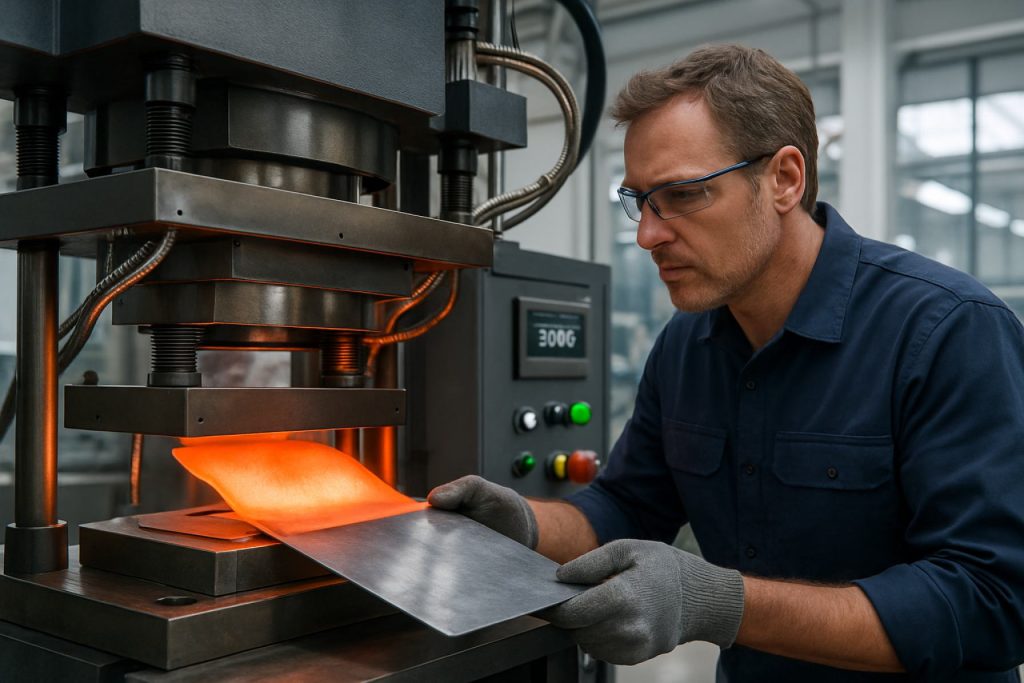
Het ontsluiten van de kracht van warmvormen: hoe magnesiumlegeringen de lichte techniek transformeren. Ontdek de wetenschap, technologie en toekomstige impact van dit baanbrekende proces. (2025)
- Inleiding tot warmvormen en magnesiumlegeringen
- Materiaal eigenschappen: Waarom magnesiumlegeringen?
- Fundamentals van het warmvormproces
- Kernapparatuur en technologische innovaties
- Vergelijkende analyse: Warmvormen vs. koud- en heetvormen
- Industrieel gebruik: Automotive, lucht- en ruimtevaart en verder
- Uitdagingen en oplossingen in warmvormen van magnesiumlegeringen
- Duurzaamheid en milieu-impact
- Markttrends en groeivoorspellingen (2024–2030)
- Toekomstige vooruitzichten: Onderzoeksrichtingen en opkomende kansen
- Bronnen & Referenties
Inleiding tot warmvormen en magnesiumlegeringen
Warmvormen van magnesiumlegeringen is een geavanceerd metaalbewerkingsproces dat de laatste jaren aanzienlijke aandacht heeft gekregen, vooral nu industrieën op zoek zijn naar lichte, hoogwaardige materialen voor toepassingen in de auto-, lucht- en ruimtevaart en elektronica. Magnesium, als het lichtste bouwmetaal, biedt een unieke combinatie van lage dichtheid en hoge specifieke sterkte, waardoor het een aantrekkelijke alternatieve is voor aluminium en staal. Echter, de hexagonaal dichte (HCP) kristalstructuur beperkt de vervormbaarheid bij kamertemperatuur, wat uitdagingen oplevert voor conventionele koudvormtechnieken. Warmvormen, dat doorgaans bij temperaturen tussen 200°C en 400°C wordt uitgevoerd, pakt deze beperkingen aan door de vervormbaarheid en vormbaarheid van magnesiumlegeringen te verbeteren, waardoor de productie van complexe vormen mogelijk wordt met een verlaagd risico op barsten.
