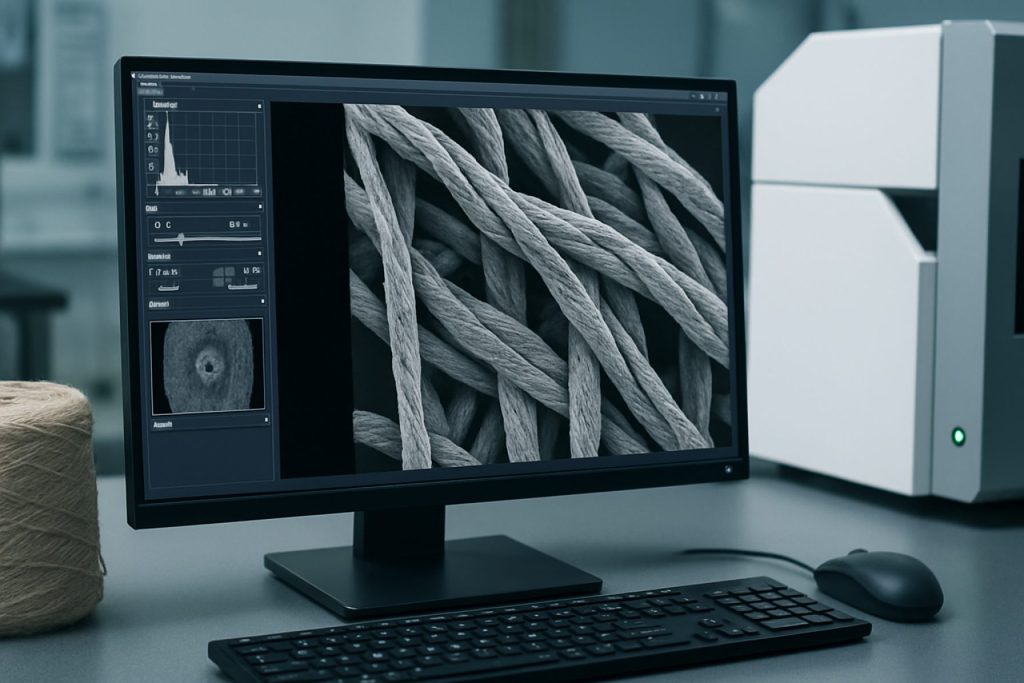
Table of Contents
- Executive Summary: Key Findings and Industry Drivers
- Technology Overview: How X-ray Tomography Enhances Fiber Analysis
- Global Market Forecasts (2025–2029): Growth Projections and Key Regions
- Competitive Landscape: Leading Companies and Innovators
- Emerging Applications: Advanced Textiles, Smart Fabrics, and Beyond
- Case Studies: Real-World Implementations and Success Stories
- Challenges and Limitations: Technical, Regulatory, and Cost Barriers
- Sustainability & Environmental Impact of X-ray Tomography in Textiles
- Regulatory Landscape and Standards (2025 Outlook)
- Future Outlook: Disruptive Trends and Investment Opportunities
- Sources & References
Executive Summary: Key Findings and Industry Drivers
Textile X-ray tomography is emerging as a transformative technology for fiber analysis, driven by demands for advanced quality control, sustainability, and process optimization in the textile industry. In 2025, industry adoption of this technique is accelerating, enabled by recent advancements in X-ray imaging resolution, automation, and data analytics. X-ray tomography provides unparalleled three-dimensional, non-destructive visualization of internal fiber structures, offering insights unattainable by traditional microscopy or surface inspection methods.
- Quality and Process Control: Leading textile manufacturers are increasingly integrating high-resolution X-ray computed tomography (CT) into their R&D and production workflows to detect defects, measure fiber orientation, and assess porosity or density variations. For example, Carl Zeiss AG has developed nano-CT systems that deliver sub-micron resolution, allowing textile engineers to optimize spinning, weaving, and nonwoven processes with greater precision.
- Sustainability and Material Characterization: The shift towards recycled and bio-based fibers has intensified the need for accurate fiber identification and structural analysis. X-ray tomography enables manufacturers to compare virgin and recycled fibers at the microstructural level, supporting certification and circular economy initiatives. Companies such as Bruker Corporation are offering tailored solutions for fiber composite and textile analysis, directly addressing sustainability goals.
