la adopción de CMC en producción en serie. Al mismo tiempo, actores asiáticos como Toshiba y Nippon Carbon están realizando movimientos estratégicos para expandir su huella global, enfocándose tanto en la aeronáutica como en la gestión del calor industrial.
Las perspectivas para los próximos años apuntan a expansiones de capacidad adicionales, con importantes inversiones en automatización y control de procesos digitales que se espera mejoren la consistencia de calidad y la rentabilidad. A medida que los CMCs se convierten en parte integral de sectores de alto rendimiento, es probable que el panorama competitivo vea una mayor diversificación, nuevas alianzas y un enfoque sostenido en aumentar la producción para satisfacer los requisitos de rendimiento y sostenibilidad cada vez más estrictos.
Últimos Avances en Tecnologías de Procesamiento de CMC
Los compuestos de matriz cerámica (CMC) han visto avances tecnológicos significativos en los procesos de fabricación hasta 2025, impulsados por el aumento de la demanda en los sectores aeroespacial, energético e industrial. Los recientes avances se centran en mejorar la escalabilidad, la eficiencia de costos y el rendimiento de los componentes, particularmente en aplicaciones de alta temperatura y alta tensión.
Un desarrollo notable es el progreso en infiltración de vapor químico (CVI) y técnicas de infiltración de lodo. Estos métodos ahora se benefician de una mayor automatización y control de procesos en tiempo real, lo que permite tolerancias de calidad más estrictas y ciclos de producción más cortos. Los principales actores de la industria, como GE Aerospace, han implementado CVI automatizado para la producción de componentes de turbinas de próxima generación, informando sobre tiempos de ciclo reducidos y mejorada repetibilidad para geometrías complejas. Esto es crucial para satisfacer la creciente demanda de motores a reacción eficientes en combustible, donde los CMCs están reemplazando a las superaleaciones convencionales en secciones calientes de turbinas.
Simultáneamente, infiltración y pirólisis de polímeros (PIP) ha madurado, con empresas como Safran optimizando el proceso para la fabricación a gran escala de piezas de CMC. Las innovaciones incluyen polímeros precerámicos modificados y arquitecturas de fibra avanzadas, resultando en una mejor densificación de la matriz y tolerancia al daño. Los últimos avances en PIP han permitido la producción de componentes más grandes y complejos sin comprometer las propiedades mecánicas, lo que es especialmente relevante para los mercados de turbinas a gas aeroespaciales y energéticas.
Otro avance clave es la adopción de fabricación aditiva (AM) para CMCs. Pioneros como Siemens están aprovechando la impresión 3D para fabricar componentes complejos de CMC de SiC/SiC y óxido/óxido, reduciendo el desperdicio de material y los tiempos de entrega. La AM está permitiendo nuevas posibilidades de diseño, incluidos canales de enfriamiento integrados y estructuras de celosía ligeras, que anteriormente eran inalcanzables con métodos de fabricación tradicionales.
Además, se han introducido mejores recubrimientos de fibra y estrategias de refuerzo híbrido para mejorar las propiedades interfaciales y la resistencia a las grietas. Las colaboraciones entre la industria y los proveedores de materiales han llevado a un robusto enlace fibra-matriz y recubrimientos resistentes a la oxidación, prolongando aún más la vida útil de los CMCs en entornos extremos.
Mirando hacia adelante, se espera que la industria continúe integrando herramientas de manufactura digital, como la optimización de procesos impulsada por el aprendizaje automático y el monitoreo de calidad in situ. Se anticipa que estos avances reducirán aún más los costos y acelerarán la adopción de CMCs en aplicaciones emergentes, incluyendo movilidad avanzada y sistemas de energía a hidrógeno. A medida que los principales fabricantes continúan invirtiendo en innovación, las tecnologías de procesamiento de CMC están posicionadas para una mayor industrialización y una mayor penetración en el mercado hasta 2025 y más allá.
Sectores Principales de Usos Finales: Aeroespacial, Energía, Automotriz y Más
Los Compuestos de Matriz Cerámica (CMCs) están experimentando un notable crecimiento en la actividad de fabricación en los principales sectores de uso final, impulsados por su superior estabilidad térmica, baja densidad y alta resistencia mecánica. A partir de 2025, y mirando hacia los próximos varios años, las industrias aeroespacial, energética y automotriz están a la vanguardia de la adopción de los CMCs, con avances continuos en tecnologías de fabricación y una sólida pipeline de esfuerzos de comercialización.
