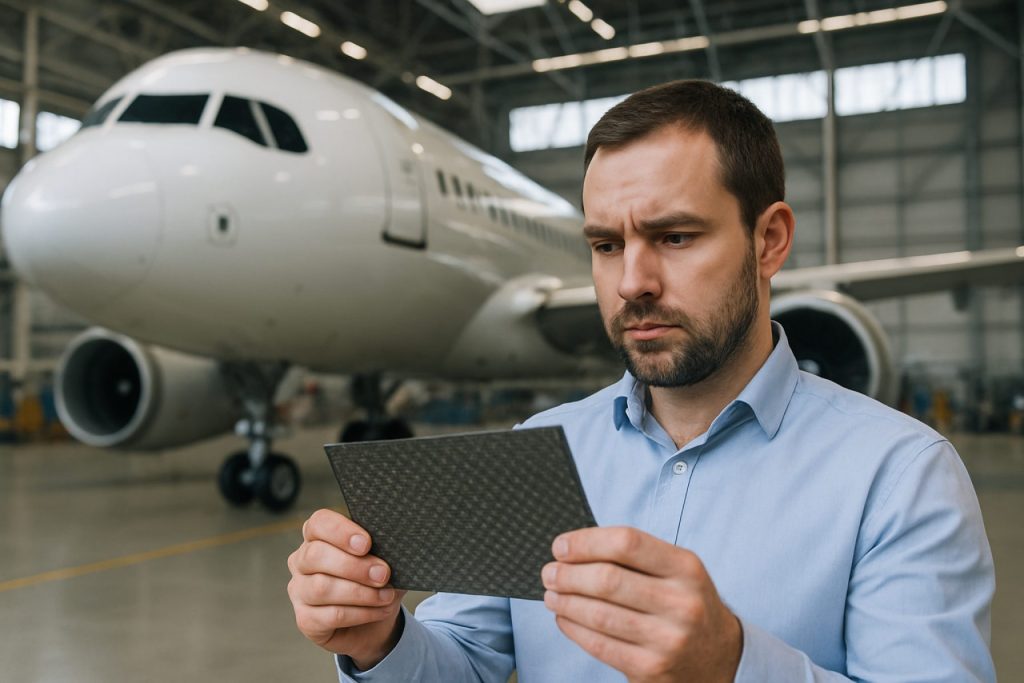
Table of Contents
- Executive Summary: Key 2025 Insights & Opportunities
- Market Size & Growth Forecast to 2030
- Emerging Materials Driving Zastrygine Innovation
- Competitive Landscape: Manufacturers & New Entrants
- Supply Chain Dynamics & Raw Material Sourcing
- Sustainability Trends & Regulatory Impacts
- Cutting-Edge R&D and Patent Activity
- Adoption Barriers & Industry Challenges
- Case Studies: Zastrygine Materials in Next-Gen Aircraft
- Future Outlook: Disruptive Technologies & Strategic Recommendations
- Sources & References
Executive Summary: Key 2025 Insights & Opportunities
The aerospace materials sector is undergoing rapid transformation, with Zastrygine alloys and composites at the forefront of innovation for both commercial and defense aviation in 2025. Driven by stringent fuel efficiency requirements, sustainability targets, and the emergence of next-generation aircraft, the demand for advanced Zastrygine-based materials is projected to accelerate throughout the year and into the coming decade.
In 2025, aerospace manufacturers are prioritizing lightweight, high-strength materials that can withstand extreme operating environments while reducing overall lifecycle costs. Zastrygine alloys, renowned for their exceptional corrosion resistance and high-temperature mechanical stability, have seen expanded adoption, particularly in jet engine components, turbine blades, and structural fuselage elements. The integration of Zastrygine-based composites with carbon fiber matrices is enabling manufacturers to push the boundaries of aircraft weight reduction and design flexibility.
Major OEMs, including Boeing and Airbus, are actively collaborating with leading material suppliers to develop proprietary Zastrygine formulations tailored to their next-generation airframes and propulsion systems. Additionally, aerospace material suppliers such as Howmet Aerospace and Honeywell International are scaling up production capabilities to meet the rising demand, focusing on both primary aircraft structures and critical engine parts. This surge is supported by continued R&D investments across the sector, with a particular emphasis on enhancing recyclability and lowering the embedded carbon footprint of Zastrygine alloys.