- Automation and AI Integration: Recent years have witnessed the integration of artificial intelligence and machine learning algorithms with X-ray tomography data, automating defect detection and classification while reducing operator subjectivity. RX Solutions is among the firms providing automated CT scanning platforms with advanced software for rapid, repeatable fiber characterization.
- Industry Collaboration and Standardization: Industry consortia and standards organizations, such as AATCC (American Association of Textile Chemists and Colorists), are actively exploring methods to standardize X-ray tomography protocols for fiber and yarn analysis, accelerating cross-sector adoption.
Looking ahead, the textile sector is poised for broader deployment of X-ray tomography systems, especially as cost barriers decline and user-friendly software matures. The next few years will likely see further integration with digital manufacturing workflows, enabling real-time feedback and more robust traceability across the textile value chain. The technology’s role in driving efficiency, product innovation, and environmental stewardship positions it as a key enabler of the industry’s ongoing transformation.
Technology Overview: How X-ray Tomography Enhances Fiber Analysis
X-ray tomography, particularly micro-computed tomography (micro-CT), has become an indispensable tool for detailed fiber analysis in the textile industry, offering non-destructive 3D imaging of fiber architectures at micron-scale resolution. As of 2025, this technology is increasingly being adopted by textile manufacturers and research institutions to obtain comprehensive insights into fiber orientation, diameter distribution, porosity, and structural integrity—all critical parameters for product development and quality assurance.
Modern systems utilize advanced X-ray sources and high-resolution detectors that enable visualization of both natural and synthetic fibers within yarns, fabrics, and composite reinforcements. For example, Carl Zeiss AG and Bruker Corporation have developed X-ray microscopes capable of resolving features down to sub-micron levels, crucial for analyzing fine fiber blends or technical textiles.
Recent years have seen the integration of automated image analysis software that can process tomographic datasets to quantify fiber volume fraction, orientation distribution, and detect defects such as broken or kinked fibers. This automation is key for scaling up the technology in industrial settings. Companies like RX Solutions and Nikon Corporation are providing solutions that combine high-throughput scanning with AI-driven analytics, allowing for batch inspection and real-time feedback in manufacturing environments.
In terms of materials, X-ray tomography is proving particularly valuable for next-generation fibers and composites, such as carbon fiber-reinforced polymers and high-performance aramids. Detailed 3D fiber mapping has enabled researchers and engineers to optimize weaving patterns, reduce weak spots, and validate simulation models, thereby accelerating development cycles for functional textiles used in aerospace, automotive, and protective clothing sectors. Institutions like Deutsche Institute für Textil- und Faserforschung are actively applying micro-CT to monitor fiber dispersion and alignment during textile processing.
Looking ahead, further miniaturization of X-ray sources, enhanced detector sensitivity, and advances in computational reconstruction are expected to bring faster scan times and higher throughput by 2027. This will facilitate broader adoption not just in R&D labs but also on production floors, supporting the textile sector’s push towards digitalization and traceability. With ongoing collaborations between technology providers and textile manufacturers, X-ray tomography is set to become a routine part of quality and innovation workflows in the industry’s near future.
Global Market Forecasts (2025–2029): Growth Projections and Key Regions
Textile X-ray tomography, a non-destructive imaging technique used for fiber analysis, is poised for substantial growth between 2025 and 2029 as industries prioritize quality control, material innovation, and sustainability. The adoption of advanced computed tomography (CT) systems in textile manufacturing and research is driven by increasing demands for detailed fiber characterization and defect detection, especially in high-value technical textiles and composites.
Key market players such as Carl Zeiss AG and Bruker Corporation are expanding their X-ray microscopy portfolios with systems capable of resolving micron-scale textile structures in three dimensions. These advancements enable precise measurement of fiber orientation, porosity, and damage, which are critical for applications in automotive, aerospace, medical, and smart textiles.
Regionally, Europe and North America are expected to lead adoption due to robust textile research infrastructure and a strong focus on high-performance materials. Projects funded by the European Union, such as those involving the European Center for Innovative Textiles (CETI), are accelerating the integration of X-ray tomography in textile R&D. In North America, collaborations between academic institutions and manufacturers continue to drive innovation in fiber analysis methodologies.
