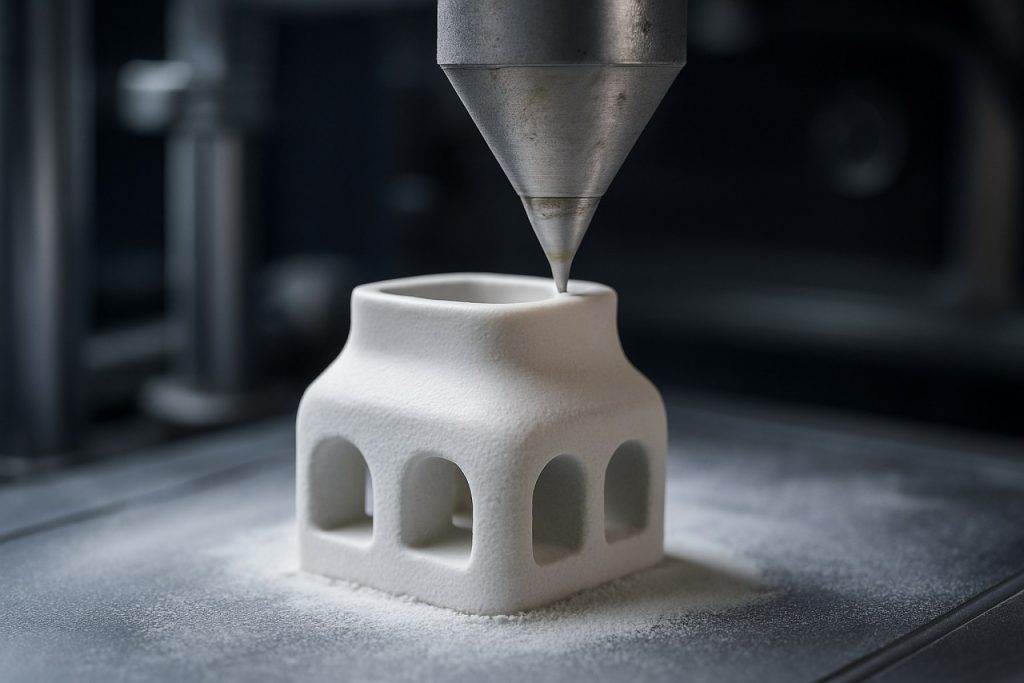
Fabrication Additive de Céramique de Zircone en 2025 : Transformer la Fabrication Avancée avec une Croissance à Deux Chiffres. Découvrez Comment les Avancées dans les Matériaux et l’Impression 3D Façonnent l’Avenir des Céramiques Haute Performance.
- Résumé Exécutif : Tendances Clés et Facteurs de Marché en 2025
- Taille du Marché, Taux de Croissance et Prévisions (2025–2030)
- Innovations Technologiques dans l’Impression 3D de Céramique de Zircone
- Acteurs Principaux et Partenariats Stratégiques
- Applications Émergentes : Médical, Aérospatial et Électronique
- Considérations sur la Chaîne d’Approvisionnement et les Matières Premières
- Environnement Réglementaire et Normes de l’Industrie
- Analyse Concurrentielle : Forces, Faiblesses et Différenciateurs
- Durabilité et Impact Environnemental
- Perspectives Futures : Opportunités, Défis et Recommandations Stratégiques
- Sources & Références
Résumé Exécutif : Tendances Clés et Facteurs de Marché en 2025
La fabrication additive de céramique de zirconie (AM) est prête pour une croissance significative en 2025, propulsée par les avancées en science des matériaux, l’optimisation des processus et l’adoption industrielle croissante. La zirconie, connue pour sa résistance mécanique exceptionnelle, sa ténacité à la rupture et sa biocompatibilité, est de plus en plus recherchée dans des secteurs tels que la dentisterie, la médecine, l’aérospatial et l’électronique. La convergence de ces propriétés avec la liberté de conception de l’AM permet la production de composants complexes et haute performance qui étaient auparavant inaccessibles par les méthodes de fabrication traditionnelles.
