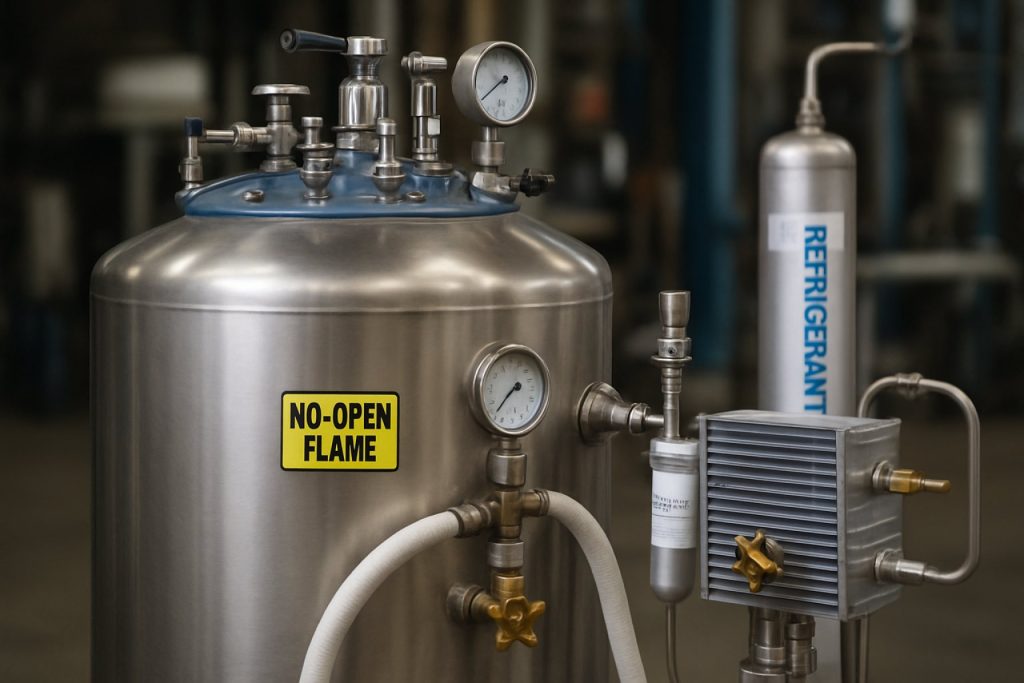
Inside the Cryovessel Refrigerant Components Revolution: What 2025 Holds and the Surprising Technologies Shaping the Next Five Years. Manufacturers and Innovators—Are You Ready for the Next Wave?
- Executive Summary: 2025 and Beyond
- Industry Overview: Cryovessel Refrigerant Components Landscape
- Key Manufacturers and Supply Chain Dynamics
- Cutting-Edge Technologies Transforming Cryogenic Components
- Regulatory Trends and Standards (2025 Update)
- Market Forecast: Volume and Revenue Projections to 2030
- Emerging Applications and End-User Sectors
- Competitive Analysis: Leading Players and Strategic Moves
- Sustainability Initiatives and Material Innovations
- Future Outlook: Opportunities, Risks, and Game-Changers
- Sources & References
Executive Summary: 2025 and Beyond
The cryovessel refrigerant components manufacturing sector is poised for significant transformation as we move through 2025 and into the latter part of the decade. Cryovessels, which serve as critical infrastructure for the storage and transport of liquefied and gaseous cryogens such as liquid nitrogen, oxygen, argon, and increasingly, hydrogen, are experiencing heightened demand driven by sectors including healthcare, energy, and advanced manufacturing.
Key players in the industry—such as Linde, Air Liquide, and Cryofab—are actively investing in advanced component manufacturing technologies. These include high-efficiency multilayer insulation, improved vacuum sealing methods, and automated welding processes. Linde continues to expand its portfolio of cryogenic equipment and components to support both industrial and medical applications, while Air Liquide is scaling up its production capacity to meet increased requirements for hydrogen storage and transport, spurred by the global energy transition.
Emerging trends in 2025 involve the integration of smart sensors and digital monitoring systems within cryovessel components to enhance operational safety and efficiency. Manufacturers such as Cryofab are exploring the adoption of IoT-based diagnostics and remote monitoring capabilities for critical subassemblies like valves, regulators, and pressure relief devices. This reflects a wider industry push toward predictive maintenance and lifecycle optimization, reducing downtime and increasing reliability—key factors as cryogenic infrastructure scales up for hydrogen and LNG supply chains.
