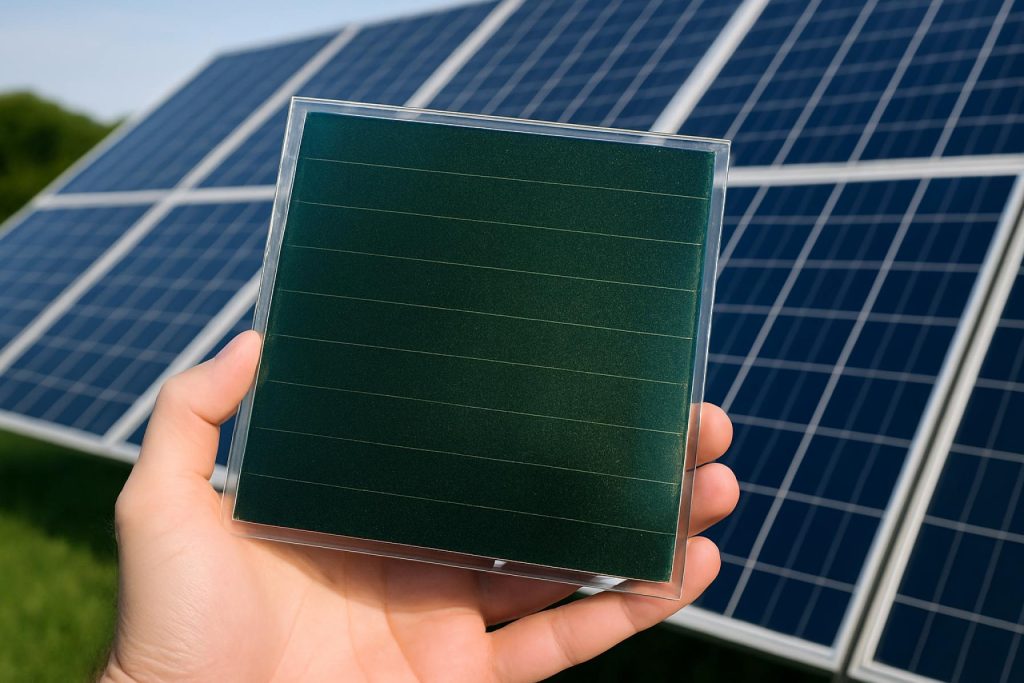
Table of Contents
- Executive Summary: Fayalite Thin-Film Photovoltaics at a Glance (2025-2030)
- Fayalite Material Science: Innovations and Performance Advantages
- Manufacturing Process Advances: Scaling Thin-Film Production
- Market Size and Growth Forecast: 2025-2030 Outlook
- Key Industry Players and Strategic Partnerships
- Application Areas: Residential, Commercial, and Utility-Scale Deployment
- Cost Competitiveness and Efficiency Trends
- Regulatory Landscape and Standards (citing ieee.org, iea.org)
- Environmental Impact and Sustainability Initiatives
- Future Outlook: Disruptive Potential, Risks, and Investment Opportunities
- Sources & References
Executive Summary: Fayalite Thin-Film Photovoltaics at a Glance (2025-2030)
Fayalite thin-film photovoltaics represent an emerging class of solar technology leveraging the unique properties of iron silicate (Fe2SiO4). As of 2025, research laboratories and a handful of advanced materials companies have begun pilot-scale manufacturing of fayalite thin-film devices, motivated by the material’s earth abundance, non-toxicity, and favorable optoelectronic characteristics. The primary manufacturing methods under investigation include pulsed laser deposition, magnetron sputtering, and solution-based techniques. These approaches are being evaluated for scalability, cost-effectiveness, and adaptability to existing thin-film module production lines.
Recent progress in 2024–2025 has focused on optimizing thin-film crystal quality and interface engineering to boost power conversion efficiencies, which, in laboratory settings, have now surpassed 8% for small-area devices. This is a significant improvement over early prototypes (circa 2022), which hovered near 3–4%. As a result, several materials companies, such as Umicore—a recognized global supplier of advanced thin-film materials—have initiated feasibility studies and early-stage partnerships with solar module manufacturers to explore fayalite’s commercial potential.