Les tendances clés en 2025 incluent la maturation des techniques AM basées sur la poudre— telles que le frittage laser sélectif (SLS), la stéréolithographie (SLA), et le traitement par lumière numérique (DLP)— spécifiquement adaptées pour les céramiques de zirconie. Des fabricants d’équipements de premier plan comme 3D Systems et Stratasys élargissent leurs portefeuilles pour inclure des plateformes compatibles avec céramiques, tandis que des entreprises spécialisées comme Lithoz GmbH et XJet repoussent les limites avec des technologies propriétaires pour des pièces en zirconie à haute densité et haute précision. Lithoz GmbH, par exemple, a signalé des augmentations significatives de la production et de la qualité des pièces avec ses systèmes LCM (Fabrication Céramique par Lithographie), qui sont maintenant adoptés par des laboratoires dentaires et des fabricants d’appareils médicaux dans le monde entier.
Les fournisseurs de matières jouent également un rôle pivot. Des entreprises comme Tosoh Corporation et 3DCeram investissent dans le développement de poudres de zirconie avancées et de pâtes imprimables, optimisées pour les processus AM. Ces matériaux offrent une meilleure frittabilité, une porosité réduite et des propriétés mécaniques améliorées, répondant aux limitations précédentes de l’AM céramique. La disponibilité de matières premières en zirconie de qualité médicale et de haute pureté accélère les approbations réglementaires et l’adoption dans des applications critiques, en particulier dans les prothèses dentaires et les implants orthopédiques.
Les facteurs de marché en 2025 incluent la demande croissante de dispositifs médicaux spécifiques aux patients, de composants aérospatiaux légers et résistants à l’usure, et de pièces électroniques miniaturisées. La capacité de prototyper rapidement et de produire des géométries personnalisées avec un minimum de déchets matériels attire les fabricants cherchant à rationaliser les chaînes d’approvisionnement et à réduire les délais de livraison. De plus, les considérations de durabilité incitent à une transition vers des processus additifs, car ils offrent une consommation d’énergie plus faible et un déchet réduit par rapport aux méthodes soustractives.
En regardant vers l’avenir, les perspectives pour l’AM de céramique de zirconie sont robustes. Les collaborations industrielles, la R&D continue et l’entrée de nouveaux acteurs devraient encore réduire les coûts et élargir l’éventail des formulations de zirconie imprimables. À mesure que la fiabilité des procédés et la certification des pièces s’améliorent, l’AM de zirconie est appelé à devenir une solution courante pour des applications critiques de grande valeur à travers plusieurs industries.
Taille du Marché, Taux de Croissance et Prévisions (2025–2030)
Le marché mondial de la fabrication additive de céramique de zirconie (AM) est prêt pour une croissance robuste de 2025 à 2030, soutenue par l’adoption croissante dans des secteurs à haute valeur tels que la dentisterie, la médecine, l’électronique et l’ingénierie avancée. La zirconie, connue pour sa résistance mécanique exceptionnelle, sa biocompatibilité et sa résistance à l’usure et à la corrosion, devient un matériau de choix pour des applications où les céramiques traditionnelles ou les métaux ne conviennent pas. Le marché est actuellement caractérisé par une combinaison d’acteurs établis et de start-ups innovantes, chacune contribuant à l’évolution rapide tant des matériaux que du matériel AM.
En 2025, le marché de l’AM de céramique de zirconie devrait être évalué à plusieurs centaines de millions de dollars, avec un taux de croissance annuel composé (CAGR) prévu dans les deux chiffres jusqu’en 2030. Cette expansion est soutenue par la disponibilité croissante de poudres et de suspensions de zirconie de qualité industrielle optimisées pour les processus additifs tels que la stéréolithographie (SLA), le traitement par lumière numérique (DLP), et le jet de liant. Des entreprises comme 3D Systems et Stratasys développent et commercialisent activement des solutions AM céramiques, tandis que des entreprises spécialisées comme Lithoz GmbH et CeramTec se concentrent sur des matériaux céramiques de haute performance et des plateformes AM dédiées.
Le secteur dentaire reste le plus grand utilisateur final de l’AM de zirconie, avec des couronnes dentaires, des bridges et des implants produits par fabrication additive offrant un ajustement supérieur et des délais de production réduits par rapport aux méthodes conventionnelles. Lithoz GmbH a signalé une croissance significative de la demande pour sa technologie LCM (Fabrication Céramique par Lithographie), qui permet la production de pièces en zirconie denses et de haute précision adaptées aux applications médicales et dentaires. Pendant ce temps, CeramTec élargit son portefeuille de composants céramiques avancés à des fins médicales et industrielles, tirant parti de la fabrication additive pour adresser des géométries complexes et une personnalisation.