Material innovation is another focal point. The shift toward lighter, higher-strength alloys and composites is being led by companies like Chart Industries, which is advancing the use of stainless steels and superinsulation foams to reduce boil-off rates and improve energy efficiency. The adoption of automated and precision manufacturing methods is expected to drive down component costs while improving consistency and safety compliance.
Looking ahead, the outlook for cryovessel refrigerant components manufacturing remains robust. The global push for decarbonization—especially the growth of green hydrogen and LNG infrastructure—points to sustained investment in cryogenic storage and transport solutions. Regulatory emphasis on safety, combined with customer demand for higher performance and digital integration, will continue to shape R&D and production strategies for the next several years. Industry leaders such as Linde, Air Liquide, Cryofab, and Chart Industries are well positioned to capitalize on these trends, underpinned by their global reach, technical expertise, and ongoing innovation.
Industry Overview: Cryovessel Refrigerant Components Landscape
The global landscape for cryovessel refrigerant components manufacturing in 2025 is characterized by robust activity, ongoing innovation, and a strategic focus on supply chain security. Cryovessels—which include dewars, cryogenic tanks, and associated storage solutions—rely on precisely engineered components such as valves, vacuum jackets, multi-layer insulation, piping assemblies, and advanced sensors to safely store and transport liquefied gases (notably nitrogen, oxygen, argon, LNG, and hydrogen) at extremely low temperatures. The demand for these components is growing, driven by expanding applications in medical, semiconductor, energy, and aerospace sectors.
Leading manufacturers are concentrated in regions with advanced industrial infrastructure, notably North America, Europe, and parts of Asia. Chart Industries (USA) is among the dominant players, offering comprehensive manufacturing capabilities for cryogenic equipment and integrated refrigerant components, including proprietary vacuum systems and insulation methods. European firms such as Linde and Air Liquide maintain vertically integrated operations, producing both the bulk gases and the specialized cryogenic vessels and fittings required for safe handling. In Asia, companies like Taiyo Nippon Sanso and Taylor-Wharton (with global operations) serve both domestic and export markets with a full range of refrigerant components, from valves to multilayer insulation panels.
2025 sees continued investment in automation and quality control technologies. Manufacturers are expanding their use of robotic welding, additive manufacturing for complex component geometries, and digital inspection systems to enhance reliability and consistency. The push for decarbonization—including the rapid scale-up of hydrogen liquefaction and LNG infrastructure—has triggered new requirements for materials that withstand thermal cycling and aggressive cryogens, spurring R&D in high-performance alloys and advanced composites. Herose is notable for its international specialization in cryogenic valves, while Messer Group operates both as a gas supplier and a component manufacturer, emphasizing custom solutions.
Supply chain resilience remains a central concern as geopolitical and logistical uncertainties persist. Many manufacturers are localizing critical component production and forming strategic partnerships to ensure uninterrupted supply of precision parts and specialty materials. Regulatory harmonization is also underway, with pressure to meet or exceed international standards for safety, emissions, and efficiency.
Looking ahead, the cryovessel refrigerant components sector is expected to consolidate around companies capable of vertical integration, digitalization, and rapid prototyping. Demand for ultra-high purity gas systems, especially for semiconductor and quantum technology applications, is likely to drive tighter tolerances and digital traceability. The market outlook through the next few years is bullish, with capacity expansions and technological upgrades underway at key manufacturing sites globally.
Key Manufacturers and Supply Chain Dynamics
The cryovessel refrigerant components manufacturing sector is entering 2025 with a robust pipeline of projects and considerable focus on both innovation and supply chain resilience. Cryovessels, integral to liquid hydrogen, helium, and LNG storage and transport, rely on advanced refrigerant components such as multi-layer insulation, vacuum valves, cryogenic pumps, and heat exchangers. As global demand for clean energy, medical, aerospace, and semiconductor applications rises, manufacturers are scaling up both capacity and technology integration.
Key players in this segment include Linde, Air Liquide, and Chart Industries. These companies are recognized for their vertically integrated manufacturing, covering design, fabrication, and supply of cryogenic equipment and associated refrigerant components. Linde and Air Liquide maintain extensive global networks, with manufacturing hubs in Europe, Asia, and North America, ensuring regional supply stability and rapid response to demand surges. Chart Industries specializes in highly engineered vacuum-insulated vessels and advanced cryogenic pumps, supporting both LNG and hydrogen infrastructure buildouts.
