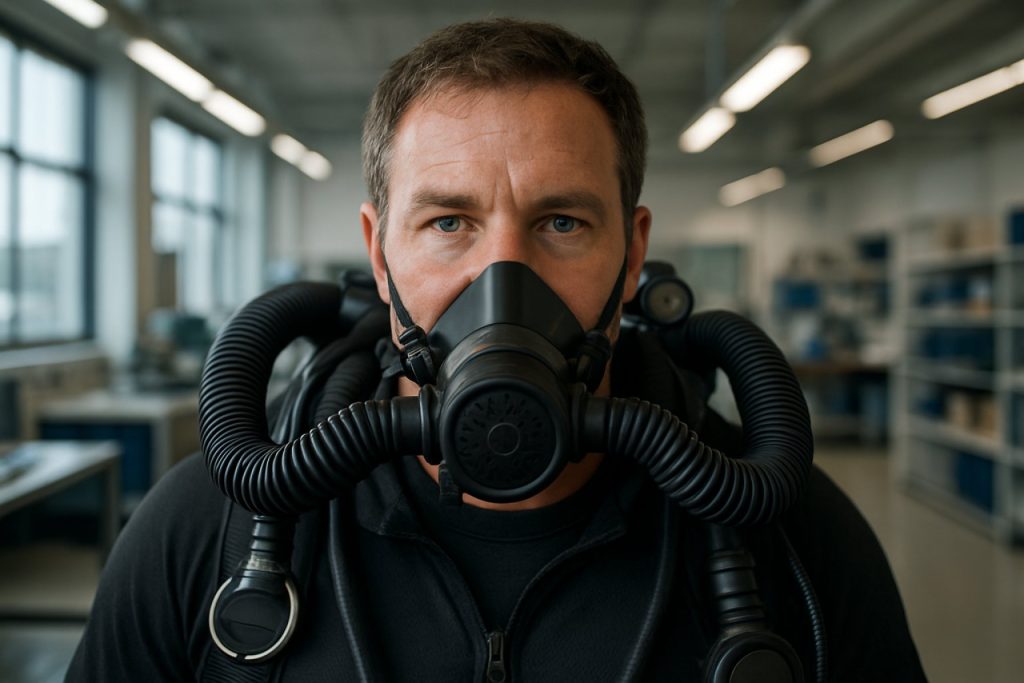
Tabla de Contenidos
- Resumen Ejecutivo: Trayectoria del Mercado 2025–2030
- Tecnologías de Microfabricación Emergententes en Componentes de Rebreather
- Jugadores Clave y Sociedades Estratégicas (e.g., hollis.com, apeksdiving.com)
- Aplicaciones Actuales: Buceo, Defensa y Más
- Innovaciones en Materiales: Nano-Revestimientos, MEMS y Fabricación Aditiva
- Paisaje Regulatorio y Normas Industriales (e.g., ssi.com, padi.com)
- Impulsores del Mercado: Sostenibilidad, Miniaturización y Demandas de Seguridad
- Análisis Competitivo y Paisaje de Patentes
- Pronósticos de Mercado 2025–2030: Ingresos, Volumen y Tendencias Regionales
- Perspectivas Futuras: Tecnología Disruptiva y Oportunidades de Inversión
- Fuentes y Referencias
Resumen Ejecutivo: Trayectoria del Mercado 2025–2030
El período de 2025 a 2030 se prevé que sea testigo de avances significativos en la microfabricación de componentes de rebreathers, impulsados por la innovación continua en la ciencia de materiales, la ingeniería de precisión y la automatización. A medida que los rebreathers se vuelven cada vez más vitales tanto para aplicaciones militares como civiles—desde la exploración en aguas profundas hasta operaciones en entornos peligrosos—la demanda de componentes compactos, fiables y altamente eficientes está acelerándose. Las tecnologías de microfabricación son centrales en esta tendencia, permitiendo la producción de sensores, válvulas y módulos de gestión de gas miniaturizados que son ligeros y robustos.
Fabricantes líderes como JFD y Teledyne Marine están invirtiendo en procesos de microfabricación de última generación, que incluyen fabricación aditiva avanzada y mecanizado láser de precisión. Estos métodos facilitan la integración de materiales novedosos, como cerámicas de alta resistencia y polímeros especializados, optimizando tanto la durabilidad como la densidad funcional de los componentes críticos de los rebreathers. Por ejemplo, los sensores de oxígeno y los transductores de presión basados en sistemas microelectromecánicos (MEMS) están entrando ahora en fases de producción piloto, ofreciendo una mayor fiabilidad y formas en comparación con los diseños anteriores.