Met ingang van 2025 blijft de wereldwijde druk voor het verlichten van voertuigen en het verbeteren van brandstofefficiëntie de research en industriële adoptie van warmvormprocessen voor magnesiumlegeringen stimuleren. De automotive sector, in het bijzonder, benut deze vooruitgangen om de massa van voertuigen te verminderen en te voldoen aan strenge emissienormen. Vooruitstrevende autofabrikanten en leveranciers werken samen met onderzoeksinstellingen om de warmvormparameters en legeringsamenstellingen te optimaliseren, met als doel de vervaardigbaarheid, mechanische prestaties en kosteneffectiviteit in balans te brengen. Bijvoorbeeld, de International Magnesium Association (IMA), een belangrijke brancheorganisatie, bevordert actief de ontwikkeling en toepassing van magnesiumtechnologieën wereldwijd en ondersteunt initiatieven die de warmvormtechnieken bevorderen.
Recente gegevens van industrie- en academische bronnen geven aan dat de adoptie van warmvormen voor magnesiumlegeringen gestaag toeneemt, met proefproductielijnen en demonstratieprojecten aan de gang in Azië, Europa en Noord-Amerika. Opmerkelijk is dat organisaties zoals de Minerals, Metals & Materials Society (TMS) en het National Institute of Standards and Technology (NIST) de kennisuitwisseling en standaardisatie-inspanningen faciliteren, die cruciaal zijn voor bredere commercialisering. Deze organisaties bieden technische middelen, organiseren conferenties en ondersteunen gezamenlijke onderzoek om uitdagingen aan te pakken zoals matrijsverslijt, procescontrole en legeringsontwikkeling.
Vooruitkijkend naar de komende jaren lijkt de vooruitzichten voor het warmvormen van magnesiumlegeringen positief. Voortdurende vooruitgangen in procesimulatie, gereedschapsontwerp en legeringstechniek zullen naar verwachting de vormbaarheid verder verbeteren en de productiekosten verlagen. Aangezien duurzaamheid en energie-efficiëntie steeds centraler worden in productie strategieën, zal de rol van magnesiumlegeringen—mogelijk gemaakt door warmvormen—waarschijnlijk uitbreiden naar meerdere sectoren. Voortdurende steun van brancheorganisaties en overheidsinstanties zal essentieel zijn voor het overwinnen van technische barrières en het versnellen van de integratie van deze lichte materialen in de reguliere productie.
Materiaal eigenschappen: Waarom magnesiumlegeringen?
Magnesiumlegeringen hebben de laatste jaren aanzienlijke aandacht gekregen, vooral vanwege hun toepassing in warmvormprocessen. De belangrijkste drijfveer achter deze belangstelling is de status van magnesium als het lichtste bouwmetaal, met een dichtheid die ongeveer twee derde is van die van aluminium en een kwart van die van staal. Deze lage dichtheid, gecombineerd met een hoge specifieke sterkte, maakt magnesiumlegeringen zeer aantrekkelijk voor sectoren zoals de automotive en lucht- en ruimtevaart, waar gewichtsvermindering direct gekoppeld is aan verbeterde brandstofefficiëntie en verlaagde emissies.
Ondanks deze voordelen is de brede acceptatie van magnesiumlegeringen historisch beperkt geweest door hun slechte vormbaarheid bij kamertemperatuur. Deze beperking ontstaat door hun hexagonaal dichte (HCP) kristalstructuur, die het aantal beschikbare schuifsystemen voor plastische vervorming beperkt. Als gevolg hiervan vertonen magnesiumlegeringen de neiging om bros gedrag en beperkte vervormbaarheid onder koudvormomstandigheden te vertonen.
Warmvormen, dat doorgaans in een temperatuurbereik van 200–350°C wordt uitgevoerd, is opgekomen als een oplossing voor deze uitdagingen. Bij verhoogde temperaturen worden aanvullende schuifsystemen actief in de HCP-structuur, waardoor de vervormbaarheid significant toeneemt en het risico op barsten afneemt. Recente studies en industriële proeven hebben aangetoond dat warmvormen de rek bij breuk van veelvoorkomende magnesiumlegeringen zoals AZ31 en ZK60 met enkele keren kan verhogen in vergelijking met kamertemperatuurvormen. Bijvoorbeeld, rekwaarden kunnen stijgen van minder dan 10% bij kamertemperatuur tot meer dan 30% bij optimale warmvormtemperaturen.
De automotive sector in het bijzonder versnelt de adoptie van warmgevormde magnesiumcomponenten. Belangrijke autofabrikanten en leveranciers werken samen met onderzoeksinstellingen om legeringsamenstellingen en vormparameters te optimaliseren. Organisaties zoals de International Magnesium Association (IMA) en de Minerals, Metals & Materials Society (TMS) ondersteunen actief onderzoek, standaardisatie en verspreiding van best practices op dit gebied. Deze inspanningen worden verwacht nieuwe magnesiumlegeringen met verbeterde vormbaarheid en corrosie weerbaarheid op te leveren, specifiek afgestemd op warmvormtoepassingen.
