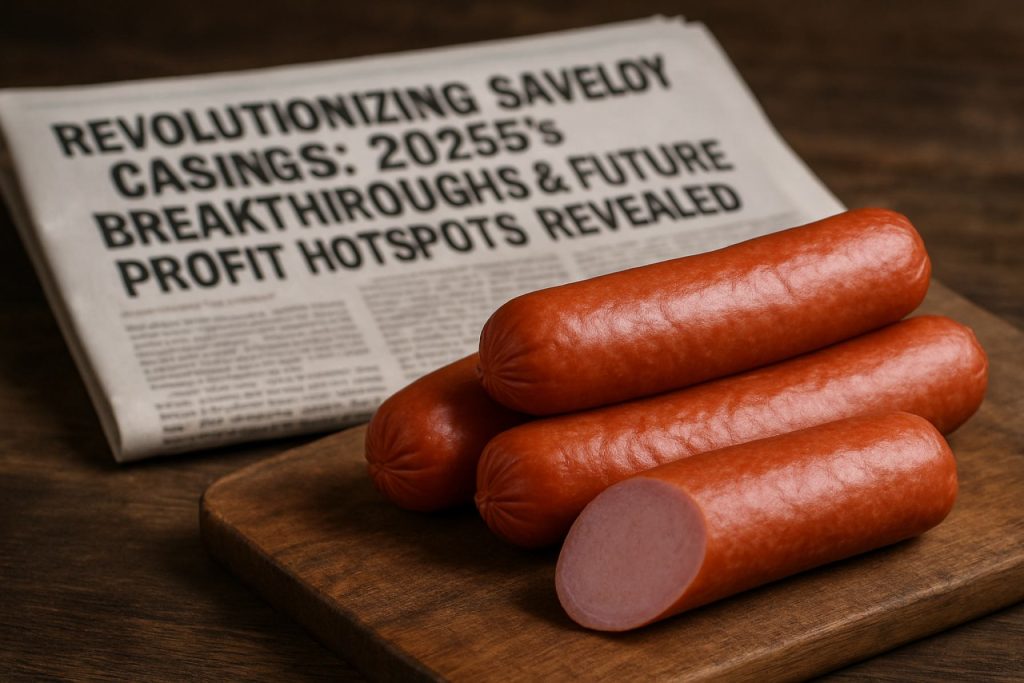
Table of Contents
- Executive Summary: 2025 Outlook for Saveloy Casing Manufacturing
- Global Market Forecast: Growth & Demand 2025–2030
- Emerging Technologies Transforming Saveloy Casings
- Key Manufacturers and Industry Players (Sources: devro.com, viskase.com, kalle.de)
- Sustainability Trends and Eco-Friendly Innovations
- Raw Materials: Advances in Collagen, Cellulose, and Alternatives
- Automation & Smart Manufacturing for Casings
- Regulatory Landscape and Compliance Challenges
- Competitive Analysis: Strategies and Market Share
- Future Opportunities: Investment Hotspots & Next-Gen Tech
- Sources & References
Executive Summary: 2025 Outlook for Saveloy Casing Manufacturing
The saveloy casing manufacturing sector is poised for continued technological evolution in 2025, driven by increasing demand for improved product consistency, sustainability, and operational efficiency. Traditionally dominated by natural casings sourced from animal intestines, the market has seen a significant shift toward cellulose and collagen-based alternatives. This transition is fueled by both supply chain stability and food safety concerns, as well as heightened consumer expectations for uniformity and appearance.
Leading manufacturers such as Devro and Viskase Companies, Inc. are investing in the latest extrusion and co-extrusion technologies to enhance the mechanical properties of edible and non-edible casings. These advancements enable higher production speeds, better diameter control, and customization options—critical for large-scale saveloy producers seeking to differentiate their products. The adoption of precise automated systems, including inline quality monitoring and digital data logging, is becoming standard across top-tier manufacturing lines.
Sustainability is an increasingly important factor shaping technology investments. Producers such as Kalle GmbH are developing casings made from renewable or recycled materials, aiming to reduce the industry’s environmental footprint. Water and energy-saving initiatives in casing production are being promoted by industry bodies such as the International Sausage Casings Association (ISCA), with member companies adopting best practices for waste minimization and process optimization.
