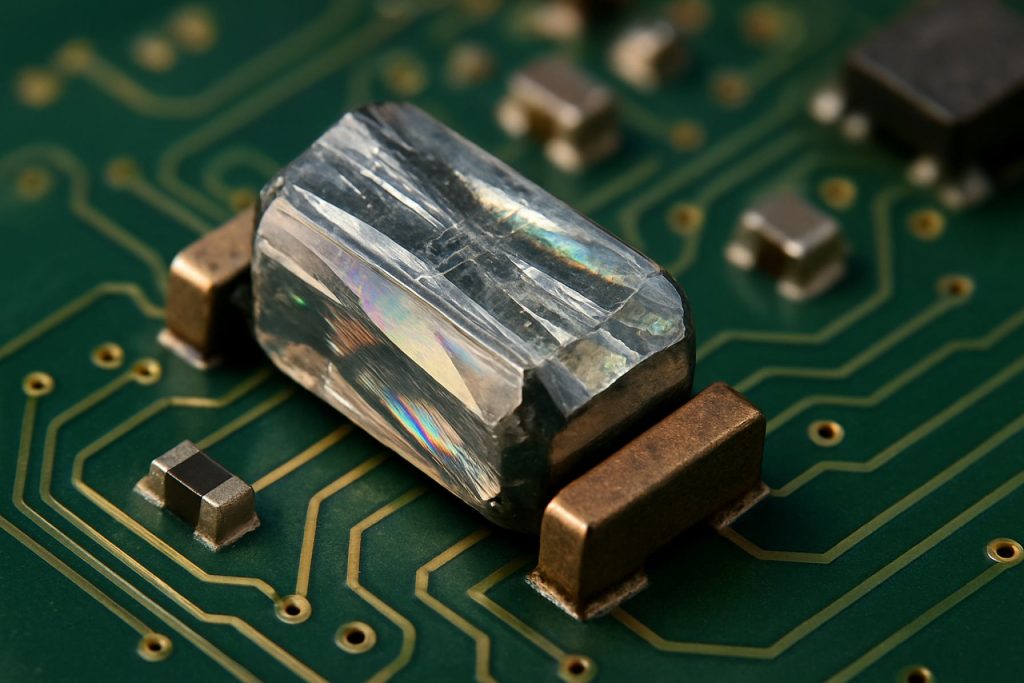
Why Zirconium Crystal Resonator Manufacturing Is Poised for Disruption in 2025: New Innovations, Market Leaders, and What’s About to Change Everything
- Executive Summary: 2025 Outlook & Key Takeaways
- Global Market Size and 5-Year Forecast (2025–2029)
- Breakthroughs in Zirconium Crystal Resonator Technology
- Leading Manufacturers and Industry Players
- Supply Chain Dynamics and Sourcing Strategies
- Emerging Applications in Electronics and Beyond
- Regulatory Updates and Industry Standards
- Competitive Landscape: Mergers, Partnerships & Innovations
- Sustainability, Environmental Impact, and Material Sourcing
- Future Trends: Where Is Zirconium Resonator Manufacturing Headed?
- Sources & References
Executive Summary: 2025 Outlook & Key Takeaways
The zirconium crystal resonator manufacturing sector enters 2025 at an inflection point, shaped by rising demand for high-performance frequency control devices across telecommunications, automotive, and advanced industrial applications. Zirconium-based resonators, prized for their superior thermal stability, mechanical robustness, and resistance to corrosion, are increasingly being adopted in environments demanding extreme reliability and miniaturization.
Major manufacturers, such as Murata Manufacturing Co., Ltd. and Kyocera Corporation, have continued to scale their investments in advanced crystal growth techniques and automated assembly lines. These companies, long established as leaders in piezoelectric and precision ceramic components, are expanding their production capacities to address growing orders from 5G infrastructure and automotive electronics suppliers. In particular, Murata’s commitment to innovation in frequency control technology is evident in its continuous R&D investments, with a specific focus on material purity and process automation for zirconium-based components.
Meanwhile, TDK Corporation, another key player in the resonator market, is leveraging its expertise in thin-film and bulk acoustic wave technology to refine the manufacturing of zirconium crystal resonators. TDK’s integration of zirconium materials into their resonator lines aims to meet stringent demands for high-frequency precision and miniaturization, especially relevant for next-generation wireless modules and IoT devices.
