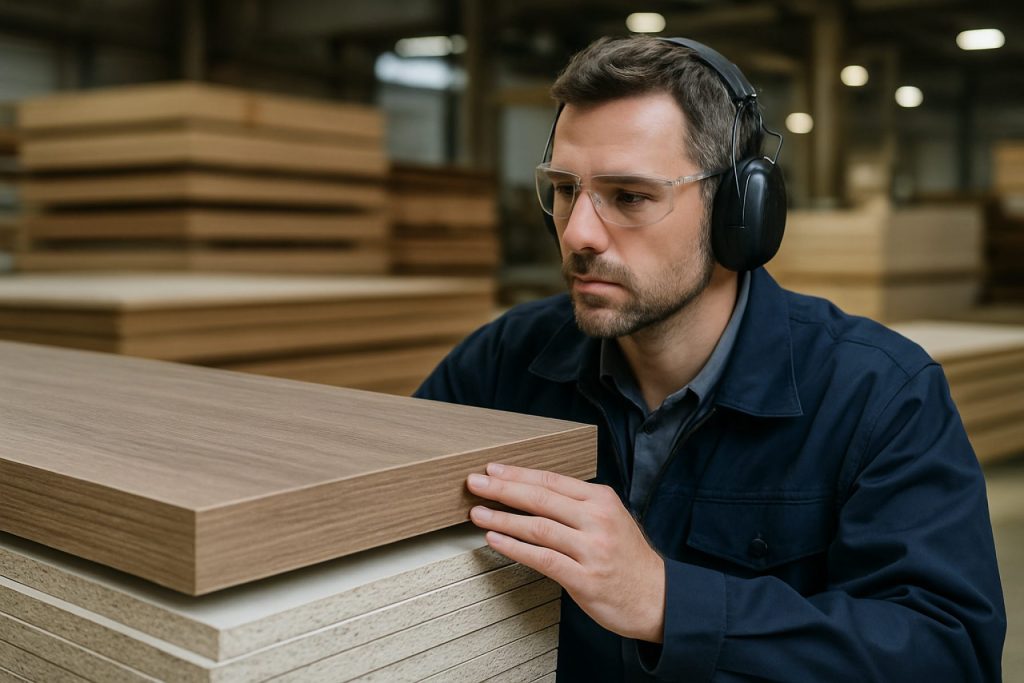
Table of Contents
- Executive Summary: Key Trends for 2025–2030
- Global Market Forecast and Emerging Regional Hotspots
- Latest Advances in Melamine Resin Formulation and Laminate Engineering
- Sustainability: Eco-Friendly Materials and Circular Economy Approaches
- Competitive Landscape: Profiles of Leading Manufacturers and Innovators
- Supply Chain and Raw Material Sourcing: Opportunities and Risks
- Applications Across Sectors: Construction, Furniture, Automotive, and More
- Regulatory Compliance and Industry Standards (e.g., iso.org, compositepanel.org)
- Digitalization and Automation in Laminate Production Processes
- Future Outlook: Disruptive Technologies and Investment Hotspots
- Sources & References
Executive Summary: Key Trends for 2025–2030
The melamine-based laminates engineering sector is poised for significant transformation between 2025 and 2030, driven by rapid advancements in material science, sustainability imperatives, and shifting market demands. As global construction and furniture industries rebound and innovate post-pandemic, melamine laminates are increasingly favored for their durability, versatility, and cost-effectiveness. Leading manufacturers are investing in upgraded production technologies and eco-friendly processes to align with tightening environmental regulations and evolving customer preferences.
A notable trend for 2025 is the acceleration of digital printing and surface texturing techniques, enabling highly customized and aesthetically diverse laminate surfaces. Companies such as Fundermax and EGGER Group are pioneering in the deployment of synchronized pore technology and digital decor printing, allowing for hyper-realistic wood, stone, and abstract finishes that closely mimic natural materials while offering enhanced resistance to abrasion and chemicals.