Asia-Pacific markets, particularly China and Japan, are projected to see rapid increases in X-ray tomography adoption, fueled by investments in smart manufacturing and textile quality standards. Leading industrial X-ray solution providers like Rigaku Corporation are enhancing their offerings to meet the region’s growing demand for sophisticated fiber analysis tools.
- 2025–2026: Market growth is expected to be propelled by the textile industry’s push for automated quality inspection and traceability, with new installations of high-resolution CT systems in both established and emerging textile hubs.
- 2027–2029: The focus will likely shift towards AI-powered analysis and cloud-based data management, allowing real-time monitoring of textile processes and predictive maintenance. Integration with smart factory platforms is anticipated to become standard in leading textile production facilities.
With ongoing developments in X-ray source technology, detector sensitivity, and image reconstruction algorithms, the global market for textile X-ray tomography is forecasted to grow at a robust pace. The technology’s ability to deliver actionable insights on fiber structure and integrity is expected to solidify its role in the next generation of textile manufacturing and R&D worldwide.
Competitive Landscape: Leading Companies and Innovators
The competitive landscape for textile X-ray tomography, specifically in fiber analysis, is rapidly evolving as advanced imaging technologies become increasingly integral to quality assurance and product development within the textile industry. As of 2025, a handful of specialized imaging and metrology companies dominate this niche sector, each bringing unique strengths in hardware, software, and application-specific expertise.
Leading the field is Carl Zeiss AG, whose X-ray microscopy systems are widely adopted for non-destructive three-dimensional analysis of textile fibers. ZEISS’s solutions support ultra-high resolution imaging, enabling the inspection of fiber orientation, cross-sectional geometry, and internal defects without sample destruction—a critical advantage for research and industrial quality control. ZEISS continues to refine its hardware for faster scan times and automated workflows, and is investing in AI-driven image analysis to streamline fiber segmentation and quantitative measurement.
Another major player, Bruker Corporation, leverages its expertise in micro-computed tomography (micro-CT) to address the needs of textile manufacturers and researchers. Bruker’s SkyScan systems offer sub-micron resolution, supporting detailed analysis of fiber blends, porosity, and composite structures. Bruker is also collaborating with textile institutes to develop standardized protocols for fiber assessment, aiming to accelerate industrial adoption and regulatory acceptance.
Meanwhile, Rigaku Corporation is making significant strides with its modular X-ray CT instruments, which combine flexibility with high throughput for inline textile inspection. Rigaku’s systems are gaining traction for their ability to integrate into existing production lines, allowing real-time monitoring of fiber alignment and integrity—features increasingly important as manufacturers strive for zero-defect production.
Innovation is also driven by startups and academic-industry partnerships. For example, Xnovo Technology is emerging as a notable innovator, providing advanced reconstruction software optimized for fiber materials, enabling faster, artifact-free 3D models from X-ray data. Their collaborations with textile research centers are focused on automating fiber orientation and diameter analysis, addressing a key bottleneck in digital textile characterization.
Looking ahead to the next few years, the sector is expected to see increased convergence between X-ray tomography and machine learning, with companies investing in automated defect detection and digital twin solutions for smart manufacturing. As textile sustainability and traceability become more critical, X-ray tomography is poised to play a vital role in certifying recycled content and validating fiber origins, further expanding its competitive landscape and market relevance.
Emerging Applications: Advanced Textiles, Smart Fabrics, and Beyond
Textile X-ray tomography, particularly X-ray computed tomography (XCT), has rapidly advanced as a pivotal tool for fiber analysis in advanced textiles and smart fabrics. This non-destructive imaging technique enables researchers and manufacturers to visualize and quantify the three-dimensional structure of textile fibers, yarns, and fabrics at micron and sub-micron scales. As of 2025, several industry leaders and research-focused organizations are developing and deploying XCT systems specifically tailored for textile analysis.
Key developments include the integration of high-resolution micro-CT scanners into textile R&D labs, allowing for detailed analysis of fiber orientation, porosity, and the spatial relationships between functional additives or embedded sensors. Companies such as Carl Zeiss AG and Bruker Corporation have introduced XCT systems with specialized sample holders and software solutions for fibrous materials, supporting automated segmentation and quantitative analysis of fiber networks. These capabilities are essential for the development of smart fabrics, where performance often hinges on the precise placement and connectivity of conductive or responsive fibers.