En el ámbito aeroespacial, los CMCs se están integrando rápidamente en aplicaciones tanto civiles como de defensa, particularmente para componentes de sección caliente de motores. Los principales fabricantes de motores como GE Aerospace y Safran han aumentado la producción de carcazas de turbina de CMC, forros de combustión y boquillas para motores a reacción de próxima generación. Estos componentes permiten temperaturas de operación más altas y una mejor eficiencia de combustible, apoyando directamente los objetivos de sostenibilidad. Para 2025, GE Aerospace tiene como objetivo aumentar la producción de CMC en sus instalaciones dedicadas en los Estados Unidos, mientras que Safran continúa sus esfuerzos de colaboración en Europa para expandir la integración de CMC en plataformas comerciales y militares.
El sector energético, particularmente las turbinas de gas para generación de energía, también es un adoptante significativo. Empresas como Siemens Energy están invirtiendo en tecnología de CMC para extender la vida útil y eficiencia de los componentes en ambientes de turbinas de alta temperatura. Esta tendencia se espera que se acelere a medida que los servicios públicos busquen formas de reducir las emisiones y los costos de mantenimiento, aprovechando la resistencia de los CMCs a la oxidación y la fatiga térmica.
En el sector automotriz, la adopción de los CMCs está creciendo, especialmente en vehículos de alto rendimiento y eléctricos donde la reducción de peso y la gestión térmica son críticas. Pioneros como Brembo están empleando CMCs en sistemas de frenos avanzados, proporcionando mejor dissipación del calor y durabilidad para vehículos deportivos y de lujo. Con una presión regulatoria creciente sobre las emisiones y la electrificación, se espera que los fabricantes de automóviles evalúen aún más los CMCs para componentes estructurales y barreras térmicas hasta 2025 y más allá.
Otros sectores, como el procesamiento industrial, defensa y espacio, también están explorando los CMCs para aplicaciones que van desde armaduras protectoras hasta escudos térmicos. Fabricantes clave como CoorsTek y 3M están ampliando sus carteras de productos y capacidades de fabricación para abordar esta creciente demanda.
De cara al futuro, las perspectivas para la fabricación de CMC en estos sectores siguen siendo sólidas, con inversiones continuas en métodos de producción automatizados, aumento de la producción de fibras y asociaciones estratégicas entre OEMs y proveedores de materiales. Estos desarrollos probablemente impulsarán una mayor integración de los CMCs en componentes críticos de misión, reforzando su posición como una clase de material transformadora durante el resto de la década.
Innovaciones en la Cadena de Suministro y Estrategias de Sourcing de Materias Primas
La fabricación de compuestos de matriz cerámica (CMC) en 2025 está experimentando innovaciones transformadoras en la cadena de suministro y estrategias de aprovisionamiento de materias primas, impulsadas por la creciente demanda de los sectores aeroespacial, defensa y energía. A medida que los OEMs y los proveedores de primer nivel intensifican su enfoque en materiales ligeros y resistentes a altas temperaturas, el sector de CMC está respondiendo con cambios tanto en la parte superior como en la inferior de la cadena para asegurar la resiliencia de suministro y la rentabilidad.
Una tendencia importante en 2025 es la integración vertical del suministro de materias primas. Los principales fabricantes de CMC, como GE y Safran, han asegurado acuerdos de suministro a largo plazo para entradas críticas como fibras de carburo de silicio (SiC) de alta pureza y matrices de alúmina. Estas estrategias están diseñadas para protegerse contra la escasez de materias primas y los riesgos geopolíticos, particularmente para la fibra de SiC, que sigue siendo un cuello de botella de suministro debido a la limitada capacidad de producción global. Empresas como Mitsubishi Chemical han ampliado sus instalaciones de fabricación de fibra de SiC, con el objetivo de satisfacer los crecientes requerimientos de producción de componentes de CMC a gran escala.