Component specialization is also notable. For instance, HEROSE is a leading manufacturer of cryogenic valves, offering safety and control solutions vital for reliable vessel operation. Cryocomp and Pfeiffer Vacuum supply vacuum valves and instrumentation used in multi-layer insulation systems, essential to minimizing thermal losses in cryovessels. Cryostar is prominent in cryogenic pump production, catering to LNG, industrial gases, and hydrogen refueling stations.
A significant supply chain trend for 2025 is increased localization of critical component manufacturing, especially in Europe and North America, to mitigate geopolitical risks and logistics disruptions. Companies like Linde and Chart Industries have announced investments in regional production facilities and supplier development to ensure redundancy and reduce lead times. Additionally, there is a growing emphasis on digital integration, with manufacturers deploying IoT-enabled sensors and remote monitoring for predictive maintenance and supply chain visibility.
Looking ahead, the sector anticipates sustained demand growth, driven by hydrogen economy expansion and semiconductor fabrication investments. Key manufacturers are expected to continue scaling up capacity, investing in automation, and pursuing strategic partnerships with material suppliers to secure high-performance alloys and insulation materials. Collaborative efforts between equipment makers and end-users—especially in aerospace and energy transition projects—will further fuel innovation in cryovessel refrigerant component technologies.
Cutting-Edge Technologies Transforming Cryogenic Components
The landscape of cryovessel refrigerant components manufacturing is undergoing a marked transformation as the industry integrates advanced technologies to meet growing demands for performance, efficiency, and sustainability. In 2025, several cutting-edge developments are driving change, particularly in the materials science, automation, and digitalization domains.
One of the most significant technological advancements is the adoption of high-performance alloys and composite materials for critical components such as heat exchangers, transfer lines, and vacuum-insulated vessels. Companies are leveraging improved stainless steels, aluminum alloys, and even novel composite structures to enhance mechanical strength while minimizing thermal conductivity, leading to lower heat ingress and improved thermal efficiency. This is especially evident in the development of large-scale LNG storage and hydrogen applications, where performance under extreme conditions is paramount. Cryofab and Chart Industries are among the prominent manufacturers investing in these material innovations to extend service life and reduce boil-off rates.
Automation and precision manufacturing technologies are also transforming the cryovessel refrigerant component sector. Advanced robotic welding, automated seam inspection, and high-precision forming processes are being deployed to ensure repeatable quality and to handle the production of intricate geometries required for modern cryogenic applications. These automated systems, often integrated with real-time quality monitoring and non-destructive testing, are reducing human error and improving overall process efficiency. Linde, with its global manufacturing footprint, has reported significant improvements in throughput and consistency by incorporating such automation into its cryogenic equipment production lines.
Digitalization is another key trend, as manufacturers increasingly embed sensors and IoT connectivity in refrigerant components. This enables remote monitoring of vessel integrity, leak detection, and predictive maintenance—capabilities that are in high demand for critical infrastructure such as medical oxygen supply, semiconductor fabrication, and space exploration. The integration of digital twins and data analytics platforms allows operators to simulate performance, optimize energy use, and preempt costly downtime. Companies like Air Products are rolling out digital-enabled cryogenic systems that provide customers with actionable operational insights.
Looking ahead, the sector is poised for further innovation, driven by the global pivot toward clean energy—particularly hydrogen and LNG—as well as intensified requirements for reliability and safety. The convergence of new materials, smart manufacturing, and digital intelligence is expected to yield cryovessel refrigerant components that are not only more efficient and durable, but also more adaptable to emerging applications in the energy transition and advanced manufacturing sectors.
Regulatory Trends and Standards (2025 Update)
The regulatory environment governing cryovessel refrigerant components manufacturing is undergoing significant evolution in 2025, reflecting advances in technology, heightened safety concerns, and the global push towards sustainability. The sector, integral to applications in liquefied gases, medical storage, and industrial processing, faces increasingly rigorous standards that affect material choices, design, testing, and traceability.
Key international standards remain foundational. The American Society of Mechanical Engineers (ASME) continues to update its Boiler and Pressure Vessel Code (BPVC), which is broadly referenced for cryogenic vessel and component fabrication, including mandatory requirements for pressure relief devices, welding procedures, and non-destructive examination. In 2025, revisions focus on digital traceability of critical components and stricter material certification protocols. The European Committee for Standardization (CEN) similarly advances harmonized EN standards, such as EN 13458 for cryogenic vessels, integrating lifecycle sustainability assessments and extended reporting for refrigerant-related components.
