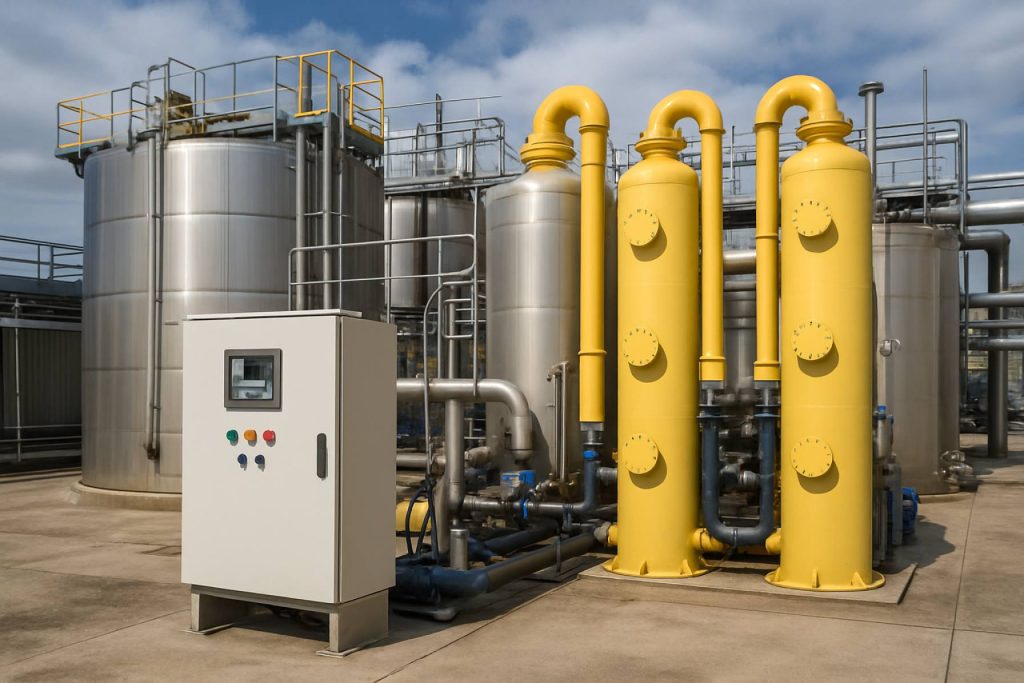
Will 2025 Be the Breakthrough Year for Vanillin Wastewater Neutralization Systems? Discover the Innovations, Market Shifts, and Untapped Opportunities Poised to Transform Environmental Compliance.
- Executive Summary: The State of Vanillin Wastewater Neutralization in 2025
- Market Size and 2025–2030 Growth Projections
- Key Regulatory Drivers and Compliance Trends
- Cutting-Edge Technologies Shaping Neutralization Systems
- Major Industry Players and Their Latest Solutions
- Case Studies: Successful Implementations from Leading Manufacturers
- Challenges in Scaling and Integration
- Sustainability Impact: Environmental and Economic Benefits
- Investment Trends and Strategic Partnerships
- Future Outlook: Emerging Innovations and Market Opportunities Through 2030
- Sources & References
Executive Summary: The State of Vanillin Wastewater Neutralization in 2025
In 2025, vanillin wastewater neutralization systems are at a pivotal juncture, driven by tightening environmental regulations, heightened sustainability demands, and rapid technological advancements. Vanillin—widely used in food, fragrance, and pharmaceutical industries—generates significant wastewater streams, often characterized by high chemical oxygen demand (COD), acidity, and persistent organic pollutants. The effective neutralization and treatment of these effluents remain critical for compliance and environmental stewardship.
Recent years have witnessed the deployment of advanced neutralization techniques at both new and existing vanillin production facilities. Chemical neutralization using caustic soda, lime, or magnesium hydroxide remains a standard, with system upgrades focusing on precise pH control and automation to reduce chemical overuse and sludge generation. Companies such as Takeda—a major player in pharmaceutical and specialty chemicals—have adopted integrated pH adjustment and real-time monitoring technologies to optimize process efficiency and minimize environmental impact.
