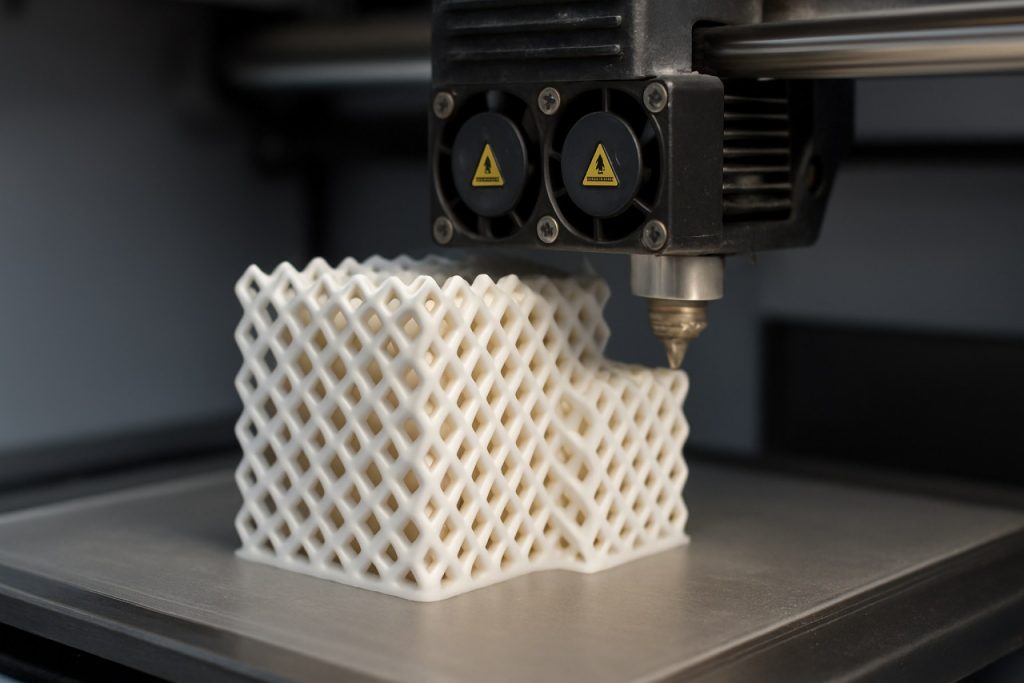
Zirconia Ceramic Additive Manufacturing in 2025: Unleashing Next-Gen Performance and Market Expansion. Explore How Advanced 3D Printing is Transforming High-Precision Industries.
- Executive Summary: Key Trends and 2025 Outlook
- Market Size, Growth Rate, and Forecasts to 2030
- Core Technologies: Innovations in Zirconia Ceramic 3D Printing
- Major Players and Strategic Partnerships (e.g., 3dceram.com, lithoz.com, ceramtec.com)
- End-Use Applications: Medical, Aerospace, Electronics, and Beyond
- Material Science Advances: Purity, Strength, and Processability
- Regional Analysis: North America, Europe, Asia-Pacific, and Emerging Markets
- Competitive Landscape and Barriers to Entry
- Sustainability, Regulatory, and Quality Standards (e.g., ceramtec.com, iso.org)
- Future Outlook: Disruptive Opportunities and Market Drivers to 2030
- Sources & References
Executive Summary: Key Trends and 2025 Outlook
Zirconia ceramic additive manufacturing (AM) is rapidly advancing as a critical technology for high-performance applications in sectors such as dental, medical, electronics, and aerospace. As of 2025, the field is characterized by significant improvements in material formulations, process reliability, and industrial adoption, driven by the unique properties of zirconia—such as high strength, fracture toughness, and biocompatibility.
Key trends shaping the zirconia ceramic AM landscape include the maturation of binder jetting, stereolithography (SLA), and digital light processing (DLP) techniques specifically optimized for zirconia powders and slurries. Leading equipment manufacturers such as 3D Systems and Lithoz have expanded their portfolios to include dedicated zirconia-capable printers, with Lithoz’s CeraFab systems and 3D Systems’s Figure 4 platform supporting high-density, medical-grade zirconia parts. These systems are now being deployed in both prototyping and serial production environments, particularly in dental prosthetics and custom medical implants.
