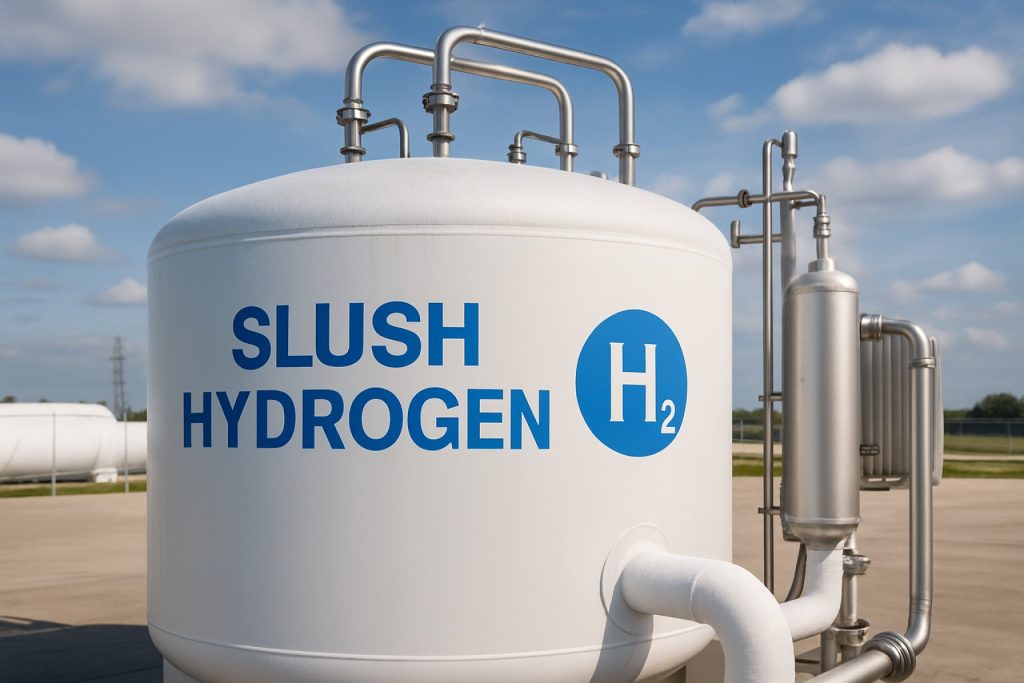
Table of Contents
- Executive Summary: The State of Slush Hydrogen Storage in 2025
- Core Principles: How Slush Hydrogen Storage Systems Work
- Key Industry Players and Official Technology Roadmaps
- Recent Breakthroughs: Materials, Safety, and System Integration
- Global Market Forecasts Through 2030: Capacity, Demand, and Growth Rates
- Cost Dynamics and Economic Viability Analysis
- Policy, Regulatory, and Safety Standards Shaping the Sector
- Major Deployment Projects: Case Studies from Leading Companies
- Competitive Landscape: Slush vs. Other Hydrogen Storage Solutions
- Future Outlook: Challenges, Opportunities, and Next Steps for Industry Leadership
- Sources & References
Executive Summary: The State of Slush Hydrogen Storage in 2025
Slush hydrogen storage systems represent a technologically advanced approach to hydrogen liquefaction and containment, offering increased density and improved thermal stability compared to traditional liquid hydrogen storage. As of 2025, global interest in hydrogen as a clean energy vector—particularly for aerospace, heavy transport, and emerging hydrogen infrastructure—has accelerated the exploration and limited-scale deployment of slush hydrogen technologies.
Slush hydrogen is a mixture of solid and liquid hydrogen at temperatures near the melting point of hydrogen (approximately 14 K), providing a higher volumetric density than liquid hydrogen. This higher density enables more efficient storage for applications where weight and space are critical, such as in launch vehicles and long-range aircraft. Recent years have seen major aerospace and technology companies, including Airbus and Arianespace, invest in research partnerships and demonstration programs to evaluate the feasibility of slush hydrogen storage for next-generation propulsion systems.
Current progress in 2025 is characterized by laboratory-scale demonstration units and early-stage prototype tanks. Airbus, for instance, has publicly outlined its exploration of cryogenic hydrogen storage and fueling for its ZEROe aircraft concepts, with slush hydrogen storage identified as a potential pathway to maximizing onboard energy density. Similarly, Lockheed Martin continues to refine cryogenic tank materials and insulation technologies to address boil-off management—a principal technical hurdle for slush hydrogen containment. Efforts by global industrial gas suppliers such as Linde and Air Liquide focus on advancing large-scale cryogenic infrastructure, which may provide enabling technologies for commercialization in the late 2020s.