Environmental compliance is intensifying, with the phase-down of high-global warming potential (GWP) refrigerants under the Kigali Amendment to the Montreal Protocol. Manufacturers are required to adapt to new refrigerant chemistries—such as low-GWP hydrofluoroolefins (HFOs) and natural refrigerants—necessitating requalification of valves, seals, and instrumentation. Companies like Linde and Air Liquide, both major producers and users of cryogenic vessels and gases, are actively collaborating with regulatory bodies to ensure their component designs meet evolving requirements for leak-tightness and environmental safety.
In the United States, the Department of Transportation (DOT) and the Occupational Safety and Health Administration (OSHA) are updating guidelines for the transport and workplace safety of cryogenic equipment, focusing on enhanced incident reporting and the use of smart sensors for real-time monitoring of refrigerant containment. The International Organization for Standardization (ISO) is pushing for greater harmonization, with ISO 21009 and ISO 20421 (for gas storage and transport vessels) undergoing reviews to address digital documentation and the integration of Internet of Things (IoT) diagnostics into component certification processes.
Looking ahead, regulatory trends point to increased digitization of compliance records, mandatory sustainability disclosures, and more rapid adaptation to new refrigerant chemistries. Leading manufacturers such as Chart Industries and Cryo AB are enhancing their quality management systems to not only ensure conformity with these evolving standards but also to provide transparent traceability from raw material sourcing to end-of-life component recycling. This alignment with regulatory trends is expected to become a key differentiator in the global market for cryovessel refrigerant components over the next several years.
Market Forecast: Volume and Revenue Projections to 2030
The global market for cryovessel refrigerant components manufacturing is positioned for steady growth through 2030, driven by expansion in sectors such as medical technology, quantum computing, aerospace, and energy. Cryovessels, critical for storing and transporting liquefied gases like nitrogen, helium, and hydrogen, rely on highly specialized refrigerant components—including vacuum-insulated vessels, multilayer insulation, high-efficiency heat exchangers, and advanced valves—whose demand is expected to intensify with ongoing investments in cryogenic infrastructure.
In 2025, the worldwide shipment volume of cryovessel refrigerant components is projected to surpass several hundred thousand units, with a cumulative value estimated in the multibillion-dollar range. Leading manufacturers such as Linde, Air Liquide, and Chart Industries are scaling up production capacities to address rising requirements from life sciences, semiconductor manufacturing, and green hydrogen projects. For example, Chart Industries has reported increased orders for cryogenic tanks and components, reflecting broad-based customer demand for both established and emerging applications.
Between 2025 and 2030, analysts anticipate a compound annual growth rate (CAGR) in the high single digits for both volume and revenue, underpinned by the expansion of large-scale infrastructure projects and government investments targeting clean energy. The rollout of national hydrogen strategies in Europe, Asia, and North America is particularly significant, with major industrial gas companies such as Linde and Air Liquide actively involved in scaling up liquid hydrogen storage and distribution networks. These initiatives are expected to drive robust demand not only for new cryovessels but also for advanced refrigerant components capable of handling ultra-low temperatures and high purity requirements.
Medical and biotechnology sectors will remain substantial contributors to market volumes, with cryogenic storage of biological materials and vaccines necessitating reliable, high-performance refrigerant components. Major suppliers including Thermo Fisher Scientific and Praxair (now part of Linde) continue to invest in next-generation vessel and component manufacturing to support evolving standards in sample preservation and logistics.
By 2030, the market outlook is characterized by increasing sophistication in product offerings, including digitalized monitoring systems and enhanced thermal efficiency. Companies with vertically integrated supply chains and a focus on R&D—such as Air Products—are likely to capture greater value share as customers seek both performance and sustainability in cryogenic operations. The overall sector is expected to remain competitive, with ongoing consolidation and partnerships shaping the volume and revenue trajectory of cryovessel refrigerant component manufacturing.
Emerging Applications and End-User Sectors
The landscape of cryovessel refrigerant components manufacturing is rapidly evolving as new applications and end-user sectors drive both technological innovation and market expansion. As of 2025, several key trends are shaping the demand for specialized components, from advanced materials to enhanced system integration.