Recent years have also seen collaborations between textile manufacturers and instrument suppliers to optimize XCT protocols for diverse applications. For instance, USTER Technologies is working on integrating advanced imaging with traditional fiber property testing, aiming to provide holistic quality assessments for high-performance textiles. Similarly, Thermo Fisher Scientific has demonstrated micro-CT’s utility in mapping the distribution of functional elements in smart yarns, such as those used in wearable sensors and e-textiles.
Looking ahead to the next few years, the adoption of textile X-ray tomography is expected to grow, driven by the need for precision in advanced textile manufacturing and increasing demand for smart textiles in medical, aerospace, and consumer applications. Ongoing improvements in scanner resolution, speed, and AI-powered image analysis promise even greater insights into fiber morphology, damage mechanisms, and the effects of finishing processes. These advances will support the design of textiles with tailored mechanical, electrical, and sensory properties, facilitating the commercialization of next-generation smart fabrics. Industry collaborations and standardization efforts—such as those promoted by bodies like AATCC—are likely to accelerate the integration of XCT into routine textile quality control and innovation pipelines through 2025 and beyond.
Case Studies: Real-World Implementations and Success Stories
In 2025, the deployment of X-ray tomography for fiber analysis in the textile industry has transitioned from experimental phases to real-world applications, offering unprecedented insights into fiber structure, orientation, and defects. High-resolution computed tomography (CT) systems are now being utilized by textile manufacturers and research institutions to non-destructively analyze yarn and fabric samples, leading to improved product quality and process optimization.
One notable implementation is by Carl Zeiss AG, whose X-ray microscopy solutions have been adopted by textile research centers in Europe. These systems allow for 3D imaging of fiber architecture within technical textiles and composites, supporting the development of lightweight, high-strength materials for automotive and aerospace industries. Zeiss reports that textile labs using their Xradia platforms have achieved sub-micron resolution, enabling precise measurement of fiber diameter distributions, alignment, and porosity—parameters critical to the performance of advanced woven and nonwoven fabrics.
In Asia, Rigaku Corporation has partnered with leading textile manufacturers to integrate micro-CT scanners into quality control workflows. These scanners provide automated quantitative analysis of fiber bundles and detect internal defects such as voids or inclusions, which are otherwise invisible with surface inspection. According to Rigaku, their customers have reported significant reductions in material wastage and improved consistency in fabric strength and elasticity since adopting micro-CT-based inspection.
On the academic front, the Deutsche Institute für Textil- und Faserforschung Denkendorf (DITF) in Germany has published data on using X-ray tomography for the analysis of recycled fiber blends. By reconstructing 3D fiber networks, DITF researchers can differentiate between virgin and recycled fibers, supporting efforts to increase the content of recycled materials in new textiles without compromising mechanical performance. The ability to quantify blending ratios and monitor fiber integrity is seen as a key enabler for sustainability and closed-loop recycling in the industry.
Looking ahead, industry leaders anticipate broader adoption of X-ray tomography as systems become more affordable and user-friendly. Automated image analysis powered by AI is poised to further accelerate data interpretation, transforming large-scale fiber analytics into a routine part of textile manufacturing. As such, X-ray tomography is expected to play a central role in quality assurance, innovation, and sustainability initiatives across the global textile sector in the coming years.
Challenges and Limitations: Technical, Regulatory, and Cost Barriers
Textile X-ray tomography has emerged as a promising tool for advanced fiber analysis, offering unprecedented 3D visualization of fibrous structures. However, the widespread adoption of this technology in the textile sector faces several challenges and limitations across technical, regulatory, and cost dimensions as of 2025 and in the near future.
- Technical Barriers: High-resolution X-ray tomography systems, particularly those capable of distinguishing individual fibers in complex textile assemblies, require precision instrumentation and optimization for textile-specific parameters. Key challenges include achieving sufficient contrast between fibers of similar composition, minimizing sample damage due to X-ray exposure, and handling the large volumes of data generated by 3D scans. System integration for high-throughput industrial environments remains complex; for example, Carl Zeiss AG highlights ongoing developments in micro- and nano-CT systems to address resolution and speed for soft materials like textiles. Despite these advances, robust automated segmentation and analysis algorithms tailored to mixed natural and synthetic fibers are still under development, as noted by Bruker Corporation.