Despite significant advances, commercialization of slush hydrogen storage systems remains in its infancy. The main technical barriers include precise temperature control, robust cryogenic tank design, and cost-effective slush production. However, industry outlooks anticipate that sustained investment and ongoing demonstration projects in the aerospace and clean transport sectors will drive incremental progress. By the late 2020s, pilot-scale deployment in space launch and long-range aviation is plausible, contingent upon the resolution of outstanding engineering challenges.
In summary, 2025 marks a period of accelerated research and strategic prototyping for slush hydrogen storage systems, with leading aerospace, industrial gas, and technology companies actively engaged in foundational development. The sector’s trajectory suggests a cautiously optimistic outlook for broader adoption as technical and economic barriers are addressed in the coming years.
Core Principles: How Slush Hydrogen Storage Systems Work
Slush hydrogen storage systems are engineered to leverage the unique thermophysical properties of slush hydrogen—a cryogenic mixture of solid and liquid hydrogen at temperatures near the hydrogen triple point (≈13.8 K). The core principle behind these systems is to capitalize on slush hydrogen’s increased density (up to 16% greater than liquid hydrogen) and reduced boil-off rates compared to conventional liquid hydrogen storage, which enhances storage efficiency and operational safety.
Producing slush hydrogen involves controlled cooling of liquid hydrogen below its melting point, often by depressurization or mechanical agitation, to induce the formation of solid hydrogen particles suspended within the liquid phase. Specialized cryogenic equipment is required for this process, including advanced insulation and precise temperature regulation systems, as hydrogen must be maintained at extremely low temperatures to prevent rapid phase changes and associated risks.
A typical slush hydrogen storage system in 2025 consists of a double-walled, vacuum-insulated vessel equipped with cryocoolers or subcooled helium heat exchangers to maintain the necessary low temperatures. Integrated mixing devices ensure uniform distribution of solid hydrogen particles, preventing stratification and enabling consistent withdrawal. The increased density of slush hydrogen allows for more compact storage solutions, which is particularly relevant for space launch vehicles and aerospace applications, where volume and mass constraints are critical.
In operation, slush hydrogen storage systems require robust monitoring and control mechanisms to manage pressure, temperature, and phase changes. Boil-off gas is minimized due to the system’s ability to absorb heat via the melting of suspended solid hydrogen, effectively serving as a thermal buffer. This results in improved storage durations and reduced hydrogen losses, an essential factor for both terrestrial and extraterrestrial missions.
- Key Components: Double-walled vacuum-insulated tanks, cryocoolers, mixing and agitation devices, advanced sensors for temperature and pressure, and sophisticated safety systems.
- Current Developments: As of 2025, organizations such as NASA and aerospace manufacturers are leading the advancement of slush hydrogen technology, with increasing focus on scalable ground storage and in-flight refueling systems.
- Outlook: With the global momentum for hydrogen as a clean energy carrier, slush hydrogen storage systems are expected to see expanded prototyping and pilot deployments over the next several years, particularly in sectors requiring ultra-high energy density and minimized hydrogen boil-off.
The successful implementation of slush hydrogen storage hinges on continued innovations in cryogenic engineering and material science, as well as close collaboration among industry leaders such as Air Liquide and governmental agencies focused on hydrogen technologies.
Key Industry Players and Official Technology Roadmaps
Slush hydrogen, a cryogenic mixture of solid and liquid hydrogen, is gaining renewed attention in the context of advanced energy storage and aerospace propulsion, due to its higher density and improved thermal properties compared to liquid hydrogen. As of 2025, significant developments in slush hydrogen storage systems are being spearheaded by a select group of industry players, primarily within the aerospace and energy infrastructure sectors.
Among the most prominent organizations actively advancing slush hydrogen storage technologies is NASA, which continues to explore slush hydrogen for space launch vehicle applications. Their focus is on achieving higher fuel mass fraction and improved storage efficiency, with recent efforts targeting novel tank designs and advanced slush production techniques. In parallel, European Space Agency (ESA) is also investigating cryogenic storage innovations, with slush hydrogen forming part of their roadmap for next-generation upper stage propulsion and long-duration deep space missions.