One of the most significant drivers is the global push for quantum computing and superconducting technologies. These fields require ultra-low-temperature environments, which are only achievable with highly reliable cryogenic vessels and sophisticated refrigerant components. Major players such as Praxair (now part of Linde) and Air Liquide are investing in the development of new vessel geometries, insulation systems, and refrigerant management modules tailored for these demanding applications. Their engineering divisions collaborate closely with quantum hardware manufacturers, ensuring compatibility and performance at the sub-Kelvin temperature range.
Another emerging application is in the healthcare and biomedical sectors, notably within cryopreservation and cell therapy logistics. The expansion of cell and gene therapy pipelines has led to a surge in demand for cryogenic storage and transport solutions that guarantee sample integrity. Companies like Thermo Fisher Scientific are advancing vessel component manufacturing by incorporating smart sensors, improved phase separators, and refillable, low-loss dewars to support long-duration and global distribution requirements.
The energy sector is also stimulating growth in cryovessel refrigerant components manufacturing. Hydrogen, as a clean fuel, necessitates the liquefaction and storage of large volumes at cryogenic temperatures. Established gas technology firms such as Linde and Air Products are scaling up their manufacturing capacities to deliver high-throughput, safety-certified components—such as multi-layer vacuum insulation, precision valves, and automated level gauges—specifically designed for liquid hydrogen storage and transport.
Space exploration and aerospace technology continue to be a crucial end-user sector, with private and governmental organizations requiring advanced cryogenic vessels for propellant storage and life support systems. Leading aerospace suppliers, in partnership with manufacturers like Cryofab, are pushing boundaries in lightweight composite materials and modular vessel designs for space applications.
Looking forward, the outlook for cryovessel refrigerant components manufacturing is one of sustained growth and diversification. Industry participants are investing in automation, additive manufacturing, and digital monitoring for real-time diagnostics, responding to the increasingly specialized needs across quantum technology, biomedicine, clean fuels, and aerospace. As these end-user sectors expand, the sector is expected to see continued innovation and robust demand into the late 2020s.
Competitive Analysis: Leading Players and Strategic Moves
The cryovessel refrigerant components manufacturing sector is defined by a competitive landscape featuring a blend of established multinationals and specialized engineering firms. As of 2025, the industry has seen intensified competition, driven by increasing demand for advanced cryogenic solutions in healthcare, energy, and industrial gas sectors. Companies are focusing on technological innovation, capacity expansion, and strategic collaborations to secure market leadership and respond to evolving client requirements for reliability, safety, and efficiency in cryogenic storage and transport.
A key player in this field is Linde plc, widely recognized for its comprehensive portfolio of cryogenic vessels and refrigerant components. Linde’s global manufacturing footprint, in combination with its strong R&D capabilities, enables the company to offer highly engineered components for liquid nitrogen, argon, and oxygen storage. In recent years, Linde has invested in digitalized production processes and advanced materials, aiming to improve thermal insulation and reduce product lifecycle costs.
Air Liquide is another major force, leveraging its expertise in industrial gases and cryogenic technologies to supply high-performance vessels and subcomponents. Air Liquide has emphasized sustainable production methods, including the use of recycled materials and energy-efficient manufacturing. The company is also collaborating with research institutions to develop next-generation refrigerant valves and pressure regulation systems.
In the United States, Chart Industries has consolidated its position through acquisitions and organic growth. Chart’s product range spans cryogenic tanks, piping, and essential refrigerant components, serving both large-scale industrial and medical applications. The company has expanded its production capacity in North America and Europe and is focusing on modular cryovessel solutions to cater to the growing demand for decentralized gas supply systems.
- Cryofab, Inc., a specialized manufacturer, is known for custom-engineered cryogenic vessels and associated hardware. The company has recently introduced new insulation techniques and quick-connect refrigerant component systems, targeting the research and laboratory market segment.
- HEROSE GmbH stands out in the production of cryogenic safety and control valves, with a strong focus on precision engineering and compliance with evolving international standards.
- Praxair (now part of Linde plc) continues to supply cryogenic equipment and components, maintaining a strong presence in the Americas with broad distribution networks.
Looking ahead, the competitive environment is expected to see further consolidation, as leading players pursue mergers and strategic alliances to enhance technological capabilities and global reach. Investments in smart manufacturing, automation, and sustainability will likely differentiate the frontrunners, while new entrants may focus on niche materials, IoT-enabled monitoring, and customized refrigerant componentry to carve out market share. The next few years will be shaped by both incremental innovation and the adoption of advanced digital and sustainable practices within the cryovessel refrigerant components manufacturing sector.