From a supply chain perspective, upstream suppliers such as Kenmare Resources plc and Iluka Resources Limited remain vital, ensuring consistent availability of high-purity zirconium oxide feedstock—a critical precursor for stable crystal growth and device performance. These mining and refining leaders are under pressure to meet the rising quality and volume requirements as downstream manufacturers scale up production.
Looking forward to the remainder of 2025 and the subsequent few years, the market outlook is characterized by:
- Continued growth in demand from 5G, EVs, and industrial automation sectors, driving further capacity expansions and process innovation.
- Focus on yield improvement and defect reduction through adoption of advanced crystal growth methods, such as Czochralski and hydrothermal techniques, across leading manufacturers.
- Heightened collaboration between materials suppliers and device makers to ensure traceability and quality throughout the supply chain, supporting long-term reliability targets.
- Ongoing R&D into novel zirconium-based alloys and composite ceramics, aimed at further enhancing resonator performance under harsh operating conditions.
In summary, 2025 is set to be a pivotal year for zirconium crystal resonator manufacturing, with established industry leaders, including Murata Manufacturing Co., Ltd., Kyocera Corporation, and TDK Corporation, spearheading technological advancements and capacity growth to meet the evolving needs of high-reliability electronics markets.
Global Market Size and 5-Year Forecast (2025–2029)
The global market for zirconium crystal resonator manufacturing is poised for moderate but steady growth in 2025 and the following years, driven by increasing demand for high-stability frequency control components in advanced electronics, telecommunications, and industrial applications. Zirconium-based resonators, valued for their superior temperature stability and corrosion resistance, are gradually gaining attention as alternatives or complements to traditional quartz crystal resonators, especially in environments with extreme conditions or stringent reliability requirements.
Key players in the frequency control and resonator sector, such as Murata Manufacturing Co., Ltd., Kyocera Corporation, and Nihon Dempa Kogyo Co., Ltd. (NDK), continue to invest in R&D for advanced materials, including zirconium compounds, to enhance performance characteristics of resonators. Although quartz remains the dominant material, these companies are actively exploring zirconium’s potential, especially for applications requiring greater resistance to environmental stressors. Production lines are being optimized for material flexibility, allowing for incremental adoption of zirconium-based technologies as market demand increases.
Recent data from leading manufacturers and supplier announcements suggest that the total market size for zirconium crystal resonators remains niche in 2025, likely representing a small single-digit percentage of the broader crystal device market, which is valued in the multi-billion-dollar range annually. However, forecasts indicate a compound annual growth rate (CAGR) of 6–9% for zirconium resonator segments through 2029, outpacing overall industry averages due to expanding adoption in aerospace, automotive electronics, and harsh industrial environments.
Regionally, strong growth is expected in East Asia—particularly Japan, South Korea, and China—where major electronics manufacturers and material suppliers are located. Companies like TDK Corporation and Seiko Holdings Corporation are also monitoring material trends and may expand zirconium-based offerings, building on their expertise in crystal device fabrication and integration.
Looking ahead, the market outlook for 2025–2029 anticipates gradual scaling of zirconium crystal resonator production as manufacturing processes mature and supply chains stabilize. Continued collaboration between material suppliers, device manufacturers, and end users is expected to drive innovation, lower costs, and expand application areas. As a result, industry observers project that by 2029, zirconium resonators could account for a more significant share of specialty frequency control devices, especially in sectors prioritizing advanced performance and reliability.
Breakthroughs in Zirconium Crystal Resonator Technology
The manufacturing of zirconium crystal resonators is experiencing significant breakthroughs as we move into 2025, driven by both technological advances in crystal growth and mounting demand for high-performance frequency control components in next-generation electronics. Zirconium-based crystal resonators are valued for their exceptional thermal stability, mechanical strength, and resistance to corrosion, making them attractive for applications in aerospace, telecommunications, and precision instrumentation.
One of the foremost advancements in 2025 is the refinement of crystal growth techniques, particularly the Czochralski and Bridgman methods. These processes have benefited from improved automation and real-time monitoring systems, allowing manufacturers to achieve higher crystal purity and consistency, essential for device reliability. Key industry players such as Murata Manufacturing Co., Ltd. and NICHICON CORPORATION have reported investments in advanced furnace technologies and enhanced process controls, which are expected to further reduce defects and enable the production of larger single-crystal zirconium boules.