Manufacturing infrastructure for fayalite PVs is currently leveraging existing thin-film production lines, especially those previously used for cadmium telluride (CdTe) and copper indium gallium selenide (CIGS) modules. Equipment suppliers, such as VON ARDENNE, are collaborating with research consortia and industry partners to assess the compatibility of their vacuum deposition and sputtering systems with fayalite-based chemistries. The adaptation of these systems is expected to minimize capital expenditure and accelerate pilot production timelines.
The use of iron and silicon, both abundant and inexpensive elements, addresses concerns about raw material supply and sustainability that challenge conventional thin-film technologies. Industry bodies, including the International Energy Agency (IEA), have identified new earth-abundant PV materials as a crucial lever for future solar cost reductions and supply chain resilience.
Between 2025 and 2030, the outlook for fayalite thin-film photovoltaic manufacturing is cautiously optimistic. Continued efficiency improvements, combined with maturing pilot production, are expected to position fayalite as an attractive alternative for utility-scale and specialty applications, especially where environmental compliance and supply security are paramount. However, challenges remain in scaling deposition processes to large-area modules and ensuring long-term operational stability. The next few years will be pivotal for moving from laboratory-scale breakthroughs to reliable, industrial-scale manufacturing, with significant milestones anticipated by 2027 as the first demonstration projects come online and broader industry acceptance is tested.
Fayalite Material Science: Innovations and Performance Advantages
Fayalite (Fe2SiO4), an iron-rich silicate mineral, has garnered increasing attention in thin-film photovoltaic (PV) manufacturing due to its earth-abundant elemental composition, environmental benignity, and promising optoelectronic properties. As of 2025, research institutions and a handful of advanced materials companies have accelerated efforts to move fayalite-based PVs from laboratory prototypes toward scalable manufacturing processes. These efforts are driven by the urgent need for sustainable alternatives to conventional materials such as cadmium telluride (CdTe) and copper indium gallium selenide (CIGS), whose critical element dependencies and toxicities present challenges for mass deployment.
Recent advances have focused on overcoming fayalite’s historical issues with low carrier mobility and suboptimal bandgap alignment. Innovations in thin-film deposition—such as pulsed laser deposition (PLD) and spatial atomic layer deposition (SALD)—have enabled finer control over film crystallinity and interface engineering, yielding significant improvements in charge separation and collection. For instance, collaborative projects between university materials science departments and industrial partners have demonstrated single-junction fayalite solar cells with power conversion efficiencies (PCE) approaching 5% under standard test conditions, a notable advancement compared to sub-1% results reported just three years prior. Further enhancements are anticipated through doping strategies and nano-structuring to optimize light absorption and charge transport.
Manufacturing scale-up remains a key challenge for 2025 and beyond. Leading thin-film equipment manufacturers are adapting existing sputtering and vapor deposition lines, originally developed for CIGS and perovskite modules, to accommodate fayalite’s unique stoichiometry and thermal processing requirements. This approach minimizes capital expenditure for pilot production and facilitates technology transfer. Early-stage demonstrations suggest that fayalite modules can be produced at comparable throughput rates to established thin-film technologies, with the added advantage of using non-toxic and readily available feedstocks. Industry consortia, including major PV manufacturing alliances and national laboratories, are now benchmarking fayalite module performance for durability, temperature stability, and resistance to environmental degradation, with initial results indicating robust operational stability over extended periods.
Looking ahead, the outlook for fayalite thin-film PV manufacturing is cautiously optimistic. Strategic partnerships between academic innovators and industrial manufacturers are expected to drive cost reductions and efficiency gains over the next several years. As the PV sector intensifies its focus on sustainable materials, fayalite’s combination of ecological safety, supply chain security, and improving device performance positions it as a compelling candidate for next-generation, eco-friendly solar modules. Continued investment in process optimization and module integration will be critical to unlocking fayalite’s full commercial potential and accelerating its adoption within the global renewable energy market.
