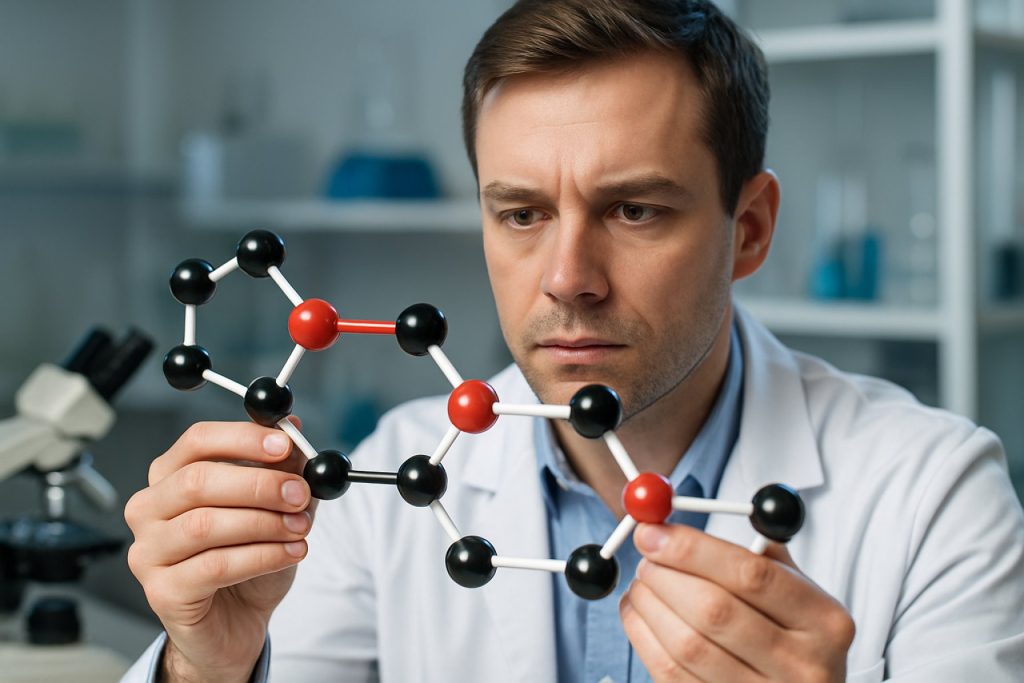
Table of Contents
- Executive Summary: 2025 Outlook for Double-Bond Linkage Polymers
- Key Market Drivers and Restraints Shaping Demand
- Innovative Synthesis Methods and Technological Advances
- Competitive Landscape: Leading Players and Strategic Initiatives
- End-Use Industry Applications: Automotive, Aerospace, Electronics, and Beyond
- Regional Analysis: Growth Hotspots and Emerging Markets
- Sustainability and Regulatory Trends Impacting Polymer Development
- Investment Opportunities and M&A Activity Forecast (2025–2030)
- Challenges: Scalability, Cost, and Performance Barriers
- Future Outlook: Next-Generation Double-Bond Linkage Polymers and Market Forecasts Through 2030
- Sources & References
Executive Summary: 2025 Outlook for Double-Bond Linkage Polymers
The market and technological landscape for double-bond linkage polymers is entering a critical period in 2025, shaped by both advances in synthesis techniques and growing demand from high-performance applications. Double-bond linkage polymers, which are characterized by the presence of carbon-carbon double bonds within their backbone or side chains, are crucial for sectors such as automotive, electronics, medical devices, and specialty coatings. Their unique chemical structure imparts tunable mechanical strength, elasticity, and chemical resistance, driving innovation in both materials science and end-use application development.
Key industry players are actively scaling up production and refining polymerization processes to improve efficiency and sustainability. Companies such as Dow and BASF continue to invest in research and development to enhance the properties of polybutadiene, polystyrene-butadiene, and other double-bond linkage polymers, focusing on molecular weight distribution control and improved catalyst systems. These advances are expected to reduce costs while meeting the stringent performance requirements of modern manufacturing.
In 2025, regulatory and market pressures for sustainable materials are accelerating the adoption of bio-based and recyclable double-bond linkage polymers. Manufacturers are responding by developing novel monomers from renewable feedstocks, with companies like Arkema and SABIC introducing new grades aimed at reducing the carbon footprint of polymer products. There is also a concerted push toward circularity, with chemical recycling technologies enabling the recovery and reuse of these polymers at the end of their lifecycle.