Vooruitkijkend naar 2025 en verder, is de vooruitzichten voor warmvormen van magnesiumlegeringen hoopvol. Voortdurend onderzoek richt zich op het verder verbeteren van de mechanische eigenschappen van magnesiumlegeringen door middel van legering en thermomechanische verwerking. Bovendien stellen vooruitgangen in simulatie en procescontrole steeds nauwkeurigere voorspellingen en optimalisaties van warmvormoperaties in staat. Aangezien duurzaamheid en gewichtsreductie topprioriteiten blijven voor fabrikanten, staan magnesiumlegeringen—mogelijk gemaakt door warmvormen—op het punt om een steeds belangrijkere rol te spelen in de transport en consumentproducten van de volgende generatie.
Fundamentals van het warmvormproces
Warmvormen van magnesiumlegeringen is een kritisch productieproces dat de inherente beperkingen van de lage vervormbaarheid van magnesium bij kamertemperatuur aanpakt. Magnesiumlegeringen, gewaardeerd om hun lage dichtheid en hoge specifieke sterkte, worden steeds meer gezocht in de automotive, lucht- en ruimtevaart en elektronica industrieën voor lichtere toepassingen. Echter, hun hexagonaal dichte (HCP) kristalstructuur beperkt de schuifsystemen bij omgevingsomstandigheden, wat resulteert in slechte vormbaarheid. Warmvormen—meestal uitgevoerd in het temperatuurbereik van 200°C tot 350°C—maakt de activatie van aanvullende schuifsystemen mogelijk, waardoor de vervormbaarheid significant verbetert en het risico op barsten tijdens vervorming vermindert.
In 2025 versnellen het onderzoek en de industriële adoptie van warmvormprocessen voor magnesiumlegeringen, gedreven door de behoefte aan duurzame mobiliteit en energie-efficiëntie. De fundamentele processen vereisen nauwkeurige controle van temperatuur, rek snelheid en vorm snelheid om de microstructurele evolutie en mechanische eigenschappen te optimaliseren. Recente studies, waaronder die ondersteund door het National Institute for Materials Science (NIMS) in Japan en de Minerals, Metals & Materials Society (TMS), hebben aangetoond dat warmvormen bij 250°C–300°C de rek bij breuk kan verhogen met tot 300% in vergelijking met kamertemperatuurvormingen, terwijl bovendien de vereiste vormkrachten met 30–50% verminderen.
Belangrijke procesvarianten zijn onder andere warm diep trekken, warm walsen en warm hydrovormen. Deze methoden worden verfijnd om complexe automotive componenten zoals deurpanelen, zittingframes en instrumentenbehuizingen te produceren. Bijvoorbeeld, de International Magnesium Association meldt dat verschillende vooraanstaande autofabrikanten pilotprojecten uitvoeren met warmgevormde magnesiumonderdelen in elektrische voertuigen van de volgende generatie, met als doel het gewicht van het voertuig met 10–20% te verminderen zonder in te boeten op veiligheid of prestaties.
Procesmodellering en simulatie zijn ook in ontwikkeling, waarbij organisaties zoals het National Institute of Standards and Technology (NIST) digitale tweelingen en voorspellende modellen ontwikkelen om warmvormparameters te optimaliseren en defecten te minimaliseren. Deze inspanningen worden ondersteund door de groeiende beschikbaarheid van hoogwaardige magnesiumlegeringen en verbeterde matrijsmaterialen die bestand zijn tegen verhoogde temperaturen en cyclische belasting.
Vooruitkijkend naar de komende jaren lijkt de vooruitzichten voor warmvormen van magnesiumlegeringen robuust. Voortdurende samenwerkingen tussen onderzoeksinstellingen, industriële consortia en normenorganen zullen naar verwachting nieuwe legeringsamenstellingen en procesinnovaties opleveren. De focus blijft liggen op het verbeteren van de vervormbaarheid, het verlagen van het energieverbruik en het opschalen van de productie voor massamarkttoepassingen, met name in transport en consumentenelektronica. Aangezien de druk op regelgeving voor lichte, low-emissie producten toeneemt, staat warmvormen op het punt om een mainstream productieoplossing voor magnesiumlegeringen te worden.
Kernapparatuur en technologische innovaties
Het warmvormen van magnesiumlegeringen is een snel voortschrijdend veld, gedreven door de behoefte aan lichte, hoogwaardige componenten in de automotive, lucht-, ruimtevaart en elektronica-industrieën. Met ingang van 2025 zijn er verschillende belangrijke apparatuur ontwikkelingen en technologische innovaties die het landschap van magnesiumlegeringsverwerking vormgeven.