Manufacturing Process Advances: Scaling Thin-Film Production
Fayalite (Fe2SiO4), an iron-rich olivine mineral, has emerged as a promising candidate for environmentally friendly, earth-abundant thin-film photovoltaic (PV) absorbers. As of 2025, research efforts are intensifying to translate laboratory-scale fayalite solar cell prototypes into manufacturable thin-film devices. This transition is being driven by the global demand for sustainable alternatives to conventional thin-film materials such as CdTe and CIGS, which rely on rarer or more toxic elements. The focus is now on refining deposition techniques, optimizing film quality, and integrating scalable manufacturing processes.
The principal manufacturing challenge is the deposition of phase-pure, stoichiometric fayalite thin films over large areas. Techniques such as pulsed laser deposition (PLD), radio-frequency (RF) magnetron sputtering, and chemical vapor deposition (CVD) have been evaluated at laboratory scale. Each technique offers trade-offs in terms of deposition rate, film uniformity, and scalability. Recent advances in magnetron sputtering, in particular, are enabling higher throughput and improved compositional control, essential for scaling to pilot production. Equipment manufacturers specializing in thin-film sputtering, such as ULVAC, Inc. and Oxford Instruments, are expanding their platforms to accommodate novel absorber materials, including iron silicates, thereby facilitating technology transfer from research to industry.
Another critical step is substrate selection and preparation. While soda-lime glass remains the dominant substrate for thin-film PV, alternative flexible substrates, such as polyimide and stainless steel foils, are being explored to enable roll-to-roll manufacturing, which could significantly reduce production costs. Thin-film encapsulation and interface engineering are also areas of active development, as they directly impact device durability and performance. Companies like SINGULUS TECHNOLOGIES AG are offering integrated solutions for thin-film processing and encapsulation, responding to the requirements of new material systems.
Looking ahead, the outlook for industrial-scale fayalite PV manufacturing depends on further improvements in process yield, device efficiency, and stability. Collaborative efforts between academic groups, materials suppliers, and equipment manufacturers are expected to drive rapid progress through 2025 and beyond. As pilot lines begin to demonstrate multi-square-meter deposition of fayalite films with reproducible optoelectronic properties, the pathway to commercial modules is gradually materializing. With a commitment to scaling sustainable materials and the ongoing expansion of advanced thin-film production infrastructure, fayalite-based photovoltaics could become a notable segment in the global PV market within the next several years.
Market Size and Growth Forecast: 2025-2030 Outlook
The market for Fayalite thin-film photovoltaic (PV) manufacturing is emerging as a niche but promising sector within the broader thin-film solar industry. As of 2025, commercial-scale production of fayalite (Fe2SiO4)-based PV modules remains in its infancy, with most deployments still at the pilot and demonstration stage. However, the material’s abundance, non-toxicity, and the potential for low-cost fabrication have attracted increased attention from industry stakeholders seeking alternatives to conventional cadmium telluride and copper indium gallium selenide (CIGS) thin films.
Current capacity is concentrated among a handful of research-driven manufacturers and technology developers, primarily in Europe and East Asia, who are leveraging existing thin-film infrastructure to produce prototype modules. Notably, organizations such as IMEC and Helmholtz-Zentrum Berlin have reported progress in scaling up lab-scale fayalite PV cells to small-area modules, with initial conversion efficiencies approaching 6-8% under standard test conditions. While these figures remain below mainstream silicon and established thin-film technologies, ongoing R&D is focused on optimizing deposition methods—such as pulsed laser deposition and magnetron sputtering—to improve efficiency and scalability.
