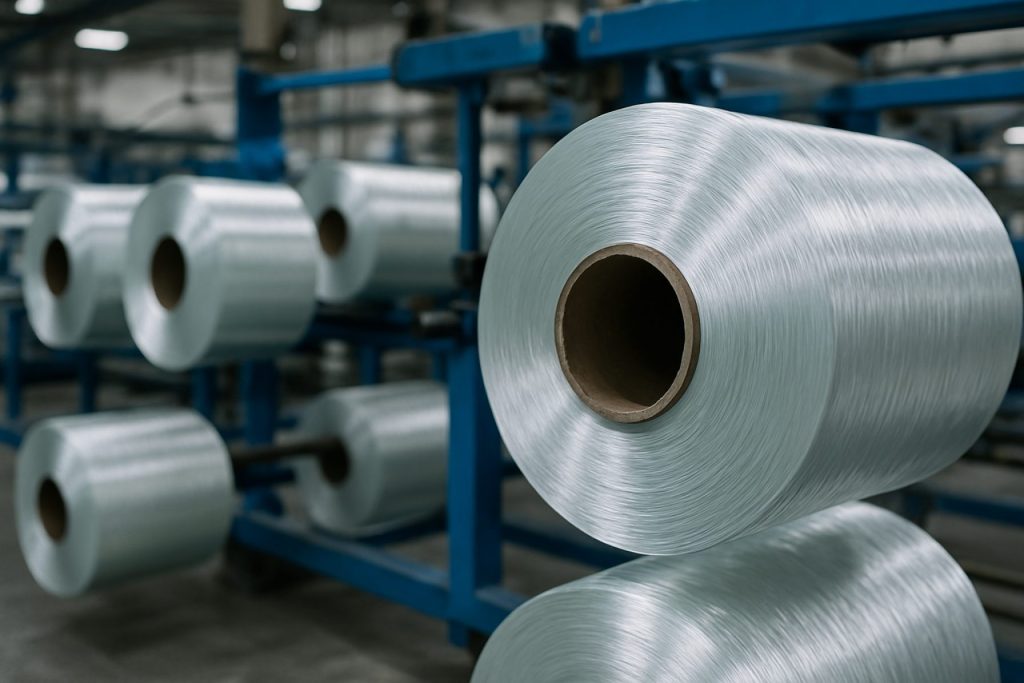
High-Strength Glass Microfiber Manufacturing in 2025: Innovations, Market Forces, and the Road Ahead. Discover how advanced materials are reshaping industries and what the next five years hold for this high-performance sector.
- Executive Summary: Key Findings and 2025 Outlook
- Market Size and Growth Forecasts Through 2030
- Emerging Applications and End-User Industries
- Technological Innovations in Glass Microfiber Production
- Competitive Landscape: Leading Manufacturers and New Entrants
- Supply Chain Dynamics and Raw Material Sourcing
- Sustainability Initiatives and Environmental Impact
- Regulatory Landscape and Industry Standards
- Investment Trends and Strategic Partnerships
- Future Opportunities and Challenges: 2025–2030
- Sources & References
Executive Summary: Key Findings and 2025 Outlook
The high-strength glass microfiber manufacturing sector is poised for robust growth in 2025, driven by escalating demand from filtration, advanced composites, and energy storage industries. High-strength glass microfibers, characterized by their superior tensile strength, thermal stability, and chemical resistance, are increasingly integral to next-generation filtration media, battery separators, and lightweight structural components. The sector is witnessing significant investments in capacity expansion, process innovation, and sustainability initiatives, particularly among leading global producers.
Key manufacturers such as Owens Corning, Johns Manville, and Nittobo are at the forefront of technological advancements, focusing on refining melt-blown and wet-laid processes to achieve finer fiber diameters and enhanced mechanical properties. Owens Corning has announced ongoing investments in its glass fiber facilities to meet the surging demand for high-performance filtration and composite applications. Similarly, Johns Manville continues to expand its product portfolio, emphasizing specialty glass microfibers for air and liquid filtration, as well as for use in electric vehicle (EV) battery separators.