The integration of advanced analytics and real-time process monitoring is another emerging trend. Adoption of Industry 4.0 solutions by firms such as Covestro is enabling more precise quality control and faster response to market demands. This is particularly important for double-bond linkage polymers, where small changes in polymerization conditions can significantly alter end-use performance.
Looking ahead, the double-bond linkage polymer segment is poised for steady growth through 2025 and beyond. The convergence of sustainability mandates, technological innovation, and expanding applications in areas like electric vehicle components and flexible electronics is expected to drive both market expansion and further R&D investment. Industry stakeholders are likely to focus on lifecycle management, high-value specialty grades, and robust global supply chains to maintain competitiveness in this evolving landscape.
Key Market Drivers and Restraints Shaping Demand
The market for double-bond linkage polymer analysis is poised for continued growth in 2025, driven by a confluence of technological, industrial, and regulatory factors. Key demand drivers include the expanding utilization of double-bond containing polymers across sectors such as automotive, electronics, and healthcare, where precise characterization of double-bond structures is critical for ensuring product performance and regulatory compliance. The increasing adoption of advanced materials like thermoplastic elastomers, polyurethanes, and specialty rubbers is also propelling the need for sophisticated analytical techniques that can accurately quantify and map double-bond linkages.
Advancements in analytical instrumentation—particularly nuclear magnetic resonance (NMR) spectroscopy, Fourier-transform infrared (FTIR) spectroscopy, and chromatography—are enabling higher sensitivity and throughput in double-bond analysis. Companies such as Bruker and Agilent Technologies have continued to refine their platforms, offering integrated solutions tailored for polymer research. These developments support manufacturers in optimizing polymerization processes, enhancing material properties, and accelerating product innovation cycles.
On the regulatory front, increasing scrutiny over polymer composition and safety, particularly in sectors like medical devices and food packaging, is reinforcing the demand for precise double-bond linkage analysis. Compliance with evolving standards—such as those issued by organizations like the International Organization for Standardization (ISO)—requires robust analytical verification of chemical structures, further incentivizing investments in state-of-the-art testing capabilities.
However, several restraints temper market expansion. High capital expenditure associated with advanced analytical equipment remains a significant barrier for small- and mid-sized enterprises. Additionally, the complexity of sample preparation and data interpretation in double-bond analysis often necessitates specialized expertise, creating operational bottlenecks. Despite efforts by instrument manufacturers to simplify workflows and offer user-friendly software, a persistent skills gap may limit broader adoption.
Looking ahead to the next few years, ongoing digitalization—including the integration of AI-driven data analytics—promises to streamline double-bond linkage analysis, potentially reducing costs and expanding accessibility. Collaboration between instrument providers and polymer manufacturers, exemplified by partnerships involving companies like SABIC and BASF, is expected to drive further innovation in both analytical methods and material development. Nonetheless, market growth will depend on balancing the pace of technological advancement with the practical needs and resource constraints of end users.
Innovative Synthesis Methods and Technological Advances
The year 2025 marks a pivotal period for double-bond linkage polymer analysis, as the synthesis and characterization of such polymers are at the forefront of both academic and industrial innovation. Double bonds within polymer backbones enable unique properties such as tunable conductivity, enhanced chemical reactivity, and potential for post-polymerization modifications. Recent advances in controlled polymerization techniques, including ring-opening metathesis polymerization (ROMP) and reversible addition–fragmentation chain-transfer (RAFT) polymerization, have enabled the precise incorporation and analysis of double bonds in polymer structures. Companies such as Evonik Industries and Dow are actively developing new monomers and catalysts that facilitate these processes, demonstrating industry commitment to innovation in this area.
Analytical methods for characterizing double-bond linkages have also advanced significantly. High-resolution nuclear magnetic resonance (NMR) spectroscopy and Fourier-transform infrared (FTIR) spectroscopy are now routinely employed to elucidate the configuration and distribution of double bonds within polymer chains. Instrument manufacturers like Bruker and Thermo Fisher Scientific have expanded their instrumentation offerings to support the growing needs of polymer chemists, focusing on sensitivity and throughput improvements tailored to complex polymer matrices.
