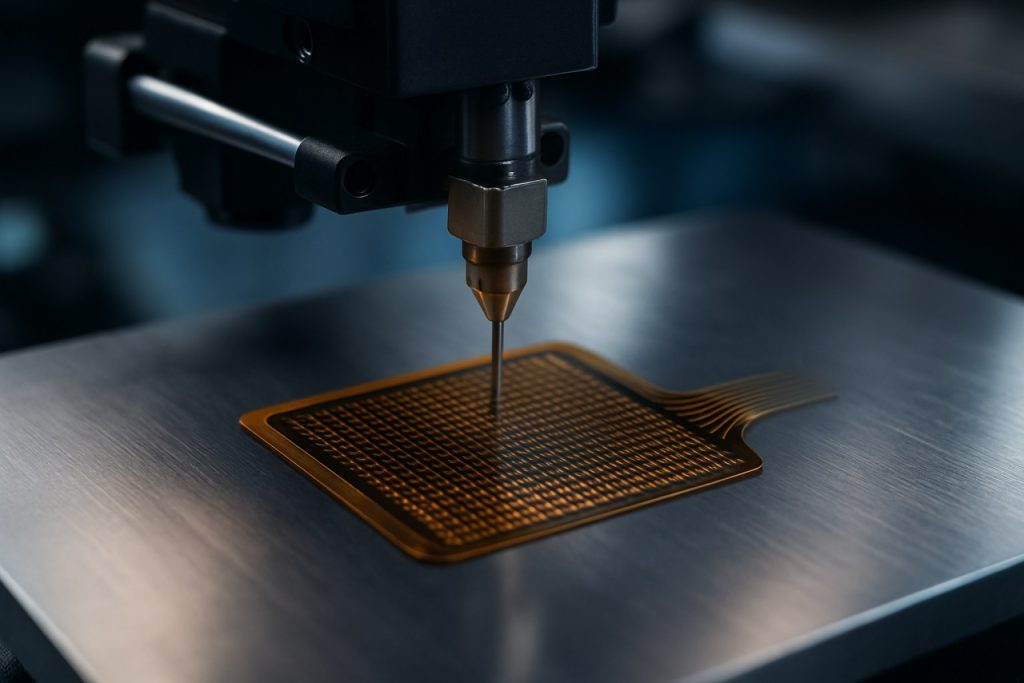
High-Density Electrode Array Manufacturing in 2025: Unleashing Precision, Miniaturization, and Market Momentum. Explore How Advanced Fabrication and Demand for Neural Interfaces Are Shaping the Industry’s Future.
- Executive Summary: 2025 Market Landscape and Key Drivers
- Technology Overview: High-Density Electrode Array Fundamentals
- Manufacturing Innovations: Materials, Processes, and Automation
- Key Players and Industry Ecosystem (e.g., blackrockneurotech.com, neuroloop.de, imec-int.com)
- Emerging Applications: Neurotechnology, Bioelectronics, and Beyond
- Market Forecasts: Revenue, Volume, and Regional Growth (2025–2030)
- Supply Chain and Scalability Challenges
- Regulatory and Standards Landscape (e.g., ieee.org, fda.gov)
- Investment Trends and Strategic Partnerships
- Future Outlook: Disruptive Technologies and Long-Term Opportunities
- Sources & References
Executive Summary: 2025 Market Landscape and Key Drivers
The high-density electrode array manufacturing sector is poised for significant growth and transformation in 2025, driven by rapid advancements in neurotechnology, medical diagnostics, and brain-computer interface (BCI) applications. The demand for higher channel counts, miniaturization, and biocompatibility is pushing manufacturers to innovate in both materials and fabrication processes. Key industry players are scaling up production capabilities to meet the needs of research institutions, medical device companies, and emerging neuroprosthetic applications.
In 2025, the market is characterized by the increasing adoption of advanced microfabrication techniques such as photolithography, laser micromachining, and thin-film deposition. These methods enable the production of electrode arrays with channel counts exceeding 1,000, supporting high-resolution neural recording and stimulation. Companies like Blackrock Neurotech and NeuroNexus Technologies are recognized for their leadership in developing and supplying high-density arrays for both research and clinical use. Blackrock Neurotech continues to expand its Utah Array platform, while NeuroNexus Technologies is advancing customizable silicon-based probes for diverse neuroscience applications.