Para abordar los desafíos de sostenibilidad y costos, los productores de CMC están adoptando cada vez más procesos de reciclaje de circuito cerrado y aprovisionamiento de precursores alternativos. Por ejemplo, Rolls-Royce ha pilotado programas para reciclar desechos de CMC fuera de especificación y reintroducir fibras recuperadas en nuevos lotes de fabricación, reduciendo la dependencia de materiales vírgenes y disminuyendo los costos totales del ciclo de vida. Al mismo tiempo, la industria está explorando el uso de precursores y aglutinantes bio-basados para la formación de matrices, aunque estos todavía se encuentran en la etapa de demostración en 2025.
La gestión digital de la cadena de suministro es otro área de rápido progreso. Los fabricantes están aprovechando gemelos digitales, trazabilidad basada en blockchain y análisis avanzados para optimizar niveles de inventario, monitorear la calidad del proveedor y mejorar la transparencia. Safran, por ejemplo, ha implementado un seguimiento en tiempo real para las entregas críticas de materias primas, lo que permite respuestas ágiles ante interrupciones y mejora la colaboración con socios en la parte superior de la cadena.
Mirando hacia el futuro, las perspectivas para la innovación en la cadena de suministro de CMC son robustas. A medida que los programas aeroespaciales globales, especialmente los liderados por GE y Rolls-Royce, aumentan la producción de motores de próxima generación, la demanda de materias primas de CMC de alta calidad y confiables incentivará aún más expansiones de capacidad y nuevos entrantes en la fabricación de fibras. Los actores de la industria anticipan asociaciones continuas entre productores de CMC y proveedores de materiales para garantizar la seguridad del suministro y acelerar la adopción de estrategias de aprovisionamiento avanzadas al menos hasta el final de la década.
Puntos Calientes Regionales: Norteamérica, Europa y Tendencias en Asia-Pacífico
La fabricación de compuestos de matriz cerámica (CMC) está experimentando un crecimiento regional dinámico, impulsado por la creciente demanda en los sectores aeroespacial, defensa, energía y automotriz. A partir de 2025, Norteamérica, Europa y Asia-Pacífico se destacan como puntos calientes principales, cada uno avanzando con estrategias e inversiones distintas.
Norteamérica, liderada por los Estados Unidos, continúa dominando la innovación y producción de CMC, particularmente en aplicaciones aeroespaciales y de defensa. Los principales fabricantes como GE Aerospace y Northrop Grumman están ampliando el despliegue de componentes de CMC en motores de aeronaves y plataformas hipersónicas. Notablemente, la planta de CMC de GE en Huntsville, Alabama, está aumentando la producción para motores a reacción de próxima generación, aprovechando la tecnología de matriz de carburo de silicio patentada de la empresa. El Departamento de Energía de EE.UU. también ha anunciado esfuerzos colaborativos para acelerar la resiliencia de la cadena de suministro nacional para cerámicas avanzadas, señalando un apoyo federal continuo a través de 2025 y más allá.
Europa está reforzando su posición a través de asociaciones estratégicas e inversiones centradas en la movilidad limpia y la eficiencia energética. Empresas como Safran y Rolls-Royce están integrando los CMCs en nuevos diseños de motores aeroespaciales, con el objetivo de reducir peso y mejorar el rendimiento térmico. Los programas Horizonte de la Unión Europea están fomentando la investigación transfronteriza sobre compuestos de nueva generación, mientras que Alemania y Francia siguen siendo líderes en producción. Además, el sector automotriz en Europa está explorando los CMCs para sistemas de frenos de alto rendimiento y otros componentes, con proveedores como Brembo innovando en este espacio.
Asia-Pacífico, liderada por China y Japón, está acelerando la capacidad de CMC tanto para uso doméstico como para suministro global. Fabricantes chinos, incluida la Corporación de la Industria de Aviación de China (AVIC), están ampliando instalaciones para satisfacer las necesidades de mercados aeroespaciales y energéticos en rápida expansión. Mitsubishi Heavy Industries y Toray Industries de Japón están pioneros en tecnologías para mejorar las propiedades de los materiales de CMC y la eficiencia de fabricación. La región también está presenciando un aumento en la inversión de gobiernos que apoyan la localización de materiales avanzados, con un enfoque en la transición energética y el transporte de alta velocidad.