In Asia, Nittobo and Shandong Fiberglass Group are scaling up production capacities and targeting export markets, leveraging advanced manufacturing lines and proprietary formulations. These companies are also investing in R&D to develop microfibers with tailored surface chemistries and improved dispersion characteristics, catering to the evolving needs of the electronics and energy sectors.
Sustainability is emerging as a central theme, with manufacturers adopting energy-efficient furnaces, closed-loop water systems, and recycled glass cullet in their processes. Industry bodies such as the Glass Manufacturing Industry Council are promoting best practices and facilitating collaboration on environmental standards, reflecting growing regulatory and customer expectations for greener production.
Looking ahead to 2025 and beyond, the outlook for high-strength glass microfiber manufacturing remains highly positive. The sector is expected to benefit from continued growth in clean energy, air quality management, and lightweighting trends in transportation and construction. Ongoing process automation and digitalization are anticipated to further enhance product consistency and operational efficiency. As end-user requirements become more stringent, manufacturers are likely to accelerate innovation in fiber morphology, surface treatment, and hybrid material integration, solidifying high-strength glass microfibers as a critical material platform for advanced industrial applications.
Market Size and Growth Forecasts Through 2030
The high-strength glass microfiber manufacturing sector is positioned for robust growth through 2030, driven by expanding applications in filtration, advanced composites, battery separators, and thermal/acoustic insulation. As of 2025, the market is experiencing heightened demand from industries such as automotive, electronics, energy storage, and construction, all seeking lightweight, durable, and high-performance materials.
Key manufacturers, including Owens Corning, Auburn Manufacturing, Inc., and Nitto Denko Corporation, are scaling up production capacities and investing in process innovations to meet the evolving requirements for finer fiber diameters, higher tensile strengths, and improved chemical resistance. Owens Corning, a global leader in glass fiber technology, continues to expand its product portfolio and manufacturing footprint, particularly in North America and Europe, to address the surging demand for high-strength microfibers in filtration and composite reinforcement applications.
The Asia-Pacific region, led by China, Japan, and South Korea, is expected to maintain the highest growth rate through 2030, fueled by rapid industrialization, infrastructure development, and the proliferation of electric vehicles and renewable energy systems. Companies such as Nitto Denko Corporation and Nippon Electric Glass Co., Ltd. are at the forefront of technological advancements in microfiber production, focusing on energy-efficient melting processes and the development of specialty glass compositions tailored for next-generation applications.
In the United States and Europe, regulatory pressures for improved air quality and energy efficiency are accelerating the adoption of high-strength glass microfibers in HVAC filtration, industrial emissions control, and building insulation. Auburn Manufacturing, Inc. is notable for its focus on high-temperature glass microfiber products, serving critical sectors such as aerospace and industrial processing.
Looking ahead, the market outlook through 2030 remains positive, with annual growth rates projected in the high single digits, underpinned by ongoing R&D investments and the emergence of new end-use sectors such as hydrogen fuel cells and advanced battery technologies. Strategic collaborations between manufacturers and end-users are expected to accelerate product development cycles and expand the range of high-strength glass microfiber applications. As sustainability and circular economy principles gain traction, manufacturers are also exploring recycling and closed-loop production models to reduce environmental impact and enhance resource efficiency.
Emerging Applications and End-User Industries
High-strength glass microfiber manufacturing is experiencing a surge in emerging applications and end-user industries, driven by the material’s unique combination of low density, high tensile strength, thermal stability, and chemical resistance. As of 2025, the landscape is rapidly evolving, with several sectors adopting advanced glass microfibers to meet stringent performance and sustainability requirements.
One of the most prominent growth areas is the filtration industry. High-strength glass microfibers are increasingly used in HEPA and ULPA filters for cleanrooms, pharmaceuticals, and semiconductor manufacturing, where particle retention and durability are critical. Companies such as AeroFiber and Hollingsworth & Vose are expanding their product lines to address the demand for finer, more robust microfiber media capable of withstanding aggressive cleaning and sterilization cycles.
The energy sector is another key adopter, particularly in battery separators and fuel cell components. High-strength glass microfibers offer excellent ionic conductivity and thermal stability, making them ideal for next-generation lithium-ion and solid-state batteries. 3M and Nitto Denko Corporation are actively developing microfiber-based separators to improve battery safety and lifespan, with pilot projects underway for electric vehicles and grid storage systems.