Material innovation remains a key driver, with a focus on flexible substrates such as polyimide and parylene to improve chronic implantation outcomes and reduce tissue response. Neuralink is notable for its proprietary flexible electrode threads and automated robotic insertion systems, aiming to scale manufacturing for human clinical trials and eventual commercial deployment. Meanwhile, Microprobes for Life Science and Ad-Tech Medical Instrument Corporation are expanding their portfolios to include higher-density grid and depth arrays for both research and clinical monitoring.
The sector is also witnessing increased collaboration between device manufacturers and semiconductor foundries to leverage advanced MEMS (Micro-Electro-Mechanical Systems) processes. This partnership is expected to further reduce feature sizes and enable mass production of complex array geometries. Regulatory pathways are evolving, with agencies such as the U.S. FDA providing clearer guidance for neural interface devices, which is anticipated to accelerate product development and market entry.
Looking ahead, the next few years will likely see further integration of wireless data transmission, on-array signal processing, and closed-loop feedback systems. The convergence of these technologies is expected to expand the application space for high-density electrode arrays, from fundamental neuroscience to next-generation neuroprosthetics and adaptive BCIs. As manufacturing capabilities mature, the sector is set to play a pivotal role in the broader neurotechnology and medical device landscape.
Technology Overview: High-Density Electrode Array Fundamentals
High-density electrode arrays (HDEAs) are at the forefront of neural interface technology, enabling precise recording and stimulation of neural activity across large populations of neurons. The manufacturing of these arrays in 2025 is characterized by rapid advancements in microfabrication, materials science, and scalable production techniques, driven by the demands of both clinical and research applications.
The core of HDEA manufacturing lies in the integration of hundreds to thousands of microelectrodes onto flexible or rigid substrates, often using advanced photolithography, thin-film deposition, and etching processes. Silicon remains a dominant substrate due to its compatibility with established semiconductor fabrication methods, but there is a growing shift toward flexible polymers such as polyimide and parylene-C, which offer improved biocompatibility and conformability to neural tissue. Companies like Blackrock Neurotech and NeuroNexus Technologies are recognized for their silicon-based and polymer-based array platforms, respectively, each leveraging proprietary microfabrication workflows to achieve high channel counts and fine electrode pitches.
Recent years have seen the emergence of novel manufacturing approaches, such as laser micromachining and additive manufacturing, which allow for rapid prototyping and customization of electrode geometries. For example, Neuralink has publicized the use of automated robotic assembly and ultra-fine flexible threads, pushing the boundaries of electrode density and minimally invasive implantation. Meanwhile, Blackrock Neurotech continues to refine its Utah Array platform, focusing on increasing channel density and long-term reliability through improved materials and encapsulation techniques.
A key challenge in HDEA manufacturing is ensuring consistent quality and yield at scale. This has led to the adoption of in-line inspection systems and advanced packaging solutions, such as hermetic sealing and biocompatible coatings, to enhance device longevity and safety. Industry leaders are also investing in scalable cleanroom facilities and automation to meet the growing demand from both academic and commercial partners.
Looking ahead, the next few years are expected to bring further miniaturization, higher electrode counts, and integration with on-chip signal processing. Collaborative efforts between device manufacturers, materials suppliers, and research institutions are likely to accelerate the translation of HDEAs from laboratory prototypes to clinically approved products. As regulatory pathways become clearer and manufacturing technologies mature, high-density electrode arrays are poised to play a pivotal role in next-generation brain-computer interfaces and neuroprosthetic systems.
Manufacturing Innovations: Materials, Processes, and Automation
The manufacturing of high-density electrode arrays is undergoing rapid transformation in 2025, driven by advances in materials science, microfabrication processes, and automation. These arrays, essential for applications in neuroscience, brain-computer interfaces, and advanced medical diagnostics, require precise engineering to achieve high channel counts, biocompatibility, and long-term stability.
A key trend is the adoption of novel materials that enhance both performance and manufacturability. Polyimide and parylene C remain popular substrate choices due to their flexibility and biocompatibility, but there is growing interest in silicon carbide and graphene for their superior electrical properties and mechanical robustness. Companies such as Blackrock Neurotech and NeuroNexus Technologies are actively developing arrays with these advanced materials, aiming to improve signal fidelity and device longevity.
