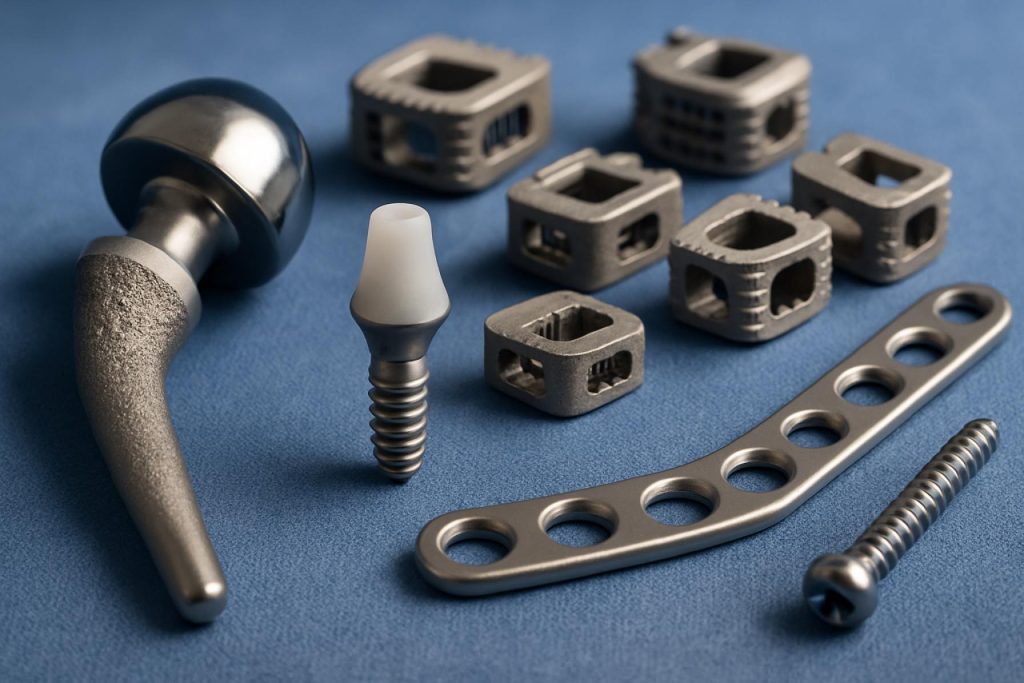
Производство имплантируемых устройств из титанового сплава в 2025 году: раскрытие возможностей новой биосовместимости и роста рынка. Изучите, как передовые сплавы и прецизионная инженерия формируют будущее медицинских имплантов.
- Резюме: Рыночные перспективы на 2025 год и ключевые факторы
- Мировой размер рынка, темпы роста и прогнозы до 2030 года
- Прорывы в материалах титанового сплава и технологиях поверхностей
- Регуляторная среда и соблюдение норм (FDA, ISO, EU MDR)
- Ведущие производители и стратегические партнерства
- Применения: ортопедия, стоматология, сердечно-сосудистая хирургия и не только
- Инновации в производстве: аддитивное производство и прецизионная механика
- Динамика цепочки поставок и закупка сырья
- Устойчивость, переработка и экологический след
- Будущие тренды: умные импланты, персонализация и цифровая интеграция
- Источники и ссылки
Резюме: Рыночные перспективы на 2025 год и ключевые факторы
Сектор производства имплантируемых устройств из титанового сплава готов к значительному росту в 2025 году, чему способствует объединение передовой науки о материалах, технологий прецизионного производства и растущего глобального спроса на медицинское обслуживание. Титановые сплавы, особенно Ti-6Al-4V, остаются предпочтительным материалом для ортопедических, стоматологических и сердечно-сосудистых имплантов благодаря их превосходной биосовместимости, коррозионной стойкости и механической прочности. Сектор наблюдает за увеличением применения аддитивного производства (AM) и передовой механики, что позволяет производить сложные имплантаты, индивидуально подобранные для пациента, с повышенной остеоинтеграцией и сокращенными сроками выполнения.