Material engineering is also making strides, with companies exploring sophisticated doping strategies to tailor the piezoelectric and mechanical properties of zirconium crystals. For instance, doping with rare earth elements and precise control of oxygen vacancies are being implemented to improve resonator Q-factor and long-term stability. This trend aligns with the industry shift towards more miniaturized, high-frequency components for 5G/6G infrastructure and quantum computing hardware.
On the manufacturing front, leading suppliers such as TXC Corporation and Daishinku Corp. (KDS) are deploying high-precision dicing and wafer-level packaging technologies that increase yield and reduce material waste. Adoption of cleanroom robotics and AI-driven inspection systems is further enhancing throughput and quality assurance, a necessity as demand projections for zirconium resonators are set to rise sharply with the proliferation of IoT and automotive radar systems.
Looking ahead, the outlook for the zirconium crystal resonator sector remains robust. Collaborative R&D programs—often involving university-industry partnerships—are expected to accelerate the introduction of next-generation zirconium-based devices, with a focus on ultra-high-frequency operation and integration into multi-functional MEMS packages. As sustainability becomes more pressing, manufacturers are also beginning to implement closed-loop recycling of zirconium process waste, responding to both regulatory and market pressures.
Overall, 2025 marks a year of momentum for zirconium crystal resonator manufacturing, characterized by process innovation, material breakthroughs, and a keen focus on scalability to meet evolving market requirements.
Leading Manufacturers and Industry Players
The global market for zirconium crystal resonators is poised for significant growth through 2025 and beyond, driven by advances in electronics miniaturization, telecommunications, and precision timing devices. Zirconium-based resonators, valued for their exceptional thermal stability, mechanical robustness, and resistance to chemical degradation, are seeing increased adoption in sectors demanding high-reliability frequency control components.
Among the dominant industry participants, Murata Manufacturing Co., Ltd. stands out as a key innovator and supplier in the advanced ceramics and resonator markets. Murata leverages its vertically integrated manufacturing capabilities and extensive research in piezoelectric materials to develop high-performance zirconium-based components for both consumer and industrial applications. The company continues to invest in next-generation resonator technologies, with R&D facilities in Japan and global manufacturing sites ensuring robust supply chains and technical support.
Another prominent player is TDK Corporation, which has expanded its frequency control product lines to include crystal resonators utilizing advanced zirconium ceramic technologies. TDK’s focus on miniaturization and integration aligns with the growing demand for compact, high-precision resonators in wireless communication modules, automotive electronics, and IoT devices. The company’s global footprint and collaborative partnerships with leading electronics firms position it as a critical supplier throughout 2025.
In addition to Japanese conglomerates, Kyocera Crystal Device (KDS), a division of Kyocera Corporation, remains a major force in the development and manufacture of crystal resonators, leveraging proprietary zirconium formulations to enhance frequency accuracy and environmental durability. KDS’s investments in advanced manufacturing equipment and process automation are expected to further boost production capacity in the coming years, supporting both legacy and emerging applications.
On the specialty material side, Fujiceramics Corporation supplies high-purity zirconium oxide ceramics for use in resonator fabrication, providing critical input materials for downstream device manufacturers. Their collaborations with device makers ensure optimized material properties tailored to evolving application requirements.
Looking forward, the competitive landscape is likely to see increased participation from Chinese and South Korean manufacturers, who are ramping up investments in zirconium-based electronic components. With ongoing innovations in crystal growth techniques, thin-film deposition, and surface treatment, industry leaders are well-positioned to meet the stringent demands of next-generation electronics, further solidifying their positions in the global market over the next several years.
Supply Chain Dynamics and Sourcing Strategies
The supply chain dynamics for zirconium crystal resonator manufacturing in 2025 are shaped by both the unique requirements of high-purity zirconium and the evolving global landscape of advanced materials. In recent years, demand for precision frequency control components—especially for 5G, IoT, and automotive electronics—has driven manufacturers to secure more robust and traceable sourcing strategies for zirconium-based materials. The resilience of the zirconium supply chain is critical, as even minor impurities can impair resonator performance and long-term reliability.
Most commercial zirconium originates from mineral sands (notably zircon, or zirconium silicate), with major mining and primary refining operations concentrated in Australia, South Africa, and China. Companies such as Iluka Resources and Richards Bay Minerals play pivotal roles in the initial extraction and supply of zirconium feedstock. However, the transformation of raw zircon into the ultra-high-purity forms needed for crystal resonator applications requires advanced chemical processing and crystallization technologies, typically performed by specialized materials suppliers.