Microfabrication techniques are also evolving. Photolithography and thin-film deposition remain foundational, but innovations in laser micromachining and deep reactive ion etching (DRIE) are enabling finer feature sizes and higher electrode densities. Blackrock Neurotech has reported progress in scaling up Utah Array production, leveraging automated wafer-level processes to increase throughput and consistency. Meanwhile, NeuroNexus Technologies continues to refine its planar silicon probe manufacturing, integrating automated inspection and packaging steps to reduce defects and improve yield.
Automation is a central focus for 2025 and beyond. The integration of robotics and machine vision into assembly lines is reducing manual labor and variability, particularly in the delicate steps of electrode placement and bonding. Neuralink is notable for its investment in fully automated assembly systems, which are designed to handle the ultra-fine wires and high channel counts of their flexible arrays. This approach not only accelerates production but also supports the scalability required for future clinical and commercial deployment.
Looking ahead, the sector anticipates further convergence of material innovation and process automation. The next few years are expected to see the introduction of hybrid arrays combining multiple materials and electrode types, as well as the adoption of additive manufacturing techniques for custom geometries. As regulatory pathways for implantable devices become clearer, manufacturers are positioning themselves to meet rising demand from both research and clinical markets, with a strong emphasis on quality control and reproducibility.
Key Players and Industry Ecosystem (e.g., blackrockneurotech.com, neuroloop.de, imec-int.com)
The high-density electrode array manufacturing sector is characterized by a dynamic ecosystem of specialized companies, research institutes, and technology suppliers, each contributing to the rapid evolution of neural interface technologies. As of 2025, the industry is witnessing significant advancements in both the scale and sophistication of electrode arrays, driven by demand from neuroscience research, brain-computer interface (BCI) development, and clinical neuroprosthetics.
A leading player in this space is Blackrock Neurotech, renowned for its Utah Array, which remains a gold standard for intracortical recording and stimulation. Blackrock Neurotech continues to innovate in electrode miniaturization and array density, supporting both academic and commercial BCI initiatives. Their manufacturing processes emphasize biocompatibility and long-term stability, critical for chronic implantation.
In Europe, neuroloop is advancing flexible, high-density cuff electrodes for peripheral nerve applications. Their proprietary manufacturing techniques enable the integration of hundreds of contacts on soft, conformable substrates, addressing the need for selective nerve stimulation in medical devices. Neuroloop’s close collaboration with clinical partners accelerates the translation of these arrays into therapeutic products.
On the research and foundry side, imec stands out as a global leader in microfabrication and nanoelectronics. Imec’s open innovation model allows startups and established companies to leverage its advanced cleanroom facilities for prototyping and scaling up high-density electrode arrays. Their recent work includes CMOS-based neural probes with thousands of recording sites, pushing the boundaries of spatial resolution and data throughput.
Other notable contributors include NeuroNexus, which supplies customizable silicon-based arrays for both research and clinical use, and Microprobes for Life Science, specializing in precision manufacturing of microwire and silicon arrays. These companies are integral to the supply chain, offering both catalog products and bespoke solutions tailored to specific experimental or therapeutic needs.
The industry ecosystem is further supported by collaborations with academic institutions and medical device manufacturers, fostering rapid iteration and validation of new designs. As regulatory pathways for implantable neurotechnologies become clearer, the next few years are expected to see increased investment in automated, scalable manufacturing processes, as well as the integration of novel materials such as graphene and flexible polymers.
Looking ahead, the convergence of microfabrication, materials science, and data analytics is poised to enable even higher-density arrays with improved longevity and safety profiles. This will expand the clinical and research applications of neural interfaces, solidifying the role of these key players in shaping the future of neurotechnology.
Emerging Applications: Neurotechnology, Bioelectronics, and Beyond
High-density electrode array manufacturing is undergoing rapid transformation in 2025, driven by surging demand from neurotechnology, bioelectronics, and adjacent fields. The push for higher channel counts, miniaturization, and biocompatibility is shaping both the technical landscape and the competitive dynamics among leading manufacturers.
In neurotechnology, high-density arrays are central to next-generation brain-computer interfaces (BCIs), neural recording, and stimulation devices. Companies such as Blackrock Neurotech and NeuroNexus Technologies are at the forefront, offering silicon- and polymer-based arrays with hundreds to thousands of channels. These arrays enable high-resolution mapping of neural activity, essential for both clinical and research applications. Blackrock Neurotech continues to refine its Utah Array platform, focusing on increased channel density and improved long-term stability, while NeuroNexus Technologies leverages microfabrication to produce customizable, flexible probes for both acute and chronic implantation.
