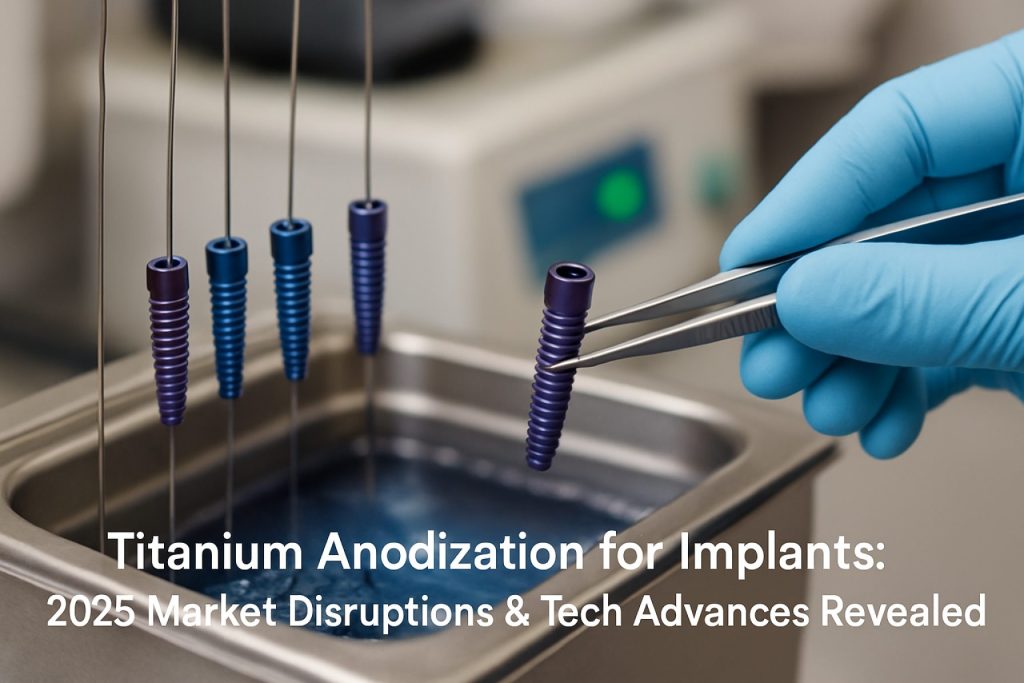
Table of Contents
- Executive Summary: 2025 Snapshot & Five-Year Outlook
- Market Size, Growth Projections, and Key Industry Players
- Breakthroughs in Titanium Anodization Technology for Biomedical Implants
- Competitive Landscape: Leading Companies and Strategic Initiatives
- Emerging Applications: Expanding Use Cases in Orthopedic, Dental, and Cardiovascular Implants
- Regulatory and Quality Standards: Navigating Compliance in 2025
- Sustainability and Biocompatibility: Addressing the Demands of Next-Gen Implants
- Challenges and Barriers: Technical, Cost, and Supply Chain Considerations
- Investment Trends and Partnership Opportunities
- Future Outlook: Innovations, Market Drivers, and Forecasts to 2030
- Sources & References
Executive Summary: 2025 Snapshot & Five-Year Outlook
The global demand for titanium anodization services catering to biomedical implants is set to experience robust growth in 2025, driven by rising requirements for advanced implant surfaces that enhance biocompatibility, corrosion resistance, and osseointegration. Titanium anodization, a process that modifies the oxide layer on implant surfaces, is increasingly adopted by medical device manufacturers to improve clinical outcomes and meet stringent regulatory standards. In 2025, the landscape is characterized by strong collaborations between implant producers and specialized surface treatment providers, as well as ongoing investment in process automation and validation technologies.
Leading implant manufacturers and contract service providers are expanding capacity and enhancing technical capabilities. For example, Titanium Finishing Company and SurfaceLink are providing tailored anodization services that include color coding, improved wear resistance, and surface roughening specifically optimized for orthopedic and dental applications. These services support major device OEMs in the U.S., Europe, and Asia, reflecting the sector’s globalized supply chains.