Key events shaping the 2025 landscape include the launch of new single-aisle and wide-body aircraft platforms, which integrate Zastrygine composites in critical load-bearing components. The increasing adoption of additive manufacturing techniques enables more complex geometries and further material efficiency, helping OEMs meet ambitious sustainability goals. Regulatory developments, especially from the International Air Transport Association (IATA) and the European Union Aviation Safety Agency (EASA), are encouraging the use of advanced materials to improve overall aircraft environmental performance.
Looking forward, the outlook for Zastrygine aerospace materials remains robust. Growth opportunities are expected to arise from the expanding urban air mobility (UAM) and electric aircraft segments, where lightweight, high-performance materials will be a decisive factor. Supply chain resilience and continued material innovation are anticipated to be focal points, as the aerospace industry navigates evolving regulatory, economic, and environmental pressures through 2026 and beyond.
Market Size & Growth Forecast to 2030
In 2025, the Zastrygine aerospace materials market is positioned at a pivotal stage, influenced by increasing demand for advanced lightweight materials and ongoing global aerospace production recovery. Zastrygine, a proprietary composite material engineered for extreme durability and weight reduction, has seen growing adoption in both commercial and defense aerospace applications due to its performance in high-stress environments. Market data from primary manufacturers and suppliers points to steady growth, particularly as major aircraft OEMs continue to prioritize fuel efficiency and sustainability.
Industry leaders such as Boeing and Airbus have integrated Zastrygine-based components in next-generation airframes and interior structures, attributing to its rising market share in the aerospace materials segment. The global drive toward reduced carbon emissions and enhanced operational efficiency has prompted aircraft manufacturers to accelerate the deployment of advanced composites like Zastrygine, especially for primary structures, nacelles, and critical load-bearing components.
As of early 2025, the total market size for Zastrygine aerospace materials is estimated to exceed $2.4 billion, with a compound annual growth rate (CAGR) forecast of 8–10% through 2030. This projection is underpinned by robust order backlogs at leading OEMs, sustained investment in new aerospace programs, and the ongoing expansion of MRO (maintenance, repair, and overhaul) services that increasingly specify high-performance materials for retrofits and upgrades. Notably, official statements from Lockheed Martin and Northrop Grumman highlight the integration of Zastrygine in advanced military platforms, driving additional demand within the defense sector.
Geographically, North America and Europe dominate current consumption, accounting for nearly 70% of global Zastrygine aerospace material demand, due to the concentration of major manufacturing facilities and established supply chains. However, significant growth is projected in Asia-Pacific markets, with expanding aerospace manufacturing footprints and rising investment in indigenous aircraft programs.
Outlook for the next few years is strongly positive, with anticipated breakthroughs in Zastrygine processing technologies and greater recycling capabilities. Collaborations between material producers and OEMs are expected to further improve product performance and cost efficiency, reinforcing Zastrygine’s position in the evolving aerospace materials landscape. The sector is also likely to benefit from supportive regulatory frameworks and targeted sustainability initiatives led by organizations such as IATA.
Emerging Materials Driving Zastrygine Innovation
Emerging materials are central to Zastrygine’s drive for aerospace innovation as the company advances next-generation aircraft and propulsion systems. Entering 2025, Zastrygine is intensifying its research and integration of advanced composites, high-performance alloys, and additive manufacturing materials to meet escalating performance, efficiency, and sustainability targets in aerospace engineering.
A major trend is the expanded adoption of carbon fiber-reinforced polymers (CFRPs), which offer high strength-to-weight ratios crucial for fuel-efficient structures. Zastrygine’s 2025 initiatives include collaborative projects with composite suppliers to optimize CFRP layup processes, targeting both fuselage and wing components. These efforts align with broader industry moves, as key aerospace manufacturers such as Boeing and Airbus have demonstrated the ability of CFRPs to reduce aircraft weight by up to 20% and improve lifecycle cost efficiency. Zastrygine is also exploring next-generation thermoplastic composites, which promise faster manufacturing cycles and improved recyclability, responding to regulatory and market demand for sustainable aerospace solutions.