Another notable trend for 2025 is the application of antimicrobial coatings and barrier technologies, which extend shelf life and improve food safety in ready-to-eat sausage products like saveloys. Companies including Viskase Companies, Inc. have introduced new product lines featuring enhanced functional casings, enabling manufacturers to address regulatory and consumer demands for cleaner labels and reduced additives.
Looking ahead, the sector is expected to see further integration of digital technologies such as real-time production analytics and traceability solutions, supporting both quality assurance and compliance with evolving international standards. With ongoing R&D collaborations and pilot projects among leading suppliers and food processors, the saveloy casing manufacturing landscape in 2025 and beyond will likely be defined by continued innovation, sustainability, and responsiveness to dynamic market requirements.
Global Market Forecast: Growth & Demand 2025–2030
The global market for saveloy casing manufacturing technologies is poised for notable growth during 2025–2030, driven by evolving consumer preferences, advancements in production methods, and expanding international demand for processed meat products. As of 2025, the sector is experiencing increased investment in both natural and artificial casing technologies, with a particular focus on scalability, hygiene, and automation.
Key players such as Devro plc and Viskase Companies, Inc. are investing heavily in research and development to optimize collagen and cellulose casings specifically tailored for saveloy and similar cooked sausage applications. These efforts are yielding casings with improved strength, flexibility, and uniformity, addressing the industry’s demand for high-speed, automated filling processes while maintaining product consistency.
Recent years have seen a shift toward plant-based and biodegradable casing alternatives, reflecting both regulatory trends and consumer sustainability concerns. Viskase Companies, Inc. has expanded its product portfolio to include casings that cater to vegetarian and vegan saveloy formulations. Similarly, World Casing Corporation reports growing inquiries from manufacturers seeking to diversify casing materials without compromising traditional texture and bite.
Geographically, Europe and Asia-Pacific remain the largest markets for saveloy casing technologies, but increased adoption is anticipated in Latin America and Africa as processed meat consumption rises. Major European casing manufacturers, including Kalle GmbH, are scaling up production to meet anticipated demand surges, citing improved logistics and strategic partnerships with regional distributors.
Automation and digitalization of casing production lines are central to the industry’s outlook through 2030. Companies are integrating advanced inline quality monitoring and traceability systems in their manufacturing facilities to enhance food safety and reduce waste. For example, Devro plc has reported investments in smart manufacturing technologies to streamline production and respond flexibly to custom sizing requests from saveloy producers.
Given these trends, the saveloy casing manufacturing sector is expected to achieve steady growth rates, with technological innovation, sustainability, and regional market expansion as primary drivers. The collaborative efforts among leading casing producers to address both traditional and emerging market needs will likely shape the competitive landscape over the next five years.
Emerging Technologies Transforming Saveloy Casings
In 2025, saveloy casing manufacturing is witnessing significant transformation driven by both technological advancements and evolving consumer demands. Traditional saveloy casings, often made from natural pork or beef intestines, are increasingly being supplemented—or even replaced—by innovative collagen and plant-based alternatives. This shift is largely fueled by the push for greater efficiency, consistency, and sustainability in sausage production.
One of the most prominent trends is the widespread adoption of highly automated production lines for collagen casings. Leading manufacturers such as Devro have invested in state-of-the-art extrusion and crosslinking technologies, enabling more precise control over casing diameter, strength, and permeability. These systems integrate real-time quality monitoring through advanced sensors, reducing waste and ensuring uniformity—a critical factor as high-speed sausage filling machines become standard in the industry.
Another pivotal development is the rise of plant-based casing technologies. Responding to the burgeoning market for vegetarian and vegan saveloys, companies like Viskase Companies, Inc. are scaling up production of cellulose and alginate casings. These alternatives are not only allergen-free but also biodegradable, aligning with increasingly stringent regulatory and consumer sustainability expectations. In 2025, further improvements in the gelling and strength properties of alginate casings are anticipated, facilitating their use in both traditional and novel saveloy formulations.