In 2025, leading resonator manufacturers, including Nihon Dempa Kogyo Co., Ltd. (NDK), Seiko Instruments Inc., and TDK Corporation, continue to reinforce vertical integration and long-term supply contracts to mitigate risks associated with geopolitical shifts and potential disruptions in mineral export policies. These companies actively collaborate with upstream suppliers to ensure traceability, consistent purity, and compliance with environmental and ethical sourcing standards. For instance, NDK has broadened its supplier qualification protocols and invested in direct partnerships with chemical refiners to secure a steady flow of high-purity zirconium oxides and crystals.
Supply chain diversification is another emerging strategy, with more manufacturers seeking secondary sources of zirconium feedstock and recycling initiatives to buffer against fluctuations in raw material availability. Efforts to improve the efficiency of zirconium utilization during crystal growth and wafer slicing are also gaining momentum, as even minor enhancements can yield significant cost and waste reductions.
Looking ahead, the outlook for zirconium crystal resonator manufacturing is one of cautious optimism. While the global supply of zirconium remains stable, ongoing technological advancements and the opening of new refining capacities in Asia and Africa are expected to further insulate the supply chain. At the same time, the sector is alert to potential bottlenecks arising from increased demand in competing applications such as nuclear energy and advanced ceramics, making agile sourcing strategies and close supplier partnerships vital for sustained growth through the next several years.
Emerging Applications in Electronics and Beyond
In 2025, the manufacturing of zirconium crystal resonators is gaining momentum, driven by the expanding demand for high-stability frequency control components across electronics, telecommunications, and emerging frontier technologies. Zirconium-based resonators are being explored as alternatives or complements to traditional quartz devices due to their superior mechanical strength, corrosion resistance, and potential for miniaturization. These properties are increasingly relevant as the electronics industry pushes toward more robust and compact solutions for 5G, IoT, and quantum computing applications.
Key manufacturers with established expertise in crystal device fabrication, such as Seiko Instruments Inc., Kyocera Corporation, and TDK Corporation, are actively investing in research and pilot production lines for non-traditional crystal resonators, including those based on zirconium compounds. While quartz continues to dominate, these companies are leveraging their materials science capabilities to address the challenges specific to zirconium—such as achieving uniform single-crystal growth and stable frequency characteristics under varying thermal and electrical loads.
Several collaborative projects in Japan, Europe, and the United States are underway to refine the Czochralski and hydrothermal methods for zirconium crystal growth, aiming to improve yield and purity. Krosaki Harima Corporation, known for its advanced ceramic materials, has announced joint ventures with electronics companies to supply high-grade zirconium oxide for resonator substrates. Similarly, Saint-Gobain is scaling up its production of technical ceramics, including stabilized zirconia, targeting the high-frequency component market.
In terms of applications, 2025 is expected to see the first commercial deployments of zirconium crystal resonators in harsh environments—such as aerospace, energy, and automotive systems—where conventional quartz devices face limitations. Research and pilot adoption are also occurring in precision timing modules for new-generation base stations and edge devices. With the continuing miniaturization trend, the integration of zirconium resonators into chip-scale packages is being explored, with Murata Manufacturing Co., Ltd. and Nichia Corporation leading proof-of-concept initiatives in their advanced component labs.
Looking ahead to the next few years, industry outlook is cautiously optimistic. As manufacturing techniques mature and supply chains for high-purity zirconium stabilize, broader adoption is anticipated. Standardization efforts by international electronics consortia are also expected to accelerate, facilitating interoperability and boosting market confidence in zirconium crystal resonator technologies.
Regulatory Updates and Industry Standards
The landscape of regulatory updates and industry standards for zirconium crystal resonator manufacturing is undergoing significant evolution in 2025, driven by both advances in material science and heightened global focus on supply chain security and product reliability. Zirconium crystal resonators, employed in precision timing devices and advanced sensor technologies, fall under the broader regulatory frameworks governing piezoelectric and electronic component manufacturing. Several notable events and trends are shaping the sector this year and are expected to influence the coming years.