Sustainability remains a central pillar shaping the industry outlook through 2030. Several major producers have announced ambitious targets to reduce carbon emissions, increase the proportion of recycled content in core and overlay materials, and transition to formaldehyde-free or low-emission resins in melamine-based laminates. Kronospan and Swiss Krono Group have introduced laminate lines that incorporate recycled wood and comply with stringent E1 and CARB2 emissions standards, reflecting a broader industry shift toward circular economy principles.
The ongoing digitalization of manufacturing environments, embracing Industry 4.0 concepts, is expected to further optimize process efficiency and product consistency. Real-time quality monitoring, predictive maintenance, and automated handling systems are being integrated in leading facilities to drive down costs and shorten development cycles. Strategic partnerships between laminate producers and chemical suppliers, such as those seen with BASF, are facilitating the adoption of new melamine resin formulations tailored for improved performance and environmental compliance.
Looking ahead, market analysts expect continued growth in demand across both residential and commercial segments, fueled by urbanization and the trend toward modular, prefabricated construction. Geographic expansion into Asia-Pacific and Latin American markets is anticipated as local manufacturing capacity ramps up. Overall, melamine-based laminates engineering in 2025–2030 will be defined by innovation, sustainability, and the integration of advanced digital technologies, positioning the sector for robust, adaptable growth.
Global Market Forecast and Emerging Regional Hotspots
The global market for melamine-based laminates engineering is poised for notable expansion in 2025 and the subsequent years, propelled by construction, furniture, and interior design sectors seeking durable, aesthetically versatile surfacing solutions. As economic recovery and urbanization accelerate in Asia-Pacific, North America, and selected European regions, demand is shifting both in volume and in specialized applications.
Asia-Pacific continues to dominate as the largest and fastest-growing market for melamine-based laminates, driven by robust manufacturing capacity, rising middle-class incomes, and infrastructure investment. Major regional producers such as Aica Kogyo Co., Ltd. and Greenlam Industries are scaling up production and innovating with antimicrobial, fire-retardant, and low-emission laminates to capture evolving consumer and regulatory demands. In China, increased focus on green building standards and the ongoing push for urban redevelopment is fostering a migration from traditional surfacing materials toward engineered laminates with improved environmental profiles.
Europe remains a significant market, especially for premium and specialty melamine-based laminates. Companies like FunderMax and EGGER Group are investing in product differentiation via digital printing techniques and sustainable resin chemistries. The European Union’s tightening of formaldehyde emission limits—scheduled for enforcement in the coming years—has prompted research into resins with reduced volatile organic compounds (VOCs), aligning with broader Green Deal initiatives.
In North America, demand is stabilizing post-pandemic, with heightened interest in residential remodeling and commercial retrofits. The U.S.-based Wilsonart and Formica Group are leveraging advances in decorative surfaces, including synchronized texture printing and seamless edge technologies, positioning melamine laminates as a preferred alternative to natural wood and stone.
Emerging hotspots include the Middle East and Southeast Asia, where rapid hotel, retail, and office space development is fueling consumption. Investments in local production capacity and partnerships with global suppliers are expected to reduce dependency on imports and enhance supply chain resilience in these regions.
Looking ahead to the late 2020s, industry consensus points to continuous growth, with innovation in sustainability and performance as key differentiators. The sector’s outlook is buoyed by regulatory changes, evolving consumer preferences for eco-friendly yet affordable décor, and ongoing investments in manufacturing automation and digitalization across all leading regions.
Latest Advances in Melamine Resin Formulation and Laminate Engineering
The melamine-based laminates sector is witnessing significant innovation as manufacturers refine resin formulations and engineering processes to address performance, sustainability, and design trends. One of the most notable advances in 2025 is the development of low-formaldehyde and formaldehyde-free melamine resins, responding to increasingly stringent global regulations and market demand for safer indoor materials. Leading producers such as BASF and Hexion are accelerating the commercialization of next-generation melamine-formaldehyde resins featuring optimized cross-linking and enhanced emission control, positioning their products for compliance with evolving standards in Europe, North America, and Asia.