Membrane bioreactors (MBRs) and advanced oxidation processes (AOPs) are gaining traction as viable secondary and tertiary treatment options to further reduce COD and break down refractory compounds present in vanillin effluents. Suppliers like Veolia and SUEZ are actively involved in retrofitting existing plants with modular MBR and AOP units, targeting smaller footprints and higher treatment yields. These solutions are particularly attractive in Europe and East Asia, where regulatory standards for industrial wastewater discharge continue to tighten.
The global market is seeing an influx of automated, digitally integrated neutralization systems, leveraging IoT sensors and AI-driven analytics for predictive maintenance and real-time compliance monitoring. Industrial automation leaders such as Siemens are partnering with chemical manufacturers to deploy sensors and cloud-based dashboards, enabling facility operators to proactively address pH imbalances and optimize chemical dosing.
Looking forward, the outlook for vanillin wastewater neutralization systems is one of robust growth and innovation. Pressure from regulators and downstream brand owners is expected to accelerate investments in closed-loop water recycling and resource recovery, such as the extraction of vanillin byproducts and water reuse. Pilot projects and commercial installations from major solution providers are likely to set new industry benchmarks over the next few years. Stakeholders can anticipate a continued shift toward integrated, data-driven systems that balance operational efficiency, regulatory compliance, and environmental responsibility.
Market Size and 2025–2030 Growth Projections
The global market for vanillin wastewater neutralization systems is poised for steady growth between 2025 and 2030, influenced by expanding vanillin production, tightening environmental regulations, and technological advancements in industrial wastewater treatment. Vanillin, widely used in the food, pharmaceutical, and cosmetics industries, is primarily synthesized via chemical processes that generate effluents with high chemical oxygen demand (COD), acidity, and persistent organic pollutants. This makes effective neutralization and treatment systems a critical operational requirement for manufacturers.
In 2025, the demand for vanillin wastewater neutralization systems is closely tied to the broader synthetic vanillin production sector, which continues to expand in Asia-Pacific, particularly in China and India. These countries are home to major vanillin manufacturers such as Solvay (Belgium/France, with significant Asian operations), Borregaard (Norway, with global reach), and Camlin Fine Sciences (India). Each of these companies employs advanced effluent treatment and neutralization processes as part of their production facilities, with ongoing investments in compliance and sustainability.
While precise market size estimates for vanillin-specific wastewater systems are not typically published independently, the segment can be contextualized within the broader industrial wastewater treatment equipment market, which is valued in the tens of billions of USD globally. The segment focused on specialty chemical effluent systems, which includes vanillin plants, is projected to see above-average growth rates—often estimated in the 6–8% CAGR range for the latter half of the 2020s. This is driven by stricter discharge limits and increased public scrutiny in key manufacturing regions.
Growth is further supported by innovation from suppliers specializing in wastewater neutralization and biological treatment. Companies such as Veolia and SUEZ (now part of Veolia) deliver custom solutions for the neutralization of acidic industrial effluents, including those from vanillin synthesis, integrating pH adjustment, advanced oxidation, and biological treatment to address both regulatory demands and sustainability goals.
Looking ahead to 2030, the market outlook remains robust as regulatory requirements continue to tighten, especially in China and the European Union. Emerging trends—including the adoption of digital monitoring for process optimization and the integration of resource recovery (such as by-product valorization)—are expected to shape the next generation of vanillin wastewater neutralization systems. Consequently, the sector is likely to experience sustained investment and incremental technological progress, with major players and regional specialists both contributing to the evolving landscape.
Key Regulatory Drivers and Compliance Trends
The regulatory environment governing vanillin wastewater neutralization systems is becoming increasingly stringent in 2025, as global and regional authorities intensify their focus on sustainable chemical manufacturing and effluent management. Vanillin production, especially via synthetic routes, generates high-strength effluents with elevated chemical oxygen demand (COD), colorants, and acidic characteristics, necessitating robust neutralization prior to discharge or reuse.
In the European Union, the Industrial Emissions Directive (IED) and the Urban Waste Water Treatment Directive drive the adoption of advanced neutralization and treatment systems for vanillin manufacturers, mandating tightened thresholds on pH, COD, and persistent organic pollutants in discharged water. These regulations are being reinforced by ongoing updates that emphasize the Best Available Techniques (BAT) for chemical sectors, promoting the use of automated pH adjustment, online monitoring, and integrated biological-chemical treatment solutions. Companies with established vanillin production in Europe, such as Solvay and Evolva, are investing in modern neutralization and wastewater treatment infrastructure to achieve compliance and reduce environmental impact.