- Regulatory and Safety Considerations: The use of X-ray-based imaging technologies in industrial settings requires strict compliance with radiation protection regulations. In regions such as the EU and North America, operators must adhere to guidelines set by regulatory bodies to ensure workplace safety, necessitating comprehensive training and facility adaptations. Additionally, the use of X-ray equipment may require periodic certification and calibration, further complicating deployment. Organizations like OEKO-TEX® Association are monitoring the implications of advanced textile testing methods, although specific standards for X-ray tomography in textiles are still evolving.
- Cost Barriers: The acquisition and maintenance costs of high-performance X-ray tomography systems remain significant, often limiting adoption to research institutes and large manufacturers. The financial outlay includes not only the equipment itself but also ancillary infrastructure for data processing and storage. While companies like Rigaku Corporation are working to develop more compact and cost-efficient systems, achieving a price point suitable for widespread industrial or quality control use remains a challenge for the coming years.
Looking ahead, overcoming these barriers will be critical to the broader integration of X-ray tomography in textile fiber analysis. Progress is expected as technology providers collaborate more closely with textile manufacturers to co-develop application-specific solutions, and as regulatory frameworks adapt to encompass advanced imaging technologies.
Sustainability & Environmental Impact of X-ray Tomography in Textiles
Textile X-ray tomography is increasingly recognized for its transformative potential in advancing the sustainability agenda within the fiber and textile analysis sector. As 2025 unfolds, leading equipment manufacturers and research institutions are refining the technique to minimize its environmental footprint, while simultaneously enabling deeper insights into fiber morphology, blend uniformity, and structural integrity.
Traditionally, fiber analysis required destructive sample preparation and chemical treatments, generating hazardous waste and consuming significant resources. In contrast, modern X-ray computed tomography (XCT) systems offer non-destructive, label-free imaging that preserves samples for further analysis or reuse. This attribute directly supports waste reduction initiatives and aligns with circular economy principles promoted by industry organizations such as Textile Exchange.
Recent advances from equipment leaders such as Carl Zeiss Microscopy and Bruker have further improved instrument energy efficiency and scan speed. These developments reduce both the operational carbon footprint and the physical energy required per analysis. For instance, Zeiss’ new generation X-ray microscopes employ optimized detectors and advanced reconstruction algorithms that cut energy consumption and analysis time, while maintaining submicron image resolution—crucial for detailed fiber characterization.
Moreover, X-ray tomography’s ability to deliver exhaustive 3D structural data in a single scan reduces the need for multiple, redundant tests. This streamlined workflow lowers overall resource consumption, including chemicals, water, and disposable labware, which are significant contributors to the environmental impact of traditional textile analysis.
In 2025 and beyond, sustainability objectives are further driving collaborative efforts between X-ray equipment manufacturers and textile producers. For example, Uster Technologies is exploring integration of non-destructive imaging modalities to enhance fiber quality control without increasing laboratory waste or environmental burden. Similarly, research initiatives inspired by industry guidelines from groups such as EURATEX are evaluating lifecycle impacts of laboratory instrumentation, incentivizing the adoption of greener analytical technologies.
Looking forward, the continued refinement of X-ray tomography hardware and analytical protocols is expected to further decrease environmental impact, particularly as renewable energy becomes a more prominent power source for laboratory operations. As regulatory and consumer pressures for sustainable practices intensify, X-ray tomography is well positioned to become a core analytical tool in the drive toward greener, more transparent textile supply chains.
Regulatory Landscape and Standards (2025 Outlook)
The regulatory landscape for textile X-ray tomography is evolving rapidly as the technology gains traction in fiber analysis and quality assurance processes. In 2025, regulatory bodies and standards organizations are increasingly recognizing the transformative potential of non-destructive X-ray computed tomography (XCT) in providing detailed, three-dimensional insights into textile microstructures, particularly for synthetic and technical fibers. The demand for greater transparency and traceability in textile supply chains, along with stricter requirements for product performance and safety, is driving the integration of XCT into standardized testing protocols.