Sustainability Initiatives and Material Innovations
The sustainability profile of cryovessel refrigerant components manufacturing is evolving rapidly in 2025, with major industry players and component suppliers implementing a mix of eco-conscious practices and material innovations. Driven both by regulatory pressure and industry-wide decarbonization goals, manufacturers are exploring new approaches to reduce environmental impact, improve efficiency, and extend product life cycles.
A significant focus is on the adoption of low-carbon and recyclable materials for critical refrigerant-contact components. Stainless steel remains the dominant material due to its mechanical strength and low permeability at cryogenic temperatures, but several manufacturers, such as Linde and Air Liquide, are increasing the use of higher recycled-content steel and introducing traceable supply chain practices to ensure responsible sourcing. In parallel, alternative alloys and advanced composite materials are being tested for non-structural parts, aiming to reduce overall weight and embodied carbon without compromising performance.
Innovations in insulation systems are particularly noteworthy. Companies like Cryofab and Cryostar are developing multilayer insulation (MLI) and vacuum jacketed piping using materials with lower environmental footprints, such as aerogels and recycled glass fibers, in place of traditional foams and perlite. These materials not only improve thermal efficiency—lowering boil-off rates and reducing energy demand for refrigeration—but also enhance recyclability at end-of-life.
Process improvements are central to sustainability efforts. Leading fabricators are investing in renewable-powered manufacturing lines, with Linde and Air Products reporting increased use of solar and wind energy in their European and North American operations. Waste minimization programs, such as closed-loop water systems and scrap metal recycling, are becoming standard practice, contributing to a lower overall environmental footprint for refrigerant component production.
Looking ahead over the next few years, the outlook for sustainable cryovessel refrigerant component manufacturing is promising. Industry collaborations—such as joint research on low-GWP (global warming potential) refrigerants and new materials—and wider adoption of lifecycle assessment frameworks are expected to further accelerate these trends. As regulatory standards tighten and end-users prioritize green procurement, the sector is likely to see increased investment in research, eco-design, and digital traceability, positioning material innovation and sustainability at the core of future manufacturing strategies.
Future Outlook: Opportunities, Risks, and Game-Changers
The future outlook for cryovessel refrigerant components manufacturing is shaped by a convergence of technological advances, supply chain dynamics, and evolving end-user requirements across sectors such as energy, healthcare, and aerospace. As of 2025, the sector is witnessing significant investments in both R&D and production capacity to address the rising global demand for high-performance cryogenic solutions, particularly in liquid hydrogen, LNG, and medical applications.
One notable opportunity lies in the anticipated scaling-up of hydrogen infrastructure, where robust and efficient cryovessel components are indispensable for storage and transport. Major industrial gas companies such as Linde and Air Liquide are expanding their technology portfolios and manufacturing footprints to support the burgeoning hydrogen economy. Both companies are investing in advanced manufacturing techniques and materials—such as high-strength stainless steels and super-insulated multilayer foils—to enhance the safety and efficiency of refrigeration components within cryogenic vessels.
Another driver is the increasing complexity and miniaturization of cryogenic systems for medical and scientific use. Companies like Chart Industries and Cryofab are developing more compact, modular refrigerant component designs to support applications in MRI, biotechnology, and quantum computing. These innovations are expected to proliferate as end-users demand greater reliability, lower boil-off rates, and simplified integration into broader systems.
On the risk side, the cryovessel refrigerant components manufacturing segment faces challenges tied to material supply and quality assurance. The sector is highly sensitive to fluctuations in the availability of specialty alloys and insulation materials, which can impact lead times and cost structures. Furthermore, the critical nature of these components—where even minor defects can lead to catastrophic failures—means that manufacturers must continually invest in advanced inspection and testing capabilities. Ongoing geopolitical tensions and potential trade restrictions on high-grade materials also add an extra layer of risk to global supply chains.
A potential game-changer emerging in the next few years is the adoption of automation and digital manufacturing technologies. Leading firms are piloting Industry 4.0 approaches, including real-time monitoring, digital twins, and predictive quality assurance, to boost yield and traceability while reducing labor dependency. For example, Linde and Air Liquide have publicly committed to digital transformation initiatives aimed at both process optimization and sustainability.
Overall, while the cryovessel refrigerant components manufacturing sector is poised for robust growth, its trajectory will depend on its ability to innovate materials, assure quality in a stringent regulatory environment, and adapt to rapidly changing industrial demands over the next several years.