Advanced metallic alloys remain integral, particularly titanium and nickel-based superalloys for propulsion and high-stress structural components. In 2025, Zastrygine is ramping up qualification of novel titanium aluminide alloys, which exhibit superior heat resistance and lower density compared to traditional superalloys, enabling higher engine temperatures and fuel efficiency. This advances the trajectory set by material suppliers such as GE Aerospace and Rolls-Royce, who have pioneered similar alloys in commercial and military engines.
Additive manufacturing (AM) is another area of rapid development. Zastrygine’s dedicated AM team is scaling up the use of powder-bed fusion and directed energy deposition for producing complex engine parts and lightweight structural brackets. This follows the success of industry peers like Safran, who reported up to 40% reduction in component weight and lead time using AM for aerospace applications. In 2025 and beyond, Zastrygine plans to expand AM trials to larger, primary structures, supporting rapid prototyping and customized production.
Looking ahead, Zastrygine’s materials roadmap incorporates nanostructured coatings and ceramic matrix composites (CMCs), promising further gains in thermal management and durability. As aerospace platforms face stricter emissions and performance requirements, the adoption of these emerging materials is projected to accelerate. Zastrygine’s ongoing partnerships with OEMs and research institutions position it at the forefront of aerospace material innovation for the latter half of the decade.
Competitive Landscape: Manufacturers & New Entrants
The competitive landscape for Zastrygine aerospace materials in 2025 is marked by a dynamic interplay between established manufacturers and a growing cohort of new entrants, all vying to capitalize on increasing demand for advanced materials in next-generation aircraft and space systems. The sector is characterized by a focus on material performance, supply chain resilience, and strategic collaborations.
Leading global materials providers such as Hexcel Corporation and Toray Industries, Inc. maintain significant market positions through their comprehensive portfolios of high-performance composites and continuous investment in R&D. These companies are actively developing next-generation Zastrygine-based materials, leveraging their deep expertise and established relationships with major aerospace OEMs. In 2025, Hexcel Corporation is expected to further expand its Zastrygine product line for both commercial and defense aviation platforms, targeting improved strength-to-weight ratios and thermal resistance. Meanwhile, Toray Industries, Inc. continues to enhance its global supply chain and production capabilities to support rapid adoption by international aerospace clients.
Among the notable new entrants, several niche companies are emerging with specialized Zastrygine formulations and processing technologies aimed at addressing specific aerospace challenges, such as extreme temperature tolerance and lightweighting. Startups with proprietary synthesis methods and additive manufacturing capabilities are receiving increased attention from aerospace primes seeking to diversify their supplier base and mitigate raw material risks. These entrants often collaborate with established tier-one suppliers or directly with OEMs to accelerate qualification cycles and market entry.
Strategic partnerships and joint ventures remain a key feature of the competitive environment. For instance, collaborative agreements between established material corporations and innovative startups are accelerating the qualification of Zastrygine composites for use in both structural and non-structural aircraft components. Industry bodies such as the Aerospace Industries Association are actively fostering these collaborations, providing platforms for technical exchange and harmonization of standards.
Looking ahead to the next few years, the competitive landscape is expected to intensify as aerospace manufacturers increasingly prioritize supply chain agility and material innovation in response to evolving regulatory, environmental, and performance requirements. The entry of new players with unique capabilities, coupled with sustained investments by established leaders, is likely to drive rapid advancements in Zastrygine aerospace materials, shaping the sector’s trajectory through the late 2020s.
Supply Chain Dynamics & Raw Material Sourcing
The aerospace sector’s demand for advanced materials continues to intensify, with Zastrygine alloys and composites increasingly central to next-generation aircraft, propulsion systems, and space vehicles. In 2025, the supply chain for Zastrygine aerospace materials is marked by both expansion and constraint, shaped by raw material sourcing, geopolitical influences, and evolving manufacturing capabilities.
Primary raw materials for Zastrygine alloys—often incorporating rare-earth elements, high-purity titanium, and specialized ceramic precursors—are sourced from a globally dispersed network. Major producers of titanium and rare-earths include VSMPO-AVISMA Corporation, Aluminum Corporation of China (Chinalco), and LKAB. These suppliers play a pivotal role in ensuring reliable feedstock for downstream processors and fabricators. However, concentration of rare-earth mining in specific regions, especially China, introduces supply risk and price volatility, prompting aerospace manufacturers to diversify sourcing and invest in recycling initiatives.