Warmvormprocessen werken doorgaans in het temperatuurbereik van 200–350°C, waar magnesiumlegeringen verbeterde vervormbaarheid en verminderde vormkrachten vertonen in vergelijking met kamertemperatuur. Dit heeft geleid tot de aanpassing en verfijning van conventionele vormapparatuur, zoals hydraulische en servomechanische persen, om nauwkeurige temperatuurcontrole en snelle verwarmings-/koelingscycli mogelijk te maken. Vooruitstrevende apparatuur fabrikanten integreren geavanceerde thermomanagementsystemen, waaronder inductie- en weerstandverwarming, om een gelijkmatige temperatuurverdeling over matrijzen en werkstukken te waarborgen. Deze systemen zijn cruciaal om defecten zoals barsten te minimaliseren en om consistente mechanische eigenschappen in gevormde onderdelen te bereiken.
Een significante innovatie in 2025 is de implementatie van gesloten-lus procescontrolesystemen die gebruik maken van realtime feedback van ingebedde sensoren om temperatuur, rek en kracht tijdens het vormen te monitoren. Deze datagestuurde benadering maakt adaptieve controle van procesparameters mogelijk, wat resulteert in een hogere kwaliteit van onderdelen en verminderde afvalpercentages. Bovendien stelt de integratie van digitale tweelingen—virtuele replica’s van het vormproces—vooruitzien en procesoptimalisatie mogelijk, waardoor de betrouwbaarheid en productiviteit van apparatuur verder worden verbeterd.
Onderzoeksinstellingen en industriële consortia, zoals de Minerals, Metals & Materials Society (TMS) en het National Institute for Materials Science (NIMS) in Japan, werken actief samen met apparatuurfabrikanten om next-generation warmvormtechnologieën te ontwikkelen. Deze omvatten hybride vormmethoden die warmvormen combineren met superplastic vormen of incrementeel plaatvormen, waardoor de reikwijdte van haalbare geometrieën wordt vergroot en de gereedschapskosten worden verlaagd. Opmerkelijk is dat autofabrikanten en tier-one leveranciers investeren in pilotlijnen uitgerust met deze geavanceerde systemen om de adoptie van magnesiumcomponenten in voertuigstructuren te versnellen.
Vooruitkijkend is de vooruitzichten voor warmvormapparatuur gekenmerkt door toenemende automatisering, een groter gebruik van kunstmatige intelligentie voor procesoptimalisatie, en de ontwikkeling van modulaire vormcellules die snel opnieuw kunnen worden geconfigureerd voor verschillende legeringsklassen en onderdeel geometrieën. De voortdurende samenwerking tussen onderzoeksorganisaties, apparatuur leveranciers en eindgebruikers zal naar verwachting verdere doorbraken stimuleren, waardoor het warmvormen van magnesiumlegeringen kosteneffectiever en schaalbaarder wordt voor massaproductietoepassingen in de komende jaren.
Vergelijkende analyse: Warmvormen vs. koud- en heetvormen
De vergelijkende analyse van warmvormen versus koud- en heetvormen van magnesiumlegeringen is een middelpunt in de huidige materialen techniek, vooral nu de automotive en lucht- en ruimtevaartsectoren hun zoektocht naar lichte, hoogwaardige componenten intensiveren. Warmvormen, dat doorgaans in het temperatuurbereik van 200–350°C wordt uitgevoerd, wordt steeds meer erkend vanwege de mogelijkheid om de beperkingen van koud- en heetvormprocessen in evenwicht te brengen, vooral voor magnesiumlegeringen, die bekend staan om hun slechte vervormbaarheid bij kamertemperatuur en hoge reactiviteit bij verhoogde temperaturen.
Bij koudvormen vertonen magnesiumlegeringen beperkte vervormbaarheid door hun hexagonaal dichte (HCP) kristalstructuur, die de schuifsystemen bij kamertemperatuur beperkt. Dit leidt vaak tot barsten en lage rek, waardoor koudvormen alleen geschikt is voor eenvoudige vormen of uitgebreide nabewerking vereist. Daarentegen verbetert heetvormen (boven 350°C) de vervormbaarheid, maar introduceert uitdagingen zoals oxidatie, korrelgroei en verhoogd energieverbruik, die de oppervlaktekwaliteit en dimensionale nauwkeurigheid kunnen compromitteren.
Warmvormen komt naar voren als een compromis, waarbij verbeterde vervormbaarheid en vormbaarheid worden geboden zonder de zware oxidatie en korrelgroei die bij heetvormen worden gezien. Recente studies en industriële proeven in 2024–2025 hebben aangetoond dat warmvormen rekwaarden van 20–30% kan bereiken in veelvoorkomende magnesiumlegeringen zoals AZ31 en ZK60, vergeleken met minder dan 10% bij kamertemperatuur. Deze verbetering wordt toegeschreven aan de activatie van aanvullende schuifsystemen en dynamische recrystallisatie bij intermediaire temperaturen, die een gelijkmatigere vervorming vergemakkelijken en het risico op barsten verminderen.