Ключевые игроки отрасли, такие как Smith & Nephew, Zimmer Biomet и Stryker, активно инвестируют в цифровые производственные платформы и автоматизацию для оптимизации производства и обеспечения отслеживаемости. Эти компании также расширяют свои глобальные производственные базы, открывая новые предприятия и создавая партнерства в Азиатско-Тихоокеанском регионе и Европе для удовлетворения растущего регионального спроса. Например, Stryker продолжает развивать свои возможности аддитивного производства, сосредоточив внимание на собственных технологиях 3D-печати из титана для ортопедических и спинальных имплантов.
Регуляторная среда меняется, и такие агентства, как Управление по контролю за продуктами и лекарствами США (FDA) и Европейское агентство по лекарственным средствам (EMA), подчеркивают необходимость более строгих контрольных мер качества и постмаркетингового наблюдения для имплантируемых устройств. Это побуждает производителей инвестировать в современные системы контроля и цифровое управление качеством, что, в свою очередь, способствует инновациям в секторе. Кроме того, стремление к устойчивости влияет на выбор материалов и производственные практики, компании исследуют замкнутый цикл переработки титана и энергоэффективные методы производства.
Данные рынка от ведущих поставщиков титана, включая TIMET (Titanium Metals Corporation) и VSMPO-AVISMA, указывают на стабильное предложение и продолжающиеся инвестиции в производство медицинского титана высокой чистоты. Эти поставщики имеют решающее значение для поддержки роста сектора, обеспечивая стабильное качество и отслеживаемость сырья. Ожидается, что интеграция цифровых решений в цепочке поставок дополнительно повысит прозрачность и реактивность в ближайшие годы.
Смотря в будущее, рынок производства имплантируемых устройств из титанового сплава будет получать выгоду от демографических тенденций, таких как старение населения и увеличение заболеваемости опорно-двигательным аппаратом. Перспективы сектора на 2025 год и далее характеризуются продолжающейся инновацией, глобальной экспансией и акцентом на соблюдение нормативных требований и устойчивое развитие, что позиционирует его как ключевой фактор следующего поколения медицинского обслуживания.
Мировой размер рынка, темпы роста и прогнозы до 2030 года
Глобальный рынок имплантируемых устройств из титанового сплава готов к значительному росту к 2025 году и в последующие годы десятилетия, чему способствует растущий спрос на передовые ортопедические, стоматологические и сердечно-сосудистые импланты. Титановые сплавы, особенно Ti-6Al-4V, предпочитают за их биосовместимость, коррозионную стойкость и механическую прочность, что делает их предпочтительным материалом для широкого спектра медицинских имплантов.
В 2025 году прогнозируется, что размер рынка имплантируемых устройств из титанового сплава превысит несколько миллиардов долларов США, при этом ведущие производители сообщают о сильной очереди заказов и расширении мощностей. Например, Smith+Nephew, крупнейшая глобальная медицинская технологическая компания, продолжает инвестировать в решения на основе титана для ортопедии, в то время как Zimmer Biomet и Stryker расширяют свои портфели имплантов из титанового сплава для реконструкции суставов и травматологических приложений. DePuy Synthes, часть Johnson & Johnson, также является значительным игроком, использующим титановые сплавы в системах спинальных и черепных имплантов.
Прогнозируемые темпы роста сектора остаются сильными, с прогнозируемыми среднегодовыми темпами роста (CAGR) в диапазоне от 5% до 7% до 2030 года, согласно консенсусу отрасли и перспективам компаний. Это расширение поддерживается несколькими факторами:
- Увеличение глобальной заболеваемости опорно-двигательного аппарата и старение населения, особенно в Северной Америке, Европе и Азиатско-Тихоокеанском регионе.
- Технологические достижения в аддитивном производстве (3D-печать) титановыми имплантами, позволяющие создавать индивидуальные решения и более сложные геометрии. Такие компании, как Smith+Nephew и Stryker, сделали значительные инвестиции в 3D-напечатанные титановые импланты.
- Расширение инфраструктуры здравоохранения и увеличение доступа к современным хирургическим процедурам на развивающихся рынках.