Recent years have seen significant advancements in process control, with providers leveraging digital monitoring and real-time quality control systems to ensure repeatable and validated outcomes—a requirement for regulatory compliance. Electrochem Solutions, for instance, has integrated advanced process monitoring in its anodization lines dedicated to medical device components, aiming to reduce variability and ensure traceability across large production volumes.
- In 2025, the sector continues to address evolving standards from regulatory bodies such as the U.S. Food and Drug Administration (FDA) and the European Medicines Agency (EMA), with a focus on documentation, validated cleaning, and surface characterization.
- Medical device OEMs are increasingly seeking partnerships with anodization specialists to accelerate device development timelines, manage cost pressures, and ensure rapid scalability for new product launches.
- There is heightened interest in novel anodization techniques, such as micro- and nano-structured surfaces, to support next-generation implants with enhanced bioactivity and integration potential.
Looking ahead over the next five years, demand for titanium anodization services is expected to further increase, paralleling trends in aging populations, rising orthopedic and dental implant procedures, and growing device complexity. Providers are likely to invest in automation, environmentally sustainable processes, and R&D for innovative surface treatments. Strategic alliances between implant OEMs and surface finishing firms are anticipated to accelerate, as both sides aim to navigate regulatory challenges and bring differentiated products to the biomedical market.
Market Size, Growth Projections, and Key Industry Players
The global market for titanium anodization services—particularly for biomedical implants—continues to demonstrate robust growth in 2025, driven by increasing demand for advanced surface treatments that enhance implant biocompatibility, corrosion resistance, and osseointegration. Titanium anodization, a process that creates an oxide layer on titanium surfaces, is widely adopted for dental, orthopedic, and cardiovascular implants due to its ability to improve both functional and aesthetic properties. With the aging global population and rising incidence of musculoskeletal and dental disorders, healthcare systems are witnessing a surge in implant procedures, directly fueling demand for specialized surface treatments.
Key industry players providing titanium anodization services include vertically integrated medical device manufacturers and specialized third-party service providers. For example, Zimmer Biomet and Stryker Corporation are established leaders manufacturing and finishing their own titanium implants, frequently employing proprietary anodization technologies as part of their production. Meanwhile, dedicated surface engineering firms such as BMT Medical Technology and Titanium Finishing Company offer contract anodization services to a range of medical device OEMs. These companies have invested in advanced anodization lines capable of supporting both custom batches and high-volume production, complying with strict regulatory standards like ISO 13485 and FDA regulations for medical devices.
Market growth is also propelled by innovations in anodization techniques, such as color anodization for implant identification and the development of nano-structured oxide layers that promote superior bone integration. Companies including Titanium Industries, Inc. are expanding their service portfolios to include advanced surface modification technologies tailored for the biomedical sector.
- By 2025, the global value of the titanium anodization services market for biomedical implants is estimated to exceed several hundred million USD, with a projected compound annual growth rate (CAGR) in the high single digits through 2028, as suggested by strong order books and facility expansions reported by sector leaders.
- Geographically, North America and Europe remain the largest markets, driven by high healthcare expenditure and established medical device industries, while Asia-Pacific is emerging rapidly due to increased local manufacturing and adoption of international quality standards.
- Strategic partnerships and vertical integration between implant manufacturers and anodization service providers are increasingly common, as seen in announcements by Smith+Nephew and DePuy Synthes regarding investment in new finishing capabilities.
Looking ahead, continued investments in automation, quality control, and R&D are expected among leading companies to meet both regulatory requirements and the evolving design needs of next-generation biomedical implants.
Breakthroughs in Titanium Anodization Technology for Biomedical Implants
Recent years have witnessed significant advancements in titanium anodization technology, specifically tailored for biomedical implants. As of 2025, the demand for enhanced surface modification techniques has grown due to the increasing use of titanium and titanium alloys in orthopedic, dental, and cardiovascular implants. Anodization, an electrochemical process that thickens and modifies the oxide layer on titanium surfaces, is recognized for improving corrosion resistance, biocompatibility, and surface integration of implants.