Anuncios recientes de Norcros y esfuerzos colaborativos dentro de la Sociedad de Arquitectos Navales e Ingenieros Marinos (SNAME) destacan un enfoque en la microfabricación aditiva y sustractiva para geometrías complejas de componentes. Estas tecnologías permiten la personalización de componentes para perfiles de misión específicos, reduciendo significativamente los tiempos de entrega y habilitando el prototipado rápido. Además, se espera que la integración de herramientas de gemelos digitales y simulación agilice aún más el proceso de microfabricación, reduciendo tasas de error y desperdicio de materiales.
- Eventos: 2025 está marcado por el inicio de consorcios conjuntos entre la industria y el ámbito académico, con el objetivo de estandarizar los protocolos de microfabricación y acelerar la transferencia de tecnología. Los pilotos industriales están aumentando en centros clave de fabricación en Europa y América del Norte.
- Datos: Pruebas de campo iniciales realizadas por JFD y Teledyne Marine sugieren una reducción del 20–30% en el peso de los componentes y hasta un 40% en el tiempo de ensamblaje para módulos de rebreather de próxima generación.
- Perspectivas: Entre 2025 y 2030, se espera que la rápida maduración de la microfabricación permita una mayor miniaturización, una mejor interoperabilidad de los componentes y un uso ampliado de sistemas de monitoreo inteligentes dentro de los rebreathers. La adopción de prácticas de la Industria 4.0 y la robótica en las líneas de producción probablemente harán que la avanzada tecnología de componentes de rebreather sea más accesible y rentable, apoyando una mayor implementación en los sectores de defensa, buceo comercial e investigación científica.
En general, la trayectoria para la microfabricación de componentes de rebreather durante los próximos cinco años está definida por una innovación acelerada, colaboración intersectorial y un marcado movimiento hacia entornos de producción digitalizados y de alta precisión.
Tecnologías de Microfabricación Emergentes en Componentes de Rebreather
Las tecnologías de microfabricación están teniendo un impacto significativo en el diseño y fabricación de componentes avanzados de rebreathers, siendo 2025 un periodo de rápida traducción de la investigación de laboratorio a prototipos comerciales y adopción temprana. Tradicionalmente, los sistemas de rebreathers han confiado en métodos convencionales de mecanizado y ensamblaje para piezas clave como sensores de gas, válvulas y cartuchos de absorción. Sin embargo, la demanda de sistemas más pequeños, ligeros y robustos—impulsada tanto por el mercado militar como por el de buceo recreativo—está acelerando la integración de sistemas microelectromecánicos (MEMS), fabricación aditiva y microfabricación avanzada de polímeros.
Los sensores de oxígeno y dióxido de carbono basados en MEMS están siendo desarrollados y probados para rebreathers de circuito cerrado de próxima generación. Estos sensores, fabricados mediante micromecanizado de silicio y deposición de películas delgadas, prometen mejorar el tiempo de respuesta, la miniaturización y la fiabilidad en comparación con las celdas electroquímicas anteriores. Varias empresas, incluidas Teledyne Technologies y AMETEK, están refinando plataformas de sensores de gas MEMS protegidas con encapsulación robusta y capacidades de autoc calibración. Los prototipos de principios de 2025 han demostrado un funcionamiento estable bajo entornos de alta presión y alta humedad, y se anticipan pruebas de campo para finales de 2025.
La fabricación aditiva, especialmente la sinterización selectiva por láser (SLS) a microescala y la estereolitografía (SLA), se está aprovechando para el prototipado rápido de canales de flujo complejos, micro-válvulas y carcasas miniaturizadas de absorción. Líderes de la industria como Stratasys y 3D Systems han ampliado sus carteras para incluir capacidades de microfabricación de polímeros y metales de alta precisión, que ahora están siendo aprovechadas por los OEM para producir piezas de rebreather a medida y funcionalmente gradientes. La capacidad para iterar rápidamente diseños y fabricar geometrías intrincadas con características de detección incorporadas se espera que reduzca los ciclos de desarrollo y permita ensamblajes de rebreathers más ergonómicos y eficientes hasta 2026 y más allá.