In China, the world’s largest vanillin producer, updated policies under the Ministry of Ecology and Environment (MEE) require stricter pre-treatment of phenolic and aromatic wastes. New standards, effective in 2025, raise the bar for pH-neutralization efficiency and the removal of hazardous organics. Chinese vanillin suppliers are increasingly adopting automated dosing systems and advanced oxidation processes, often sourced from specialized water technology firms such as Veolia and SUEZ, to align with these mandates.
In the United States, the Environmental Protection Agency (EPA) continues to enforce effluent guidelines for organic chemicals manufacturing, including specific pH and COD requirements for vanillin facilities. The EPA’s National Pollutant Discharge Elimination System (NPDES) permits are being revised to include more frequent monitoring and reporting obligations, pushing manufacturers such as IFF to integrate real-time control and alarm systems within their neutralization setups.
Looking ahead, regulatory agencies worldwide are expected to introduce digital compliance verification, traceability requirements, and mandatory sustainability reporting for industrial wastewater streams by 2027. This trend will likely accelerate the adoption of smart neutralization systems with remote monitoring, data logging, and AI-driven process optimization—further supported by global suppliers like Evoqua Water Technologies. The convergence of regulatory pressure and technological innovation is set to define the landscape of vanillin wastewater neutralization over the next several years.
Cutting-Edge Technologies Shaping Neutralization Systems
The landscape of vanillin wastewater neutralization is undergoing rapid technological transformation as the global food, fragrance, and pharmaceutical industries grow and environmental regulations tighten. Traditionally, vanillin production—especially via processes such as lignin oxidation, guaiacol synthesis, or biotechnological fermentation—yields effluents that are acidic, contain high chemical oxygen demand (COD), and include recalcitrant organic compounds. The imperative to neutralize these streams in a cost-effective and sustainable manner has driven innovation in 2025, with several cutting-edge technologies leading the sector.
Advanced oxidation processes (AOPs) are increasingly adopted to address the persistent organics in vanillin wastewater. Technologies such as Fenton, photo-Fenton, and ozonation are being integrated with conventional neutralization steps to achieve higher degradation rates of complex aromatics and phenolics. Companies like Evoqua Water Technologies and Veolia have expanded their portfolios in recent years to include modular AOP systems that can be customized for vanillin wastewater streams, enabling both neutralization and reduced toxicity.
Membrane-based separation is another area seeing strong momentum. High-resilience nanofiltration and reverse osmosis membranes are now being deployed post-neutralization to polish vanillin effluents, targeting the reduction of COD and color. SUEZ and Kubota Corporation have both highlighted the deployment of advanced membrane bioreactors (MBRs) in Asian facilities that process flavor and fragrance industry wastewaters, including vanillin. These systems provide both pH neutralization and advanced contaminant removal, aligning with stricter discharge limits now enforced in major production regions like China and India.
Biological neutralization strategies are also evolving. Engineered microbial consortia capable of tolerating low pH and degrading aromatic compounds are being trialed in pilot plants. BASF, a leader in vanillin production and chemical process innovation, has publicly committed to implementing more sustainable wastewater solutions across its sites and is investing in collaborative R&D on bio-augmentation and enzymatic treatments for effluents.
Looking to 2025 and beyond, the outlook is for further convergence of digitalization and automation. Smart neutralization systems equipped with real-time sensors, IoT connectivity, and predictive controls are being rolled out, promising to optimize reagent dosing and energy consumption while ensuring compliance. Industry stakeholders and technology providers are expected to intensify partnerships to scale up these innovations, as the environmental footprint of vanillin production faces growing scrutiny from regulators and customers alike.
Major Industry Players and Their Latest Solutions
The global market for vanillin wastewater neutralization systems is shaped by the growing demand for sustainable production processes in the flavor and fragrance industry. As vanillin is predominantly synthesized through chemical routes such as lignin and guaiacol processing, the management and neutralization of highly acidic and organic-laden wastewater remains a significant environmental challenge. Major players in the chemical engineering and water treatment sectors are actively developing and deploying advanced neutralization technologies tailored for vanillin manufacturing plants.
Among the leaders, Veolia has continued to expand its portfolio of integrated water treatment solutions, offering customized pH neutralization systems and advanced oxidation processes specifically designed for effluents from fine chemical and flavor manufacturing. Veolia’s modular approach enables adaptation to varying scales of vanillin production, and its latest installations reportedly leverage automated dosing and real-time monitoring to ensure compliance with environmental discharge norms.