The manufacturing process for these arrays increasingly relies on advanced microelectromechanical systems (MEMS) techniques, thin-film deposition, and photolithography. Micron Technology, a global leader in semiconductor manufacturing, is expanding its capabilities in microfabrication, which is directly relevant to the production of high-density electrode arrays. The integration of semiconductor-grade cleanroom processes is enabling finer feature sizes and higher yields, critical for scaling up production to meet growing demand.
In bioelectronics, companies like Neuralink are pushing the boundaries with flexible, thread-like electrode arrays designed for minimally invasive brain implantation. Their manufacturing approach combines automated precision assembly with biocompatible materials, aiming for both high channel counts and long-term safety. The company’s public demonstrations and regulatory filings indicate ongoing progress toward scalable, high-throughput manufacturing lines.
Looking ahead, the next few years are expected to see further convergence between semiconductor manufacturing and bioelectronic device fabrication. Industry leaders are investing in automation, quality control, and new materials such as graphene and conductive polymers to enhance performance and manufacturability. The emergence of contract manufacturers specializing in medical microdevices, such as Cirtec Medical, is also accelerating time-to-market for startups and established firms alike.
Overall, the outlook for high-density electrode array manufacturing in 2025 and beyond is marked by rapid innovation, increased production capacity, and a broadening range of applications—from advanced BCIs to wearable bioelectronic sensors—driven by the combined efforts of established players and new entrants in the field.
Market Forecasts: Revenue, Volume, and Regional Growth (2025–2030)
The high-density electrode array manufacturing sector is poised for robust growth between 2025 and 2030, driven by escalating demand in neuroscience research, brain-computer interfaces (BCIs), and advanced medical diagnostics. The market is expected to witness a compound annual growth rate (CAGR) in the high single digits, with global revenues projected to surpass several hundred million USD by 2030. This expansion is underpinned by increasing investments in neurotechnology, miniaturization of electronics, and the proliferation of applications in both clinical and research settings.
North America is anticipated to maintain its leadership position, owing to the presence of major manufacturers and a strong ecosystem of academic and medical research institutions. Companies such as Blackrock Neurotech and NeuroNexus Technologies are at the forefront, supplying high-density arrays for both preclinical and clinical use. The United States, in particular, benefits from significant funding initiatives and a favorable regulatory environment, which are expected to accelerate the adoption of next-generation electrode arrays.
Europe is projected to follow closely, with countries like Germany, Switzerland, and the United Kingdom investing heavily in neurotechnology infrastructure. Firms such as CorTec and TMC are expanding their manufacturing capabilities to meet growing demand from both research and medical device sectors. The European market is also buoyed by collaborative projects and public-private partnerships aimed at advancing brain research and neuroprosthetics.
The Asia-Pacific region is expected to register the fastest growth rate, propelled by increasing healthcare expenditures, expanding neuroscience research, and the emergence of local manufacturers. Countries like China, Japan, and South Korea are investing in domestic production capabilities and fostering innovation through government-backed initiatives. While the region currently lags behind North America and Europe in terms of market share, its rapid development is likely to narrow the gap by 2030.
In terms of volume, the number of high-density electrode arrays shipped annually is forecast to rise significantly, with research applications accounting for the majority of units, followed by clinical and commercial BCI deployments. The trend toward higher channel counts and flexible, biocompatible materials is expected to further stimulate demand, as end-users seek improved spatial resolution and long-term reliability.
Overall, the outlook for high-density electrode array manufacturing is highly positive, with technological advancements, expanding applications, and regional investments converging to drive sustained market growth through 2030.
Supply Chain and Scalability Challenges
The manufacturing of high-density electrode arrays—critical components for advanced neurotechnology, brain-computer interfaces, and next-generation medical devices—faces significant supply chain and scalability challenges as of 2025. The sector is characterized by rapid innovation, but also by bottlenecks in materials sourcing, precision fabrication, and quality assurance, all of which are magnified as demand grows for higher channel counts and miniaturized architectures.