Mirando hacia el futuro, estos puntos calientes regionales están preparados para impulsar el crecimiento global de la fabricación de CMC, impulsados por la demanda multi-sectorial y los continuos avances tecnológicos. Las asociaciones estratégicas, el respaldo gubernamental y un enfoque en la sostenibilidad están configurados para dar forma al panorama competitivo hasta finales de la década de 2020.
Inversión, M&A y Asociaciones Estratégicas en la Fabricación de CMC
El panorama de inversión, fusiones y adquisiciones (M&A) y asociaciones estratégicas en la fabricación de Compuestos de Matriz Cerámica (CMC) está experimentando una notable transformación a partir de 2025, impulsada por el aumento de la demanda en los sectores aeroespacial, energético y automotriz. Las características de alto rendimiento de los CMCs—como su estabilidad térmica, durabilidad y baja peso—siguen atrayendo flujos de capital significativos e iniciativas colaborativas entre actores establecidos y nuevos entrantes.
En el último año, varios importantes fabricantes de CMC han anunciado nuevas rondas de inversión y expansiones de capacidad de producción. Por ejemplo, GE Aerospace ha continuado aumentando su inversión en sus instalaciones de fabricación de CMC en los Estados Unidos, apuntando tanto a aplicaciones de motores de aviación como de energía. La planta de Auburn, Alabama, de la compañía sigue siendo una piedra angular de su estrategia, con actualizaciones en curso destinadas a aumentar el rendimiento y la automatización de procesos.
En Europa, Safran y Airbus han reforzado su asociación de larga data, centrándose en la industrialización de CMCs de óxido-óxido y SiC/SiC de próxima generación para componentes de turbinas y estructurales. La asociación de Safran con MTU Aero Engines también se ha intensificado, con proyectos de desarrollo conjunto e inversión compartida en I+D para acelerar los niveles de preparación tecnológica para la aviación comercial.
Las alianzas estratégicas se han multiplicado, particularmente entre fabricantes de CMC y proveedores de fibras avanzadas y materiales precursores. CeramTec ha profundizado su colaboración con proveedores de fibra para asegurar la cadena de valor en la parte superior, asegurando tanto calidad como escalabilidad. Mientras tanto, COI, un fabricante japonés de CMC, ha ampliado sus asociaciones con OEMs automotrices para co-desarrollar componentes de freno de CMC, con el objetivo de capturar la creciente demanda de piezas de automóvil ligeras y de alto rendimiento.
Se espera que la actividad de M&A siga siendo robusta a lo largo de 2025 y más allá, ya que los actores más grandes buscan adquirir proveedores de tecnología de nicho y asegurar ventajas competitivas en tecnologías de procesos o propiedad intelectual. Esta tendencia está ejemplificada por el interés continuo de conglomerados como 3M, que históricamente ha expandido su cartera de materiales avanzados a través de adquisiciones dirigidas. Además, la creciente presencia de fondos de capital privado y fondos soberanos, particularmente en América del Norte y Asia, señala una creciente confianza en las perspectivas a largo plazo del sector.
Mirando hacia el futuro, se espera que el sector de fabricación de CMC experimente una intensificación de las inversiones transfronterizas, una mayor integración vertical y un aumento en las iniciativas de I+D colaborativa—factores esenciales para aumentar la producción y cumplir con los estrictos requisitos de los sistemas aeroespaciales y energéticos de próxima generación.
Sostenibilidad e Impacto Ambiental de la Producción de CMC
La sostenibilidad y el impacto ambiental de la fabricación de compuestos de matriz cerámica (CMC) se están convirtiendo en preocupaciones centrales para la industria en 2025 y más allá. A medida que aumenta la demanda de CMCs en aplicaciones aeroespaciales, energéticas y automotrices, los fabricantes enfrentan una presión creciente para minimizar la huella ecológica de sus procesos. Los CMCs, en particular los compuestos de carburo de silicio y óxido, ofrecen ventajas ambientales significativas en el ciclo de vida en comparación con las aleaciones tradicionales—principalmente a través de la reducción de peso, la mejora de la eficiencia del combustible y la durabilidad mejorada en servicio. Sin embargo, los impactos ambientales de sus procesos de producción, incluyendo el uso de energía, la obtención de materias primas y la generación de desechos, están recibiendo un mayor escrutinio.