Another prominent company, SUEZ, has strengthened its position through proprietary chemical dosing and neutralization packages, which are increasingly adopted by vanillin producers in Asia and Europe. SUEZ’s technologies are focused on minimizing sludge generation and optimizing reagent usage, thus addressing both operational cost and sustainability criteria. Their recent pilot installations in China and France have demonstrated consistent reduction of chemical oxygen demand (COD) and pH normalization, aligning with tightening regulatory frameworks.
In the Asia-Pacific region, where the majority of vanillin manufacturing occurs, Sinofloc has emerged as a notable supplier of specialty chemical solutions for industrial wastewater, including coagulants and neutralizing agents suitable for vanillin process streams. Sinofloc’s products are reported to facilitate rapid pH adjustment and improved sedimentation, supporting compliance with increasingly stringent Chinese discharge limits.
Looking ahead to 2025 and beyond, the outlook for vanillin wastewater neutralization systems is shaped by the push for circular chemistry and water reuse. Leading system integrators are investing in digitalization—deploying IoT-based sensors and control platforms to optimize chemical dosing, monitor effluent quality in real time, and reduce overall water consumption. Major vanillin producers are expected to continue partnering with solution providers to pilot closed-loop water systems and explore resource recovery (such as extracting residual organics for biogas), further integrating sustainability into their processes.
With regulatory pressures mounting and consumer preferences shifting toward green chemistry, industry collaboration will likely accelerate the adoption of advanced neutralization solutions, ensuring that the environmental impact of vanillin production is increasingly mitigated through innovative engineering and process optimization.
Case Studies: Successful Implementations from Leading Manufacturers
As environmental regulations tighten worldwide, vanillin manufacturers are increasingly investing in advanced wastewater neutralization systems to address the unique challenges posed by their effluent streams—typically characterized by high chemical oxygen demand (COD), acidity, and organic load. In 2025, several leading producers and technology suppliers have reported successful deployments of innovative neutralization and treatment solutions, demonstrating both regulatory compliance and sustainable practices.
One noteworthy example is the implementation of integrated neutralization and biological treatment systems by Solvay, a global leader in aroma chemicals including synthetic vanillin. Solvay’s French and Chinese production sites have upgraded their wastewater facilities with automated pH adjustment and multi-stage aerobic bioreactors. These systems achieve effluent standards well below local discharge limits, and Solvay’s sustainability disclosures highlight a reduction in COD discharge by over 30% at key sites since 2022. The company attributes this success to the combination of lime-based neutralization and high-efficiency membrane bioreactors (MBR), ensuring both environmental compliance and operational reliability.
Another case involves Evonik Industries, a major specialty chemicals producer with a robust vanillin portfolio. Evonik has collaborated with water technology specialists to integrate continuous pH monitoring and automated alkali dosing systems into its wastewater treatment lines. In 2024, the company reported a 25% reduction in caustic soda consumption for neutralization, achieved by optimizing dosing algorithms and leveraging predictive analytics. This not only improved effluent quality but also reduced chemical costs and sludge generation, aligning with Evonik’s broader circular economy goals.
In China, where vanillin production capacity is concentrated, leading suppliers such as Borregaard have invested in closed-loop neutralization systems that recover and recycle process water. Borregaard’s Suzhou facility, for instance, utilizes advanced sensors and real-time control systems to dynamically adjust acid and base dosing, minimizing freshwater intake and maximizing reuse. By 2025, the plant reported water savings exceeding 15% and a significant reduction in environmental impact, as detailed in its annual sustainability report.
Looking ahead, the outlook for vanillin wastewater neutralization systems is shaped by continued innovation and regulatory pressure. Manufacturers are expected to invest further in digital monitoring, automation, and hybrid treatment technologies, with a focus on resource efficiency and long-term sustainability. Partnerships between chemical producers and water technology firms will likely accelerate, driving both environmental and economic benefits across the vanillin value chain.