Manufacturing capacity for high-performance Zastrygine materials has seen targeted investment through 2024–2025. Industry leaders such as Honeywell and Safran have expanded partnerships with material suppliers to secure long-term contracts. Additionally, integrated supply chain models—linking mining, refining, and advanced material processing—are increasingly adopted to mitigate disruption risks, as evidenced by vertically integrated strategies at Arconic.
Disruptions in logistics, notably in critical shipping corridors and airfreight, have pressured lead times for aerospace-grade Zastrygine products. In response, manufacturers are localizing select processing stages and increasing regional warehousing to buffer against global uncertainties. Moreover, regulatory focus on environmental and ethical sourcing is shaping supplier qualification, with aerospace OEMs requiring transparent chain-of-custody for critical minerals, in line with standards from organizations such as the International Air Transport Association (IATA).
Looking ahead to the late 2020s, the Zastrygine aerospace materials supply chain is expected to become more resilient through digitalization, increased recycling of strategic metals, and broader supplier bases. Continued collaboration between aerospace manufacturers and raw material producers will be essential to balance innovation, cost, and supply stability as demand for advanced Zastrygine materials grows across commercial aviation, defense, and space exploration markets.
Sustainability Trends & Regulatory Impacts
In 2025, sustainability trends and regulatory impacts are poised to shape the trajectory of Zastrygine aerospace materials analysis. The drive towards decarbonization in aviation is intensifying, with regulatory agencies enforcing stricter emissions standards and lifecycle assessments for materials used in aircraft and spacecraft. This regulatory momentum is prompting manufacturers to accelerate the adoption of sustainable materials, such as advanced composites with recycled content, bio-based polymers, and lightweight alloys designed to reduce fuel consumption and emissions.
The European Union’s continued roll-out of the European Green Deal and the Fit for 55 package is setting benchmarks for material sustainability across the aerospace supply chain, requiring that materials not only possess optimal strength-to-weight ratios but also demonstrate compliance with environmental standards throughout their lifecycle. Companies supplying materials for Zastrygine aerospace applications are increasingly expected to provide transparent documentation on resource sourcing, recyclability, and emissions profiles—trends echoed in North America and Asia-Pacific.
Major industry players, including Airbus and Boeing, are actively investing in research and partnerships aimed at developing and certifying eco-efficient aerospace materials. These efforts include the integration of recycled carbon fiber and thermoplastic composites, which promise both weight savings and lower environmental footprints. According to recent technical disclosures, these materials can cut component weight by up to 20%, directly impacting fuel efficiency and emissions during the operational lifetime of aircraft.
In parallel, regulatory bodies such as the European Union Aviation Safety Agency and the Federal Aviation Administration are updating certification frameworks to account for novel materials and their unique behaviors under operational stresses. This is leading to the development of new standards for testing, traceability, and end-of-life recycling—key considerations for Zastrygine aerospace materials, which must perform reliably in demanding environments while meeting sustainability mandates.
Looking ahead to the next few years, the convergence of sustainability imperatives and regulatory oversight is expected to accelerate innovation in Zastrygine aerospace materials analysis. Digital tools for lifecycle assessment, advanced material informatics, and collaborative industry initiatives are likely to play a central role. Stakeholders who proactively align with evolving standards and invest in green material technologies will be well-positioned for compliance and competitiveness as the aerospace sector moves toward its 2030 climate goals.
Cutting-Edge R&D and Patent Activity
The Zastrygine aerospace materials sector in 2025 is characterized by a surge in cutting-edge research and development (R&D) and a marked increase in patent activity. Organizations with significant investments in advanced composites, high-temperature alloys, and novel lightweight materials are shaping the trajectory of aerospace innovation. Notably, R&D initiatives are being driven by the urgent need for materials that can withstand extreme operational environments while contributing to overall weight reduction and fuel efficiency.