A primary challenge lies in the procurement of ultra-pure, biocompatible materials such as platinum, iridium, and specialized polymers. These materials are essential for both the electrical performance and long-term stability of electrode arrays. Fluctuations in global metal markets and limited suppliers of medical-grade polymers have led to increased lead times and cost volatility. Companies like Heraeus and LivaNova are among the few established suppliers capable of meeting the stringent purity and traceability requirements for neurotechnology applications.
On the fabrication side, the transition from low-volume, research-scale production to industrial-scale manufacturing presents formidable hurdles. High-density arrays require advanced microfabrication techniques, such as photolithography, laser micromachining, and thin-film deposition, often adapted from the semiconductor industry. However, the unique geometries and biocompatibility requirements of neural interfaces necessitate custom process development and specialized cleanroom environments. Leading manufacturers like Blackrock Neurotech and NeuroNexus have invested heavily in proprietary processes, but scaling these to meet growing clinical and commercial demand remains a work in progress.
Supply chain fragility is further exacerbated by the limited number of vendors capable of producing high-precision components, such as microelectrode shanks and flexible substrates. Disruptions—whether due to geopolitical tensions, pandemic-related shutdowns, or regulatory changes—can have outsized impacts on production timelines. To mitigate these risks, some companies are pursuing vertical integration or forming strategic partnerships with key suppliers. For example, Neuralink has publicly discussed efforts to internalize critical manufacturing steps and develop in-house expertise in both materials science and automated assembly.
Looking ahead, the outlook for supply chain resilience and scalability in high-density electrode array manufacturing will depend on continued investment in automation, standardization, and supplier diversification. Industry groups and consortia are beginning to emerge to address shared challenges, but the path to truly scalable, cost-effective production is likely to require both technological breakthroughs and new models of collaboration across the value chain.
Regulatory and Standards Landscape (e.g., ieee.org, fda.gov)
The regulatory and standards landscape for high-density electrode array manufacturing is rapidly evolving as the technology matures and its applications in neuroprosthetics, brain-computer interfaces, and advanced medical diagnostics expand. In 2025, regulatory agencies and standards organizations are intensifying their focus on ensuring the safety, efficacy, and interoperability of these complex devices.
In the United States, the U.S. Food and Drug Administration (FDA) continues to play a central role in overseeing the approval and post-market surveillance of high-density electrode arrays, particularly those intended for human implantation. The FDA’s Center for Devices and Radiological Health (CDRH) has updated its guidance to address the unique challenges posed by microfabricated, high-channel-count arrays, emphasizing biocompatibility, long-term stability, and electromagnetic compatibility. Manufacturers are increasingly required to provide comprehensive preclinical and clinical data, including accelerated aging studies and in vivo performance metrics, to demonstrate device reliability over extended periods.
On the standards front, the Institute of Electrical and Electronics Engineers (IEEE) is actively developing and revising standards relevant to neural interface technologies. The IEEE P2725 series, for example, is focused on establishing performance, safety, and interoperability benchmarks for neural interface devices, including high-density electrode arrays. These standards are expected to become increasingly influential in procurement decisions and regulatory submissions, as they provide a common framework for evaluating device quality and compatibility.
Internationally, the International Organization for Standardization (ISO) and the International Electrotechnical Commission (IEC) are collaborating on harmonized standards for active implantable medical devices, which encompass high-density electrode arrays. The ISO 14708 series and IEC 60601 family are being updated to reflect advances in microfabrication, wireless telemetry, and power management, all of which are critical for next-generation electrode arrays.
Looking ahead, regulatory bodies are expected to place greater emphasis on cybersecurity, data privacy, and the ethical implications of neural data collection. The convergence of medical device regulations with emerging standards for artificial intelligence and machine learning—often integral to high-density array systems—will further shape the compliance landscape. Manufacturers and developers must remain agile, engaging proactively with regulators and standards organizations to ensure that their products meet evolving requirements and can be brought to market efficiently and safely.
Investment Trends and Strategic Partnerships
The high-density electrode array manufacturing sector is experiencing a surge in investment and strategic partnerships as demand for advanced neural interfaces, brain-computer interfaces (BCIs), and next-generation medical devices accelerates in 2025. This momentum is driven by the convergence of neuroscience, microfabrication, and materials science, with both established players and emerging startups vying for technological leadership.
