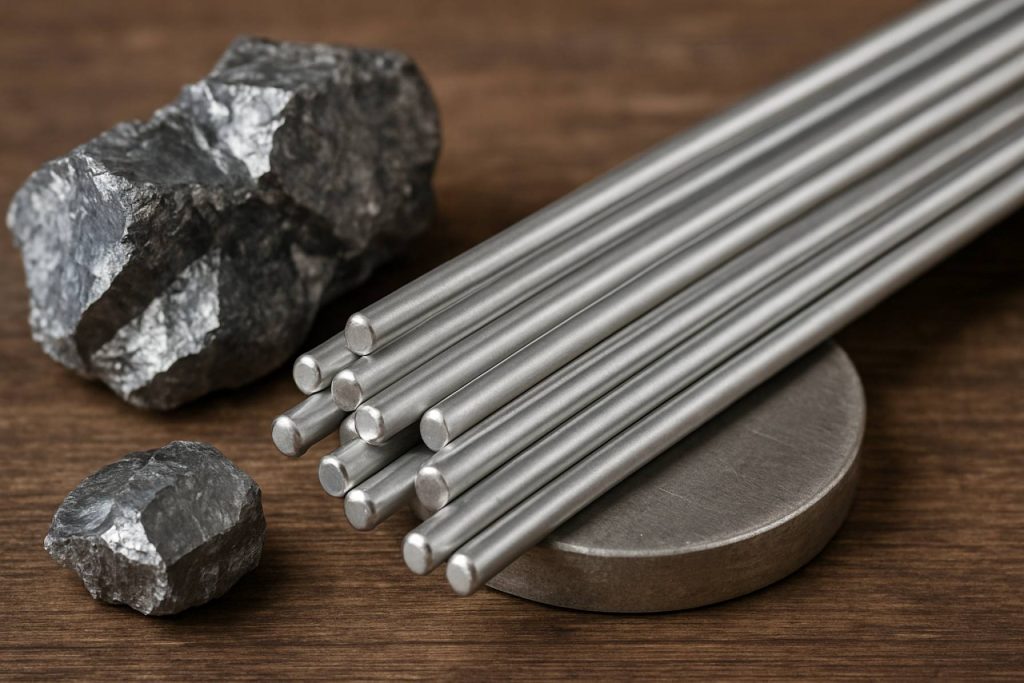
Table of Contents
- Executive Summary: 2025 Outlook & Key Findings
- Market Size, Growth Projections, and Revenue Forecasts (2025–2030)
- Core Applications: Aerospace, Energy, Electronics & Beyond
- Technology Innovations: New Alloy Formulations and Process Advancements
- Key Manufacturers and Industry Players (with Official Sources)
- Supply Chain & Raw Material Trends: Zirconium and Gallium Sourcing
- Competitive Landscape: Global and Regional Analysis
- Challenges: Technical Barriers, Standards, and Regulatory Environment
- Emerging Opportunities: Niche Markets and Future Use Cases
- Strategic Recommendations & Future Outlook for Investors and Engineers
- Sources & References
Executive Summary: 2025 Outlook & Key Findings
The engineering landscape for zirconium-gallium (Zr-Ga) brazing alloys is poised for notable advancements in 2025, driven by escalating demands in high-temperature and corrosive environment applications. These alloys are recognized for their superior wettability, high-temperature stability, and resistance to oxidation, making them pivotal in sectors such as aerospace, nuclear energy, and advanced electronics packaging. The global market is experiencing increased R&D investment and capacity expansion, with leading alloy manufacturers and suppliers reporting heightened interest from component fabricators seeking next-generation joining solutions.
Recent developments reflect a shift towards optimizing Zr-Ga alloy compositions for improved flow characteristics and enhanced compatibility with refractory and dissimilar substrates. Companies such as Plansee Group and H.C. Starck Solutions have expanded their technical data offerings and are collaborating with R&D teams to customize alloy formulations for critical assemblies, particularly in thermal management and vacuum applications. Additionally, Kennametal and Materion Corporation are reported to be developing proprietary Zr-Ga-based brazing materials targeting improved joint reliability and longevity at service temperatures exceeding 1000°C.