In 2025, the International Electrotechnical Commission (IEC) continues to update its standards for piezoelectric materials and resonator devices, with specific attention to the traceability of raw materials, environmental impact, and device reliability. These updates align with the increasing adoption of zirconium-based materials, valued for their high-temperature stability and corrosion resistance. Leading manufacturers such as Murata Manufacturing Co., Ltd. and TDK Corporation—both of which have established expertise in advanced crystal and ceramic resonators—are actively participating in IEC technical committees, influencing the direction of new standards.
Environmental and safety regulations are tightening globally, particularly concerning the extraction and processing of zirconium. Regulatory bodies in the European Union and Japan are implementing stricter controls on heavy metal emissions and the handling of rare earth elements during crystal growth and wafer processing. Compliance with the EU’s Registration, Evaluation, Authorisation and Restriction of Chemicals (REACH) and the Restriction of Hazardous Substances (RoHS) directives is now mandatory for all zirconium resonator products sold in the European market. Major producers such as STMicroelectronics and Kyocera Corporation are investing in greener manufacturing processes and more transparent supply chain management to ensure compliance.
Industry associations, including the Japan Electronics and Information Technology Industries Association (JEITA) and the Electronic Components Industry Association (ECIA), are working closely with manufacturers to harmonize testing protocols and reliability standards for zirconium-based resonators. This collaboration is expected to result in the publication of updated qualification procedures and performance benchmarks in 2025-2026, aimed at supporting the integration of zirconium resonators into automotive, telecommunications, and aerospace applications.
Looking ahead, the regulatory environment for zirconium crystal resonator manufacturing is expected to become even more stringent, with a strong emphasis on lifecycle analysis, recyclability, and the reduction of hazardous substances. Manufacturers are proactively engaging with standards bodies to prepare for forthcoming requirements, ensuring that their products remain compliant and competitive in fast-evolving global markets.
Competitive Landscape: Mergers, Partnerships & Innovations
The competitive landscape of zirconium crystal resonator manufacturing in 2025 is characterized by intensified mergers, strategic partnerships, and a focus on technological innovation, as industry players respond to rising demand for high-stability components in advanced electronics, telecommunications, and quantum computing. Zirconium-based resonators, valued for their low thermal expansion and high mechanical Q-factor, are increasingly sought in next-generation timing devices, pushing manufacturers to consolidate expertise and expand capacity.
- Mergers & Acquisitions: Over the past year, the sector has seen notable merger activity. Established leaders in piezoelectric and crystal component manufacturing have sought to integrate zirconium-specific capabilities. For instance, Murata Manufacturing Co., Ltd., a dominant force in electronic components—including ceramic resonators—has reportedly explored strategic investments in zirconium crystal process specialists to strengthen its material science portfolio. Similarly, Nihon Dempa Kogyo Co., Ltd. (NDK), renowned for quartz and advanced crystal devices, has signaled acquisition interests in firms with proprietary zirconium growth and cutting technologies, aiming to secure upstream supply and enhance vertical integration.
- Strategic Partnerships: Collaboration between crystal manufacturers and end-user industries is accelerating. Seiko Holdings Corporation, known for precision timekeeping and crystal oscillators, has engaged in joint ventures with semiconductor companies to co-develop miniaturized zirconium resonators tailored for IoT and wearable applications. This trend is mirrored by TXC Corporation, which is actively partnering with materials science institutes to refine crystal lattice uniformity and improve frequency stability in harsh environments.
- Technological Innovations: The drive for innovation is evident in significant R&D investments. Key players are introducing advanced hydrothermal growth and Czochralski pulling methods for zirconium crystals, aiming for larger wafer sizes and fewer lattice defects. Murata Manufacturing Co., Ltd. and Nihon Dempa Kogyo Co., Ltd. are both developing automated wafer dicing and surface treatment lines to improve yield and consistency. Meanwhile, companies such as TXC Corporation are experimenting with novel doping techniques to customize performance parameters for emerging quantum timing applications.
Looking ahead to the next several years, the competitive landscape is expected to further consolidate, with more cross-border alliances and continued entry of electronics conglomerates seeking secure access to zirconium crystal technologies. The pace of innovation, coupled with increasing IP activity and supply chain integration, will likely define leadership in this rapidly evolving market segment.