Autofabrikanten, waaronder die verbonden aan de Toyota Motor Corporation en BMW Group, hebben lopend onderzoek en pilotproductielijnen gerapporteerd die gebruik maken van warmvormen voor structurele en interieurcomponenten. Deze inspanningen worden ondersteund door samenwerkingsprojecten met onderzoeksinstellingen zoals het National Institute for Materials Science (NIMS) in Japan en de Fraunhofer Society in Duitsland, beiden erkend voor hun geavanceerd materialenonderzoek en procesoptimalisatie.
Vooruitkijkend naar 2025 en verder, lijkt de vooruitzichten voor warmvormen van magnesiumlegeringen veelbelovend. Het proces wordt naar verwachting verder in gebruik genomen naarmate industrieën de massa van voertuigen willen verminderen en de brandstofefficiëntie willen verbeteren zonder in te boeten op mechanische prestaties. Voortdurende vooruitgangen in matrijsontwerp, temperatuurcontrole en legeringsontwikkeling worden verwacht om het toepassingsbereik uit te breiden en de kloof tussen laboratoriumresultaten en massaproductie verder te sluiten. Aangezien de druk op regelgeving voor lichte en duurzame producten toeneemt, staat warmvormen op het punt om een gangbare productieroute voor magnesiumlegeringen te worden, met een overtuigende balans tussen vervormbaarheid, kosten en prestaties.
Industrieel gebruik: Automotive, lucht- en ruimtevaart en verder
De industriële toepassing van warmvormen van magnesiumlegeringen staat op het punt om in 2025 en de komende jaren aanzienlijk te groeien, gedreven door de toenemende vraag naar lichte, hoogwaardige componenten in sectoren zoals automotive, lucht- en ruimtevaart en consumentenelektronica. Warmvormen, doorgaans uitgevoerd bij temperaturen tussen 200°C en 400°C, pakt de beperkte vervormbaarheid en vormbaarheid van magnesiumlegeringen bij kamertemperatuur aan, waardoor de productie van complexe vormen met verbeterde mechanische eigenschappen mogelijk wordt.
In de automotive industrie versnelt de druk voor brandstofefficiëntie en verlaagde emissies de adoptie van magnesiumlegeringen voor structurele en niet-structurele componenten. Grote autofabrikanten en leveranciers zijn actief bezig met het ontwikkelen van warmvormprocessen om onderdelen te vervaardigen zoals instrumentpanelen, zittingframes en transmissie behuizingen. Bijvoorbeeld, de Toyota Motor Corporation en de BMW Group hebben beide magnesiumlegeringen toepassingen onderzocht in hun voertuigplatforms, gebruikmakend van de lage dichtheid van het materiaal om aanzienlijke gewichtswinst te behalen. De trend zal naar verwachting intensiveren naarmate de druk op emissienormen wereldwijd toeneemt, en zoals elektrische voertuigen (EV’s) verdere massa-reductie vereisen om de actieradius te verlengen.
In de lucht- en ruimtevaart is de behoefte aan lichte materialen nog duidelijker. Organisaties zoals Airbus en Boeing onderzoeken het gebruik van warmgevormde magnesiumlegeringen voor binnencomponenten, zittingsstructuren en zelfs bepaalde vliegtuigonderdelen. Het vermogen om ingewikkelde geometrieën te vormen bij gematigde temperaturen zonder in te boeten op sterkte of corrosieweerstand is bijzonder aantrekkelijk voor ontwerpen van vliegtuigen van de volgende generatie. De strenge veiligheids- en prestatiestandaarden van de lucht- en ruimtevaartsector stimuleren voortdurend onderzoek naar legeringsontwikkeling en procesoptimalisatie, met samenwerkingsinspanningen van onderzoeksinstituten en industrieconsortia.
Buiten de automotive en lucht- en ruimtevaart vindt warmvormen van magnesiumlegeringen ook toepassingen in consumentenelektronica, waar de vraag naar dunne, lichte behuizingen voor laptops, tablets en smartphones blijft toenemen. Bedrijven zoals Lenovo en Samsung Electronics hebben magnesiumlegeringcomponenten in hun productlijnen opgenomen, profiterend van de gunstige sterkte-gewichtsverhouding en de elektromagnetische afschermings eigenschappen van het materiaal.