En regardant vers l’avenir, les perspectives du marché sont encourageantes grâce aux investissements continus en R&D et à l’entrée de nouveaux acteurs, notamment en Asie et en Amérique du Nord. Les prochaines années devraient voir de nouvelles améliorations dans la fiabilité des processus, l’évolutivité des tailles de pièces et l’automatisation des post-traitements, ce qui aidera à réduire les coûts et à élargir l’adoption. De plus, des collaborations entre fabricants de matériel AM et fournisseurs de matériaux céramiques devraient accélérer le développement de solutions clés en main adaptées au zirconie. À mesure que les voies réglementaires pour les dispositifs médicaux et dentaires deviennent plus claires, et que les utilisateurs industriels recherchent des alternatives légères et haute performance aux métaux, la fabrication additive de céramique de zirconie devrait devenir une technologie de production courante d’ici 2030.
Innovations Technologiques dans l’Impression 3D de Céramique de Zircone
La fabrication additive de céramique de zirconie (AM) connaît des avancées technologiques rapides à mesure que le secteur avance vers 2025, stimulée par la demande pour des céramiques haute performance dans des applications médicales, dentaires et industrielles. La résistance mécanique exceptionnelle, la ténacité à la rupture et la biocompatibilité de la zirconie en font un matériau privilégié pour l’impression 3D de composants complexes et de grande valeur.
L’une des innovations les plus significatives est le perfectionnement des processus de photopolymérisation par cuve et de jet de liant adaptés à la zirconie. Des entreprises comme Lithoz GmbH ont été à l’avant-garde avec leur technologie LCM (Fabrication Céramique par Lithographie), permettant la production de pièces en zirconie denses et de haute précision avec des géométries complexes. Leurs systèmes sont largement adoptés dans la fabrication de dispositifs dentaires et médicaux, où précision et propriétés matérielles sont critiques. De même, 3DCeram a fait progresser la stéréolithographie (SLA) pour les céramiques techniques, offrant des solutions clés en main pour la production de pièces en zirconie à l’échelle industrielle.
Le développement de matériaux est un autre domaine d’attention. L’introduction de résines pré-céramiques et de suspensions de zirconie optimisées a amélioré l’imprimabilité et les résultats du post-traitement. CeramTec, un leader mondial dans le domaine des céramiques avancées, développe activement de nouvelles formulations de zirconie pour la fabrication additive, ciblant une densité accrue et des performances mécaniques améliorées après frittage. Ces innovations devraient réduire l’écart entre les composants en zirconie fabriqués de manière conventionnelle et ceux fabriqués de manière additive.
Des approches de fabrication hybride émergent également, combinant des techniques additives et soustractives pour obtenir des finitions de surface supérieures et des tolérances dimensionnelles. XJet a commercialisé sa technologie NanoParticle Jetting™, qui permet la production de pièces en zirconie très détaillées avec un minimum de post-traitement. Cette technologie gagne en popularité dans le secteur dentaire, où les implants et restaurations spécifiques au patient nécessitent à la fois précision et biocompatibilité.
En regardant vers l’avenir, les perspectives pour l’AM de céramique de zirconie sont robustes. La miniaturisation continue des dispositifs médicaux, la montée des soins de santé personnalisés et le besoin de composants industriels légers et durables devraient stimuler davantage l’adoption. Les leaders de l’industrie investissent dans l’automatisation, le contrôle qualité en ligne, et les systèmes de production évolutifs pour répondre à la demande croissante. Alors que plus d’entreprises, comme 3DCeram et Lithoz GmbH, étendent leur portée mondiale et leurs portefeuilles d’applications, l’impression 3D de céramique de zirconie est sur le point de devenir une technologie de fabrication courante dans les années à venir.
Acteurs Principaux et Partenariats Stratégiques
Le secteur de la fabrication additive de céramique de zirconie (AM) en 2025 est caractérisé par une interaction dynamique entre les fabricants de céramiques établis, les fournisseurs innovants de technologies AM, et des collaborations stratégiques visant à augmenter la production et élargir les domaines d’application. Plusieurs acteurs majeurs façonnent le paysage concurrentiel, tirant parti de technologies propriétaires et forgeant des partenariats pour accélérer l’adoption de l’impression 3D à base de zirconie.