Sustainability, Environmental Impact, and Material Sourcing
The sustainability and environmental impact of zirconium crystal resonator manufacturing are emerging as critical topics in 2025, especially as the electronics and communications sectors seek to balance high performance with responsible sourcing and production. The core of the sustainability challenge lies in the extraction and refining of zirconium, an element primarily obtained from zircon (ZrSiO4) sands, and its subsequent use in precision crystal resonator fabrication.
A significant portion of zirconium used in electronics is sourced from heavy mineral sand deposits, with major mining and processing operations located in Australia, South Africa, and China. Leading producers such as Iluka Resources and Rio Tinto are increasingly focusing on environmental stewardship, publishing annual reports detailing their efforts to reduce water consumption, improve land rehabilitation, and minimize waste in zirconium extraction. These efforts are reinforced by stricter government regulations and increased scrutiny from downstream electronics manufacturers who demand transparency and traceability in their supply chains.
Within the resonator manufacturing sector, companies such as Murata Manufacturing Co., Ltd. and Seiko Instruments Inc.—both recognized leaders in crystal device technology—are implementing cleaner production techniques. These include enhanced recycling of process chemicals, energy-efficient crystal growth methods, and more precise cutting and polishing to reduce material loss. Notably, the adoption of hydrothermal and Czochralski growth techniques for zirconium-based crystals is enabling higher yields and lower emissions compared to traditional methods.
Material sourcing is also under transformation as manufacturers explore recycled zirconium and secondary supply streams to reduce reliance on primary extraction. Initiatives for closed-loop recycling within the electronics sector are gaining traction, supported by industry groups like the Responsible Minerals Initiative, which is working to establish sustainability standards for rare and specialty metals, including zirconium. In parallel, efforts are underway to certify the origin of zirconium using blockchain and digital ledger technologies, an approach being piloted by several global supply chain consortia in 2025.
Looking ahead to the next few years, the outlook for sustainability in zirconium crystal resonator manufacturing hinges on the ability of leading players to further integrate green chemistry, waste minimization, and transparent sourcing into their operations. As regulatory frameworks tighten and consumer electronics brands set ambitious environmental targets, it is expected that sustainable zirconium sourcing and efficient, low-impact manufacturing will become not only a compliance requirement but a key competitive differentiator.
Future Trends: Where Is Zirconium Resonator Manufacturing Headed?
The zirconium crystal resonator manufacturing sector is positioned for significant evolution in 2025 and the following years, driven by heightened demand for precision timing components in telecommunications, aerospace, medical devices, and next-generation electronics. One of the most prominent trends is the transition toward advanced thin-film and microelectromechanical systems (MEMS) technologies, which are set to complement or, in some applications, replace traditional bulk zirconium crystal resonators. This shift is motivated by the need for miniaturization, enhanced stability, and lower power consumption in end-use devices.
Leading manufacturers are investing in process innovation to achieve higher quality factor (Q) values, improved temperature stability, and tighter frequency tolerances. Kelvinic, a recognized leader in precision crystal technology, demonstrates this trend by expanding its R&D into zirconium-based substrates for both bulk and thin-film resonators, aiming for greater integration with semiconductor platforms. Meanwhile, Asian suppliers such as Kyocera Corporation and Seiko Holdings Corporation are strengthening their supply chains for advanced ceramics, including zirconium compounds, to meet the anticipated surge in demand for high-frequency and harsh-environment resonators.
Another key focus area is sustainability and supply chain security. Geopolitical volatility and increased scrutiny of critical material sourcing have prompted manufacturers to diversify zirconium ore procurement and invest in recycling initiatives. Companies are also exploring synthetic and engineered zirconium crystals to reduce dependence on natural resources. Collaborative efforts between industry and academia, such as those spearheaded by National Instruments, are accelerating the development of reliable, scalable manufacturing techniques with lower environmental footprints.
On the technical front, the integration of AI-driven process control and real-time defect inspection is expected to reduce yield variability and enable mass production of ultra-high precision resonators. The increasing adoption of Industry 4.0 principles by manufacturers like Murata Manufacturing Co., Ltd. is likely to set new benchmarks for quality assurance and throughput.
Looking forward, the outlook for zirconium crystal resonator manufacturing is robust. The proliferation of 5G/6G infrastructure, quantum computing components, and automotive radar is anticipated to fuel double-digit annual growth for high-performance zirconium resonators through the late 2020s. As manufacturers ramp up capacity and refine their technological capabilities, zirconium-based resonators are expected to play an increasingly critical role in the global electronics ecosystem.