2025 is expected to see further integration of Zr-Ga brazing alloys in nuclear reactor fuel assembly and superalloy turbine blade manufacturing. Industry initiatives focus on process automation, reproducibility of joint quality, and compliance with evolving international standards for nuclear and aerospace components. In parallel, supply chain resilience is being reinforced; alloy producers are securing stable sources of high-purity zirconium and gallium, as well as investing in recycling and recovery technologies to address sustainability and cost concerns.
Looking forward, the outlook for Zr-Ga brazing alloys engineering remains robust. Industry participants anticipate moderate to strong growth, particularly in Asia-Pacific and North America, where government-backed infrastructure and technology programs are accelerating advanced material adoption. Collaborative efforts among alloy producers, end-users, and research institutions are expected to yield new standards and best practices, supporting broader industry acceptance. The convergence of material innovation, digital manufacturing, and stringent performance requirements positions Zr-Ga brazing alloys as a critical enabler in the next phase of engineering solutions for extreme environments.
Market Size, Growth Projections, and Revenue Forecasts (2025–2030)
The global market for zirconium-gallium brazing alloys is entering a period of measured expansion, propelled by the increasing adoption of advanced materials in aerospace, electronics, and energy sectors. For 2025, industry insiders project steady demand growth, underpinned by the alloys’ exceptional high-temperature performance, corrosion resistance, and compatibility with difficult-to-join ceramics and refractory metals. This trend is particularly evident in the manufacturing of next-generation electronics and specialized aerospace components, where reliability and material integrity are paramount.
While the zirconium-gallium brazing alloy segment remains a niche within the broader brazing alloys market, its value is expected to rise as more manufacturers seek tailored solutions for demanding applications. According to major producers such as H.C. Starck and Materion Corporation, inquiries and custom orders for zirconium- and gallium-based alloys have increased over the past two years, signaling a shift from research-scale utilization toward limited but growing industrial-scale production. These companies report that aerospace and semiconductor customers are driving much of this demand, especially for alloys engineered to join dissimilar materials under harsh service conditions.
Looking toward 2030, industry consensus suggests a compound annual growth rate (CAGR) for zirconium-gallium brazing alloys in the mid-single-digit range, outpacing the broader brazing materials market. This is attributed to both technological advancements in alloy formulation and processing, as well as the expanding range of high-performance applications. Revenue forecasts for 2025–2030 are difficult to disaggregate due to the segment’s small absolute size and the custom nature of many orders; however, established suppliers such as Plansee Group and Tanaka Precious Metals are investing in capacity upgrades and R&D efforts aimed at both improving product purity and broadening alloy design options.
In summary, while the zirconium-gallium brazing alloys market will continue to represent a specialized slice of the global advanced joining materials sector, its revenue base is expected to expand through 2030, fueled by the needs of high-tech industries and ongoing innovations by leading material science companies. Strategic investments, coupled with evolving end-user requirements, will likely ensure sustained, albeit moderate, market growth over the forecast period.
Core Applications: Aerospace, Energy, Electronics & Beyond
Zirconium-gallium brazing alloys are expected to play an increasingly pivotal role in high-performance joining technologies across multiple industries in 2025 and the coming years. Their unique combination of high-temperature stability, corrosion resistance, and compatibility with refractory and reactive metals positions them as critical materials for advanced engineering applications.
In the aerospace sector, the demand for lightweight, heat-resistant assemblies continues to rise, driven by next-generation propulsion systems and hypersonic vehicle development. Zirconium-gallium brazing alloys are being utilized to join components made from titanium, zirconium, and various nickel-based superalloys, where traditional brazes may fail due to interfacial reactions or insufficient high-temperature strength. Aerospace manufacturers, such as Honeywell and GE Aerospace, are reportedly exploring advanced brazing materials for turbine engines and structural assemblies, where service temperatures often exceed 1000°C.
The energy sector—especially in nuclear and emerging fusion technologies—relies on zirconium-based alloys for cladding and structural components because of their low neutron absorption and excellent corrosion resistance. Zirconium-gallium brazing alloys provide a compatible joining solution for these demanding applications, facilitating the assembly of fuel rods and heat exchangers. Industry actors such as Westinghouse Electric Company and Framatome are actively investing in the development and qualification of advanced joining techniques to support next-generation reactors and high-temperature gas-cooled systems.