- Los sensores de oxígeno miniaturizados y de bajo consumo con MEMS están acercándose a la aprobación regulatoria para su uso en sistemas de rebreather comerciales, con procesos de verificación en curso tanto en Europa como en América del Norte.
- Las micro-válvulas, fabricadas mediante litografía de alta precisión, están siendo evaluadas por su potencial para proporcionar un control más fino y automatizado de la mezcla y entrega de gas, mejorando la seguridad del buceador.
- Polímeros biocompatibles avanzados, como los suministrados por DSM, están siendo personalizados a microescala para mejorar la resistencia a la corrosión salina y la fouling biológico.
Mirando hacia el futuro, se espera que la convergencia de la microfabricación con el diseño digital y monitoreo en tiempo real dé lugar a sistemas de rebreather más inteligentes y adaptativos. Las alianzas industriales entre desarrolladores de sensores, fabricantes aditivos y OEM de equipos de buceo probablemente acelerarán la comercialización, con los primeros módulos de rebreather completamente microfabricados previstos para aparecer en pruebas de campo para 2026. A medida que las normas regulatorias se adapten para acomodar estas innovaciones, los próximos años serán decisivos para establecer la microfabricación como una piedra angular de la evolución de la tecnología de rebreathers.
Jugadores Clave y Sociedades Estratégicas (e.g., hollis.com, apeksdiving.com)
A medida que la tecnología de rebreathers se vuelve cada vez más sofisticada, la microfabricación de componentes críticos está emergiendo como un punto focal para los líderes de la industria. En 2025 y en los próximos años, un selecto grupo de fabricantes, proveedores de materiales y especialistas en electrónica están impulsando la innovación a través de asociaciones estratégicas y procesos de ingeniería avanzada.
Jugadores clave como Hollis y Apeks Diving han desarrollado capacidades internas y colaboraciones para avanzar en la miniaturización y la fabricación de precisión de componentes como sensores de oxígeno, válvulas solenoides y controladores de flujo de gas. Estas empresas integran cada vez más sistemas microelectromecánicos (MEMS) y polímeros avanzados para mejorar la fiabilidad, la eficiencia energética y el monitoreo en tiempo real dentro de sistemas de rebreather compactos.
Las asociaciones estratégicas entre marcas de buceo establecidas y empresas especializadas en electrónica o materiales están dando forma al panorama competitivo. Hollis, por ejemplo, se ha asociado con proveedores de tecnología de sensores y control para co-desarrollar sensores de oxígeno miniaturizados y transductores de presión que soportan el exigente medio ambiente submarino. Mientras tanto, Apeks Diving colabora con proveedores de elastómeros de alto rendimiento y conjuntos de micro-válvulas, subrayando la importancia de las alianzas intersectoriales para avanzar en la seguridad y eficiencia de los rebreathers.
Más allá de los fabricantes tradicionales de equipos de buceo, proveedores de componentes como TE Connectivity están involucrados activamente en la microfabricación de sensores de presión y gas adaptados para ensamblajes de rebreather. Estos sensores, a menudo fabricados utilizando tecnología MEMS, ofrecen una mayor precisión y un tamaño reducido, lo que permite una mayor miniaturización de la electrónica del circuito respiratorio. Además, Parker Hannifin sigue suministrando avanzadas válvulas solenoides micro y soluciones de sellado adecuadas para los estrictos requisitos de los rebreathers de circuito cerrado.
Mirando hacia el futuro, la industria anticipa una creciente integración de fabricación aditiva y micromecanizado láser de precisión en la producción de componentes de rebreather. A medida que crece la demanda de sistemas compactos, ligeros y duraderos—especialmente para aplicaciones militares, científicas y de buceo técnico—se espera que se intensifiquen las colaboraciones entre fabricantes de equipos originales (OEM) y especialistas establecidos en microfabricación. Estas alianzas buscan empujar los límites de la ciencia de materiales y la fabricación digital, impulsando la evolución de los rebreathers de alto rendimiento hasta 2025 y más allá.
Aplicaciones Actuales: Buceo, Defensa y Más
Las tecnologías de microfabricación se han convertido en centrales para la evolución de los componentes de rebreathers, impulsando avances en buceo, defensa y sectores adyacentes a lo largo de 2025. A medida que las misiones submarinas exigen duraciones más largas, una mayor fiabilidad y sistemas de soporte vital más compactos, la integración de elementos microfabricados—como sensores de gas, válvulas y absorbentes—ha cobrado una importancia crítica. Estos componentes miniaturizados ofrecen una mejor eficiencia y seguridad al reducir el tamaño del dispositivo, optimizando el flujo de gas y mejorando las capacidades de monitoreo en tiempo real.