A key breakthrough has been the optimization of anodization parameters—such as voltage, electrolyte composition, and processing time—to produce highly controlled oxide layers with desired thickness and porosity. Leading service providers, including Titanium Finishing Company and Accubeam Laser, have reported the capability to deliver color-coded and functionalized titanium surfaces that support osseointegration and reduce bacterial adhesion. These services are now widely accessible for custom and mass-scale biomedical implant production.
In 2025, the industry focus has shifted towards developing anodized surfaces that not only enhance integration but also deliver specific therapeutic benefits. For example, the creation of nanotubular and nanoporous oxide structures through advanced anodization protocols is enabling the controlled release of drugs or growth factors from implant surfaces. Pioneers like Tiodize are offering specialized anodization services that cater to dental and orthopedic device manufacturers by producing surfaces optimized for cellular response and antibacterial performance.
Another breakthrough is the integration of automated process control and real-time monitoring during anodization. This ensures reproducible surface properties—critical for regulatory compliance and patient safety. Companies such as Orthoplastics are collaborating with implant OEMs to ensure that anodization processes meet the stringent requirements of ISO 13485 and FDA guidelines for medical devices.
Looking ahead, the outlook for titanium anodization services in the biomedical sector appears robust. With global implant demand rising and regulatory emphasis on surface quality, anodization providers are expected to invest further in automation, process validation, and customized surface functionalities. The next few years will likely see the adoption of smart anodization techniques, such as AI-driven parameter optimization and in-line surface analytics, ensuring consistent, high-performance implants for a growing patient population.
Competitive Landscape: Leading Companies and Strategic Initiatives
The competitive landscape for titanium anodization services in the biomedical implant sector is evolving rapidly in 2025, driven by heightened demand for advanced surface modification and strict regulatory requirements. Several established and emerging players are positioning themselves to capitalize on the growing need for durable, biocompatible implant surfaces.
Among the global leaders, Ti-Systems GmbH continues to leverage its proprietary anodization processes, offering tailored surface treatments to enhance osseointegration and corrosion resistance of dental and orthopedic implants. The company’s investments in automated anodization lines have bolstered their capacity to meet increasing orders from OEMs, particularly in Europe and Asia.
In the United States, Titanium Finishing Company has expanded its biomedical division in 2025, integrating real-time process monitoring and advanced quality assurance systems. Their focus on compliance with ISO 13485 and FDA standards has made them a preferred partner for medical device manufacturers seeking reliable and traceable anodization services.
Meanwhile, Bodycote, a multinational provider of thermal processing and surface technology, has scaled up its medical sector operations. Bodycote’s strategic alliances with implant manufacturers focus on high-volume anodization, emphasizing repeatability and customized coloring for product differentiation.
Asia-Pacific companies are also strengthening their presence. Kobe Steel, Ltd. has announced new investments in titanium surface treatment facilities in Japan, aiming to supply both domestic and international medical device markets with precision-anodized components. The company’s R&D initiatives target improved nanostructured surfaces that promote cellular adhesion.
In the realm of strategic initiatives, cross-industry collaborations are becoming more common. For example, some anodization specialists are partnering with additive manufacturing firms to develop post-processing solutions for 3D-printed titanium implants with complex geometries—a trend expected to accelerate through 2026.
Looking ahead, the competitive landscape is likely to see further consolidation as companies seek to broaden their service portfolios and global reach. Investments in automation, digital process control, and validation services are anticipated to be key differentiators. As implant manufacturers demand shorter lead times and tighter tolerances, service providers with robust quality management and regulatory expertise are poised to capture a larger share of the market.
Emerging Applications: Expanding Use Cases in Orthopedic, Dental, and Cardiovascular Implants
Titanium anodization is gaining significant traction in biomedical implant manufacturing, with 2025 marking a pivotal year for emerging applications across orthopedic, dental, and cardiovascular sectors. This electrochemical surface modification process enhances titanium’s biocompatibility, corrosion resistance, and osseointegration, making it an attractive solution for next-generation implants.
In orthopedics, demand for advanced surface treatments is surging due to the need for durable and infection-resistant implants. Companies such as Zimmer Biomet and Smith+Nephew are increasingly incorporating anodized titanium in hip and knee prostheses, targeting improved bone bonding and reduced risk of implant loosening. Anodization methods, including color coding for component identification and nano-texturing for enhanced cell adhesion, are being adopted in response to clinical performance requirements and regulatory updates.