Meanwhile, hybrid casings—combining collagen and plant-derived materials—are emerging as a solution to bridge performance gaps between natural and synthetic options. Firms such as Nitta Gelatin Inc. are developing new composite casing materials with enhanced elasticity and improved barrier properties, which cater to the unique texture and flavor requirements of saveloys. These efforts are complemented by research into edible coatings that can impart antimicrobial features, thereby extending shelf life and reducing the need for preservatives.
Looking ahead, the saveloy casing sector is poised for continued innovation. The integration of artificial intelligence in process control, further enhancements in edible and biodegradable casings, and greater customization for regional tastes are all expected to shape the market over the next several years. With leading manufacturers continually expanding their R&D and production capabilities, the outlook for saveloy casing technology is one of rapid modernization, improved sustainability, and growing product diversity.
Key Manufacturers and Industry Players (Sources: devro.com, viskase.com, kalle.de)
The global saveloy casing manufacturing sector in 2025 is dominated by a handful of specialized companies, primarily focusing on advanced sausage casing technologies that ensure product consistency, safety, and scalability. The leading manufacturers—Devro, Viskase Companies, Inc., and Kalle GmbH—continue to shape industry trends through innovative materials and production processes.
Devro, headquartered in Scotland, remains a significant player with its collagen casing technologies, which are widely used in the production of saveloys and similar cooked sausages. In recent years, Devro has focused on optimizing its collagen extraction and processing methods, leveraging automation and quality control systems to boost efficiency and reduce production waste. The company’s 2024-2025 product lines emphasize both standard and customized casings, targeting regional preferences in texture and diameter, while also prioritizing sustainability by reducing energy consumption per unit of output (Devro).
Viskase Companies, Inc., a US-based multinational, continues to advance its expertise in cellulose and fibrous casings, both of which are integral to the manufacture of saveloys. Recent technological upgrades include improved permeability controls and enhanced peeling characteristics, which facilitate high-speed, automated sausage production lines. Viskase’s global network of production and technical support centers enables real-time customer collaboration and rapid adaptation to shifting market demands in Europe, Australia, and Asia, where saveloy consumption is strong (Viskase Companies, Inc.).
Kalle GmbH, based in Germany, is at the forefront of developing functional casings—casings that impart additional value through smoke flavoring, color transfer, or antimicrobial properties. In 2025, Kalle’s innovations include new multi-layer casings engineered for improved moisture retention and product shelf life, responding to consumer and retailer demand for longer-lasting, high-quality saveloys. The company’s emphasis on food safety and traceability is supported by digital batch monitoring systems, supporting global quality standards and regulatory compliance (Kalle GmbH).
Looking to the next few years, these manufacturers are investing in sustainable raw material sourcing and biodegradable casing solutions, aligning with consumer interest in eco-friendly food packaging. The integration of data-driven quality assurance and process automation is expected to further reduce costs and improve product uniformity, maintaining the leading positions of these key industry players while setting new benchmarks for the saveloy casing sector worldwide.
Sustainability Trends and Eco-Friendly Innovations
Sustainability and environmental stewardship have become central priorities in saveloy casing manufacturing, with 2025 marking a year of accelerated adoption of eco-friendly technologies and practices. Traditionally, saveloy casings—integral to the production of this popular sausage—have relied on both natural (animal-derived) and synthetic materials, with the latter often based on plastics such as polyamide or cellulose. However, mounting regulatory pressure and consumer demand for greener products are catalyzing innovation across the sector.
Manufacturers are increasingly investing in the development and commercialization of biodegradable and compostable casing materials. For example, Devro plc, a leading global supplier of collagen casings, has intensified research into casings derived from sustainable, traceable animal sources, emphasizing reduced water usage and lower greenhouse gas emissions throughout their production processes. Devro’s 2025 sustainability roadmap sets targets for a 30% reduction in carbon footprint per unit of product and expanded use of renewable energy in manufacturing operations.