Vooruitkijkend is de vooruitzichten voor warmvormen van magnesiumlegeringen veelbelovend. Vooruitgangen in legering ontwerp, proces simulatie, en vormapparatuur worden verwacht om het toepassingsbereik verder uit te breiden. Industriepartnerschappen en door de overheid ondersteunde initiatieven, met name in Azië, Europa en Noord-Amerika, zullen waarschijnlijk de technologieoverdracht van onderzoek naar massaproductie versnellen. Aangezien duurzaamheid en energie-efficiëntie topprioriteiten blijven, zal de industriële adoptie van warmgevormde magnesiumlegeringen een cruciale rol spelen in het vormgeven van de volgende generatie lichte techniek oplossingen.
Uitdagingen en oplossingen in warmvormen van magnesiumlegeringen
Het warmvormen van magnesiumlegeringen, een proces dat doorgaans bij temperaturen tussen 200°C en 400°C wordt uitgevoerd, staat in 2025 nog steeds voor verschillende technische en industriële uitdagingen. De hexagonaal dichte (HCP) kristalstructuur van magnesium beperkt de vervormbaarheid bij kamertemperatuur, waardoor verhoogde temperaturen noodzakelijk zijn om voldoende plastische vervorming voor het vormen van complexe vormen mogelijk te maken. Echter, zelfs bij deze temperaturen blijven problemen zoals beperkte vervormbaarheid, snelle oxidatie en gereedschapsverslijt bestaan, wat de wijdverspreide acceptatie van magnesiumlegeringen in automotive, lucht- en ruimtevaart en elektronica-sectoren beïnvloedt.
Een van de belangrijkste uitdagingen is het smalle verwerkingsvenster. Magnesiumlegeringen vertonen alleen binnen een specifiek temperatuurbereik verbeterde vervormbaarheid; buiten dit venster neemt het risico op barsten of onvoldoende vervormbaarheid toe. Recent onderzoek, inclusief gezamenlijke projecten geleid door organisaties zoals het National Institute for Materials Science (NIMS) in Japan en de Fraunhofer Society in Duitsland, heeft gefocust op legeringsontwerp en procesoptimalisatie om dit venster te verruimen. Bijvoorbeeld, de toevoeging van zeldzame aardelementen en zink heeft veelbelovend resultaat opgeleverd voor het verbeteren van de vervormbaarheid en het verminderen van anisotropie, maar kosten- en toeleveringsketenoverwegingen blijven bestaan.
Oxidatie bij verhoogde temperaturen is een andere aanzienlijke zorg. Magnesium is zeer reactief, en oppervlakteoxidatie kan leiden tot defecten en gecompromitteerde mechanische eigenschappen. Om dit aan te pakken, ontwikkelen onderzoeksgroepen en industriële consortia, waaronder degenen gecoördineerd door de International Magnesium Association, geavanceerde beschermende atmosferen en coatings voor matrijzen en werkstukken. Deze oplossingen zijn gericht op het minimaliseren van oxidatie zonder overmatige complexiteit of kosten aan het vormproces toe te voegen.
Gereedschapsverslijt en levensduur van matrijzen zijn ook kritieke kwesties, aangezien de slijtage van magnesium bij warmvormtemperaturen kan leiden tot frequente onderhouds- en stilstandtijden. De Minerals, Metals & Materials Society (TMS) heeft voortdurende inspanningen benadrukt om nieuwe matrijsmaterialen en oppervlaktbehandelingen te ontwikkelen die bestand zijn tegen de zware omstandigheden van warmvormen, waardoor de economische en betrouwbare processen verbeterd worden.
Vooruitkijkend is de vooruitzichten voor warmvormen van magnesiumlegeringen voorzichtig optimistisch. Vooruitgangen in simulatie en procescontrole, ondersteund door digitale productie-initiatieven van organisaties zoals het National Institute of Standards and Technology (NIST), zullen naar verwachting de vormparameters verder verfijnen en het proefondervindelijk werken in industriële omgevingen verminderen. Aangezien duurzaamheid en gewichtsvermindering prioriteit blijven, vooral in transport, zal het overwinnen van deze uitdagingen cruciaal zijn voor de bredere acceptatie van magnesiumlegeringen in de komende jaren.
Duurzaamheid en milieu-impact
De duurzaamheid en milieu-impact van warmvormen van magnesiumlegeringen worden steeds significanter naarmate industrieën proberen hun CO2-voetafdruk te verkleinen en de hulpbronnen efficiënt te benutten. Magnesiumlegeringen, die behoren tot de lichtste bouwmaterialen, bieden aanzienlijke gewichtsreductiemogelijkheden voor de automotive, lucht, ruimtevaart en elektronica sectoren, wat direct bijdraagt aan een lagere brandstofconsumptie en emissies tijdens de gebruiksfase van producten. Warmvormen, doorgaans uitgevoerd bij temperaturen tussen 200°C en 400°C, stelt de verwerking van magnesiumlegeringen in staat met verbeterde vervormbaarheid en vormbaarheid vergeleken met koudvormen, terwijl het minder energie verbruikt dan traditionele heetvormmethoden.