Перспективы на ближайшие несколько лет включают продолжение инноваций в обработке поверхностей и покрытиях для улучшения остеоинтеграции и уменьшения рисков инфекций. Кроме того, устойчивая цепочка поставок и закупка сырья остаются ключевыми направлениями, при этом крупнейшие поставщики титана, такие как TIMET (Titanium Metals Corporation) и VSMPO-AVISMA, поддерживают сектор медицинских устройств высокочистыми титанами.
К 2030 году ожидается, что рынок имплантируемых устройств из титанового сплава достигнет новых высот, чему будет способствовать продолжаемое НИОКР, регуляторные одобрения новых устройств и глобальная тенденция к медицинскому обслуживанию на основе ценности. Ожидается, что траектория роста сектора останется позитивной, при этом ведущие производители и поставщики играют ключевые роли в формировании будущего имплантируемой медицинской технологии.
Прорывы в материалах титанового сплава и технологиях поверхностей
Ландшафт производства имплантируемых устройств из титанового сплава испытывает значительные прорывы как в науке о материалах, так и в инженерии поверхности на 2025 год. Титановые сплавы, особенно Ti-6Al-4V, продолжают оставаться золотым стандартом для ортопедических, стоматологических и сердечно-сосудистых имплантов благодаря их исключительной биосовместимости, коррозионной стойкости и механической прочности. Однако недавние достижения расширяют границы возможностей этих материалов, сосредотачиваясь на улучшении остеоинтеграции, снижении рисков инфекций и обеспечении индивидуальных решений для пациентов.
Одним из самых заметных трендов является разработка и коммерциализация титановыми сплавами следующего поколения с индивидуально подобранными микроструктурами. Компании, такие как ATI и Carpenter Technology Corporation, активно производят современные титановые сплавы с улучшенной стойкостью к усталости и низким модулем упругости, которые лучше соответствуют свойствам человеческой кости и уменьшают эффект защиты от нагрузок. Эти сплавы принимаются для нагрузочных имплантов, таких как замены тазобедренного и коленного суставов, где долговечность и результаты для пациентов имеют критическое значение.
Технологии модификации поверхности также демонстрируют быстрые инновации. Плазменное электрохимическое окисление (PEO), лазерное текстурирование и методы нано-покрытия интегрируются в производственные процессы для создания биоактивных поверхностей, которые способствуют более быстрому росту костной ткани и уменьшают прилипание бактерий. Zimmer Biomet и Smith+Nephew внедрили собственные методы обработки поверхности для своих титановыми имплантами, стремясь ускорить заживление и минимизировать послеоперационные осложнения. Эти технологии поверхности все чаще подтверждаются клиническими данными, поддерживающими их использование в регуляторных подачах и закупках в больницах.
Аддитивное производство (AM), особенно плавление электронным лучом (EBM) и селективное лазерное плавление (SLM), революционизирует производство сложных, индивидуально подобранных титановых имплантов. Stryker и DePuy Synthes создали специализированные предприятия AM, что позволяет производить пористые структуры, имитирующие естественную костную архитектуру и улучшающие биологическую фиксацию. Масштабируемость и индивидуализация, которые предлагает AM, ожидается, будут способствовать дальнейшему принятию в ближайшие годы, особенно по мере упрощения регуляторных путей для 3D-печатных имплантов.
Смотря в будущее, интеграция антимикробных покрытий, технологий умных сенсоров и биоразлагаемых легирующих элементов ожидается, чтобы еще больше расширить функциональность имплантируемых устройств из титанового сплава. Лидеры отрасли инвестируют в НИОКР, сотрудничая с академическими учреждениями и стартапами в области медицинских устройств, чтобы ускорить переход этих инноваций от лаборатории к клинике. Поскольку регуляторные агентства продолжают обновлять стандарты для новых материалов и процессов, следующие несколько лет обещают волну имплантов из титанового сплава, которые будут безопаснее, долговечнее и лучше отвечать потребностям пациентов.