Los principales productores de CMC como GE Aerospace, Safran y COI Ceramics han iniciado medidas para abordar estos desafíos. Los esfuerzos actuales se centran en optimizar el consumo de energía en los pasos de procesamiento a alta temperatura, como la infiltración de vapor químico y el sinterizado, que son algunas de las etapas más intensivas en energía. Por ejemplo, GE Aerospace ha informado públicamente sobre su progreso en la reducción de la huella de carbono de su fabricación de CMC, aprovechando fuentes de energía renovable y mejorando los controles del proceso para reducir las emisiones por unidad de producción.
La gestión de desechos y el reciclaje también están surgiendo como prioridades clave. La naturaleza inherentemente inerte y estable de las matrices cerámicas complica el reciclaje, pero los líderes de la industria están pilotando sistemas de circuito cerrado para recuperar recortes y partes defectuosas. Safran ha anunciado programas de desarrollo destinados a la reintegración de los desechos de producción en nuevos componentes, con el objetivo de reducir los desechos en vertederos y la demanda de materias primas primarias. Algunos fabricantes también están explorando precursores y aglutinantes bio-derived para reducir la dependencia de químicos basados en fósiles.
El uso de agua y los subproductos peligrosos están siendo evaluados, particularmente en procesos que involucran lodos o tratamientos químicos. Las empresas líderes están invirtiendo en sistemas avanzados de filtración y recuperación de solventes para mitigar los vertidos ambientales.
Mirando hacia los próximos años, se espera que la industria vea una mayor colaboración en torno a estándares de sostenibilidad y metodologías de evaluación del ciclo de vida (LCA) para los CMCs. Organizaciones como la CONFERENCIA EUROPEA DE AERONÁUTICA Y CIENCIAS DEL ESPACIO (EUCASS) están fomentando el diálogo sobre métricas armonizadas y mejores prácticas. A medida que aumentan las presiones regulatorias y los clientes exigen cada vez más credenciales de fabricación verde, los productores de CMC probablemente acelerarán su adopción de tecnologías más limpias y principios de economía circular. Este cambio está destinado a mejorar el perfil de sostenibilidad de los CMCs, fortaleciendo aún más su papel en la habilitación de soluciones de ingeniería de alto rendimiento y bajas emisiones de carbono.
Pronóstico del Mercado 2025–2030: Ingresos, Volumen y Perspectivas de Precios
El sector de fabricación de compuestos de matriz cerámica (CMC) está preparado para un crecimiento robusto de 2025 a 2030, sustentado por la expansión de la demanda en las industrias aeroespacial, de defensa, energía y automotriz. A partir de 2025, las partes interesadas de la industria anticipan un aumento continuo tanto en ingresos como en volúmenes de producción, reflejando un cambio estratégico hacia materiales de alto rendimiento y bajo peso que pueden resistir entornos extremos.
Las aplicaciones aeroespaciales siguen siendo el principal motor de la adopción de CMC, con empresas como General Electric acelerando la integración de CMCs en los motores a reacción de próxima generación. Los motores LEAP de GE y GE9X, por ejemplo, presentan componentes de turbina de CMC, los cuales contribuyen a una mayor eficiencia de combustible y reducción de emisiones. Safran y Rolls-Royce también están avanzando en iniciativas similares, invirtiendo en capacidad de fabricación de CMC e investigación para sistemas de propulsión. Se espera que estos proyectos aumenten significativamente los volúmenes de producción entre 2025 y 2030 a medida que los programas de aviones comerciales y militares aumenten su ritmo.
En el sector energético, Siemens está aprovechando los CMCs para mejorar el rendimiento de las turbinas de gas industriales, buscando aumentar la resistencia térmica y las vidas útiles operativas. Los fabricantes de automóviles también están explorando los CMCs para aplicaciones de alta temperatura como sistemas de frenos, con Brembo liderando el desarrollo de discos de freno de CMC para vehículos de lujo y eléctricos—una tendencia que se espera gane impulso comercial durante este período.