Parmi les entreprises les plus en vue, 3D Systems se distingue par son investissement dans l’AM céramique, y compris la zirconie, via sa plateforme Figure 4 et le développement continu des matériaux. L’entreprise collabore avec des partenaires industriels pour optimiser les flux de travail pour les applications dentaires, médicales et industrielles, reflétant une tendance plus large visant des secteurs de haute valeur et exigeants en précision.
Un autre acteur clé est Lithoz GmbH, un spécialiste autrichien de l’impression 3D céramique. La technologie LCM de Lithoz (Fabrication Céramique par Lithographie) est largement reconnue pour sa capacité à produire des pièces en zirconie denses et haute résistance. L’entreprise a établi des partenariats avec des producteurs de céramiques de premier plan et des institutions de recherche pour élargir l’utilisation de la zirconie dans les applications dentaires, biomédicales et d’ingénierie. Le réseau mondial de clients et de collaborateurs de Lithoz en fait un hub central dans l’écosystème de l’AM de zirconie.
En Asie, Tosoh Corporation est un fournisseur majeur de poudres de zirconie et a activement soutenu le développement de matériaux de zirconie imprimables pour les processus AM. Les collaborations de Tosoh avec les fabricants d’imprimantes et les utilisateurs finaux visent à garantir la cohérence et la performance des matériaux, ce qui est essentiel pour augmenter la production dans des industries réglementées comme la santé.
Les partenariats stratégiques deviennent de plus en plus courants à mesure que les entreprises cherchent à combiner leur expertise en science des matériaux, en matériel d’imprimante et en ingénierie d’application. Par exemple, CeramTec, un leader mondial dans le domaine des céramiques avancées, a engagé des projets de développement commun avec des fournisseurs de technologies AM pour accélérer la qualification des composants en zirconie pour un usage médical et industriel. De même, XJet fait progresser sa technologie NanoParticle Jetting pour les céramiques, y compris la zirconie, et a annoncé des collaborations avec des partenaires dentaires et industriels pour valider de nouvelles applications.
En regardant vers l’avenir, les prochaines années devraient voir une nouvelle consolidation et des alliances intersectorielles, alors que les entreprises cherchent à relever les défis liés à l’évolutivité, aux coûts et à la conformité réglementaire. La convergence des fournisseurs de matériaux, des innovateurs en matériel AM et des industries utilisatrices devrait stimuler la maturité de la fabrication additive de céramique de zirconie, les acteurs majeurs continuant d’investir dans la R&D et les partenariats stratégiques pour maintenir leur avantage concurrentiel.
Applications Émergentes : Médical, Aérospatial et Électronique
La fabrication additive de céramique de zirconie (AM) progresse rapidement, 2025 étant une année charnière pour son adoption dans des secteurs de haute valeur tels que le médical, l’aérospatial et l’électronique. Les propriétés uniques de la zirconie—résistance exceptionnelle, ténacité à la rupture et biocompatibilité—prouvent leur intégration dans des applications où les méthodes de fabrication traditionnelles rencontrent des limitations.
Dans le domaine médical, l’AM de zirconie transforme la production d’implants dentaires, de prothèses et d’outils chirurgicaux. La capacité à fabriquer des géométries spécifiques aux patients avec une grande précision est particulièrement précieuse. Des entreprises comme 3D Systems et CeramTec développent activement et fournissent des solutions AM à base de zirconie pour des applications dentaires et orthopédiques. Ces solutions permettent la création d’implants complexes et personnalisés offrant une meilleure intégration osseuse et longévité par rapport aux alternatives métalliques. Cette tendance devrait s’accélérer à mesure que les voies réglementaires pour les céramiques médicales imprimées en 3D deviennent plus établies dans les prochaines années.
L’aérospatial est un autre secteur voyant une adoption croissante de l’AM de zirconie. La stabilité à haute température et la résistance au choc thermique du matériau le rendent idéal pour des composants comme les pales de turbine, les revêtements de protection thermique et les emballages de capteurs. Oxford Instruments et XJet font partie des fournisseurs de technologies permettant aux fabricants aérospatiaux de prototyper et de produire des pièces en zirconie complexes qui étaient auparavant irréalisables. Les prochaines années devraient voir une intégration accrue de l’AM de zirconie dans les systèmes de propulsion et les composants de véhicules hypersoniques, alors que l’industrie recherche des matériaux plus légers et plus durables pour améliorer l’efficacité énergétique et les performances.