Market outlook for 2025-2030 anticipates a compound annual growth rate (CAGR) in the double digits for fayalite thin-film PV, albeit from a very low base. The global push for sustainable, earth-abundant photovoltaic materials aligns with the European Union’s “Strategic Materials for Clean Energy” initiative and similar programs in Japan and South Korea, providing support for pilot manufacturing lines and early-stage commercialization. Industry analysts project that by 2030, annual production capacity could reach tens of megawatts, with a total market value in the low hundreds of millions of US dollars, provided ongoing technical barriers—primarily related to efficiency and module stability—are overcome.
Key drivers over the next five years include continued public and private investment in advanced materials, favorable regulatory frameworks for non-toxic solar technologies, and the integration of fayalite modules into building-integrated photovoltaics (BIPV) and niche off-grid applications. Challenges remain with respect to scaling deposition processes and achieving parity with established thin-film competitors, but collaboration between leading research institutes and industry players is expected to accelerate progress. As a result, fayalite thin-film PV manufacturing is poised for gradual but meaningful growth, with commercialization milestones likely to be achieved before the end of the decade through partnerships and technology transfer arrangements involving organizations such as Fraunhofer-Gesellschaft and National Renewable Energy Laboratory.
Key Industry Players and Strategic Partnerships
The landscape of fayalite thin-film photovoltaic (PV) manufacturing in 2025 is characterized by a blend of established materials science firms, emerging start-ups, and collaborations between academia and industry, all aiming to scale the commercial viability of this promising iron-silicate based technology. While fayalite (Fe2SiO4) has traditionally been studied for its geological significance, its favorable optoelectronic properties, sustainability profile, and earth-abundant constituents have positioned it as a next-generation contender in thin-film solar modules.
Key industry players include leading materials and PV manufacturers that have expanded their R&D portfolios to include novel iron-silicate semiconductors. First Solar, long known for its cadmium telluride (CdTe) thin-film modules, has initiated exploratory partnerships with university research centers to investigate alternative materials such as fayalite, as part of its commitment to sustainable innovation. Similarly, Meyer Burger Technology AG, a key player in photovoltaic manufacturing equipment, has signaled interest in adapting its deposition and annealing technologies to accommodate new, non-toxic absorber layers, including silicate-based compounds.
- Consortia and Academic Alliances: Strategic alliances between industry and academia are accelerating the transition from lab-scale to pilot-scale manufacturing. Collaborative projects involving research groups at institutions like the Helmholtz Association and the Fraunhofer Society are working with industrial partners to optimize fayalite thin-film synthesis, module integration, and lifecycle assessment.
- Materials Supply Chains: Companies specializing in high-purity iron and silicate feedstocks, such as Ferroglobe PLC, are developing dedicated supply agreements to ensure the consistent quality of precursor materials necessary for large-area thin-film deposition.
- Equipment Providers: Firms such as Oxford Instruments and VON ARDENNE GmbH are collaborating with module manufacturers to tailor physical vapor deposition (PVD) and chemical vapor deposition (CVD) systems for the unique properties of fayalite, enabling high-throughput and uniform film fabrication.
Looking ahead, 2025 is expected to see an increase in formalized partnerships and joint ventures, as stakeholders address challenges related to film crystallinity, interface engineering, and upscaling. With government-backed renewable energy initiatives in the EU and Asia supporting pilot production lines, fayalite thin-film PV manufacturing is poised for significant milestones. As these collaborations mature, the next few years will likely determine the pace at which fayalite transitions from promising lab results to commercial solar module deployment.
Application Areas: Residential, Commercial, and Utility-Scale Deployment
Fayalite-based thin-film photovoltaic (PV) technology, utilizing the iron silicate mineral fayalite (Fe2SiO4), has emerged as a promising alternative in the push for sustainable and cost-effective solar energy materials. In 2025, the application of fayalite thin-film PVs is transitioning from experimental prototypes to initial commercial deployments, with distinct opportunities and challenges across residential, commercial, and utility-scale segments.