On the computational front, machine learning and artificial intelligence models are being increasingly leveraged to predict the reactivity and physical properties of double-bond-rich polymers. This trend is supported by companies such as BASF, which has publicly emphasized digitalization and data-driven approaches in polymer R&D pipelines. These computational techniques are particularly valuable in screening candidate monomers and reaction conditions, dramatically accelerating the development cycle.
Looking forward, the next several years are expected to bring further integration of in situ and real-time analytical technologies, such as Raman spectroscopy and mass spectrometry, into polymer synthesis workflows. These technologies, spearheaded by firms like Agilent Technologies, will allow for continuous monitoring of double-bond incorporation, enabling immediate process adjustments and enhanced product consistency. Additionally, sustainability considerations are driving the development of bio-based double-bond monomers and green chemistry approaches, as seen in initiatives from Covestro and SABIC.
In summary, the landscape of double-bond linkage polymer analysis in 2025 is defined by rapid technological progress in synthesis, characterization, and computational prediction. The convergence of these innovations is poised to unlock new classes of functional polymers with bespoke properties, supporting applications in electronics, coatings, and sustainable materials.
Competitive Landscape: Leading Players and Strategic Initiatives
The competitive landscape for double-bond linkage polymer analysis in 2025 is characterized by the active engagement of leading chemical and analytical instrumentation companies, intensified research collaborations, and the integration of advanced analytical technologies. The demand for precise characterization of double-bond linkages in polymers—crucial for performance tuning in sectors such as automotive, electronics, and medical devices—continues to drive innovation and competition.
Major players like BASF, Dow, and SABIC maintain significant R&D investments in developing and producing high-performance polymers with tailored double-bond architectures. These companies are increasingly leveraging advanced spectroscopic and chromatographic techniques to ensure precise analysis of double-bond content and distribution, supporting the design of polymers with specific mechanical, chemical, and thermal properties.
Instrumentation manufacturers such as Bruker and Agilent Technologies are at the forefront of supplying the analytical tools critical for double-bond linkage polymer analysis. Recent product launches and upgrades in nuclear magnetic resonance (NMR), Fourier-transform infrared (FTIR) spectroscopy, and mass spectrometry (MS) have improved sensitivity, throughput, and automation features. These advancements enable faster and more reliable detection of structural motifs in complex polymer matrices, a key competitive differentiator for both polymer producers and analytical labs.
Collaborative research initiatives and open innovation platforms are increasingly shaping the landscape. Companies such as Evonik Industries and Solvay have announced collaborations with academic institutions and technology startups to access novel analysis methods, incorporate artificial intelligence in data interpretation, and accelerate the commercialization of next-generation polymers. These partnerships are expected to yield more rapid and cost-effective double-bond analysis methods, benefiting downstream industries.
Looking ahead, the competitive environment is likely to intensify as sustainability pressures and regulatory requirements push for greener polymers with well-characterized double-bond linkages. Leading players are anticipated to invest further in digitalization and automation of analytical workflows, while mergers, acquisitions, and strategic alliances may increase as companies seek to expand their capabilities and global reach. The ability to offer integrated analysis solutions and support rapid material innovation will be a key factor distinguishing market leaders in the coming years.
End-Use Industry Applications: Automotive, Aerospace, Electronics, and Beyond
Double-bond linkage polymers, notably those containing carbon–carbon double bonds (e.g., polybutadiene, polychloroprene, and certain grades of EPDM and SBR), play a pivotal role across a spectrum of end-use industries. Their unique molecular structure offers tunable elasticity, chemical resistance, and processability, making them integral to the performance demands of sectors such as automotive, aerospace, and electronics.
In the automotive industry, double-bond linkage polymers are foundational to tire manufacturing, as well as seals, hoses, and vibration-damping components. The sector’s continued focus in 2025 on electric vehicle (EV) advancement and fuel efficiency is spurring demand for lightweight, durable materials. For instance, high-performance synthetic rubbers—predominantly based on double-bond linkages—are seeing increased adoption for low rolling resistance tires, which contribute directly to vehicle energy efficiency and reduced emissions. Leading manufacturers such as LANXESS and SIBUR are investing in process innovations and new polymer grades aimed at enhancing properties like heat aging resistance and dynamic performance to meet these evolving requirements.
The aerospace sector, with its stringent standards for material reliability under harsh conditions, leverages double-bond linkage polymers in sealing systems, fuel hoses, and vibration isolators. These polymers’ ability to withstand ozone, high temperatures, and aggressive chemicals is critical for flight safety and durability. Aerospace suppliers and OEMs, including Honeywell International, continue to specify high-performance elastomeric compounds, with current research focusing on increasing the service life and reducing maintenance intervals of key polymer-based components.