In addition, engineering improvements are focusing on increasing laminate durability and expanding design possibilities. Enhanced impregnation techniques and the use of nanomaterials are now being integrated into production lines by manufacturers including FINSA and Kronospan. These innovations enable the creation of laminates with higher abrasion, impact, and chemical resistance, while maintaining or even reducing overall material thickness. Such capabilities open doors for lightweight furniture and interior solutions, highly sought after in both residential and commercial sectors.
Digital printing and advanced embossing technologies are also shaping the competitive landscape. Market leaders like EGGER are investing in synchronized pore technology, which aligns surface textures precisely with printed wood grain patterns. This advancement not only elevates the aesthetic realism of melamine-faced panels but also allows for rapid customization and shorter design-to-market cycles, which are increasingly important for architects and furniture manufacturers.
From a sustainability perspective, circularity and resource efficiency are coming to the forefront. Companies such as Sonae Arauco are integrating recycled wood fibers and exploring bio-based components within melamine-based laminates, aiming to reduce reliance on virgin petrochemicals and improve lifecycle performance. These initiatives align with broader industry moves toward environmental product declarations (EPDs) and certification under schemes like FSC and PEFC.
Looking ahead, the industry outlook for 2025 and beyond suggests a continued trajectory of technical optimization and sustainability-driven reformulation. Strategic investments in plant upgrades and R&D, coupled with closer collaboration between resin producers, board manufacturers, and end-users, are expected to further enhance product value and support the adoption of melamine-based laminates in premium and demanding applications worldwide.
Sustainability: Eco-Friendly Materials and Circular Economy Approaches
Sustainability has become a central focus in melamine-based laminates engineering as industries respond to increasing environmental regulations, consumer demand for “green” materials, and commitments to circular economy principles. In 2025, manufacturers are intensifying efforts to reduce the ecological footprint of their products, from raw material sourcing to end-of-life management.
A significant development is the integration of recycled and renewable raw materials into laminate production. Leading producers are investigating bio-based resins and adhesives to partially replace conventional melamine-formaldehyde systems, aiming to lower emissions and dependence on fossil resources. For example, EGGER Group and Kronospan, two major laminate manufacturers, have publicized strategies to incorporate recycled wood fibers and to use responsibly sourced wood certified by organizations such as the Forest Stewardship Council (FSC).
Waste minimization and resource efficiency are also key trends. Manufacturers are investing in closed-loop systems, wherein offcuts and production scraps are reintroduced into the manufacturing cycle. This not only conserves raw materials but also reduces landfill burden. The move towards water-based and low-emission surface treatments further aligns with international standards for indoor air quality and chemical safety, as seen in the product lines of Arpa Industriale and Fundermax.
End-of-life strategies are progressing beyond landfill disposal. Some companies have piloted take-back programs and recycling schemes for spent laminates, though technical and economic challenges remain due to the cross-linked nature of melamine resins. However, research into depolymerization or material recovery is ongoing, with several European and Asian consortia exploring scalable solutions to laminate recycling.
Looking ahead, regulatory drivers such as the European Green Deal and anticipated stricter chemical regulations in North America and Asia-Pacific are expected to accelerate the adoption of eco-friendly materials and circular economy approaches in melamine-based laminates. The outlook for 2025–2028 suggests increased collaboration across the value chain—raw material suppliers, manufacturers, designers, and recyclers—to create certified, lower-impact products and establish transparent environmental reporting. Investments in R&D for alternative resins, digitalization of material flows, and take-back logistics are likely to shape the next generation of sustainable melamine laminates.
Competitive Landscape: Profiles of Leading Manufacturers and Innovators
The competitive landscape of melamine-based laminates engineering in 2025 is shaped by a mix of established global manufacturers and dynamic innovators driving advancements in technology, sustainability, and design. Industry leaders maintain significant market share through large-scale production capacities, robust distribution networks, and continuous investment in R&D, while newer entrants and specialized companies push the boundaries of performance and eco-friendly solutions.
Among the most prominent players is Fundermax, an Austrian manufacturer renowned for its high-pressure laminates (HPL) and compact panels. Fundermax has focused on integrating digital printing and smart surface treatments, enabling high customization and improved resistance to wear and chemicals. Their recent efforts include the development of panels with enhanced fire retardancy and antibacterial properties, catering to the evolving needs of the healthcare and transportation sectors.