Регуляторная среда и соблюдение норм (FDA, ISO, EU MDR)
Регуляторная среда для имплантируемых устройств из титанового сплава быстро развивается в 2025 году, формируемая строгими требованиями со стороны главных властей, таких как Управление по контролю за продуктами и лекарствами США (FDA), Международная организация по стандартизации (ISO) и Регулирование медизделий ЕС (EU MDR). Эти структуры имеют ключевое значение для производителей, поскольку они определяют стандарты безопасности, эффективности и управления качеством в производстве титановых имплантов, которые широко используются в ортопедии, стоматологии и сердечно-сосудистой хирургии.
В Соединенных Штатах FDA продолжает активно применять свои правила о качестве (QSR) 21 CFR Part 820, которые требуют обширных систем управления качеством для производителей медицинских устройств. Для имплантов из титанового сплава это включает строгий контроль за источниками материалов, отслеживаемостью и валидацией процессов. Путевые журналы предмаркетингового одобрения (PMA) и 510(k) требуют обширных данных о биосовместимости и механическом тестировании, особенно для новых составов титанового сплава или аддитивных производственных (AM) техник. Ведущие производители США, такие как Zimmer Biomet и Smith+Nephew, инвестируют в современные системы соблюдения норм, чтобы оптимизировать подачи и постмаркетинговое наблюдение, отражая растущее внимание агентства к реальным данным и отслеживанию устройств.
На глобальном уровне ISO 13485:2016 остается краеугольным камнем для управления качеством в производстве медицинских устройств, с акцентом на управление рисками, валидацию процессов и контроль поставщиков. Для имплантов из титанового сплава стандарты серии ISO 5832 определяют химический состав и механические свойства, требуемые для хирургических имплантов, обеспечивая постоянство и безопасность на международных рынках. Такие компании, как Sandvik, крупный поставщик титанов порошков и прутков, и Sandvik Materials Technology (сейчас Alleima), активно участвуют в согласовании своих производственных процессов и документации с этими стандартами с целью поддержки глобальных производителей устройств.
В Европейском Союзе реализация Регулирования EU MDR (Регламент (ЕС) 2017/745) значительно повысила требования к клиническим доказательствам, постмаркетинговому наблюдению и отслеживаемости. Система уникальной идентификации устройства (UDI) регламента и более строгие требования к обзору уполномоченных органов привели к более длительным срокам одобрения и увеличению документации для имплантов из титанового сплава. Европейские производители, такие как Stryker и DePuy Synthes, адаптируются, улучшая свои команды по регуляторным вопросам и инвестируя в цифровые инструменты соблюдения норм.
Смотря вперед, ожидается, что регуляторная среда станет еще более гармонизированной, с продолжающимися усилиями по согласованию требований FDA, ISO и EU MDR. Эта тенденция, вероятно, будет способствовать дальнейшим инвестициям в цифровые системы управления качеством, аналитике данных в реальном времени и передовым решениям для отслеживания среди производителей титанов имплантов. По мере ужесточения регуляторного контроля компании, которые проактивно адаптируются к этим меняющимся стандартам, окажутся в наилучшей позиции для поддержания доступа на рынок и обеспечения безопасности пациентов.
Ведущие производители и стратегические партнерства
Сектор имплантируемых устройств из титанового сплава в 2025 году характеризуется динамичным ландшафтом ведущих производителей и растущим акцентом на стратегические партнерства для стимулирования инноваций, масштабирования и соблюдения нормативных требований. Титановые сплавы, особенно Ti-6Al-4V, остаются предпочтительным материалом для ортопедических, стоматологических и сердечно-сосудистых имплантов благодаря своей превосходной биосовместимости, коррозионной стойкости и механической прочности.
Среди глобальных лидеров Smith & Nephew продолжает расширять свой портфель титановыми ортопедическими имплантами, используя передовые технологии аддитивного производства (AM) для создания высокоиндивидуализированных и пористых структур, способствующих остеоинтеграции. Аналогично, Zimmer Biomet сохраняет сильные позиции на рынке, продолжая инвестировать как в традиционное литье, так и в передовые технологии 3D-печати для спинальных, тазобедренных и коленных имплантов.