In electronics and microelectronics, the miniaturization and reliability requirements for packaging and interconnects have prompted the adoption of novel brazing materials. Zirconium-gallium alloys, with their low vapor pressure and controlled reactivity, enable hermetic sealing and robust connections in sensors, power modules, and vacuum devices. Companies like Heraeus and Alfa Aesar supply high-purity zirconium and gallium products, supporting R&D and small-scale production in this sector.
Looking ahead, the outlook for zirconium-gallium brazing alloys includes expansion into fields such as medical device manufacturing, where biocompatibility and sterilization resistance are valued. Ongoing collaboration between alloy producers, end-users, and research institutions is likely to yield further composition optimization and process enhancements, solidifying the role of these alloys in critical applications through 2025 and beyond.
Technology Innovations: New Alloy Formulations and Process Advancements
The engineering of zirconium-gallium (Zr-Ga) brazing alloys is experiencing significant technological advancements as industries seek materials with superior performance in demanding environments, particularly within the aerospace, electronics, and nuclear sectors. In 2025, research and development efforts are focusing on new alloy formulations that optimize the melting range, wettability, and corrosion resistance of Zr-Ga alloys. These innovations are critical as traditional silver-based and nickel-based brazing filler metals face increasing limitations in high-temperature and corrosive settings.
Leading manufacturers are actively refining Zr-Ga alloy compositions to achieve improved mechanical strength and compatibility with advanced ceramics and refractory metals. For example, the incorporation of minor alloying elements such as tin, indium, or nickel is under investigation to further tailor the phase behavior and diffusion characteristics of Zr-Ga systems. These incremental modifications are intended to deliver enhanced joint reliability for vacuum and inert gas applications, where minimizing interfacial reactions and porosity is paramount. Companies such as PLANSEE Group and H.C. Starck are known for their ongoing materials engineering efforts in this domain.
Process advancements are equally notable. The adoption of precision-controlled atmosphere furnaces and induction heating technologies is enabling more consistent brazing cycles and tighter control over joint microstructure. Automation and digital process monitoring are becoming standard, allowing engineers to optimize brazing parameters in real time. In 2025 and beyond, the implementation of Industry 4.0 principles—such as digital twin modeling and predictive maintenance—aims to boost productivity and quality assurance throughout the brazing workflow. Suppliers like Vacuum Furnace Engineering are making strides in providing advanced thermal processing equipment tailored for the unique requirements of Zr-Ga alloys.
Outlook for the next several years suggests that Zr-Ga brazing alloys will see increased adoption in next-generation electronic packages, fuel cell components, and high-temperature heat exchangers. The emerging shift toward hydrogen economy infrastructure and fusion power systems is expected to drive further demand for robust, low-activation brazing solutions—an area where Zr-Ga alloys excel due to their low neutron absorption cross-section and chemical stability. As a result, close collaboration between alloy producers, equipment manufacturers, and end-users will remain vital to accelerate innovation and standardization in this evolving field.
Key Manufacturers and Industry Players (with Official Sources)
The global landscape for zirconium-gallium brazing alloys is shaped by a select group of manufacturers and industry stakeholders, each playing a pivotal role in advancing engineering applications, quality standards, and supply stability. As of 2025, the focus remains on aerospace, electronics, and high-performance industrial sectors, where these alloys are prized for their unique joining characteristics, especially in demanding, high-temperature environments.
- Heraeus Group: As a well-established global manufacturer of advanced materials and specialty metals, Heraeus Group is recognized for its expertise in customized brazing alloys, including zirconium and gallium-containing compositions. The company supports the electronics and aerospace industries with tailored solutions, leveraging its robust R&D infrastructure to address evolving performance criteria in 2025.
- Materion Corporation: With a strong presence in engineered materials, Materion Corporation specializes in high-purity alloys and brazing products, including those utilizing reactive and refractory elements. Their development of zirconium-gallium brazing alloys is driven by stringent quality controls and application-specific engineering, particularly for joining dissimilar materials in advanced assemblies.
- Umicore: Umicore is a leader in the production of high-tech metal solutions and braze materials, supplying a range of sectors that require precise alloy performance. The company’s commitment to sustainability and innovation positions it as a key player in the ongoing refinement of zirconium and gallium-based brazing alloys.