On the industrial side, companies such as Air Liquide and Linde continue to develop cryogenic hydrogen infrastructure, including storage systems that could be adapted for slush hydrogen. While their main commercial offerings currently focus on liquid hydrogen, both companies have publicly stated interests in advanced hydrogen storage solutions, which include slush hydrogen as a future possibility for improving transport density and reducing boil-off losses.
In Japan, Japan Aerospace Exploration Agency (JAXA) has a well-documented history of slush hydrogen research, with recent collaborative projects involving domestic industrial partners to design storage tanks and transfer systems compatible with high-density hydrogen. Their 2025 technology roadmap outlines plans for integrated ground and flight demonstrations over the next several years, aiming to validate slush hydrogen’s practical advantages in aerospace and possibly heavy transport applications.
Looking ahead, official technology roadmaps from these organizations converge on three main goals: increasing storage density, reducing hydrogen boil-off, and enabling safer, more efficient fuel management for large-scale applications. While commercial deployment of slush hydrogen systems remains nascent, ongoing pilot projects and prototype demonstrations are expected to yield critical data and drive industrial readiness between 2025 and 2030. As investment in hydrogen infrastructure accelerates worldwide, the role of slush hydrogen storage systems is set to expand, particularly where maximizing energy density is mission-critical.
Recent Breakthroughs: Materials, Safety, and System Integration
Slush hydrogen—an ultra-cold mixture of solid and liquid hydrogen—offers higher density and enhanced storage efficiency compared to conventional liquid hydrogen. Over the past two years, substantial breakthroughs have occurred in the materials, safety, and system integration of slush hydrogen storage systems, signaling promising advances as the sector moves into 2025.
Materials Innovation: Modern slush hydrogen storage demands tank materials capable of withstanding extreme cryogenic temperatures (below 14 K) and significant thermal cycling. Recent developments have centered on advanced composite materials and multilayer insulation systems. For example, aerospace suppliers and hydrogen storage specialists have jointly advanced carbon fiber–reinforced polymers with proprietary resin matrices, improving both strength and thermal insulation while reducing weight. Companies such as Airbus and Air Liquide have demonstrated new cryogenic liner technologies that mitigate hydrogen embrittlement and gas permeation, which are critical for safe, long-term containment of slush hydrogen.
Safety Enhancements: Safety remains paramount, given the volatility and low temperature of slush hydrogen. Recent test campaigns have led to the integration of advanced leak detection and venting systems, as well as robust emergency pressure-relief designs. In 2024, industrial suppliers introduced sensor arrays capable of real-time monitoring of stratification, phase changes, and micro-leaks inside storage tanks. Furthermore, organizations such as CEA (French Alternative Energies and Atomic Energy Commission) have released guidelines for slush hydrogen handling, focusing on reducing boil-off rates and preventing solid blockages in transfer lines.
System Integration: The challenge of integrating slush hydrogen storage into aerospace and mobility platforms is being addressed through modular system designs. Recent demonstrators by Airbus and Arianespace (for reusable launchers) have shown that integrated tank and transfer systems can maintain slush state for longer durations, reducing hydrogen losses and improving refueling turnaround times. These efforts are supported by automation and digital twin technologies, enabling predictive maintenance and optimization of cooling cycles.
Outlook for 2025 and Beyond: The coming years are expected to bring pilot deployments in both aerospace and high-performance mobility applications. Industry participants project that slush hydrogen storage will move from laboratory-scale demonstration to early commercial trials, particularly where volumetric efficiency and fast refueling are decisive. The next phase will likely emphasize further material robustness, life-cycle safety validation, and seamless system integration for operational platforms, driven by ongoing collaboration among leading aerospace and industrial gas companies.
Global Market Forecasts Through 2030: Capacity, Demand, and Growth Rates
The global market for slush hydrogen storage systems is poised for significant development as the demand for efficient and high-density hydrogen storage accelerates through 2030. Slush hydrogen—a mixture of solid and liquid hydrogen at temperatures below -253°C—offers superior volumetric density compared to conventional liquid hydrogen, making it attractive for applications in aerospace, advanced mobility, and large-scale hydrogen infrastructure.
By 2025, the installed capacity for slush hydrogen storage remains limited, primarily confined to research, pilot programs, and select demonstration projects. Major aerospace companies and energy conglomerates are actively exploring slush hydrogen storage for its benefits in reducing tank size and weight, which is particularly valuable for next-generation launch vehicles and future hydrogen-powered aircraft. For example, Airbus is investigating advanced cryogenic storage solutions as part of its ZEROe program, while ArianeGroup and NASA continue to test slush hydrogen in rocketry and space exploration contexts.