В Азиатско-Тихоокеанском регионе United Orthopedic Corporation стал значимым игроком, сосредоточив внимание на системах замены суставов из титановыми сплавами и расширяя свои производственные мощности, чтобы удовлетворить растущий региональный спрос. Тем временем, Stryker остается в авангарде инноваций, в частности благодаря приобретению компаний, специализирующихся на аддитивном производстве и технологиях модификации поверхности, которые критически важны для имплантируемых устройств следующего поколения.
Стратегические партнерства становятся все более важными для формирования конкурентного ландшафта. Например, DePuy Synthes, часть Johnson & Johnson, вошла в сотрудничество с компаниями в области науки о материалах и цифрового здравоохранения для интеграции технологий умных сенсоров в титаны импланты, стремясь улучшить постоперационное наблюдение и результаты для пациентов. Medtronic также примечен своими союзами с поставщиками титана и контрактными производителями, что обеспечивает надежную цепочку поставок и быстрое масштабирование новых продуктовых линий.
Поставщики сырья, такие как TIMET (Titanium Metals Corporation) и VSMPO-AVISMA играют основополагающую роль, предоставляя высокочистые титановые сплавы производителям медицинских устройств по всему миру. Эти поставщики все чаще участвуют в совместных предприятиях с производителями устройств для совместной разработки собственных марок сплавов, адаптированных для конкретных приложений имплантов.
Смотря вперед, ожидается, что в ближайшие несколько лет произойдет дальнейшая консолидация среди производителей, более глубокая интеграция цифровых производственных технологий и расширенные межсекториальные партнерства, особенно по мере усиления регуляторных требований к отслеживаемости и производительности. Перспективы сектора остаются прочными, нарастая на фоне демографических тенденций, технологических достижений и продолжающегося сдвига к индивидуально подобранным имплантам из титанового сплава высокой производительности.
Применения: ортопедия, стоматология, сердечно-сосудистая хирургия и не только
Имплантируемые устройства из титанового сплава занимают центральное место в современной медицине, их применение охватывает ортопедию, стоматологию, сердечно-сосудистую хирургию и новые области. В 2025 году спрос на эти устройства продолжает расти благодаря старению мирового населения, увеличению заболеваемости хроническими заболеваниями и достижениям в хирургических техниках. Титановые сплавы, особенно Ti-6Al-4V, остаются предпочтительным материалом благодаря своей биосовместимости, коррозионной стойкости и механической прочности.
В ортопедии импланты из титанового сплава широко используются для замены суставов, фиксации позвоночника и травматологических устройств. Ведущие производители, такие как Zimmer Biomet и Smith+Nephew, расширяют свои портфели, включая импланты, индивидуально подобранные для пациентов, и компоненты, напечатанные на 3D-принтере, используя аддитивное производство для улучшения остеоинтеграции и сокращения времени восстановления. Ожидается, что применение 3D-печати ускорится, позволяя создавать более сложные геометрии и пористые структуры, имитирующие естественную кость, что подтверждается продолжающимися инвестициями от Stryker в современные производственные предприятия.
Стоматологические приложения представляют собой другой значимый сегмент, где титановые сплавы используются для корневидных имплантов, абатментов и протетических конструкций. Компании, такие как Nobel Biocare и Dentsply Sirona, стоят на переднем крае, предлагая системы, которые интегрируют цифровые рабочие процессы и технологии поверхностных обработок для улучшения остеоинтеграции и долгосрочной стабильности. Стоматологический сектор также наблюдает сдвиг в сторону минимально инвазивных процедур, что дополнительно увеличивает спрос на прецизионно изготовленные титановые компоненты.
В сердечно-сосудистой области титановые сплавы необходимы для оболочек кардиостимуляторов, рамок сердечных клапанов и сосудистых стентов. Medtronic и Boston Scientific используют немагнитные и коррозионно-стойкие свойства титана для обеспечения долговечности устройств и совместимости с диагностической визуализацией. В следующих нескольких годах ожидается увеличение использования титана в транскатетерных и минимально инвазивных сердечно-сосудистых устройствах, отражая более широкую тенденцию к менее инвазивным вмешательствам.