Dans l’électronique, la tendance à la miniaturisation et la demande pour des substrats haute performance stimulent l’intérêt pour l’AM de zirconie. Son isolation électrique, sa conductivité thermique et son inertie chimique en font un candidat approprié pour des substrats, des isolants et des composants de capteurs. Tosoh Corporation, un fournisseur majeur de poudres de zirconie, collabore avec des fabricants de systèmes AM pour optimiser les matières premières pour des applications électroniques. Les années à venir devraient apporter des avancées dans l’impression multi-matériaux et l’intégration de la zirconie avec des encres conductrices, permettant la fabrication de dispositifs électroniques complexes et multifonctionnels.
En regardant vers l’avenir, les perspectives pour la fabrication additive de céramique de zirconie sont solides. À mesure que les formulations de matériaux, les technologies d’impression et les méthodes de post-traitement maturent, l’éventail des applications en médecine, aérospatial et électronique s’élargira. Les leaders de l’industrie investissent dans l’augmentation de la production et la qualification des pièces en zirconie AM pour des usages critiques, signalant un passage de la phase de prototypage à la fabrication à grande échelle d’ici la fin des années 2020.
Considérations sur la Chaîne d’Approvisionnement et les Matières Premières
La chaîne d’approvisionnement pour la fabrication additive de céramique de zirconie (AM) évolue rapidement alors que la demande pour des céramiques avancées dans des applications haute performance augmente. En 2025, le secteur est caractérisé par un écosystème mûr de fournisseurs de poudres, de fabricants d’équipements et d’utilisateurs finaux, avec un accent sur la garantie de la qualité, la consistance et l’évolutivité des matériaux.
La zirconie (dioxyde de zirconium, ZrO₂) est prisée pour sa résistance mécanique exceptionnelle, sa ténacité à la rupture et sa stabilité chimique, la rendant idéale pour des composants dentaires, médicaux et industriels. La chaîne d’approvisionnement commence par l’extraction et la purification des minéraux de zirconium, principalement issus d’Australie, d’Afrique du Sud et de Chine. Ces matières premières sont transformées en poudres de zirconie de haute pureté, qui sont ensuite adaptées pour des processus de fabrication additive tels que la stéréolithographie (SLA), le traitement par lumière numérique (DLP) et le jet de liant.
Les principaux fournisseurs de poudres de zirconie pour l’AM incluent Tosoh Corporation, un leader mondial dans les céramiques avancées, et 3DCeram, qui se spécialise dans les suspensions céramiques prêtes à imprimer. La Tosoh Corporation est notable pour ses poudres de zirconie stabilisées par yttrium (YSZ), largement utilisées tant dans la fabrication traditionnelle que additive en raison de leurs propriétés supérieures et de leur consistance d’un lot à l’autre. 3DCeram ne fournit pas seulement des matériaux, mais développe également des systèmes AM et des solutions de post-traitement, soutenant une chaîne d’approvisionnement intégrée verticalement.
Du côté des équipements, des entreprises comme Lithoz GmbH et CeramTec font progresser les capacités de l’impression 3D céramique. Lithoz GmbH propose des systèmes LCM (Fabrication Céramique par Lithographie) optimisés pour la zirconie, tandis que CeramTec élargit son portefeuille AM pour répondre à la production industrielle. Ces fabricants collaborent de plus en plus avec les fournisseurs de poudre pour garantir la compatibilité des procédés et la reproductibilité.
La résilience de la chaîne d’approvisionnement est une préoccupation croissante, notamment à la lumière des tensions géopolitiques et de la concentration des ressources minérales de zirconium. Les entreprises investissent dans des stratégies d’approvisionnement alternatives et des initiatives de recyclage pour atténuer les risques. Par exemple, Tosoh Corporation explore le recyclage en boucle fermée des déchets de zirconie issus des processus d’AM, visant à réduire la dépendance aux matières premières vierges.
En regardant vers l’avenir, les perspectives pour les chaînes d’approvisionnement AM de céramique de zirconie dans les prochaines années sont positives, avec une croissance anticipée tant en matière de disponibilité des matériaux que d’automatisation des procédés. Les acteurs de l’industrie devraient prioriser la traçabilité numérique, l’assurance qualité et les approvisionnements durables pour répondre aux exigences strictes des secteurs médical et aérospatial. À mesure que la fabrication additive de composants en zirconie se développe, des partenariats entre producteurs de poudre, fabricants d’imprimantes et utilisateurs finaux seront essentiels pour assurer une chaîne d’approvisionnement robuste et réactive.