Dental implantology is another area witnessing rapid uptake of anodized titanium. Leading manufacturers like Straumann and Nobel Biocare are offering anodized implant surfaces designed to accelerate osseointegration and shorten patient recovery times. In 2025, the focus is on optimizing oxide layer thickness and surface porosity through precise anodization protocols, directly impacting the success rates of immediate-load and narrow-diameter dental implants.
The cardiovascular field is also embracing titanium anodization, particularly for devices such as heart valve frames and vascular stents. Companies like Medtronic have initiated integration of anodized titanium components to reduce thrombogenicity and improve endothelialization. Anodization’s ability to tailor oxide film properties is being leveraged to minimize adverse reactions and extend device longevity in the harsh vascular environment.
Looking to the remainder of 2025 and beyond, the outlook for titanium anodization services is robust. Growing regulatory emphasis on implant safety and performance is driving contract service providers and OEMs to expand their anodization capacities and develop new proprietary processes. For example, EOS is collaborating on combining additive manufacturing with post-production anodization to deliver customized, patient-specific implants with enhanced biological integration.
As research continues into optimizing anodization parameters for specific anatomical and clinical needs, and as more clinical data supports its efficacy, the adoption curve for anodized titanium implants in orthopedics, dental, and cardiovascular applications is expected to steepen through 2025 and the following years.
Regulatory and Quality Standards: Navigating Compliance in 2025
As the demand for titanium anodization in biomedical implants continues to rise, regulatory and quality standards are evolving to address the unique requirements of these critical medical devices. In 2025, compliance with international and regional standards is paramount for manufacturers and service providers to ensure patient safety, product efficacy, and market access.
The U.S. Food and Drug Administration (FDA) maintains stringent oversight of medical implants, requiring that surface treatments like anodization meet both device-specific and process-specific standards. Titanium anodization processes must conform to Good Manufacturing Practices (GMP) under 21 CFR Part 820, which mandates rigorous quality management systems, process validation, and traceability. Additionally, the FDA’s guidance on biocompatibility (ISO 10993 series) is crucial, as anodized surfaces must demonstrate no adverse biological response when implanted (U.S. Food & Drug Administration).
In Europe, the Medical Device Regulation (MDR 2017/745) governs the conformity assessment of implants, with a strong emphasis on risk management and post-market surveillance. Manufacturers offering anodization services must provide technical documentation proving the safety, efficacy, and reproducibility of their processes. Notified bodies perform audits and review the effectiveness of quality management systems such as ISO 13485:2016, which has become a de facto global benchmark for medical device manufacturing quality (TÜV SÜD). The European Pharmacopoeia also provides standards for the chemical composition and surface quality of implantable materials.
Sector leaders such as Precision Titanium Products and Parker Hannifin highlight their adherence to these regulatory frameworks, emphasizing validated processes, cleanroom environments, and comprehensive traceability systems. They also invest in advanced analytical techniques, such as X-ray photoelectron spectroscopy (XPS) and scanning electron microscopy (SEM), to ensure anodized surfaces meet required specifications for thickness, color coding, and corrosion resistance.
Looking ahead, regulators are expected to tighten requirements for surface characterization, documentation, and supply chain transparency. Initiatives such as the Unique Device Identification (UDI) system and digital traceability platforms are poised to become integral, enhancing post-market surveillance and recall efficiency. Manufacturers and anodization service providers must remain agile, adopting the latest quality standards, digital tools, and validation methodologies to navigate this increasingly complex regulatory environment in 2025 and beyond.
Sustainability and Biocompatibility: Addressing the Demands of Next-Gen Implants
Titanium anodization has become a cornerstone surface modification technique for biomedical implants, directly addressing the dual imperatives of sustainability and biocompatibility in next-generation medical devices. As the medical device industry intensifies its focus on patient safety and environmental responsibility through 2025 and beyond, anodization services are evolving to meet these new standards.