За пределами этих утвержденных областей титановые сплавы исследуются для устройств нейростимуляции, кохлеарных имплантов и даже систем доставки лекарств. Универсальность титана, в сочетании с продолжающимися достижениями в модификации поверхностей и аддитивном производстве, скорее всего, расширит его области применения. Лидеры отрасли, такие как DePuy Synthes и Smith+Nephew, инвестируют в НИОКР для решения новых клинических потребностей, включая антимикробные покрытия и технологии умных имплантов.
Смотря в будущее, перспективы производства имплантируемых устройств из титанового сплава остаются прочными. Слияние цифрового проектирования, аддитивного производства и науки о материалах приведет к инновациям, сосредоточенным на индивидуально подобранных решениях и улучшении клинических результатов. Регуляторные органы также адаптируются к этим достижениям, упрощая пути одобрения новых имплантов на основе титана, что должно ускорить рост рынка до 2025 года и далее.
Инновации в производстве: аддитивное производство и прецизионная механика
Ландшафт производства имплантируемых устройств из титанового сплава претерпевает значительные изменения в 2025 году, что обусловлено слиянием аддитивного производства (AM) и передовой прецизионной механики. Титановые сплавы, особенно Ti-6Al-4V, остаются предпочитаемым материалом для ортопедических, стоматологических и сердечно-сосудистых имплантов благодаря своей биосовместимости, коррозионной стойкости и механической прочности. Применение инновационных производственных технологий позволяет производить более сложные, индивидуально подобранные и высокопроизводительные импланты.
Аддитивное производство, особенно селективное лазерное плавление (SLM) и плавление электронным лучом (EBM), стоит на переднем крае этой эволюции. Эти технологии позволяют производить сложные решетчатые структуры и пористые поверхности, которые улучшают остеоинтеграцию и уменьшают вес имплантов. Ведущие производители медицинских устройств, такие как Stryker и Zimmer Biomet, активно инвестируют в возможности AM, с процессом AMagine от Stryker и использованием EBM от Zimmer Biomet для ортопедических имплантов. Эти компании используют AM для производства имплантов и компонентов, соответствующих индивидуальному подходу, с оптимизированными геометриями, которые сложно или невозможно достичь с помощью традиционных вычитающих методов.
Прецизионная механика продолжает оставаться важной, особенно для достижения необходимых допусков и отделки поверхностей, требуемых для критических интерфейсов имплантов. Компании, такие как DePuy Synthes (компания Johnson & Johnson) и Smith+Nephew, продолжают улучшать свои процессы ЧПУ, интегрируя автоматизацию и контроль качества в реальном времени, чтобы обеспечить согласованность и соблюдение строгих норм. Гибридные производственные подходы, объединяющие AM для производства близких к нетто-форми и прецизионной механики для финишной обработки, становятся все более распространенными.
В 2025 году цифровизация и основанное на данных производство еще больше улучшают контроль процессов и отслеживаемость. Интеграция мониторинга в процессе AM, а также передовой метрологии в механике снижает количество дефектов и повышает производительность. Компании, такие как GE (через GE Additive), возглавляют реализацию замкнутых систем, использующих данные в реальном времени для корректировки параметров и обеспечения качества деталей.
Смотря в будущее, ожидается, что в ближайшие несколько лет будет дальнейшее расширение применения AM для массовой индивидуализации, при этом регуляторные органы будут предоставлять более четкие пути для одобрения аддитивно произведенных имплантов. Продолжающаяся эволюция производства титанового порошка, переработка и технологии постобработки будут способствовать снижению затрат и расширению диапазона имплантируемых устройств, которые могут извлечь выгоду из этих инноваций в производстве.