In the construction and transportation industries, high-strength glass microfibers are being integrated into composite materials for lightweight panels, insulation, and reinforcement. This trend is fueled by the push for energy efficiency and reduced emissions. Owens Corning and Saint-Gobain are notable for their investments in advanced glass microfiber composites, targeting applications in automotive body panels, aerospace interiors, and high-performance building envelopes.
Healthcare and life sciences are also emerging as significant end-users. Glass microfibers are utilized in diagnostic devices, wound care, and biopharmaceutical filtration, where their inertness and customizable porosity are advantageous. Merck KGaA and Pall Corporation are expanding their portfolios to include microfiber-based solutions for single-use bioprocessing and medical filtration.
Looking ahead, the outlook for high-strength glass microfiber manufacturing is robust. The convergence of regulatory pressures, sustainability goals, and technological advancements is expected to drive further adoption across sectors. Industry leaders are investing in process innovation—such as precision fiber diameter control and surface functionalization—to unlock new applications and enhance performance, positioning glass microfibers as a critical material in the advanced manufacturing landscape through 2025 and beyond.
Technological Innovations in Glass Microfiber Production
The manufacturing of high-strength glass microfibers is undergoing significant technological transformation as the industry responds to increasing demand from sectors such as filtration, advanced composites, and energy storage. In 2025, the focus is on enhancing fiber strength, uniformity, and process efficiency, driven by both end-user requirements and sustainability imperatives.
One of the most notable innovations is the adoption of advanced melt-spinning and flame attenuation techniques, which allow for the production of microfibers with diameters consistently below 1 micron while maintaining high tensile strength. Companies such as Owens Corning and Johns Manville have invested in proprietary furnace designs and real-time process monitoring systems that optimize glass composition and fiber drawing parameters. These improvements have resulted in microfibers with enhanced mechanical properties and reduced defect rates, making them suitable for demanding applications in battery separators and high-performance filtration media.
Another area of innovation is the development of new glass formulations. Traditional E-glass is being supplemented by specialty compositions, such as S-glass and high-silica glass, which offer superior strength-to-weight ratios and chemical resistance. Nittobo, a leading Japanese manufacturer, has introduced high-strength glass microfiber products tailored for the electronics and automotive industries, leveraging proprietary glass chemistries and surface treatments to improve fiber-matrix adhesion in composites.
Automation and digitalization are also reshaping the production landscape. Inline quality control using machine vision and AI-driven analytics is becoming standard, enabling manufacturers to detect and correct process deviations in real time. Saint-Gobain has reported the integration of Industry 4.0 technologies in its glass fiber plants, resulting in higher yields and more consistent product quality.
Sustainability is a growing priority, with manufacturers seeking to reduce energy consumption and emissions. Innovations include the use of electric melting furnaces and the recycling of cullet (waste glass) into the production process. These efforts are supported by industry-wide initiatives to lower the carbon footprint of glass fiber manufacturing, as highlighted by organizations such as Glass Alliance Europe.
Looking ahead, the next few years are expected to see further advances in nanofiber production, hybrid fiber systems, and bio-based glass formulations. These developments will likely expand the application scope of high-strength glass microfibers, particularly in emerging fields such as hydrogen storage, next-generation batteries, and lightweight structural composites.
Competitive Landscape: Leading Manufacturers and New Entrants
The competitive landscape of high-strength glass microfiber manufacturing in 2025 is characterized by a mix of established global leaders and dynamic new entrants, each leveraging advanced technologies and expanding production capacities to meet rising demand across filtration, composites, and specialty applications. The sector is marked by significant investments in R&D, sustainability initiatives, and regional expansion, as manufacturers seek to differentiate their offerings and secure market share.
Among the established players, Owens Corning remains a dominant force, with a global footprint and a comprehensive portfolio of glass microfiber products tailored for high-performance filtration and insulation. The company continues to invest in process innovation, focusing on energy efficiency and product consistency, and has announced plans to further expand its manufacturing capabilities in North America and Asia to address growing demand in automotive and industrial sectors.