- Johnson Matthey: As a global supplier of specialist materials, Johnson Matthey provides brazing alloys engineered for reliability in extreme environments. Their product portfolio includes bespoke zirconium-gallium compositions, developed in collaboration with customers in the electronics and aerospace fields.
- TANAKA Precious Metals: TANAKA Precious Metals is known for its advanced precious and specialty metal solutions, actively developing and supplying high-purity brazing alloys that incorporate zirconium and gallium for niche, high-reliability applications.
Looking toward the next few years, these companies are expected to deepen collaborations with OEMs and research institutes to refine alloy design and performance. The push for miniaturization in electronics and reliability in next-generation energy systems drives ongoing investment in R&D, process optimization, and supply chain resilience. As industry standards evolve, direct engagement with these key players will be essential for manufacturers seeking to adopt or advance zirconium-gallium brazing alloy technologies.
Supply Chain & Raw Material Trends: Zirconium and Gallium Sourcing
The global supply chain for zirconium and gallium—critical constituents in zirconium-gallium brazing alloys—faces a dynamic landscape entering 2025. The majority of zirconium is sourced from mineral sands, primarily as zircon (ZrSiO4), with major producers including Iluka Resources (Australia), Rio Tinto (Australia/Global), and The Chemours Company (USA). These companies dominate supply chains through mining operations in Australia, South Africa, and the United States, collectively contributing to a stable but tightly balanced market.
For gallium, sourcing is more complex due to its byproduct status in aluminum and zinc refining. Major gallium producers are concentrated in China, which supplies over 90% of the world’s refined gallium, with companies like Aluminum Corporation of China Limited (CHALCO) and Huludao Zinc Industry playing significant roles. European and North American gallium production remains limited, although recent policy initiatives are stimulating investment in secondary recovery and recycling to reduce dependency on Chinese exports.
Supply chain risks for both elements have grown more pronounced due to geopolitical developments and increased demand from the semiconductor, aerospace, and energy sectors. In 2024, export restrictions imposed by China on gallium compounds, as reported by industry sources, have heightened concerns about availability and price volatility for gallium-based alloys outside Asia. Meanwhile, zirconium supply has been affected by logistical disruptions and environmental regulations impacting mineral sands mining, though global output has otherwise remained resilient due to diversified sources.
Leading alloy manufacturers such as Umicore (Belgium) and Plansee (Austria) are actively pursuing more secure raw material streams and developing recycling-based supply chains. These efforts are mirrored by end users in the electronics and aerospace industries, who are seeking assurances of supply chain transparency and sustainability.
Looking forward into 2025 and beyond, the outlook for zirconium-gallium brazing alloys hinges on continued supply chain adaptation. With ongoing investment in zirconium extraction technologies and recycling infrastructure for gallium, market participants are expected to partially offset external risks. Nevertheless, heightened scrutiny of sourcing practices and persistent geopolitical pressures suggest that alloy producers will continue to prioritize supply chain resilience and diversification in the years ahead.
Competitive Landscape: Global and Regional Analysis
The competitive landscape for zirconium-gallium brazing alloys engineering in 2025 is characterized by a combination of established specialty alloy manufacturers and emerging regional producers, each leveraging unique technological capabilities and supply chain networks. The sector remains relatively niche due to the specialized nature of zirconium-gallium alloys, which are primarily utilized in high-temperature, corrosion-resistant joining applications across aerospace, nuclear, and advanced electronics industries.
Globally, leading producers such as H.C. Starck Solutions and Plansee Group continue to dominate the market, owing to their robust R&D infrastructure and vertically integrated supply chains. These companies focus on developing customized alloy compositions to meet the stringent requirements of next-generation fusion reactors and high-performance turbine components. Their competitive edge is reinforced by long-term partnerships with aerospace primes and nuclear technology providers.
In the Asia-Pacific region, countries like China, Japan, and South Korea are increasing their investments in advanced materials engineering. Companies such as Toyo Metal have expanded their zirconium-gallium alloy offerings, capitalizing on the region’s growing electronics and energy sectors. Chinese manufacturers are also scaling up production capacities, driven by government initiatives to localize critical material supply for domestic aerospace and defense programs.
Europe remains a key hub for R&D-focused alloy development. Organizations in Germany and France are collaborating with research institutes to optimize alloy microstructures for improved thermal stability and oxidation resistance. This trend is expected to intensify through 2025, as the EU’s emphasis on supply chain resilience and technological sovereignty spurs additional funding for advanced joining materials.