Internationally, the International Organization for Standardization (ISO) has been engaged in updating and developing standards for advanced non-destructive testing methods, including digital volume imaging. Committees such as ISO/TC 38 (Textiles) and ISO/TC 135 (Non-destructive testing) are reviewing the applicability of XCT for fiber orientation, porosity, and defect analysis in textiles. The harmonization of XCT methodologies is anticipated to lead to new or revised ISO standards in the near future, aimed at ensuring consistency and reproducibility of X-ray-based fiber characterization.
Within the European Union, regulatory frameworks are influenced by both product safety directives and sustainability goals. The European Apparel and Textile Confederation (EURATEX) and the European Commission are promoting the adoption of advanced analytical technologies to meet requirements on material traceability and recyclability, as set out in the EU Strategy for Sustainable and Circular Textiles. X-ray tomography is being considered as a tool to verify recycled content and fiber blends, which could become part of mandatory reporting under the upcoming Digital Product Passport system.
In the United States, the ASTM International Committee D13 on Textiles is monitoring the integration of X-ray tomography for fiber and yarn analysis. While current ASTM standards mainly address traditional mechanical and chemical testing, industry input is stimulating the development of guidelines for XCT validation and calibration, particularly for technical textiles in aerospace, automotive, and medical sectors.
On the manufacturer side, leading X-ray technology suppliers such as Carl Zeiss AG and Bruker Corporation are engaging with standards bodies and textile industry consortia to define best practices for XCT-based measurements. Collaborative pilot projects with textile manufacturers aim to demonstrate compliance with both existing and emerging standards, fostering trust in the technology’s accuracy and repeatability.
Looking ahead, the next few years are expected to bring increased standardization, regulatory clarity, and broader acceptance of X-ray tomography in fiber analysis—especially as industry and regulators align on protocols for data interoperability, privacy, and quality assurance. These advances are poised to make XCT an integral component of textile certification, sustainability verification, and product innovation frameworks by the late 2020s.
Future Outlook: Disruptive Trends and Investment Opportunities
Textile X-ray tomography is rapidly emerging as a transformative tool for fiber analysis, promising significant advancements in both industrial process control and R&D within the textile sector. As of 2025, several disruptive trends and investment opportunities are shaping the future landscape of this technology.
A notable trend is the acceleration of high-resolution, non-destructive imaging platforms tailored for textiles. X-ray computed tomography (XCT) systems historically used in materials science are being adapted to resolve the microstructure of natural and synthetic fibers, enabling comprehensive three-dimensional visualization and quantification of fiber orientation, porosity, and defects at the micron scale. For instance, Carl Zeiss AG has been advancing XCT solutions that cater to emerging demands in textile R&D, emphasizing automation and AI-driven image analysis.
In 2025, industry leaders and textile innovation centers are investing in X-ray tomography for quality assurance, particularly in high-performance sectors such as medical textiles, filtration media, and composites. Companies like Bruker Corporation are offering micro-CT systems that allow textile manufacturers to track changes in fiber distribution and assess the impact of finishing treatments or recycling processes on material integrity. This is especially relevant with the global push for sustainable textile manufacturing, as precise fiber analysis supports circular economy initiatives and regulatory compliance.
Another disruptive trend is the integration of tomographic data with digital twin frameworks and simulation platforms. By feeding real 3D fiber architectures into textile production models, companies can optimize weaving, knitting, or nonwoven manufacturing in silico, reducing trial-and-error and material waste. Organizations like Technische Universität Dresden are piloting such approaches, combining XCT data with advanced computational modeling to drive process innovation.
Looking forward, investment opportunities are expected to flourish in software development for faster image processing, cloud-based analytics, and AI-powered defect detection. Partnerships between textile manufacturers, instrument suppliers, and academic institutes are forecast to intensify, furthering the commercialization of tomography-guided fiber analysis. As pricing of high-resolution systems drops and operational workflows become more user-friendly, adoption of X-ray tomography in mainstream textile production is likely to accelerate, making 3D fiber analysis a standard for quality and innovation by the late 2020s.
Sources & References
- Carl Zeiss AG
- Bruker Corporation
- AATCC
- Nikon Corporation
- Deutsche Institute für Textil- und Faserforschung
- Rigaku Corporation
- USTER Technologies
- Thermo Fisher Scientific
- OEKO-TEX® Association
- Textile Exchange
- EURATEX
- International Organization for Standardization (ISO)
- European Apparel and Textile Confederation (EURATEX)
- European Commission
- ASTM International
- Technische Universität Dresden