Another key player, Johns Manville, a Berkshire Hathaway company, is recognized for its advanced glass microfiber solutions used in air and liquid filtration, battery separators, and specialty composites. Johns Manville has recently upgraded its European production facilities, integrating automation and digital quality control systems to enhance throughput and product uniformity. The company’s commitment to sustainability is evident in its efforts to reduce emissions and increase the use of recycled glass in its manufacturing processes.
In Asia, Nittobo (Nitto Boseki Co., Ltd.) stands out as a leading supplier of high-strength glass microfibers, particularly for high-efficiency particulate air (HEPA) filters and advanced composite materials. Nittobo has expanded its R&D activities to develop ultra-fine microfiber grades and is actively collaborating with electronics and battery manufacturers to tailor products for next-generation applications.
Emerging entrants are also reshaping the competitive landscape. Companies such as Shandong Fiberglass Group in China are rapidly scaling up production capacity and investing in proprietary melt-blown and centrifugal spinning technologies. These firms are targeting both domestic and international markets, often offering cost-competitive alternatives and flexible customization options.
Looking ahead, the competitive environment is expected to intensify as demand for high-strength glass microfibers grows in response to stricter environmental regulations, the electrification of vehicles, and the proliferation of cleanroom and filtration technologies. Manufacturers are likely to prioritize digitalization, circular economy practices, and strategic partnerships to maintain their edge. The entry of new players, particularly from Asia, is anticipated to drive further innovation and price competition, shaping the industry’s trajectory through the remainder of the decade.
Supply Chain Dynamics and Raw Material Sourcing
The supply chain for high-strength glass microfiber manufacturing in 2025 is characterized by a complex interplay of raw material sourcing, global logistics, and evolving supplier relationships. The primary raw materials—high-purity silica sand, alumina, boron compounds, and various mineral additives—are sourced from a limited number of specialized mining and chemical processing companies. The quality and consistency of these inputs are critical, as even minor impurities can significantly affect the mechanical properties and performance of the final microfiber products.
Leading manufacturers such as Owens Corning, Saint-Gobain, and Nitto Denko Corporation maintain vertically integrated supply chains or long-term contracts with raw material suppliers to ensure stable access and quality control. For example, Owens Corning operates its own glass melting and fiberizing facilities, allowing for tight oversight of material inputs and process parameters. Similarly, Saint-Gobain leverages its global network of raw material sources and manufacturing plants to mitigate regional supply disruptions and optimize logistics.
In 2025, the industry faces ongoing challenges related to the volatility of raw material prices, particularly for high-purity silica and boron, which are subject to fluctuations due to mining constraints and geopolitical factors. Supply chain resilience has become a strategic priority, with manufacturers diversifying their supplier base and investing in digital supply chain management systems to enhance transparency and responsiveness. Companies are also exploring alternative sourcing strategies, such as recycling glass waste and developing synthetic substitutes for certain mineral additives, to reduce dependency on traditional suppliers and improve sustainability.
Environmental regulations and sustainability goals are increasingly influencing sourcing decisions. Major players like Saint-Gobain and Owens Corning have announced initiatives to increase the use of recycled glass (cullet) in their production processes, aiming to lower energy consumption and carbon emissions. This shift not only addresses regulatory pressures but also appeals to customers seeking greener materials for applications in filtration, composites, and advanced insulation.
Looking ahead, the outlook for high-strength glass microfiber supply chains is shaped by continued investment in automation, digitalization, and sustainability. The integration of real-time monitoring and predictive analytics is expected to further streamline raw material procurement and inventory management. As demand grows in sectors such as electric vehicles, renewable energy, and high-performance filtration, manufacturers are likely to deepen collaborations with raw material suppliers and logistics partners to secure reliable, high-quality inputs and maintain competitive advantage.
Sustainability Initiatives and Environmental Impact
The high-strength glass microfiber manufacturing sector is undergoing significant transformation in 2025, driven by increasing regulatory pressure, customer demand for sustainable products, and the need to reduce environmental impact. Major manufacturers are investing in cleaner production technologies, circular economy models, and energy efficiency improvements to address the environmental footprint of glass microfiber production, which traditionally involves high energy consumption and emissions.