En 2025, los fabricantes de rebreathers militares y comerciales están aprovechando cada vez más los sistemas microelectromecánicos (MEMS) y el mecanizado láser de precisión para producir sensores de oxígeno ultra compactos y lechos de absorción de dióxido de carbono. Por ejemplo, empresas líderes como JFD y Oceanic están invirtiendo en integración de sensores MEMS, permitiendo un análisis continuo y rápido de la composición del gas dentro de los circuitos respiratorios de los rebreathers. Estos desarrollos responden a los requisitos tanto de las fuerzas especiales navales como de los exploradores de aguas profundas, donde incluso pequeñas mejoras en el tiempo de respuesta de los sensores o en el tamaño pueden mejorar la capacidad de la misión.
Otra área clave es la microfabricación de válvulas y actuadores, lo que ha resultado en mecanismos de adición y ventilación de gas más ligeros y responsive. Empresas como AP Diving están explorando técnicas de fabricación aditiva y micromecanizado para producir geometrías de válvulas personalizadas, adaptadas a flujos específicos y propiedades mecánicas. Estos avances reducen la complejidad mecánica de los rebreathers, contribuyendo a una mayor fiabilidad y un mantenimiento más sencillo, especialmente valioso en aplicaciones de defensa donde se debe minimizar el tiempo de inactividad operativo.
Además, las camas de catalizador microfabricadas para el despojo de CO2 están volviéndose más prevalentes. Los materiales de absorbente granular tradicionales están siendo reemplazados o complementados con arreglos de microcanales estructurados, que ofrecen un área de superficie aumentada y caminos de flujo más predecibles. Con el apoyo de innovadores y proveedores de ciencia de materiales, como 3M, estos absorbentes microingenierizados están siendo probados tanto para buceo como para sistemas respiratorios aeroespaciales.
Mirando hacia el futuro, se espera que la continuada convergencia de la microfabricación, la integración de sensores y los materiales avanzados produzcan sistemas de rebreather aún más compactos, inteligentes y eficientes en energía para finales de la década de 2020. Esta trayectoria probablemente verá la tecnología de rebreather expandirse más allá del buceo y la defensa tradicionales hacia la seguridad industrial, la lucha contra incendios y la exploración espacial—sectores que requieren soluciones de soporte vital robustas y miniaturizadas.
Innovaciones en Materiales: Nano-Revestimientos, MEMS y Fabricación Aditiva
En 2025, la microfabricación de componentes de rebreather está experimentando una rápida evolución, impulsada por avances en la ciencia de materiales y la fabricación de precisión. Tres tendencias tecnológicas primarias—nano-revestimientos, sistemas microelectromecánicos (MEMS) y fabricación aditiva—se están convergiendo para permitir rebreathers de circuito cerrado más seguros, eficientes y duraderos para aplicaciones de buceo e industriales.
Los nano-revestimientos han visto un aumento en su adopción para proteger los componentes sensibles de los rebreathers de la corrosión, la fouling biológica y la degradación química. Estas películas ultradelgadas, a menudo aplicadas mediante deposición de capas atómicas o deposición de vapor químico, mejoran la longevidad y la fiabilidad de sensores de oxígeno, carcasas de absorción y caminos de flujo. Líderes de la industria como Evonik Industries AG están suministrando materiales de polímero avanzados y tecnologías de superficie que permiten la creación de recubrimientos robustos, hidrofóbicos y antimicrobianos específicamente adaptados para entornos submarinos y difíciles. Esto es particularmente relevante para los cartuchos de absorción de CO2, donde los nano-revestimientos pueden reducir significativamente las pérdidas de rendimiento debido a la entrada de humedad.
Simultáneamente, la integración de MEMS está revolucionando la miniaturización y el rendimiento de los sensores. Los sensores de oxígeno y dióxido de carbono basados en MEMS, que incorporan electrodos y canales a microescala, ofrecen tiempos de respuesta más rápidos, menor consumo de energía y mayor durabilidad en comparación con los homólogos tradicionales a macroescala. Empresas como ams OSRAM y Sensirion AG están desarrollando sensores de gas MEMS compactos con una robusta encapsulación y capacidades de autoc calibración. Se espera que la implementación de estos sensores dentro de los rebreathers mejore el monitoreo de gas en tiempo real y el diagnóstico del sistema, contribuyendo a la seguridad general del buceador.