El consenso de la industria prevé que los ingresos globales por la fabricación de CMC experimenten una tasa de crecimiento anual compuesta (CAGR) en los dígitos altos, con un valor total de mercado que podría superar varios miles de millones de USD para 2030. El crecimiento en volumen será respaldado por inversiones en técnicas de fabricación avanzadas, incluyendo la colocación de fibra automatizada e infiltración de vapor químico, tal como lo han adoptado productores como COI Ceramics y Snecma (una compañía de Safran). Se espera que estos avances ayuden a reducir los costos de producción y mejorar la escalabilidad.
A pesar de las aumentos anticipados en volumen, los precios de los CMCs probablemente se mantendrán elevados en comparación con cerámicas tradicionales o aleaciones metálicas, debido a los complejos requisitos de procesamiento y los altos costos de materias primas—particularmente para fibras y matrices de carburo de silicio. Sin embargo, a medida que los procesos de fabricación maduren y se realicen economías de escala, se pueden observar reducciones incrementales en los precios por unidad, mejorando la accesibilidad para aplicaciones industriales más amplias.
En general, las perspectivas para la fabricación de CMC de 2025 a 2030 se caracterizan por una expansión de capacidad, maduración tecnológica y un flujo constante de demanda en mercados finales, señalando un período de crecimiento dinámico y transformación para el sector.
Perspectiva Futura: Aplicaciones de Nueva Generación y Hoja de Ruta Tecnológica
Mirando hacia 2025 y los años siguientes, el sector de fabricación de compuestos de matriz cerámica (CMC) está preparado para avances significativos impulsados por la maduración tecnológica, las inversiones en la cadena de suministro y la creciente adopción de usos finales. Los CMCs, valorados por su excepcional relación resistencia-peso y resistencia a temperaturas, son cada vez más críticos en aplicaciones aeroespaciales, energéticas, de defensa y automotrices.
Aeroespacial sigue siendo el principal impulsor de la fabricación de CMC de próxima generación. Los principales fabricantes de motores están aumentando la integración de CMC en motores a reacción comerciales y militares. Por ejemplo, GE Aerospace ha seguido invirtiendo en capacidad de producción de CMC, con el objetivo de aumentar su uso en componentes de sección caliente para permitir temperaturas de operación más altas de los motores y mejorar la eficiencia del combustible. De manera similar, Safran está acelerando la adopción de CMC en sus motores LEAP, colaborando estrechamente con proveedores para mejorar la escalabilidad y reducir los tiempos de ciclo.
En el frente tecnológico, están surgiendo varias innovaciones de proceso. La colocación automatizada avanzada de fibra, la infiltración química de vapor rápida (CVI) y las técnicas de infiltración de lodo están siendo refinadas para optimizar la producción y reducir costos. SGL Carbon está avanzando en el uso de enfoques de fabricación híbrida, combinando fabricación aditiva con CVI tradicional, para crear geometrías más complejas y reducir desperdicios. El enfoque también se está desplazando hacia la digitalización—integrando monitoreo del proceso en tiempo real y analíticas predictivas para mejorar la calidad y la repetibilidad.
Más allá de la aeroespacial, las aplicaciones energéticas están ganando impulso. Siemens Energy está explorando los CMCs para turbinas de gas de alta eficiencia, donde su estabilidad térmica permite operar a temperaturas y presiones más altas. La industria automotriz está mostrando un renovado interés, con Brembo y otros fabricantes de frenos desarrollando discos de freno basados en CMC para vehículos de rendimiento y eléctricos—enfocándose en longevidad, reducción de peso y alta conductividad térmica.
Los desarrollos en la cadena de suministro también son centrales para la hoja de ruta de CMC. Principales proveedores de materiales, incluidos Hexcel y Toray Industries, están ampliando las capacidades de producción de fibras y preformas para satisfacer la demanda proyectada. Se anticipa que las colaboraciones interindustriales aceleren los ciclos de calificación y estandarización de procesos de fabricación, abriendo aún más nuevos espacios de aplicación.
Para finales de la década de 2020, con continuas inversiones en automatización, control de procesos digitales y I+D de materiales, se espera que la fabricación de CMC logre una mayor escala y competitividad en costo. Esto no solo impulsará una mayor adopción en mercados tradicionales, sino que también desbloqueará nuevos usos en áreas como vehículos hipersónicos, procesamiento industrial y sistemas de energía a hidrógeno.