Challenges in Scaling and Integration
The scaling and integration of vanillin wastewater neutralization systems present significant challenges, particularly as global demand for vanillin—used extensively in food, fragrance, and pharmaceutical industries—continues to rise in 2025. The main sources of vanillin wastewater stem from both synthetic and biotechnological production routes. This wastewater is characterized by high chemical oxygen demand (COD), acidic pH, and persistent aromatic compounds, demanding robust and adaptive treatment strategies for regulatory compliance and environmental safety.
One primary challenge is the variability in wastewater composition, often driven by fluctuations in process feedstocks and production scales. As companies like Solvay and ENN Group expand biovanillin production capacity in Asia and Europe, treatment plants must be designed with flexibility to handle variable loads and contaminant profiles. This requirement complicates both the engineering and operational aspects of integration, as standard neutralization systems may fall short in addressing spikes in acidity or organic loading.
Space constraints and capital expenditure are additional barriers. Established chemical producers such as LANXESS and Borregaard, who operate at large scale, are retrofitting existing plants with advanced neutralization and biological treatment units. The integration process often involves temporary shutdowns and phased rollouts to minimize production losses, yet these upgrades can be costly and logistically complex. Smaller producers, particularly in emerging markets, struggle to finance and implement modular or advanced treatment systems, furthering the divide between industry leaders and smaller players.
Technological limitations persist, especially as companies seek to deploy novel neutralization and secondary treatment technologies, such as membrane bioreactors or advanced oxidation processes. While these methods offer higher efficiency and compact footprints, their integration is hindered by maintenance demands, membrane fouling, and compatibility with upstream process chemistries. Companies like Veolia, which specializes in industrial water solutions, are piloting hybrid systems that combine chemical neutralization with biological polishing to address these issues, but widespread adoption remains gradual due to cost and operational complexity.
Looking forward, regulatory tightening—especially in the EU and China—will accelerate the need for scalable, resilient, and easily integrated vanillin wastewater neutralization systems. Industry leaders are investing in digital monitoring and automation to optimize process control and reduce manual intervention. However, ensuring that these solutions are accessible and adaptable for a range of plant sizes and configurations will remain a focal challenge over the next several years.
Sustainability Impact: Environmental and Economic Benefits
Vanillin production, particularly from petrochemical and lignocellulosic sources, generates significant volumes of wastewater containing acidic organics and residual chemicals. The deployment of advanced vanillin wastewater neutralization systems in 2025 is driving notable sustainability gains, with both environmental and economic benefits becoming increasingly evident. Key manufacturers and process technology providers are integrating these systems within existing vanillin plants to address tightening discharge regulations and support corporate sustainability goals.
Environmentally, neutralization systems reduce the toxicity and acidity of vanillin effluents before their release or further treatment. This directly lessens the risk of aquatic ecosystem damage and soil acidification in receiving environments. Companies such as Evonik Industries AG and Solvay S.A., both major suppliers of vanillin and specialty chemicals, are implementing on-site neutralization and biological treatment stages at their vanillin production facilities. These upgrades have led to measurable improvements in effluent quality, including pH stabilization and reduced chemical oxygen demand (COD), aligning with European Union and Asia-Pacific wastewater standards.
Economically, the adoption of modular and automated neutralization systems is reducing operational costs and resource consumption. Upstream neutralization minimizes the load on downstream biological treatment, lowering energy consumption and the need for supplemental chemicals. Leading technology providers such as Veolia offer integrated neutralization and water reuse solutions, helping vanillin producers recover process water and reduce freshwater intake. This not only meets regulatory requirements but also offsets rising water and wastewater management costs, which have been escalating due to stricter environmental oversight.
In 2025 and the coming years, vanillin producers are expected to further optimize these systems by leveraging process automation, real-time monitoring, and advanced dosing controls. The integration of digital process control, championed by firms like Siemens AG, enables precise management of neutralizing agents and minimizes reagent waste, enhancing both environmental and cost performance. There is also growing collaboration between vanillin manufacturers and engineering firms to design closed-loop systems that achieve near-zero liquid discharge (ZLD), further increasing the sustainability profile of vanillin production.
With global demand for vanillin rising and regulatory expectations tightening, investment in advanced neutralization systems is set to deliver long-term sustainability dividends for the sector. The dual benefits of reduced environmental impact and operational savings are making these systems a standard feature in new and retrofitted vanillin production plants worldwide.