Within electronics, the miniaturization trend and increasing operating temperatures in devices are driving the use of double-bond linkage polymers in insulating materials, flexible connectors, and encapsulants. These polymers offer customizable dielectric properties and resistance to thermal degradation, critical for reliability in compact, high-performance electronics. Companies like Dow are advancing material formulations to address demands for higher purity, flexibility, and long-term stability in semiconductor and consumer electronics applications.
Beyond these core industries, double-bond linkage polymers are also being deployed in construction (sealants, waterproofing membranes), healthcare (medical tubing, seals), and renewable energy systems (cable insulation, protective films). The next few years are expected to see further specialization of polymer grades tailored for emerging requirements, such as improved recyclability, lower environmental impact, and compatibility with advanced manufacturing processes (e.g., additive manufacturing). As regulatory and sustainability pressures mount, industry leaders are poised to accelerate R&D and strategic collaborations to expand the performance envelope and application reach of double-bond linkage polymers.
Regional Analysis: Growth Hotspots and Emerging Markets
The regional landscape for double-bond linkage polymer materials—such as polybutadiene, polyisoprene, and other diene-based polymers—is evolving rapidly in 2025, shaped by industrialization, technological upgrades, and sustainability initiatives. Asia-Pacific remains the undisputed growth engine, with China, India, and Southeast Asian economies leading demand due to robust automotive, tire, and construction sectors. Major manufacturers have expanded production capacities and R&D hubs in this region, leveraging local talent and proximity to downstream users. SIBUR, a key global producer, continues to enhance its footprint in Asia, aligning with the region’s push for high-performance elastomers and specialty polymers.
Europe is emerging as a critical innovation center, driven by sustainability mandates and a transition toward circular materials. The European Union’s Green Deal and push for advanced recycling are fostering investment into bio-based and recyclable double-bond linkage polymers. Companies like LANXESS are investing in sustainable product lines and collaborations with local universities to accelerate commercialization of environmentally friendly alternatives. The region is also witnessing increased adoption in niche applications such as medical devices and high-performance adhesives.
In North America, the United States maintains steady demand, especially in automotive, packaging, and electronics. Shale gas feedstock advantages continue to support competitive production of synthetic rubbers and elastomers. However, supply chain volatility and labor shortages are prompting companies like ExxonMobil to adopt digitalization and automation in polymer production. North American research organizations and manufacturers are actively developing new double-bond linkage polymer grades with enhanced reactivity and durability, targeting both traditional and emerging sectors.
Emerging markets in Latin America and Africa are displaying gradual growth, propelled by infrastructure expansion and rising consumer goods production. Local investments and technology transfers from global leaders are facilitating capacity upgrades, with Brazil and South Africa being notable hotspots. The Middle East, leveraging its petrochemical base, is also expanding participation in double-bond linkage polymer production, supported by initiatives from players such as SABIC.
Looking ahead, regional growth hotspots will continue to shift as manufacturers respond to regulatory changes, supply risks, and the imperative for sustainability. Asia-Pacific’s dominance is forecast to persist, but Europe’s role in green polymer innovation and North America’s focus on operational efficiency will shape the market’s next phase. Emerging economies, meanwhile, are poised to benefit from increased technology adoption and foreign direct investment, expanding their influence on the global stage.
Sustainability and Regulatory Trends Impacting Polymer Development
The landscape of double-bond linkage polymer development is increasingly shaped by a convergence of sustainability imperatives and evolving regulatory frameworks. In 2025, regulatory agencies worldwide are intensifying their scrutiny of polymer chemistries, particularly those with environmental persistence or potential toxicity, prompting a shift in research and industrial strategy toward greener alternatives and safer-by-design polymers. Double-bond linkages, such as those found in polyolefins and unsaturated polyester resins, are at the forefront of this transformation due to their ubiquity and functional tunability.
The European Union’s implementation of the Chemicals Strategy for Sustainability (CSS) and the ongoing expansion of the REACH regulation are directly impacting the synthesis and application of double-bond linkage polymers. New restrictions on monomers and additives deemed hazardous—such as certain phthalates and bisphenol derivatives—are driving polymer manufacturers to innovate with safer double-bond-containing monomers or adopt bio-based feedstocks. For instance, industry leaders like Covestro and BASF have accelerated their efforts to develop bio-based and recyclable alternatives that leverage double-bond chemistry for improved end-of-life options and reduced carbon footprint.