Material suppliers such as Tosoh Corporation and Kerafol Keramische Folien GmbH have responded to growing demand by developing advanced zirconia powders and feedstocks tailored for AM processes, focusing on improved sinterability, particle size distribution, and consistency. This has enabled the production of parts with mechanical properties approaching those of conventionally manufactured zirconia ceramics, a key milestone for broader industrial acceptance.
In 2025, the dental sector remains the largest adopter of zirconia AM, with companies like CeramTec and Ivoclar integrating AM workflows for crowns, bridges, and implant abutments. The medical device industry is also accelerating adoption, leveraging the design freedom and patient-specific customization enabled by AM. Aerospace and electronics are emerging as growth areas, with ongoing qualification of zirconia AM components for wear-resistant and insulating applications.
Looking ahead, the outlook for zirconia ceramic AM is robust. Industry stakeholders anticipate further reductions in production costs, increased automation, and the introduction of multi-material and functionally graded zirconia parts. Standardization efforts and regulatory pathways are expected to mature, supporting wider adoption in safety-critical fields. As a result, zirconia AM is poised to transition from niche prototyping to mainstream manufacturing across multiple high-value sectors in the next few years.
Market Size, Growth Rate, and Forecasts to 2030
The global market for zirconia ceramic additive manufacturing (AM) is experiencing robust growth, driven by increasing demand for high-performance ceramics in sectors such as dental, medical, electronics, and aerospace. As of 2025, the market is characterized by a surge in adoption of advanced AM technologies—such as stereolithography (SLA), digital light processing (DLP), and binder jetting—capable of processing zirconia powders into complex, high-precision components. Key industry players, including 3D Systems, XJet, Lithoz, and CeramTec, are actively expanding their portfolios and production capacities to meet rising demand.
In 2025, the zirconia ceramic AM market is estimated to be valued in the low hundreds of millions USD, with a compound annual growth rate (CAGR) projected between 20% and 30% through 2030. This rapid expansion is underpinned by the increasing use of zirconia in dental prosthetics—where its biocompatibility and mechanical strength are highly valued—as well as in industrial applications requiring wear resistance and thermal stability. Companies such as Lithoz and XJet have reported significant growth in orders for their ceramic 3D printers and materials, particularly from dental labs and medical device manufacturers.
The Asia-Pacific region, led by China, Japan, and South Korea, is emerging as a major growth engine, fueled by investments in advanced manufacturing and healthcare infrastructure. European companies, notably Lithoz (Austria) and CeramTec (Germany), are also expanding their reach, leveraging strong R&D capabilities and established customer bases in medical and industrial sectors. North America remains a key market, with 3D Systems and XJet (with operations in the US and Israel) driving innovation and adoption.
Looking ahead to 2030, the zirconia ceramic AM market is expected to benefit from ongoing advancements in printer hardware, material formulations, and post-processing techniques. The introduction of multi-material and hybrid AM systems, as well as the integration of digital workflows, will further accelerate market penetration. Strategic partnerships between printer manufacturers, material suppliers, and end-users are anticipated to play a pivotal role in scaling production and reducing costs. As a result, zirconia ceramic AM is poised to become a mainstream manufacturing solution for high-value, precision components across multiple industries.
Core Technologies: Innovations in Zirconia Ceramic 3D Printing
Zirconia ceramic additive manufacturing (AM) is rapidly advancing, driven by the demand for high-performance components in sectors such as dental, medical, electronics, and aerospace. As of 2025, the field is characterized by the maturation of several core technologies, each addressing the unique challenges of processing zirconia—an advanced ceramic prized for its mechanical strength, fracture toughness, and biocompatibility.
Among the most prominent technologies is stereolithography (SLA) and digital light processing (DLP), which use photopolymerizable ceramic slurries. These methods enable the production of highly detailed zirconia parts with fine feature resolution and smooth surface finishes. Companies like Lithoz GmbH have established themselves as leaders in this space, offering industrial DLP-based systems specifically optimized for zirconia and other technical ceramics. Their CeraFab systems are widely adopted in both research and production environments, with ongoing improvements in slurry formulation and process automation expected to further enhance throughput and part quality in the coming years.
Another significant innovation is binder jetting, which allows for the rapid fabrication of complex zirconia geometries without the need for support structures. ExOne, now part of Desktop Metal, has developed binder jetting platforms capable of processing ceramic powders, including zirconia, with post-processing sintering steps to achieve full density. This technology is gaining traction for applications requiring larger build volumes and faster production rates, such as industrial tooling and custom medical devices.