La fabricación aditiva (AM), particularmente la sinterización selectiva por láser (SLS) y la impresión 3D multi-material, está ganando terreno para el prototipado rápido y la producción de geometrías complejas de rebreathers que de otro modo serían difíciles de fabricar. Esto permite a los fabricantes optimizar los caminos de flujo, integrar deflectores y reducir el número de componentes, todo mientras utilizan polímeros avanzados y aleaciones metálicas. Por ejemplo, Stratasys Ltd. y 3D Systems Corporation están colaborando con fabricantes de equipos de defensa y buceo para producir carcasas y boquillas de rebreathers personalizadas y ligeras, aprovechando la libertad de diseño y el potencial iterativo de AM.
Mirando hacia adelante, los próximos años están destinados a ver una mayor convergencia de estas tecnologías, permitiendo la integración de superficies nano-ingenierizadas, sensores MEMS incrustados y arquitecturas fabricadas por adición en una nueva generación de rebreathers inteligentes y autodiagnósticos. La continua miniaturización y las mejoras en el rendimiento se espera que mejoren la resistencia a las misiones y la seguridad operativa, expandiendo el uso de rebreathers tanto en sectores profesionales como recreativos.
Paisaje Regulatorio y Normas Industriales (e.g., ssi.com, padi.com)
El paisaje regulatorio para la microfabricación de componentes de rebreather está evolucionando rápidamente, reflejando el cambio de la industria hacia técnicas de fabricación avanzadas y la crítica importancia de la seguridad en los sistemas de soporte vital. A partir de 2025, la integración de componentes microfabricados—como sensores de oxígeno de precisión, cartuchos de absorción miniaturizados y microválvulas personalizadas—ha llevado tanto a la industria como a los organismos reguladores a reevaluar los estándares existentes y los procedimientos de supervisión.
Los principales organismos de certificación de buceo, como Scuba Schools International (SSI) y Professional Association of Diving Instructors (PADI), han proporcionado históricamente directrices para el uso de rebreathers, centrándose principalmente en la seguridad operativa, la formación del buceador y el mantenimiento del equipo. Sin embargo, la aparición de la microfabricación en la fabricación de componentes de rebreather está llevando ahora a estas organizaciones a consultar con los fabricantes y organismos de estándares para abordar nuevos riesgos y variables de rendimiento asociadas con piezas miniaturizadas.
Los fabricantes que adoptan procesos de microfabricación para elementos críticos de rebreather están cada vez más haciendo referencia a estándares internacionales tanto para la seguridad del producto como para la validación del proceso. La serie ISO 24801 e ISO 10218, que se refiere a la formación de buceadores y la seguridad de las máquinas, se cita con frecuencia, pero ahora se complementa con directrices específicas para sistemas microelectromecánicos (MEMS) y la fabricación de dispositivos médicos de precisión. Este cambio es evidente en las prácticas de empresas como Ambient Pressure Diving y PADI TecRec, que están comprometidas en esfuerzos colaborativos para garantizar que las piezas microfabricadas cumplan con los criterios emergentes de durabilidad, precisión y compatibilidad con los ensamblajes de rebreather tradicionales.
En 2025, la supervisión regulatoria es más pronunciada en la certificación y prueba de micro-sensores y elementos de absorción, donde la falla de un componente podría comprometer directamente la seguridad del buceador. Hay una creciente tendencia hacia la prueba y certificación de tercera parte, con agencias que exigen a los fabricantes documentación sobre las condiciones de fabricación en salas limpias, rastreabilidad de materias primas y pruebas de lotes rigurosas para las piezas microfabricadas. Esto es apoyado por asociaciones técnicas entre fabricantes y organizaciones como Divex, que están trabajando para alinear la garantía de calidad interna con los estándares internacionales en evolución.