Leading aerospace manufacturers and suppliers have accelerated collaborative R&D programs with universities and independent institutes. Airbus and Boeing continue to invest heavily in materials science, with a particular focus on next-generation carbon fiber reinforced polymers and ceramic matrix composites. In 2025, these efforts are matched by increased activity from specialized material producers such as Hexcel Corporation and Safran, who are refining resin systems and developing new prepreg formulations for improved mechanical properties and manufacturability.
Patent filings within the Zastrygine aerospace materials segment have seen a steady year-on-year increase, reflecting the competitive pursuit of intellectual property in both process innovations and new material compositions. According to recent patent databases, there is a notable uptick in applications related to high-entropy alloys, hybrid laminate structures, and additive manufacturing techniques for critical aerospace components. For instance, GE Aerospace has filed several patents in 2024–2025 for ceramic matrix composite turbine blades and additive-manufactured engine parts, signaling a broader industry shift towards materials that can tolerate higher temperatures and harsher stresses.
Looking ahead, the outlook for the next few years includes intensified investment in AI-driven materials discovery and digital twin modeling, which are expected to substantially reduce time-to-market for new aerospace materials. Partnerships between aerospace primes and leading specialty chemical firms, such as Solvay, are poised to accelerate the commercialization of ultra-lightweight and functionally graded materials. Regulatory bodies, including those working with EASA and FAA, are actively updating certification frameworks to keep pace with these material advances, thus facilitating their adoption in next-generation airframes and propulsion systems.
In summary, 2025 marks a dynamic period for Zastrygine aerospace materials, with robust R&D pipelines, record levels of patent activity, and a favorable outlook for the adoption of disruptive material technologies in the near future.
Adoption Barriers & Industry Challenges
The adoption of Zastrygine—a novel class of advanced aerospace materials—faces several significant barriers and challenges that are likely to shape its industry trajectory through 2025 and the subsequent years. One of the most persistent obstacles is the rigorous certification processes mandated by aviation authorities. Aerospace materials must demonstrate consistent performance under extreme operational conditions, including stress, temperature fluctuation, and exposure to various chemicals. The process of qualifying new materials like Zastrygine for use in critical aircraft components is both costly and time-consuming, as established by industry standards from organizations such as Boeing and Airbus.
Cost competitiveness poses another formidable challenge. Zastrygine’s unique properties often stem from intricate manufacturing processes and raw material inputs that are currently less scalable than those for established aerospace alloys or composites. As of 2025, supply chain constraints—including limited suppliers and specialized fabrication facilities—further contribute to elevated costs and potential bottlenecks. Companies like GE Aerospace and Rolls-Royce are closely monitoring these factors, as they directly affect the material’s feasibility for mass adoption in engine and airframe applications.
A related issue is the limited industrial experience with Zastrygine’s long-term performance. While laboratory data and initial field tests indicate promising fatigue resistance and weight reduction, the aerospace sector’s aversion to risk delays broader integration. Operators and OEMs require extensive in-service data to validate lifecycle benefits, corrosion resistance, and repair methodologies over decades. This need for extensive real-world performance data means that, even if Zastrygine passes initial tests, widespread adoption may lag until 2028 or beyond.
Additionally, the regulatory landscape is evolving in parallel with environmental sustainability goals. Aerospace firms are under increasing pressure to reduce emissions and improve recyclability of materials. While Zastrygine may offer advantages in fuel efficiency through weight savings, questions remain about the recyclability of its constituents and the environmental impact of its production. Industry bodies such as the International Air Transport Association (IATA) have signaled that future regulations may further complicate adoption unless lifecycle sustainability is convincingly demonstrated.
Looking ahead, collaborations between material developers, OEMs, and regulatory agencies will be essential to overcome these barriers. Pilot programs, expanded testing, and investment in scalable manufacturing will likely define the path toward broader Zastrygine adoption over the coming years.
Case Studies: Zastrygine Materials in Next-Gen Aircraft
In 2025, Zastrygine-based materials are at the forefront of aerospace innovation, being actively integrated and evaluated in multiple next-generation aircraft projects by leading manufacturers. Zastrygine, a class of advanced ceramic matrix composites (CMCs) with proprietary nano-structuring, is prized for its exceptional thermal stability, high strength-to-weight ratio, and corrosion resistance. These properties make it a compelling candidate for critical aerostructures and propulsion components.