The North American market is marked by the presence of established players and a growing number of specialized SMEs focused on custom alloy solutions for space and nuclear applications. For example, Praxair Surface Technologies (now part of Linde) continues to invest in powder metallurgy and coating technologies relevant to zirconium-gallium brazing, strengthening its competitive position.
Looking ahead, the competitive landscape is likely to see further consolidation, with strategic alliances and joint ventures aimed at securing raw material sources and developing proprietary alloy formulations. Environmental regulations and the push for sustainable manufacturing practices will also influence competitive dynamics, prompting firms to innovate cleaner production processes and recycling initiatives for rare metals.
Challenges: Technical Barriers, Standards, and Regulatory Environment
The engineering of zirconium-gallium brazing alloys faces notable challenges in 2025, shaped by technical barriers, evolving standards, and a complex regulatory environment. These alloys, prized for their high-temperature stability and corrosion resistance, are increasingly sought after in demanding sectors such as nuclear power, aerospace, and advanced electronics. However, widespread adoption is hindered by several intertwined factors.
A primary technical barrier lies in the careful control of alloy composition and microstructure. Zirconium’s high reactivity, particularly at elevated brazing temperatures, demands stringent atmospheric control during manufacturing and joining processes. The presence of impurities or oxygen can lead to embrittlement or the formation of undesirable intermetallics, compromising joint reliability. Furthermore, the precise melting range required for zirconium-gallium alloys necessitates advanced process control to avoid partial melting or incomplete wetting of substrates, which remains a significant engineering hurdle for many manufacturers.
On the standards front, industry-wide specifications for zirconium-gallium brazing alloys are still emerging. While organizations such as the ASM International and International Organization for Standardization provide general frameworks for brazing material performance and testing, dedicated standards tailored to zirconium-gallium compositions are limited. This lack of harmonized standards complicates material qualification, especially in regulated sectors where traceability, repeatability, and certification are paramount. Efforts are underway to develop more specific guidelines, but progress is incremental.
The regulatory environment adds another layer of complexity. In the nuclear industry, for example, zirconium-based alloys must adhere to rigorous controls on radiopurity and corrosion resistance, governed by bodies like the U.S. Nuclear Regulatory Commission. Aerospace applications face their own certification challenges under agencies such as the Federal Aviation Administration, demanding exhaustive documentation of material properties and long-term performance. The introduction of gallium as an alloying element triggers additional scrutiny, as its diffusion characteristics and potential effects on neighboring materials (such as aluminum or copper) are still being studied.
Looking forward to the coming years, the outlook for overcoming these challenges is cautiously optimistic. Collaborative initiatives between alloy producers, users, and industry bodies aim to refine production protocols and develop tailored standards. Companies like H.C. Starck Solutions and Plansee SE are investing in research and pilot-scale manufacturing to address process consistency and supply chain reliability. As regulatory frameworks adapt and more application-specific data becomes available, the pathway to broader acceptance and deployment of zirconium-gallium brazing alloys is expected to gradually open, though technical and compliance hurdles will persist in the near term.
Emerging Opportunities: Niche Markets and Future Use Cases
As the global demand for advanced joining technologies intensifies, zirconium-gallium brazing alloys are emerging as a focal point for innovation in several niche markets. Traditionally valued for their high-temperature stability, corrosion resistance, and compatibility with refractory and reactive metals, these alloys are experiencing renewed interest driven by developments in aerospace, nuclear, and electronics engineering.
In 2025, the aerospace sector continues to be a prominent adopter, with research and pilot projects focusing on the use of zirconium-gallium alloys for joining titanium and nickel-based superalloys in turbine engines and hypersonic vehicle components. The alloys’ ability to form strong, diffusion-resistant joints at elevated temperatures makes them attractive for these applications, as highlighted by manufacturers such as H.C. Starck Solutions and Plansee, both of whom are actively developing customized brazing materials for demanding environments.
The nuclear industry represents another key opportunity, particularly in the fabrication and repair of zirconium alloy fuel cladding and structural assemblies in next-generation reactors. Zirconium-gallium brazing alloys offer a solution for joining zirconium-based components while minimizing the risk of radioactive contamination and ensuring long-term stability under irradiation. Suppliers like ATI and Sandvik are expanding R&D efforts to support the evolving requirements of nuclear infrastructure modernization.