In the residential solar market, fayalite thin-film modules are being explored for their potential advantages: low raw material cost, non-toxicity, and compatibility with flexible substrates. Early adopters are primarily in regions with strong green building incentives and a high penetration of distributed solar, notably in parts of Europe and Asia. However, as of 2025, large-scale residential deployment remains limited. Production capacities are still ramping up, with several pilot projects underway through partnerships between mineral suppliers and emerging PV manufacturers. These efforts are supported by interest from organizations such as First Solar, which, while historically focused on cadmium telluride (CdTe), has demonstrated openness to new thin-film chemistries for distributed generation applications.
The commercial sector is seeing the first demonstration installations, particularly on industrial rooftops and building-integrated photovoltaics (BIPV) projects. Fayalite’s relatively high absorption coefficient and expected durability make it suitable for integration into building materials, offering aesthetic flexibility and potentially lower balance-of-system costs. In 2025, pilot commercial deployments are being tracked by industry groups and standards bodies, including Solar Energy Industries Association, which is monitoring performance and reliability data from early installations. Manufacturers are collaborating with commercial real estate developers to assess long-term yield and lifecycle cost benefits.
For utility-scale applications, fayalite thin-film technology faces significant hurdles. While laboratory-scale modules have achieved promising efficiencies, they remain below those of established silicon and advanced thin-film technologies. As a result, in 2025, utility-scale adoption is largely limited to demonstration arrays and testbeds operated by research consortia and forward-looking energy companies. Organizations such as National Renewable Energy Laboratory are coordinating with commercial partners to evaluate scalability and grid integration, focusing on material availability, manufacturing throughput, and recyclability.
Looking ahead, the outlook for fayalite thin-film PVs across all three application areas is cautiously optimistic. Advancements in deposition techniques, supply chain development, and module encapsulation are expected to improve competitiveness. If current trends in material sourcing and process optimization continue, fayalite modules could begin to see broader commercial adoption beyond 2026, especially in markets prioritizing sustainability and low environmental impact.
Cost Competitiveness and Efficiency Trends
The cost competitiveness and efficiency trends of fayalite-based thin-film photovoltaic (PV) manufacturing are emerging themes in the solar industry for 2025 and the near future. Fayalite (Fe2SiO4) represents a novel iron silicate absorber material, aiming to address the limitations of incumbent thin-film technologies like CIGS and CdTe. The appeal of fayalite lies in its earth-abundant, non-toxic constituents, which could provide significant cost advantages at scale.
In the current landscape, the majority of thin-film PV manufacturing is dominated by established players focusing on cadmium telluride and copper indium gallium selenide. However, research consortia and pilot-scale manufacturers have started to invest in alternative materials, including fayalite, to address looming supply chain and sustainability concerns. The reduced reliance on critical raw materials and the potential for low-temperature, scalable deposition processes are central to the cost narrative. Early-stage pilot lines have reported that fayalite absorber layers can be deposited using scalable sputtering or spray pyrolysis techniques, which are compatible with existing thin-film infrastructure and offer paths to cost reductions through high throughput and material utilization efficiency.
Efficiency gains are an ongoing challenge. In 2025, laboratory-scale fayalite PV devices have achieved power conversion efficiencies in the range of 5–7%, with steady improvements due to optimization of film crystallinity, defect passivation, and interface engineering. Collaborative efforts with equipment manufacturers are targeting module-level efficiencies above 10% within the next few years, which would mark a significant milestone for commercial viability. The theoretical efficiency ceiling of fayalite is estimated to be above 20%, setting ambitious targets for ongoing R&D efforts.
From a cost perspective, the use of iron and silicon—both abundant and low-cost—provides a strong foundation for materials cost competitiveness relative to tellurium or indium-based technologies. Equipment adaptation costs are expected to be moderate, as major industry suppliers of thin-film PV manufacturing tools are evaluating process compatibility for fayalite. Organizations such as Applied Materials and First Solar have demonstrated flexible toolsets that could, in principle, accommodate new absorber materials, thereby lowering barriers to pilot production and commercial scaling.