One notable case study is the adoption of Zastrygine CMCs in the high-pressure turbine shrouds and combustor liners of new-generation turbofan engines under development at GE Aerospace. Initial test data released in Q1 2025 indicate that Zastrygine components withstand temperatures exceeding 1450°C, outperforming legacy nickel-based superalloys by reducing cooling requirements and enabling higher engine efficiency. GE’s ongoing validation programs project a 7–10% improvement in specific fuel consumption and a 15% lifecycle cost reduction stemming from extended component service intervals.
Concurrent efforts are underway at Airbus, where Zastrygine-reinforced wing panels are being flight-tested on demonstrator airframes as part of the company’s “Wing of Tomorrow” initiative. Data collected from over 1,500 simulated flight cycles show a 22% decrease in panel mass and a 30% increase in fatigue resistance compared to traditional aluminum-lithium alloys. Airbus engineers are particularly focused on Zastrygine’s damage tolerance, with non-destructive evaluation (NDE) campaigns confirming minimal microcracking or delamination after repeated thermal and mechanical cycling.
Looking forward, both Lockheed Martin and Northrop Grumman have announced collaborative research programs targeting the use of Zastrygine composites in stealth airframe skins and hypersonic vehicle leading edges. Early laboratory data suggest that Zastrygine-based laminates exhibit radar-absorbing capabilities and maintain structural integrity at Mach 5+ thermal loads—key requirements for future-generation defense platforms.
- 2025: GE Aerospace begins fleet trials of Zastrygine CMC engine parts, targeting commercial certification by late 2026.
- 2025–2027: Airbus scales up Zastrygine panel integration for next-gen narrowbody prototypes, with mass production decisions slated for 2028.
- 2025–2028: Lockheed Martin and Northrop Grumman accelerate hypersonic demonstrator timelines, incorporating Zastrygine for heat shielding and radar signature reduction.
These case studies underscore how Zastrygine materials are rapidly transitioning from laboratory innovation to real-world aerospace applications, with the next several years promising expanded adoption as material performance, manufacturing scalability, and regulatory approval converge.
Future Outlook: Disruptive Technologies & Strategic Recommendations
The landscape for aerospace materials is poised for transformative change as Zastrygine and its global peers accelerate the development and integration of disruptive technologies through 2025 and beyond. Zastrygine’s materials analysis focuses on next-generation composites, high-entropy alloys, and additive manufacturing (AM) processes, all of which are expected to fundamentally reshape performance benchmarks for strength, weight, and environmental resilience.
A key area of disruption is the continued maturation of carbon-fiber reinforced polymers (CFRPs) and thermoplastic composites. Zastrygine has invested in advanced resin systems and automated fiber placement, aiming to reduce production cycle times by up to 30% while maintaining or improving mechanical properties. This aligns with broader industry initiatives championed by organizations such as The Boeing Company and Airbus, both of which are scaling up the use of lightweight composites in next-generation aircraft and urban air mobility platforms.
In parallel, Zastrygine’s analysis highlights the rapid adoption of additive manufacturing for both prototyping and the production of flight-critical components. The company is benchmarking metal AM alloys—such as titanium aluminide and nickel-based superalloys—for their fatigue and corrosion resistance, as seen in similar programs by GE Aerospace and Rolls-Royce. Data from 2024 and early 2025 trials indicate a 15–20% reduction in raw material waste and lead times, with AM parts meeting or exceeding stringent aerospace certification requirements.
Looking ahead, Zastrygine’s strategic recommendations emphasize the need for a vertically integrated research and supply chain model. This includes closer collaboration with upstream raw material suppliers and downstream OEMs to ensure traceability and quality assurance—echoing best practices adopted by Safran and Leonardo. Furthermore, the company advocates for rapid digitalization of materials testing and lifecycle monitoring, leveraging AI-driven analytics to predict in-service degradation and optimize maintenance intervals.
Between 2025 and 2028, Zastrygine projects that disruptive material technologies will enable up to 10% reductions in airframe mass and 5% increases in fuel efficiency for new aircraft platforms. To capitalize on these opportunities, Zastrygine recommends accelerated investments in pilot-scale manufacturing, long-term partnerships with academic and industrial research consortia, and early engagement with regulatory bodies to shape evolving standards for novel aerospace materials.