Market data from 2025 indicates that the global installed capacity of slush hydrogen storage systems is estimated to be less than 50 metric tons, with most deployments located in the United States, Europe, and Japan. Demand is projected to rise rapidly as hydrogen adoption expands, with compound annual growth rates (CAGR) for slush hydrogen storage anticipated in the range of 25-35% through 2030. This surge is driven by the proliferation of hydrogen-centric infrastructure, government decarbonization targets, and the need for more efficient energy carriers in long-duration transport.
- In the Asia-Pacific region, major industrial players such as Tokyo Gas Co., Ltd. and Mitsubishi Corporation are assessing slush hydrogen’s role in the future energy mix, with pilot facilities expected to commence operations by 2027.
- In Europe, collaborative projects led by organizations like Air Liquide and Linde plc are targeting scalable, safe, and cost-effective slush hydrogen storage to support the continent’s hydrogen backbone.
Looking ahead, global slush hydrogen storage capacity is forecast to exceed 200 metric tons by 2030, underpinned by increasing investment and technology maturity. However, widespread commercialization depends on overcoming technical challenges related to cryogenic management, cost reduction, and safety assurance. As standards and supply chains mature, slush hydrogen storage is expected to play a pivotal role in the decarbonized energy landscape and the hydrogen economy’s next phase of growth.
Cost Dynamics and Economic Viability Analysis
The economic viability of slush hydrogen storage systems is a subject of growing interest as hydrogen infrastructure expands in 2025 and beyond. Slush hydrogen, a mixture of liquid and solid hydrogen, offers a higher density than liquid hydrogen, which can significantly reduce storage volume requirements and associated costs—especially relevant for aerospace, energy, and mobility sectors. However, the unique technical demands of producing, storing, and handling slush hydrogen introduce both cost drivers and potential savings.
Currently, the primary cost components for slush hydrogen systems include advanced cryogenic production, specialized storage tank fabrication, insulation technologies, and safety systems. Manufacturers such as Air Liquide and Linde have developed expertise in cryogenic hydrogen systems, but slush hydrogen equipment typically commands a premium over conventional liquid hydrogen solutions due to its greater complexity. The additional requirement to maintain temperatures near 14 K and to manage solid-liquid phase transitions necessitates advanced materials and controls, pushing capital expenditures higher.
Despite these initial cost premiums, the denser storage achievable with slush hydrogen can yield downstream economic advantages. For instance, in aerospace applications, reduced tank size and mass translate to higher payload efficiency, which is a critical metric for both government and commercial launch programs. Ongoing demonstration projects, such as those involving NASA and its industry partners, are evaluating integrated slush hydrogen storage systems to quantify lifecycle cost reductions and operational efficiencies.
From an operational cost perspective, slush hydrogen’s enhanced density reduces boil-off losses compared to standard liquid hydrogen, potentially lowering recurring refueling and maintenance expenses. Companies such as Royal IHC and Cryostar, who supply cryogenic handling solutions, have reported that improvements in insulation and automated phase management are expected to further decrease operating costs over the next several years.
Looking to the near future, the outlook for cost reduction is positive as economies of scale and technology maturation take effect. With increased deployment—driven by the decarbonization efforts in aviation, shipping, and heavy industry—manufacturers anticipate incremental reductions in both capital and operational expenditures. Collaborative R&D, such as joint ventures between industrial gas suppliers and aerospace firms, is targeting cost parity with advanced liquid hydrogen systems by the late 2020s. As such, while slush hydrogen storage systems remain a premium option in 2025, their economic attractiveness is projected to improve, particularly where ultra-high-density storage confers significant value.
Policy, Regulatory, and Safety Standards Shaping the Sector
The regulatory landscape for slush hydrogen storage systems is rapidly evolving as governments and industry stakeholders address the unique challenges and opportunities associated with this advanced hydrogen storage technology. Slush hydrogen, a mixture of liquid and solid hydrogen, offers higher density and improved storage efficiency compared to conventional liquid hydrogen, but introduces new safety, handling, and regulatory considerations due to its ultra-low temperature and phase characteristics.
In 2025, policy frameworks at both national and international levels are beginning to specifically reference slush hydrogen as part of broader hydrogen strategies. The International Organization for Standardization (ISO) is actively working on updates to standards such as ISO 13985 (Liquid hydrogen — Land vehicle fuelling system interface), with working groups examining modifications necessary for slush hydrogen’s unique properties. These international standards set the foundation for regional and national bodies to develop more specific regulations.