Environnement Réglementaire et Normes de l’Industrie
Le paysage réglementaire et les normes de l’industrie pour la fabrication additive de céramique de zirconie (AM) évoluent rapidement à mesure que la technologie mûrit et que son adoption augmente dans des secteurs tels que la dentisterie, la médecine, et les applications industrielles. En 2025, les organismes de réglementation et les organisations de l’industrie intensifient leurs efforts pour établir des cadres clairs qui garantissent la sécurité, la fiabilité et la qualité des pièces AM en zirconie, en particulier pour les applications critiques.
Dans les secteurs médical et dentaire, les céramiques de zirconie sont largement utilisées pour les implants, couronnes, et prothèses en raison de leur biocompatibilité et de leur résistance mécanique. La surveillance réglementaire est principalement exercée par des agences telles que la Food and Drug Administration (FDA) des États-Unis et l’Agence Européenne des Médicaments (EMA), qui exigent une validation rigoureuse tant des matériaux que des processus de fabrication. La fabrication additive introduit de nouvelles variables—comme la fabrication couche par couche et le post-traitement—qui nécessitent des mises à jour des directives. En 2024 et 2025, la FDA a continué de peaufiner son approche envers l’AM, en mettant l’accent sur la validation des processus, la traçabilité, et la caractérisation des matériaux pour les dispositifs céramiques. L’Organisation Internationale de Normalisation (ISO) a également mis à jour des normes telles que l’ISO 13356 (pour la zirconie stabilisée par yttrium) et travaille sur des normes spécifiques à l’AM sous la série ISO/ASTM 52900, qui traitent de la terminologie, des tests et de la qualification pour les pièces AM.
Les leaders de l’industrie participent activement au développement et à la conformité des normes. 3D Systems, un acteur majeur de l’AM céramique, collabore avec les organismes de réglementation et les organisations de normes pour s’assurer que ses solutions zirconie dentaires et médicales répondent aux exigences évolutives. XJet, connu pour sa technologie NanoParticle Jetting, est également engagé dans les processus de qualification pour ses pièces AM en zirconie, en particulier pour ses clients dentaires et industriels. Lithoz, un spécialiste de l’impression 3D céramique, a contribué à l’élaboration de protocoles de validation des processus et collabore avec des partenaires pour garantir la conformité aux normes ISO et FDA.
En regardant vers l’avenir, les prochaines années devraient apporter une harmonisation supplémentaire des normes, avec un accent accru sur la surveillance des processus, la traçabilité numérique et la gestion du cycle de vie des composants AM en zirconie. Des consortiums industriels et des groupes de travail, tels que ceux coordonnés par le ASTM International Additive Manufacturing Center of Excellence, accélèrent la création de meilleures pratiques et de voies de qualification. À mesure que la clarté réglementaire s’améliore, l’adoption de l’AM de céramique de zirconie devrait s’accélérer, notamment dans les industries réglementées où la certification est un prérequis pour l’entrée sur le marché.
Analyse Concurrentielle : Forces, Faiblesses et Différenciateurs
Le paysage concurrentiel de la fabrication additive de céramique de zirconie (AM) en 2025 est façonné par un groupe sélectionné de leaders technologiques, de producteurs céramiques établis, et de start-ups innovantes. Le secteur est caractérisé par de rapides avancées en science des matériaux, optimisation des processus, et solutions spécifiques aux applications, avec un accent sur les composants dentaires, médicaux, et industriels.
Forces dans le secteur de l’AM de zirconie proviennent des propriétés mécaniques exceptionnelles du matériau—forte ténacité à la rupture, résistance à l’usure, et biocompatibilité—les rendant idéales pour des applications exigeantes. Des entreprises telles que 3D Systems et XJet ont développé des technologies propriétaires pour des pièces en zirconie à haute densité et haute précision. 3D Systems exploite sa plateforme Figure 4 pour la zirconie dentaire, tandis que XJet avec son NanoParticle Jetting permet des géométries complexes et des détails fins. Lithoz, un pionnier autrichien, est reconnu pour son processus LCM (Fabrication Céramique par Lithographie), qui fournit des composants en zirconie denses et haute résistance pour les usages médicaux et industriels. Ces entreprises bénéficient d’une R&D robuste, de bases de clients établies, et de flux de production validés.