A notable trend is the emergence of advanced polymerization techniques—such as reversible addition–fragmentation chain-transfer (RAFT) and atom transfer radical polymerization (ATRP)—which enable precise control over double-bond incorporation and facilitate recyclability or depolymerization. This is particularly relevant as regulatory pressures mount to design polymers with circularity in mind. The deployment of these advanced methods is evident in product lines focused on high-performance and specialty applications, as seen in the portfolios of Evonik Industries and Dow.
Globally, the United States Environmental Protection Agency (EPA) is also revising its approach to polymer risk evaluation, emphasizing data transparency and lifecycle analysis. This is anticipated to affect the approval and market introduction of new double-bond linkage polymers, particularly in sectors such as packaging, automotive, and construction. Manufacturers are responding by investing in robust analytical capabilities for traceability and compliance, as well as lifecycle assessment tools that can quantify the environmental impacts of double-bond-containing polymers from cradle to grave.
Looking ahead, the next few years will likely see a rapid uptake of sustainable double-bond linkage polymers, supported by industry-wide collaborations and public-private partnerships. Companies are expected to increase disclosures regarding polymer compositions, recyclability, and biobased content, aligning with voluntary sustainability standards and mandatory regulations. Ultimately, the dual influence of sustainability and regulation is acting as a catalyst for innovation, pushing the sector toward more circular, safe, and environmentally resilient double-bond polymer solutions.
Investment Opportunities and M&A Activity Forecast (2025–2030)
The landscape for investment opportunities and mergers and acquisitions (M&A) within the double-bond linkage polymer segment is poised for notable evolution between 2025 and 2030. The sector, encompassing polymers such as polybutadiene, polydienes, and advanced copolymers featuring double-bond backbones, is drawing increased attention due to its role in high-performance elastomers, specialty plastics, and sustainable material solutions.
Key industry players are ramping up efforts to expand capacity and innovate product portfolios, with capital expenditures and strategic acquisitions anticipated to intensify. For example, LANXESS and SIBUR have both signaled ongoing interest in expanding synthetic rubber and polybutadiene production, driven by demand from tire, automotive, and construction sectors. These trends are expected to persist as the electrification of vehicles and regulatory pressure on material sustainability drive the adoption of new polymer chemistries featuring double-bond linkages.
On the technology front, investments are increasingly flowing into R&D for double-bond linkage polymers with enhanced recyclability and durability. SABIC and Dow are actively developing advanced copolymers and elastomers that integrate renewable feedstocks and offer improved environmental footprints, suggesting a competitive race for next-generation materials. These innovation-driven strategies are likely to accelerate M&A activity as companies seek to acquire specialized expertise and proprietary technologies.
Additionally, the growing demand for high-performance sealants, adhesives, and coatings—especially in sectors such as renewable energy and electronics—will spur further consolidation. Companies with strong intellectual property positions or established production capabilities in double-bond linkage polymers are expected to become attractive acquisition targets. For example, Sinopec continues to strengthen its synthetic polymer portfolio, indicating a preference for vertical integration and global market expansion.
Looking ahead to 2030, the sector is likely to see increased cross-border M&A activity, particularly as Asian manufacturers expand their global footprint and Western companies seek access to innovative materials and cost-effective production. Strategic joint ventures and alliances, especially for circular economy initiatives and advanced polymer recycling, are also anticipated.
In summary, the 2025–2030 outlook for investment and M&A in double-bond linkage polymers is robust, underpinned by industrial demand, sustainability mandates, and rapid technological progress. Stakeholders should monitor the activities of major producers and innovators such as LANXESS, SIBUR, SABIC, Dow, and Sinopec, as these entities are likely to shape the competitive landscape through both organic growth and strategic transactions.
Challenges: Scalability, Cost, and Performance Barriers
The analysis and industrial adoption of double-bond linkage polymers face a complex set of challenges related to scalability, cost, and performance—factors that continue to dominate the sector in 2025 and are expected to shape its trajectory over the next several years. Double-bond linkages, such as those found in polyenes, polyacetylene, and many advanced specialty polymers, offer unique properties but also introduce significant obstacles to mass production and widespread application.