The European Union, under the revised Alternative Fuels Infrastructure Regulation, is expected to publish guidance in 2025 that will include reference to slush hydrogen as a strategic storage medium for both mobility and grid-scale applications. At the same time, regulatory agencies like the European Committee for Standardization (CEN) and the Deutsches Institut für Normung (DIN) are updating codes related to cryogenic hydrogen storage to ensure safe design, operation, and emergency response protocols for slush systems. Efforts include specifying material compatibility, insulation requirements, and risk assessment methodologies tailored to the colder temperatures and higher densities of slush hydrogen.
In the United States, the U.S. Department of Energy and National Fire Protection Association (NFPA) are working with industry partners to develop best practices and fire codes for slush hydrogen storage and transfer. The American Society of Mechanical Engineers (ASME) is also reviewing pressure vessel and piping codes to account for slush hydrogen’s thermal and mechanical stresses.
Safety standards remain a top priority, with industry players such as Air Liquide and Linde participating in safety trials and sharing data with regulators to inform policy. These companies are contributing to a growing body of evidence supporting the safe handling and storage of slush hydrogen, including studies on insulation integrity, rapid phase transitions, and emergency venting procedures.
Looking ahead, it is expected that by 2026-2028, harmonized standards for slush hydrogen storage systems will emerge, enabling wider commercial deployment. The ongoing collaboration between industry, standards bodies, and regulators will be crucial to ensure that slush hydrogen storage solutions meet stringent safety, reliability, and environmental requirements as the hydrogen economy matures.
Major Deployment Projects: Case Studies from Leading Companies
Slush hydrogen—an ultra-cold mixture of liquid and solid hydrogen—offers significant advantages for energy density, boil-off reduction, and storage efficiency. As global demand for high-performance hydrogen storage grows, several leading organizations are advancing slush hydrogen storage solutions through large-scale projects and demonstrator programs. Recent years, especially leading into 2025, have seen increased momentum, with notable deployments in aerospace, space exploration, and advanced mobility sectors.
One of the most prominent initiatives is underway at NASA, which has prioritized slush hydrogen for next-generation launch systems. The agency’s research and demonstration programs at Kennedy Space Center and Stennis Space Center have advanced the engineering of slush hydrogen tanks, focusing on thermal management and transfer systems for future lunar and Mars missions. NASA’s public technical documentation cites successful tests of slush hydrogen storage and transfer, validating the reduced boil-off rates and improved mass efficiency compared to conventional liquid hydrogen tanks.
In the private sector, Ariens Company and partners have begun pilot projects in cryogenic hydrogen storage for advanced mobility and aerospace applications. These projects aim to demonstrate the practicality of slush hydrogen in refueling infrastructure and heavy-duty vehicle operations, where longer storage times with minimal losses are critical. While large-scale commercial deployment is still in the early stages, prototype systems have been constructed and are undergoing operational trials in collaboration with industry and government partners.
Meanwhile, in Japan, Japan Aerospace Exploration Agency (JAXA) has been at the forefront of slush hydrogen research for over a decade. Current projects focus on optimizing slush hydrogen production and storage methods for space launch vehicles. JAXA’s recent test campaigns have yielded slush hydrogen storage tanks capable of maintaining ultra-low temperatures during extended ground holds, a crucial step for future deep-space missions and reusable launch systems.
Looking to the next few years, the outlook for slush hydrogen storage systems is positive but cautious. Key challenges remain around large-scale production, long-term insulation, and safe transfer technologies. Nevertheless, as hydrogen gains traction for both terrestrial and space-based energy systems, the ongoing work by NASA, JAXA, and commercial partners points toward expanded field deployments and possible integration into commercial launch and mobility platforms by the late 2020s.
Competitive Landscape: Slush vs. Other Hydrogen Storage Solutions
As the hydrogen economy accelerates in 2025, slush hydrogen storage systems are emerging as a frontier technology in the competitive landscape of hydrogen storage solutions. Slush hydrogen—a cryogenic mixture of liquid and solid hydrogen—offers higher density than conventional liquid hydrogen, promising reduced storage volume and potentially lower boil-off losses. This positions slush hydrogen as a compelling alternative to compressed gaseous and liquid hydrogen storage, particularly for applications demanding high gravimetric and volumetric efficiencies, such as aerospace and advanced mobility sectors.