Another significant entity is Formica Group, a globally recognized brand with a vast portfolio ranging from decorative laminates to specialty surface solutions. Formica continues to champion sustainable manufacturing by increasing the proportion of recycled materials in its products and optimizing energy efficiency across its facilities. Their “Everform” solid surface line—leveraging melamine technology—exemplifies the fusion of aesthetics and durability, meeting the stringent requirements of commercial and residential interiors.
Italian-based Arpa Industriale stands out for its innovation in engineered surfaces, particularly its “FENIX” range, which showcases ultra-matte, fingerprint-resistant laminates using advanced acrylic resins and melamine overlays. Arpa’s ongoing investments in nanotechnology and sustainable resins are anticipated to further enhance product performance and eco-credentials in the coming years.
Within the Asia-Pacific region, manufacturers like Greenlam Industries play a pivotal role, supplying melamine-based laminates to both domestic and international markets. Greenlam’s focus on antimicrobial surfaces and formaldehyde emission reductions aligns with growing regulatory scrutiny and consumer demand for healthier indoor environments.
Looking ahead, the competitive landscape is expected to intensify as manufacturers invest in digitalization, automation, and circular economy principles. The push for formaldehyde-free and bio-based melamine resins, along with the adoption of Industry 4.0 practices, is poised to reshape production processes and product offerings. Strategic collaborations, mergers, and acquisitions among key players will likely accelerate technological innovation and global market expansion through 2025 and beyond.
Supply Chain and Raw Material Sourcing: Opportunities and Risks
The supply chain for melamine-based laminates engineering in 2025 is shaped by both expanding opportunities and emerging risks. Melamine-formaldehyde resin, the critical component in these laminates, largely relies on the upstream availability of melamine and formaldehyde. The global supply of melamine is dominated by a few large chemical manufacturers, such as BASF, Borealis, and QatarEnergy, who control substantial production capacities and influence global pricing and supply security.
In 2025, opportunities are emerging from the expansion of melamine production capacities in Asia and the Middle East. Investments in new production lines and facility upgrades by companies like Borealis and QatarEnergy are expected to ease historical supply bottlenecks and enhance the stability of raw material sourcing. These developments may help laminate manufacturers secure more reliable and competitively priced feedstock, particularly as demand for decorative surfaces in construction, furniture, and automotive sectors continues to grow.
However, risks persist in the form of raw material price volatility and logistical disruptions. The global chemical sector continues to face challenges in energy supply, shipping container shortages, and geopolitical tensions, particularly in regions critical to melamine and urea production. For example, any disruption to natural gas supplies—crucial for ammonia and subsequently urea synthesis—can have a cascading impact on melamine availability and laminate production. Companies such as BASF have highlighted their ongoing efforts to diversify feedstock sources and optimize supply chain logistics to mitigate such vulnerabilities.
Environmental regulations present another layer of risk and opportunity. Regulatory requirements on formaldehyde emissions and sustainable chemical sourcing are intensifying in Europe, North America, and East Asia. This is prompting laminate producers and raw material suppliers to invest in cleaner production technologies and green chemistry approaches, as seen in recent initiatives by BASF. Industry players are increasingly seeking ISCC PLUS or similar certifications to ensure traceability and compliance, which can open new market segments but may also increase costs and complexity.
Looking ahead, the supply chain for melamine-based laminates is likely to become more resilient and sustainable as manufacturers invest in regional production hubs and circular economy practices. Yet, heightened attention to supply chain transparency, environmental stewardship, and geopolitical developments will remain pivotal for risk management and capturing new opportunities through 2025 and beyond.
Applications Across Sectors: Construction, Furniture, Automotive, and More
Melamine-based laminates are engineered materials prized for their durability, versatility, and design flexibility, making them integral across several sectors in 2025. Their adoption is propelled by ongoing innovation in resin technology and growing industry demand for aesthetically pleasing, robust, and cost-effective surfacing solutions.