Material extrusion, particularly in the form of fused filament fabrication (FFF) and robocasting, is also being refined for zirconia. 3DCeram and CeramTec are notable for their work in developing printable zirconia pastes and filaments, enabling more accessible entry points for laboratories and small-scale manufacturers. These approaches are expected to benefit from advances in feedstock formulation and extrusion hardware, improving both the mechanical properties and dimensional accuracy of printed parts.
Looking ahead, the outlook for zirconia ceramic AM is robust. The convergence of improved printer architectures, smarter process monitoring, and more reliable material systems is set to drive broader adoption across industries. The dental sector, in particular, is anticipated to remain a key growth area, with companies like CeramTec and Lithoz GmbH expanding their offerings for chairside and laboratory-based solutions. As these technologies mature, the next few years will likely see increased standardization, cost reductions, and the emergence of new applications leveraging the unique properties of zirconia ceramics.
Major Players and Strategic Partnerships (e.g., 3dceram.com, lithoz.com, ceramtec.com)
The zirconia ceramic additive manufacturing (AM) sector is rapidly evolving, with several major players driving innovation, commercialization, and global adoption. As of 2025, the landscape is characterized by a mix of established ceramics manufacturers, specialized AM technology providers, and strategic partnerships aimed at scaling production and expanding application domains.
A leading force in this field is 3DCeram, a French company specializing in stereolithography (SLA) for technical ceramics, including zirconia. 3DCeram’s turnkey solutions—encompassing printers, materials, and post-processing—are widely adopted in medical, dental, and industrial sectors. The company has recently expanded its global footprint through collaborations with research institutes and industrial partners, focusing on high-precision dental prosthetics and complex industrial components.
Another key innovator is Austria-based Lithoz, renowned for its LCM (Lithography-based Ceramic Manufacturing) technology. Lithoz’s systems are capable of producing dense, high-strength zirconia parts with intricate geometries, making them a preferred choice for biomedical and aerospace applications. In 2024–2025, Lithoz has intensified its strategic partnerships, notably with major dental manufacturers and research consortia, to accelerate the adoption of 3D-printed zirconia in serial production. The company’s ongoing R&D efforts are also directed at multi-material printing and scaling up throughput for industrial users.
On the materials side, CeramTec stands out as a global supplier of advanced ceramic materials, including high-purity zirconia powders and components. While CeramTec is traditionally known for conventional manufacturing, it has increasingly engaged in additive manufacturing initiatives, supplying tailored zirconia feedstocks compatible with leading AM platforms. The company’s collaborations with printer manufacturers and end-users are aimed at optimizing material properties and ensuring regulatory compliance, especially for medical and dental applications.
Strategic partnerships are a defining trend in 2025. For example, equipment manufacturers are teaming up with dental labs and medical device companies to streamline the workflow from digital design to finished zirconia implants. Cross-industry alliances are also emerging, with aerospace and electronics firms exploring the unique properties of 3D-printed zirconia for high-performance applications. These collaborations are expected to accelerate certification processes, improve supply chain resilience, and foster the development of new standards for ceramic AM.
Looking ahead, the next few years will likely see further consolidation among technology providers, deeper integration of digital workflows, and the entry of new players from adjacent sectors. The continued focus on strategic partnerships and ecosystem-building is poised to drive the mainstream adoption of zirconia ceramic additive manufacturing across diverse industries.
End-Use Applications: Medical, Aerospace, Electronics, and Beyond
Zirconia ceramic additive manufacturing (AM) is rapidly advancing as a transformative technology for high-performance end-use applications across medical, aerospace, electronics, and other sectors. In 2025 and the coming years, the adoption of zirconia AM is expected to accelerate, driven by its unique combination of mechanical strength, biocompatibility, and thermal stability.
In the medical field, zirconia’s biocompatibility and wear resistance make it a preferred material for dental restorations, implants, and surgical tools. Additive manufacturing enables the production of highly customized dental crowns, bridges, and implant abutments with complex geometries and precise fit. Companies such as 3D Systems and XJet are actively developing and commercializing zirconia AM solutions for dental and orthopedic applications, leveraging technologies like binder jetting and nanoparticle jetting to achieve high density and surface quality. The trend toward patient-specific medical devices is expected to further boost demand for zirconia AM in the healthcare sector.