Mirando hacia el futuro, se espera que los próximos años traigan una mayor armonización entre los estándares de microfabricación industrial y las regulaciones de equipos de buceo. Los grupos de la industria anticipan nuevas especificaciones técnicas ISO adaptadas a componentes de soporte vital microfabricados. Organizaciones de formación como SSI y PADI se están preparando para actualizar sus estándares y materiales de capacitación para reflejar los desafíos únicos de mantenimiento e inspección que plantean los componentes de rebreather miniaturizados, asegurando que la seguridad del buceador siga siendo primordial a medida que avanza la tecnología.
Impulsores del Mercado: Sostenibilidad, Miniaturización y Demandas de Seguridad
La microfabricación de componentes de rebreather se ha convertido en un punto focal en las industrias de soporte vital y aparatos de buceo, particularmente a medida que los impulsores del mercado como la sostenibilidad, la miniaturización y las crecientes demandas de seguridad convergen en 2025 y los próximos años. Las presiones regulatorias y las expectativas del usuario final están estimulando una rápida innovación en cómo se diseñan y fabrican los componentes—como sensores de gas, válvulas y cartuchos de absorción.
La sostenibilidad es un impulsor prominente, con los fabricantes buscando reducir la huella ambiental tanto de los procesos de producción como del ciclo operativo de los rebreathers. La microfabricación permite el uso de materiales avanzados, como polímeros biocompatibles y compuestos reciclables, y facilita la ingeniería de precisión que minimiza desechos. Empresas como Teledyne Technologies Incorporated y Honeywell International Inc. están desarrollando sensores de gas a microescala y módulos electrónicos que son no solo más energéticamente eficientes, sino también diseñados para intervalos de servicio prolongados y un reciclaje más fácil al final de su vida útil. Esto se alinea con los objetivos más amplios de sostenibilidad de la industria y regulaciones de materiales cada vez más estrictas.
La miniaturización sigue siendo una tendencia crítica, impulsada tanto por aplicaciones profesionales como recreativas donde se demandan sistemas portátiles y compactos. Las técnicas de microfabricación como MEMS (Sistemas Microelectromecánicos) y la fabricación aditiva avanzada permiten la integración de funcionalidades complejas en huellas más pequeñas. Smiths Group plc ha informado sobre inversiones continuas en válvulas de control microfluídicas y arreglos de sensores compactos adaptados para ensamblajes de rebreather, con el objetivo de mejorar tanto la portabilidad como la fiabilidad. Estos avances permiten a los fabricantes ofrecer unidades de rebreather más ligeras y menos intrusivas que no comprometen el rendimiento, un diferenciador clave en mercados competitivos.
Las consideraciones de seguridad también están acelerando la adopción de componentes microfabricados. El monitoreo en tiempo real mejorado de la composición del gas y el diagnóstico del sistema—posible a través de sensores altamente sensibles a microescala—mejora tanto la confianza del usuario como el cumplimiento con los estándares de seguridad en evolución. Empresas como Drägerwerk AG & Co. KGaA están a la vanguardia, integrando sensores de gas microfabricados y sistemas de control a prueba de fallos en sus últimos modelos de rebreather para abordar tanto los requisitos del sector civil como de defensa.
Mirando hacia el futuro, se espera que en los próximos años se produzca una adopción más amplia de procesos automatizados y de alto rendimiento de microfabricación, reduciendo los costos por unidad y mejorando aún más los métricas de sostenibilidad. La continua convergencia de sostenibilidad, miniaturización y demandas de seguridad probablemente impulsará esfuerzos colaborativos entre fabricantes establecidos y empresas especializadas en microfabricación, creando nuevos estándares para la calidad y el rendimiento de los componentes de rebreather.
Análisis Competitivo y Paisaje de Patentes
El paisaje para la microfabricación de componentes de rebreather está evolucionando rápidamente a medida que los fabricantes y proveedores de tecnología responden a la creciente demanda de aparatos de respiración compactos, eficientes y fiables tanto para aplicaciones profesionales como recreativas. A partir de 2025, el entorno competitivo está definido por un puñado de jugadores establecidos, nuevas startups y una actividad significativa de propiedad intelectual (IP), particularmente en la miniaturización de sensores, válvulas y sistemas de gestión de gas.
Los líderes clave de la industria, como JFD Global y Ambient Pressure Diving, están invirtiendo activamente en técnicas de microfabricación para mejorar el rendimiento y las características de seguridad de sus líneas de productos de rebreather. Estas empresas están aprovechando los avances en sistemas microelectromecánicos (MEMS) para reducir las huellas de los componentes mientras mejoran la durabilidad y la integración con sistemas de monitoreo digital. Por ejemplo, los sensores de oxígeno basados en MEMS y las válvulas solenoides compactas están volviéndose cada vez más prevalentes, impulsados por la necesidad de mejor fiabilidad y menor consumo de energía.