Динамика цепочки поставок и закупка сырья
Цепочка поставок для имплантируемых устройств из титанового сплава характеризуется сложным взаимодействием между закупкой сырья, производством сплавов и прецизионным производством, все это поддерживается строгими регуляторными требованиями. На 2025 год спрос на титановые сплавы, в первую очередь на Ti-6Al-4V (категория 5) и его медицинские варианты, остается большим, что обусловлено продолжающимся ростом рынков ортопедических, стоматологических и сердечно-сосудистых имплантов. Биосовместимость, коррозионная стойкость и механическая прочность титановых сплавов делают их предпочтительным материалом для нагружаемых и долговременных имплантируемых устройств.
Сырой титан в основном добывается из минеральных концентратов, таких как ильменит и рутил, причем крупные горнодобывающие предприятия расположены в Австралии, Южной Африке и Китае. Преобразование этих минералов в высокочистый титан является преобладающим среди нескольких глобальных производителей, включая TOYOTA TSUSHO CORPORATION и VSMPO-AVISMA Corporation. VSMPO-AVISMA Corporation, расположенная в России, признана крупнейшим производителем титана в мире, поставляя значительную долю медицинского титана, используемого в производстве имплантов по всему миру. Однако продолжающиеся геополитические напряженности и торговые ограничения побуждают производителей медицинских устройств диверсифицировать свою базу поставщиков и искать альтернативные источники, особенно в Японии, США и Европе.
Титановые сплавные слитки и полуфабрикаты далее обрабатываются специализированными компаниями, такими как TIMET (Titanium Metals Corporation), которая управляет предприятиями в Северной Америке и Европе, и Sandvik, шведской инженерной группой с сильным присутствием в области медицинских материалов. Эти компании поставляют прецизионно кованные бары, пластины и стержни, соответствующие строгим стандартам производителей имплантируемых устройств. Цепочка поставок поддерживается также такими фирмами, как Carpenter Technology Corporation, которая фокусируется на высокопроизводительных специализированных сплавах для медицинских применений.
В 2025 году цепочка поставок титана сталкивается с несколькими проблемами, включая волатильность цен из-за затрат на энергетику, логистические сбои и необходимость отслеживаемости и сертификации. Производители медицинских устройств все чаще требуют полной документированной истории материалов и соблюдения международных стандартов, таких как ASTM F136 и ISO 5832-3. Для удовлетворения этих требований поставщики инвестируют в системы цифровой отслеживаемости и более тесную интеграцию с нижестоящими партнерами.
Смотря вперед, прогнозы для производства имплантируемых устройств из титанового сплава остаются позитивными, при этом ожидаемый рост минимально инвазивных и индивидуально подобранных имплантов будет способствовать спросу на изделия из титана высокой степени. Однако устойчивость цепочки поставок и устойчивое закупка сырья останутся критическими приоритетами, подталкивающими ведущих игроков к дальнейшим инвестициям в переработку, альтернативные источники сырья и региональные центры поставок.
Устойчивость, переработка и экологический след
Устойчивость и экологический след производства имплантируемых устройств из титанового сплава становятся все более важными для отрасли медицинских устройств в 2025 году и на последующие годы. Титановые сплавы, особенно Ti-6Al-4V, предпочтительны за их биосовместимость, коррозионную стойкость и механическую прочность, но их извлечение, обработка и производство требуют больших затрат энергии и производят значительные отходы. По мере роста регуляторного и общественного давления производители принимают новые стратегии для минимизации воздействия на окружающую среду и повышения круговоротности.
Ключевым трендом является интеграция процессов переработки как для предварительного потребления (отходы производства), так и постпотребительского (извлеченные импланты) титана. Ведущие производители, такие как TIMET и Carpenter Technology Corporation инвестируют в замкнутые системы переработки, возвращая титановые отходы и обрезки от операций обработки. Эти материалы переплавляются и легируются заново, уменьшая потребность в первичном титановом сплаве и снижая связанные с этим углеродные выбросы. Sandvik, крупный поставщик титанов для медицинских применений, также внедрил передовые протоколы по переработке, стремясь увеличить долю переработанных материалов в своих медицинских сплавах.