In aerospace, the need for lightweight, high-temperature-resistant components is driving interest in advanced ceramics. Zirconia’s thermal shock resistance and low thermal conductivity make it suitable for applications such as turbine components, thermal barriers, and sensor housings. Additive manufacturing allows for the design of intricate cooling channels and lattice structures that are difficult or impossible to achieve with traditional methods. CeramTec and 3DCeram are among the companies exploring aerospace-grade zirconia parts, with ongoing collaborations with aerospace OEMs to qualify AM components for flight-critical applications.
The electronics industry is also embracing zirconia AM for its electrical insulation properties and chemical inertness. Applications include substrates for microelectronics, insulators, and components for high-frequency devices. The ability to rapidly prototype and produce small batches of complex ceramic parts is particularly valuable for R&D and low-volume production. CeramTec and XJet are notable players providing solutions for electronic and semiconductor applications.
Beyond these sectors, zirconia AM is being explored for energy, automotive, and industrial tooling applications, where its hardness and corrosion resistance offer significant advantages. As process reliability, throughput, and material properties continue to improve, the outlook for zirconia ceramic additive manufacturing is robust, with increasing adoption expected across a broad range of high-value industries through 2025 and beyond.
Material Science Advances: Purity, Strength, and Processability
Zirconia ceramic additive manufacturing (AM) is experiencing significant material science advances, particularly in the domains of purity, mechanical strength, and processability. As of 2025, the industry is witnessing a convergence of improved powder synthesis, binder chemistry, and sintering protocols, all aimed at unlocking the full potential of zirconia for demanding applications in medical, dental, and industrial sectors.
A key trend is the refinement of zirconia powder characteristics. Leading manufacturers such as Tosoh Corporation and Kyocera Corporation are producing ultra-high-purity yttria-stabilized zirconia (YSZ) powders with controlled particle size distributions and minimal agglomeration. These powders are tailored for AM processes like stereolithography (SLA), digital light processing (DLP), and binder jetting, ensuring dense, defect-free final parts. Purity levels exceeding 99.9% are now standard, directly impacting the mechanical reliability and biocompatibility of printed components.
Mechanical strength remains a focal point, with recent advances enabling printed zirconia parts to approach or match the properties of conventionally manufactured ceramics. For instance, the adoption of optimized sintering cycles and the use of advanced dopants have led to flexural strengths surpassing 1,000 MPa and fracture toughness values above 8 MPa·m1/2. Companies like 3DCeram and CeramTec are at the forefront, offering AM-ready zirconia materials and validated process parameters that minimize porosity and maximize density, critical for load-bearing applications.
Processability is also advancing rapidly. The development of new photopolymerizable resins and optimized binder systems has expanded the range of printable geometries and reduced post-processing complexity. Lithoz GmbH has introduced proprietary LCM (Lithography-based Ceramic Manufacturing) technology, enabling the production of intricate zirconia parts with layer thicknesses as low as 25 microns and surface finishes suitable for end-use applications. These innovations are reducing the gap between design freedom and manufacturability, a long-standing challenge in ceramic AM.
Looking ahead to the next few years, the outlook is for further integration of in-situ monitoring and closed-loop process control, which will enhance reproducibility and quality assurance. The ongoing collaboration between material suppliers, printer manufacturers, and end-users is expected to yield new zirconia formulations with tailored properties for specific industries, such as ultra-translucent dental ceramics and wear-resistant industrial components. As the ecosystem matures, zirconia AM is poised to transition from prototyping to full-scale production, driven by these material science breakthroughs.
Regional Analysis: North America, Europe, Asia-Pacific, and Emerging Markets
The global landscape for zirconia ceramic additive manufacturing (AM) is rapidly evolving, with distinct regional dynamics shaping the sector’s growth and innovation. As of 2025, North America, Europe, and Asia-Pacific remain the primary hubs for technological advancement and market adoption, while emerging markets are beginning to establish a presence in this specialized field.
North America continues to be a leader in zirconia ceramic AM, driven by robust investments in research, a strong base of advanced manufacturing, and the presence of pioneering companies. The United States, in particular, is home to key players such as 3D Systems and ExOne (now part of Desktop Metal), both of which have expanded their ceramic AM portfolios to include zirconia-based solutions. The region benefits from close collaboration between industry and research institutions, supporting the development of new materials and scalable production methods. The medical and dental sectors are significant adopters, leveraging zirconia’s biocompatibility and mechanical properties for implants and prosthetics.