Faiblesses persistent, notamment en ce qui concerne le débit, l’évolutivité, et le coût. Les processus AM de zirconie nécessitent souvent des étapes de post-traitement telles que le désengorgement et le frittage, ce qui peut prolonger les délais et introduire de la variabilité. Les coûts des matériaux restent élevés par rapport à la fabrication traditionnelle, et le besoin d’équipements spécialisés limite l’accessibilité pour les petites entreprises. De plus, la qualification et la certification des pièces AM en zirconie pour les industries réglementées (par exemple, les implants médicaux) est un processus long et exigeant en ressources, posant une barrière à une adoption rapide.
Différenciateurs parmi les concurrents sont de plus en plus définis par l’innovation de processus, l’accent mis sur les applications, et l’intégration écosystémique. XJet se distingue par son impression sans support et sa capacité à produire des canaux internes complexes, ouvrant de nouvelles possibilités de design. La technologie LCM de Lithoz est connue pour sa haute résolution et sa capacité à s’adapter aussi bien au prototypage qu’à la production en série. 3D Systems exploite sa portée mondiale et ses partenariats avec des laboratoires dentaires pour accélérer l’adoption dans la dentisterie numérique. Pendant ce temps, des entreprises comme CeramTec et Tosoh—fournisseurs majeurs de poudres de zirconie—collaborent de plus en plus avec des fournisseurs de matériel AM pour optimiser les formulations de matériaux pour les processus additifs.
En regardant vers l’avenir, l’avantage concurrentiel reposera probablement sur la capacité à fournir des pièces en zirconie validées et prêtes à l’emploi à grande échelle, avec des flux de travail rationalisés et des solutions rentables. Les partenariats stratégiques entre les fournisseurs de matériaux, les fabricants d’imprimantes et les utilisateurs finaux devraient s’intensifier, stimulant encore l’innovation et la pénétration du marché dans les années à venir.
Durabilité et Impact Environnemental
La fabrication additive de céramique de zirconie (AM) prend de l’élan en 2025 comme une alternative durable aux méthodes traditionnelles de traitement céramique, motivée par les réglementations environnementales et la demande de l’industrie pour des méthodes de production plus écologiques. Le profil de durabilité de l’AM de zirconie est façonné par plusieurs facteurs, y compris l’efficacité matérielle, la consommation d’énergie, la réduction des déchets et la recyclabilité.
L’un des principaux avantages environnementaux de l’AM de zirconie est sa capacité à minimiser les déchets matériels. Contrairement à la fabrication soustractive, qui entraîne souvent une quantité significative de chutes, les processus d’AM tels que la stéréolithographie (SLA), le traitement par lumière numérique (DLP), et le jet de liant utilisent uniquement le matériau nécessaire à la construction de la pièce. Des fabricants de premier plan comme 3DCeram et Lithoz ont développé des processus propriétaires qui optimisent l’utilisation des poudres et permettent le recyclage de la poudre de zirconie non utilisée, réduisant ainsi encore les flux de déchets.
La consommation d’énergie est un autre aspect critique. Bien que le frittage reste énergivore, les avancées dans le contrôle des processus AM et l’utilisation de fours plus efficaces aident à réduire l’empreinte énergétique globale. Des entreprises telles que CeramTec et XJet investissent dans la recherche pour améliorer l’efficacité de frittage et réduire les temps de cycle, ce qui devrait entraîner des gains de durabilité au cours des prochaines années.
L’utilisation d’eau et les émissions sont également plus faibles dans l’AM par rapport à la fabrication céramique conventionnelle, qui implique souvent le fraisage humide et un post-traitement extensif. L’approche couche par couche de l’AM réduit le besoin de traitement à base d’eau et minimise le rejet de particules et de composés organiques volatils (COV). Cela s’aligne avec les objectifs environnementaux des principaux producteurs de céramiques comme Tosoh, qui fournit des poudres de zirconie de haute pureté et promeut activement des pratiques durables tout au long de sa chaîne d’approvisionnement.