On the synthetic front, Viskase Companies, Inc. is piloting new cellulose-based casings incorporating renewable feedstocks and non-toxic additives, aiming to enable easier post-use composting and recycling. The company’s recent public disclosures reveal plans to phase in these next-generation casings across European and North American facilities by 2026, aligning with tightening EU packaging directives and the broader food industry’s shift toward circular economy models.
Another breakthrough comes from Kalle GmbH, which in 2025 launched a line of plant-based, GMO-free casings utilizing industrial hemp fibers. These casings not only reduce reliance on petrochemicals but also support regenerative agriculture practices, as hemp cultivation is associated with soil improvement and lower pesticide requirements. Initial field trials report comparable performance to traditional plastic casings, with added benefits in terms of end-of-life compostability.
Industry bodies such as the International Sausage Casing Association are also fostering sustainability by issuing updated guidelines in 2025 for the environmental assessment of casing production, including lifecycle analysis and best practices for waste minimization. These standards are expected to inform procurement decisions by major food producers and shape regulatory compliance in key markets.
Looking ahead, the transition to eco-friendly casing technologies is projected to accelerate, driven by ongoing R&D investments, consumer expectations for transparency, and policy incentives. The sector is poised to deliver measurable reductions in environmental impact while maintaining the quality and functionality required for saveloy production.
Raw Materials: Advances in Collagen, Cellulose, and Alternatives
The manufacturing technologies for saveloy casings are being rapidly transformed by advances in raw materials, especially in collagen, cellulose, and alternative substrates. As of 2025, manufacturers are responding to both regulatory pressures and evolving consumer preferences for clean label, allergen-free, and sustainable products. This has spurred significant investment and innovation in the sourcing, processing, and application of casing materials.
Collagen casings, derived primarily from bovine and porcine hides, continue to dominate the market due to their ease of use and consistency in high-speed, automated sausage production. Recent years have seen leading suppliers such as Devro plc and Viskase Companies, Inc. invest in proprietary purification and cross-linking processes that improve casing strength, bite, and barrier properties while reducing the need for chemical additives. These technical refinements allow for thinner, yet more robust, casings—enhancing yield and reducing material waste.
In parallel, cellulose casings, favored for their uniformity and permeability, are undergoing their own evolution. Companies like Viskase Companies, Inc. have introduced cellulose casings with enhanced smoke permeability and improved stripping characteristics, tailored for high-volume cooked sausage applications such as saveloy. Ongoing R&D is directed toward developing cellulose casings from more sustainable wood pulp sources and incorporating compostable or biodegradable features, aligning with industry-wide environmental goals.
Looking to alternatives, plant-derived and novel biopolymer casings are garnering growing interest. FANAGORIA and other emerging players are experimenting with polysaccharide and protein blends that can mimic the performance of collagen and cellulose without relying on animal or traditional wood sources. These alternatives are particularly attractive for markets demanding vegetarian, vegan, or allergen-free products. While not yet mainstream, pilot-scale production and commercial trials are expected to accelerate in the next few years, supported by partnerships between casing specialists and food technology startups.
The outlook for saveloy casing manufacturing technologies in the near term is one of incremental, yet impactful, innovation. The primary focus remains on efficiency—maximizing material functionality while minimizing environmental impact and costs. As regulatory frameworks in regions such as the EU and North America tighten around food contact materials and labeling, further advances in traceable sourcing, process transparency, and “clean” manufacturing are anticipated. The coming years will likely see a broader adoption of hybrid approaches, where traditional materials are enhanced or partially replaced by next-generation alternatives, shaping the future landscape of saveloy casing production.
Automation & Smart Manufacturing for Casings
The saveloy casing manufacturing sector is undergoing significant transformation in 2025, driven by the adoption of automation and smart manufacturing technologies. Traditionally reliant on labor-intensive processes, casing production—whether for collagen, cellulose, or synthetic types—now increasingly leverages robotics, IoT (Internet of Things), and advanced monitoring systems to optimize efficiency, quality, and traceability.