Аддитивное производство (AM), или 3D-печать, является еще одной областью, которая способствует улучшению устойчивости. Технологии AM, широко используемые такими компаниями, как Stryker и Zimmer Biomet, позволяют производить импланты с близкими к нетто-формами, существенно уменьшая запасы материалов по сравнению с традиционной вычитающей механикой. Это не только сохраняет сырой титан, но и уменьшает потребность в энергии для постобработки и отделки. Более того, AM позволяет использовать переработанные титановые порошки, еще больше закрывая материалопат.
Оценки экологического воздействия также включаются в управление цепочкой поставок. Компании, такие как Smith+Nephew, все чаще открыты в своих источниках и производственных практиках, публикуя отчеты по устойчивому развитию и устанавливая цели по сокращению выбросов и эффективному использованию ресурсов. Ожидается, что переход на возобновляемые источники энергии в установках плавления и обработки титана ускорится, и несколько производителей уже тестируют нервные и ветряные установки.
Смотря вперед, регуляторные рамки в ЕС и Северной Америке, вероятно, будут требовать более строгой отчетности и снижения экологических воздействий для производителей медицинских устройств. Отраслевые организации, такие как International Titanium Association, сотрудничают с производителями, чтобы разработать передовые методы для переработки и управления жизненным циклом имплантов из титана. В результате в следующих нескольких годах произойдет продолжение перехода к более экологически чистому производству, сосредоточенного на максимальной переработке, минимизации отходов и сокращении углеродного следа имплантируемых устройств из титанового сплава.
Будущие тренды: умные импланты, персонализация и цифровая интеграция
Ландшафт производства имплантируемых устройств из титанового сплава быстро развивается, и 2025 год знаменует собой ключевой момент для интеграции умных технологий, персонализации и цифровых рабочих процессов. Титановые сплавы, особенно Ti-6Al-4V, остаются предпочтительным материалом для ортопедических, стоматологических и сердечно-сосудистых имплантов благодаря своей биосовместимости, коррозионной стойкости и механической прочности. Однако следующие несколько лет, вероятно, будут свидетелями трансформационных тенденций, которые переопределят как процесс производства, так и клиническую эффективность этих устройств.
Основным трендом является рост умных имплантов — устройств, встроенных с сенсорами или электронными компонентами, которые мониторят физиологические параметры, выявляют ранние признаки осложнений и обеспечивают передачу данных в реальном времени. Ведущие производители, такие как Smith+Nephew и Zimmer Biomet, инвестируют в исследования и партнерства для разработки титанных имплантов с интегрированной сенсорной технологией. Ожидается, что эти умные системы улучшат постоперационный уход и результаты для пациентов, предоставляя клиницистам действенные данные, что, вероятно, ускорится по мере развития беспроводного питания и миниатюрной электроники.
Персонализация является еще одним ключевым фактором, обеспечиваемым благодаря достижениям в цифровом проектировании и аддитивном производстве (AM). Компании, такие как Stryker и DePuy Synthes, используют 3D-печать для производства индивидуально подобранных титанных имплантов, адаптированных к индивидуальной анатомии и патологии пациента. Такой подход не только улучшает соответствие и функцию импланта, но также сокращает время операции и риск осложнений. Ожидается, что применение AM будет расширяться в 2025 году и далее, поскольку регуляторные пути становятся более четкими, а возможности печати в больницах растут.
Цифровая интеграция производственных и клинических рабочих процессов также набирает популярность. Цифровые двойники, оптимизация проектирования на основе ИИ и облачные платформы совместной работы внедряются производителями для упрощения процесса разработки и валидации титанных имплантов. GE, через свое подразделение аддитивного производства, активно разрабатывает цифровые решения для сектора медицинских устройств, обеспечивая мониторинг качества производства в реальном времени и отслеживаемость каждого импланта. Эта цифровая нить от проектирования до развертывания предполагается как стандартная практика, повысившая эффективность и соблюдение норм.
Смотря вперед, слияние умных функций, персонализации и цифровой интеграции определит следующее поколение имплантируемых устройств из титанового сплава. Поскольку производители продолжают инвестировать в НИОКР и цифровую инфраструктуру, сектор готов к значительным достижениям в уходе за пациентами, производительности устройств и гибкости производства до 2025 года и в последующие годы.