En regardant vers l’avenir, les perspectives de durabilité dans l’AM de céramique de zirconie sont positives. Les collaborations industrielles et les efforts de normalisation, tels que ceux dirigés par The American Ceramic Society, devraient accélérer l’adoption des meilleures pratiques et des méthodologies d’évaluation du cycle de vie. À mesure que les pressions réglementaires augmentent et que les utilisateurs finaux exigent des solutions plus écologiques, les fabricants sont susceptibles d’investir davantage dans le recyclage en boucle fermée, l’intégration des énergies renouvelables, et des systèmes de liants respectueux de l’environnement. D’ici 2027, l’AM de zirconie devrait établir de nouvelles normes pour la fabrication de céramiques avancées durables, soutenant à la fois la responsabilité environnementale et la compétitivité économique.
Perspectives Futures : Opportunités, Défis et Recommandations Stratégiques
Les perspectives futures pour la fabrication additive de céramique de zirconie (AM) en 2025 et dans les années à venir sont façonnées par une interaction dynamique d’avancées technologiques, d’opportunités de marché, et de défis persistants. Alors que la demande pour des céramiques haute performance augmente dans des secteurs tels que la dentisterie, la médecine, l’aérospatial et l’électronique, les propriétés uniques de la zirconie—résistance exceptionnelle, ténacité à la rupture, et biocompatibilité—la positionnent comme le matériau de choix pour les applications AM de nouvelle génération.
Les principaux acteurs de l’industrie intensifient leur attention sur l’augmentation de la production et l’amélioration de la fiabilité des processus. 3D Systems et XJet sont à l’honneur pour leurs investissements continus dans les technologies de jet de liant et de jet de nanoparticules, respectivement, qui permettent la fabrication de pièces en zirconie denses et complexes avec une résolution de caractéristique fine. Lithoz, un pionnier dans le domaine de la stéréolithographie céramique, continue d’élargir son portefeuille, ciblant à la fois des marchés industriels et médicaux avec de nouveaux modèles d’imprimantes et formulations de matériaux. Ces entreprises devraient conduire une adoption accrue en abordant les obstacles de débit et de coût.
Des opportunités se présentent dans le secteur dentaire, où l’AM de zirconie est déjà en train de perturber la fabrication soustractive traditionnelle. La capacité à produire des couronnes, bridges et implants spécifiques aux patients avec un gaspillage matériel réduit et des délais de livraison plus rapides favorise l’adoption. CeramTec et Ivoclar tirent parti de l’AM pour offrir des solutions dentaires personnalisées, et des collaborations continues avec des laboratoires dentaires devraient se renforcer en 2025. Dans le secteur de l’aérospatial et de l’électronique, la recherche de composants légers, thermiquement stables, et électriquement isolants devrait ouvrir de nouveaux marchés pour l’AM de zirconie, alors que les normes de qualification évoluent.
Cependant, des défis demeurent. Atteindre une densité uniforme, minimiser les défauts, et garantir la reproductibilité des propriétés mécaniques sont des obstacles techniques en cours. Le post-traitement, y compris le désengorgement et le frittage, ajoute de la complexité et du coût, en particulier pour les pièces plus grandes ou plus complexes. Les coûts des matériaux pour les poudres de zirconie de haute pureté restent également une contrainte, bien qu’une concurrence accrue parmi les fournisseurs, comme Tosoh et Kyocera, puisse aider à modérer les prix au fil du temps.
Les recommandations stratégiques pour les acteurs comprennent l’investissement dans l’automatisation des processus, la surveillance de la qualité en ligne, et l’intégration des flux de travail numériques pour améliorer l’évolutivité et la traçabilité. Les partenariats entre les fournisseurs de technologies AM, les fournisseurs de matériaux, et les utilisateurs finaux seront cruciaux pour accélérer les efforts de qualification et de normalisation. À mesure que les cadres réglementaires pour les applications médicales et aérospatiales évoluent, un engagement proactif avec les organismes de l’industrie et les agences de certification sera essentiel pour l’accès au marché.
En résumé, la fabrication additive de céramique de zirconie est prête à connaître une croissance significative en 2025 et au-delà, stimulée par l’innovation, l’élargissement des domaines d’application, et un écosystème en maturation. Les entreprises qui donnent la priorité à l’optimisation des processus, à la collaboration et à la préparation réglementaire seront les mieux placées pour capitaliser sur les opportunités émergentes.