Europe is characterized by a strong emphasis on precision engineering and materials science, with Germany, France, and Switzerland at the forefront. Companies such as CeramTec and 3DCeram are recognized for their expertise in technical ceramics and have made substantial investments in additive manufacturing technologies for zirconia. The European Union’s focus on advanced manufacturing and sustainability is fostering innovation in powder development, binder jetting, and stereolithography processes. The region’s automotive, aerospace, and healthcare industries are increasingly integrating zirconia AM for high-performance components, supported by a well-established regulatory framework.
Asia-Pacific is witnessing rapid growth, led by China, Japan, and South Korea. The region’s expansion is fueled by government initiatives to localize advanced manufacturing and by the presence of major ceramics producers. Companies such as Tosoh Corporation in Japan are notable for their production of high-purity zirconia powders, which are essential for AM applications. China’s manufacturing ecosystem is quickly adopting ceramic AM, with a focus on cost-effective production and scaling up for industrial applications. The dental and electronics sectors are particularly active, reflecting the region’s broader industrial strengths.
Emerging markets in Latin America, the Middle East, and parts of Southeast Asia are at an earlier stage of adoption. However, increasing awareness of the benefits of zirconia ceramics and the gradual establishment of AM infrastructure are expected to drive growth in the coming years. Partnerships with established technology providers and investments in workforce training are likely to accelerate regional capabilities.
Looking ahead, the next few years are expected to see intensified competition and collaboration across regions, with ongoing advancements in material quality, process reliability, and application diversity. As the technology matures, regional strengths—such as North America’s innovation ecosystem, Europe’s regulatory leadership, and Asia-Pacific’s manufacturing scale—will continue to shape the global trajectory of zirconia ceramic additive manufacturing.
Competitive Landscape and Barriers to Entry
The competitive landscape of zirconia ceramic additive manufacturing (AM) in 2025 is characterized by a mix of established ceramics producers, specialized AM technology developers, and a growing number of entrants leveraging advances in materials science and digital manufacturing. The sector is still relatively niche compared to metal or polymer AM, but it is rapidly evolving as demand for high-performance ceramics in medical, dental, electronics, and aerospace applications increases.
Key players in the zirconia AM market include 3D Systems, which offers ceramic 3D printing solutions through its Figure 4 platform, and XJet, known for its NanoParticle Jetting technology that enables the production of dense, high-precision zirconia parts. Lithoz is another significant competitor, specializing in LCM (Lithography-based Ceramic Manufacturing) and collaborating with both industrial and medical partners to expand the use of zirconia in additive manufacturing. CeramTec, a global leader in advanced ceramics, has also entered the AM space, focusing on the development and supply of zirconia powders and components for 3D printing.
Barriers to entry in this sector remain substantial. The foremost challenge is the technical complexity of processing zirconia, which requires precise control over particle size, binder systems, and sintering protocols to achieve the desired mechanical and aesthetic properties. The capital investment for specialized AM equipment and post-processing infrastructure is significant, often limiting participation to well-funded companies or those with existing ceramics expertise. Intellectual property (IP) protection is another hurdle, as leading firms have secured patents on key processes and formulations, creating a high threshold for new entrants.
Material qualification and regulatory compliance, especially for medical and dental applications, further complicate market entry. Companies must demonstrate biocompatibility, mechanical reliability, and repeatability, which involves extensive testing and certification. This is particularly relevant for dental zirconia, where Envista Holdings (through its Nobel Biocare and KaVo Kerr brands) and Straumann Group are prominent, leveraging their regulatory experience and distribution networks to maintain competitive advantage.
Looking ahead, the competitive landscape is expected to intensify as more materials companies and AM technology providers invest in zirconia solutions. However, the high technical and regulatory barriers will likely continue to favor established players and those with strong R&D capabilities. Strategic partnerships between AM hardware manufacturers, materials suppliers, and end-users are anticipated to accelerate innovation and adoption, but the path to widespread commercialization remains challenging in the near term.