Emerging electronic and photonic device markets are also presenting novel use cases. The alloys’ favorable wetting behavior and low reactivity with sensitive substrates enable microjoining applications in power electronics, vacuum devices, and advanced sensor modules. Enhanced process control and miniaturized assembly offered by companies such as Umicore are expected to facilitate the adoption of zirconium-gallium alloys in hermetic sealing and MEMS packaging, especially where conventional solders fail due to thermal or chemical constraints.
- Growing interest in hydrogen energy systems is spurring investigations into zirconium-gallium alloys for joining high-purity metal membranes and reactors, a trend supported by suppliers like Materion.
- Medical device manufacturers are exploring these alloys for biocompatible joining in implantable devices and surgical tools, leveraging their corrosion resistance and mechanical reliability.
Looking ahead, advances in powder metallurgy and additive manufacturing are poised to unlock further customization of zirconium-gallium brazing alloys. This will enable highly tailored compositions for specific thermal, chemical, and mechanical demands, accelerating their penetration into high-value niche markets. As industrial qualification processes and supply chain maturity improve, the sector anticipates steady growth in adoption through 2025 and beyond.
Strategic Recommendations & Future Outlook for Investors and Engineers
As zirconium-gallium (Zr-Ga) brazing alloys transition from niche applications to broader adoption in high-performance sectors, investors and engineers should consider several strategic actions and anticipated trends for 2025 and beyond. The unique properties of Zr-Ga alloys—such as excellent high-temperature stability, corrosion resistance, and compatibility with advanced ceramics and refractory metals—poise them as critical materials in next-generation aerospace, nuclear, and electronics engineering.
Strategically, stakeholders should monitor ongoing alliances and technology transfers between alloy producers, end-users, and research institutions. Companies such as H.C. Starck Solutions and Plansee are expanding their advanced materials portfolios, with increasing attention to Zr-based brazing products for demanding vacuum and high-temperature processes. This trend is driven by the miniaturization of electronic devices and the need for superior joining materials in hermetic packaging and sensor technologies.
For engineers, the immediate focus should be on optimizing process parameters for Zr-Ga alloys in both vacuum and inert gas environments. Collaboration with alloy suppliers to tailor composition—particularly controlling gallium content for wetting behavior and joint strength—is advised. Early 2025 has seen several pilot projects in Europe and Asia where Zr-Ga brazes are being evaluated for turbine blade repair, advanced battery housings, and superconducting device assemblies.
Investors should watch for regional capacity expansions and vertical integration moves. For example, Toyotsu Material and Mitsubishi Materials are reportedly enhancing their capabilities in reactive and refractory alloy production, including Zr-Ga systems, in response to tightening quality requirements from aerospace and fusion energy sectors. This indicates a robust demand outlook and the potential for long-term contracts.
Looking forward, the market will likely see increased standardization efforts, especially as international bodies and industry groups work to define specifications for Zr-Ga alloy compositions and performance metrics. This will aid in reducing qualification lead times and facilitate inter-company collaboration. Continued advances in powder metallurgy and additive manufacturing will further enable the customization of Zr-Ga brazing foils and pastes, opening opportunities for new applications in quantum computing hardware and next-gen photonics.
- Engineers should engage early with suppliers to co-develop application-specific Zr-Ga alloys.
- Investors should prioritize companies investing in production scalability and R&D for Zr-Ga alloys.
- Both groups should track regulatory and industry standardization activities to anticipate qualification hurdles and market timing.
In summary, the outlook for zirconium-gallium brazing alloys is positive, driven by technological advancements and expanding end-use requirements. Strategic collaboration and proactive investment in R&D and manufacturing capacity will be crucial to capitalizing on this growth trajectory in the coming years.
Sources & References
- H.C. Starck Solutions
- Kennametal
- Materion Corporation
- Tanaka Precious Metals
- Honeywell
- GE Aerospace
- Framatome
- Heraeus
- Alfa Aesar
- Vacuum Furnace Engineering
- Umicore
- Johnson Matthey
- Rio Tinto
- Aluminum Corporation of China Limited (CHALCO)
- Praxair Surface Technologies
- Linde
- ASM International
- International Organization for Standardization
- Sandvik