Leading industrial gas suppliers and aerospace manufacturers are actively advancing slush hydrogen storage solutions. Notably, companies with established expertise in cryogenic technologies, such as Linde and Air Liquide, are conducting research and pilot-scale demonstrations to compare slush hydrogen’s storage efficiency with that of liquid hydrogen. In parallel, organizations like NASA continue to explore slush hydrogen for rocket propulsion, leveraging its higher density to increase mission payload and range.
While slush hydrogen offers clear theoretical advantages, commercial deployment in 2025 remains limited compared to mature solutions such as compressed hydrogen tanks (350–700 bar) and standard liquid hydrogen vessels. Compressed hydrogen remains dominant in automotive and stationary applications due to established supply chains and lower system complexity. Liquid hydrogen, while more energy-intensive to produce and store, is well-proven for large-scale and long-duration energy storage, with major infrastructure investments ongoing from providers like Linde and Air Liquide.
- Slush hydrogen typically achieves a 16–20% higher density than liquid hydrogen, directly translating to increased storage capacity within the same tank volume.
- However, slush hydrogen requires advanced refrigeration, agitation, and insulation technologies to maintain the solid-liquid equilibrium, posing engineering and cost challenges compared to simpler storage forms.
- Safety standards and codes for slush hydrogen systems are currently less developed than those for gaseous and liquid hydrogen, potentially slowing regulatory approval and adoption.
Looking ahead to the next few years, the competitive adoption of slush hydrogen storage will likely depend on further breakthroughs in cryocooler efficiency, tank material innovation, and integration with end-use technologies such as fuel cells and rocket engines. Demonstration projects by leading industrial gas and aerospace companies will be critical in validating operational reliability and cost-effectiveness. As global hydrogen demand grows and high-density storage becomes more critical in sectors like aviation and space, slush hydrogen is expected to carve out a niche, particularly where maximum payload and storage efficiency are paramount.
Future Outlook: Challenges, Opportunities, and Next Steps for Industry Leadership
Slush hydrogen storage systems, leveraging a mixture of liquid and solid hydrogen, are drawing increasing attention as industries seek solutions for high-density, cryogenic hydrogen storage. As of 2025, the sector is marked by prototype deployments, ambitious R&D, and early-stage commercialization efforts. The unique properties of slush hydrogen—such as higher density and improved cooling capacity compared to liquid hydrogen—position it as a potential enabler for sectors like aerospace, heavy mobility, and large-scale energy storage.
However, the technical hurdles remain significant. Slush hydrogen requires sophisticated cryogenic infrastructure to maintain temperatures near 14 K, along with robust insulation and reliable mixing systems to prevent stratification. Current industry leaders, including Air Liquide and Linde, are investing in next-generation cryogenic storage and transfer technologies, with pilot programs exploring the feasibility of slush hydrogen systems for both stationary and mobile applications. These efforts are often conducted in collaboration with aerospace agencies and advanced propulsion projects, where maximizing hydrogen density is critical.
A major opportunity lies in the synergy between slush hydrogen storage and the ongoing push toward hydrogen-powered aviation and spaceflight. The increased density of slush hydrogen enables greater fuel capacity within limited space, a crucial requirement for long-range missions. Organizations such as European Space Agency (ESA) and NASA are evaluating slush hydrogen as part of their future propulsion strategies, with test campaigns focused on storage system reliability, refueling protocols, and safety management.
Despite the promise, challenges persist around cost, materials durability under repeated thermal cycling, and the complexity of slush generation and handling. The industry is actively pursuing solutions, including advanced vacuum insulation, novel composite materials, and automated slush production techniques. Regulatory frameworks and safety codes for slush hydrogen are still in development, necessitating close cooperation between technology providers, government agencies, and standards organizations such as ISO.
Looking ahead to the next few years, demonstration projects and pilot-scale validation will be critical. Success will require industry leadership to invest in both technological innovation and cross-sector collaboration. As governments and private sector leaders set more ambitious hydrogen targets, those who can overcome the engineering and regulatory barriers of slush hydrogen storage are well-positioned to shape the future of high-density hydrogen applications.
Sources & References
- Airbus
- Lockheed Martin
- Linde
- Air Liquide
- NASA
- European Space Agency (ESA)
- Japan Aerospace Exploration Agency (JAXA)
- ArianeGroup
- Tokyo Gas Co., Ltd.
- Mitsubishi Corporation
- International Organization for Standardization (ISO)
- European Committee for Standardization (CEN)
- National Fire Protection Association (NFPA)
- American Society of Mechanical Engineers (ASME)
- Ariens Company