Key industry players such as Owens Corning, Saint-Gobain, and Nitto Denko Corporation are at the forefront of these sustainability initiatives. Owens Corning has set ambitious 2030 sustainability goals, including reducing greenhouse gas emissions by 50% and sourcing 100% of its electricity from renewable sources. The company is also working to increase the recycled content in its glass fiber products, which directly reduces the need for virgin raw materials and lowers energy use during melting and fiberization processes.
Similarly, Saint-Gobain has committed to achieving carbon neutrality by 2050 and is actively developing low-carbon glass melting technologies. The company is piloting electric furnaces and optimizing batch formulations to reduce both energy consumption and CO2 emissions. In 2025, Saint-Gobain is expanding its closed-loop recycling programs, enabling the collection and reprocessing of post-industrial and post-consumer glass fiber waste into new high-strength microfiber products.
Water usage and waste management are also critical focus areas. Nitto Denko Corporation has implemented advanced water recycling systems in its microfiber production facilities, aiming to minimize freshwater withdrawal and reduce effluent discharge. The company is also exploring bio-based binders and alternative chemistries to replace traditional resins, which can have a significant environmental impact during both production and end-of-life disposal.
Industry-wide, the adoption of life cycle assessment (LCA) tools is becoming standard practice, allowing manufacturers to quantify and communicate the environmental impacts of their products. Organizations such as the Glass Alliance Europe are supporting members with best practices and harmonized sustainability metrics, fostering transparency and continuous improvement across the sector.
Looking ahead, the outlook for sustainability in high-strength glass microfiber manufacturing is positive. With ongoing investments in decarbonization, recycling, and green chemistry, the industry is expected to make measurable progress in reducing its environmental footprint over the next few years, aligning with global climate and circular economy objectives.
Regulatory Landscape and Industry Standards
The regulatory landscape for high-strength glass microfiber manufacturing in 2025 is shaped by a combination of international standards, regional directives, and evolving industry best practices. As demand for advanced composites and filtration media grows, manufacturers are increasingly required to comply with stringent quality, safety, and environmental regulations. The industry is primarily governed by standards set by organizations such as the International Organization for Standardization (ISO), with ISO 9001 (quality management systems) and ISO 14001 (environmental management systems) being widely adopted benchmarks among leading producers.
In the European Union, the Registration, Evaluation, Authorisation and Restriction of Chemicals (REACH) regulation continues to play a pivotal role in dictating the permissible use of raw materials and additives in glass microfiber production. Compliance with REACH is mandatory for companies operating or selling within the EU, compelling manufacturers to maintain detailed documentation on chemical safety and to substitute hazardous substances where possible. The European Committee for Standardization (CEN) also issues specific standards for glass fibers, including EN 14020, which addresses product specifications and testing methods.
In the United States, oversight is provided by agencies such as the Occupational Safety and Health Administration (OSHA) and the Environmental Protection Agency (EPA), which regulate workplace exposure limits and emissions from glass fiber manufacturing facilities. The American Society for Testing and Materials (ASTM) publishes standards such as ASTM C1666/C1666M for glass fiber products, which are widely referenced by domestic manufacturers. Companies like Owens Corning and PPG Industries are known to actively participate in the development and adoption of these standards, ensuring their products meet or exceed regulatory requirements.
Globally, the industry is witnessing a trend toward harmonization of standards, driven by the increasing cross-border trade of high-strength glass microfiber products. Major Asian producers, including Nittobo and China Jushi, are aligning their manufacturing processes with international norms to access global markets. This includes certification to ISO standards and adherence to local environmental regulations, such as China’s Ministry of Ecology and Environment guidelines for industrial emissions.
Looking ahead, regulatory focus is expected to intensify on sustainability and worker safety. Anticipated updates to ISO and ASTM standards may introduce stricter requirements for energy efficiency, recycling of process waste, and reduction of airborne fiber emissions. Industry leaders are proactively investing in advanced filtration and monitoring technologies to stay ahead of compliance curves, positioning themselves for continued growth in a more regulated and environmentally conscious market.