Scalability remains a primary concern. Many double-bond linkage polymers require precise control over reaction environments, including temperature, pressure, and catalyst selection. This level of control is more manageable at laboratory scale but becomes exponentially more challenging in an industrial context. For example, the synthesis of conjugated polymers like polythiophenes and poly(p-phenylene vinylene) demands stringent conditions to avoid defects that compromise material properties. Companies such as BASF and Dow are actively developing process intensification techniques and improved catalyst systems to address these issues, but high-throughput, reproducible production lines for these polymers are still in the early stages of commercial deployment.
Cost is intricately tied to scalability and remains a significant barrier. The need for high-purity monomers, specialized catalysts, and inert atmosphere processing drives up raw material and operational expenditures. The current price volatility of feedstocks—such as acetylene and substituted aromatic compounds—further complicates budgeting for manufacturers. Despite incremental improvements, companies like SABIC continue to note that the economic feasibility of double-bond linkage polymers, particularly for use in mainstream applications like packaging or automotive, is not yet competitive with established alternatives (e.g., polyethylene or polypropylene).
Performance barriers are evident in both the intrinsic properties of double-bond linkage polymers and their long-term durability. While these materials often provide superior electronic or optical characteristics, they can suffer from environmental instability—such as oxidation or UV degradation—owing to the reactive nature of double bonds. Manufacturers, including Solvay, are currently researching advanced stabilization strategies and copolymerization techniques to enhance resistance to environmental factors. Nevertheless, balancing high performance with longevity and cost-effectiveness is an ongoing challenge.
Looking ahead, the sector is expected to see incremental advances rather than disruptive breakthroughs through 2025 and beyond. Continued R&D investments by major chemical producers and collaborative efforts between academia and industry are likely to yield gradual progress in process efficiency, feedstock flexibility, and material robustness. However, unless transformative innovations in synthesis or stabilization emerge, double-bond linkage polymers will likely remain niche materials reserved for high-value, specialized applications in the near term.
Future Outlook: Next-Generation Double-Bond Linkage Polymers and Market Forecasts Through 2030
The landscape of double-bond linkage polymer analysis is poised for significant evolution through 2030, as both technological advancements and market forces converge to accelerate innovation. Double-bond linkage polymers—characterized by their unsaturated carbon–carbon double bonds within the main chain or side groups—are critical for a range of high-performance applications, including advanced elastomers, specialty coatings, and next-generation electronic materials.
The next several years are expected to witness breakthroughs in the precision synthesis of these polymers, driven by rising demand for tailored mechanical, electrical, and chemical properties. Major chemical producers such as BASF and Dow are investing in R&D aimed at developing novel catalysts and process technologies that enable controlled incorporation of double bonds, enhancing polymer functionality and recyclability. For example, ongoing research into metathesis polymerization and living radical polymerization is enabling the design of polymers with tunable cross-linking density, molecular weights, and degradation profiles, which are increasingly important for sustainability and end-of-life management.
From a market perspective, the coming years are expected to see robust growth in sectors leveraging double-bond linkage polymers. The tire and automotive industries, where double-bond linkages underpin the performance of synthetic rubbers, are projected to benefit from the global shift toward electric vehicles and lightweight materials. Companies such as SABIC and Arkema are expanding their polymer portfolios to meet the requirements for enhanced durability, flexibility, and chemical resistance in transportation and infrastructure.
Additionally, the electronics industry is anticipated to increase its adoption of double-bond-rich polymers for flexible displays, semiconductors, and encapsulation materials, spurred by the miniaturization and flexibility demands in consumer electronics. The medical device sector is also exploring these polymers for biocompatible and drug-eluting products, supported by the material’s customizable surface and degradation features.
Looking ahead to 2030, sustainability will be a defining theme. Industry bodies such as PlasticsEurope are advocating for circular economy models, encouraging the development of double-bond linkage polymers that are either more readily recyclable or biodegradable. Strategic collaborations between material suppliers and end users are expected to accelerate the commercialization of these next-generation polymers, with continuous innovation in analytical techniques—such as advanced spectroscopy and chromatography—further enabling precise characterization and quality control.
In summary, the future of double-bond linkage polymers through 2030 is marked by dynamic growth, technological sophistication, and an increasing alignment with global sustainability imperatives, positioning these materials as central to the next wave of advanced polymer solutions.