Las startups y proveedores especializados, como Norcotek, están avanzando al desarrollar sensores y controladores de flujo microfabricados patentados adaptados para los exigentes entornos de los rebreathers submarinos. Estas innovaciones no solo se están incorporando en nuevos diseños de productos, sino que también se están licenciando a OEM establecidos, intensificando la competencia y fomentando un dinámico paisaje de IP.
Las solicitudes de patentes en los últimos dos años reflejan estas tendencias, con un aumento notable en las aplicaciones relacionadas con sensores de gas miniaturizados, ensamblajes de micro-válvulas y tecnologías de sellado avanzadas. Las bases de datos de patentes muestran un número creciente de solicitudes tanto de fabricantes existentes como de nuevos entrantes, indicando una carrera por asegurar tecnologías fundamentales. Por ejemplo, Teledyne Technologies y Honeywell han ampliado sus carteras de patentes en las áreas de detección de gas basada en MEMS y control microfluídico pertinente a los ensamblajes de rebreather, sugiriendo un potencial de transferencia de tecnología entre industrias.
Mirando hacia adelante, el sector está preparado para una mayor consolidación a medida que entidades más grandes busquen adquirir startups prometedoras para asegurar el acceso a novedosos procesos de microfabricación y IP única. Al mismo tiempo, se espera que las colaboraciones entre fabricantes de componentes y ensambladores de sistemas aceleren la traducción de innovaciones a escala de laboratorio a productos comerciales. Los estándares regulatorios y las especificaciones militares también están influyendo en las prioridades de diseño, presionando para una mayor robustez y seguimiento del ciclo de vida a nivel de componente.
En general, el paisaje competitivo y de patentes para la microfabricación de componentes de rebreather en 2025 está marcado por estrategias de IP agresivas, asociaciones intersectoriales y un fuerte enfoque en la miniaturización, señalando un período de innovación sostenida y diferenciación de mercado a través de tecnología propietaria.
Pronósticos de Mercado 2025–2030: Ingresos, Volumen y Tendencias Regionales
Se anticipa que el período de 2025 a 2030 sea testigo de avances significativos y expansión del mercado en la microfabricación de componentes de rebreather. La microfabricación, que permite la producción de componentes altamente miniaturizados y precisos, es cada vez más crítica para mejorar el rendimiento, la seguridad y la facilidad de uso de los sistemas de rebreather tanto en aplicaciones de buceo militar como comercial.
Los líderes de la industria están invirtiendo fuertemente en sistemas microelectromecánicos (MEMS) y procesos avanzados de fabricación aditiva para producir sensores, válvulas y módulos electrónicos integrados a microescala. Empresas como Parker Hannifin y Honeywell están ampliando sus capacidades de microfabricación, suministrando componentes críticos de sensor y control que respaldan la seguridad y eficiencia de los rebreathers de circuito cerrado.
Los pronósticos de ingresos para el sector de microfabricación de componentes de rebreather son optimistas, impulsados por una creciente adopción de rebreathers de circuito cerrado (CCR) en los mercados militares, profesionales y recreativos. Para 2030, se proyecta que los ingresos globales anuales para componentes de rebreather microfabricados superen los 300 millones de dólares, marcando un crecimiento anual compuesto (CAGR) del 8–10% desde los niveles de 2025. Se espera que la producción aumente correspondientemente, con la producción de sensores y micro-válvulas basados en MEMS aumentando en más del 30% para satisfacer la creciente demanda, particularmente de programas de adquisición de defensa y operadores de buceo comercial.
Regionalmente, se prevé que América del Norte y Europa mantengan el liderazgo del mercado, respaldadas por OEM establecidos, una robusta infraestructura de I+D y un gasto significativo en defensa. Estados Unidos, en particular, probablemente verá inversiones sostenidas tanto del Departamento de Defensa como de contratistas principales como Lockheed Martin y Northrop Grumman, que están integrando sensores y elementos de control microfabricados avanzados en los rebreathers de combate de próxima generación. En Europa, empresas como Divex (parte de JFD Global) también están acelerando la adopción de electrónica microfabricada y módulos de control de gas.