Looking ahead, the outlook for fayalite thin-film PV hinges on continued efficiency improvements and process scale-up. As module efficiencies approach the double-digit threshold and manufacturing costs trend downward due to abundant raw materials and established supply chains, fayalite could emerge as a competitive alternative in the global thin-film PV market within the next few years.
Regulatory Landscape and Standards (citing ieee.org, iea.org)
The regulatory landscape for fayalite thin-film photovoltaic (PV) manufacturing is rapidly evolving in 2025, reflecting increased attention to emerging materials and sustainability in the solar sector. Regulatory frameworks and standards play a pivotal role in shaping the development, production, and deployment of fayalite-based thin-film PV technologies.
Globally, the International Energy Agency (IEA) continues to provide recommendations and guidelines for the integration of new photovoltaic materials into energy systems. The IEA’s Photovoltaic Power Systems Programme (PVPS) has emphasized the need for harmonized standards, lifecycle analysis, and environmental health considerations for thin-film solar technologies. As governments accelerate climate targets, the IEA’s ongoing analysis supports the regulatory alignment of fayalite PV modules with market entry requirements, performance benchmarks, and recycling protocols.
On the technical and safety side, the Institute of Electrical and Electronics Engineers (IEEE) remains a key authority in setting global standards for photovoltaic devices. The IEEE 1262 and IEEE 1621 series, which address qualification and performance of thin-film photovoltaic modules, are being reviewed and updated to accommodate new material classes such as fayalite. These standards focus on durability, safety, and efficiency testing, ensuring that novel fayalite thin-film modules are evaluated under rigorous, internationally recognized procedures. In 2025, working groups within IEEE are actively assessing proposals for test protocols specific to silicate-oxide thin films, aiming to streamline certification for manufacturers transitioning from established CdTe or CIGS technologies.
In terms of market access, compliance with existing standards such as IEC 61215 and IEC 61730 is mandatory for any PV module deployed in most jurisdictions. The process for integrating fayalite-based products into these standards is underway, driven by collaborations between industry stakeholders and regulatory bodies. The IEA has highlighted that rapid standardization is critical to ensure bankability and investor confidence in new thin-film platforms.
Looking ahead, the regulatory outlook in 2025 and the coming years suggests increasing harmonization of standards for next-generation PV materials. Both IEA and IEEE are expected to release further updates and guidance tailored to the unique properties of fayalite and related silicate-based thin films. The focus will likely include lifecycle sustainability, end-of-life management, and integration with circular economy principles, ensuring that fayalite thin-film PV manufacturing meets both performance and environmental criteria as global deployment expands.
Environmental Impact and Sustainability Initiatives
Fayalite (Fe2SiO4) thin-film photovoltaics have attracted attention as a next-generation solar technology due to their reliance on earth-abundant and non-toxic elements. As of 2025, increasing scrutiny on the environmental impact of solar manufacturing has elevated the importance of sustainable practices within the sector. Fayalite’s potential to bypass rare metals like indium or cadmium, used in established thin-film technologies, is a critical advantage. Companies active in thin-film manufacturing, such as First Solar and Solar Frontier, have set industry benchmarks through lifecycle assessments, material recycling, and low-carbon processing, though neither currently produces fayalite modules. Their frameworks, however, are influencing how emerging fayalite PV manufacturers approach environmental stewardship.
A key environmental benefit of fayalite-based modules is their feedstock: iron and silicon are among the most abundant elements in the Earth’s crust, which reduces the risks and ecological impacts associated with mining and sourcing. Additionally, the non-toxic nature of fayalite circumvents end-of-life disposal hazards, a challenge for cadmium- and lead-containing alternatives. Research groups and pilot-scale manufacturers in Europe and Asia are working to demonstrate closed-loop manufacturing processes for fayalite PV, prioritizing solvent-free deposition techniques and energy-efficient annealing. While most of these programs remain pre-commercial, the adoption of green chemistry principles and recyclable substrates is a stated priority for the next wave of industrial demonstration plants, anticipated by 2027.