Investment Trends and Strategic Partnerships
The landscape of investment and strategic partnerships in vanillin wastewater neutralization systems is experiencing a noticeable transformation in 2025, driven by tightening environmental regulations and the global push for sustainable chemical manufacturing. As vanillin production—predominantly from lignin or petrochemical sources—generates highly alkaline and organic-laden effluents, there is mounting pressure on manufacturers to adopt advanced neutralization and treatment technologies.
Several established players in chemical processing and water treatment are now actively investing in research and scaling up their solutions to capture this niche but growing segment. Evonik Industries AG, a major specialty chemicals company with a strong portfolio in process water treatment chemicals and modular systems, has increased R&D spending for tailored neutralization solutions suitable for aromatic compound byproducts. Similarly, Veolia Environnement S.A., a global leader in water and wastewater treatment, has announced new projects in Asia and Europe aimed at integrating neutralization modules with biological and membrane-based polishing, targeting vanillin and other fine chemical effluents.
Strategic alliances are also emerging as a key trend. In early 2025, several vanillin producers in China and India—the world’s two largest vanillin manufacturing hubs—entered into joint ventures with process technology suppliers. These partnerships often focus on pilot-scale trials and scaling up proprietary neutralization chemistries, such as advanced lime dosing, CO₂ neutralization, or hybrid acid-base balancing, combined with automated controls. For instance, SUEZ has intensified partnerships with regional chemical parks to deploy decentralized treatment skids, reflecting a move towards flexible, on-site neutralization rather than centralized treatment.
- Corporate venture capital arms of major chemical companies are targeting startups commercializing new neutralization catalysts and sensor-based monitoring for real-time pH and organic content adjustment.
- Public-private partnerships are being fostered in the European Union to co-develop zero-liquid discharge and resource recovery solutions tailored for vanillin and other flavorings industries.
- Technology licensing agreements are facilitating the spread of patented neutralization process designs, especially in Southeast Asia, where vanillin output is rising.
Looking ahead, with ESG (Environmental, Social, and Governance) criteria becoming more central to investment decisions, the sector is likely to see continued inflows of strategic capital and technical collaboration. Innovation in neutralization efficiency and integration with downstream purification processes is expected to be a focal point for both investors and industrial partners over the next few years.
Future Outlook: Emerging Innovations and Market Opportunities Through 2030
The future of vanillin wastewater neutralization systems is poised for significant transformation by 2030, driven by tightening environmental regulations, technological advancements, and evolving market dynamics. In 2025 and the coming years, manufacturers of vanillin—primarily in Asia-Pacific regions such as China and India—are under mounting pressure to innovate in effluent treatment due to stricter discharge standards and heightened scrutiny on environmental compliance.
A key trend is the integration of advanced physicochemical and biological neutralization techniques. Leading chemical producers, including Solvay and Symechem, are exploring the use of modular systems that combine pH adjustment, advanced oxidation processes (AOP), and bioreactor technologies. These integrated solutions are capable of efficiently neutralizing acidic effluents while breaking down recalcitrant organic compounds that characterize vanillin wastewater.
The adoption of real-time monitoring and process automation is also accelerating. Major plant engineering firms, such as Veolia and SUEZ, have begun deploying sensor-driven control platforms that enable dynamic adjustment of neutralizing agents (e.g., lime, sodium hydroxide) in response to fluctuating effluent loads. This not only ensures regulatory compliance but also reduces chemical consumption and operational costs.
A notable innovation on the horizon is the valorization of vanillin wastewater by-products. R&D initiatives, particularly in Europe, are investigating the recovery of valuable chemicals—such as ferulic acid and lignin derivatives—from neutralized effluents, transforming waste streams into sources of revenue and supporting circular economy objectives. Companies like Borregaard, a leader in biorefinery technologies, are at the forefront of such efforts, developing processes for upcycling vanillin-related waste.
Looking ahead, market opportunities are expected to expand as food, flavor, and fragrance producers seek more sustainable and cost-effective neutralization solutions. Strategic partnerships between vanillin manufacturers and specialized wastewater technology providers are likely to proliferate, with a focus on turnkey systems tailored to specific plant requirements. The continued global expansion of the vanillin market—projected to grow steadily through 2030—will further drive demand for high-performance neutralization systems that align with evolving environmental standards.
Ultimately, the convergence of digitalization, modular engineering, and resource recovery will define the next generation of vanillin wastewater neutralization systems, positioning the sector for both regulatory resilience and enhanced profitability through 2030.