Sustainability, Regulatory, and Quality Standards (e.g., ceramtec.com, iso.org)
Zirconia ceramic additive manufacturing (AM) is rapidly evolving, with sustainability, regulatory compliance, and quality standards becoming central to its industrial adoption in 2025 and the coming years. As the sector matures, manufacturers and end-users are increasingly focused on minimizing environmental impact, ensuring product safety, and meeting stringent quality benchmarks.
Sustainability is a growing priority for zirconia AM, driven by both regulatory pressures and customer demand. Additive processes inherently offer material efficiency advantages over traditional subtractive methods, as they generate less waste and enable near-net-shape production. Leading ceramic manufacturers such as CeramTec are actively promoting the environmental benefits of advanced ceramics, including zirconia, highlighting their durability, recyclability, and potential for energy savings in end-use applications. In 2025, companies are expected to further invest in closed-loop recycling of zirconia powders and the use of renewable energy in production facilities, aligning with broader industry sustainability goals.
Regulatory frameworks are also tightening around advanced ceramics, particularly in sectors like medical devices, dental prosthetics, and aerospace, where zirconia AM is gaining traction. Compliance with international standards is essential. The International Organization for Standardization (ISO) continues to update and expand its portfolio of standards relevant to ceramic materials and additive manufacturing, such as ISO 13356 for implantable zirconia ceramics and ISO/ASTM 52900 series for AM processes. In 2025, the industry anticipates further harmonization of standards to address the unique challenges of additively manufactured ceramics, including powder quality, process validation, and traceability.
Quality assurance remains a critical focus. Companies like CeramTec and 3DCeram are implementing rigorous in-process monitoring, post-processing inspection, and certification protocols to ensure that zirconia AM parts meet or exceed conventional benchmarks for strength, biocompatibility, and dimensional accuracy. Automated quality control systems, including non-destructive testing and digital twins, are being adopted to support repeatability and scalability.
Looking ahead, the outlook for zirconia ceramic AM is shaped by the convergence of sustainability initiatives, evolving regulatory landscapes, and the drive for uncompromising quality. As industry standards become more robust and widely adopted, and as manufacturers invest in greener and more transparent supply chains, zirconia AM is poised to expand its role in high-value, safety-critical applications across healthcare, electronics, and beyond.
Future Outlook: Disruptive Opportunities and Market Drivers to 2030
The future outlook for zirconia ceramic additive manufacturing (AM) through 2030 is shaped by a convergence of technological advancements, expanding industrial applications, and strategic investments from leading materials and AM system providers. As of 2025, zirconia’s unique combination of high strength, fracture toughness, and biocompatibility continues to drive its adoption in sectors such as dental, medical, electronics, and advanced engineering.
A key market driver is the ongoing evolution of AM hardware and materials specifically optimized for zirconia. Companies like 3D Systems and XJet have developed specialized printers and processes—such as binder jetting and nano-particle jetting—that enable the production of dense, high-precision zirconia parts. XJet’s Carmel AM systems, for example, are already being used for dental and medical applications, and the company is expanding its material portfolio to include advanced zirconia formulations. Similarly, 3D Systems has partnered with dental labs and device manufacturers to deliver patient-specific zirconia implants and prosthetics, leveraging the material’s superior wear resistance and aesthetics.
Another significant driver is the increasing demand for personalized healthcare solutions. The dental sector, in particular, is witnessing rapid adoption of zirconia AM for crowns, bridges, and implant abutments, with companies like CeramTec and Ivoclar supplying high-purity zirconia powders and preforms tailored for AM processes. These companies are investing in R&D to improve powder flowability, sintering behavior, and final part properties, aiming to reduce production costs and expand the range of printable geometries.
Looking ahead, the electronics and aerospace industries are poised to become major growth areas. Zirconia’s electrical insulation and thermal stability make it attractive for components such as substrates, sensors, and fuel cell parts. CeramTec and Tosoh Corporation are actively developing advanced zirconia materials for these high-performance applications, with pilot projects underway to validate AM’s potential for complex, miniaturized parts.
By 2030, the convergence of digital manufacturing, material innovation, and regulatory acceptance is expected to unlock disruptive opportunities for zirconia AM. The sector will likely see increased automation, in-line quality control, and integration with digital workflows, further reducing lead times and enabling mass customization. As more industries recognize the value proposition of zirconia AM—combining design freedom with exceptional material properties—the market is set for robust growth, with established players and new entrants alike driving innovation and adoption.