In the construction sector, melamine-based laminates remain a mainstay for interior wall panels, partitions, and cabinetry. Their resistance to abrasion, moisture, and heat is especially valued in high-traffic commercial and institutional buildings. Manufacturers such as Arauco and Kronospan have expanded product ranges with laminates that offer antimicrobial surfaces and improved fire resistance, aligning with increased regulatory focus on hygiene and safety in public spaces. The adoption of digital printing technologies is further enabling architects and designers to specify customized patterns and textures, enhancing creative expression in both residential and commercial interiors.
The furniture industry continues to be a leading consumer of melamine-based laminates. Companies like EGGER and FINSA highlight the material’s role in the mass production of ready-to-assemble furniture, office fixtures, and kitchen cabinetry. The sector’s shift toward modular and sustainable furniture solutions is supported by laminates’ compatibility with recycled wood substrates and their ability to mimic natural materials, such as wood and stone, without the associated cost or resource depletion. Enhanced surface finishes, including fingerprint-resistant and soft-touch coatings, are being introduced to improve user experience and product longevity.
In the automotive sector, melamine-based laminates are increasingly used for interior components, including dashboards, door panels, and trim. Their lightweight nature and resistance to scratching and chemicals make them attractive for electric vehicles and next-generation car interiors, where both performance and aesthetics are prioritized. Suppliers such as Sonae Arauco are collaborating with automotive OEMs to develop tailored laminate solutions, integrating advanced decorative effects and improved durability for demanding in-vehicle environments.
Beyond these core sectors, melamine-based laminates are finding new applications in retail fixtures, healthcare furniture, and educational environments, where easy maintenance and hygienic surfaces are essential. Looking ahead, ongoing research into bio-based resins and closed-loop recycling processes is poised to further expand the environmental credentials and market reach of melamine-based laminates, positioning them as a cornerstone material in the circular economy initiatives emerging across industries.
Regulatory Compliance and Industry Standards (e.g., iso.org, compositepanel.org)
The landscape of regulatory compliance and industry standards for melamine-based laminates is rapidly evolving as 2025 approaches, driven by increasing demands for sustainability, product safety, and performance consistency. Melamine-based laminates, widely used in furniture, flooring, and interior surfaces, must meet a complex array of regional and international standards to ensure market access and consumer trust.
Globally, the International Organization for Standardization (ISO) sets foundational benchmarks through standards like ISO 4586, which covers high-pressure decorative laminates, specifying requirements for appearance, mechanical properties, and chemical resistance. The ISO framework is under continuous revision to reflect advancements in raw materials and manufacturing processes, particularly as the industry adopts more eco-friendly resins and surface treatments. ISO’s ongoing updates aim to harmonize safety, durability, and sustainability expectations worldwide.
In North America, the Composite Panel Association (CPA) and its ANSI-accredited standards, such as ANSI A208.1 for particleboard and ANSI A208.2 for medium-density fiberboard, remain central to compliance for laminated panel products. The CPA’s Eco-Certified Composite (ECC) program, which includes stringent criteria for recycled/recovered wood fiber content, formaldehyde emissions, and responsible wood sourcing, is gaining traction among manufacturers seeking to demonstrate environmental stewardship.
Formaldehyde emission regulations are a particularly dynamic area. The U.S. Environmental Protection Agency’s TSCA Title VI and California’s CARB Phase 2 set some of the strictest emission limits, influencing both domestic production and imports. Melamine-based laminates, while generally lower in formaldehyde emissions due to their resin chemistry, still require rigorous third-party testing and certification to ensure compliance. Major manufacturers such as Fundermax and Arauco actively publicize their adherence to these standards and invest in continuous improvement of their emission control technologies.
Looking forward to 2025 and beyond, regulatory frameworks are expected to tighten further, with the European Union’s Chemicals Strategy for Sustainability and upcoming updates to the EN 438 laminate standard likely to introduce lower thresholds for hazardous substances and greater transparency in material sourcing. Industry stakeholders are increasingly collaborating through organizations like Composite Panel Association and ISO to anticipate changes and shape future guidelines, ensuring that melamine-based laminates align with evolving market and societal expectations.
Manufacturers that proactively align with these evolving standards and transparently communicate their compliance credentials are poised to enhance their competitive positioning, particularly as green building certifications and consumer awareness of indoor air quality continue to rise.