In 2025 worden de milieuvoordelen van warmvormen van magnesiumlegeringen erkend in verschillende lopende industriële en onderzoeksinitiatieven. Bijvoorbeeld, de International Magnesium Association (IMA), een toonaangevende mondiale organisatie die het gebruik van magnesium bevordert, benadrukt dat de adoptie van warmvormprocessen de algehele energieconsumptie in de productie met tot 30% kan verminderen in vergelijking met conventioneel heetvormen. Deze vermindering wordt toegeschreven aan lagere verwerkingstemperaturen en kortere cyclustijden, wat ook de broeikasgasemissies die met de productie gepaard gaan, vermindert.
Bovendien is magnesium zeer recyclebaar, en het warmvormproces is compatibel met gerecycled grondstof, wat de principes van de circulaire economie ondersteunt. De European Aluminium Association, die ook lichte metalen, waaronder magnesium, dekt, meldt dat het recyclen van magnesium slechts ongeveer 5% van de energie vereist die nodig is voor primaire productie, wat de duurzaamheidsvoordelen versterkt wanneer het wordt gecombineerd met efficiënte vormtechnologieën.
Levenscyclusanalyses (LCA’s) uitgevoerd door onderzoeksconsortia en industriële partners in 2024 en 2025 geven aan dat magnesiumcomponenten die zijn geproduceerd via warmvormen tot 20% lagere cradle-to-gate CO2-emissies kunnen bereiken in vergelijking met die gevormd door traditionele methoden. Deze bevindingen stimuleren de interesse van autofabrikanten, vooral in Europa en Azië, waar de druk op voertuiguitstoot toeneemt.
Vooruitkijkend zijn de vooruitzichten voor warmvormen van magnesiumlegeringen positief, met voortdurend onderzoek dat zich richt op het verder verminderen van energieverbruik, het verbeteren van de recyclebaarheid van legeringen en het minimaliseren van procesafval. Organisaties zoals het National Institute of Standards and Technology (NIST) in de Verenigde Staten ondersteunen projecten gericht op het optimaliseren van procesparameters en het ontwikkelen van nieuwe legeringsamenstellingen die zijn afgestemd op duurzame productie. Naarmate deze inspanningen zich ontwikkelen, wordt verwacht dat de milieuvoordelen van warmvormen van magnesiumlegeringen nog duidelijker en meer uitgesproken zullen worden, wat hun rol in de overgang naar groenere productiepraktijken versterkt.
Markttrends en groeivoorspellingen (2024–2030)
De markt voor warmvormen van magnesiumlegeringen staat op het punt om aanzienlijke groei te ervaren tussen 2024 en 2030, gedreven door de toenemende vraag naar lichte materialen in de automotive, lucht- en ruimtevaart en elektronica-industrieën. Magnesiumlegeringen, bekend om hun lage dichtheid en hoge specifieke sterkte, zijn vooral aantrekkelijk voor toepassingen waarbij gewichtsreductie cruciaal is. Warmvormprocessen, doorgaans uitgevoerd bij temperaturen tussen 200°C en 400°C, maken verbeterde vervormbaarheid en vormbaarheid van magnesiumlegeringen mogelijk in vergelijking met koudvormen, waarmee een van de sleuteluitdagingen bij hun bredere acceptatie wordt aangepakt.
In 2025 blijft de automotive sector de grootste afnemer van warmgevormde magnesiumcomponenten, aangezien fabrikanten hun inspanningen intensiveren om te voldoen aan strenge emissie- en brandstofefficiëntienormen. Grote autofabrikanten en leveranciers investeren in geavanceerde vormtechnologieën om meer magnesiumonderdelen in voertuigstructuren te integreren, zoals instrumentpanelen, zittingframes en transmissiehuizen. De European Aluminium Association en de European Automobile Manufacturers’ Association hebben beide de rol van lichte metalen, waaronder magnesium, benadrukt in het behalen van de doelstellingen van de Europese Unie voor decarbonisatie en voertuig efficiëntie die vastgesteld zijn in de Green Deal.
Lucht- en ruimtevaarttoepassingen breiden ook uit, waarbij organisaties zoals NASA en de European Space Agency magnesiumlegeringen onderzoeken voor structurele en binnencomponenten om launches te verlichten en de laadcapaciteiten te verbeteren. De elektronica-industrie, met name in Azië, neemt warmgevormde magnesiumlegeringen aan voor behuizingen en frames in smartphones, laptops en andere draagbare apparaten, waarbij het materiaal profiteert van zijn elektromagnetische afschermings eigenschappen en lichtheid.