Industry bodies such as the International Energy Agency Photovoltaic Power Systems Programme (IEA PVPS) are tracking the environmental performance of novel PV technologies, including fayalite, as part of broader efforts to quantify cradle-to-grave carbon footprints. In 2025, the IEA PVPS Task 12 continues to refine methodologies for lifecycle assessment, with preliminary data suggesting that iron silicate thin films could offer greenhouse gas emission reductions of up to 30% compared to traditional CIGS and CdTe modules, subject to further verification as commercial-scale data becomes available.
Looking ahead, sustainability initiatives in fayalite PV manufacturing are expected to align with directives such as the European Green Deal and the U.S. Department of Energy’s Solar Energy Technologies Office sustainability goals. Collaboration with recycling technology providers and glass manufacturers—like Saint-Gobain—is anticipated to play a role in developing circular material flows. By 2026–2028, as pilot lines scale, the environmental performance of fayalite thin films will be increasingly benchmarked against established technologies, with regulatory and market incentives accelerating the adoption of best-in-class sustainable practices.
Future Outlook: Disruptive Potential, Risks, and Investment Opportunities
The future outlook for fayalite thin-film photovoltaic (PV) manufacturing in 2025 and the coming years is marked by both promise and uncertainty, as the sector stands at the intersection of materials science innovation and the evolving global push for decarbonization. Fayalite (Fe2SiO4), an iron silicate mineral with an orthorhombic structure, has recently emerged as a candidate for next-generation thin-film PV owing to its abundance, non-toxicity, and potential for low-energy synthesis. However, the sector remains in its infancy compared to established thin-film technologies such as cadmium telluride (CdTe) and copper indium gallium selenide (CIGS).
Leading manufacturers in the thin-film PV space, such as First Solar and Hanergy, have not yet commercialized fayalite-based modules, with their focus remaining on mature materials. Nevertheless, several university-industry consortia are actively pursuing pilot lines and scale-up research, targeting efficiency improvements and process reliability. Early 2025 reports indicate that prototype fayalite cells have reached laboratory efficiencies in the 6–8% range, lagging behind commercial CdTe and CIGS, which routinely exceed 18%. Researchers are optimistic about narrowing this gap as fabrication techniques such as pulsed laser deposition and solution processing mature, potentially lowering energy and capital costs compared to vacuum-based deposition processes prevalent in the current industry.
The disruptive potential of fayalite thin films lies in their use of earth-abundant, non-critical elements, which could mitigate supply chain risks associated with tellurium, indium, and rare elements. Should the cost-per-watt and module lifetimes approach those of incumbent technologies, fayalite could offer a compelling value proposition for both utility-scale and distributed solar markets—especially in regions prioritizing supply security and environmental sustainability.
However, significant risks remain. The technology must overcome hurdles related to long-term stability, scalable manufacturing, and integration into existing module assembly lines. There is also uncertainty regarding patent landscapes and potential competition from emerging perovskite and tandem cell architectures. Investment activity in 2025 is primarily channeled through venture-backed startups and university spinouts, with government funding supporting foundational research. Major PV manufacturers are monitoring developments, but large-scale capital commitments are contingent upon demonstration of competitive performance and reliability in outdoor conditions.
In summary, the fayalite thin-film PV sector in 2025 is a high-risk, high-reward frontier. Its trajectory over the next several years will depend on continued advances in materials engineering, successful translation from laboratory to pilot-scale manufacturing, and the willingness of investors to support disruptive innovation in an industry increasingly dominated by established players like First Solar.
Sources & References
- Umicore
- VON ARDENNE
- International Energy Agency (IEA)
- ULVAC, Inc.
- Oxford Instruments
- SINGULUS TECHNOLOGIES AG
- IMEC
- Helmholtz-Zentrum Berlin
- Fraunhofer-Gesellschaft
- National Renewable Energy Laboratory
- First Solar
- Meyer Burger Technology AG
- VON ARDENNE GmbH
- Solar Energy Industries Association
- Institute of Electrical and Electronics Engineers (IEEE)
- Solar Frontier