Recent years have witnessed a marked increase in the adoption of anodized titanium for orthopedic, dental, and cardiovascular implants. The anodization process not only enhances the corrosion resistance and wear properties of titanium but also improves osseointegration by tailoring surface topography and oxide layer thickness. For instance, companies like Ti-Systems GmbH have developed advanced anodization protocols that optimize implant surface roughness to promote cellular attachment and accelerate bone in-growth, leading to faster patient recovery times.
Biocompatibility remains a central concern in implant development. Titanium anodization creates a stable, non-toxic oxide layer that minimizes adverse biological reactions. Zimmer Biomet, a global leader in orthopedic implants, utilizes specialized anodization techniques to color-code implants for easy identification and to enhance tissue compatibility. These innovations are increasingly sought after as regulatory bodies tighten requirements for implant safety and traceability.
Sustainability is also shaping anodization service offerings. Modern anodization lines are designed to reduce chemical consumption, lower water use, and minimize waste generation. Metalor Technologies highlights its closed-loop water recycling systems and advanced effluent treatment technologies, aligning with global sustainability goals and the medical sector’s push for greener manufacturing practices. These measures are particularly pertinent as healthcare providers and implant manufacturers set ever more ambitious environmental targets through 2025.
Looking forward, the outlook for titanium anodization services in biomedical implants is robust. The ongoing miniaturization of medical devices and the demand for patient-specific solutions are driving further customization of anodization processes. Surface engineering firms are investing in digital process controls and real-time monitoring to ensure reproducibility and compliance with evolving international standards. As manufacturers like Stryker expand their implant portfolios, the demand for sustainable, biocompatible anodization solutions is expected to accelerate, underpinning the next wave of innovation in medical implants.
Challenges and Barriers: Technical, Cost, and Supply Chain Considerations
The titanium anodization sector for biomedical implants faces several notable challenges and barriers as 2025 unfolds, primarily in the realms of technical complexity, cost structures, and supply chain reliability.
Technical Challenges: Achieving consistent, high-quality anodized surfaces that meet the stringent requirements for biomedical implants is technically demanding. Variations in electrolyte composition, voltage control, and process uniformity can lead to inconsistencies in oxide layer thickness and coloration, impacting implant biocompatibility and osseointegration. Additionally, the industry is under pressure to develop advanced anodization protocols tailored for increasingly complex implant geometries produced by additive manufacturing. Leading manufacturers like Zimmer Biomet and Stryker are actively refining their process controls and surface characterization methods to address these concerns, but widespread standardization remains elusive.
Cost Considerations: The cost of titanium anodization services remains relatively high due to the precision required and the need for cleanroom environments, especially when serving Class III medical device applications. Fluctuations in the cost of high-purity titanium feedstock and specialized chemicals further add to financial pressures. Smaller contract manufacturers and service providers must also invest in regular equipment upgrades and staff training to stay compliant with evolving ISO 13485 standards. Companies like Titanium Finishing Company emphasize the need for continued investment in process automation and quality assurance to maintain cost-competitiveness while meeting regulatory demands.
Supply Chain Vulnerabilities: The global titanium supply chain has experienced disruptions in recent years, primarily due to geopolitical tensions and transportation bottlenecks. These interruptions have affected the availability and lead times of titanium raw materials, as well as specialized anodization chemicals. Major suppliers such as TIMET are working to diversify sourcing and build more resilient logistics networks. However, smaller anodization service providers often lack the leverage to secure priority access to critical materials, increasing the risk of production delays for implant OEMs.
Outlook: Looking ahead to the next few years, the sector is expected to prioritize investments in process optimization, digital quality control, and supply chain risk mitigation. Collaborative initiatives between implant manufacturers and surface treatment specialists are anticipated, with the goal of developing standardized anodization protocols and robust supply agreements. As regulatory scrutiny over implant surface modification intensifies, the importance of overcoming these technical, cost, and supply chain barriers will only grow, shaping the future competitiveness of titanium anodization services for biomedical applications.
Investment Trends and Partnership Opportunities
Investment in titanium anodization services for biomedical implants is accelerating in 2025, driven by heightened demand for advanced surface modifications that enhance implant biocompatibility, corrosion resistance, and osseointegration. Key manufacturers and suppliers are capitalizing on these trends, seeking both organic growth and strategic partnerships to expand their market presence and technological capabilities.