Key industry players are investing in fully or semi-automated production lines that integrate real-time quality control and data analytics. For example, Devro, a leading collagen casing manufacturer, has implemented automated extrusion and drying systems to reduce human error and increase throughput. Their factories feature in-line sensors and centralized process control dashboards, enabling operators to monitor material consistency and intervene quickly if parameters deviate. Similarly, Viskase Companies, Inc. has reported enhancements in cellulose casing production, using automated cutting, shirring, and packaging lines to standardize output and reduce waste.
Machine vision and AI-guided inspection are becoming standard for identifying defects such as air pockets or thickness variations. Nitta Casings Inc. has piloted systems using high-resolution cameras and pattern recognition algorithms to flag non-conforming casings before further processing, minimizing costly recalls and rework. These smart solutions also generate actionable data, supporting continuous improvement and regulatory compliance.
IoT-enabled equipment is another emerging trend, with sensors embedded throughout the production environment. This technology allows for predictive maintenance; for instance, vibration and temperature data from extrusion machinery can indicate wear before failures occur, reducing unplanned downtime. Companies like Kalle GmbH are trialing cloud-connected systems that provide remote diagnostics and performance analytics, accessible to both plant engineers and equipment suppliers.
Looking ahead, industry analysts expect further integration of digital twins—virtual replicas of manufacturing lines—enabling simulation of process changes and swift troubleshooting. Cyber-physical systems and interoperability with ERP (Enterprise Resource Planning) platforms will streamline supply chain management, enhancing responsiveness to market shifts.
Overall, the outlook for saveloy casing manufacturing technologies in 2025 and beyond is characterized by accelerating automation and smart factory adoption. This not only addresses ongoing labor shortages but also positions manufacturers to meet stringent quality demands and sustainability targets, ensuring competitiveness in a rapidly evolving protein processing landscape.
Regulatory Landscape and Compliance Challenges
The regulatory landscape for saveloy casing manufacturing technologies in 2025 is shaped by evolving food safety standards, sustainability directives, and material innovation oversight. Manufacturers of both natural and artificial casings must navigate a complex framework of national and international regulations, with particular focus on traceability, allergen control, and permissible additives.
In the European Union, the implementation of the revised General Food Law Regulation (EU Regulation 178/2002) has heightened scrutiny over food contact materials, directly affecting casing producers. The European Food Safety Authority (EFSA) continues to evaluate and update lists of approved substances for edible and non-edible casings, with particular attention to plasticizers and colorants used in collagen and cellulose casings. Recent guidance has required manufacturers such as Devro plc to perform additional migration testing and submit comprehensive dossiers for new or modified casing materials.
In the United States, the Food and Drug Administration (FDA) enforces compliance through the Food Safety Modernization Act (FSMA), focusing on preventive controls throughout the supply chain. Major suppliers like Viskase Companies, Inc. have responded by investing in advanced traceability systems and allergen management protocols, aiming to preempt recalls and ensure rapid response to contamination events. The USDA Food Safety and Inspection Service (FSIS) has also intensified oversight of imported casings, particularly those of natural origin, requiring detailed origin documentation and residue testing.
Globally, there is increasing attention to sustainability and animal welfare in casing sourcing, echoing consumer demands and policy trends. The World Health Organization (WHO) and the Food and Agriculture Organization (FAO) have issued recommendations on the use of animal by-products, influencing manufacturers’ sourcing strategies. Companies such as Nitta Gelatin Inc. are investing in certifications like ISO 22000 and FSSC 22000 to demonstrate food safety and responsible sourcing, while also developing plant-based alternatives to meet future regulatory and market requirements.
Looking ahead, regulatory bodies are expected to further tighten restrictions on chemical additives and demand greater transparency in labeling, particularly for artificial and hybrid casings. Manufacturers anticipate increased compliance costs due to more rigorous documentation, batch-level traceability, and ongoing testing. At the same time, the push for harmonization of international standards—driven by organizations such as the International Organization for Standardization (ISO)—offers potential to streamline compliance for global operators. The next few years will see the saveloy casing sector balancing innovation with the need to meet stringent and evolving regulatory expectations.
Competitive Analysis: Strategies and Market Share
The competitive landscape of saveloy casing manufacturing technologies in 2025 is characterized by a blend of innovation, strategic partnerships, and a focus on sustainable practices. Market leaders and emerging players are actively investing in research and development to enhance product quality, reduce environmental impact, and meet evolving regulatory standards.