Investment Trends and Strategic Partnerships
The high-strength glass microfiber manufacturing sector is experiencing a notable surge in investment and strategic partnerships as global demand for advanced composites, filtration media, and energy storage materials intensifies. In 2025, this trend is being driven by the need for lightweight, durable materials in automotive, aerospace, electronics, and renewable energy applications. Major industry players are expanding production capacity and forming alliances to secure supply chains, accelerate innovation, and address sustainability goals.
Key manufacturers such as Owens Corning, Nitto Denko Corporation, and PPG Industries are at the forefront of these developments. Owens Corning has announced significant capital investments in its glass fiber facilities, focusing on process automation and energy efficiency to meet the growing demand for high-performance microfibers. Similarly, Nitto Denko Corporation is leveraging its expertise in specialty materials to expand its microfiber product lines, targeting filtration and battery separator markets.
Strategic partnerships are also shaping the competitive landscape. In 2024 and 2025, collaborations between glass microfiber producers and downstream users—such as battery manufacturers and filtration system suppliers—have intensified. For example, PPG Industries has entered into joint development agreements with leading battery technology firms to co-develop next-generation glass microfiber separators for lithium-ion and solid-state batteries. These partnerships aim to accelerate product development cycles and ensure that new materials meet stringent performance and safety requirements.
Investment is not limited to established players. Regional manufacturers in Asia and Europe are attracting venture capital and government funding to build new production lines and pilot plants. This is particularly evident in China, where local companies are scaling up to serve both domestic and international markets, supported by policy incentives for advanced materials and clean energy technologies.
Looking ahead, the outlook for investment and partnerships in high-strength glass microfiber manufacturing remains robust. The sector is expected to see continued consolidation as companies seek to secure raw material sources and intellectual property. Additionally, sustainability is emerging as a key driver, with manufacturers investing in recycling technologies and low-carbon production processes to align with global environmental standards.
- Major investments by Owens Corning and Nitto Denko Corporation in capacity and R&D.
- Strategic alliances between PPG Industries and battery/filtration companies.
- Emergence of new entrants in Asia, supported by government and private funding.
- Focus on sustainability and supply chain resilience shaping future investments.
Future Opportunities and Challenges: 2025–2030
The period from 2025 to 2030 is poised to be transformative for high-strength glass microfiber manufacturing, driven by surging demand in advanced filtration, battery separators, and lightweight composites. As industries such as electric vehicles, renewable energy, and high-performance construction materials expand, the need for robust, thermally stable, and chemically resistant glass microfibers is expected to intensify.
Key manufacturers, including Owens Corning, Nitto Denko Corporation, and PFG Fiber Glass Corporation, are investing in process automation, energy efficiency, and advanced melting technologies to enhance both product quality and production scalability. For example, Owens Corning has publicly committed to reducing the carbon footprint of its glass fiber operations, aligning with global sustainability targets and customer expectations for greener materials.
A major opportunity lies in the development of ultra-fine, high-strength microfibers for next-generation lithium-ion and solid-state battery separators. These applications require precise control over fiber diameter, porosity, and surface chemistry—areas where proprietary manufacturing techniques and continuous R&D investment will be decisive. Companies such as Nitto Denko Corporation are already recognized for their advanced microfiber solutions in battery and filtration markets, and are expected to further expand their product portfolios to meet evolving technical requirements.
However, the sector faces several challenges. Raw material price volatility, particularly for high-purity silica and specialty dopants, could impact cost structures. Additionally, the energy-intensive nature of glass melting and fiberization processes presents both economic and regulatory hurdles, especially as governments tighten emissions standards. Manufacturers are responding by exploring electric melting furnaces, waste heat recovery, and increased use of recycled glass cullet to mitigate environmental impact and operational costs.
Geopolitical factors and supply chain resilience will also shape the industry’s outlook. With a significant portion of global glass microfiber capacity concentrated in East Asia, companies in North America and Europe are evaluating local production expansions to reduce dependency and ensure supply continuity. For instance, PFG Fiber Glass Corporation has signaled intentions to scale up its North American operations in response to regional demand growth.
In summary, the next five years will see high-strength glass microfiber manufacturing characterized by technological innovation, sustainability initiatives, and strategic capacity investments. Success will depend on the ability of leading producers to balance cost, quality, and environmental stewardship while meeting the increasingly sophisticated needs of downstream industries.