A significant investment trend involves the expansion of production facilities and the adoption of state-of-the-art anodization technologies. Companies such as Titanium Finishing Company in the United States and Bodycote in Europe are scaling their specialized titanium surface treatment services to meet the stringent quality demands of medical device OEMs. These investments are often accompanied by the integration of automated process controls and enhanced quality assurance systems, reflecting the sector’s commitment to regulatory compliance and traceability.
Partnerships between implant manufacturers and surface treatment specialists are also on the rise. For example, Zimmer Biomet and TST Coatings have explored collaborations to co-develop proprietary anodization solutions tailored for specific implant designs, enabling differentiated product offerings and improved clinical outcomes. Such alliances are increasingly formalized through multi-year supply agreements or joint development projects that leverage each party’s strengths—device design and application knowledge from implant OEMs, and process innovation from anodization providers.
In addition, industry bodies such as ASTM International and U.S. Food & Drug Administration are updating standards and regulatory guidance for surface-treated implants, prompting further investments in compliance, validation, and documentation infrastructure. Companies are responding by enhancing their analytical and testing capabilities, sometimes through partnerships with accredited laboratories or by acquiring specialized firms.
The outlook for 2025 and beyond suggests continued momentum, with investors targeting companies that can demonstrate both technical excellence and reliable scalability. As value-based healthcare and personalized medicine become more prominent, there is growing interest in bespoke anodization services—customized for patient-specific implants or novel materials. Furthermore, emerging markets in Asia and South America are attracting joint ventures and technology transfer agreements as local demand for advanced biomedical implants increases.
Overall, the titanium anodization sector for biomedical implants is marked by dynamic investment, collaborative innovation, and a strong alignment with evolving regulatory and clinical requirements, positioning it for robust growth in the coming years.
Future Outlook: Innovations, Market Drivers, and Forecasts to 2030
The future of titanium anodization services for biomedical implants is shaped by a confluence of technological advancements, regulatory shifts, and evolving healthcare demands. As of 2025, market momentum is underpinned by the expanding global adoption of titanium-based implants in orthopedics, dentistry, and cardiovascular applications—driven by their biocompatibility, corrosion resistance, and superior osseointegration. Innovative anodization techniques are increasingly employed to tailor surface properties, enhance implant performance, and support next-generation device design.
Key industry players are focusing on the development of controlled anodization processes to produce highly uniform nanotopographies, which have been shown to facilitate faster cell adhesion and bone integration. Companies such as Titanium Finishing Company and Tiodize are investing in proprietary anodization solutions that allow for precise control over oxide layer thickness and coloration, catering to both functional and aesthetic requirements of implant manufacturers. These advances are expected to drive demand for contract anodization services, particularly among OEMs seeking to differentiate their products in a competitive regulatory landscape.
Market drivers through 2030 include the rising prevalence of age-related musculoskeletal disorders, increased patient demand for minimally invasive and durable solutions, and the globalization of medical device supply chains. Regulatory agencies in North America, Europe, and Asia-Pacific are emphasizing enhanced surface engineering as a route to improved implant safety and longevity, further incentivizing investment in advanced anodization capabilities. For example, Smith+Nephew is exploring novel surface treatments to extend implant lifespan and minimize post-surgical complications.
Looking ahead, ongoing R&D is likely to yield breakthroughs such as antibacterial and drug-eluting anodized surfaces, aiming to reduce infection rates and accelerate healing. The integration of digital quality control and traceability systems—leveraging AI and machine vision—will also become more commonplace, driven by demands for robust validation and transparency from both regulators and healthcare providers. Leading suppliers like Micron Metal Finishing are already adopting such technologies to enhance process reliability and documentation.
Overall, the next five years are expected to see steady growth in the titanium anodization services sector, with customization, regulatory compliance, and value-added functionalities as primary differentiators. The combination of expanding clinical indications, sophisticated manufacturing partnerships, and continuous innovation positions the industry for robust expansion through 2030 and beyond.