Major investments are being funneled into scaling up production capabilities and refining manufacturing processes. Blackrock Neurotech, a pioneer in neural interface technology, has attracted significant funding rounds in recent years to expand its manufacturing infrastructure and accelerate commercialization of its high-channel-count arrays. Similarly, Neuralink continues to draw global attention and capital, leveraging its vertically integrated approach to develop and manufacture ultra-high-density electrode arrays for both research and clinical applications. The company’s ongoing recruitment of microfabrication and process engineering talent underscores its commitment to in-house manufacturing scale-up.
Strategic partnerships are also shaping the competitive landscape. In 2024 and 2025, collaborations between device manufacturers and semiconductor foundries have intensified, aiming to leverage advanced MEMS (Micro-Electro-Mechanical Systems) fabrication techniques. For example, imec, a leading R&D hub for nanoelectronics, has partnered with several medical device companies to co-develop scalable, biocompatible electrode arrays using its state-of-the-art cleanroom facilities. These alliances are critical for translating laboratory-scale prototypes into mass-producible, regulatory-compliant products.
In addition, cross-sector partnerships are emerging between neural device firms and materials science companies. BIOTRONIK, known for its expertise in medical device manufacturing, has initiated joint ventures to explore novel electrode coatings and flexible substrates, aiming to enhance device longevity and patient safety. Such collaborations are expected to yield new intellectual property and accelerate time-to-market for next-generation arrays.
Looking ahead, the sector is poised for further consolidation and vertical integration as companies seek to control critical supply chains and protect proprietary manufacturing know-how. The influx of venture capital and strategic investment is expected to continue, particularly as regulatory pathways for implantable neural devices become clearer and clinical demand rises. The next few years will likely see increased M&A activity, with larger medical technology firms acquiring innovative startups to secure access to advanced electrode array manufacturing capabilities.
Future Outlook: Disruptive Technologies and Long-Term Opportunities
The landscape of high-density electrode array manufacturing is poised for significant transformation in 2025 and the years immediately following, driven by advances in materials science, microfabrication, and integration technologies. As demand surges for neural interfaces in both clinical and research settings, manufacturers are racing to overcome challenges related to scalability, biocompatibility, and signal fidelity.
One of the most notable trends is the shift toward flexible and stretchable substrates, which promise to improve the long-term stability and comfort of implanted arrays. Companies such as Blackrock Neurotech and Neuralink are at the forefront, leveraging microelectromechanical systems (MEMS) and advanced polymer technologies to fabricate arrays with thousands of channels. These innovations are expected to enable higher spatial resolution and more robust chronic implantation, addressing key limitations of traditional silicon-based arrays.
Automated, high-throughput manufacturing processes are also emerging as a disruptive force. For example, Neuralink has developed robotic systems capable of inserting flexible electrode threads with micron-level precision, a technology that could soon be adapted for mass production. Meanwhile, Blackrock Neurotech continues to refine its Utah Array platform, focusing on increasing channel counts and improving reliability through advanced packaging and hermetic sealing techniques.
Material innovation remains a critical area of opportunity. The adoption of novel coatings such as conductive polymers, graphene, and nanostructured metals is anticipated to enhance both the electrical performance and biocompatibility of electrode arrays. Companies like Neuralink and Blackrock Neurotech are investing in research to optimize these materials for chronic use, with the goal of reducing immune response and extending device lifespans.
Looking ahead, the integration of on-array electronics—such as amplifiers, multiplexers, and wireless communication modules—will likely become standard. This trend is expected to reduce wiring complexity and improve signal quality, paving the way for fully implantable, high-channel-count systems. Industry leaders are also exploring scalable manufacturing partnerships and supply chain optimizations to meet anticipated demand from both medical and consumer neurotechnology markets.
In summary, the next few years will see high-density electrode array manufacturing evolve rapidly, with disruptive technologies enabling higher performance, greater scalability, and broader application. As regulatory pathways clarify and manufacturing matures, the sector is positioned for substantial growth and long-term opportunity.
Sources & References
- Blackrock Neurotech
- NeuroNexus Technologies
- Neuralink
- Microprobes for Life Science
- Ad-Tech Medical Instrument Corporation
- neuroloop
- imec
- Micron Technology
- Cirtec Medical
- CorTec
- TMC
- Heraeus
- Blackrock Neurotech
- NeuroNexus
- Neuralink
- Institute of Electrical and Electronics Engineers
- International Organization for Standardization
- BIOTRONIK