Se espera que Asia-Pacífico registre el crecimiento más rápido, impulsado por un aumento de la actividad marítima y programas de modernización naval en expansión en países como China, Corea del Sur y Australia. Los fabricantes regionales están comenzando a invertir en capacidades de microfabricación doméstica, buscando reducir la dependencia de importaciones y desarrollar tecnologías de rebreather autóctonas.
Mirando hacia el futuro, la continua miniaturización e integración funcional de los componentes de rebreather a través de la microfabricación seguirá siendo central para la innovación de productos. La integración de detección de gas en tiempo real, telemetría inalámbrica y control de flujo automatizado a microescala se anticipa para establecer nuevos estándares de rendimiento y seguridad, reforzando la trayectoria ascendente de este segmento de mercado hasta 2030.
Perspectivas Futuras: Tecnología Disruptiva y Oportunidades de Inversión
El paisaje de la microfabricación de componentes de rebreather está preparado para una transformación significativa a través de 2025 y los próximos años, impulsada por avances en ciencia de materiales, fabricación aditiva y técnicas de miniaturización. A medida que la exploración submarina, la defensa y las operaciones de rescate exigen sistemas de soporte vital cada vez más fiables y compactos, la integración estratégica de tecnologías de microfabricación disruptivas ofrece tanto mejoras en el rendimiento como nuevas avenidas de inversión.
Los actores clave en el mercado de rebreathers, como James Fisher and Sons plc (a través de su subsidiaria Divex) y Teledyne Marine, están aprovechando cada vez más la fabricación a microescala para desarrollar absorción de CO2 más ligeras y eficientes, sensores de oxígeno avanzados y reguladores de flujo de alta precisión. Estos componentes se benefician de procesos microelectromecánicos (MEMS), lo que permite la integración de sensores y micro-válvulas directamente en plataformas a escala de chip, reduciendo la complejidad del ensamblaje y los puntos de fallo.
A partir de 2025, la adopción industrial de microreactores cerámicos y materiales microporosos está acelerando, inspirada por desarrollos en los sectores médico y aeroespacial más amplios. Empresas como Oxis Energy (notada por su experiencia en tecnología de baterías de litio-azufre y materiales avanzados) están explorando sinergias en microfabricación tanto para el almacenamiento de energía como para la gestión de gas dentro de aparatos de respiración de circuito cerrado. La convergencia de la impresión 3D con microfluidos está permitiendo el prototipado rápido de componentes de rebreather de diseño personalizado, adaptados a perfiles de misión específicos o datos fisiológicos del usuario.
En el frente de inversión, se espera que las asociaciones estratégicas entre contratistas de defensa, fabricantes de rebreathers establecidos y empresas de ingeniería de precisión se intensifiquen. El enfoque está en aumentar la producción de sensores de oxígeno basados en MEMS e integrar diagnósticos inteligentes dentro de módulos de control compactos. Honeywell International Inc. continúa invirtiendo en miniaturización de sensores y robustas tecnologías de monitoreo ambiental, con potenciales aplicaciones posteriores en sistemas de rebreather de próxima generación.
Mirando hacia adelante, la maduración del empaquetado a nivel de oblea, recubrimientos biocompatibles y catalizadores nanoestructurados está preparada para interrumpir aún más los enfoques tradicionales al diseño de componentes de rebreather. Los analistas de la industria anticipan que a finales de la década de 2020, las piezas microfabricadas se convertirán en estándar en equipos profesionales y recreativos de buceo, proporcionando una seguridad mejorada, una mayor resistencia a las misiones y capacidades de mantenimiento predictivo. Esta evolución abre nuevas oportunidades de inversión para las partes interesadas en materiales, automatización de fabricación y ecosistemas de soporte vital habilitados para IoT, consolidando la microfabricación como una piedra angular de la innovación futura en rebreathers.
Fuentes y Referencias
- Teledyne Marine
- Norcros
- Sociedad de Arquitectos Navales e Ingenieros Marinos
- Teledyne Technologies
- AMETEK
- Stratasys
- 3D Systems
- DSM
- AP Diving
- Evonik Industries AG
- ams OSRAM
- Sensirion AG
- Professional Association of Diving Instructors (PADI)
- Ambient Pressure Diving
- Honeywell International Inc.
- Smiths Group plc
- Norcotek
- Lockheed Martin
- Northrop Grumman
- JFD Global