Digitalization and Automation in Laminate Production Processes
The melamine-based laminates sector is undergoing a significant transformation driven by digitalization and automation, shaping production processes through 2025 and beyond. The integration of Industry 4.0 principles, including real-time data collection, process automation, and connectivity, is being rapidly adopted by leading manufacturers to boost efficiency, product consistency, and sustainability.
Key players in the industry have been investing in advanced manufacturing execution systems (MES), automated quality control, and interconnected machinery. For instance, Surteco Group SE—a major European surface specialist—has expanded its use of digital process control and inline inspection systems, allowing for immediate defect detection, reduced waste, and more agile production scheduling. Likewise, EGGER Group is advancing its digitalization strategy with fully automated pressing lines and robotic handling systems, enabling higher throughput and minimal downtime while ensuring consistent laminate quality.
Digital printing technology is another area of rapid development, offering unprecedented design flexibility and on-demand customization. Companies such as FINSA and Kronospan have incorporated high-definition digital decor printing, allowing for short-run and bespoke laminate surfaces that respond to dynamic market trends. This technology not only accelerates design-to-market timelines but also minimizes inventory requirements and material usage.
Automation extends beyond the production floor to supply chain management and order processing. The adoption of digital twins, predictive maintenance, and integrated ERP systems is enabling manufacturers to optimize resource allocation and anticipate equipment servicing needs, reducing unplanned downtime. Sonae Arauco reports significant improvements in operational efficiency and energy management through its ongoing digital transformation initiatives.
Looking forward, the trend towards fully smart factories is accelerating, with investments in IoT-enabled sensors, AI-driven process analytics, and remote monitoring platforms. These advancements are expected to further reduce manual intervention, enhance traceability, and support sustainability goals via better material and energy utilization. As regulatory and market pressures for eco-friendly production intensify, digitalization and automation will be pivotal for melamine-based laminate producers to remain competitive globally. By 2025 and in the following years, these innovations are set to redefine industry standards for productivity, customization, and environmental performance.
Future Outlook: Disruptive Technologies and Investment Hotspots
The future landscape of melamine-based laminates engineering is poised for significant transformation, with technological innovation and targeted investments shaping the sector through 2025 and beyond. Disruptive advances are emerging primarily in two domains: sustainable material development and digital manufacturing integration.
A major area of focus is the development of eco-friendly melamine resins and laminates. There is a marked industry shift toward bio-based resins and the reduction of formaldehyde emissions, responding to tightening global environmental regulations and growing customer demand for sustainable products. For instance, leading manufacturers such as FINSA and Kronospan have invested in R&D to introduce low-emission or formaldehyde-free melamine panels, aiming to meet E1 and even the more stringent E0 standards for indoor air quality. This trend is expected to accelerate, with the EU Green Deal and North American regulatory changes acting as catalysts for widespread adoption of greener laminate products.
Digitalization is another disruptive force. The integration of Industry 4.0 technologies—such as IoT-enabled process monitoring, AI-driven quality control, and advanced digital printing—is revolutionizing laminate production. Companies like EGGER and SURTECO GROUP SE are adopting digital printing to offer unprecedented design flexibility and customization, reducing lead times and enabling on-demand manufacturing. This shift is supporting the proliferation of short-run and bespoke laminate offerings, particularly in high-value segments like interior design and contract furniture.
Investment hotspots for the coming years are concentrated in Asia-Pacific, especially China, Vietnam, and India, where rapid urbanization and expanding middle classes are driving construction and furniture markets. Major players such as Greenlam Industries are ramping up capacity and investing in high-efficiency, automated plants to meet surging regional demand. Concurrently, Europe remains an innovation hub, with established firms focusing on sustainable processes and digital transformation.
Looking ahead, the sector is expected to see further convergence between advanced materials science and smart manufacturing. The result will likely be a market characterized by highly customized, eco-friendly melamine laminates produced with minimal environmental impact and optimized operational efficiency. As sustainability and digital agility become central to competitive advantage, companies that invest early in these disruptive domains are positioned to lead the industry’s next growth cycle.