Key manufacturers such as Viskase Companies, Inc., Devro plc, and Kalle GmbH continue to dominate the global market. These companies leverage proprietary technologies to produce both natural and cellulose-based casings tailored for the unique requirements of saveloy production. Over the past year, Viskase Companies, Inc. has expanded its production capabilities in Europe and Asia, strategically positioning itself to serve growing demand in these regions and to offer high-performance, customizable casing solutions.
Meanwhile, Devro plc has adopted a dual strategy: investing in advanced collagen casing materials and collaborating with regional sausage producers to co-develop products suited to local tastes and processing conditions. The company’s 2024 annual report highlights their ongoing commitment to R&D, with particular attention to improving casing strength and uniformity, key attributes for consistent saveloy quality.
Sustainability is emerging as a significant differentiator. Kalle GmbH has introduced new eco-friendly cellulose casings, emphasizing reduced water and energy consumption during manufacturing, and improved biodegradability. These initiatives aim to align with both regulatory trends and the sustainability goals of major food producers. Such environmentally conscious product lines are expected to capture a larger share of the market as food manufacturers seek to enhance their green credentials.
On the supply chain front, manufacturers are strengthening relationships with saveloy processors and meat producers to ensure reliable sourcing and just-in-time delivery. This approach minimizes downtime for sausage makers and provides valuable feedback for iterative product improvement.
Looking ahead, the saveloy casing market is projected to see incremental growth through 2027, driven by rising demand in Asia-Pacific and Europe. Companies that prioritize technical innovation, flexible production, and eco-friendly materials are poised to gain market share. The competitive environment will likely intensify, with established firms defending their positions through patents, while new entrants attempt to disrupt with novel materials and process efficiencies. Strategic mergers and acquisitions may also shape the sector as companies seek to broaden their technology portfolios and market reach.
Future Opportunities: Investment Hotspots & Next-Gen Tech
The global saveloy casing manufacturing sector is entering a transformative phase in 2025, marked by a surge of innovation and capital influx. Traditionally dominated by natural casings, the market is seeing accelerated adoption of advanced collagen and cellulose casings, driven by shifting consumer preferences, regulatory demands, and efficiency needs. As regulatory frameworks emphasize food safety and traceability, manufacturers are investing in automation and digitalization to ensure compliance and consistency.
A prominent trend is the integration of high-precision extrusion and co-extrusion technologies in collagen casing production. Companies like Devro and Viskase Companies, Inc. are expanding their use of proprietary processing equipment that enhances casing uniformity and strength, optimizing throughput while reducing material waste. For example, Devro’s recent upgrades in their Czech and Chinese facilities focus on energy-efficient processes and closed-loop water systems, aligning with environmental mandates and cost efficiency goals (Devro).
Meanwhile, the adoption of automation and AI-driven quality control is becoming central to competitiveness. Sensor-based inspection systems now enable real-time detection of micro-defects in casing films, minimizing recalls and product loss. Kalle has piloted machine learning algorithms to adjust casing thickness and permeability dynamically, improving product consistency for high-speed sausage production lines (Kalle).
Investment hotspots are emerging in Asia-Pacific and Latin America, where expanding meat processing industries and fast-growing quick-service restaurant sectors fuel demand. Strategic alliances and direct investments are being made by global casing leaders to localize production and reduce logistics costs. For instance, Viskase Companies, Inc. announced capacity expansions in Brazil and the Philippines in response to regional growth (Viskase Companies, Inc.).
Looking ahead, the next few years are poised to see breakthroughs in biodegradable and edible casing materials, aligned with sustainability imperatives. R&D into plant-based polymers and modified cellulose offers the promise of new product lines that cater to clean-label and vegan meat analogues. Leading manufacturers are collaborating with food tech startups to trial next-gen casings that deliver traditional saveloy bite and texture but with reduced environmental impact (Devro). As these technologies move from pilot to commercial scale, the sector’s investment landscape will remain dynamic, guided by the twin imperatives of operational efficiency and sustainable innovation.