Recente gegevens van het WorldAutoSteel consortium en het International Atomic Energy Agency (dat innovatie van materialen voor energie toepassingen volgt) wijzen op een samengestelde jaarlijkse groei (CAGR) van de vraag naar magnesiumlegeringen in de orde van 7–10% tot 2030, met warmvormprocessen die een toenemend aandeel van deze groei vertegenwoordigen. Deze groei wordt ondersteund door voortdurende R&D-investeringen van toonaangevende producenten en onderzoeksinstellingen, zoals de International Magnesium Association, die wereldwijde inspanningen coördineert om legeringsamenstellingen en vormtechnieken te verbeteren.
Vooruitkijkend is de marktprognose voor warmvormen van magnesiumlegeringen robuust, met verwachte doorbraken in legeringsontwerp en vormapparatuur, die de kosten verder zullen verlagen en toepassingsgebieden zullen uitbreiden. Regelgevende steun voor gewichtsreductie, in combinatie met vooruitgangen in procesautomatisering en kwaliteitscontrole, zal de adoptie in meerdere sectoren waarschijnlijk versnellen tegen 2030.
Toekomstige vooruitzichten: Onderzoeksrichtingen en opkomende kansen
De toekomst van warmvormen van magnesiumlegeringen staat op het punt om aanzienlijke vooruitgangen te maken als de onderzoeks- en industriële belangstelling in 2025 en de komende jaren toeneemt. Magnesiumlegeringen, gewaardeerd om hun lage dichtheid en hoge specifieke sterkte, worden steeds meer gericht op lichtere toepassingen in automotive, lucht- en ruimtevaart, en elektronica sectoren. Echter, hun beperkte vervormbaarheid bij kamertemperatuur heeft de wijdverspreide acceptatie historisch beperkt. Warmvormen—verwerking bij intermediaire temperaturen (gewoonlijk 200–400°C)—biedt een veelbelovende route om deze uitdagingen te overwinnen door de vervormbaarheid te verbeteren en de vormkrachten te verminderen.
Huidig onderzoek richt zich op het optimaliseren van procesparameters, legeringsamenstellingen en gereedschapsontwerpen om de vervormbaarheid en mechanische eigenschappen van magnesiumcomponenten verder te verbeteren. Bijzonder is dat verschillende toonaangevende onderzoeksinstellingen en industrieconsortia samenwerken om nieuwe magnesiumlegeringklassen te ontwikkelen die specifiek zijn afgestemd op warmvormen. Bijvoorbeeld, de Minerals, Metals & Materials Society (TMS) blijft internationale symposia en werkgroepen coördineren die zijn gewijd aan innovaties in magnesiumverwerking, ter bevordering van kennisuitwisseling en standaardisatie-inspanningen.
Opkomende kansen worden ook gedreven door de druk van de automotive industrie om te voldoen aan strengere emissie- en brandstofefficiëntienormen. Grote autofabrikanten en leveranciers investeren in pilotlijnen en demonstratieprojecten om warmvormprocessen voor structurele en sluitingsonderdelen te valideren. De Magna International, een wereldwijde automotive leverancier, heeft publiekelijk de belofte gedaan om zijn portfolio aan lichte materialen, inclusief magnesium, uit te breiden ter ondersteuning van voertuigstructuren van de volgende generatie. Evenzo ondersteunen de European Aluminium Association en zijn partners onderzoek naar multi-materiaalverbindingen en hybride structuren, waarbij warmgevormde magnesium een cruciale rol zou kunnen spelen.
Op wetenschappelijk vlak worden geavanceerde karakterisatietechnieken—zoals in-situ elektronenmicroscopie en synchrotron X-ray diffractie—benut om de microstructurele evolutie van magnesiumlegeringen tijdens warmvormen te ontrafelen. Deze kennis wordt verwacht te helpen bij het ontwerpen van nieuwe legeringen met verbeterde textuurcontrole en verminderde anisotropie, die belangrijke barrières voor industriële acceptatie aanpakken. Bovendien worden digitale productie- en simulatiehulpmiddelen geïntegreerd in procesontwikkeling, waarmee snelle prototyping en optimalisatie van vormoperaties mogelijk is.
Vooruitkijkend is het waarschijnlijk dat de komende jaren de commercialisering van warmgevormde magnesiumcomponenten zal toenemen, vooral in elektrische voertuigen en lichte consumentenelektronica. Voortdurende samenwerking tussen de academische wereld, industrie en normenorganisaties zal essentieel zijn om resterende technische uitdagingen aan te pakken en om de betrouwbaarheid en kosteneffectiviteit van deze geavanceerde productiesystemen te waarborgen.